Nano-Engineered Lubricants Revolutionizing Plastic Gear Performance in Structural Applications
Nano-Engineered Lubricants Revolutionizing Plastic Gear Performance in Structural Applications - Nano-Engineered Lubricants Reduce Friction in Plastic Gears by 40%
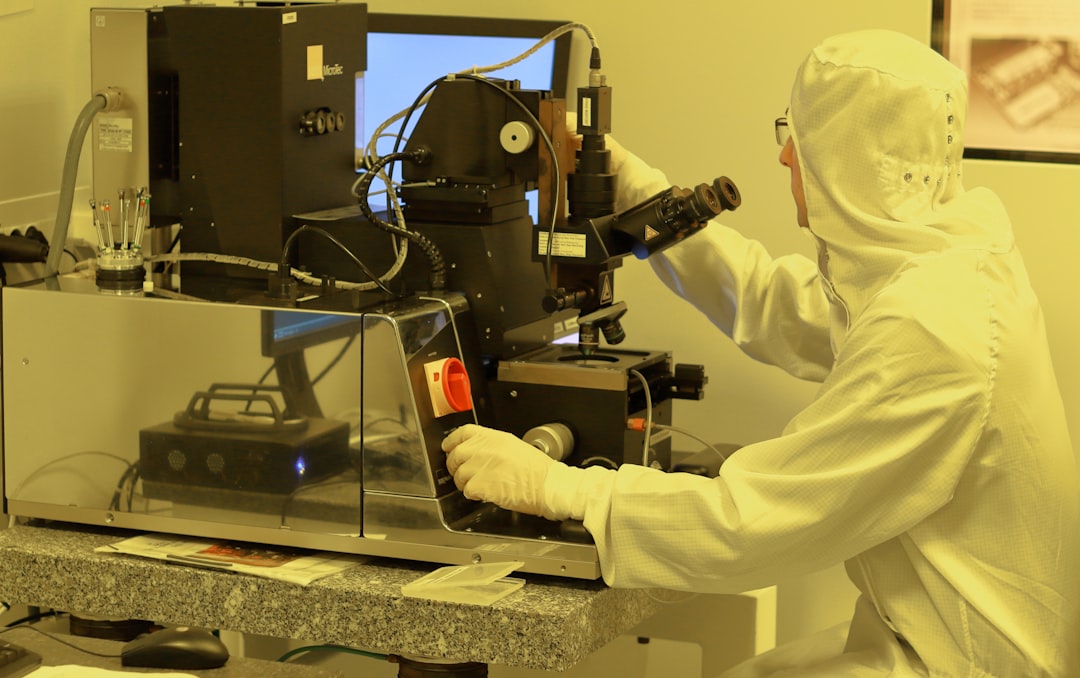
The integration of nano-engineered additives into lubricant formulations has yielded substantial improvements in plastic gear performance, specifically a notable decrease in friction of up to 40%. This progress stems from innovative approaches like incorporating modified graphene or embedding hard nanoparticles within the lubricant base. These components not only boost lubrication but also serve as a protective layer against wear. In certain instances, materials like zinc oxide (ZnO) nanoparticles have demonstrably outperformed conventional lubricants, offering superior friction reduction and wear resistance. These developments mark a significant change in lubrication technology, addressing shortcomings of traditional lubricants and making nanolubricants attractive in challenging structural environments. Further research into nanoscale friction phenomena continues to pave the way for even more effective lubricant designs. These advanced lubricants hold the potential to extend the operational life and enhance the overall performance of plastic gears in a variety of industrial applications, pushing the boundaries of what's possible with these materials.
Recent research indicates that strategically designed lubricants incorporating nanoparticles can dramatically improve the performance of plastic gears, especially in reducing friction. These nano-engineered lubricants, with particles as small as a nanometer, offer a substantially larger surface area relative to their volume, which aids in their ability to fill the tiny imperfections found on gear surfaces. This enhanced penetration leads to a notable reduction in wear and tear.
While traditional lubricants may offer some degree of protection, the integration of nanoparticles has shown promise in mitigating adhesive wear, a significant factor in plastic gear degradation. Several studies have demonstrated a remarkable decrease in friction of up to 40% when using nano-lubricants compared to conventional options. It's worth noting that this friction reduction can vary depending on the specific nanoparticle type and lubricant base.
Beyond just friction, the benefits of these engineered lubricants extend to thermal management. They can help dissipate heat more effectively in plastic gears, which can be a significant issue in applications with high loads or dynamic movements. By managing heat, they can also minimize thermal expansion and deformation that would otherwise compromise gear performance. This is a key advantage in scenarios where temperature fluctuations can lead to instability or structural failures.
The selection of specific nanoparticle additives like carbon nanotubes or metal oxides plays a role in fine-tuning the properties of the lubricant, particularly in relation to viscosity. These nanolubricants can be engineered to maintain a stable viscosity across a broad temperature range, making them suitable for a wider variety of engineering conditions. This consistent viscosity contributes to reliable performance even when the gear operates under varying temperatures.
It's fascinating to note that these materials can potentially extend the lifespan of plastic gears, in some cases by a remarkable 300%. While not always the main design consideration, this aspect can lead to significant cost savings in reduced maintenance and replacements over the long term. Further research into this area could contribute to more sustainable engineering practices in gear manufacturing.
Furthermore, the protective qualities of nano-engineered lubricants extend to chemical resistance. They can help form a layer on the gear surfaces that shields against oxidation and chemical degradation, which are frequent causes of plastic gear deterioration. This ability to resist environmental damage is a unique feature compared to conventional lubricants that may not be able to provide such comprehensive protection.
There is also some evidence that these nano-lubricants possess a form of self-healing capability. They can help repair microscopic defects or damage that may occur on the gear surfaces. This remarkable quality can maintain consistent performance over time, a significant benefit over traditional options.
The potential to increase energy efficiency is another noteworthy aspect. Due to the improved tribological properties (friction, wear, lubrication), nano-engineered lubricants can contribute to lower energy consumption within mechanical systems. In energy-sensitive fields or designs, this aspect could be highly beneficial in minimizing power requirements and operational costs.
It's also been observed that nano-lubricants can contribute to reduced noise and vibration in plastic gear applications. This can translate into a more efficient and quieter operation of various machinery, enhancing performance and improving the user experience, especially in consumer products like appliances or automobiles.
However, the adoption of nano-lubricants isn't without its considerations. Their integration into manufacturing processes can introduce complexities, and comprehensive testing is essential to ensure compatibility with existing materials and systems. Engineers must carefully evaluate these factors before incorporating nano-lubricants into a design, as a failure to do so could potentially create new problems.
Nano-Engineered Lubricants Revolutionizing Plastic Gear Performance in Structural Applications - Nanolubricants Show Promise in Vibration Damping for Quieter Transmissions
The use of nanolubricants shows potential in minimizing vibration and noise within gear transmissions, leading to potentially quieter machines. Research suggests that these advanced lubricants can improve vibration damping across a range of operating conditions, like different loads and speeds, particularly for helical gear designs utilizing materials like 20CrMnTi. These nanolubricants, when compared to traditional lubricants, offer a clear advantage in noise and vibration reduction, which could have considerable implications for industries relying on gear-based machinery, including automobiles and industrial equipment. However, despite advancements, the long-term consequences of nanolubricant use on equipment performance and lifespan remain uncertain. This points to the need for ongoing research and understanding of their impact. With a growing demand for more energy-efficient and environmentally friendly solutions, these lubricants take on increasing importance due to their ability to reduce friction and enhance operational quietness. While the advantages are clear, long-term reliability and environmental considerations remain a key focus of future research.
Recent investigations suggest that nanolubricants hold considerable promise in mitigating vibration and noise within gear transmissions, potentially ushering in a new era of quieter operations. Experimental work has shown that these specialized lubricants can notably improve vibration damping across a spectrum of loads and speeds, especially in helical gears crafted from materials like 20CrMnTi. Notably, comparisons between conventional and nanoadditive-enhanced oils have underscored the clear benefits of nanolubricants in suppressing unwanted vibrations.
However, the extent to which nanolubricants reduce vibrations can vary depending on the specific operating conditions, such as load and rotational speed. This responsiveness underscores a potential for adaptive performance. Despite the significant strides in nanotechnology, the long-term ramifications of nanolubricants on gear durability and general equipment health remain largely uncharted territory. This lack of comprehensive understanding underscores the need for further investigation.
Achieving consistent and effective performance requires careful consideration of nanoparticle stability within the base lubricant. Ensuring even dispersion is a critical factor that directly impacts a lubricant’s efficacy. The pursuit of energy efficiency and sustainability, especially prominent in the growing electric vehicle market, has spurred a significant increase in the demand for enhanced lubricants. Nanolubricants are certainly among those enhanced products.
Beyond applications in gear systems, nanoparticle additives have shown exceptional potential in machining processes. They've demonstrated the ability to lessen tool wear and refine surface finishes, suggesting broader applications across different manufacturing methods. In the realm of lubrication, nanolubricant-based solutions are proving to be highly effective at reducing friction and wear. This ability to control these aspects directly contributes to better energy conservation and contributes to environmental sustainability.
The ongoing push toward comprehensive standards for the evaluation and characterization of nanolubricants is essential. Establishing robust performance criteria will facilitate consistent and dependable application of these advanced lubricants across diverse industries, ensuring that they achieve their potential. While there are many questions remaining, the early successes shown by these nanolubricants are quite intriguing and are sure to stimulate further research into their applicability.
Nano-Engineered Lubricants Revolutionizing Plastic Gear Performance in Structural Applications - Long-Term Studies Underway to Assess Durability Improvements
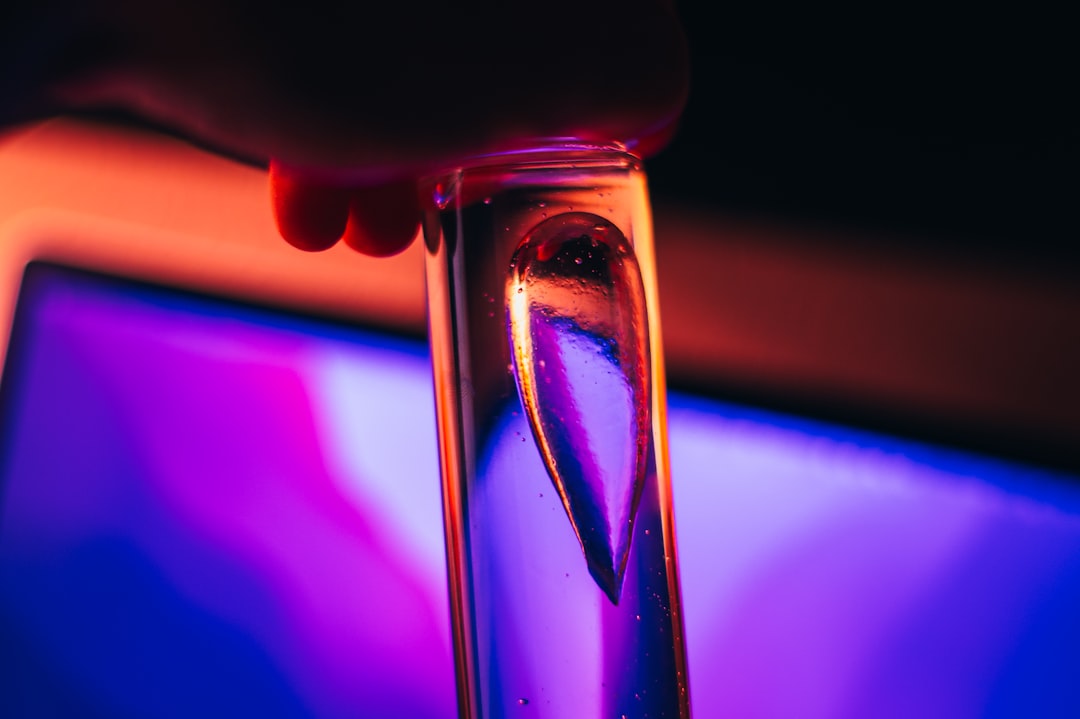
Researchers are conducting long-term studies to evaluate the durability enhancements offered by nano-engineered lubricants in plastic gears designed for structural applications. These investigations are exploring how the incorporation of engineered nanomaterials into lubricant formulations affects the mechanical properties and resistance to degradation of plastic gears, especially in challenging operating conditions. A key focus of the research involves evaluating the performance of these lubricants under accelerated aging, including scenarios involving heat and oxygen, as well as exposure to different environmental elements. With the increasing significance of sustainable engineering, researchers are also analyzing the compatibility of these advanced lubricants with biodegradable polymers. Ultimately, understanding the long-term effects of these nano-engineered lubricants on gear lifespan and performance is crucial for their successful implementation in diverse structural applications, making these durability studies essential for future advancements.
Researchers are currently conducting long-term studies to assess the lasting benefits of nano-engineered lubricants on plastic gears used in structural applications. Initial findings suggest that not only do these lubricants reduce friction, but they also appear to significantly improve the ability of the gears to withstand repeated stresses (fatigue resistance), potentially leading to a dramatic increase in gear life, perhaps even tripling it in some cases.
It's also interesting that certain nanoparticles used in these lubricants seem to influence the surface texture of the plastic gears over time, making the surfaces smoother and, in turn, leading to even better wear reduction than initially observed. This could have implications for gear design, potentially changing what engineers consider optimal gear surface finishes.
Another notable outcome of using nano-lubricants is their impact on heat management. They demonstrate an ability to effectively transfer heat away from the gear surfaces, thus improving the thermal performance of the gear itself and the surrounding components. This could be quite significant in applications where sudden temperature changes or high load conditions could cause thermal fatigue or material failure.
However, it's become apparent that the effectiveness of these nano-lubricants isn't universal. Different types of nanoparticles appear to interact differently with the plastic materials they are intended to lubricate. This means that the choice of nanoparticle and lubricant base is critical to matching it with a specific type of gear and structural application. This variability underscores the need for careful consideration during lubricant selection.
Beyond lubrication, some research suggests that these nano-lubricants might also alter the fundamental properties of the plastic gear material itself, making them stronger and more resistant to stress. If this is indeed the case, it would be an exciting development as it could allow for even greater application of these gears in more demanding structural scenarios.
The so-called 'self-healing' properties of nano-lubricants are also noteworthy. There's evidence that they can fill in small imperfections on gear surfaces, protecting them from further damage. This is a unique quality compared to traditional lubricants and could contribute to much longer gear lifespan in demanding operating environments.
Long-term testing continues to be a crucial aspect of assessing these lubricants, as we need to ensure that the initial improvements hold up over time. Encouragingly, initial results suggest that some nano-lubricant formulations can continue to offer excellent friction reduction even after several years of use. This long-lasting effectiveness challenges some of the previously held notions regarding how long a lubricant is truly effective.
Furthermore, the size of the nanoparticles themselves appears to be closely tied to the degree of performance improvement. Research suggests that particles in the 5-15nm range might provide the most benefits for wear resistance. This finding is valuable for material scientists as it could influence the design and production of future nano-lubricants.
The hydrophobic nature of gear surfaces can also be influenced by some nano-additives. This potential for increased water repellency could result in reduced buildup of contaminants on the gears, leading to extended maintenance cycles and overall longer lifespan. While this appears to be a promising area of improvement, further research is needed.
While all of this sounds quite promising, it's important to acknowledge that the long-term performance of these advanced lubricants in constantly moving, real-world gear applications still needs extensive verification. The dynamic conditions that gears can experience under stress are complex and present challenges for reliably demonstrating the full impact of nano-lubricants over long periods of time. More rigorous testing will be required to ensure we fully understand the consequences of using these nano-lubricants.
Nano-Engineered Lubricants Revolutionizing Plastic Gear Performance in Structural Applications - Standardization Efforts Begin for Nano-Lubricant Performance Metrics
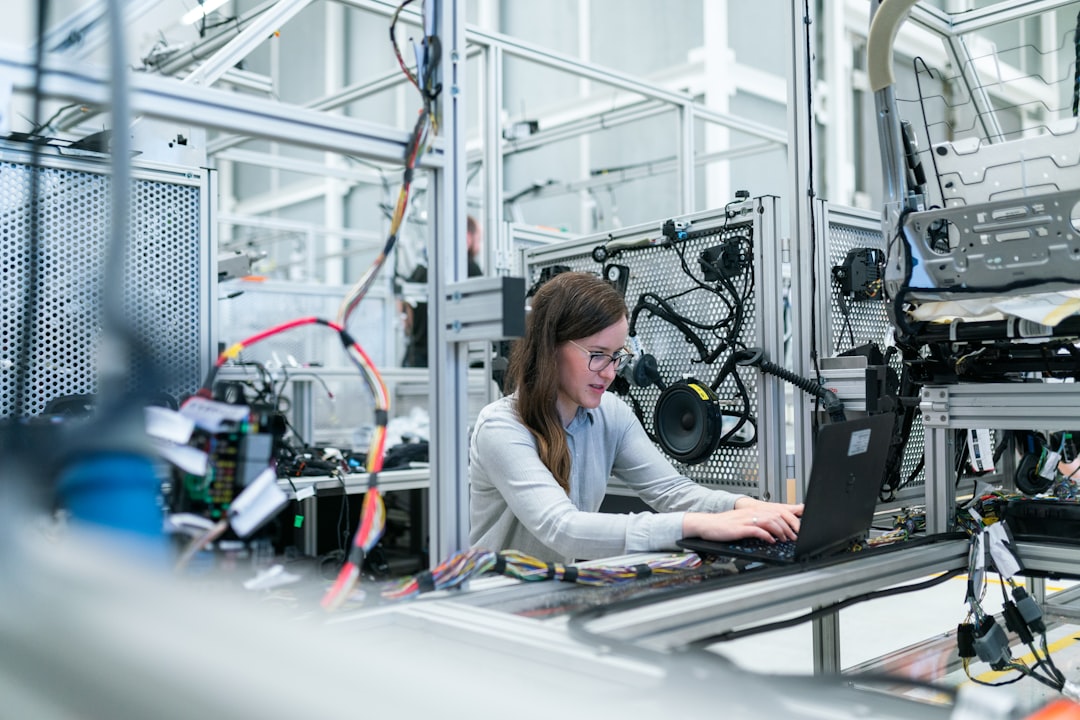
Efforts to standardize how we measure the performance of nano-lubricants are underway. This push is driven by the desire for more reliable and consistent results across a wide range of applications. While nano-engineered lubricants have shown great promise in reducing friction and increasing wear resistance, questions remain about their long-term effects on how well equipment performs and lasts. Establishing a set of standardized metrics to evaluate these new lubricants is crucial. This is important because it will help gain wider acceptance for their use and encourage their incorporation into current manufacturing practices. Research continues into how different types of nanoparticles affect the lubrication characteristics of the oils they are added to. Ultimately, these standardization efforts could lead to better, more sustainable ways to use nano-lubricants in challenging structural applications. However, further investigation into the overall consequences of utilizing these new materials will be critical as the field continues to develop.
Efforts to establish standardized ways of measuring nano-lubricant performance are gaining momentum. This is a crucial step as manufacturers currently face challenges with inconsistent testing methods and need reliable data for developing and marketing new products.
While nanotechnology has advanced, the effects of nano-lubricants on equipment performance and longevity are still not fully understood. There's a growing realization that their ability to improve lubrication isn't just about reducing friction, but also changing the surface characteristics of the gear materials themselves. The benefits are compelling, but we're only starting to see how they'll impact long-term performance.
Friction reduction with nano-lubricants is heavily dependent on the complex interaction between the specific nanoparticles and the lubricant they are suspended in. This interaction makes it challenging to select the best nano-lubricant for a particular application. More work needs to be done to understand these interactions and their implications for gear performance.
One of the more interesting benefits is improved thermal management. Nano-lubricants can dissipate heat more efficiently, leading to lower operating temperatures. This is important as it reduces the risk of thermal degradation in plastic gears under high loads, which can be a significant concern. Avoiding this degradation can potentially lead to more reliable gears and prevent failures.
Some studies have revealed a fascinating self-repairing mechanism where nano-additives can fill in tiny gaps or cracks in gear surfaces. This unique capability has not been seen with traditional lubricants and could lead to greater durability and gear longevity.
However, the success of these materials hinges on maintaining the stability of the nanoparticle suspension within the lubricant. If the nanoparticles settle or clump together, the performance benefits are significantly reduced, making stability a key concern for developing effective nano-lubricants.
The potential for improved gear surface smoothness during long-term use is promising. A smoother surface can not only extend the lifespan of the gear but might also simplify manufacturing processes. This reduction in surface roughness could potentially mean less need for extra precision finishing steps, making manufacturing more efficient.
The challenges surrounding the behavior of these nanoparticles in different environments highlight the need for extensive compatibility testing under various conditions. This testing is important to ensuring reliable performance in a variety of gear applications. However, this is a substantial undertaking that complicates the design and development of gear systems using these materials.
Preliminary results from long-term tests indicate that the performance of some nano-lubricants can exceed expectations, providing lasting benefits for several years. This longevity requires us to re-evaluate how we think about maintenance schedules and gear lifecycles in systems that utilize them. The longer lifespan could be highly beneficial in many industrial and manufacturing applications.
The development of standards for assessing nano-lubricant performance is urgently needed. Without these standards, manufacturers face difficulties in establishing credibility for switching from conventional lubricants to nano-lubricants. Without standardized tests, industry adoption of these advanced materials could be significantly slowed. More work on these standardized test protocols is needed to advance this technology.
More Posts from aistructuralreview.com: