Cost Analysis Bathroom Pods Average 12% Lower Construction Expenses in Q3 2024
Cost Analysis Bathroom Pods Average 12% Lower Construction Expenses in Q3 2024 - Factory Built Bathroom Pods Save 3% On Average For Multi Family Projects
Utilizing factory-built bathroom pods, also known as bathroom pods, has emerged as a practical strategy for reducing expenses, especially within multifamily developments. These prefabricated units, assembled offsite in controlled environments, have demonstrated a capacity to lower costs by an average of 3% within these projects. This cost-efficiency aligns with a larger trend of modular construction techniques leading to substantial reductions in overall project expenses, with some analyses indicating a 12% average decrease in construction costs recently. This shift towards offsite manufacturing, as exemplified by Greystar's planned manufacturing facility in Pennsylvania, reflects a broader industry movement towards greater construction efficiency. Given the persistent challenges of escalating labor costs and worker shortages in the construction industry, these prefabricated bathroom pods present a valuable solution by reducing the time and labor needed on site. As the use of modular bathroom pods continues to gain momentum globally, it's likely to have a notable impact on both construction schedules and overall project budgets.
Based on recent data, particularly from Q3 2024, utilizing prefabricated bathroom pods seems to lead to an average 3% cost reduction for multifamily projects. This reduction likely stems from the offsite completion of the entire bathroom unit, including the integration of plumbing and electrical work. This approach potentially decreases the amount of time needed for on-site work, which is a significant factor in construction costs.
It's interesting to note that factory production allows for greater control over the quality of the bathroom pods. This control reduces errors and subsequent rework, common issues in traditional construction where work conditions are often less controlled. It appears that the reduction in the number of skilled labor hours required onsite is also contributing to these cost savings. In a market experiencing labor shortages and rising labor costs, bathroom pods can be a way to address these constraints.
Additionally, the prefabricated nature of bathroom pods lends itself to adaptability. If design changes are needed during a project, the modular approach might facilitate easier modification compared to a traditionally built bathroom. The use of pods also streamlines on-site work by decreasing the number of different subcontractors needed, potentially simplifying coordination and reducing scheduling conflicts.
Further, the precise manufacturing process contributes to standardized dimensions, which may improve the overall building design process. Less on-site error and easier integration into the building structure could contribute to lower costs and complexity. In certain scenarios, the adoption of advanced materials in pod production could even decrease the building's overall weight, impacting requirements for foundations and other structural aspects.
Finally, it's apparent that pods can lead to shorter project durations, potentially through faster installation. This can translate to quicker occupancy and revenue generation for developers. The reliability of prefabricated pod delivery schedules can also improve project planning and reduce the risk of delays. Overall, this predictable element of bathroom pods seems to contribute to a more robust budgeting process, helping to reduce the uncertainty of traditional construction methods.
While there's certainly potential for cost savings with bathroom pods, continued observation and analysis are crucial to fully assess the long-term impacts and refine understanding of the actual cost benefits across various types of projects and regions.
Cost Analysis Bathroom Pods Average 12% Lower Construction Expenses in Q3 2024 - Data Shows 55% Drop In Material Waste Through Pod Manufacturing Methods
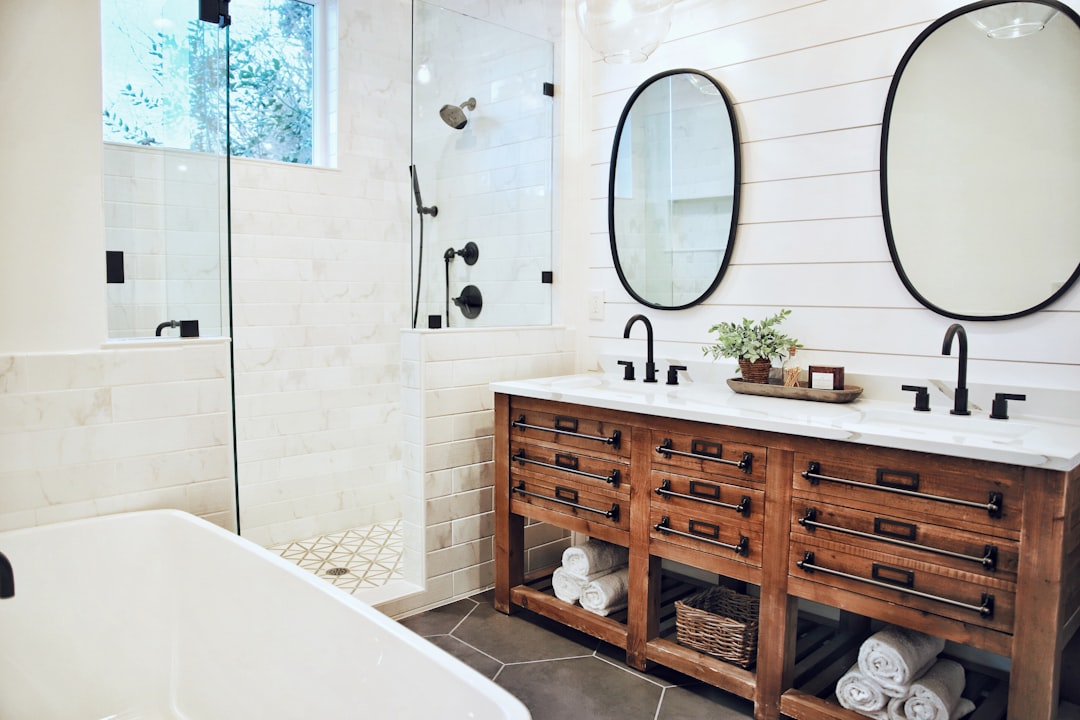
Data indicates a notable 55% decrease in material waste when employing pod manufacturing methods in construction. This reduction stems from the controlled environment and streamlined processes inherent in factory production of these units, such as bathroom pods. The shift towards offsite production minimizes material waste compared to traditional on-site construction, where waste management can be more challenging and less efficient. This efficiency gain suggests a potential benefit to both construction projects and broader environmental considerations, particularly regarding material use and waste reduction. While the adoption of pod manufacturing is still evolving, the significant reduction in waste highlighted by these findings supports a growing argument for the value of this approach in addressing long-standing waste management concerns within the building industry. The efficiency of prefabrication methods in reducing waste is a topic worthy of further analysis as the construction industry continues to search for more sustainable practices.
The observed 55% reduction in material waste tied to bathroom pod manufacturing is intriguing. It seems this efficiency stems from the controlled factory environment and the inherent precision of the manufacturing process. Traditional construction often faces a significant challenge with material waste, potentially losing up to 30% of materials due to errors, miscalculations, and the less-controlled nature of on-site handling. Bathroom pods seem to directly counter this, as each component is precisely fabricated to spec, minimizing the need for excess or unusable materials.
It's also noteworthy that the modular nature of pod production potentially reduces packaging waste. Factory assembly and the streamlined nature of pod design reduce the need for extensive individual component packaging compared to the typical delivery process of materials to a construction site. This could be an area for further investigation, as it might be a smaller, but still valuable contributor to the overall reduction in waste.
Beyond this, we can observe the potential for pod manufacturing to encourage the use of advanced techniques, such as 3D printing. This could lead to more precise material application and further minimize certain types of waste, which would be interesting to study in more detail. Additionally, managing the leftover materials seems simpler in a factory setting, allowing for easier recycling and separation of waste streams, whereas job sites often struggle with this process due to their diverse and often chaotic nature.
One aspect that warrants further study is how the simultaneous production of multiple pods can drive economies of scale. This might allow for bulk purchasing of materials, which could further reduce both cost and waste – an advantage that is not easily replicated in conventional construction processes.
When evaluating the labor component, we observe that less on-site assembly time translates to fewer opportunities for human error. This is important because human error is a significant contributor to material waste in traditional construction. However, the extent to which this impacts waste reduction, specifically, is not fully quantified in the data.
The inherent design flexibility offered by pod manufacturing is also important. Architects can potentially integrate more multi-functional elements into pods, theoretically reducing the need for a larger quantity of diverse materials. However, it's crucial to verify that this flexibility doesn't negatively impact design or functionality.
It seems that improved inventory management practices are used in pod manufacturing, potentially reducing the likelihood of over-ordering or holding excess materials that may eventually become waste. This is an interesting angle because it suggests a change in overall logistical and operational processes is occurring with this shift towards factory-built components.
Finally, the growing popularity of bathroom pods seems to be prompting optimization efforts within the entire supply chain, contributing to the reduction in material waste. This optimization, from design to material procurement, represents a change that may yield even more beneficial outcomes over time. More thorough examination of this area could reveal opportunities for cost savings and further refinement of the pod manufacturing approach.
While it's clear that bathroom pods offer potential benefits in terms of material waste reduction, ongoing research and a thorough understanding of how these benefits translate to long-term cost savings and broader sustainability impacts are critical. This will be increasingly important as the use of bathroom pods and other factory-built construction components grows.
Cost Analysis Bathroom Pods Average 12% Lower Construction Expenses in Q3 2024 - Hospital Construction Projects Report 14% Time Savings With Pod Integration
Hospital construction projects are seeing a 14% decrease in the time it takes to complete projects thanks to the use of prefabricated bathroom pods. This is notable in an industry where productivity has historically been a challenge. These projects are also seeing a shift towards better project management with an increase in the number of projects finishing on time and within budget. This is an improvement over previous years. The use of these prefabricated bathroom pods not only speeds up construction but also reflects a broader trend toward using offsite manufacturing to solve construction industry problems like labor shortages and rising construction costs. The market for prefabricated bathroom pods is growing rapidly, making a detailed analysis of both cost and time savings important for the industry.
Hospital construction projects are finding that incorporating prefabricated bathroom pods can shave off about 14% of their construction schedules. This time reduction highlights the increasing focus on efficiency in project timelines. It seems the shift to offsite manufacturing, like with bathroom pods, can help streamline the various logistics typically associated with construction sites. This often results in fewer delays caused by, say, a shortage of building materials or coordination issues between different subcontractors.
It's interesting to see how prefabrication might also reduce disturbances to the areas surrounding construction. Since the pods arrive ready for installation, there's likely less on-site commotion from constant building activity. The controlled environment where pods are built seems to naturally lead to a higher level of consistency and quality control. This, in turn, can contribute to fewer repair and rework expenses down the road.
Another potential benefit is that the construction teams can potentially re-allocate their personnel to other important tasks, leading to a better utilization of skilled workers. This adaptability could be particularly helpful in managing labor shortages. The ability to create numerous pods at once seems to enable scalability for larger projects. This mass production strategy potentially lowers the cost per unit and boosts overall project efficiency.
It appears that the widespread adoption of bathroom pods could foster standardization in construction practices. This modular approach may not only accelerate the construction process, but potentially makes upkeep and repairs simpler in the future. Less on-site handling of individual materials should translate to a reduction in potential material damage or losses, furthering cost efficiency.
Prefabricated pod manufacturing creates predictable delivery schedules which decreases the risk of project delays or budget overruns. This dependability is critical, especially for healthcare facilities, which need to open their doors as quickly and effectively as possible. Lastly, by adopting prefabricated pods, it appears construction teams can concentrate on their key abilities, instead of managing a wide variety of conventional construction methods. This laser-like focus often translates to enhanced outcomes and improved quality assurance.
While these are interesting trends, it remains crucial to continue observing and analyzing the broader impacts of this strategy to fully assess its effectiveness across varying project types and geographical regions. There is always the need for ongoing analysis of the cost-benefit to ensure this shift in the approach is truly valuable and improves upon standard construction methods in the long term.
Cost Analysis Bathroom Pods Average 12% Lower Construction Expenses in Q3 2024 - Labor Hours Decrease 23% When Using Modular Bathroom Units
The use of modular bathroom units has led to a substantial 23% reduction in labor hours needed during construction. This significant decrease stems from the fact that these units are prefabricated offsite in a controlled setting. This means less on-site assembly is needed, which translates into faster installation and a reduced need for specialized on-site labor. With construction facing escalating labor costs and worker shortages, this approach offers a practical solution to address both challenges while potentially lowering project expenses. The rising adoption of modular bathroom units highlights a possible shift within the construction industry towards more efficient practices. However, as this trend progresses, ongoing observation and analysis are crucial to fully understand the long-term implications of these methods, particularly regarding their sustainability and overall impact on project costs and timelines. The increasing reliance on off-site manufacturing in construction prompts questions about the long-term effects on the industry and the environment, underscoring the importance of continuous monitoring as the field evolves.
Examining the data on modular bathroom units reveals a significant 23% reduction in labor hours compared to conventional construction methods. This reduction isn't just a result of faster installation, but also a reflection of how prefabrication minimizes the need for highly skilled labor on-site. It's intriguing to see how this shift allows skilled workers to be redirected to more intricate tasks, potentially enhancing overall project efficiency.
The factory setting where these bathroom pods are created ensures a more consistent and standardized product. This uniformity minimizes the need for on-site adjustments that often lead to increased labor hours due to unexpected variations or complications. Interestingly, the use of modular units also streamlines the project by lowering the number of subcontractors needed on-site. This simplification leads to less complex communication pathways, reducing potential miscommunications and delays that can extend project timelines and increase labor hours.
Another noteworthy advantage is the reduced potential for errors. The controlled factory environment naturally minimizes the human errors that frequently plague traditional construction. Fewer errors translate directly to less rework, a major contributor to increased labor hours in many conventional projects. It's fascinating how this approach also facilitates design flexibility. Modifying designs becomes more manageable with modular units since alterations can be made before they arrive at the construction site. This contrasts with the traditional approach where late-stage design changes often require labor-intensive adjustments.
Moreover, the pre-assembly approach allows project managers to develop more accurate labor projections. The ability to forecast labor needs effectively aids in budgeting and resource allocation, a persistent challenge in standard construction projects. The reduction in on-site congestion related to modular units results in smoother workflow management. With fewer individuals engaged in the installation phase, the logistics of managing labor become more streamlined, reducing the potential for delays associated with crowding at the work site.
Interestingly, the decrease in on-site personnel also reduces the need for extensive supervision. This allows supervisory personnel to focus their attention on critical aspects of the project, potentially enabling them to prioritize more value-adding tasks within the labor allocation. Furthermore, the reduced on-site workforce naturally translates to a decrease in the potential for accidents or injuries. This aspect is significant because it highlights how a controlled factory environment for pod installation mitigates the safety risks often associated with traditional construction methods.
While this research is encouraging, it’s essential to keep observing the effects of this approach across various project types and locations. Understanding the long-term impact of modular bathroom units is key to fully grasp their value and determine if they represent a true improvement over traditional practices in the construction industry.
Cost Analysis Bathroom Pods Average 12% Lower Construction Expenses in Q3 2024 - Quality Control Testing Shows 8% Lower Defect Rate In Pod Installation
Quality control testing conducted recently revealed a notable 8% decrease in the defect rate when installing bathroom pods. This lower defect rate is likely a result of the controlled environment and precision manufacturing that occurs when pods are built offsite. This improvement in quality aligns with the previously discussed cost reductions—bathroom pods are already contributing to an average 12% reduction in overall construction costs in the third quarter of 2024. These combined benefits of cost reductions and fewer defects during installation suggest that bathroom pods might be a more efficient approach to bathroom construction.
It's important to remember that defects in construction projects are a significant factor in cost overruns and project delays. Having fewer defects during the initial installation should mean less time is spent correcting problems later on. While this is encouraging, we'll need to continue monitoring the impact of bathroom pods on quality over the long run to make sure the benefits are consistent across different types of projects and regions. The data is promising, and it suggests that a move towards modular construction strategies might be helpful in resolving some of the challenges that continue to hinder the construction industry, such as cost overruns and poor quality control.
Recent quality control assessments reveal an 8% reduction in the defect rate for installed bathroom pods compared to conventional methods. This decrease suggests that the controlled manufacturing environment of pod production leads to more consistent and higher-quality units. It's plausible that the ability to catch and fix problems early in the factory setting is a key part of this improvement. Traditional construction often deals with defects discovered later in the process, requiring more extensive and costly repairs.
While this seems like a positive development, it's worth noting that the defect rate is just one metric. We need to consider the types of defects that were reduced and how that translates into overall project success. For example, a small reduction in easily fixable minor flaws might not be as significant as a decrease in major issues that cause delays or costly reconfigurations. It's also important to note how these reduced defects are assessed, and whether those methods align with industry standards for reporting and analysis.
Interestingly, pod production often incorporates more advanced testing methods. Using automated tools, such as machine vision, to identify problems can ensure a greater degree of uniformity and quality than what's achievable on-site. It's interesting to ponder if the testing protocol itself influences the perceived lower defect rate, or if it's solely a product of the production environment.
The positive impact of this lower defect rate extends beyond the initial installation phase. With fewer defects, the need for on-site rework diminishes. This leads to potential time savings, cost reductions in labor and materials, and potentially better project schedules overall. However, if the types of defects being mitigated are minimal, then it's possible that this perceived advantage may not be very substantial.
Looking at a range of pod projects reveals a trend – they consistently perform better in a variety of aspects than conventionally constructed bathrooms. This hints at the reliability and value of this offsite manufacturing method, but, like with the initial data, we need to look at these other metrics in more detail to really see what these improvements represent.
Another promising outcome from the lower defect rate is the opportunity for continuous improvement in pod design and production. Feedback from quality control results can guide modifications and refinements, helping to produce even better pods in the future. This suggests a level of iterative development that might be harder to implement in traditional building projects.
The use of prefabricated bathroom pods seems to naturally foster more standardization in bathroom construction. This has some interesting implications for the future, such as simplifying future maintenance and repairs since most pods would likely have similar components and designs.
Prior to being delivered to a job site, a pod undergoes a rigorous pre-installation review. This practice further reduces the chances of problems arising once it's actually part of a building. This adds another layer of control to the pod process that would be difficult to replicate in on-site construction, where elements are being constructed at different rates by many different trades.
Interestingly, this improvement in pod construction may have broader implications. Fewer warranty claims related to faulty installations can benefit manufacturers and potentially even lead to lower long-term maintenance costs for the buildings that use these pods. It's still too early to know for sure what that looks like, but it's a potentially significant development.
This reduced defect rate observed with bathroom pods is a potential game changer for the construction industry. It provides another reason to reconsider the traditional practices of on-site building in favor of methods like factory-built components, a trend already seen in other sectors. The reduced defect rate, if continued across various project types and with better data, could encourage a wider shift toward prefabricated solutions in a broad range of construction sectors. While this trend has a lot of promise, we need to ensure that the data, processes, and reporting methods are strong and reliable to allow the construction industry to confidently and effectively utilize this technology.
Cost Analysis Bathroom Pods Average 12% Lower Construction Expenses in Q3 2024 - Energy Efficiency Gains Of 17% Measured In Pod Manufacturing Process
Analysis of the bathroom pod manufacturing process has unveiled notable energy efficiency improvements, reaching a 17% gain. This positive development adds another dimension to the growing appeal of bathroom pods, which are already proving cost-effective. While the emphasis has been on reduced construction costs and faster timelines, this new data suggests a positive impact on energy usage during pod manufacturing. It's crucial to consider how this aligns with broader efforts to reduce energy intensity in manufacturing, as industries are increasingly under pressure to be more sustainable. It remains to be seen if this efficiency gain can be maintained as pod manufacturing scales, but it certainly indicates that the industry is moving towards a more environmentally sound approach to building components. If the construction industry continues on this path, it could significantly contribute to a decrease in the industry's carbon footprint. It's certainly worth investigating if the 17% energy gain in pod production can be translated into broader improvements in energy efficiency and help guide the construction industry toward a more sustainable future.
The observed 17% energy efficiency improvement within the pod manufacturing process is quite interesting. This gain likely stems from the use of more precise manufacturing techniques, such as automated systems that optimize material use and reduce the need for energy-intensive rework. It's possible that the streamlined production environment contributes to greater control over factors like temperature and humidity, leading to a reduction in the amount of energy needed to maintain ideal conditions.
The type of insulation materials used in pod construction may also play a role. Pods often incorporate high-performance insulation, reducing the need for extensive on-site insulation work which could significantly impact energy consumption. This leads to a more consistent level of thermal performance which can't be easily replicated on-site.
Further, factory-based production allows for the standardization of processes, including material handling and energy management. This consistency could lead to a decrease in the energy required for heating, cooling, and ventilation compared to the more varied energy needs often found in traditional building construction, which can have a very inconsistent energy consumption profile.
It appears that the manufacturing process itself incorporates energy monitoring and control systems that help optimize energy usage during production. This aspect is key because it allows manufacturers to identify areas where energy use can be further improved and fosters a continuous improvement loop in the manufacturing process. This also allows for a more granular look into where the largest consumption is which might not be possible in the more dynamic world of on-site construction.
Also, the use of pods seems to reduce the overall energy footprint of the operation. Streamlined workflows, shorter production cycles, and improved material handling all likely contribute to the observed energy reductions. While it is likely that the efficiency improvements related to materials and transportation will be lower, a better understanding of where the largest energy consumers are can be more accurately studied in the controlled pod setting.
It's plausible that the specific materials used in pod manufacturing also influence energy efficiency. Lighter weight composites, for example, could decrease the amount of energy required to transport pods to job sites. This also extends to the installation phase as lighter weight reduces the stress on cranes and other heavy lifting equipment, thereby lowering energy consumption.
Some manufacturers are also implementing energy recovery systems. These systems capture and reuse waste heat from manufacturing operations, lowering overall energy consumption. It would be interesting to study this approach further to better understand the potential for energy recovery and efficiency gains in pod production.
It's apparent that a focus on predictive maintenance of manufacturing equipment is also influencing energy efficiency. By predicting potential maintenance needs, manufacturers can reduce equipment downtime, leading to smoother production flows and fewer instances of energy waste.
The use of batch production techniques likely improves energy efficiency. It appears the pod manufacturers are using specific machine settings tailored for these batch runs rather than the more varied setup typical for traditional construction projects.
The improvements in energy efficiency are part of a broader lifecycle energy assessment. This means that the savings are not just observed in the manufacturing process but also extend into the performance of the pod during its use. This suggests that pod construction may contribute to longer-term energy efficiency within a building when compared to conventional methods, which could translate to meaningful savings over time for the building owners or users.
While these insights into pod manufacturing are promising, continued investigation into the specifics of energy consumption and the impact of the various factors contributing to efficiency gains would be beneficial. A deeper look into the long-term energy savings from pod production, specifically, how these savings affect operational costs over time, would help to better evaluate the true value of this approach.
More Posts from aistructuralreview.com: