Recent Updates to Garage Drywall Codes What Homeowners Need to Know in 2024
Recent Updates to Garage Drywall Codes What Homeowners Need to Know in 2024 - Type X Gypsum Board Now Required for Attached Garages
Recent changes in building codes have made Type X gypsum board the mandatory material for walls in attached garages. This shift prioritizes fire safety, particularly where the garage is connected to the living space of a home. The International Residential Code now requires a minimum of 5/8-inch thick Type X drywall on any garage wall sharing a boundary with the house. This is intended to create a robust fire barrier. Furthermore, if there are living areas built above the garage, the ceiling of the garage must also be finished with this same Type X material. It's worth noting that detached garages typically have more flexibility in their wall construction, but attached garages face these stricter standards.
While national codes provide general guidelines, local regulations can be more stringent. Homeowners undertaking projects involving attached garages need to be aware of these changes and ensure that their construction plans comply with all applicable codes, both national and local, to avoid potential issues and ensure the safety of their home.
Recent building code updates mandate the use of Type X gypsum board for walls in attached garages, primarily due to its superior fire resistance properties. This type of drywall incorporates additives that enhance its ability to withstand high temperatures and resist structural failure during a fire, a critical factor given the potential fire hazards associated with vehicles stored in garages.
The International Residential Code (IRC) has been updated to specify 5/8-inch Type X for garage walls connecting to living spaces, creating a fire separation barrier. Interestingly, the IRC doesn't have specific requirements for detached garages, allowing for a broader range of materials such as plywood or metal panels, reflecting the lower fire risk in those cases.
However, it's important to recognize that local jurisdictions may have even stricter requirements than the IRC. For instance, if habitable spaces are constructed above a garage, Type X must also be installed on the ceiling.
The increased density and thickness of Type X do contribute to its fire resistance, but it also means it's heavier, which builders should consider during framing. It's not simply about increased fire resistance; the material's composition also limits smoke and gas transmission during a fire, improving the chance of occupant safety.
Despite its fire resistance, Type X gypsum board does not inherently offer waterproofing. Therefore, if there's a risk of moisture exposure, additional waterproofing layers are necessary. Moreover, achieving optimal fire safety depends not just on the type of drywall but also on meticulous attention to details like proper sealing around outlets and seams.
While the initial cost of using Type X can be a consideration (typically between $1 and $3 per square foot), it's crucial to understand its value in terms of fire protection and potential insurance implications. Ignoring these new code requirements can not only lead to violations but also jeopardize insurance coverage in the event of a fire.
The development of Type X is fascinating, rooted in the growing need for increased fire safety as buildings became taller in the mid-20th century. This need for better fire-resistant materials led to innovation, with subsequent variants like Type C offering even higher levels of fire protection. Type X is now frequently used in various fire-rated assemblies, illustrating its wide acceptance as a crucial component in building safety.
Recent Updates to Garage Drywall Codes What Homeowners Need to Know in 2024 - Detached Garage Drywall Rules Remain Flexible
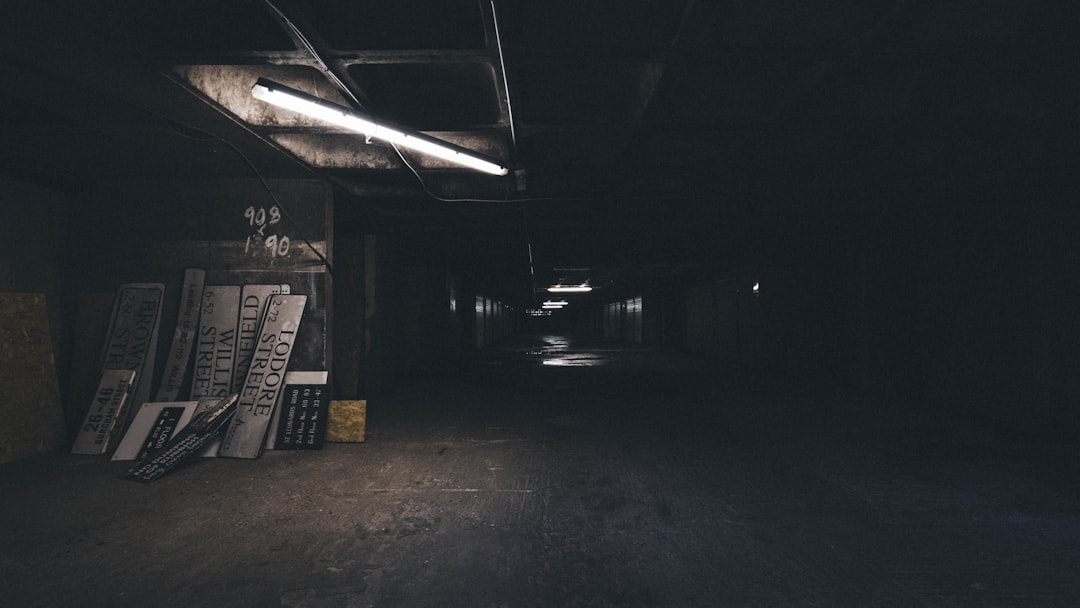
Unlike attached garages, which now face stricter drywall requirements, detached garages enjoy a more relaxed set of rules. The updated building codes, specifically the International Residential Code, focus on fire safety by mandating Type X drywall for attached garages that share a wall with living spaces. However, these stringent guidelines don't extend to detached garages. This means homeowners have more freedom when choosing materials for their detached garage walls. While standard drywall is a common choice, options such as plywood or metal siding are also viable, offering flexibility based on individual needs and project goals.
It's important to remember that local regulations can differ from the national code. Some municipalities may have their own safety standards regarding detached garages, including those near other structures or in areas with a higher risk of fire or water damage. While homeowners benefit from a wider array of choices with detached garages, aspects like fire safety, moisture resistance, and insulation are still critical elements to consider when designing and building. Ultimately, creating a safe and functional detached garage requires a thoughtful approach that balances desired aesthetics and materials with local codes and personal safety priorities.
Detached garages, unlike their attached counterparts, aren't subject to the same rigid drywall requirements. This offers homeowners a degree of freedom in material selection, allowing for the use of alternatives such as plywood or metal siding. While this flexibility can be advantageous from a cost and design perspective, it's crucial to understand that this lack of strict regulation comes with its own set of considerations.
It's often overlooked that while Type X drywall, commonly used in attached garages, offers exceptional fire resistance, it also contributes to sound dampening, which can be beneficial in garages that function as workshops or recreational spaces. This is because the additives that enhance its fire-resistance also contribute to sound insulation, reducing noise transfer between the garage and adjacent living areas.
However, while Type X provides increased fire resistance, its enhanced properties also come with a tradeoff. The increased density, about 25% heavier than standard drywall, needs to be factored into the design and framing of the garage structure. This difference in weight impacts how structural supports are engineered and installed, requiring careful consideration by the builder.
While Type X drywall can help contain the spread of fire, it's important to remember that it does not eliminate the production of harmful gases during a fire. This emphasizes the importance of proper ventilation within a garage, regardless of the type of drywall used, to prevent the buildup of smoke and hazardous fumes that can be deadly if inhaled.
A frequent misconception is that Type X inherently offers moisture resistance. It doesn't. If a garage is located in a humid area or is prone to water spills, then additional waterproofing layers are necessary to prevent material degradation and mold growth. It's crucial to remember that fire safety and material integrity are both paramount, and relying solely on Type X for moisture protection is insufficient.
Interestingly, even with the more relaxed code requirements for detached garages, the ceiling of a detached garage must still be finished with Type X if there are habitable spaces above it. This underlines a core principle in building codes—fire safety requirements are often tied to the presence of living spaces and potential exposure to people.
Another point to consider is that local building codes can sometimes impose stricter regulations on detached garages than those outlined in national codes. This highlights the critical need for homeowners to meticulously review local zoning regulations before undertaking garage construction. It's a reminder that while national guidelines provide a starting point, the final authority lies with local jurisdictions.
Home insurance premiums are often influenced by a structure's safety profile. Consequently, garages that adhere to all relevant fire safety codes, including the use of specified drywall types where applicable, might qualify for lower insurance rates. Conversely, structures that don't adhere to these standards could potentially face higher premiums or even difficulty securing insurance.
It's also important to realize that code requirements are not just about the materials used. Codes reflect an understanding of the risks associated with how people use their garages. Keeping combustible materials like gasoline cans or tools without proper storage in attached garages adds to the overall fire risk, and this risk can't be solely mitigated by using Type X.
Finally, it's fascinating to see the constant innovation in drywall technology. While Type X is prevalent, the development of even more fire-resistant panels, with the capacity to withstand flames for up to four hours, indicates the ongoing progress in the field. This pursuit of enhanced fire safety features will likely continue to impact building standards for both residential and commercial structures in the future, pushing the boundaries of fire protection and safety.
Recent Updates to Garage Drywall Codes What Homeowners Need to Know in 2024 - Three-Sided Enclosed Structures Must Meet Garage Codes
Recent building code updates have broadened the definition of what constitutes a "garage," impacting a wider range of structures. Specifically, any enclosed space with three walls and no garage door, while perhaps not a traditional garage, is now subject to similar code requirements. This means that even if a structure lacks a typical overhead door, if it's enclosed on three sides, it must meet safety standards traditionally associated with garages.
This expanded definition particularly affects attached structures where the potential for fire spread is a major concern. The use of Type X drywall in these situations is now a requirement, providing the needed fire resistance for walls shared with living spaces. Notably, attached garages are now mandated to have 5/8-inch Type X drywall. Detached garages, on the other hand, often face less rigid requirements for their walls. However, even in detached structures, the ceiling must comply with fire separation codes if it's located beneath a habitable space. Additionally, if the garage is situated in a damp or flood-prone area, moisture-resistant drywall might be necessary to protect the structure.
These updated codes highlight a growing focus on fire safety and the need to consider potential risks in all aspects of home construction. While these changes can initially seem complex, understanding the underlying reasons—fire prevention and occupant safety—can assist homeowners in making informed decisions during renovations or new builds. Ultimately, the responsibility lies with homeowners to verify local code requirements and ensure that their projects meet all applicable standards, thus safeguarding their home and property from potential dangers.
Three-sided enclosed structures, even if they don't have a traditional garage door, are often caught in a gray area regarding garage code compliance. This is because, from a fire safety perspective, these partially enclosed areas can pose similar risks to fully enclosed garages. Building codes acknowledge this, mandating that they must meet certain standards, especially when integrated with a garage structure, to mitigate potential fire hazards.
The presence of three sides alters the airflow in a way that can create problems. These structures can trap flammable gases if not properly ventilated, increasing the risk of fire. Designing for adequate airflow is critical in these situations and involves careful consideration of ventilation and insulation interactions.
Fire-resistance requirements for materials in these partially enclosed structures can differ based on the chosen materials and the overall garage design. Homeowners and builders need to carefully navigate these variations to ensure they are meeting the appropriate code standards, as a misunderstanding here can lead to safety concerns.
When evaluating the choice of materials for a three-sided enclosed structure, fire resistance becomes paramount. While not as strict as for fully enclosed garages, these structures still require fire-resistant components. However, simply choosing a fire-resistant material is not enough. How these materials interact with the surrounding structure under fire conditions is important in understanding overall structural integrity.
Regional building codes vary when it comes to three-sided structures, further complicating the issue. Local codes may reflect specific geographic concerns like increased wildfire risk or high humidity, leading to more stringent requirements. Therefore, it's essential for homeowners to understand the exact stipulations of local building codes to avoid costly penalties.
Interestingly, failing to adhere to building codes for a partially enclosed structure can have financial consequences. In addition to potential fines, insurance companies often consider compliance with building standards as a key factor in determining insurance rates and coverage. This means that non-compliant structures could face higher premiums or even difficulty in securing adequate coverage.
The dynamics of fire spread in garages with these three-sided enclosures are complex. Research using fire dynamics modeling suggests that these spaces can trap gases if poorly sealed. This further reinforces the need for appropriate ventilation, sealing, and openings.
Moreover, three-sided enclosures are not only subject to fire code scrutiny. These designs also need to factor in local seismic and wind conditions. The potential for failure due to extreme weather or seismic events needs careful consideration during the design phase.
Building codes are not static. As our understanding of building science and fire safety evolves, it's likely that regulations surrounding three-sided structures will also adapt. Homeowners and builders should be mindful of potential revisions in building codes to ensure their structures remain compliant and safe over time.
The overall picture is that partially enclosed spaces adjacent to a garage are not a simple extension of open space, but require more attention to detail from a code perspective. By understanding the interplay of fire dynamics, building materials, and local code requirements, homeowners can ensure that any three-sided structure on their property meets safety standards, protecting their investment and their family.
Recent Updates to Garage Drywall Codes What Homeowners Need to Know in 2024 - Fire Separation Wall Mandatory Between Garage and Living Spaces
Recent changes to building codes have introduced a mandatory fire separation wall between attached garages and living areas within homes. This reflects a growing awareness of the fire risks associated with garages, especially those directly connected to living spaces. To meet these updated standards, at least a half-inch thick layer of gypsum board is required on the garage side of the shared wall. If a living space is situated above the garage, the ceiling must also be upgraded, requiring a minimum of 5/8-inch Type X gypsum board. These specifications are designed to create a fire-resistant barrier capable of withstanding fire for at least 45 minutes.
It's crucial for homeowners to be aware of these updates, as they can influence insurance coverage and overall home safety. These changes are not optional; adherence to local regulations is vital for both safety and compliance. Any alterations made within these code guidelines should factor in potential impacts on insurance policies. Failing to comply with these newer building codes could result in safety hazards and, potentially, issues with insurance coverage. Ultimately, understanding and implementing these updates to garage construction standards is essential for ensuring the safety and security of a home and its occupants.
In the realm of building codes, a significant update has emerged concerning fire separation between garages and living spaces, particularly in attached garages. These changes center on the mandatory use of Type X gypsum board, which has superior fire resistance compared to standard drywall. This shift emphasizes the need for robust fire barriers, especially where the garage is directly connected to a home's living areas. The International Residential Code now mandates a minimum thickness of 5/8-inch Type X drywall for any garage wall that shares a boundary with the living space. This requirement extends to ceilings in garages if living areas are situated above them.
It's worth noting that this heightened fire safety focus is primarily for attached garages; detached garages often have more flexibility in material choices. This difference in regulations likely stems from the higher fire risk associated with attached garages due to their proximity to living spaces.
Interestingly, the building code modifications extend beyond material choices. They address issues like flame spread, smoke generation, and heat transfer. While Type X excels in preventing fire spread, it also reduces the rate of flame propagation and smoke production, giving residents more time and potentially a better chance of survival in a fire event. Moreover, Type X's lower thermal conductivity helps maintain cooler temperatures on the non-fire side, limiting heat transfer and protecting adjacent living spaces.
However, the increased weight of Type X (about 25% heavier than standard drywall) requires careful consideration during framing. Structural engineers need to ensure that the garage’s framework can adequately support the added load. This is particularly relevant in areas prone to seismic activity where the weight can influence a building’s ability to resist lateral forces.
Expanding on the updated codes, any three-walled enclosed space, whether it's a traditional garage or not, is now subject to these stricter requirements. This change essentially broadens the definition of a “garage” from a fire safety perspective. The code change aims to address the potential for fire spread in these partially enclosed spaces, emphasizing the importance of fire safety, regardless of the structure's primary purpose.
This emphasis on fire safety can influence architectural designs and construction. The update highlights that fire safety regulations are not limited to national codes. Local jurisdictions frequently enact their own regulations, reflecting their unique geographical risk profiles—such as being situated in a fire-prone area. These variations in local codes necessitate thorough examination before any garage construction or renovations.
Moreover, it's important to consider the long-term financial repercussions of non-compliance. Building code violations can lead to fines and penalties, and insurance companies often factor code compliance into their risk assessments, potentially resulting in higher premiums or difficulty obtaining insurance coverage. Homeowners would be wise to prioritize compliance to protect their financial interests.
Research into fire dynamics in these partially enclosed spaces highlights the potential for trapping flammable gases if proper ventilation is not implemented. This discovery underscores the importance of careful design and integration of ventilation features to maintain airflow and minimize the risk of fire.
The field of fire-resistant materials is continually evolving, with advancements in drywall technology yielding products with extended fire resistance capabilities. These innovations signify a dedicated effort to enhance building safety and reflect an ongoing commitment to improving fire protection standards for homes and other structures.
Beyond the selection of specific materials like Type X, proper installation techniques, such as sealing around seams and outlets, are crucial. Such attention to detail prevents the unintended spread of fire and smoke, further enhancing the overall fire safety of a garage and the entire home.
It's clear that the recent changes to garage drywall codes aim to significantly enhance fire safety in residences. By implementing Type X drywall where required, builders and homeowners are prioritizing the protection of life and property. Recognizing the evolving landscape of building codes and actively seeking information about local regulations is crucial for maintaining safety and complying with all legal standards. The constant innovation in fire-resistant materials promises to continue shaping building codes in the years to come, further pushing the boundaries of fire protection and safety in the residential sector.
Recent Updates to Garage Drywall Codes What Homeowners Need to Know in 2024 - Updated Ceiling Requirements for Living Areas Above Garages
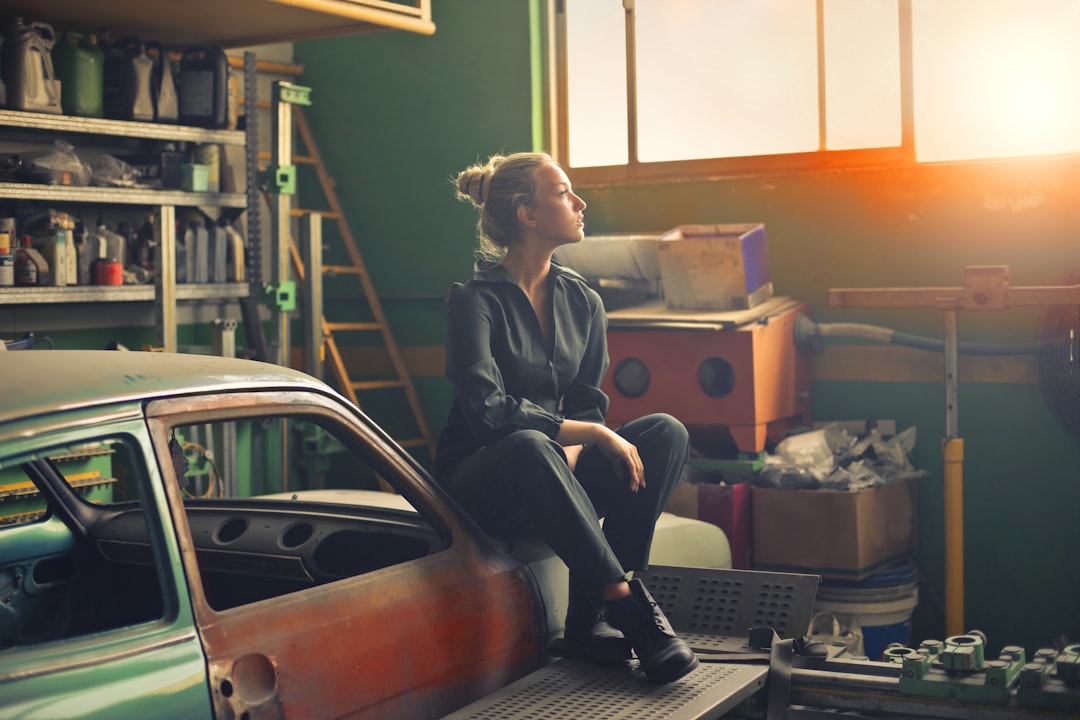
Recent building code updates have introduced new requirements for ceilings in living areas built above garages. The International Residential Code now dictates that if a garage has living space built above it, the garage ceiling must be finished with a minimum of 5/8-inch thick Type X gypsum board. This specific type of drywall is essential for fire protection, creating a barrier to prevent flames from spreading from the garage into the living areas above. Furthermore, the garage side of this ceiling/wall structure should have at least a ½-inch thick layer of drywall to help maintain fire separation. These new regulations are intended to enhance the safety of homes, and it's crucial that homeowners are aware of these changes, especially when undertaking renovations or new construction. Compliance with these codes is not just a suggestion, it is vital to help ensure the safety and structural integrity of your home.
1. **Expanding the Scope of "Garage":** The recent building code revisions have broadened the definition of a garage, now including any three-sided enclosed space. This means that structures previously not considered garages, from a code perspective, are now subject to similar fire safety regulations. This is interesting as it shows how building codes are adapting to changing construction practices and the evolving understanding of fire hazards.
2. **Extended Fire Resistance Time:** Building codes now require that the fire separation wall between a garage and living areas must withstand fire for a minimum of 45 minutes. This is a significant change, focusing on giving people more time to escape in the event of a fire, highlighting a renewed emphasis on human safety in residential design.
3. **Structural Impact of Type X's Density:** The increased density of Type X gypsum board, about 25% heavier than standard drywall, poses some design challenges. It's crucial for builders to account for this added weight in the structural framework, particularly in areas prone to earthquakes, where the load from a heavier ceiling can influence a building's resistance to lateral forces.
4. **Fire Behavior in Three-Sided Structures:** Research has shown that partially enclosed structures can trap combustible gases if not properly ventilated. This makes understanding the specific fire dynamics of such spaces crucial during the design and construction phases. It reminds us that fire safety is more than just materials; ventilation needs to be carefully considered.
5. **Ventilation as a Key Safety Element:** The importance of adequate ventilation in garages cannot be overstated. While the new codes don't explicitly say this, they imply that fire safety is about more than just the walls. It's about how the whole space is designed, and ensuring good ventilation helps prevent smoke build-up and reduces the severity of potential fires.
6. **Navigating Local Code Variations:** While the national codes provide a starting point, local building codes often impose more stringent requirements. This difference is due to the fact that local authorities may consider specific factors like wildfire risk, and it stresses the need for homeowners to thoroughly investigate the local regulations before any garage construction.
7. **The Cost of Non-Compliance:** Failure to comply with the updated building codes can result in substantial financial consequences. Beyond penalties and fines, insurance companies often factor code compliance into their risk assessment, which can translate to higher premiums or even difficulty obtaining coverage. It's an important financial motivation to follow the rules.
8. **Innovation in Fire-Resistant Materials:** The field of fire-resistant materials is constantly evolving, with new drywall products being developed that can withstand fire for extended durations. This ongoing progress is a testament to the industry's commitment to improving residential fire safety. This means there's a likelihood building codes will be updated in the future.
9. **Temperature Control with Type X:** Type X's lower thermal conductivity contributes to keeping temperatures cooler on the non-fire side during a fire event. This characteristic helps protect adjacent living spaces and reduces the extent of potential damage, enhancing overall occupant safety. It highlights that even a material's thermal properties impact fire safety.
10. **Installation Matters: The Importance of Sealing:** While Type X offers enhanced fire resistance, its effectiveness hinges on proper installation. Thorough sealing around seams, joints, and electrical outlets is essential to prevent unintended fire or smoke spread. This emphasizes that fire safety is not just about the material, but also the builder's attention to detail in execution.
Recent Updates to Garage Drywall Codes What Homeowners Need to Know in 2024 - New Cost Estimates for Garage Drywall Installation in 2024
The recent changes to garage drywall codes in 2024 have also influenced the cost of installation. Homeowners can now expect to spend anywhere from $800 to $5,000 to drywall a garage, with the final price being determined by factors like the size of the garage and the desired finish quality. The cost of labor and materials can vary significantly, with a range of $150 to $350 per square foot, and an average of roughly $2 per square foot when labor is included. It's not surprising that this cost variation exists since labor rates differ based on location, and the specific requirements for insulation and finish materials will also impact the final price. If you are considering a garage project this year, it's prudent to account for these cost factors as part of your planning. Keeping fire safety and building codes in mind during the budgeting process is crucial given the regulatory shift, especially if the project involves attached garages or habitable spaces above the garage. The combination of new codes and the varied labor and material costs make it essential to approach garage drywall projects with a clear understanding of potential expenses in 2024.
Current estimates for garage drywall installation in 2024 show a range of $800 to $5,000, influenced by factors like the garage's size and desired finish. While this range may seem broad, understanding the factors driving costs is important. For instance, the cost per square foot, including both materials and labor, can fall between $1.50 and $3.50, with an average around $2. Interestingly, a simple one-car garage typically costs between $850 and $1,100 to drywall, but a three-car garage's cost can jump considerably higher.
These costs are further affected by whether the project involves new walls or replacements, the specifics of the local market, including labor rates, and the level of finish homeowners choose. It's worth considering that if a homeowner wants a 12x12 room drywalled, costs may range from around $580 to $1,800, offering some perspective on smaller projects within the garage.
It's also worth noting that the rising cost of Type X drywall, the fire-resistant material now required in many cases, can impact project budgets. The material itself can range from $1 to $3 per square foot, and combined with the labor required for its installation, it can make a significant difference. Adding insulation to the garage walls and installing drywall is generally factored into the wider cost range of $165 to $375 per square foot when using a contractor.
Several factors are driving these cost changes in 2024. The growing awareness of the need for enhanced fire safety, particularly with attached garages, is driving an increase in the demand for Type X drywall. It is a more complex material to work with, demanding greater skill and care during installation. This heightened demand can contribute to supply chain fluctuations and drive up the overall costs.
Furthermore, the weight of Type X drywall is 25% higher than standard drywall, potentially needing modifications to the framing structure. This could increase framing costs, adding to the overall expense. The cost of non-compliance is a factor, as penalties can be incurred for ignoring newer building code requirements for safety.
These updated regulations are also likely influencing home insurance costs. Garages that meet the new code standards could receive reduced insurance premiums. Homeowners should therefore, consider the long-term costs and benefits when deciding between various material options. While the initial investment in Type X drywall might seem more expensive, it might prevent higher costs in the future due to insurance premiums and safety requirements. It's also quite possible that materials costs may fluctuate due to supply chain issues or increased demand for Type X, requiring constant monitoring as the year progresses.
It's important for homeowners to take a long-term view when making decisions about garage drywall installation, considering not only the immediate cost but also the ongoing impact on their home's safety, structural integrity, and even their insurance premiums. By factoring in the weight, labor costs, and material price changes, homeowners can make informed choices that enhance their properties while complying with the latest code requirements.
More Posts from aistructuralreview.com: