AI-Driven Rapid Prototyping Accelerating Product Development Cycles in 2024
AI-Driven Rapid Prototyping Accelerating Product Development Cycles in 2024 - 3D Printing Drives Cost-Effective Design Workflows in 2024
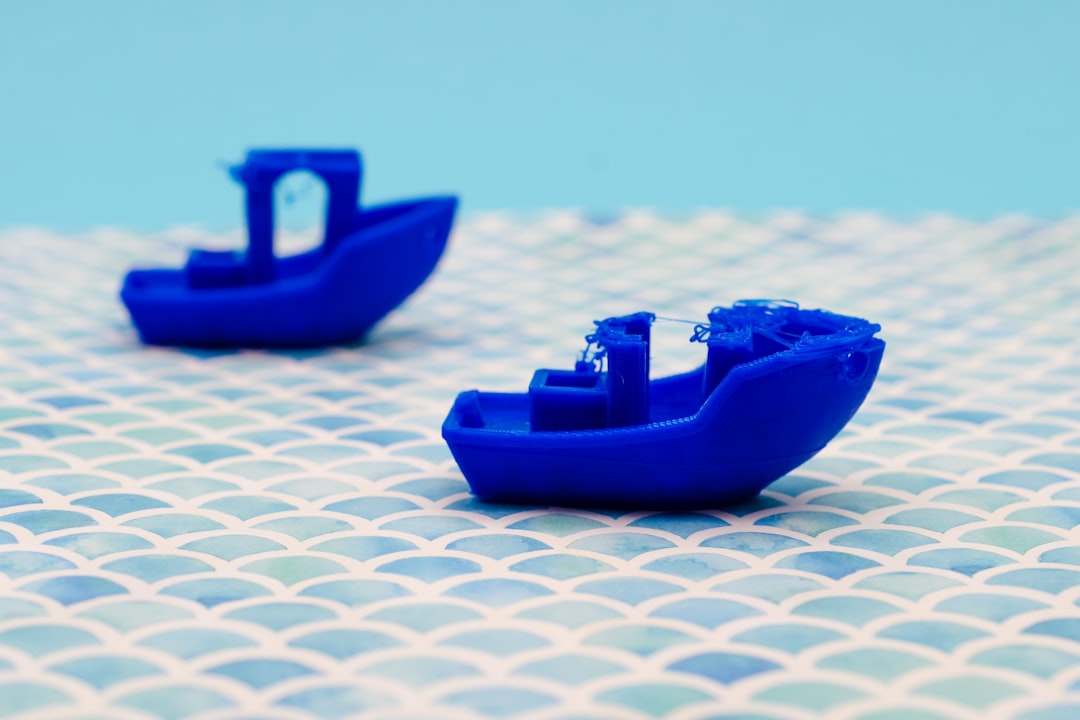
Throughout 2024, 3D printing is proving to be a game-changer in design, enabling cost-effective production methods that drastically reduce development timelines. The integration of AI-powered design tools and improvements in computer-aided design (CAD) are allowing for rapid prototyping cycles without the usual high costs associated with traditional molds and tooling. This agile approach offers companies the ability to swiftly adapt designs, enabling a more responsive and efficient reaction to market fluctuations. While the impact of 3D printing is felt across industries, its adoption in areas such as dental and aerospace demonstrates its increasing importance in boosting output and refining product precision. This shift towards additive manufacturing is fundamentally transforming how new products are brought to market. However, it's crucial to acknowledge the continued research into a wider range of printable materials, including metals, ceramics, and biocompatible options, to expand the scope of 3D printing's applications even further.
It's fascinating how 3D printing, or additive manufacturing as it's often called, is becoming a more affordable option for design exploration. We're seeing a noticeable drop in the cost of producing intricate parts, which opens up new possibilities for engineers to experiment with designs that were once out of reach due to cost constraints. This cost reduction is a major factor behind the expanding 3D printing service market, particularly as industries demand more rapid prototyping and bespoke products. This trend is especially prominent in the dental field where the speed and accuracy of digital dental solutions powered by 3D printing are transforming how things are done.
One of the more striking aspects of 3D printing is how it speeds up the design process. Engineers can easily make changes to designs and iterate through prototypes in a matter of hours, a far cry from the days or weeks it would take using traditional methods with molds and tooling. This has implications for the speed of product development across the board, from aerospace to healthcare. Though the US market is seeing a lot of growth in this area, it's the Asia Pacific region that's projected to see the most rapid expansion in the near future. It's not surprising, then, that various industry reports point to 3D printing as the key to streamlined and affordable design workflows for prototyping.
The research community is also exploring a wider array of materials for 3D printing, from the usual plastics and metals to ceramics and even biomaterials. Each of these materials offers distinct benefits depending on the desired application. This area of research promises some really interesting and potentially impactful applications, as we're seeing with bioprinting in the medical field. It's an area to watch closely. While the field is still developing, it's becoming increasingly clear that 3D printing allows for more flexibility in product design and quicker time-to-market, with benefits extending across a diverse set of industries. However, it's worth noting that there are always limitations and challenges with emerging technologies, so further study and refinement of these processes will likely be necessary to fully realize the potential of this approach.
AI-Driven Rapid Prototyping Accelerating Product Development Cycles in 2024 - Hybrid Manufacturing Technologies Enhance Complex Prototyping
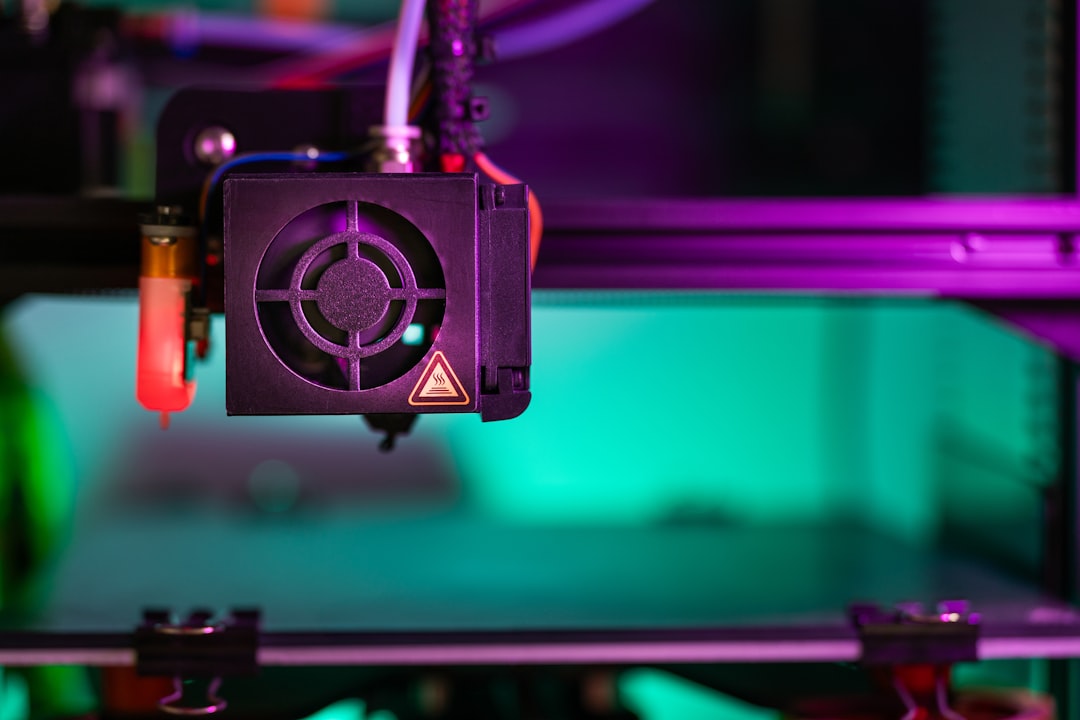
In 2024, the field of prototyping is witnessing a surge in the adoption of hybrid manufacturing technologies. These techniques cleverly combine additive and subtractive processes, such as seamlessly integrating CNC machining with laser-powder bed fusion. This approach paves the way for crafting highly complex and intricate prototypes with an unprecedented level of efficiency. The integration of these manufacturing methods, fueled by the ongoing AI revolution in rapid prototyping, is proving invaluable for industries struggling to keep up with dynamic market demands. Businesses are now able to respond more swiftly to market shifts while simultaneously lowering costs and speeding up production cycles.
Yet, the reliance on increasingly sophisticated and specialized technologies in prototyping presents a potential challenge. Concerns about the viability of conventional manufacturing processes arise, as industries become more heavily dependent on AI-driven and hybrid manufacturing practices. The potential for established manufacturing methods to become obsolete or marginalized is a notable consequence. Going forward, striking a balance between harnessing the potential of cutting-edge prototyping techniques while ensuring the continued relevance of existing manufacturing capabilities will be crucial to sustaining a robust and resilient manufacturing landscape.
Hybrid manufacturing techniques are increasingly important in 2024, particularly for complex prototyping. The ability to combine additive and subtractive processes, like 3D printing and CNC machining, is allowing for a new level of precision and intricacy in the designs we can create. For industries where complex parts are the norm, like aerospace and medical devices, this is a significant advancement.
One of the advantages of this blending of manufacturing methods is the ability to work with a wider variety of materials within a single production run. This means we can create parts that need different mechanical properties in different sections—a part that needs to be both strong and flexible, for example. It's a fascinating step toward more complex and functional prototypes.
The speed at which we can generate prototypes has also been dramatically improved by hybrid systems. Production times are often much shorter compared to traditional manufacturing methods, which has a huge impact on the pace of the overall product development cycle. It's impressive how quickly engineers can now move from concept to a physical representation of their design.
Hybrid manufacturing opens up a new world of design possibilities. We aren't as limited by the constraints of traditional machining, which allows engineers to think outside the box and explore novel features that would have been impractical before. For instance, we're now seeing things like lightweight, internal lattice structures in prototypes that were impossible to manufacture before.
Unlike some traditional manufacturing techniques, hybrid systems offer real-time monitoring and adjustment during the production process. This is quite valuable for complex prototypes where precise control is important, and it allows for better quality control and reduced errors. It's a much more dynamic approach to manufacturing.
While the initial investment in hybrid manufacturing equipment can be substantial, the long-term benefits can outweigh this cost. Reductions in tooling and labor costs can be quite substantial over time. It's a decision that needs careful consideration, but it offers an appealing option for companies looking to enhance their prototyping process.
The faster prototyping cycles enabled by hybrid manufacturing also create more effective feedback loops. Designers can iterate quickly, and with more iterations comes a better end product. We're able to incorporate feedback and make changes to the designs much faster, which leads to a higher-quality final design.
A notable feature of hybrid manufacturing is its scalability. Whether you need a few prototypes or a large batch, it's possible to adapt the approach to meet your needs. This makes it a great option for both smaller companies needing a few unique parts and larger corporations looking for a more efficient mass-production process.
With hybrid methods, we can tailor prototypes to the specific requirements or specifications needed. This can be critical for markets that value highly personalized or customized products, a trend that is gaining momentum across many industries.
The complex nature of hybrid manufacturing inevitably involves greater collaboration across different engineering fields—mechanical, materials science, and software engineers all come into play. This has the beneficial consequence of fostering more innovation within companies and helping accelerate the overall development cycle.
These changes in manufacturing processes are creating a need for new knowledge and skills, which is exciting for those of us involved in research and development. It's indicative of a broader shift towards integrated and more complex approaches to engineering. The future of prototyping looks quite promising, with hybrid manufacturing technologies offering significant improvements in speed, flexibility, and overall efficiency in product development.
AI-Driven Rapid Prototyping Accelerating Product Development Cycles in 2024 - Generative AI Shifts from Hype to Practical Applications
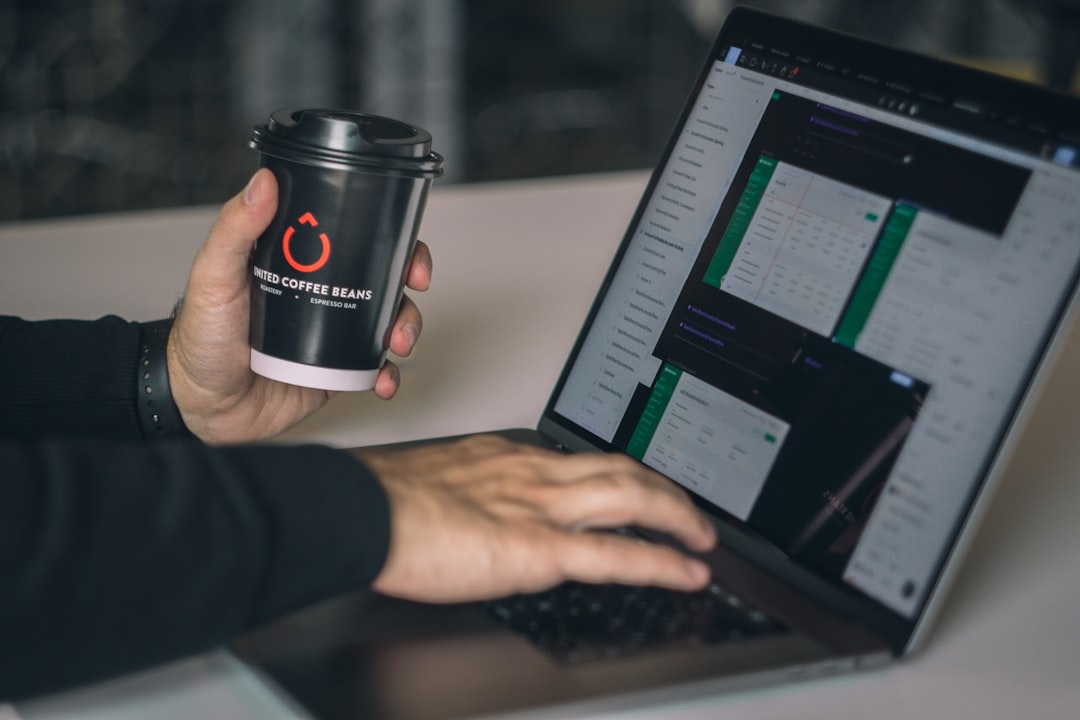
Generative AI, once primarily a topic of hype and speculation, is now finding its footing in practical applications across a range of industries. The initial excitement surrounding foundational models is giving way to a more measured approach, with companies focusing on how these tools can deliver tangible results. We are seeing the emergence of more advanced AI models like Claude 3, and anticipation for future iterations like GPT-5, which are pushing the boundaries of AI capabilities and demonstrating ongoing innovation. This development is pushing businesses to explore how generative AI can be leveraged in specific, practical situations, particularly in areas like automating customer support interactions or streamlining human resource tasks. Early successes in these areas suggest that incorporating generative AI can lead to tangible improvements in efficiency and effectiveness.
While the potential is undeniable, this shift towards practicality also highlights the challenges companies face in adopting these novel technologies. The integration of generative AI requires careful consideration of how it fits within existing workflows and the need to manage the potential risks and biases inherent in these tools. Nevertheless, the promise of faster and more efficient product development cycles through the application of generative AI in rapid prototyping processes is driving continued interest and exploration. As we progress, it will be crucial for organizations to assess the practical limitations and potential downsides alongside the benefits to ensure they're using these tools in a responsible and effective manner.
The buzz surrounding generative AI seems to be transitioning from a peak of hype to a more grounded focus on practical applications. We're seeing a shift from simply being excited about the underlying models to exploring specific ways to use them to solve real-world problems. New AI models, like Claude 3 and the anticipated GPT-5, are pushing the boundaries of what AI can do, demonstrating that the field is still evolving quickly.
This rapid development is leading to a stronger emphasis on using generative AI in different industries. Early successes, especially in areas like creating FAQs and supporting human resources tasks, suggest that companies are starting to find valuable applications for it. We're likely to see this trend continue, with experts predicting that by 2026, a significant majority of software developers will be using these tools, compared to the current adoption rate.
It's interesting to see that, even with a bit of a slowdown in spending on generative AI, many businesses still recognize the need to adopt it to stay competitive. This suggests that while the initial wave of excitement might be calming down, it's not fading away entirely. Instead, organizations are moving past the hype and looking for tangible benefits. Gartner's report highlights this shift, identifying autonomous AI and developer productivity, along with generative AI, as areas where significant progress is expected this year.
It's becoming clear that the goal is now about leveraging generative AI to achieve longer-term objectives, rather than simply chasing the latest technology. As companies integrate AI-driven rapid prototyping into their processes, we can expect this shift to further speed up product development cycles.
A recent webinar touched on how companies can separate the hype from the reality of generative AI. This is an important step in ensuring that the adoption of these tools is informed and productive. It feels like we're at a crucial stage where the true potential of generative AI is starting to become evident, moving beyond early demonstrations and into practical use cases that could reshape many aspects of how things are designed and built.
AI-Driven Rapid Prototyping Accelerating Product Development Cycles in 2024 - AI Transforms Product Development Lifecycle Stages
AI is fundamentally altering the traditional product development lifecycle in 2024. It's no longer just a futuristic idea; it's becoming deeply embedded in the process, from the initial spark of an idea to a product hitting the market. AI-powered tools, including generative design and the ability to rapidly create prototypes, are allowing design teams to experiment and refine product concepts at a much faster pace. This agility is particularly valuable in today's rapidly changing marketplace. The ability to test and tweak designs more quickly is a significant advantage. Moreover, AI can inject a fresh wave of creativity into the design process, empowering teams to explore new and innovative solutions.
But with these technological leaps come questions and challenges. The heavy reliance on AI-driven methods raises concerns about the long-term relevance of more established manufacturing techniques. Is there a risk of losing essential skills and knowledge that have been built up over many years? Maintaining a healthy balance—keeping the benefits of AI while also valuing established methods—is going to be vital as the industry continues to change. Companies that are at the forefront of implementing these new AI-driven processes need to be mindful of these potential downsides and make informed decisions. Ultimately, understanding how to effectively harness AI's potential within the existing product development infrastructure will be a key determinant of success for companies in the future.
AI's influence on product development extends beyond just the design phase. It can also optimize things like supply chain management, potentially reducing lead times by a significant amount—up to 30% in some cases. This increased efficiency allows for more agility in responding to market changes and encourages faster design iterations.
Generative design tools, powered by AI, can churn out a huge number of design variations within a short timeframe, often just minutes, based on predefined parameters. This accelerates the design process considerably compared to traditional methods. We're essentially shifting the focus from laborious manual design iterations to a more creatively driven approach.
Prototyping with AI is changing the game when it comes to predictive analytics. AI models can anticipate and identify potential flaws in a design even before a physical prototype is built. This ability can significantly reduce the number of prototypes needed, leading to lower costs.
The more sophisticated AI models use machine learning to analyze user feedback in real-time, offering designers a window into how consumers react to their work. This enables design teams to react quickly to changing user preferences, helping to ensure that products are closely aligned with user needs right from the beginning.
Hybrid manufacturing, now enhanced by AI, isn't just a faster way to produce; it unlocks the creation of intricate and complex parts that conventional methods struggle with. This allows for innovation in product design where certain features were either impractical or prohibitively expensive before.
AI algorithms are being used to simulate how a product will perform under diverse conditions. This improved pre-release testing can significantly accelerate the refinement process. The upshot is more durable and reliable products.
Some interesting trends are emerging. We're seeing reports that companies utilizing AI-driven rapid prototyping are experiencing a dramatic speed-up in usability testing—up to 50% in some instances. This transformation turns consumer feedback into actionable insights far earlier in the development process.
In fields like medical device development, AI is driving the ability to quickly create customized prototypes that precisely cater to individual patient requirements. The potential impact is substantial, including the acceleration of regulatory approvals.
The intersection of AI and materials science is exciting. AI research is fueling the development of novel composite materials with enhanced performance, specifically designed for demanding applications, including industries like aerospace and automotive.
Even with all the benefits of AI-powered rapid prototyping, there's a key challenge that needs to be addressed—the human element. We are seeing a gap in skilled personnel capable of effectively interpreting the huge amounts of data and feedback that AI systems generate. If this skills gap isn't addressed, it could limit the true potential of these powerful new tools in the product development cycle.
AI-Driven Rapid Prototyping Accelerating Product Development Cycles in 2024 - AI-Powered Tools Reduce Development Cycle Time

In 2024, AI-powered tools are dramatically altering product development by significantly shrinking development timelines and boosting output. Generative AI, in particular, has enabled developers to complete tasks remarkably fast, often achieving a twofold increase in speed compared to conventional approaches. This acceleration is further fueled by AI's ability to swiftly analyze market trends and user feedback, empowering companies to adapt designs with greater agility. However, as industries become more reliant on these AI-driven tools, concerns about the long-term viability of traditional manufacturing methods are emerging. The possibility of established skills and knowledge being sidelined is a notable worry. Maintaining a healthy equilibrium between leveraging AI innovations and preserving established practices will be essential for navigating this dynamic landscape.
The integration of AI is fundamentally changing the pace of product development in 2024. We're witnessing a shift away from traditional, often lengthy, design cycles towards a more agile approach driven by AI-powered tools. For example, AI can generate a multitude of design variations within minutes, a stark contrast to the weeks it used to take to iterate through a few manual designs. It's almost as if AI is letting engineers explore a vast design space in a fraction of the time. Interestingly, some AI algorithms are now capable of predicting potential design flaws even before a physical model is built. This preemptive flaw detection can significantly reduce the number of physical prototypes needed, which in turn minimizes costs and development time.
Furthermore, the integration of AI allows for a faster and more direct feedback loop between the design team and potential users. Some AI systems can analyze real-time feedback from users, offering insights into what people want and don't want. This accelerates the process of refining designs to align more closely with consumer needs. We've even seen reports of companies significantly speeding up usability testing, reducing the time needed by up to 50%. It’s an exciting development because it allows design teams to incorporate feedback early on in the process. It's fascinating how AI-driven tools are opening up new possibilities in terms of designing intricate parts and customized prototypes. We're seeing things like highly individualized medical device prototypes being created in a matter of days, leading to faster regulatory approvals.
Another aspect is the growing role of AI in streamlining supply chain operations. AI is being leveraged to optimize supply chain management, which can reduce lead times by as much as 30%. This enhanced efficiency allows companies to quickly adapt to market changes and accelerate the time between prototype and product launch. AI is even influencing material science. It’s now driving the development of new composite materials with advanced properties, particularly crucial in fields like aerospace and automotive where highly specialized components are needed.
The shift towards AI-driven rapid prototyping isn’t without its challenges. While we see major gains in efficiency and innovative design capabilities, the ever-growing reliance on AI also raises concerns about the long-term viability of traditional manufacturing skills and methods. Striking a balance between the advancements offered by AI and the preservation of crucial human skills will be essential for the future of product development. There's a growing skills gap to address—educating and training engineers to work effectively with the vast amount of data generated by AI is becoming critical. If we fail to bridge this gap, we risk limiting the potential of these incredibly powerful new tools. Nonetheless, the ability to generate highly customized designs, rapidly iterate through design iterations, and leverage AI's ability to optimize supply chains and predict potential issues points to a future where the product development cycle is dramatically condensed, paving the way for more innovative and rapidly launched products.
AI-Driven Rapid Prototyping Accelerating Product Development Cycles in 2024 - Instantaneous Design Ideas Expedite Innovation Process
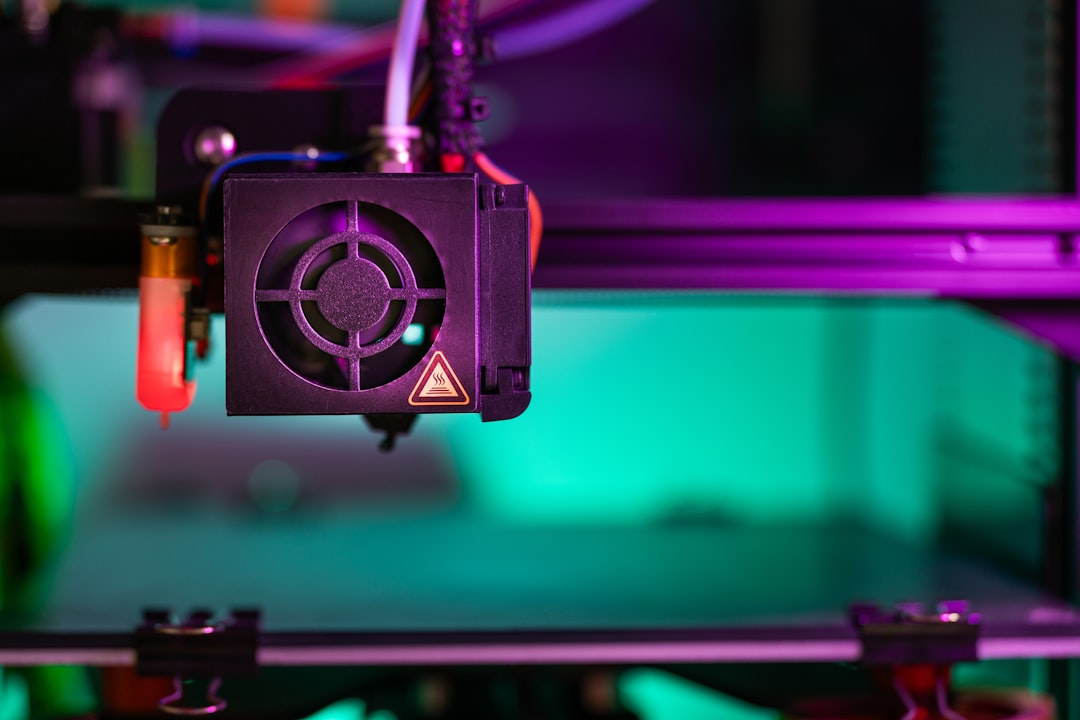
In 2024, the ability to rapidly generate design ideas through AI has become a pivotal factor in driving innovation. AI-powered tools, particularly generative AI, are automating the tedious process of manually tweaking designs, allowing teams to quickly explore numerous potential product concepts. This ability to swiftly generate and refine designs not only fuels creativity but also enables faster adjustments based on immediate feedback, ultimately leading to a marked decrease in the time it takes to bring products to market. The growing dependence on AI-driven design, however, brings about legitimate concerns regarding potential skill shortages and the future of conventional manufacturing techniques. Companies need to be mindful of these issues and take a balanced approach when incorporating AI, ensuring that the interplay between AI-powered tools and human expertise remains a central focus moving forward. The success of future innovation efforts will hinge on how well companies can navigate this shift in the design landscape.
The integration of artificial intelligence (AI) into design processes is rapidly accelerating the pace of innovation, particularly in the realm of rapid prototyping. While we've seen the cost-effectiveness of 3D printing revolutionize how designs are brought to life, AI is now taking center stage by enabling near-instantaneous design explorations. This shift is driving an unprecedented ability to quickly adjust designs based on user feedback in real-time, making prototyping a much more dynamic and responsive activity. Engineers can now experiment with a vast range of design options, generating thousands of variations in a matter of minutes, which can unearth innovative solutions that might have been missed through traditional, manual approaches.
Intriguingly, AI can also predict potential flaws in designs even before physical prototypes are created. This predictive capability significantly minimizes wasted materials and development costs, enabling a more targeted and efficient approach to design iterations. Moreover, AI-driven rapid prototyping is transcending traditional industry boundaries, with surprising applications appearing in unexpected areas like the fashion and toy industries. The ability to quickly prototype complex, intricate designs is opening up new frontiers in product creation for consumer goods.
However, the widespread adoption of AI is also impacting the knowledge transfer within design teams. The automation of repetitive design tasks allows for valuable design expertise to be effectively captured and integrated into the development process. This embedded knowledge transfer is not only preserving institutional memory but also encouraging designers to focus their talents on more complex challenges, rather than getting bogged down with routine work. The increased efficiency in prototyping allows for the development of highly customized products at a large scale, with notable impact across industries like healthcare and consumer electronics. AI-powered systems are driving personalized design solutions tailored to specific user needs, creating enhanced user experiences and increased customer satisfaction.
The ability to quickly simulate the performance of prototypes under different conditions is also changing how designs are evaluated. This advanced simulation capability provides a clearer understanding of potential weaknesses or points of failure, leading to the creation of more reliable and robust products. Hybrid manufacturing approaches, now enhanced by AI-driven instantaneous design approaches, enable real-time error correction during the prototyping stage. This dynamic feedback loop shortens development cycles by reducing time spent on debugging and refinement.
The push towards faster design cycles is also stimulating research into advanced materials. We're seeing AI driving the development of novel composite materials with unique properties, pushing the boundaries of what's possible in fields like aerospace and automotive. This ability to tailor designs to specific material properties is furthering the potential for innovation in design and engineering. Interestingly, the speed of the innovation cycle has also fostered better collaboration between diverse engineering disciplines. Multidisciplinary teams can now explore and refine ideas together more efficiently, resulting in more holistic designs and ultimately, faster development cycles.
The ability to rapidly prototype and refine product designs using AI is reshaping the product development landscape. While there are still questions regarding the long-term impact on established skills and manufacturing techniques, there's no doubt that AI-driven rapid prototyping is accelerating innovation across a wide spectrum of industries. The speed, flexibility, and potential for increased customization offered by this technology could fundamentally alter the future of how products are conceived, designed, and brought to market. However, it is crucial for researchers and engineers to be mindful of the potential consequences of relying on such sophisticated tools and to ensure that appropriate safeguards and training are in place to maximize the potential benefits while mitigating any associated risks.
More Posts from aistructuralreview.com: