Structural Engineering Marvel Sydney Harbour Bridge's 53,000-Tonne Steel Arch Design and Construction Analysis
Structural Engineering Marvel Sydney Harbour Bridge's 53,000-Tonne Steel Arch Design and Construction Analysis - Building The Coathanger From Both Ends 1923-1932 Complex Arch Assembly Analysis
The construction of the Sydney Harbour Bridge's arch, spanning from 1923 to 1932, exemplifies a complex feat of structural engineering. The innovative approach of building the arch from both sides simultaneously, culminating in a meeting at the apex, required remarkable planning and execution. The sheer scale of the project, involving the manipulation of 53,000 tonnes of steel, introduced a multitude of challenges, notably in maintaining accurate alignment and structural integrity during the assembly process. This dual-ended construction method serves as a testament to the ingenuity of the engineers involved and the importance of collaborative efforts in overcoming the immense logistical barriers to complete such a monumental project. The bridge's unique construction approach continues to fascinate structural engineers today, as it highlights the challenges of constructing large-scale structures with significant weight and height. The construction of the arch demonstrates the complexity of combining theory and practice, which played an integral role in the bridge’s successful completion.
The Sydney Harbour Bridge's construction, a project spanning from 1923 to 1932, showcases a fascinating approach to assembling the colossal 53,000-tonne steel arch. While the use of a significant quantity of steel was undoubtedly a key element, the decision to source almost 80% of it locally was a pragmatic move, mitigating transportation complexities and likely minimizing costs.
The graceful arch form was not solely an aesthetic choice but was carefully conceived to optimize weight distribution. Engineers cleverly leveraged this shape to use less material without sacrificing the structural strength essential for the bridge's purpose. The construction period was not without its challenges. Sydney's variable weather, with its bouts of harsh storms and rain, significantly impacted the construction timeline, prompting engineers to develop and apply robust construction methods.
One of the more intricate aspects of construction was the arch assembly itself. Engineers implemented innovative techniques, such as employing hydraulic jacks, to control the curvature of both halves of the arch simultaneously, guaranteeing a precise fit crucial for the overall stability of the bridge. This complex arch assembly was part of a larger design incorporating both cantilevering and arch support systems. This dual approach not only offered a visually impressive profile but enhanced the bridge's structural ability to withstand variable loads, like wind gusts and traffic flow.
Adding another layer of complexity, the engineers meticulously calculated the thermal expansion and contraction effects on the arch, crucial for preserving the arch's long-term integrity given Sydney's fluctuating temperatures. The idea of constructing the arch from both ends and joining them in the middle was, of course, ambitious. Maintaining the necessary millimeter precision throughout the construction phase required persistent monitoring and careful adjustments. While designed primarily for vehicles and pedestrians, the bridge's structural capacity was cleverly engineered to handle anticipated increases in traffic, anticipating future demands without extensive retrofits.
Furthermore, a unique system of bearings and expansion joints was integrated into the bridge's design to allow for movement and minimize stress on the arch, demonstrating the early 20th century's evolving understanding of structural engineering principles. It's also notable that, at its peak, the construction employed about 3,000 workers, many of whom had previously worked on other major infrastructure projects. This made the Sydney Harbour Bridge a focal point of highly skilled labor in the region and a testament to the capabilities of Australian engineering and construction during that era.
Structural Engineering Marvel Sydney Harbour Bridge's 53,000-Tonne Steel Arch Design and Construction Analysis - 39000 Tonnes Of Steel Six Million Hand Driven Rivets And Granite Pylons
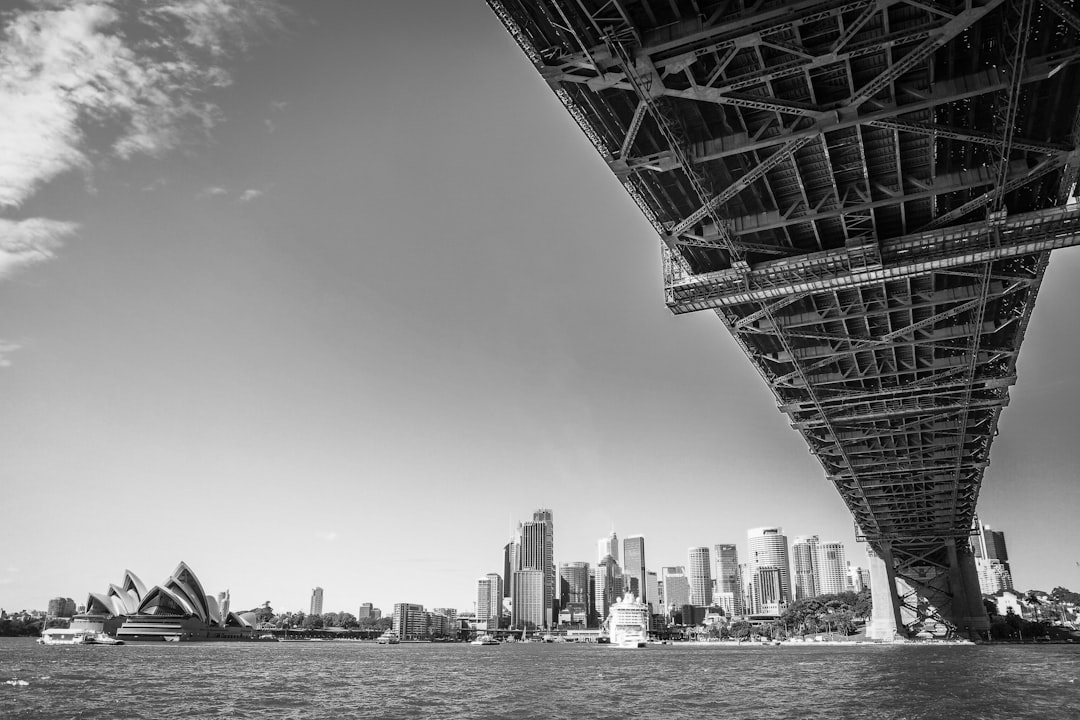
The Sydney Harbour Bridge stands as a testament to the engineering feats of the early 20th century, relying on an immense 39,000 tonnes of steel for its iconic arch alone. This colossal structure is held together by a staggering six million hand-driven rivets, a testament to the sheer labor and precision required during construction. The use of hand-driven rivets, while perhaps a less efficient method today, demonstrates the technology and methods available at the time, highlighting the remarkable dedication of the workforce, which at times involved approximately 1,400 workers. Further reinforcing its impressive structure are the granite-faced tower pylons, a design choice which contributed to the bridge's overall strength and aesthetic appeal. These pylons were the result of careful planning by consulting architects like Sir John Burnet and Partners, a reflection of the collaborative effort involved in realizing such a monumental undertaking. The combination of steel, rivets, and granite showcases the designers' ability to balance innovation with practicality, creating a structure that not only fulfilled its purpose but also served as an enduring symbol of engineering excellence. The Sydney Harbour Bridge's construction remains an awe-inspiring example of the engineering skill available at the time, highlighting the creative solutions devised to overcome the technical limitations of the era.
The sheer scale of the Sydney Harbour Bridge's construction is truly remarkable, evident in the staggering 39,000 tonnes of steel dedicated to forming the arch alone. It's a mind-boggling amount, perhaps easier to grasp by imagining it as the equivalent weight of hundreds of blue whales. This monumental quantity of steel was intricately joined together using a staggering six million hand-driven rivets. It's a testament to the dedication and skill of the workforce, each rivet playing a vital role in ensuring the structural integrity of the bridge's steel skeleton. The bridge's foundation rests upon granite pylons, impressive structures standing 89 meters high, fashioned from stone quarried locally at Mortar Creek. This decision to utilize local resources was likely influenced by a combination of factors, perhaps cost-effectiveness and the desire to promote local industry.
The 14,000 tonnes of steel, combined with the other components, represent the static load the bridge must support. This 'dead' weight, along with the dynamic forces created by moving vehicles and wind, were central considerations in the bridge's design. The elegant arch form itself wasn't just an aesthetic choice; its curvature significantly contributes to the bridge's inherent stiffness and resistance to lateral forces. The engineers were tasked with an extraordinarily demanding undertaking – constructing the arch from both sides, needing to align them with a remarkably precise tolerance of just 12 millimeters at the apex. This tight tolerance highlights the incredible precision that was achieved during the construction process. The innovative use of hydraulic jacks to control the arch's curvature in real time was a progressive engineering approach for the time. It provided a means to adapt and make fine adjustments while maintaining structural integrity throughout the arch assembly.
The bridge's design extends beyond merely handling the weight of current traffic; it was meticulously engineered to accommodate future expansions and upgrades. This is a notable example of foresight in structural design, a critical consideration for long-lasting infrastructure. The selection of materials, spanning from steel and rivets to granite, wasn't simply about brute strength. Consideration was given to how these materials would behave in Sydney's variable temperature conditions. It reflects an early, yet crucial, understanding of thermal dynamics and its impact on structural stability. The soaring granite pylons are not only integral to the bridge's structure but also contribute to its iconic, instantly recognizable silhouette. This speaks to the recognition that aesthetics play a significant role in major infrastructure projects, shaping public perception and becoming a symbol of cultural identity.
Structural Engineering Marvel Sydney Harbour Bridge's 53,000-Tonne Steel Arch Design and Construction Analysis - Testing The Bridge With Steam Locomotives And Military Tanks 1932
Prior to its grand opening in 1932, the Sydney Harbour Bridge underwent a series of intense trials to verify its structural strength. A significant part of this testing involved the use of heavy steam locomotives, totaling an impressive 7,000 tonnes. These locomotives were driven across the bridge, simulating the dynamic forces that regular vehicular traffic would exert on the structure. This approach served as a practical method of confirming the bridge's capacity to handle real-world loads and provided a critical validation of its design. Furthermore, military tanks were also employed during testing to subject the bridge to extreme stresses, exceeding what it was likely to experience in normal operation. This rigorous procedure not only highlighted the remarkable engineering achieved in the bridge's design but also underscored its vital function as a primary transportation link for a rapidly developing post-war Australia. The blend of thoughtful planning and intense testing in this final phase is a testament to the engineers' commitment to ensuring both the safety and long-term durability of this engineering marvel. This dedication, apparent in these 1932 tests, has ultimately contributed to the Sydney Harbour Bridge's enduring legacy as a symbol of robust design and construction.
The Sydney Harbour Bridge's opening in 1932 was preceded by a crucial phase of testing using steam locomotives and military tanks. This practical approach aimed to demonstrate the bridge's ability to withstand not only the expected static loads but also the dynamic forces generated by heavy, moving vehicles. The engineers selected steam locomotives, some weighing over 150 tonnes, to simulate the anticipated pressure of future traffic loads under peak conditions. This was a key part of understanding how the arch design and construction would respond to extreme loading.
Complementing the locomotive testing, military tanks, with their uneven weight distribution and high-impact movements, provided valuable insights into the bridge's strength under a different kind of dynamic load. This foresightedness, including the testing of these heavy vehicles, underlines how engineers anticipated the bridge's need to support a diverse range of heavy traffic, including potential military and industrial uses.
During the tests, engineers intently monitored the bridge's behaviour, tracking deflections, vibrations, and other structural responses. They focused on minimizing displacement, demonstrating a strong understanding of the complex relationship between loads and material behavior in the real world. These tests, while seeming like a simple procedure today, were cutting-edge for their time.
The successful completion of the tests with these heavy loads was a significant achievement, ultimately leading to the bridge's opening in March 1932, just months after the testing was concluded. This rapid transition from testing to public use highlights the project's well-managed execution despite the pressure of public expectations.
Intriguingly, the tests revealed the bridge possessed a load capacity surpassing its original design specifications. This overcapacity indicates a robust arch design, suggesting a potentially longer lifespan and a natural capacity to absorb future increases in traffic flow without significant upgrades.
Instead of relying solely on theoretical calculations, the engineers opted to use actual vehicles to validate the structural design. This commitment to empirical validation highlights an innovative approach to structural testing, an approach that had profound implications for the evolution of engineering standards and practices.
The testing involved a meticulous system for measuring load distribution, incorporating both mechanical instruments and visual observation to assess the arch's response. This combination of methods highlights the essential nature of comprehensive data collection in structural engineering.
The various load scenarios tested were crucial for confirming not only the structural strength but also the validity of the engineering assumptions that underpinned the design process. By carefully observing the bridge's behavior during the test period, engineers could detect and address potential discrepancies before the bridge entered operational service.
The Sydney Harbour Bridge is undeniably celebrated for its design and construction, yet these extensive load tests mark a crucial phase in its development. They underscore the importance of rigorous, practical validation of both engineering principles and construction methods in monumental projects. This meticulous testing process provides further insight into the dedication and attention to detail which underpinned the iconic structure’s construction and enduring legacy.
Structural Engineering Marvel Sydney Harbour Bridge's 53,000-Tonne Steel Arch Design and Construction Analysis - Expansion Joint Design For 180mm Movement In Australian Weather
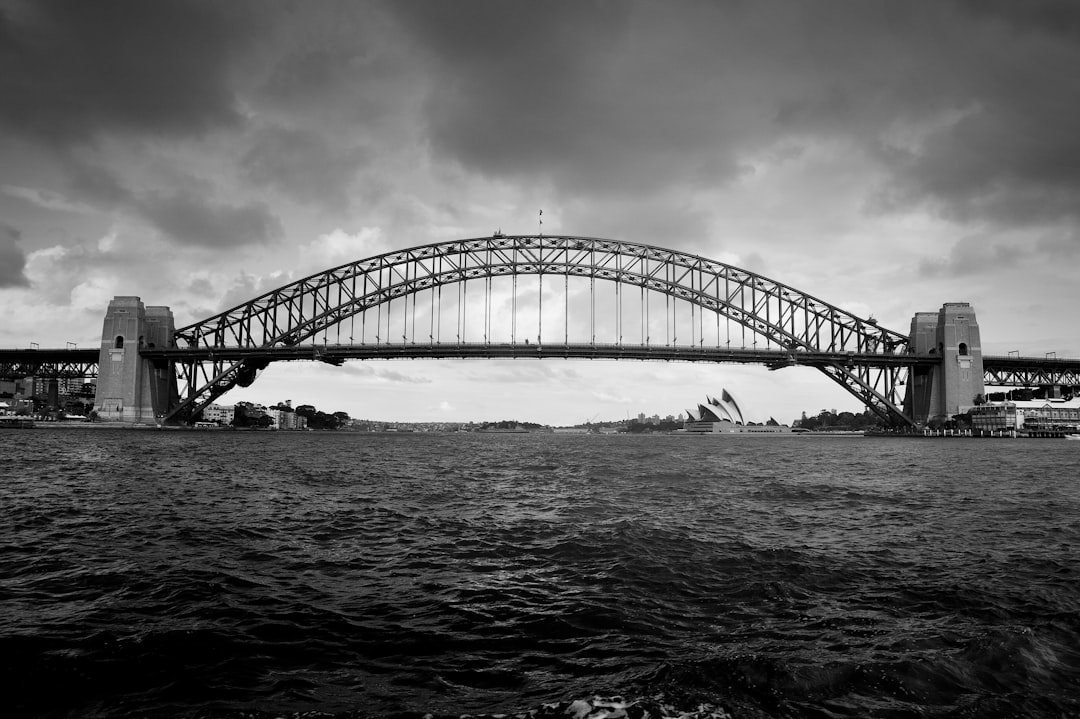
The Sydney Harbour Bridge, with its massive steel arch, highlights the critical need for carefully designed expansion joints. Australian weather conditions, characterized by wide temperature swings, necessitate joints capable of accommodating up to 180mm of movement. This is essential for maintaining the bridge's structural integrity, ensuring that expansion and contraction due to temperature changes don't lead to damage or compromise safety.
Expansion joint designs often incorporate extruded aluminum and neoprene glands to achieve this. These materials allow for a controlled movement within the bridge structure while minimizing the size of gaps that could potentially weaken the bridge. In certain situations, like areas with skewed alignments, standard expansion joint systems might not suffice. Specialized designs, like Steel Finger Expansion Joints (SFEJs), are then called for, able to manage the larger movements and complex geometries encountered in critical bridge sections.
This attention to detail in expansion joint design underscores a broader principle: As we continue to design and build large-scale infrastructure, the ability to predict and accommodate environmental factors like temperature fluctuations becomes ever more crucial. The long-term performance and durability of these structures depend heavily on how well the design anticipates and addresses these challenges.
The Sydney Harbour Bridge's 53,000-tonne steel arch necessitates meticulous consideration of expansion and contraction due to temperature fluctuations, a significant aspect of Australian weather. Expansion joints designed to manage up to 180mm of movement are crucial. This substantial range reflects the inherent challenges of steel's thermal expansion, roughly 0.012mm per meter per degree Celsius. Getting these calculations precisely right is critical for the bridge's long-term functionality and structural safety.
Over time, the repetitive cycles of expansion and contraction can induce material fatigue. Engineers must factor in the expected fatigue life of the joints themselves and the surrounding steel structures to prevent failure under repeated stresses. These joints must not only handle the effects of temperature changes but also the dynamic loads imposed by traffic and the surrounding environment. The bridge's design aims to smoothly accommodate both, requiring the expansion joints to efficiently absorb shocks and vibrations without endangering structural integrity.
The unpredictability of Australian weather poses a unique challenge. Sudden storms and intense heat can significantly impact how these joints function. It's vital that they are built to withstand torrential rain and adapt to the extreme expansions caused by heat waves, all while preserving safety and reliable functionality.
In contemporary bridge design, innovative materials like high-performance elastomers are increasingly used to enhance the flexibility and durability of expansion joints. These materials are often superior to the traditional materials used in the past, offering better resistance to environmental degradation.
Accessibility for maintenance can be severely restricted in large structures like the Sydney Harbour Bridge. This makes inspections and repairs more difficult. Careful design decisions regarding accessibility are essential for long-term maintenance and performance. The bridge's proximity to saltwater exposes its components to corrosion from sea spray. Choosing corrosion-resistant materials and applying protective coatings are vital in mitigating these effects and increasing the joints' longevity.
The design of the expansion joints has to complement the bridge's overall structure, ensuring that movement is accommodated without generating excessive stress on the steel arch. This requires detailed calculations that match the movement capacity of the joint to the arch's expected thermal behavior.
The design of expansion joints in historical structures, such as the Sydney Harbour Bridge, learns from past performance data. Insights gained from initial bridge operation and subsequent retrofitting are incorporated into current expansion joint designs to ensure durability and reduce long-term maintenance demands.
Beyond traditional static load calculations, contemporary engineers utilize advanced testing protocols to verify joint performance. Finite element analysis is a popular method, as it can simulate real-world scenarios to optimize the joints before installation. These detailed simulations and tests help to ensure the joints are truly fit for purpose.
Structural Engineering Marvel Sydney Harbour Bridge's 53,000-Tonne Steel Arch Design and Construction Analysis - Load Distribution Through 28 Steel Box Panels And Cable Networks
The Sydney Harbour Bridge's structural integrity relies heavily on a complex load distribution system. This system uses 28 steel box panels and a network of cables to distribute the immense weight of the bridge, including its 53,000-tonne steel arch, efficiently. The design of this load distribution system needed to accommodate a wide range of loads, both static (like the bridge's own weight) and dynamic (from moving traffic and wind). It's a testament to the bridge's engineering that the designers anticipated the diverse ways the bridge might be loaded and developed solutions that distribute those loads safely and efficiently. The approach blends principles of uniform load distribution with specific strategies to deal with concentrated loads, ensuring the bridge's structural stability in a variety of conditions. By understanding how these forces interact with the bridge's design, engineers were able to achieve a remarkably robust and durable structure that has stood the test of time. This focus on load distribution is a crucial aspect of the bridge's engineering success and contributed to its lasting legacy as a remarkable piece of infrastructure.
The Sydney Harbour Bridge's design incorporates a notable system for managing load distribution, relying on 28 steel box panels and a network of cables. These panels act as a crucial component for evenly distributing the forces along the bridge's arch, minimizing the potential for stress concentration, which could be problematic under dynamic loads such as those caused by moving vehicles. This arrangement not only helps with load distribution but also enhances the bridge's overall stiffness, enabling it to better withstand forces that come from lateral directions, such as strong winds.
Each of these steel box panels functions as a compressive element within the arch, efficiently transforming vertical loads into compressive stresses. This innovative method proves effective in maximizing the utilization of the steel's strength, allowing the bridge to handle significant weight while minimizing material usage. Simultaneously, the integrated cable network plays a pivotal role in stabilizing the arch against torsional and lateral movement, ensuring that the transfer of loads isn't simply vertical but accommodates multi-directional forces as well. This multi-faceted function further contributes to the overall structural stability during occurrences like seismic events or periods of high wind.
To achieve the precise alignment necessary for effective load transfer, the engineers leveraged sophisticated finite element modeling techniques. These simulations meticulously detailed how diverse loading conditions would interact with both the steel panels and the cable network. This advanced modeling not only informed the design but also played a significant role in the actual construction phase, enhancing accuracy and precision during the assembly process.
The bridge’s load distribution system cleverly combines traditional arch theory with innovative 20th-century engineering solutions. This unique marriage of design principles leads to a configuration that promotes both efficient material use and impressive long-term durability – a balance often difficult to achieve in such monumental structures. Furthermore, the bridge exhibits noteworthy resilience because of its dynamic ability to redistribute loads in real-time, thanks to the well-coordinated interplay between the steel box panels and the supporting cable system. This adaptability allows it to effectively manage variable conditions.
A critical element of the bridge's design process involved meticulous calculations of the anticipated deflection of the steel box panels under maximum anticipated load conditions. This forward-thinking approach guaranteed that the bridge not only met safety standards but also had the potential to accommodate unforeseen stresses over its lifespan. Interestingly, despite its historical context, the fundamental design principles employed in the bridge continue to be relevant in contemporary structural engineering practices. The pursuit of efficient load distribution continues to be a key factor in modern bridge design, especially in the selection of materials and the overall structural layout.
The novel combination of steel box panels and cable networks in the Sydney Harbour Bridge represented a significant advance in structural design methodologies in the early 20th century. This innovative approach ultimately paved the way for future infrastructure projects, highlighting the profound impact of meticulously planned load distribution on the performance and longevity of engineering marvels. The Sydney Harbour Bridge's design continues to be a valuable example of how thoughtful structural engineering can lead to the creation of truly exceptional infrastructure, even in the face of the formidable challenges involved in creating something of such scale.
Structural Engineering Marvel Sydney Harbour Bridge's 53,000-Tonne Steel Arch Design and Construction Analysis - Protective Paint System Evolution From Lead Based To Modern Zinc Coatings
The evolution of protective paint systems for steel structures like the Sydney Harbour Bridge has seen a notable shift from older lead-based options to modern zinc-rich coatings. Lead-based paints, while common until the 1980s, were found to be problematic due to health and environmental concerns. Modern approaches, particularly in demanding environments like Sydney Harbour, involve multi-layered paint systems. These typically include a foundational zinc-rich primer layer, providing enhanced corrosion protection. This initial layer is then covered by additional coats designed to further resist degradation. We've also seen newer technologies, including thermal spray zinc and even "smart" coatings, that offer improved protection in specific corrosive environments. The transition to these newer systems is a good example of engineering adjusting to meet current standards and is a vital aspect of extending the life and structural integrity of large steel structures. This adaptation highlights the need for engineering practices to remain up-to-date with contemporary health and environmental regulations.
The Sydney Harbour Bridge's protective paint system has seen a fascinating transformation from the lead-based paints used initially to the more modern zinc-rich coatings we see today. This change reflects a growing awareness of the long-term effects of materials and a shift towards enhanced durability and corrosion resistance. Lead-based paints, while offering protection, were later found to have significant health and environmental downsides. This realization spurred a change in practices, illustrating a heightened focus on safety and environmental concerns in the field of engineering.
Zinc coatings have become a popular alternative due to their unique 'sacrificial' nature. Zinc readily corrodes before the underlying steel, offering a level of protection even if the paint surface gets damaged. This characteristic proves especially beneficial for structures like the Sydney Harbour Bridge that face harsh environmental conditions. It's quite remarkable how the lifespan of steel structures can be greatly improved through this method.
Modern paint technologies, beyond just zinc, also incorporate polymers to further increase performance. These advanced polymers improve adhesion and offer resistance to challenging weather conditions, reducing the need for frequent maintenance. The move towards zinc-rich coatings is directly tied to the advancements in our understanding of corrosion. Today's bridge coatings are often layered systems using primers and topcoats in a way that wasn't possible during the Sydney Harbour Bridge's construction. This layering strategy is designed to maximize both adhesion and flexibility, increasing overall protection.
Interestingly, the original protective scheme for the bridge went beyond just the surface. The original design also focused on thorough treatment of hidden areas like joints and connections, showing early awareness of the need to combat internal corrosion. This early foresight highlights the evolving awareness of corrosion mechanisms within the field of structural engineering.
The Sydney Harbour Bridge, despite its robust protective system, has required ongoing maintenance throughout its life. This highlights that even modern paint systems aren't completely invincible and can suffer from localized failures, particularly from constant exposure to the elements.
The development of advanced paint formulations has enabled extended periods between maintenance cycles, increasing efficiency and reducing long-term upkeep costs. This is crucial for massive structures like the bridge, where regular maintenance can be a significant challenge and expense.
Contemporary inspection methods are also more advanced, employing techniques like ultrasonic testing to examine the integrity of protective layers without needing to remove them. This represents a substantial improvement in safety and health compared to older visual inspection methods, providing a detailed look at the structural health beneath the surface.
The Sydney Harbour Bridge's evolving maintenance practices demonstrate the value of blending expertise from different fields. Combining structural engineering and materials science allows for a more holistic approach to designing and maintaining infrastructure. This fusion of disciplines will undoubtedly play a more crucial role as we continue to build and maintain large-scale structures that need to endure for decades.
More Posts from aistructuralreview.com: