Analyzing Water Pressure A 2024 Guide to Accurate Gauge Selection and Usage
Analyzing Water Pressure A 2024 Guide to Accurate Gauge Selection and Usage - Understanding Water Pressure Fundamentals in 2024
In 2024, grasping the basics of water pressure remains vital for managing water systems across a range of applications. Water pressure, expressed as psi or bar, is a force exerted by water within a system. It's a dynamic value, influenced by factors like the design of the system, the size of the pipes, elevation changes, and even the inclusion of valves and fittings. A solid understanding of these fundamentals is crucial when troubleshooting problems like low water flow or leaks. This necessitates the use of accurate pressure gauges, and the choice of gauge must consider factors like the anticipated pressure range and the specific environmental conditions. Modern digital pressure gauges offer advantages in accuracy and ease of use, although analog gauges continue to be relevant in certain situations. It's also important to remember that pressure readings can be affected by factors like the type of fluid or the temperature. Therefore, regular calibration and proper maintenance practices are vital for maintaining the reliability of pressure measurements, ultimately ensuring accurate assessments and effective water system management. While advancements continue, the core principles underpinning water pressure haven't changed significantly, yet a deeper understanding of these fundamentals in 2024 allows us to optimize water systems and address emerging challenges more effectively.
1. Water pressure, fundamentally driven by the weight of the water column above, reveals a direct relationship with elevation. A 10-meter increase in water height corresponds to roughly 1 bar or 14.5 psi of added pressure, a core concept in understanding fluid systems.
2. The Bernoulli principle, while mostly applied to air, also provides insight into the dynamic behavior of water. As water accelerates through pipes, its pressure decreases, emphasizing the delicate balance between velocity and pressure within a flowing system.
3. Turbulent flow, a common occurrence in many systems, leads to pressure drops and reduced efficiency. These energy losses become important to consider when designing and optimizing water transport systems, especially in high-flow applications.
4. Although the ideal gas law primarily concerns gases, water’s response to pressure and temperature variations can be understood through analogous principles. This connection reveals subtle, yet significant, implications for how engineers calculate fluid behavior under various conditions.
5. The water pressure in a residential plumbing system is not always constant. It can fluctuate due to the changing demands of a community's water usage, which often peaks in the morning during periods of high consumption.
6. Submerged objects experience increased water pressure with depth. This greater pressure can significantly affect structural integrity, especially for large underwater structures. Buoyancy and stability considerations become crucial in the design of such systems.
7. Pipe diameter and material choice directly impact the achievable water pressure. Smaller diameter pipes inherently increase frictional losses, and this friction needs to be factored into calculations for accurate predictions of pressure along the length of a pipe system.
8. Static water pressure exists in a system at rest, but the moment a valve or tap opens, this static pressure transitions to dynamic pressure. Dynamic equations are required to characterize this shift and understand the dynamic changes that take place when flow occurs.
9. Pressure gauges, often equipped with color-coded zones, provide a quick visual indicator of the operating pressure range. These color-coded zones, typically green, yellow, and red, allow operators and engineers to ensure pressure stays within safe limits and prevent problems.
10. Toilet flushing can create sudden and dramatic pressure surges in a plumbing system. Understanding and predicting these transient pressures is paramount for engineers to design efficient and robust systems that can tolerate these high-pressure events without failures.
Analyzing Water Pressure A 2024 Guide to Accurate Gauge Selection and Usage - Gauge Types and Their Specific Applications
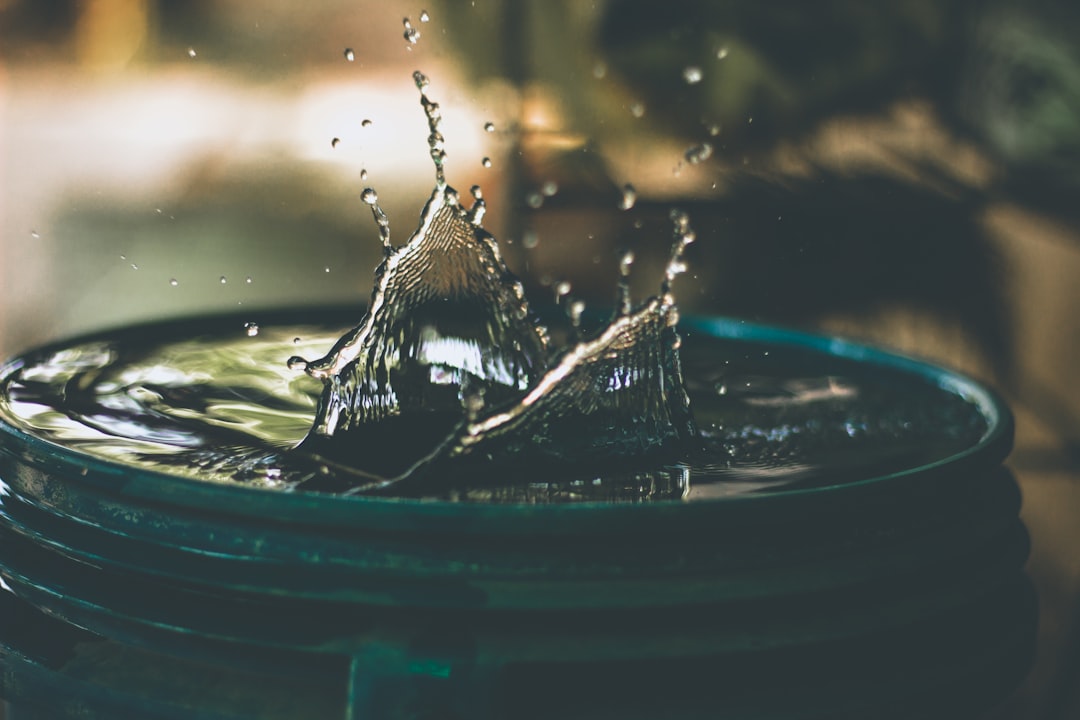
Choosing the right pressure gauge for water pressure analysis hinges on understanding the various types available and their specific applications. Mechanical gauges, like those utilizing Bourdon tubes, diaphragms, or piezometers, each have strengths and weaknesses suited to particular scenarios. The type of fluid, the operational environment, and the expected pressure range are key considerations. Selecting the ideal gauge involves a balancing act, where factors such as size, temperature range, and required accuracy play critical roles. A helpful mnemonic, STAMPED, can guide this process by highlighting essential aspects like material choice (crucial for dealing with harsh environments) and dial size (influencing readability). The importance of accurate pressure monitoring cannot be overstated. Whether in industrial settings or within residential plumbing, it directly impacts safety and system efficiency. A mismatched gauge can easily lead to inaccurate readings, potentially jeopardizing safety or creating unnecessary maintenance issues.
Pressure gauges come in a variety of types, each suited to specific applications. For instance, differential pressure gauges shine when monitoring pressure differences across a system component, like a filter. This type of gauge can help pinpoint flow restrictions and assess the efficiency of the component, which is critical for optimizing processes.
Bourdon tube gauges, a staple in mechanical pressure measurement, use the principle of elastic deformation to provide a pressure reading. They've earned their reputation for working well in challenging conditions like extreme temperatures, demonstrating robustness and reliability in diverse industrial settings.
While analog gauges hold their place, digital pressure gauges generally provide faster responses, crucial for real-time monitoring and automation tasks. In dynamic processes that demand immediate adjustments for optimal stability, the speed of these digital gauges can be very advantageous.
Some specialized gauges, like square root gauges, are engineered for specific applications like flow measurement in pipes. These types of gauges, which display readings related to the square root of the flow rate, allow engineers to finely tune a system to the exact flow conditions they need.
Gauge calibration becomes essential in situations where high accuracy is demanded. Industries like pharmaceutical manufacturing, where even slight deviations in pressure can heavily influence product quality and processing, rely on calibrated gauges.
Material selection is crucial when deploying a gauge in a corrosive environment. Engineers can use gauges constructed of durable materials like stainless steel or those with specialized coatings that can withstand these demanding conditions. This material choice becomes critical when the monitored fluid is aggressive and could potentially damage a standard gauge.
The selection between absolute and gauge pressure measurement is not trivial and impacts how readings are interpreted. Absolute pressure gauges, as the name suggests, measure pressure against a perfect vacuum, whereas gauge pressure measures pressure relative to the surrounding atmospheric pressure. Understanding this distinction becomes critical for correctly diagnosing a system's pressure behavior.
It's easy to overlook the role ambient temperature can play in gauge accuracy. Fluctuations in temperature cause expansion or contraction in the gauge materials, which can impact the precision of the readings. This can lead to misinterpretations of the true system pressure.
In systems using compressed air, for example, pressure losses due to inappropriate gauge selection or placement can easily add up to a significant amount of wasted energy. Therefore, careful selection and placement of pressure gauges in these applications is vital to minimize this problem.
Finally, high-pressure applications like those found in hydraulic systems demand gauges that can withstand immense forces. Gauges for these kinds of scenarios require special materials and engineering to function reliably and safely under pressures exceeding 10,000 psi, highlighting the need for specialized gauge designs that can withstand extreme operating conditions.
Analyzing Water Pressure A 2024 Guide to Accurate Gauge Selection and Usage - Factors Influencing Gauge Accuracy and Performance
Within the context of water pressure analysis in 2024, several factors significantly affect the accuracy and reliability of pressure gauges. Environmental influences, such as temperature changes and vibrations, can introduce errors into readings, making it crucial to consider the gauge's intended operating conditions. The gauge's construction materials are also critical; for example, mechanical gauges might struggle in extreme environments if not built with durable materials. The frequency and method of calibration are paramount for maintaining consistent and dependable pressure measurements, especially when accuracy is critical. A thorough understanding of these factors is crucial for selecting an appropriate gauge and ensuring its optimal performance in diverse applications, thus contributing to overall water system efficiency and safety. It's also notable that the specific design of the gauge, whether analog or digital, will play a role in how it functions, and the limitations of each type of gauge design should be accounted for. While some factors, like environmental conditions, are external, other factors are directly associated with the materials and manufacturing choices made in constructing the gauges, and that's not something the user can directly affect.
1. Environmental factors like temperature swings and humidity can play a significant role in how accurately a pressure gauge performs. Extreme temperatures can cause the internal components of a gauge to expand or contract, which can lead to inaccurate readings. When choosing a pressure gauge, engineers need to consider the specific environmental conditions it will be exposed to.
2. Where you place a pressure gauge matters a great deal. Putting it too close to areas with turbulent flow can result in inaccurate readings. This is due to pressure drops that happen because of friction and the swirling motion of the fluid (eddies).
3. Some digital pressure gauges have built-in smarts—they use advanced algorithms and sensors to compensate for temperature changes. This leads to much more stable and dependable pressure readings compared to older analog gauges, especially in settings where the temperature is constantly fluctuating.
4. Mechanical vibrations and impacts can really mess with a pressure gauge's ability to give you accurate readings. Engineers should think about using special mounting solutions or protective casings when a gauge is going to be in a high-vibration environment to avoid problems.
5. The lifespan of a pressure gauge isn't just tied to the wear and tear of its physical parts. Digital gauges, for example, can have issues with power supply or software glitches. This highlights the importance of having regular maintenance plans to prevent failures, especially if the gauge is used in crucial applications.
6. If a pressure gauge is exposed to pressures beyond its rated limit, it can get seriously damaged—even to the point of failing completely. When selecting gauges, engineers need to consider a safety margin and make sure the gauge can handle the maximum possible pressure.
7. Certain gauges that use both electrical and mechanical elements can provide pressure information as electrical signals. This allows engineers to monitor pressure remotely and incorporate them into automated control systems. This is a benefit that can increase efficiency across many different types of applications.
8. In situations where the flow is highly turbulent, pressure readings can change rapidly. To get a reading that's more representative of the actual pressure, engineers may need to use statistical averaging techniques. To determine the right averaging time interval, it's useful to look closely at the flow characteristics.
9. While pressure gauge accuracy is often represented as a percentage, it's important to note that this percentage is relative to the full-scale reading of the gauge, not the actual pressure range being measured. When selecting a gauge for a specific application, it's crucial to carefully examine the accuracy grade to make sure it meets the required precision.
10. For applications that require extremely precise pressure readings, such as in aerospace or medical devices, engineers often use multiple pressure gauges. This redundancy ensures system reliability in case one gauge fails. If a single gauge fails in these applications, it can lead to critical system problems, emphasizing the importance of rigorous evaluation and calibration procedures.
Analyzing Water Pressure A 2024 Guide to Accurate Gauge Selection and Usage - Selecting the Right Pressure Range for Your System
Choosing the appropriate pressure range for your water system is crucial for obtaining precise measurements and ensuring efficient operation. For the best gauge accuracy, aim to keep your system's operating pressure within the 25% to 75% range of the gauge's total scale. Ideally, the gauge's full scale should be twice the expected working pressure, providing a buffer for pressure fluctuations that are common in many systems. Factors like the gauge's construction material and its sensitivity to environmental conditions, such as temperature variations or vibrations, can influence accuracy and reliability. It's vital to select a gauge that not only meets the operational requirements of the water system but also adheres to relevant safety standards. Neglecting these considerations can result in inaccurate readings, reduced efficiency, and potentially dangerous situations within the water management system.
1. The selection of a pressure gauge can substantially affect how well a system performs. If the pressure range isn't chosen carefully, the gauge might operate in a region where its accuracy is compromised, possibly leading to incorrect calculations when designing and running the system. This underscores the importance of choosing the right tool for the job.
2. Overestimating the necessary pressure range of a gauge can lead to increased expenses since gauges designed for very high pressures often cost more. Interestingly, these high-capacity gauges might also have reduced accuracy and resolution at lower pressure levels, making them less useful for certain situations. It appears a delicate balance needs to be found.
3. The influence of atmospheric pressure variations on gauge readings is sometimes overlooked. Pressure gauges calibrated for standard atmospheric conditions can have inaccurate readings at higher altitudes, leading to reduced reliability and potentially affecting system performance. We need to carefully consider the location where these gauges are deployed.
4. The relationship between gauge selection and the specific type of piping material is often underestimated. Different materials can interact differently with pressure and temperature, ultimately affecting the lifespan and durability of the gauges used. This subtle interaction deserves more research.
5. A less-discussed aspect is that some pressure gauges exhibit hysteresis, where readings differ depending on whether pressure is increasing or decreasing. If this phenomenon isn't accounted for when evaluating system performance, it could lead to errors and confusion. The existence of this seemingly small detail highlights the need for deeper analysis.
6. In dynamic fluid systems, rapid changes in flow conditions can cause pressure spikes that occasionally exceed the maximum rating of a gauge, even if the normal operating pressure is within the accepted range. When choosing gauge specifications, it's prudent for engineers to consider these transient pressure impacts.
7. The way a pressure gauge is mounted can also impact its accuracy. For instance, vertically mounted gauges can sometimes have problems with fluid levels in their sensing elements, leading to incorrect readings. This is another factor that adds complexity to proper gauge selection and deployment.
8. Certain advanced pressure gauges have built-in self-diagnostic features that alert users when the gauge needs recalibration or if something unusual happens during operation. This capability is invaluable for avoiding costly downtime in essential applications. It's a testament to how technology can help in managing the reliability of these crucial pieces of equipment.
9. Thermal effects aren't just a concern for the internal components of gauges, as the piping materials themselves can also expand or contract, ultimately causing changes in pressure readings due to changes in the system's geometry. It's crucial to consider this geometric coupling between piping and gauge behavior when trying to assess accuracy.
10. In applications where pressure requirements vary, advanced electronic pressure gauges can automatically adjust their measurement ranges, allowing for greater flexibility and improved accuracy without needing to manually recalibrate each time the operating parameters change. This adaptable design could provide advantages in specific applications, but the long-term reliability and implications of this type of technology deserve closer scrutiny.
Analyzing Water Pressure A 2024 Guide to Accurate Gauge Selection and Usage - Environmental Considerations in Gauge Installation
Installing a pressure gauge effectively requires careful consideration of its surroundings. Environmental factors can significantly influence the accuracy and longevity of a gauge, so it's important to be mindful of them during the installation process. For example, extreme temperatures, high humidity, or exposure to dust and other particles in the air can all negatively affect the performance of a pressure gauge.
If the installation location is frequently humid, a liquid-filled gauge is often a better choice as it can help prevent condensation from forming inside the gauge and potentially affecting readings. Similarly, when selecting materials for the gauge's protective housing or enclosure (often called a cabinet), factors like stainless steel, plastic, or brass should be evaluated based on the anticipated environment, particularly if the gauge will be installed outdoors where it might be exposed to harsh weather conditions.
Understanding how these environmental factors can impact a gauge's operation is crucial to ensure the selection of a gauge that is not only appropriate for the intended pressure range but is also durable enough to withstand the environmental conditions it will face. This helps guarantee accurate and consistent pressure readings over the long term.
1. The placement of a pressure gauge during installation can significantly influence its accuracy. For example, installing a gauge near bends or valves can create turbulent flow, leading to inaccurate readings because of localized pressure drops.
2. Interestingly, pressure gauges can exhibit a phenomenon known as "zero drift," where the reading gradually shifts away from the true zero pressure point over time due to various environmental or mechanical factors. To lessen this issue, routine calibration is crucial.
3. The way a gauge is mounted can unexpectedly affect its performance. For example, horizontal mounting in certain gauges can trap fluid, potentially causing slow response times or incorrect readings.
4. The inner parts of pressure gauges, such as diaphragms, can be impacted by the fluid's chemical properties. If the fluid is corrosive, it could prematurely damage these parts, showing the need to choose compatible gauge materials.
5. While engineers typically focus on the gauge's pressure range, its response time is often overlooked. In high-speed fluid systems, a slow-responding gauge might miss sudden pressure changes, negatively impacting system monitoring.
6. It's crucial to anticipate pressure surges, particularly in systems with pump start/stop cycles. Neglecting transient pressures during gauge selection can lead to catastrophic failures, as many gauges aren't designed to handle these sudden pressure spikes.
7. The connection between gauge accuracy and the surrounding environment can be surprising. For instance, humidity can interfere with electrical gauges' sensor readings, especially in enclosed areas. This highlights the need for a thorough environmental assessment before choosing a gauge.
8. The materials used to build a pressure gauge, specifically their thermal expansion properties, are often overlooked but can lead to inaccurate readings if the system works across a wide temperature range. Engineers should factor in the thermal expansion of both the gauge and the pipe materials.
9. While some advanced digital gauges have built-in pressure compensation for factors like altitude changes, it's essential to exercise caution. Over-reliance on these automatic adjustments can mask important changes in system behavior that are better understood through direct measurements.
10. It's noteworthy that pressure gauges can be susceptible to electromagnetic interference (EMI), particularly in industrial settings where heavy machinery is present. This interference can lead to incorrect readings, suggesting the need for careful installation procedures or specialized shielding to protect the gauge.
Analyzing Water Pressure A 2024 Guide to Accurate Gauge Selection and Usage - Maintenance Practices for Long-Term Gauge Reliability
Ensuring the longevity and accuracy of pressure gauges used in water systems is paramount for reliable water pressure measurements. Proper maintenance plays a critical role in this, helping to counter the negative impacts of factors like temperature shifts, vibrations, and pressure surges that can throw off readings. It's essential that these gauges are installed with careful consideration of the surrounding conditions, as incorrect installation can lead to flawed data and potentially threaten safety. Regular calibrations and checks for any deterioration are part of a healthy maintenance regimen. Clear communication among operational staff, maintenance personnel, and management is vital to ensure preventive maintenance tasks are prioritized and consistently implemented within the operating procedures. Through a well-defined maintenance approach, the accuracy and reliability of these critical components can be safeguarded, promoting optimal performance and reduced risk within the water system. While simple to overlook, it's a necessary practice for effective water system management over the long term.
1. Maintaining pressure gauges regularly is crucial because their accuracy can drift over time. This drift can stem from factors like material fatigue or environmental influences. Ignoring maintenance can result in inaccurate readings that threaten the integrity of the system they're monitoring.
2. Calibration needs to reflect the real-world conditions where a gauge will be used. A calibration performed under ideal, standardized conditions might not ensure accuracy if the gauge later experiences significant temperature or pressure changes.
3. Mechanical shock or vibration can negatively impact pressure gauges. Not only can they impact a gauge's accuracy, but they can also shorten the gauge's life. While proper mounting techniques are a good preventative measure, their importance seems often underestimated by engineers.
4. It's a misconception to think that digital or electronic gauges don't degrade. They are susceptible to issues like power fluctuations and software problems. Implementing regular software updates and diligently checking power supply systems is important for ensuring their long-term reliability.
5. Internal parts of gauges, like seals and diaphragms, can degrade quickly in corrosive environments. This underscores the importance of material selection. Utilizing gauges designed for fluids that are corrosive can help avoid unexpected failures.
6. Some gauges struggle to respond quickly to rapid changes in pressure. This can be a problem, especially in industries that rely on oil and gas systems where pressure changes are frequent. Engineers should pay attention to manufacturers' specifications regarding a gauge's dynamic response to make sure it can handle variable conditions effectively.
7. Modern digital gauges often incorporate advanced features like automated failure alerts and calibration reminders. This proactive approach reduces the risk of catastrophic failures. However, these advanced features usually come at a higher cost compared to older, more simple designs.
8. Factors like humidity in the environment can lead to condensation forming inside the gauge, which can affect readings. Implementing protective barriers like vapor barriers or opting for liquid-filled gauges are techniques that can significantly improve accuracy in humid environments.
9. Where you install a gauge makes a difference. For example, a gauge placed at the top of a vertical pipe might not provide a true pressure reading due to trapped air pockets. Reviewing the chosen installation positions can ensure a gauge accurately reflects the actual system pressure.
10. The compatibility of a gauge with the measured fluid is critical. If the gauge isn't compatible with the fluid, there can be significant inaccuracies in the readings. This highlights the importance of thorough compatibility checks during the selection process to prevent problems later on.
More Posts from aistructuralreview.com: