Advanced Manufacturing Techniques for High-Precision Laser Projection Gratings From Diamond-Point Burnishing to Modern Nanotechnology
Advanced Manufacturing Techniques for High-Precision Laser Projection Gratings From Diamond-Point Burnishing to Modern Nanotechnology - Diamond Point Burnishing Sets 5-Nanometer Accuracy Standard in Modern Grating Production
Diamond point burnishing has become a cornerstone in the production of modern gratings, establishing a stringent 5-nanometer accuracy standard. This exceptional precision is paramount for creating high-performance optical components, necessitating extraordinarily smooth surfaces with minimal imperfections. The method distinguishes itself from conventional machining approaches by utilizing sophisticated diamond tools. These tools not only elevate surface quality but also curtail the necessity for extensive post-processing. The escalating need for components with nanoscale features has driven the evolution of related technologies, including single-point diamond turning and ultra-precision grinding, constantly pushing the boundaries of what can be achieved in optical manufacturing. This development showcases the vital confluence of advanced engineering and cutting-edge technology to satisfy the demands of contemporary applications. The ability to achieve such remarkable accuracy through diamond burnishing illustrates the progress in this field, enabling the creation of highly precise optical components with implications for a variety of industries.
Diamond point burnishing, using specialized tools with diamond tips, has emerged as a key technique in producing high-quality gratings. It can achieve exceptionally smooth surfaces with roughness values reaching as low as 10 nanometers, a crucial aspect for optimized laser performance. This precision comes from the 5-nanometer accuracy standard achievable with these tools.
The burnishing process itself introduces intricately patterned surfaces which can enhance a material's light absorption and reflection properties, impacting the final performance of optical components. However, achieving these finely controlled surface structures requires careful attention to the process parameters. For instance, the heat produced during burnishing can introduce thermal distortions in the materials, potentially impacting the accuracy of the grating. Advanced cooling techniques mitigate these issues, helping maintain tolerances within strict limits.
Furthermore, while diamond is intrinsically durable, advancements in coating technologies provide enhanced resilience for the burnishing tools. This increased lifespan translates to reduced tool replacement frequency, improving overall manufacturing efficiency, particularly in demanding high-precision environments. One of the advantages of this technique is its potential to reduce post-processing needs. The burnished surface often achieves a sufficient level of smoothness, minimizing the need for extensive polishing, thereby streamlining the manufacturing process.
The integration of CNC systems has automated the process, opening doors to increased scalability and consistency in producing intricate geometries. This control allows for efficient replication of complex patterns across numerous pieces. The versatility of diamond burnishing extends to a wide array of materials, including metals and composites, expanding its use in industries like aerospace and semiconductor manufacturing. This technique is also useful as a preparatory step for other surface treatments. For instance, it can improve the adhesion and performance of coatings and films applied to enhance the optical properties of surfaces in systems like laser projection systems.
Nevertheless, the effective use of diamond burnishing demands a high degree of operator skill, resulting in extended training periods for technicians. Mastering the nuances of the technique is essential for realizing the desired precision and quality of the gratings. This highlights the vital role of well-trained operators in achieving the high-precision outcomes that diamond burnishing can provide.
Advanced Manufacturing Techniques for High-Precision Laser Projection Gratings From Diamond-Point Burnishing to Modern Nanotechnology - Laser Direct Writing Advances Freeform Pattern Development at 50nm Resolution
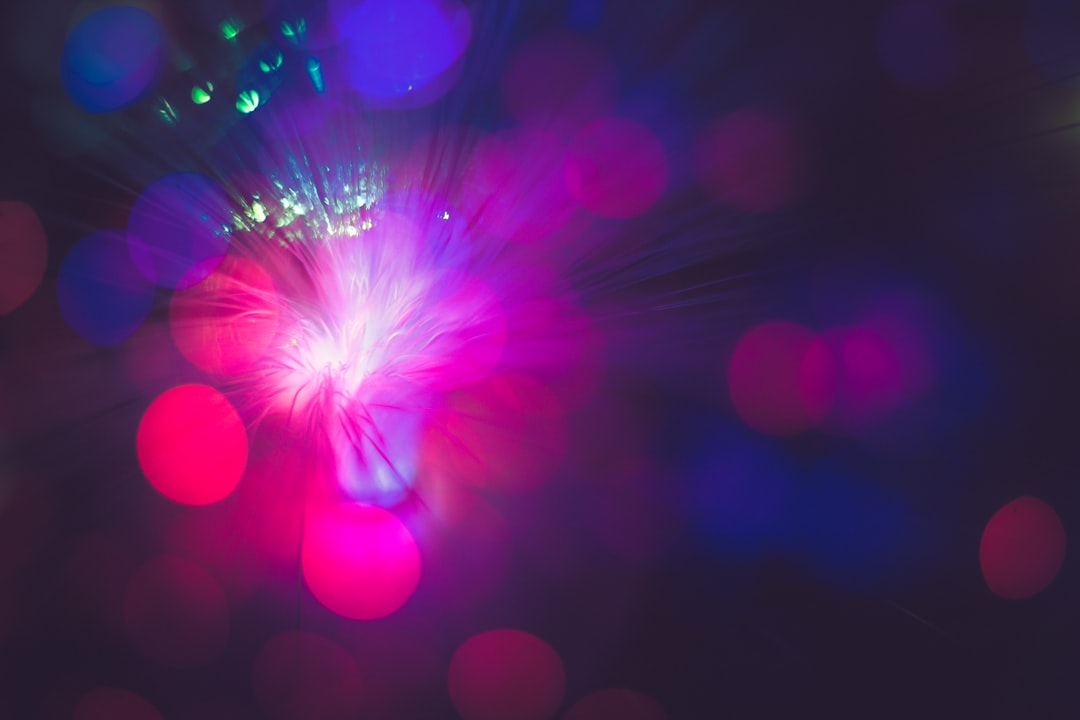
Laser direct writing (LDW) offers a compelling approach to crafting intricate freeform patterns with remarkable precision, reaching resolutions as fine as 50 nanometers. This maskless fabrication method proves advantageous in various applications, including micro-electromechanical systems and the production of optical elements. The ability to avoid masks enhances flexibility and efficiency, especially in manufacturing environments that demand adaptability.
Recent progress in LDW, incorporating techniques like two-photon polymerization, has significantly boosted its performance and expanded its potential. This improvement allows for the construction of incredibly detailed structures that are beyond the reach of traditional lithography methods. However, challenges remain. One key area of concern is maintaining mechanical stability when fabricating complex three-dimensional polymer networks using ultrafast laser pulses.
While there are roadblocks, LDW's potential for transforming advanced manufacturing, especially for creating high-precision laser projection gratings, is evident. Ongoing research and innovation should continue to refine this technology and overcome its limitations, which should lead to broader applications in the near future.
Laser direct writing (LDW) has emerged as a versatile fabrication technique, finding applications in areas like micro-electromechanical systems and photomask production due to its maskless nature, efficiency, and cost-effectiveness. Recent innovations have extended its capabilities, particularly in the creation of intricate 3D structures and high-aspect-ratio features on flexible substrates. This advancement pushes the boundaries of what's possible in 3D printing technologies, which are becoming increasingly important across numerous industries.
LDW relies on the interaction of laser beams with specific materials, and its implementation spans a range of settings, from micromachining to lithographic methods. The use of high-efficiency, low-intensity femtosecond lasers is crucial for crafting detailed metallic patterns on transparent materials. This capability is critical in addressing the performance limitations often seen in electronic and optical components.
One particularly interesting facet of LDW is its ability to produce intricate freeform patterns with high precision. This contrasts with conventional methods like interference and mask-based lithography that rely on regularly arranged patterns. While it shows promise for creating complex optical gratings, challenges remain regarding mechanical stability, especially when using ultrashort laser pulses to generate complex 3D polymer networks.
The underlying principles of two-photon absorption (TPA) and its application in two-photon polymerization (TPP) have been instrumental in furthering LDW. This concept, first theorized in 1965, has led to two-photon polymerization-based direct laser writing (TPI-DLW). In TPI-DLW, two-photon initiators (TPIs) are used to boost polymerization rates in photoresists. This ultimately influences the printing process's efficiency and resolution.
The field continues to evolve rapidly, with recent developments highlighting high-speed and holographic two-photon direct laser writing techniques. This trend toward faster, more precise methods broadens LDW's potential in nanotechnology and other advanced manufacturing applications. The use of polarization techniques, such as elliptical polarization, shows a possible path for improving write speed in multi-channel parallel laser writing. This kind of optimization can unlock greater flexibility and efficiency in LDW processes, potentially leading to even more innovative applications in the future. However, we are still quite far from understanding all the intricacies involved, particularly the interactions between the laser and the materials. Further exploration is needed to address any potential limitations in scaling these techniques for larger-scale manufacturing applications. The question of repeatability and long-term stability remains a critical area to be investigated more thoroughly. Nonetheless, these advancements demonstrate a significant step toward realizing even more complex and highly precise structures using LDW.
Advanced Manufacturing Techniques for High-Precision Laser Projection Gratings From Diamond-Point Burnishing to Modern Nanotechnology - High Power Ultrasonic Planing Creates Blazed Gratings at 101k Times Regular Speed
High-power ultrasonic planing has revolutionized the creation of blazed gratings, dramatically increasing production speeds. This innovative approach, known as ultrasonic-assisted ultraprecision planing (UAUP), leverages a round-nosed diamond tool vibrating in an elliptical pattern to achieve both high precision and remarkable efficiency. The result is a fabrication process that is a staggering 101,000 times faster than traditional methods.
Blazed gratings are essential components in modern optical engineering, primarily used for manipulating light through diffraction. Their widespread use in various fields emphasizes the importance of efficient and precise manufacturing processes. This new ultrasonic technique shows promise in overcoming the limitations of older methods like lithography or mechanical ruling, which often struggle with speed or precision. It's a clear example of how advanced manufacturing technologies can significantly impact industries reliant on high-performance optical components. While this technique is promising, it remains to be seen how it will scale for mass production and what the long-term stability of the produced gratings will be.
Ultrasonic planing, operating at high power and frequencies above 20 kHz, presents a compelling approach to accelerating the creation of blazed gratings. This technique, often referred to as ultrasonic-assisted ultraprecision planing (UAUP), employs a diamond tool that vibrates in an elliptical pattern, resulting in fabrication speeds that are remarkably faster – up to 101,000 times quicker than conventional methods. This remarkable speed gain is attributed to the use of ultrasonic vibrations to generate acoustic cavitation in the cutting fluid, which then enhances material removal rates. The implosions of these tiny bubbles can be quite forceful, effectively helping to create the fine surface features needed in specialized optical applications.
The quality of the surface produced is noteworthy. Ultrasonic planing excels at generating incredibly smooth surfaces, often with roughness values in the nanometer range. This characteristic is critical for components like blazed gratings used in optics, where even minuscule surface imperfections can dramatically affect performance.
Further, this method's ability to process difficult-to-machine materials, like certain ceramics and composites, which are increasingly used in advanced applications, is a significant benefit. It broadens the material options for producing these specialized optical components and allows for a wider range of engineering possibilities. Moreover, the technique is energy-efficient, needing less power compared to traditional methods due to the high-frequency vibrations. This attribute makes it attractive for high-volume manufacturing environments.
Another advantage lies in the reduction of tool wear. Since ultrasonic planing is a non-contact method, wear on the cutting tool is minimized compared to conventional machining, which results in extended tool life and better process consistency. This aspect is especially crucial when working with demanding high-precision tasks. The machining parameters, including vibration amplitude, frequency, and feed rates, can be finely tuned for specific materials and desired results. This level of customization is essential for crafting optical components with unique surface properties.
Beyond the mechanical aspects, ultrasonic vibrations seem to influence the material's physical properties during the machining process. The acoustic energy can help create better surface integrity, which helps maintain the dimensional accuracy of the component, potentially without the thermal distortions typical in conventional machining. This capability contributes to more precise and controlled surface modification.
The impressive speed of ultrasonic planing is a significant factor for manufacturing workflows. It provides opportunities to transition from traditional batch-oriented production toward more continuous-flow systems. This shift is particularly relevant in industries where rapid turnaround times are vital, such as aerospace and telecommunications. However, challenges remain in fully integrating ultrasonic systems into established manufacturing processes. Further advancements in transducer technologies are essential to optimize the integration of ultrasonic machining tools into traditional setups, thereby maximizing the efficiency and benefits in actual production environments.
Advanced Manufacturing Techniques for High-Precision Laser Projection Gratings From Diamond-Point Burnishing to Modern Nanotechnology - Grayscale Lithography Enables Mass Production of Large Format Optical Gratings
Grayscale lithography presents a significant advancement in the production of large-format optical gratings, which are vital for a range of high-precision optical systems. The technique leverages a specialized system that uses ultraviolet LEDs as the light source to effectively illuminate the substrate. This allows for the generation of complex microstructures featuring gradual transitions in surface features, enhancing their optical capabilities. A notable benefit of this method is its ability to fabricate structures with a thickness of up to 100 micrometers, achieved with remarkable precision.
The approach utilizes direct-writing techniques, granting significant flexibility in designing high-precision microstructures. This is especially beneficial in creating optical components for non-flat surfaces. Further advancements, like two-photon grayscale lithography, expand design possibilities even more. While this method shows great potential for increased efficiency in grating production, challenges exist in seamlessly translating the current success of producing prototypes to mass manufacturing. The ability to consistently maintain the quality of the gratings at high volumes remains an area needing further attention.
Grayscale lithography presents a compelling approach for mass-producing large-format optical gratings with impressive precision. The HighFive C system, for instance, employs a 2-watt UV LED light source, and sophisticated optics adapt the illumination profile to generate the needed patterns on microdisplays. This method stands out because it allows for the creation of gradual surface structures on substrates, achieving a remarkable range of up to 100 micrometers in depth variation. This capability for producing varying surface topographies within a single fabrication step is quite noteworthy when compared to traditional methods.
The flexibility offered by this lithography technique is substantial. Direct writing grayscale lithography allows us to create a wide variety of high-precision microstructures, including the possibility of generating patterns on non-flat surfaces, a challenging feat for some older technologies. An even more refined version, two-photon grayscale lithography (2GL), combines grayscale lithography with two-photon polymerization, potentially enhancing the precision and design flexibility even further. This hybrid technique opens up exciting possibilities, but it also brings its own set of challenges that need to be investigated.
Techniques like nanoimprint lithography can be used in tandem with grayscale lithography to effectively mass-produce microoptical elements based on molds created using the grayscale technique. This hybrid approach enables faster and cheaper manufacturing of micro-optic parts, potentially offering a more efficient route for producing many copies of a particular optical component.
Precise control over feature sizes remains critical for applications involving nanodevices used in fields like optoelectronics and plasmonics. Grayscale lithography, coupled with advanced 3D printing technologies, is showing the potential to create optical elements with multiple parameters – a considerable leap forward.
There are, however, some areas where grayscale lithography needs further development. One of the challenges is scaling up from prototypes to high-volume manufacturing, especially when it comes to advanced, wafer-level freeform microoptics. The process for transferring the desired pattern to the substrate in a repeatable, accurate way during high volume manufacturing requires careful attention. The ability to efficiently transition from prototype to manufacturing while maintaining the level of precision obtained in research settings remains an area where substantial progress is still needed. Overall, grayscale lithography appears to be a promising manufacturing technique for optical gratings, but continued research and development are needed to realize its full potential in diverse and demanding applications.
Advanced Manufacturing Techniques for High-Precision Laser Projection Gratings From Diamond-Point Burnishing to Modern Nanotechnology - Wet Etching Technology Reaches Silicon Grating Precision Below 2 Nanometers
Recent advancements in wet etching technology have allowed for the creation of silicon gratings with unprecedented precision, achieving feature sizes below 2 nanometers. This remarkable accuracy represents a significant step forward in manufacturing techniques, particularly for producing high-quality optical components. The ability to manipulate the etching process, specifically by adjusting the duration of etching, provides a level of control over the surface features of these silicon gratings. While the ability to achieve this fine level of precision is promising, there remain difficulties in consistently controlling the surface topography at such incredibly small scales. This precise control over the surface is essential for both laboratory research and for industrial-scale applications. The ability to create gratings at this level of precision speaks to the ongoing developments in manufacturing processes that seek to improve the capabilities and overall performance of optical elements in modern manufacturing.
Wet etching has achieved a remarkable level of precision, allowing for the creation of silicon gratings with features smaller than 2 nanometers. This is a significant leap forward, particularly considering the importance of nanometer-scale control in fields like nanophotonics and quantum computing where even slight variations can significantly impact performance. It's fascinating how the process parameters, such as etching time and chemical concentrations, can be finely tuned to manipulate the surface features of these gratings. This control over surface morphology is a major advantage, exceeding the capabilities of many traditional fabrication methods.
One intriguing aspect is the selective etching nature of this technology. It's able to target and remove specific materials based on their intrinsic properties, essentially allowing us to sculpt intricate 3D structures without relying on elaborate masking techniques commonly used in other processes. This opens up exciting possibilities for creating complex optical and microelectronic devices. It's crucial to remember that the effectiveness of wet etching is highly dependent on the fluid dynamics within the etching environment. Understanding these fluid flows is essential for achieving consistent etching rates and precise control over the resulting surface textures.
While promising, scaling wet etching to maintain this level of precision across larger areas remains a hurdle. It's a challenge to ensure consistent quality and uniformity when dealing with large substrates. Continuous monitoring and fine-tuning of the process are crucial to achieving consistent results in manufacturing settings. Moreover, we're still learning about the interaction of wet etching with different surface textures. This interaction can lead to interesting optical and mechanical properties, making it potentially useful for applications involving smart surfaces and light manipulation.
The ability to seamlessly integrate wet etching with other advanced manufacturing processes, such as deposition and lithography, is another strength. This integration allows us to build incredibly sophisticated multispectral optical components, combining the benefits of multiple manufacturing techniques to achieve superior results. Also, achieving anisotropic etching with wet etching is easier than some other methods, providing a better path to features with high aspect ratios. This is a crucial advantage for designing optical structures with specific light-bending properties.
Some recent applications involve chemically aggressive solutions that selectively etch certain materials, paving the way for clever solutions in substrate management and the creation of intricate geometries. This is still a relatively new field, and further investigation into the long-term effects and side-effects is warranted. Finally, the speed at which we can create prototypes and adjust designs through wet etching is noteworthy. This rapid prototyping capability accelerates the development cycle for new optical components, potentially speeding up technological progress by enabling faster refinement through testing and performance feedback.
While it has great potential, the future of wet etching at this extremely small scale remains to be seen. It's important to continue investigating this promising area and explore the ways in which we can overcome the challenges and capitalize on the incredible precision and versatility that wet etching offers.
More Posts from aistructuralreview.com: