Door Hinges The Unseen Backbone of Structural Safety
Door Hinges The Unseen Backbone of Structural Safety - Hinge engineering More than just door movement
Forget simple pivots; hinge engineering is a sophisticated discipline, vital for structural safety and dependable operation across numerous settings. Far from just enabling basic movement, these mechanical elements are intricate assemblies that integrate principles from mechanics and materials science to provide precise control and robust support. They must function reliably under diverse stresses, securing everything from standard entry points and cabinet doors to industrial access panels or complex furniture applications. While often overlooked, the ongoing evolution of hinge design reflects continuous adaptation to modern architectural demands, sometimes balancing subtle appearance with the crucial task of acting as unseen guardians, ensuring structural stability and safety without drawing undue attention.
Delving into the mechanics of door hinges reveals complexities often overlooked. From an engineering standpoint, their function extends significantly beyond merely permitting rotation.
1. Achieving millions of reliable operational cycles in high-demand architectural settings isn't simply a matter of selecting common metals. It necessitates a deep understanding of material behavior under cyclic loading. The use of specific, sometimes proprietary, metal alloys like hardened steels or bronzes, often paired with sophisticated surface treatments or specialized lubricants, is critical to managing friction and wear. However, attributing boundless life solely to materials can be misleading; real-world factors like dust, moisture, or incorrect installation inevitably influence actual longevity, potentially falling short of theoretical laboratory test cycles.
2. Far from being passive pivots, hinges are integral components of the structural load path. They are tasked with constantly supporting the door's static mass, often a significant weight, while also absorbing and transferring dynamic forces. Think about the leverage applied by someone pushing against a large door, or the considerable pressure exerted by wind during a storm. These forces are concentrated and channeled directly through the hinge connection points, into the door frame, and ideally, reliably anchored into the surrounding wall structure. Failure here isn't just inconvenient; it can compromise the door's fundamental purpose.
3. The subtle features of hinge design, particularly the geometry of the knuckles and the precision with which they are manufactured, play a disproportionate role in performance. Minute variations in manufacturing tolerances, sometimes critical down to microscopic scales, directly influence how smoothly the hinge operates throughout its swing arc. Furthermore, this precision is crucial for ensuring the door sits correctly within the frame when closed. This alignment, facilitated by the hinge assembly, is surprisingly impactful on aspects like maintaining thermal insulation seals and, notably, contributing to the overall soundproofing capability of the door assembly.
4. When hinges are specified for fire-rated doors, their engineering requirements shift from mere movement to critical containment. These components must not only permit controlled opening but, more importantly, must maintain structural integrity for a specified duration when subjected to the extreme temperatures of a fire. This demands specialized materials designed to resist rapid loss of strength or deformation under intense heat, and validated through rigorous, standardized thermal testing regimes. The challenge is ensuring the hinge holds the door in place, preserving the fire barrier even as temperatures soar.
5. The decision regarding the number and positioning of hinges on a door is a calculated engineering problem, not an aesthetic choice. Incorrectly placing hinges or using an insufficient quantity for the door's size, mass, and anticipated usage subjects the door and frame to excessive bending moments and shear forces. Over time, this inevitably leads to visible and functional issues such as sagging, binding, difficulties in latching, and premature failure of fasteners or the door/frame material itself. A proper distribution of support is essential for long-term function and preserving the integrity of the entire door system.
Door Hinges The Unseen Backbone of Structural Safety - When the structural backbone falters hinge failures
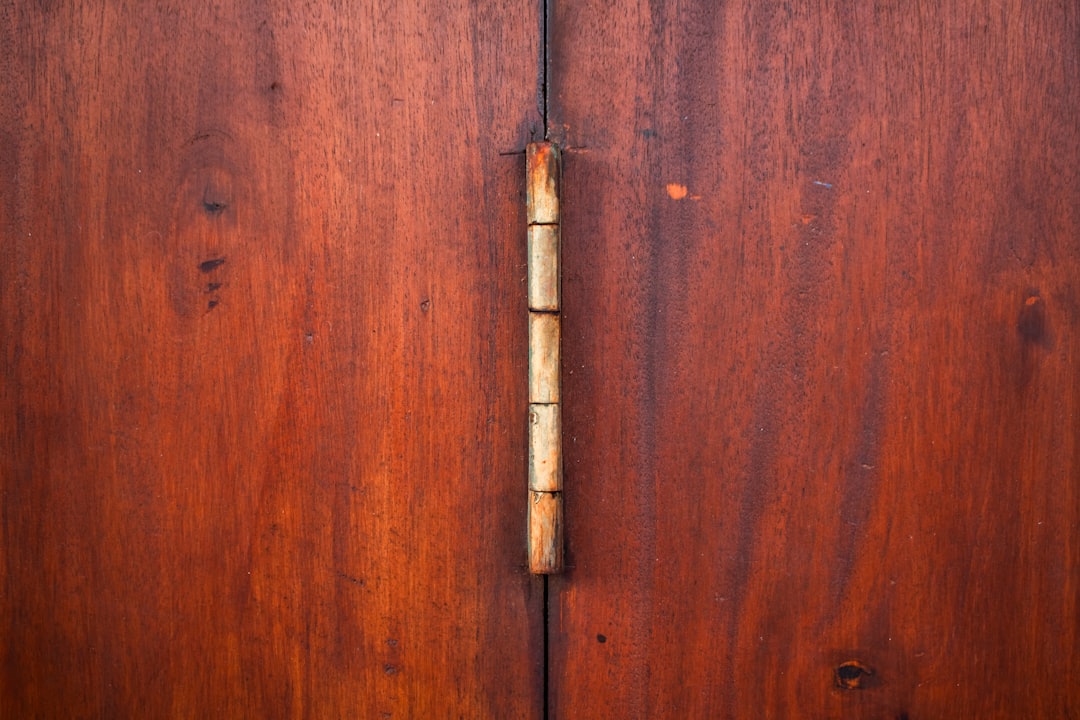
When the door system, acting as an element within the larger structure, experiences a hinge failure, the repercussions can be severe and frequently go unnoticed until a critical point is reached. Such a failure isn't merely about a door not moving correctly; it can initiate a chain reaction impacting the entire assembly's integrity, posing risks that extend to safety and potentially contributing to broader structural instability. The culprits behind these failures are often mundane but destructive: degradation from environmental factors like corrosion, cumulative wear and tear over time, and issues stemming from initial improper installation practices. These seemingly minor points can significantly worsen the probability of failure, leading to considerable hazards. Recognizing and addressing the vulnerabilities inherent in hinge components and their upkeep is crucial to protecting structural reliability and avoiding serious incidents.
Considering how critical hinges are to the functionality and safety role of a door assembly, it's worth examining the ways they can actually fail, often in less obvious ways than simple fatigue.
First, an often-underestimated failure mechanism involves internal components locking up. This 'galling' phenomenon, stemming from inadequate boundary lubrication or unfortunate material pairings, creates severe adhesive wear. Rather than permitting smooth rotation, the hinge essentially welds itself shut internally, instantly transforming the designed dynamic pivot into a rigid connection. This sudden rigidity introduces unintended and detrimental static loads onto the surrounding door and frame structure, forcing them to absorb stresses they weren't designed for.
Second, beyond the mechanical stresses, corrosive external environments pose a significant, often unseen, threat. Prolonged exposure to airborne chemicals, road salt aerosols, or even industrial byproducts can initiate processes like galvanic corrosion or pitting. This systematically degrades the hinge's material integrity, reducing cross-sectional strength from the exterior inward. What appears outwardly as minor surface discoloration or rust could mask a critical loss of structural capacity, leading to abrupt failure under loads that a healthy hinge would easily manage.
Third, significant dynamic loading events, such as a forceful swing abruptly stopped or a sharp impact, can critically damage the hinge's central pivot element – the pin. Housed deep within the knuckles and often concealed, this pin can shear or undergo plastic deformation. While the outer leaves might show little immediate distress, this internal compromise means the hinge loses its designed pivotal integrity and, crucially, its load-carrying continuity through the axis. The hinge is effectively failed functionally and structurally at its core, long before external warning signs appear.
Fourth, the interdependency of hinges in a multi-hinge configuration means the failure of a single unit is rarely an isolated event. When one hinge yields, the static and dynamic forces it was supporting are immediately redistributed, drastically increasing the load borne by the remaining hinges and the door frame. This abrupt overloading can precipitate secondary failures – perhaps overwhelming the shear capacity of neighboring pins, causing fastener pull-out from the frame or wall, or inducing localized yielding or fracture in the door frame material itself. A single component failure can thus trigger a rapid and widespread compromise of the entire door assembly's structural attachment.
Finally, while many engineering components are designed with ductility to deform plastically before failure, certain hinge materials or designs subjected to high-energy impacts or abrupt, forceful loading events can experience brittle fracture. Unlike a gradual yielding or wear, this involves a rapid crack propagation through the material, resulting in a sudden, catastrophic separation of hinge elements like leaves or knuckles, often with little to no prior visible deformation. This mode of failure presents a distinct challenge compared to fatigue or wear, as it offers minimal warning before complete loss of function.
Door Hinges The Unseen Backbone of Structural Safety - The hinge in plain sight Often ignored until it fails
Door hinges, though fundamental to the operation of every entryway, possess a remarkable capacity to blend into the background of our awareness. They are critical components, constantly performing their duty, yet they are routinely ignored until their function degrades to a point of undeniable failure. Problems that manifest in plain sight – a slight squeak signaling lubrication needs, minor stiffness indicating accumulating grime or early corrosion, or slightly loose fasteners that permit minute shifts – are frequently perceived as trivial inconveniences, not precursors to a potential breakdown. This pervasive neglect of simple, visible indicators allows underlying issues like cumulative wear and environmental degradation to advance unchecked. It's this sustained lack of attention to routine stresses and obvious symptoms that inevitably leads to a hinge reaching its critical point. When that happens, the consequences move beyond a simple operational glitch; the door's stability is directly impacted, its ability to reliably secure an opening is compromised, and a small, overlooked component suddenly becomes a significant functional and potential safety liability within the structure it serves.
Beyond the dramatic failures, a closer look reveals a spectrum of less obvious ways hinge issues can silently compromise performance and safety.
It's often missed, but subtle wear leading to minimal door sag can create persistent gaps between the door edge and frame seals. This seemingly minor issue directly undermines the intended acoustic isolation and thermal efficiency of the assembly, long before structural instability becomes evident.
A hinge assembly that has lost its precise geometric integrity doesn't just affect swing; it permits the door leaf to 'rack' under lateral load. This distortion compromises the critical alignment needed for locks and latches to engage properly with the strike plate, potentially allowing forceful entry points to fail even if the lock mechanism itself remains intact.
Consider the less obvious cyclic stresses imparted by routine environmental shifts. Diurnal and seasonal temperature fluctuations cause slight expansion and contraction in the door, frame, and surrounding structure. These minute, repetitive movements translate into subtle, persistent fatigue loading on hinge fasteners and the localized materials they anchor into, gradually degrading the connection strength over years.
The structural efficacy of a hinge connection is fundamentally limited by the integrity of the material it's attached to – be it the door core or the frame jamb. Degradation of these supporting elements, perhaps due to moisture ingress causing material softening, or long-term vibrational loosening of fasteners, can render a perfectly functional hinge ineffective by failing the crucial anchor points, often unseen within the material itself.
On systems employing concealed pivots instead of visible knuckle hinges, critical wear frequently accumulates at the buried upper or lower bearing surfaces. Unlike external hinges, this internal degradation isn't readily inspectable, and its primary symptom is often a gradual downward shift or lateral binding of the door leaf, indicating significant component wear long before external signs are apparent or total separation occurs.
Door Hinges The Unseen Backbone of Structural Safety - Selecting the right hinge for specific applications and loads
Selecting the appropriate hinge for a given application and its imposed loads is a fundamental decision for ensuring dependable function and, critically, maintaining safety. The weight of the element being hinged, often a door, stands out as perhaps the most significant factor; load capacity ratings are published for hinge types, and choosing a hinge with a rating that comfortably exceeds the expected maximum load is a basic requirement for both long-term performance and safeguarding against premature failure under stress. Consideration must also be given to the anticipated traffic or usage frequency; higher-traffic environments necessitate hinges designed and rated for such demands, potentially involving adherence to established grading standards like those indicating suitability for severe duty. The material composition and even its specific thickness – or gauge – are crucial, influencing resistance to wear, corrosion, and deformation under load, particularly in challenging environments. Beyond just opening, the required range of motion, perhaps needing a full 180-degree swing or restricted movement, dictates specific hinge geometries. For applications where maintaining fire integrity is paramount, selecting hinges certified to relevant fire safety standards is non-negotiable, rather than assuming any heavy-duty option will suffice. Ultimately, an inadequate selection based on any of these interconnected factors risks compromising the door assembly's reliability as a structural component.
Beyond merely enabling movement, selecting the appropriate hinge involves a careful technical evaluation based on the specific demands of the application and the anticipated loads. It's less about a generic catalogue pick and more about matching engineered function to required performance.
A continuous hinge, often chosen for its clean visual line, is functionally selected because it fundamentally shifts the load distribution mechanism. Instead of concentrating the static door weight and dynamic forces onto a few hinge points, it distributes the load along the entire vertical edge of the door. This isn't just about aesthetics; it's a critical engineering strategy particularly for mitigating stress on substrates that might be less robust, like particleboard cores or lighter metal frames, helping prevent localized deformation or long-term door warping under continuous load.
For door systems experiencing significant mass or subjected to frequent, demanding operational cycles, incorporating specialized bearing elements within the hinge structure – such as precision ball bearings, roller bearings, or advanced low-friction polymer bushings – moves beyond standard practice into a necessary engineering choice. These components are specifically selected to manage and significantly reduce friction and localized wear at the critical pivot point, thereby ensuring reliable, smooth operation and extended service life under stresses that would quickly lead to failure in simpler metal-on-metal pin designs. There's a cost and manufacturing complexity trade-off, of course, inherent in such designs.
When the application imposes non-standard functional requirements like security or the need to eliminate ligature points (anti-ligature design), hinge selection becomes an exercise in specialized geometric engineering. The design must achieve features like tamper resistance or the removal of protrusions, often through intricate forming and sculpting of the hinge components. The challenge is ensuring that these necessary security or safety geometries do not compromise the hinge's primary structural role or its required load capacity under potentially abusive forces.
For designers prioritising minimal visual impact, advanced concealed hinges are specified. These are far from simple pivots; they frequently employ complex internal multi-axis linkages and fold-away mechanisms. Selecting such a hinge demands confidence that its hidden, intricate design can nonetheless manage substantial door weights and absorb operational forces through its internal load paths. It highlights how aesthetic priorities directly influence the underlying mechanical complexity, and perhaps warrants consideration regarding future accessibility for inspection or maintenance of those hidden components.
Finally, the physical dimensions of a hinge's leaves – specifically their width ('spread') and material thickness ('gauge') – aren't arbitrary sizes but engineered parameters. These leaves function as miniature structural beams, transmitting forces from the door edge into the frame. Selecting wider and/or thicker leaves is a deliberate technical decision to increase the hinge's overall stiffness, enhance its leverage capacity, and improve its ability to resist bending moments and shear forces, which is particularly crucial when dealing with heavier doors or specific installation types like surface mounting where the leaves are the primary load-bearing element connecting to the substrate.
Door Hinges The Unseen Backbone of Structural Safety - Material developments influencing hinge performance
Advancements in the science of materials are continuously reshaping the design and performance limits of door hinges. While robust stalwarts like stainless steel and brass still hold significant places, newer generations of high-performance alloys and engineered composites are increasingly being incorporated. These materials aren't just alternatives; they offer distinct property profiles aimed at specific challenges. Beyond sheer tensile strength – a fundamental requirement – material selection now critically influences resistance to the relentless grind of wear, the insidious creep of corrosion in varied environments, and even the crucial parameter of frictional behavior that dictates smooth, predictable motion over time. This evolution underscores a shift from merely using available metals to strategically employing materials tailored for the stresses and demands a hinge will face throughout its operational life. The push isn't just for reliability, but to extend lifespan and maintain performance under conditions traditional materials might struggle with. However, despite these material leaps, relying solely on the material properties without meticulous consideration of the specific application and potential environmental factors remains a pathway to potential issues and reduced longevity.
Some advanced hinges now incorporate materials designed to self-lubricate over their operational life. This might involve specialized polymer composites or porous metal matrices engineered to release lubricants gradually, aiming to reduce reliance on external maintenance and mitigate wear at crucial pivot points through inherently low friction properties. However, ensuring consistent lubricant release and effectiveness across varied environmental conditions and load profiles presents an ongoing engineering challenge.
Cutting-edge approaches in hinge manufacturing often involve surface engineering techniques applied at a microscopic level, such as various forms of chemical vapor deposition (CVD) or physical vapor deposition (PVD), or thermal treatments like nitriding. The goal is to deposit or form ultra-hard, often ceramic or specific metallic compound layers on the hinge surfaces. These layers are intended to dramatically reduce surface friction and enhance corrosion resistance beyond what the base material alone can offer, which is particularly critical for components operating in challenging, abrasive, or chemically aggressive environments, though layer adhesion and resistance to impact can be concerns.
Additive manufacturing, commonly known as 3D printing, is starting to influence hinge component design by enabling complex internal geometries, such as lightweight lattice structures or variable density zones within a single part. This method allows engineers to potentially optimize material distribution precisely where needed for strength or specific functional characteristics in ways unachievable with traditional casting or machining. Yet, considerations around material property anisotropy in printed parts and consistency across production batches warrant careful evaluation for safety-critical applications.
Moving beyond traditional metals, high-performance door hinges are exploring the use of advanced structural polymers or fiber-reinforced composite materials for some primary load-bearing components. These non-metallic materials can offer inherent resistance to certain corrosive agents and provide substantial weight reduction. Furthermore, their material properties can sometimes be tailored to influence vibration damping characteristics. The challenge lies in ensuring their long-term dimensional stability and load capacity under sustained stress or temperature extremes, areas where traditional metals have historically held a clear advantage.
Developing alloys specifically for high-performance hinges requires intricate metallurgical understanding to navigate the inherent trade-offs between desirable properties. For instance, achieving sufficient hardness to resist abrasive wear under cyclical movement must be balanced with the toughness needed to absorb energy from sudden impacts or prevent brittle fracture, particularly in critical elements like the hinge pin or knuckles. Engineering specific microstructures within the alloy, often through precise heat treatments, is key to this balance, demanding rigorous process control to consistently achieve the required performance blend.
More Posts from aistructuralreview.com: