Brake Horsepower Bridging Mechanical Power and Structural Integrity
Brake Horsepower Bridging Mechanical Power and Structural Integrity - Defining Brake Horsepower in the Context of Vehicle Braking
Brake horsepower (BHP) stands as a fundamental figure for evaluating a vehicle's engine capability. This metric measures the power generated by the engine, typically taken at the crankshaft or flywheel before the power is sent through the transmission and differential. Importantly, BHP excludes the significant power losses that occur within these downstream drivetrain components, unlike power measured at the wheels which is always a lower figure. Understanding this initial measure of engine potential (BHP) is vital for engineers considering how mechanical power moves through the entire system. Analyzing BHP helps inform decisions about drivetrain design, component strength, and overall vehicle structure, highlighting the critical need to manage the flow of this power effectively and minimize inefficiencies throughout the vehicle's mechanical path.
It's rather illuminating to consider brake horsepower through the lens of actively stopping a vehicle, a perspective that often gets less attention than its use in engine output figures. During emergency braking, for instance, the instantaneous power the system is tasked with dissipating can surprisingly dwarf the peak power the engine could ever produce, highlighting the extraordinary rate at which kinetic energy must be managed.
The physical reality of this massive power management is stark: the lion's share of this 'braking horsepower' transforms directly into heat. Observing brake rotors after strenuous use reveals just how intense this process is, with temperatures often soaring well into the range where material properties become a critical design concern, easily exceeding 500 degrees Celsius during aggressive maneuvers.
To put the energy required for deceleration into relatable terms, stopping a car from open-road speeds demands the dissipation of kinetic energy equivalent to what the engine provides over several seconds of sustained full power output, but the braking system must accomplish this feat in a mere fraction of that time. This concentration of energy removal is fundamentally different from the engine's work to accelerate.
Furthermore, it's crucial to distinguish the terminology. While 'brake horsepower' in engine testing refers to power absorbed by a measuring device, in the context of vehicle braking, it quantifies the instantaneous rate at which the brake system itself acts as an energy sink, absorbing and shedding the vehicle's kinetic energy – a measure of power being destroyed or converted, rather than created.
The advent of electric vehicles introduces an intriguing complexity. Here, the braking 'horsepower' isn't solely a measure of friction-induced heat dissipation. A substantial portion of that kinetic energy can be recuperated electrically through regenerative braking, splitting the thermal load and demanding a re-evaluation of energy flow and structural implications compared to purely friction-based systems.
Brake Horsepower Bridging Mechanical Power and Structural Integrity - Early Methods for Quantifying Brake System Performance
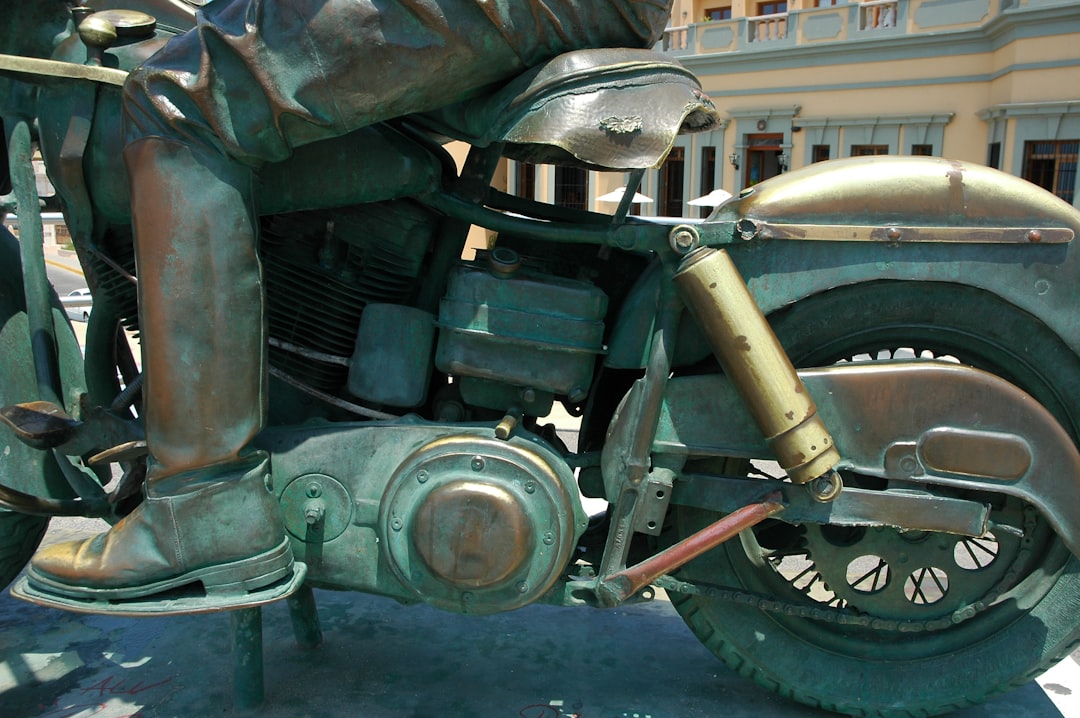
Early assessments of brake system capability predominantly relied on straightforward measurement of the forces generated and tracking the thermal behaviour under different operating conditions. These foundational tests aimed to gauge the interaction, or adhesion, between the tires and the road surface, alongside the direct mechanical effort applied by the braking components. A significant challenge quickly emerged: capturing the dynamic, fast-changing reactions of the system accurately, especially during high-stress events such as emergency stops where rapid kinetic energy management is paramount. As these testing practices evolved, it became clear that handling the considerable volume of data generated, particularly during intense evaluations like those seen in competitive motorsports, demanded increasingly sophisticated methods for analysis and representation. Nevertheless, these initial, fundamental approaches continue to shape our current understanding of brake system efficacy and its direct relevance to vehicle architecture and safety standards.
Long before the detailed transient analysis and high-speed data acquisition we employ today, the assessment of brake system capability was, frankly, rather rudimentary, relying on fairly blunt instruments. One common approach simply quantified the stopping distance from a predefined initial velocity; while straightforward, this metric was notoriously susceptible to external variables like road surface condition, ambient temperature, and even tire wear, offering little insight into the underlying brake system physics or its consistency under duress – it told you *if* it stopped, but not much about *why* or *how reliably*. Alternatively, for a more static assessment, one might test the maximum vehicle load a system could prevent from rolling on a precisely measured incline, an evaluation primarily of holding torque rather than the energy dissipation needed for dynamic stopping, a distinction perhaps overlooked at the time. For purely mechanical linkages, understanding brake performance sometimes boiled down to calculating the simple mechanical advantage provided by levers and cables, attempting to relate driver effort to theoretical clamping force, though actually quantifying the *effective* force applied at the wheel friction interface dynamically was a far more complex challenge with the available tools. Some early attempts at dynamic measurement utilized rather ingenious but basic decelerometers, often pendulum-based or simple inclinometers, which offered a single 'g' force value representing peak deceleration, a step beyond just time or distance but still a significant abstraction from the nuanced performance curve of a modern system under load and thermal stress. And perhaps most optimistically, performance was sometimes merely inferred from fundamental design specifications – factors like the total available friction material area or the diameter of a brake drum relative to the vehicle's mass, a largely theoretical exercise that assumed ideal conditions and ignored the critical dynamic effects and thermal limitations that truly define a brake system's real-world capacity.
Brake Horsepower Bridging Mechanical Power and Structural Integrity - Industry Standards Bridging Power Rating and Structural Capability
Establishing guidelines across the industry is fundamental to linking a system's power capacity with its physical resilience, particularly for vehicle braking components. These established rules provide key benchmarks for evaluating brake performance, covering crucial aspects like stopping power under varying temperatures and the system's stability during the process of absorbing energy. A significant emphasis is placed on ensuring the functional soundness of the brake system *after* it has undergone rigorous testing, underscoring the critical need for designs robust enough to endure the substantial stresses encountered when braking hard. Yet, there's a legitimate question about how effectively these frameworks keep pace with rapid technological advancements, especially given the emergence of vehicles with entirely new approaches to energy management and corresponding structural demands. As innovation continues to reshape vehicle engineering, the ongoing challenge is to develop standards that are not merely reactive to current capabilities but are agile enough to anticipate future shifts in both design and operational performance.
Understanding how industry standards tackle the connection between a brake system's power dissipation capability and its long-term structural health reveals a focus on practical endurance over isolated peak figures. It appears these guidelines prioritize testing methodologies that move beyond just surviving a single extreme event. Rather than merely focusing on headline stopping power, there's significant emphasis on how the system maintains its structural integrity and performance across repeated, high-demand stops. This focus on sustained thermal and mechanical endurance seems crucial for ensuring reliability during prolonged periods of strenuous operation.
To achieve this assessment, the standardized tests often employ rather specific, sometimes aggressive, sequences of braking events. These aren't always typical daily driving scenarios but are designed to push components hard under controlled rates of deceleration and intervals, forcing potential structural vulnerabilities to manifest reliably for assessment. It's about finding the limits predictably and repeatably.
A critical part of the evaluation, as defined by these standards, involves looking beyond the brake assembly itself. They mandate consideration of the significant, rapidly changing mechanical loads and heat loads transferred to neighboring vehicle structures – things like wheel hubs, bearings, and suspension mounting points. This underscores the necessity for a complete, integrated structural analysis of the brake's dynamic impact on the vehicle chassis, which is a more complex undertaking than just testing the brake disc and caliper in isolation.
Acknowledging that materials don't just fail from singular extremes, these standards rigorously define thermal cycling tests. They recognize that the repeated stress of heating and cooling during stops is arguably more critical for material fatigue and avoiding structural breakdown, like the formation of cracks, than merely surviving a single peak heat event. This seems a pragmatic focus on long-term durability under realistic, repeated thermal flexing.
And predictably, the arrival of electric vehicles demanded revisions. Interestingly, these standards now incorporate specialized test procedures specifically for evaluating structural integrity in EVs. This seems driven by the understanding that regenerative braking fundamentally alters how and where thermal energy and mechanical stresses are distributed throughout the system compared to conventional friction braking, requiring adapted approaches to validate component resilience.
Brake Horsepower Bridging Mechanical Power and Structural Integrity - Examining the Structural Demands on Brake System Components
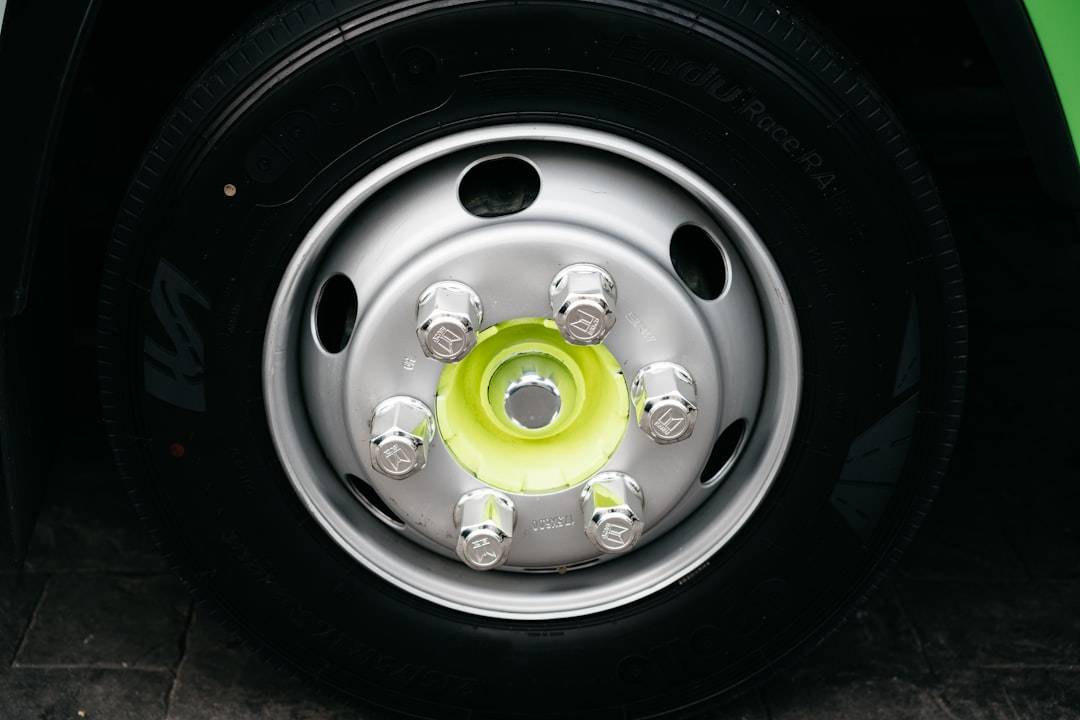
Examining the physical stresses imposed on brake system components is absolutely essential for ensuring these vital parts function dependably and safely under operational conditions. As vehicle capabilities expand, gaining a deep understanding of how these components react to the combined assault of mechanical forces and significant thermal loads becomes paramount. The sheer heat generated during aggressive braking can and does fundamentally alter material properties, presenting a genuine threat of failure if not rigorously managed through design. Therefore, a detailed structural analysis serves a critical dual purpose: identifying potential weaknesses before they manifest as failures, and providing the necessary insights to refine designs for enhanced resilience and performance in the real world. This focused attention on structural integrity takes on heightened importance as vehicle technology evolves, particularly with the introduction of electric powertrains, which bring about unique complexities in energy handling and structural stress distribution compared to traditional systems.
It is quite insightful to consider aspects of structural resilience in brake system components that aren't always immediately obvious.
One observation, perhaps counter-intuitive given their appearance, is the measurable elastic deformation within the caliper body itself when subjected to peak hydraulic pressures. This subtle 'give' under load can dynamically influence the precise alignment between the friction pads and the rotor surface during intense stops, potentially leading to non-uniform pressure distribution or momentarily altered pad contact geometry.
The hydraulic circuit presents its own structural enigma; brake lines and seals must not merely tolerate high pressures, but endure *cyclic* pressures that can regularly exceed 100 bar over their operational life. This relentless cycling imposes a significant fatigue burden, necessitating a material science approach for seals and hose reinforcement layers that prioritizes resistance to cumulative stress degradation as much as instantaneous burst strength.
Furthermore, the seemingly simple task of mounting the caliper introduces complex structural demands on fasteners and interfaces. These mounting bolts are far from just supporting a static component; they must withstand the full reaction forces of the braking torque, experiencing dynamic tensile, shear, and bending loads simultaneously during deceleration events. Ensuring the integrity of this critical joint requires preventing bolt stretch or movement that could compromise the caliper's crucial, rigid position relative to the disc.
Consider the dramatic thermal shock experienced by a fiercely hot brake rotor when it unexpectedly encounters cold environmental influences, such as splashing through standing water. The rapid, uneven cooling induces extreme thermal gradients across the disc material, generating enormous internal stresses that can, in the worst-case scenarios, trigger instantaneous structural failure through catastrophic fracture rather than just wear.
Finally, and perhaps less dramatically but equally critical in the long term, the repeated cycles of heating and cooling the brake disc undergoes during ordinary stops cause cumulative microstructural changes and fatigue. This continuous thermal flexing, even within normal operating ranges, gradually degrades the material's integrity, leading to subtle geometric distortions like warping and serving as the fundamental mechanism for the initiation and eventual propagation of fatigue cracks over the component's lifespan.
Brake Horsepower Bridging Mechanical Power and Structural Integrity - Performance Tests to Verify Structural Integrity Under Load
Central to validating a vehicle's stopping capability is conducting rigorous performance tests aimed squarely at verifying structural integrity under operational load. These evaluations delve deeper than just peak stopping power, focusing on the physical resilience of the brake system as it withstands the complex interplay of mechanical forces and significant thermal demands encountered during demanding use. Employing standardized test procedures provides a structured approach, often involving the application of cyclic loading and pushing components or entire assemblies to their limits under controlled, strenuous conditions. The fundamental objective is to ascertain that the physical components can endure not just a single extreme event, but the cumulative stress of repeated operations, thereby confirming long-term safety and functional reliability. Nevertheless, truly capturing the full spectrum of dynamic load paths and environmental thermal variability inherent in real-world driving within a laboratory test setting presents an ongoing engineering challenge.
Performance Tests to Verify Structural Integrity Under Load
Investigating the structural resilience of brake systems under operational loads necessitates employing methods that go beyond simple pass/fail criteria, probing the fundamental behavior of materials and components.
One technique involves actively 'listening' to the material under stress using acoustic emission monitoring. This isn't just about detecting outright failure; rather, it uses highly sensitive transducers to pick up the faint, high-frequency sound waves emitted by microscopic events like crack initiation or plastic deformation occurring within the material lattice well before any visible damage appears. It's a fascinating way to get early warnings from the material itself under load.
Precise optical measurement systems, such as those employing laser interferometry or high-speed digital image correlation, are often indispensable for capturing the incredibly small, dynamic deformations that occur in components like caliper bodies or mounting points during peak load applications. These techniques allow us to quantify micron-level movements and deflections that can critically influence pad-to-disc contact patterns and stress distribution, effects easily missed by less sensitive methods.
Embedding small strain gauges directly onto critical load-bearing surfaces within components, like the wheel hub interface or the bridge of a caliper, provides crucial real-time data on how mechanical stresses are distributed and concentrated during braking events. This physical measurement serves as a vital check and validation against complex finite element analysis models, revealing whether our simulated stress pathways accurately reflect reality.
Utilizing advanced infrared thermography that can 'see' through material surfaces or across component assemblies allows us to visualize heat flow pathways and thermal gradients *within* the bulk material under dynamic braking cycles. This is more than just checking surface temperature; it highlights potentially problematic internal thermal stress concentrations that aren't immediately obvious but can compromise long-term structural integrity under combined thermal and mechanical loads.
Designing structural tests that impose rapid, aggressive cycles of both mechanical loading and thermal cycling – simulating the cumulative stresses of hundreds of thousands or even millions of severe braking events within a relatively short timeframe – is a critical, if punishing, evaluation. This accelerated endurance testing forces components to confront the realities of fatigue and cumulative degradation far beyond standard use, ruthlessly exposing any latent structural weak points that might not fail in simpler static or single-event tests.
More Posts from aistructuralreview.com: