Comprehensive Analysis Schedule 10 Pipe Thickness Variations Across Nominal Sizes
Comprehensive Analysis Schedule 10 Pipe Thickness Variations Across Nominal Sizes - Schedule 10 Pipe Thickness Standards for Common Nominal Sizes
Schedule 10 pipes adhere to standardized thickness specifications across a range of nominal pipe sizes (NPS). This standardization ensures consistent design and fitting within piping systems. Take, for example, a 1-inch NPS pipe in Schedule 10, which has a wall thickness of 0.109 inches. This is notably thinner than pipes in other schedules, like Schedule 40 or Schedule 80, which are built to withstand greater pressure. It's important to remember that each Schedule 10 pipe's nominal size corresponds to a specific wall thickness. While this thinner wall construction reduces weight and can be beneficial in some applications, it also limits the suitability of Schedule 10 pipes for higher pressure situations compared to thicker walled schedules. Engineers and designers must consider these thickness variations to ensure that the selected Schedule 10 pipe appropriately addresses the specific structural requirements of any project.
1. Schedule 10 pipes, characterized by their relatively thin walls, are primarily designed for applications where pressure demands are low. This thinner construction sets them apart from heavier schedules, making them a pragmatic choice when high strength or extreme durability isn't a major concern. It's interesting to see how their design prioritizes weight reduction over robust pressure handling.
2. It's crucial to note that the nominal size of a Schedule 10 pipe isn't directly equivalent to its actual outer diameter, which can be a source of confusion. Take a 2-inch nominal pipe, for instance; it has a 2.375-inch outer diameter, but the wall thickness for Schedule 10 is a mere 0.085 inches. This discrepancy highlights the need for careful attention to the specific dimensions when working with Schedule 10.
3. The wall thickness of a Schedule 10 pipe displays a relationship with its nominal size. Smaller diameter pipes tend to have relatively thicker walls than larger ones. This approach, likely driven by design optimization, seems to ensure a level of structural integrity while also minimizing material usage. It raises the question of whether this scaling relationship is perfectly optimal, or if there's room for further refinement.
4. Standards like ASTM A53 and ASTM A106 play a crucial role in defining the parameters for Schedule 10 pipes. These standards contribute to consistency in manufacturing and help ensure that pipes from different producers meet specific quality criteria across various usage scenarios. However, it's important to remember these standards represent minimum expectations, and there's still room for variation in the actual pipe characteristics depending on the manufacturer's adherence to and interpretation of these standards.
5. One clear benefit of Schedule 10 pipes is their relatively low weight. This advantage makes them easier to install and transport compared to thicker-walled counterparts, leading to reduced project costs in those aspects. It would be interesting to quantify the cost benefits over a wide range of typical projects, to better gauge the extent of their cost-effectiveness compared to alternatives.
6. The schedule number itself represents the ratio between the pipe's nominal diameter and its wall thickness. Notably, this ratio remains consistent across different Schedule 10 pipe sizes. This consistency makes design and calculation processes more straightforward and potentially less prone to error. Is this uniformity a desirable feature in all circumstances, or are there instances where a more nuanced approach would lead to better performance?
7. Applications like HVAC and plumbing systems frequently utilize Schedule 10 pipes due to the controlled flow rates and pressures inherent in these environments. However, their thinner walls limit their suitability for demanding scenarios such as industrial process piping or structural applications where stresses are significantly higher. This underscores that design choices, driven by intended use, must account for the particular operating conditions and potential hazards.
8. Corrosion resistance is often vital in certain piping systems. When using materials like stainless steel, Schedule 10 pipes can offer both adequate strength and reduced weight. This approach combines material selection with lighter construction to extend service life without compromising functionality. But, it raises the question whether we might see more innovation in coatings and other methods to enhance corrosion resistance of other materials used in Schedule 10.
9. Manufacturing processes for Schedule 10 pipes encompass both seamless and welded techniques. Each of these methods subtly alters the resulting pipe's mechanical properties and hence their suitability for different applications. This diversity offers flexibility in design choices but highlights the need for careful consideration of these nuances to ensure the chosen process yields a pipe that performs as intended. Understanding the impact of different manufacturing processes on the long-term behavior of pipes is an important avenue for future research.
10. It's easy to overlook Schedule 10 pipes due to their thinner walls when compared to other pipe schedules. Yet, their success in niche applications like fluid transport systems highlights that effectiveness in engineering can often stem from thoughtful selection and consideration of specific project requirements, rather than relying purely on brute strength or material excess. The application of Schedule 10 to innovative areas suggests that there may be a broader, yet still untapped, potential for this type of piping in applications where high strength is not always a primary constraint. It would be beneficial to study how the use of Schedule 10 in newer technologies is advancing our understanding of structural optimization in piping.
Comprehensive Analysis Schedule 10 Pipe Thickness Variations Across Nominal Sizes - Comparison of Wall Thickness Between Schedule 10 and Higher Schedules
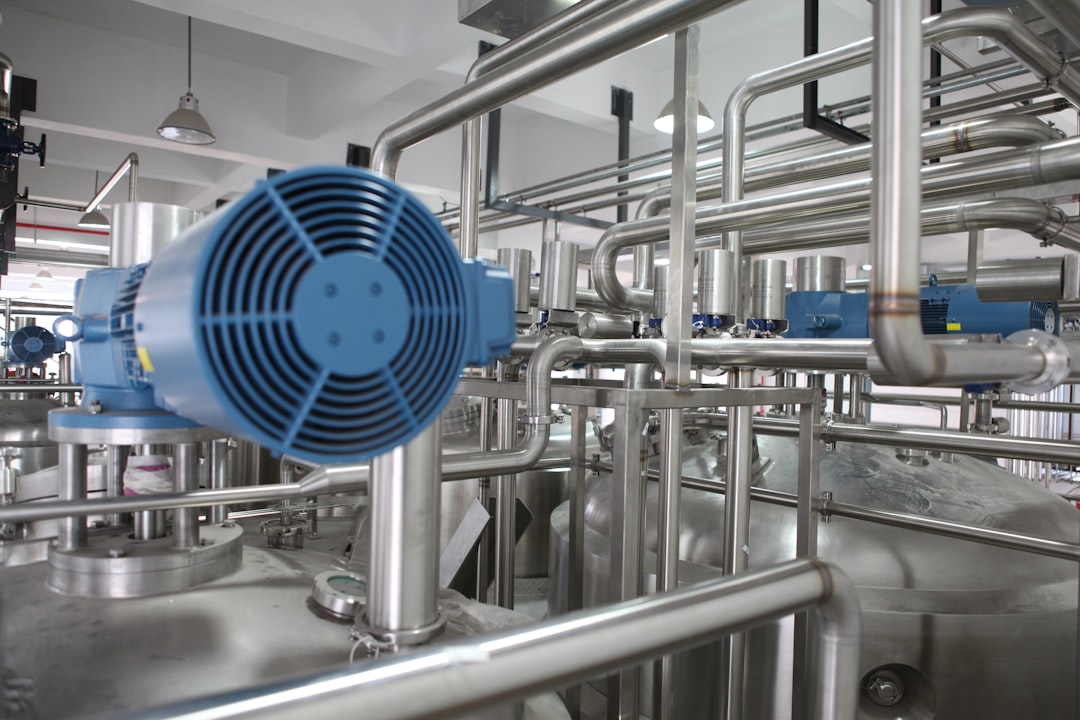
When comparing Schedule 10 pipes to those with higher schedules, such as Schedule 40 and 80, the most noticeable difference lies in their wall thickness. Schedule 10 pipes are designed with relatively thin walls, which, while reducing weight, limits their ability to withstand high pressures. For example, a 1-inch nominal pipe size in Schedule 10 has a wall thickness of only 0.109 inches. This is significantly thinner than Schedule 40 (0.133 inches) and Schedule 80 (0.179 inches) for the same nominal size.
The thicker walls of higher schedule pipes provide enhanced structural integrity and significantly improve their pressure resistance. However, this added thickness also comes with a trade-off: it reduces the inside diameter of the pipe, potentially affecting flow rates. Therefore, selecting the appropriate pipe schedule involves a careful consideration of the specific demands of the intended application. The goal is to balance weight savings with the need for sufficient structural capacity to withstand the operating conditions without compromising safety or efficacy. Failing to consider this trade-off could lead to inadequate performance and potentially dangerous outcomes.
1. While Schedule 10 pipes follow standardized wall thickness guidelines, the actual thickness varies across different nominal pipe sizes. This intriguing scaling relationship hints at a careful balance between design principles and material efficiency, raising questions about the underlying rationale behind these choices.
2. Although Schedule 10 pipes are generally associated with lower pressure capabilities, they can be useful in situations where thermal expansion and contraction play a significant role. This highlights that assessing the suitability of a pipe schedule requires considering factors beyond just static pressure ratings.
3. The substantial difference in wall thickness between Schedule 10 and other schedules, like Schedule 40 or 80, can considerably change how a piping system behaves structurally. This is particularly important when designing for dynamic loads, such as in earthquake-prone zones or environments with significant vibration. It's crucial to evaluate how the different wall thicknesses impact the pipe's ability to withstand those stresses.
4. An interesting point when comparing Schedule 10 with thicker schedules is the distribution of stress. The thinner walls of Schedule 10 can lead to higher stress concentrations around connections like welds and fittings. This requires careful design considerations to avoid potential failure in those critical areas.
5. It's a misconception that increasing wall thickness always results in a more durable pipe. Factors such as fatigue resistance and material properties are equally important. Interestingly, in some situations, Schedule 10 pipes can provide acceptable performance without the additional weight of thicker schedules.
6. The thinner walls of Schedule 10 can also make it simpler to install insulation materials. This leads to a potentially more efficient thermal performance, particularly in HVAC systems, when compared to thicker-walled pipes that might be more challenging to fit with insulation.
7. While Schedule 10 pipes have manufacturing tolerances, these tolerances can greatly affect the actual performance of the pipe. Engineers need a thorough understanding of these tolerances to ensure the final design meets specific requirements.
8. The benefits of selecting Schedule 10 over higher schedules often extend beyond just the initial purchase price. Using less material and requiring potentially less labor for installation can translate to lower overall lifecycle costs. This emphasizes the importance of understanding the long-term value of each pipe schedule.
9. When using hydraulic equations to analyze the flow within a Schedule 10 pipe, it is crucial to account for the higher flow velocities that result from the thinner walls. Increased flow velocity not only affects pressure drop but also the potential for erosion over time, necessitating careful consideration of fluid dynamics in design.
10. As industrial demands evolve and lean toward lighter-weight materials, Schedule 10 pipes might find new and innovative applications. This trend could redefine our current understanding of the strengths and limitations of traditional pipe design. It's worth exploring how the use of Schedule 10 in these newer applications might contribute to better design and engineering principles for piping systems in the future.
(October 18th, 2024)
Comprehensive Analysis Schedule 10 Pipe Thickness Variations Across Nominal Sizes - Applications and Pressure Ratings of Schedule 10 Pipes
Schedule 10 pipes, with their thinner walls compared to Schedule 40 or 80, are typically suited for low-pressure applications. These applications often involve pressures ranging from atmospheric to around 150 psi. They are frequently made from materials like stainless steel, specifically grades 304 and 316, which enhance corrosion resistance. Common uses include drainage systems, water supply lines, and irrigation. This thinner construction, though beneficial for weight and cost, restricts the use of Schedule 10 in high-pressure scenarios. It's crucial to correctly identify the appropriate pressure ratings and applications for these pipes. Engineers and designers need to ensure a suitable match between pipe characteristics and the application demands to avoid potential issues. Even though they are often overlooked due to their limitations, Schedule 10 pipes can potentially find new applications as technology evolves and the need for lightweight components increases.
1. While Schedule 10 pipes are often associated with lower pressure capabilities, it's interesting that they can be quite suitable in certain scenarios where high flow rates are needed. Their thinner walls result in a larger internal diameter, potentially leading to improved flow characteristics, as long as the pressure remains within the design limits. One might question whether this design trade-off of sacrificing some pressure resistance for increased flow is always the optimal choice.
2. It's a misconception that Schedule 10 pipes are only suitable for low-temperature applications. Depending on the material, some Schedule 10 pipes, like those made of CPVC, can withstand temperatures up to 400°F. This expands their potential applications to include hot water transport and other scenarios where thermal resistance is crucial. It begs the question of how widespread the use of high-temperature capable Schedule 10 pipes is in various sectors.
3. The reduced weight of Schedule 10 pipes can translate to considerable savings in transportation costs, especially in large-scale projects where shipping and handling are significant expenses. This can often make them a more economical choice compared to heavier schedules, even if their pressure-handling capabilities are somewhat limited. But, one needs to carefully evaluate if the cost savings outweigh potential risks associated with a lower pressure rating in the specific application.
4. Interestingly, when subjected to similar external loads, Schedule 10 pipes can demonstrate less deflection than thicker-walled schedules due to their lower inertia and flexibility. This might make them a suitable choice for applications where dynamic loads are prevalent. However, this flexibility can also introduce concerns regarding their potential for buckling under certain constraints, requiring more detailed analysis.
5. The manufacturing process for Schedule 10 pipes, particularly electric resistance welding, enables continuous production techniques, which often leads to cost reduction. This method can also contribute to tighter dimensional tolerances, reducing variation between pipes compared to other manufacturing approaches. But, it's worth considering whether these advantages are always achieved across different manufacturers and for all pipe sizes.
6. For specific chemical applications, the internal diameter of Schedule 10 pipes might be specifically beneficial. These pipes can be selected to allow for certain fluid velocities without leading to cavitation or turbulence, both of which can significantly reduce system efficiency. The optimal design for fluid conveyance needs to strike a balance between flow velocity, pressure, and material considerations.
7. Schedule 10 pipes have found their way into pharmaceutical applications, where their lighter weight and lower material cost offer advantages. This demonstrates that a thinner design can be beneficial in environments where strength requirements are manageable and other aspects like ease of handling and cost are paramount. It raises questions about whether Schedule 10 could find even wider adoption in this industry.
8. The use of Schedule 10 pipes in fire protection systems offers a fascinating example of prioritizing attributes other than pressure resistance. While these pipes might not be able to withstand extremely high static pressures, their lighter weight and ease of installation can allow for faster and more efficient deployment in critical emergency situations. The trade-offs in this application are interesting to consider in greater detail.
9. Schedule 10 pipes made of materials like PVC or CPVC are known for their chemical resistance, making them a viable option for specific applications where the fluids being transported are more important than the pressure requirements. This highlights that material selection is key to the performance of Schedule 10 pipes in specific applications.
10. The rise of modular construction has opened up new possibilities for Schedule 10 pipes. Their use in these systems shows that they can maintain structural integrity while minimizing the overall size and footprint of mechanical systems, effectively challenging traditional approaches to pipe applications. This innovation raises questions about whether these designs will inspire new approaches across other fields.
(October 18th, 2024)
Comprehensive Analysis Schedule 10 Pipe Thickness Variations Across Nominal Sizes - ANSI/ASME Standardization Method for Pipe Wall Thickness
ANSI/ASME standards provide a system for defining pipe wall thickness, ensuring consistency in pipe design and manufacturing. This method links wall thickness to the pipe's nominal size and schedule number. This system is helpful for engineers when they need to select pipes for specific pressure and operating conditions. For example, Schedule 10 pipes, known for their thinner walls, are generally suitable for lower pressure applications. However, it's vital to fully understand the capabilities and limitations of Schedule 10 pipes for proper use. The ASME standards also help to provide essential dimensions for engineering work, enabling the selection of pipes that meet the demands of an application while ensuring safety and efficient operations. As industries and technologies change, these standards are essential to address new challenges and ensure proper structural integrity in piping systems, despite varying wall thicknesses across different pipe sizes and schedules.
1. While Schedule 10 pipe wall thickness is standardized, the actual manufactured dimensions can differ slightly, which is something engineers need to be aware of when making calculations for things like pressure and flow. Failing to account for these differences could lead to miscalculations and potentially problems down the line.
2. It's interesting that even though Schedule 10 pipes are known for being lighter, their behavior in environments with a lot of vibration requires close examination. The thinner walls might make them more prone to failing from fatigue if they're constantly exposed to dynamic stresses.
3. The variation in wall thickness across different nominal sizes in Schedule 10 pipes can create unique stress patterns, especially at connections and bends. This makes it a challenge for engineers to find the best ways to design and install these pipes to prevent failures in specific spots.
4. The resistance to corrosion in Schedule 10 pipes can be different depending on what material they are made of. When using alloys like duplex stainless steel, however, the thinner walls might paradoxically make them less prone to a type of cracking that happens due to stress and corrosion because of reduced manufacturing-related stress. It's a bit unexpected.
5. The design standards for Schedule 10 pipes often restrict their use in high-pressure situations. However, when dealing with low pressures, their performance can be surprisingly similar to pipes with thicker walls, especially if the priority is high flow rates. This shows that they can be useful in unconventional ways.
6. Improvements in technology have led to better welding methods for Schedule 10 pipes, possibly boosting their mechanical strength without significantly changing the wall thickness. This makes us question some basic assumptions we have about engineering pipes with thin walls.
7. People often overlook the effect of temperature on Schedule 10 pipe performance. Though they're mostly used in lower temperatures, materials like HDPE allow them to function in environments up to 140°F, underscoring that temperature should be considered when selecting the right pipe for a job.
8. Schedule 10 pipes are sometimes favored in earthquake-prone areas due to their flexibility. Their thinner walls offer a degree of resilience that can be helpful in absorbing shock during minor quakes compared to thicker pipes, which are more rigid. This flexibility, though beneficial in some ways, may come with other drawbacks.
9. What's intriguing about using Schedule 10 pipes in fire suppression systems is how lightweight they are, which helps with quick installation. However, it's really important to carefully assess the pressure conditions to ensure they meet fire safety standards and don't compromise safety in any way.
10. As more industries move towards modular and prefabricated systems, Schedule 10 pipes are becoming a popular choice for applications that need lighter components without sacrificing structural integrity. This is prompting us to rethink the design principles of piping systems across various sectors and explore new approaches.
(October 18th, 2024)
Comprehensive Analysis Schedule 10 Pipe Thickness Variations Across Nominal Sizes - Material Density Impact on Pipe Weight Across Schedules
The weight of a pipe across various schedules, including Schedule 10, is directly influenced by the density of the material used in its construction. Denser materials, by their nature, will result in heavier pipes, even if the dimensions and wall thickness remain the same. This aspect is particularly relevant to Schedule 10 pipes, which are designed with thinner walls to minimize weight, making them a cost-effective option for lower pressure applications. However, this weight reduction comes at the cost of reduced suitability for higher pressure scenarios. Engineers must carefully weigh the benefits of lighter weight against the need for adequate strength to withstand operational conditions. The relationship between material density and weight introduces considerations for handling, installation, and overall structural integrity. These factors must be understood to ensure that pipe selection aligns with project demands and anticipated performance. There's a delicate balance to be struck here, and it's essential that the right choices are made to avoid potential complications later on.
1. The material's density plays a significant role in determining the weight of Schedule 10 pipes. Even small changes in density can result in considerable weight differences across various nominal pipe sizes, making it a key factor when optimizing for transportation efficiency, especially in large-scale projects. It's curious how such a seemingly minor property can have such a significant impact on overall system design.
2. While the thinner walls of Schedule 10 pipes contribute to a lower weight, they also make them more vulnerable to changes in material density. A slight deviation in material density during manufacturing can negatively impact the pipe's structural integrity, highlighting the necessity for stringent material quality controls throughout the production process. Perhaps this points to a need for improved consistency in the manufacturing of pipe materials to reduce the likelihood of performance variations.
3. When we consider material density, it's intriguing to see how aluminum pipes can weigh considerably less than steel pipes while still offering acceptable strength in certain applications. This observation challenges traditional material selections in pipe design, suggesting that we might be overlooking alternative materials that could provide benefits in specific contexts. There's a need to analyze the long-term performance of such alternative materials to fully evaluate their suitability for different types of projects.
4. The lighter weight achieved through thinner walls in Schedule 10 pipes can alter a piping system's vibrational characteristics. Engineers need to recognize and account for these changes as lighter pipes might be more prone to vibration-induced fatigue in certain operating environments. It seems prudent to investigate the extent to which these vibrational impacts change with varying material density and wall thickness.
5. Interestingly, the influence of material density on Schedule 10 pipe weight can also affect thermal conductivity. In some applications, the lighter pipes can lead to more rapid thermal changes, which is a critical consideration when designing systems that rely on consistent temperatures for optimal functionality. This suggests that careful thermal analysis needs to be integrated with design considerations when selecting material and schedule of pipe for certain applications.
6. The connection between density and weight also opens doors to explore new advancements in non-metallic pipe materials like fiber-reinforced polymers. These materials can significantly reduce weight while maintaining or even improving mechanical performance, posing a significant challenge to conventional pipe material use. Understanding the long-term durability and reliability of these emerging materials in real-world applications is a key area of investigation.
7. Variations in density across different pipe materials can create unforeseen cost implications. While lighter materials are generally seen as cost-effective, their different handling and installation requirements can increase manufacturing and installation expenses, underscoring the importance of a holistic cost assessment. This complexity suggests that a more thorough analysis of lifecycle costs associated with material choice is critical.
8. The emergence of advanced fabrication techniques enables innovative designs that directly manipulate material density. This allows engineers to achieve desired weight and strength profiles without strict adherence to conventional schedules, creating opportunities for customized engineering solutions. One wonders about the potential range of performance improvements with this approach and whether more projects would benefit from applying these methods.
9. Beyond the immediate context of application, the weight differences stemming from material density can impact long-term maintenance strategies. Lighter pipes might necessitate different support structures, potentially leading to adjustments in system design and influencing the overall system resilience. It's insightful to understand how the transition from heavier materials to lighter ones necessitates design adjustments to maintain structural integrity and operational efficiency.
10. Examining the effects of material density on Schedule 10 pipes encourages a broader discussion about engineering approaches. With the continuous advancements in materials science, we have the potential to develop entirely new classes of piping solutions tailored to specific weight and density requirements for specialized applications. Perhaps this is the next wave of innovation in piping systems, where we move beyond standard material selections to optimize pipe design for specific challenges.
(October 18th, 2024)
Comprehensive Analysis Schedule 10 Pipe Thickness Variations Across Nominal Sizes - Calculating Wall Thickness Requirements for Specific Applications
Determining the necessary wall thickness for specific pipe applications relies on established guidelines, such as those outlined in standards like ASME B313. These standards provide a framework for calculating wall thickness in a way that accounts for internal pressure and the material properties of the pipe, helping prevent potential failures. A key formula, which factors in internal pressure, pipe diameter, allowable stress, and joint efficiency, is used by engineers to calculate the required wall thickness. It's worth noting that while Schedule 10 pipes offer a lighter weight option for lower pressure applications, the specific needs of each project must be carefully considered to ensure safety is not compromised. The way the wall thickness varies across different nominal sizes within Schedule 10 adds another layer of complexity to the selection process, highlighting the crucial role of application-specific assessments in meeting operational requirements without sacrificing structural integrity. This meticulous approach ensures that pipes are properly matched to their intended use and designed for safe and efficient performance.
1. Schedule 10 pipes can be surprisingly useful in situations where you need high-speed fluid flow. Their thinner walls lead to bigger inner diameters, which lowers friction and improves how the fluid moves. This can be a major advantage in certain hydraulic setups, even though they're usually designed for lower pressures. It's curious how this trade-off between pressure and flow works out in practice.
2. The way Schedule 10 pipes are made has a big effect on how well they work. If the manufacturing process isn't precise, you can get variations in the wall thickness. These differences change the pressure limits and how stresses are spread out, which highlights the need for really tight quality control during production. It makes you wonder how much these variations actually impact a pipe's reliability in the real world.
3. It's kind of odd, but the kind of material used for Schedule 10 pipes can change how likely they are to break down because of stress and corrosion. Although thinner walls usually mean you can't handle as much pressure, certain materials like duplex stainless steel might actually be less prone to problems linked to stress because of how they're made. It's an interesting counterpoint to the usual expectations of thin-walled pipes.
4. If you're working with a lot of temperature shifts, Schedule 10 pipes made from materials that don't expand or contract much with temperature can be really helpful. They can handle these changes better, avoiding stresses that could lead to problems. It's interesting how this aspect is often overlooked when people are picking pipes for a project.
5. The thinner walls of Schedule 10 pipes are a real advantage in places where earthquakes are common, because they're more flexible and can handle shocks better. They're not as rigid as thicker pipes, which helps them absorb the shaking. However, this flexibility also raises worries about whether they can stand up to repeated shaking in the long run. We need to analyze this aspect more carefully.
6. It's unexpected, but Schedule 10 pipes can actually be useful in specialized fire suppression systems. Their light weight makes them fast and easy to install, and they can be configured in ways that might improve how the system works overall, as long as pressure limitations are factored in. It's worth looking at how this trade-off plays out in different fire suppression applications.
7. Contrary to what some people might think, the faster flow in Schedule 10 pipes can increase the rate of erosion. The thinner walls might not be up to the task when you're moving fluids that have a lot of particles in them. This raises concerns about whether they'll last long enough in these kinds of applications. It seems that the balance between flow rate and material erosion needs more attention in future research.
8. In newer projects that involve laying pipes sideways (laterals), Schedule 10 pipes are becoming popular because of how light they are. This makes them easier to handle and put in place, which is crucial when you're working on sloped or complex constructions. It's neat how this is changing people's views of pipes with thinner walls.
9. The relationship between Schedule 10 pipes and hydrostatic testing is an interesting one. Even though they aren't made for super high pressure, they can still be tested to see if they're sturdy enough for lower-pressure applications. This challenges what people assumed about their strength and durability. It's worth studying more about how these pipes behave under these specific tests.
10. It would be a huge step forward if we could combine Schedule 10 pipes with smart materials. By building sensors directly into the pipes, we could get real-time data on flow and structural integrity. This would make it easier to use preventative maintenance, which would be useful for keeping pipes in good shape for a long time. It's fascinating to consider the future possibilities in this area of research and design.
(October 18th, 2024)
More Posts from aistructuralreview.com: