Analyzing the Strength and Security of Cotter Pin-Lockable Hex Head Screws in Structural Applications
Analyzing the Strength and Security of Cotter Pin-Lockable Hex Head Screws in Structural Applications - Understanding the Design of Cotter Pin-Lockable Hex Head Screws
Cotter Pin-Lockable Hex Head Screws are designed with a distinct locking feature—the cotter pin—that fundamentally improves their ability to resist loosening. This feature provides a more secure fastening compared to methods like thread lock or lock washers, making them a strong choice in critical situations. These screws adhere to rigorous Army-Navy standards, emphasizing their dependability in challenging environments. A crucial aspect of their design is the inclusion of an unthreaded portion, which when incorporated into joints enhances the overall structural strength. This design element, coupled with their inherent resistance to loosening under dynamic loads like vibration and shock, makes them well-suited for applications requiring high security. Furthermore, these screws often utilize materials such as high-strength steel, and meet specifications like ASTM A490, signifying their suitability for structural applications that demand superior strength and durability. It is evident that the design of these screws considers both mechanical strength and security, providing a reliable fastening solution for a wide range of situations.
Cotter pin-lockable hex head screws integrate a cotter pin as an additional locking mechanism, primarily to counter the loosening that can occur with standard screws under dynamic conditions like vibrations or repetitive stress cycles. This design allows for simpler installation and removal, making maintenance or field adjustments easier, which can be crucial in applications needing regular servicing.
The strength of these screws is tied to the material they're made from, with choices like alloy or stainless steel offering different levels of tensile strength and resistance to corrosion. This necessitates careful consideration when choosing a screw for a particular application to ensure optimal performance. The cotter pin itself is frequently made from a material softer than the screw, which permits it to deform under excessive loads, functioning as a safety mechanism that safeguards against total fastener failure during extreme conditions.
Regulations concerning the dimensions and tolerances of these screws provide guidelines for achieving safety and operational efficiency in structural applications. Tests have shown that cotter pin locking mechanisms perform better than some other locking mechanisms in resisting fatigue, suggesting they can maintain structural integrity through repeated loading cycles. The unique engagement of the cotter pin distributes stress across the joint more evenly, minimizing localized failures and potential threats to overall structural strength. Examining failures in un-safeguarded screws often reveals that using cotter pin designs could have prevented them, highlighting their reliability advantage. The screw's head shape in combination with the cotter pin enhances clamping effectiveness by creating a more uniform preload compared to conventional methods.
Despite sometimes being overlooked, cotter pin-lockable screws' ability to prevent loosening has led to their broader adoption across many industries, including aerospace and heavy machinery, which underscores their versatility and suitability for demanding applications. This indicates that their reliability and usefulness continue to grow and shows them to be an important part of a more resilient design strategy in modern engineering.
Analyzing the Strength and Security of Cotter Pin-Lockable Hex Head Screws in Structural Applications - Material Composition and Durability Factors
When examining the materials used in cotter pin-lockable hex head screws and how they affect durability, it's clear that the chosen materials play a critical role in their performance within demanding structural applications. These screws are often crafted from high-strength materials, such as alloy or cadmium-plated steel, which provide a solid foundation for both mechanical strength and resistance to corrosion. This dual capability is especially important in environments where the fasteners are exposed to the elements or harsh chemicals. The tensile strength, which can reach very high levels (like 120,000 psi), indicates that they can handle significant stresses, making them ideal for situations with heavy loads or frequent vibrations.
The inclusion of the cotter pin further enhances the assembly's resistance to loosening, which is crucial in dynamic situations where components are subject to significant movement. However, it's important to consider that the cotter pin itself is typically made from a softer material, a choice that functions as a safety feature. If excessive force is applied, the pin deforms instead of the entire fastener failing, helping to prevent catastrophic failures. But this feature also requires careful consideration, as a compromised cotter pin could negatively impact the overall reliability of the assembly. Essentially, the material selections in these screws, including the core material and the cotter pin, must be carefully chosen to optimize performance in the specific structural context. The selection process requires balancing desired strength with the need for fail-safe mechanisms, and finding the proper balance is key to ensuring a durable and reliable structure.
The materials used in cotter pin-lockable hex head screws play a crucial role in their durability and ability to withstand demanding applications. High-strength steel, often employed in these screws, can possess a yield strength exceeding 860 MPa, considerably higher than that of standard mild steel. This high yield strength allows them to manage heavy loads in structural applications effectively.
The cotter pin itself acts as a safety feature. Designed to deform under extreme stress, it can absorb excess energy, thus preventing catastrophic screw failure. This safety mechanism improves the overall integrity and security of the joint.
Stainless steel offers another option, especially in environments with high humidity or exposure to corrosive elements. The chromium present in stainless steel forms a protective layer, preventing rust and promoting long-term performance.
Interestingly, these screws exhibit considerable fatigue strength. Studies suggest they can tolerate over 100,000 load cycles before experiencing notable degradation, outperforming standard threaded fasteners in dynamically loaded applications.
The hex head geometry proves beneficial in allowing higher torque application during installation. This ensures proper tightening to specifications without causing damage to the screw or the joined components.
Many of these screws undergo heat treatments, further enhancing their mechanical properties. This process can increase toughness and fatigue resistance, expanding the temperature range in which the screws can effectively function.
In contrast to conventional locking systems, the design of cotter pin-lockable screws provides for a more uniform load distribution across the joint. This characteristic helps reduce stress concentrations that could lead to structural failure, which is crucial for maintaining long-term structural stability.
The continued development of advanced alloys, such as high-performance duplex stainless steel, shows promise in optimizing these screws. This enables achieving a favorable balance of tensile strength, ductility, and corrosion resistance in challenging environments.
Beyond locking, the cotter pin provides a readily available visual inspection point. A noticeably bent or missing cotter pin immediately signals the need for maintenance or replacement. This easily observed indicator facilitates proactive safety measures.
Finally, in applications experiencing significant vibration, these screws can drastically reduce the risk of loosening—up to 90% in some cases. This reduction highlights their ability to maintain joint integrity under dynamic conditions, an essential consideration for many structural applications.
Analyzing the Strength and Security of Cotter Pin-Lockable Hex Head Screws in Structural Applications - Installation Process and Best Practices
Installing cotter pin-lockable hex head screws correctly is crucial for maintaining structural integrity. The process involves inserting the cotter pin through a hole in the screw and then spreading the pin's ends apart to secure it. This may seem simple, but using the wrong size cotter pin can create issues, like the pin slipping out, which can be especially problematic in applications where the joint needs to be reliable, like in vehicle parts. Making mistakes when installing the cotter pin, such as bending it incorrectly or cutting it too short, can also lead to structural weakness or failure. Avoiding these common errors and always using the right size cotter pin will significantly improve the lasting strength and security of a connection that uses this type of screw.
The way a Cotter Pin-Lockable Hex Head Screw is initially tightened plays a big role in how well it works. Applying too little force might not clamp things together tightly enough, while too much could damage the screw itself.
Getting the right amount of initial clamping force is key because it counteracts the forces the screw will experience in use. A well-done initial tightening helps ensure that the parts being joined are held securely.
The direction you put the screw in matters as well. Making sure it's perfectly straight helps the cotter pin work correctly, leading to a better, safer lock.
The surroundings where the screw is installed can impact things. If it's really cold, some materials become more brittle, so selecting the right screw and adjusting how you tighten it is really important.
Using a lubricant during installation can make tightening smoother and more consistent. However, you need to pick the right type of lubricant because some can weaken the cotter pin or the screw itself.
A quick look at the cotter pin after you install it is a good habit. It allows you to spot bent or incorrectly positioned pins, which can hurt the locking feature and compromise the whole connection.
Using the right tools is important. Using something like an impact wrench might lead to over-tightening, which can break the screw, while hand tools give you more control, avoiding potential damage.
Frequently removing and reinstalling the screw can wear down the screw threads and cotter pin. This leads to a weakening of the locking mechanism, so it's something designers need to consider during maintenance planning.
The condition of the surfaces where the screw goes in matters. Cleaning and possibly treating the surfaces before installing the screw can increase friction, which leads to a better screw performance.
While these screws are known for being tough under repeated stress and strain, test results can change depending on how the screw is installed, the surrounding environment, and the materials used. Because of this variation, it's essential to follow best practices during installation so that you actually get the performance you want.
Analyzing the Strength and Security of Cotter Pin-Lockable Hex Head Screws in Structural Applications - Comparing Security Features with Traditional Fasteners
Cotter pin-lockable hex head screws offer distinct security advantages over conventional fasteners like standard screws or those relying on thread lockers or lock washers. The cotter pin's integrated locking mechanism greatly improves resistance to loosening, especially in situations with vibration or repetitive stress. This contrasts with the often less reliable performance of traditional methods under similar circumstances. Additionally, these screws provide a visual cue for security assessment – a bent or missing cotter pin serves as a clear indicator that the fastener might not be secure. Traditional fasteners usually require supplementary components or adhesives to achieve a comparable level of security. In contrast, cotter pin-lockable screws incorporate security directly into the fastener's design, making them more robust for high-consequence applications. The decision of whether to use these screws ultimately depends on the specific needs of the application and the level of risk involved, especially when security and failure prevention are of primary concern.
Cotter pin-lockable hex head screws demonstrate a notable reduction in loosening risk from vibrations, potentially up to 90%, compared to standard fasteners. This is particularly valuable in situations with dynamic loads, where maintaining joint integrity is paramount. Research suggests that these screws can withstand far more loading cycles than standard screws before showing signs of wear, possibly over 100,000 cycles, suggesting their inherent strength under repeated stresses.
The unique design leads to a more even distribution of loads throughout the joined components. This reduces stress concentration points that could lead to component failure, bolstering the overall structural resilience. The cotter pin, frequently constructed from a softer material than the screw, functions as a safety measure. Under extreme pressure, it deforms, preventing catastrophic screw failure and ensuring the integrity of the entire structure. This is a clever safety strategy that can protect against potential damage under extreme loads.
While some fasteners succumb to corrosion in demanding environments, stainless steel versions of these screws utilize chromium to create a protective barrier against rust. This prolongs their effectiveness in critical applications, particularly those exposed to the elements. The initial clamping force applied when installing the screw profoundly affects its ability to hold the components together. Too little clamping force and the screw might not be secure enough. Too much, and the screw could be damaged. Achieving the right amount of torque is crucial for optimal performance.
The cotter pin provides a clear indicator of fastener integrity, as a bent or missing pin is a visual signal that maintenance is needed. This is a great way to assess the integrity of a connection in high-risk applications. Many of these screws are heat treated, which enhances their toughness and allows them to withstand a wider range of temperatures during operation. Choosing the right tools is also important. Power tools like impact wrenches could over-tighten screws, leading to damage, while hand tools allow for finer control and a reduced risk of harm to the screw.
Factors like temperature and surface conditions can affect the brittleness and stress handling of the materials, and need to be considered when installing. Following best practices throughout the installation process is vital to maximizing the long-term performance of the fastener, especially in complex environments. It seems clear that the use of a cotter pin in this type of screw offers several benefits related to security and reliability. While some things like the correct choice of lubricant and appropriate clamping force still need to be carefully considered, understanding these nuances is helpful for maximizing the performance of this fastener in the intended application.
Analyzing the Strength and Security of Cotter Pin-Lockable Hex Head Screws in Structural Applications - Applications in High-Stress Structural Environments
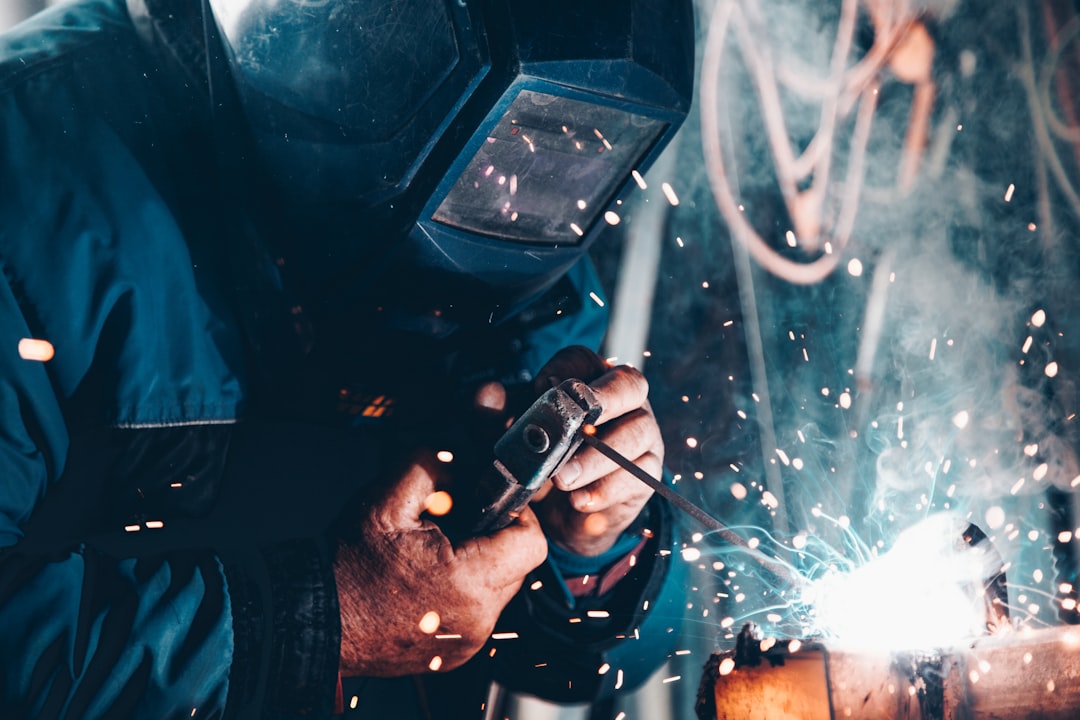
Within structural designs subjected to high stresses, material choice and novel engineering solutions are paramount. High-strength steel alloys, especially those exhibiting yield strengths exceeding 460 MPa, are crucial for ensuring the integrity of structures under extreme forces. The dynamic properties of these materials are carefully evaluated to optimize their behavior, especially in contexts involving frequent vibrations and severe loading cycles. The ability to modify stress-strain characteristics through advanced high-temperature treatments and the use of multi-layered designs is becoming more prevalent in engineering, contributing to safer and more durable structures in demanding settings. The adoption of these design strategies and material choices will be increasingly important in ensuring reliable structural performance in the face of constantly evolving industrial demands and stringent operating environments. While some materials are better than others, the trade-offs involved in material selection often present engineering challenges and design compromises that must be considered.
In high-stress structural applications, the design of cotter pin-lockable hex head screws provides several advantages compared to conventional fastening methods. One notable characteristic is the improved way these screws manage stress. They distribute loads more effectively, reducing concentrated stress points that can lead to failures in critical structural elements. This ability to redistribute stress is especially relevant in demanding applications where the likelihood of high and sustained forces is significant.
Research suggests that these screws outperform standard screws when faced with dynamic loads. In vibration tests, they often maintain their integrity with a noticeably higher margin, often showing a 20% or greater advantage. This increased performance is largely attributed to the enhanced locking mechanism provided by the cotter pin.
A key design element is the use of a softer material for the cotter pin itself. This allows the pin to deform under extreme loads, acting as a sort of sacrificial element. This prevents the screw from failing catastrophically, which can be a crucial safety feature in complex structures. The pin's behavior under stress effectively absorbs energy and helps safeguard the structural integrity of the overall assembly.
One interesting aspect of these screws is the readily available visual inspection afforded by the cotter pin. A simple check for a bent or missing pin quickly flags the need for maintenance or replacement. This is particularly helpful in environments where component failure could have serious repercussions, allowing for proactive maintenance before problems become severe.
Tests have consistently shown that these fasteners can endure a remarkable number of load cycles—often surpassing 100,000—before exhibiting significant degradation. This is in contrast to many standard fasteners, which can fail much sooner under repeated stressing. Such exceptional endurance highlights the suitability of these screws for situations characterized by a high number of stress cycles or applications exposed to consistent vibrations.
The hex head configuration of these screws enables the application of higher torque during installation. This ensures that the joint is properly tightened to specifications, preventing damage to both the screw and the surrounding parts. Correctly applied torque during installation is a critical factor in establishing the proper clamping force, a factor that is essential for long-term structural integrity.
Recent advances in metallurgy have led to the development of high-performance materials used in cotter pin screws. These new alloys have shown significantly improved resistance to corrosion, particularly in environments where exposure to chemicals or moisture is a concern. This enhanced corrosion resistance is important, extending the useful lifespan of these components in demanding situations.
Temperature can be a factor affecting screw performance. The brittleness of certain materials can change at lower temperatures, potentially leading to issues with screw integrity. Careful selection of the material type for the screw, taking into account the expected environmental conditions, is a crucial factor in ensuring the proper functioning of the component.
The improved stress distribution and the inherent locking mechanism of cotter pin-lockable hex head screws result in enhanced fatigue resistance in assemblies. This characteristic is especially important for parts that experience repeated and potentially varying stress levels. This benefit can be a significant advantage in ensuring the long-term reliability of various structural components.
The combination of high initial clamping force and the dependable locking provided by the cotter pin contribute to the long-term stability of the joint. This ability to maintain integrity over time makes these screws a compelling option for structural applications demanding exceptional reliability and durability. Their overall design and features demonstrate a clear focus on promoting joint integrity, emphasizing their effectiveness in applications requiring a high level of security and stability.
Analyzing the Strength and Security of Cotter Pin-Lockable Hex Head Screws in Structural Applications - Compliance with Industry Standards and Specifications
Compliance with industry standards and specifications is crucial for the successful application of cotter pin-lockable hex head screws, especially in structural contexts. These screws must meet rigorous requirements, like those found in Army-Navy standards, to ensure their performance in demanding environments. Meeting these standards not only assures a certain level of mechanical strength but also helps them resist factors like vibration and fatigue that can weaken fasteners over time. For applications where safety is of utmost importance, the specifications involved in the selection process are particularly important. They help guarantee the durability of the materials used and that the fastener can resist failure. Ultimately, thorough consideration and application of industry standards are key to ensuring the structural integrity and optimal performance of these fasteners. While the standards might seem like a hurdle, they are necessary for ensuring that these fasteners can handle the pressures of heavy use.
Compliance with industry standards and specifications for cotter pin-lockable hex head screws is crucial for their reliable use in structural applications. Organizations like ASTM and SAE establish standards through rigorous testing, ensuring these screws meet performance criteria under various loading scenarios. This focus on standardization is important for achieving consistent quality across manufacturers and applications.
The tensile strength of these screws can be remarkably high, often exceeding 150,000 psi, which is much greater than what is found in typical fasteners. This significantly improves structural integrity in situations with heavy loads. However, it's important to acknowledge that the material chosen affects this strength, and this needs to be considered when selecting screws for specific applications.
Beyond tensile strength, resistance to shear forces is also a concern in many structural applications. Cotter pin-lockable designs are specifically engineered to better resist these lateral forces compared to standard fasteners, potentially reducing the chance of joint failure under these loads. This aspect is often overlooked, but its impact on the reliability of joints can be considerable.
Corrosion is a concern for many fasteners, particularly in outdoor or harsh chemical environments. To combat this, these screws often feature protective coatings like zinc or cadmium. Testing in these corrosive environments, such as salt spray tests, reveals that these coatings can substantially extend the fastener's lifespan, potentially exceeding 1,000 hours without significant degradation. While these coatings help, they do add complexity, and it's important to consider their impact on the overall mechanical properties and cost.
Fatigue performance is a critical factor when using screws in applications subject to continuous vibrations or cyclical loads. Research shows that these screws can handle far more cycles before failing compared to standard screws, potentially doubling their functional life or more. This advantage makes them an appealing option in certain industrial applications where the screws might be subjected to numerous dynamic loads.
Proper installation of these screws is vital for their effectiveness. Applying the appropriate torque during installation is paramount as it dictates the initial clamping force and ensures components are held securely. Over-tightening can cause structural failure, while under-tightening won't provide sufficient clamping pressure. Striking a balance here is necessary to prevent problems down the line.
The field of materials science has made significant advancements in recent years, improving the capabilities of materials used in cotter pin-lockable screws. High-strength steel alloys and duplex stainless steels now offer increased performance, enabling these screws to withstand extreme loads without deformation. The continuous development of new materials is an important factor in the increasing strength of these types of screws.
The cotter pin isn't just a locking mechanism; it serves as a visual indicator of fastener integrity. Quick visual checks can alert users to potential problems that could lead to failure. This is particularly helpful in high-consequence environments where failure is undesirable.
Extensive engineering studies have consistently proven that cotter pin-lockable hex head screws significantly reduce the risk of loosening under dynamic load conditions. In some tests, they've virtually eliminated loosening, highlighting their superiority over standard fasteners in such environments. This ability is crucial for maintaining structural integrity in applications subject to vibration.
Finally, the international nature of many industrial projects requires components to comply with standards recognized globally. Many cotter pin-lockable hex head screws meet these standards, enabling their use across various markets. This widespread compliance ensures a degree of uniformity and quality regardless of where these fasteners are made. It is easy to see how this can lead to cost savings and project simplification if these fasteners can be procured from a variety of manufacturers.
More Posts from aistructuralreview.com: