Understanding and Preventing Lack of Fusion in Structural Welding A Critical Analysis
Understanding and Preventing Lack of Fusion in Structural Welding A Critical Analysis - Root Causes of Lack of Fusion in Structural Welding
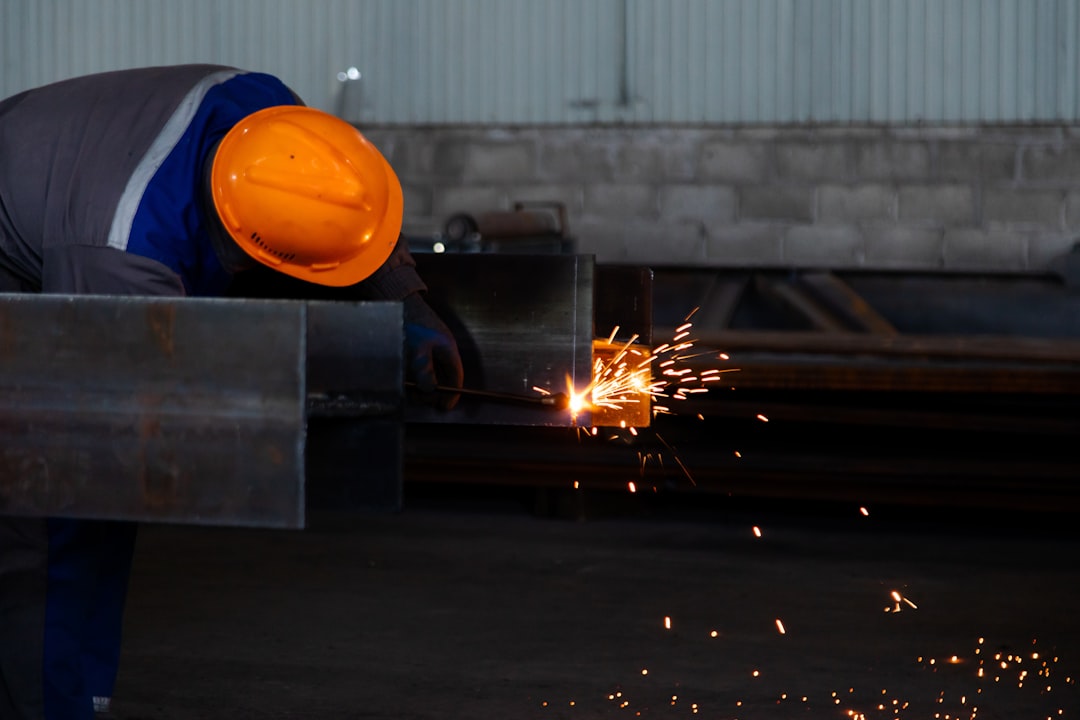
The failure of a weld to properly bond with the base metal, termed lack of fusion, represents a serious concern in structural welding. This defect can significantly weaken welded structures, threatening their overall integrity and capacity to withstand loads. A major contributor to this issue is flawed weld preparation, which can involve inadequate surface cleaning or joint design. Incorrect welding procedures and the use of suboptimal welding parameters, like voltage, current, and the amount of heat applied, also play a crucial role. The challenge becomes even greater when dissimilar metals with varying melting points are joined. This difference in melting characteristics makes achieving a strong bond at the interface difficult.
Further hindering proper fusion is the presence of contaminants on the base metal, such as rust and impurities, which interfere with the bonding process. Moreover, a crucial area of concern is lack of root fusion, where the weld metal does not adequately bond with the root of the base metal. This specific type of fusion failure can create critical vulnerabilities within the weld, jeopardizing its structural integrity. In essence, comprehending these underlying causes is fundamental for developing effective approaches that enhance weld quality and ultimately extend the lifespan of structural elements.
In the realm of structural welding, achieving a robust and durable joint hinges on the complete fusion of the weld metal with the base materials. A failure to achieve this fusion can lead to significant structural weaknesses. Inadequate preparation of the joint interface, such as a lack of meticulous surface cleaning, can introduce contaminants and oxides that impede the proper bonding of molten metal. Even the subtle nuances of torch angle and distance can impact fusion; an incorrect approach can prevent the filler metal from effectively penetrating the base metal, resulting in compromised bonds.
The thermal profile during the welding process, including excessive heat input, can affect grain structure in the base metal, creating regions less conducive to fusion with the weld. It's not only about the weld itself but also the interaction of the base metal and its inherent properties. This highlights the importance of using compatible filler materials that complement the base metals to ensure desirable melting and solidification behaviors.
Moreover, the pace at which the welding process unfolds has a direct bearing on the effectiveness of fusion. An overly rapid welding speed limits the heat input and may not provide sufficient time for proper bonding between layers, leading to areas of incomplete fusion. The arc length within the welding process also plays a role, as excessive distance between the electrode and the workpiece reduces heat transfer, hindering the desired flow and fusion of the molten metal.
Certain materials require a period of preheating before welding to address the potential for issues related to fusion and thermal stresses, especially in carbon steels. The introduction of shielding gas, while intending to protect the molten weld pool, can backfire if not properly managed. An improper gas flow can lead to oxidation, disrupting the fusion process. This illustrates how multiple factors can contribute to the formation or lack of proper fusion.
Furthermore, the differing metallurgical properties of various metals present unique challenges. When welding dissimilar metals, special procedures and techniques may be necessary due to differing melting points to ensure fusion. The challenge extends beyond the initial welding process to include post-weld procedures. Maintaining the interpass temperature is critical, as a substantial temperature drop can prevent adequate fusion during subsequent weld passes, potentially leading to flaws in the completed joint. These are but a few of the many intertwined variables that influence the outcome of a weld. This emphasizes the need for a thorough understanding of the underlying factors to create high-quality welds.
Understanding and Preventing Lack of Fusion in Structural Welding A Critical Analysis - Impact of Welding Techniques on Fusion Quality
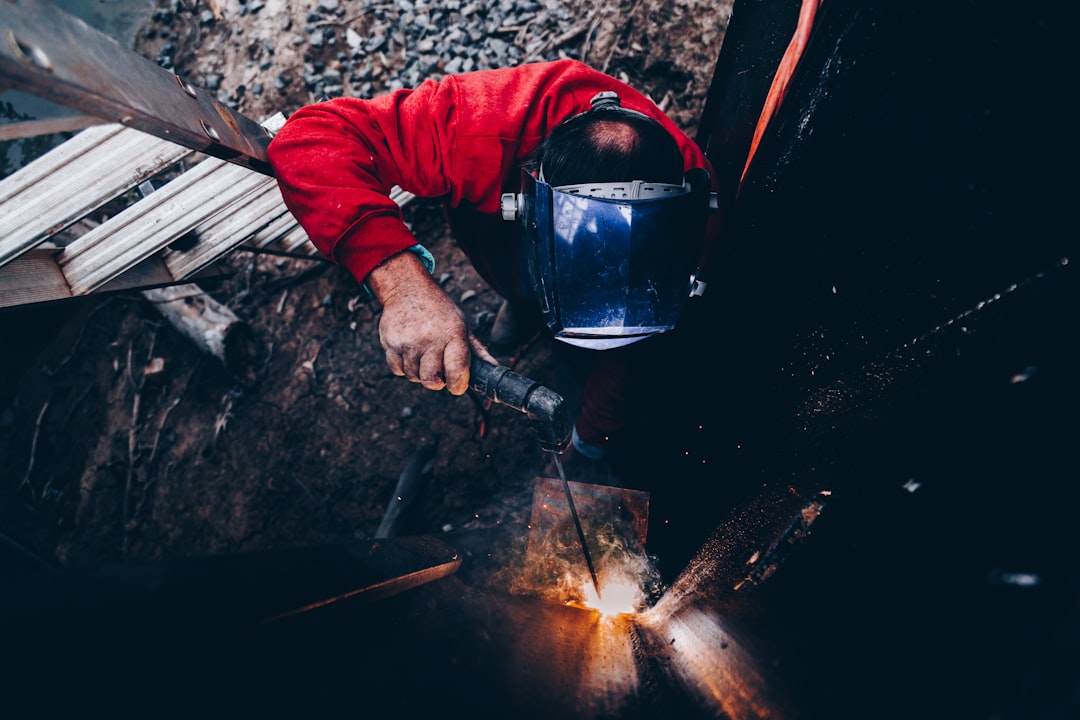
The quality of fusion, a crucial aspect of structural welding, is profoundly impacted by the welding techniques employed. The choice of a specific technique, whether it be gas metal arc welding (GMAW), submerged arc welding (SAW), or others, inherently brings its own set of operational parameters that influence fusion outcomes. For instance, GMAW, while versatile, necessitates precise control of factors such as heat input and travel speed to achieve optimal fusion. If these parameters are not managed correctly, the molten weld metal may not fully intermix with the base material, potentially resulting in a weak or discontinuous joint.
Furthermore, the preparation of the weld joint is intrinsically tied to the chosen welding technique. The effectiveness of a technique can be undermined by improper surface preparation, such as inadequate cleaning or inappropriate beveling. These shortcomings can introduce contaminants that interfere with fusion, compromising the strength and integrity of the joint.
The selection of compatible materials, including the filler metal and base metals, is another important consideration. A welding technique may excel in joining specific material combinations, but failure to carefully choose suitable materials can lead to undesirable fusion outcomes. Dissimilar metals, for example, often necessitate a specialized welding technique and material selection to manage differences in melting points and thermal expansion characteristics. This intricate relationship between the technique and material choice highlights the need for comprehensive understanding to avoid compromising fusion quality.
Ultimately, the success of achieving proper fusion relies on the combined interplay of technique, weld preparation, and material selection. Neglecting any one of these components can result in imperfections in the fused joint, jeopardizing the long-term structural integrity of the weld. A deep comprehension of these factors is therefore essential for preventing potential failure and ensuring robust, durable welds in structural applications.
The choice of welding technique significantly impacts the quality of the fusion between the weld metal and the base material. Techniques like Gas Metal Arc Welding (MIG), Gas Tungsten Arc Welding (TIG), and Shielded Metal Arc Welding (SMAW) each generate unique thermal profiles and cooling rates. For instance, the rapid cooling associated with MIG welding can alter the microstructure, potentially weakening the fusion interface.
The properties of the heat-affected zone (HAZ) can be considerably altered by the welding technique employed. Changes in grain structure within the HAZ can produce regions that don't readily bond with the weld metal, leading to areas of weakness. The composition of the electrode or filler material itself plays a role in fusion quality. SMAW electrodes, for example, may not deliver adequate fusion in high-strength steels due to their lower alloy content and melting characteristics when compared to other electrode types.
Welding speed is another critical factor impacting fusion. Faster welding speeds decrease heat input and may not allow sufficient time for the weld metal to properly bond with the base metal. Research suggests that optimal welding speeds are technique-specific, demanding precise control to ensure complete fusion. The type of shielding gas used, such as Argon or CO2, is also crucial in maintaining the integrity of the molten weld pool. Incorrect gas mixes can shift the oxidation levels within the weld pool, potentially interfering with proper fusion and potentially affecting the mechanical properties of the final weld.
The design of the joint itself can influence fusion quality. Complex joint geometries may necessitate specific welding parameters and techniques to ensure that the weld metal reaches all critical areas, especially in multi-pass welds where layers of weld material are applied. For multi-pass welds, maintaining an appropriate temperature between passes is critical. If the temperature falls too dramatically between passes, fusion may not be adequate. Furthermore, rapid cooling can introduce internal stresses that can promote cracking.
Some materials, particularly those with a high carbon content, require preheating prior to welding to lessen thermal shock and promote improved fusion. Without preheating, the rapid cooling associated with welding can hinder proper melting and bonding of the base material. The resulting welds might exhibit increased susceptibility to lack of fusion.
The welding technique has a clear influence on the metallurgical responses of both the base material and filler metal. These changes directly impact the mechanical properties of the welded joint. In critical structural applications, this variation can lead to a reduction in the overall strength and load-bearing capability of the weld. Welding dissimilar metals presents unique challenges associated with varying melting points and thermal expansion rates. In such cases, laser welding, for instance, can offer superior fusion, highlighting the importance of careful technique selection to achieve a desired outcome.
This intricate interplay of variables underscores the importance of understanding the impact of welding techniques on fusion quality. The ability to control and manipulate these factors, through proper planning and execution, is crucial for minimizing the likelihood of fusion defects and ensuring the structural integrity of the finished welds.
Understanding and Preventing Lack of Fusion in Structural Welding A Critical Analysis - Liberty Ships Failure A Case Study in Weld Integrity
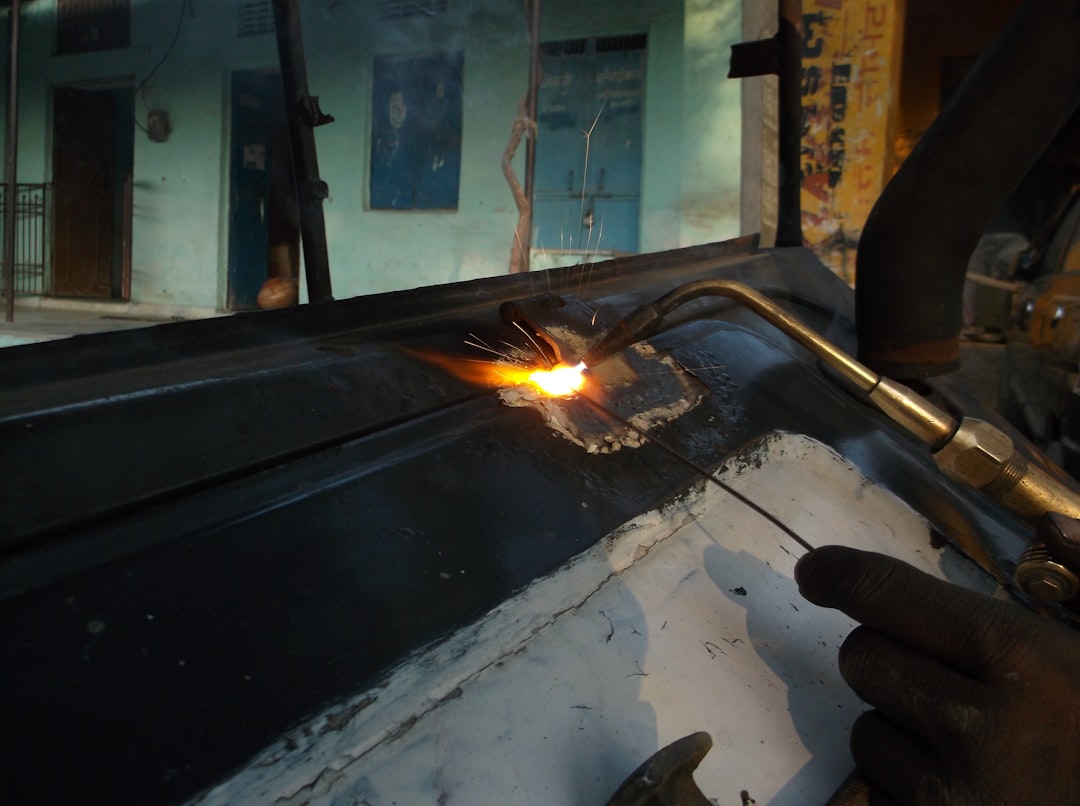
The Liberty Ship program, a massive wartime shipbuilding effort, revealed a significant flaw in weld integrity and its implications for structural safety. Despite the rapid construction of nearly 2,700 ships, a large portion encountered severe cracking, with some even breaking in two, leading to both ship and human losses. The failures, costing the U.S. millions of dollars, pointed to a brittle fracture mechanism, which was unexpected given the type of steel used. It became clear that the composition and microstructure of the steel played a pivotal role in the susceptibility to failure.
These failures weren't just isolated events. They highlighted a widespread problem across a substantial number of welded merchant ships. This unfortunate experience spurred advancements in understanding brittle fracture mechanics and the transition temperature characteristics of steel. The Liberty Ships became a poignant lesson in the necessity of establishing toughness standards for welded structures, particularly those exposed to varying temperatures. The lessons learned from the failed ships contributed to the development of fracture mechanics as a field of study and influenced engineering practices for decades to come.
Furthermore, the Liberty Ship failures revealed the potentially detrimental effects of rushing the construction process, even under extreme circumstances. Compromises in welding quality and structural integrity occurred, highlighting the need to balance speed and quality in shipbuilding and other critical industries. The Liberty Ship failures remain a crucial case study in welding and emphasize the importance of maintaining the highest standards of weld quality to prevent similar occurrences in the future. It underscores the continuous need to evaluate material selection, welding procedures, and inspection practices within structural engineering.
The Liberty Ship program, a monumental shipbuilding effort during World War II, saw the construction of roughly 2,700 vessels in just six years to support the war effort. However, this rapid pace came at a cost. Many of these ships experienced catastrophic failures, with some even splitting in two, resulting in substantial loss of life and materials, with estimates of US$50 million in damages. Of the roughly 5,000 welded merchant ships constructed during the war, over 1,000 suffered various degrees of cracking, highlighting a widespread issue with weld integrity.
These failures were primarily attributed to a brittle fracture mechanism, a phenomenon that was unexpected given the materials' presumed ductile nature. A closer look reveals that the steel composition and its resulting microstructure played a critical role in the material's susceptibility to failure. These factors were key in controlling the mechanical properties, ultimately impacting the fracture performance.
The severity of these failures spurred advancements in understanding brittle fracture mechanics and how the temperature impacts the ductile-to-brittle transition in steel. Examining the Liberty Ship failures highlighted the importance of defining toughness requirements in welded structures, especially when considering the impact of fluctuating temperatures on the structural integrity.
Post-mortem analysis of the failed ships was pivotal in developing the field of fracture mechanics, influencing future engineering practices. The urgent need to produce these vessels quickly resulted in some compromises in welding quality and overall structural integrity. This situation clearly demonstrates the potential consequences of hurried production under emergency conditions.
The study of Liberty Ship failures has served as a critical case study in weld integrity, emphasizing the importance of robust welding processes in structural applications. The lessons learned from these incidents have been integrated into modern shipbuilding, leading to improvements in structural welding practices, with a focus on preventing similar failures in future projects. This demonstrates the enduring importance of analyzing failures to refine engineering design and practice. The speed of production and a desire to rapidly field a large number of vessels introduced compromises in quality control, particularly related to welding integrity and fusion. This has led to a better understanding of the importance of careful material selection and robust welding techniques. In retrospect, the failures of Liberty Ships provided valuable insights that continue to influence how structural welds are designed, inspected and implemented.
Understanding and Preventing Lack of Fusion in Structural Welding A Critical Analysis - Safety Implications of Weak Welds in Structural Applications

The presence of weak welds in structural applications presents a serious safety hazard. These weaknesses stem from the potential for compromised structural integrity, making the entire structure vulnerable to failure under normal or unexpected stress. Lack of fusion, a condition where the weld doesn't fully bond with the base metal, is a key cause of weak welds. Factors like improper heat management during the welding process, insufficient joint preparation, and substandard welding techniques all increase the likelihood of fusion issues. This can lead to flaws within the welded structure that can have severe consequences.
Furthermore, structural elements constructed from welded steel are uniquely prone to issues like fatigue and corrosion, issues that can be significantly worsened by compromised weld quality. The combined impact of weak welds, lack of fusion, and susceptibility to environmental factors like corrosion creates substantial safety concerns. It's critical that thorough inspections and quality control procedures are part of the structural welding process to identify and correct weld defects before they lead to failures. Early identification and repair can help ensure the long-term safety and integrity of structures that rely on welded components.
Compromised structural integrity and premature failure under stress are major safety concerns associated with weak welds. These weaknesses often act as stress concentrators, leading to localized failures that can quickly escalate into catastrophic events under load. Lack of fusion, where the molten weld metal doesn't fully bond with the base material, significantly contributes to this issue. Factors like improper heat control, overlapping welds, and inadequate fusion at the weld toes and roots can all lead to these problematic welds.
Furthermore, lack of fusion raises the likelihood of fatigue failures, as the resulting stress concentrations are subjected to repeated loading. These stresses can cause surrounding material to crack and ultimately fail over time. It's important to remember that even with advanced welding technologies, lack of fusion remains a substantial cause of structural failures, highlighting the continuing need for stringent quality control during the welding process.
The way welding parameters interact with material properties can create unforeseen vulnerabilities. For example, high-strength steels, due to their sensitivity to heat input and thermal distortion, are particularly prone to lack of fusion. Materials with significant thermal expansion differences are also susceptible to fusion problems, as different contraction rates during cooling can result in voids or cracks at the weld interface. This is a recurring theme in welds that combine different metals, where careful thermal management is critical.
Nondestructive testing techniques, like ultrasonic and radiographic inspections, are essential for identifying fusion defects early on. These methods allow us to detect internal flaws that are invisible to the naked eye but can create major safety hazards. Poor welding techniques and incorrect settings can lead to a lack of weld penetration, which can cause a specific failure mode in alloy steels called lamellar tearing. This occurs when stresses are applied parallel to the weld plane, leading to material separation along the layers.
The welding environment itself can amplify the effects of lack of fusion. For instance, humidity and temperature fluctuations can cause porosity in the weld, further weakening the bond. This further emphasizes the importance of environmental considerations during the welding process. Historical data shows a significant positive impact from regular maintenance and inspections in reducing lack of fusion defects. These findings stress the value of not only excellent initial welding but also continuous monitoring of weld integrity.
Achieving complete fusion becomes even more challenging in multi-pass welding techniques. The thermal impact of each weld pass on previous layers can create a cascade of issues. Failure to maintain proper interpass temperatures can lead to poor fusion in subsequent weld passes, increasing the risk of failure in the finished structure. The interconnectedness of factors across the welding process requires a nuanced and thorough understanding to ensure weld integrity and prevent unexpected failures.
Understanding and Preventing Lack of Fusion in Structural Welding A Critical Analysis - Non-Destructive Testing Methods for Fusion Verification
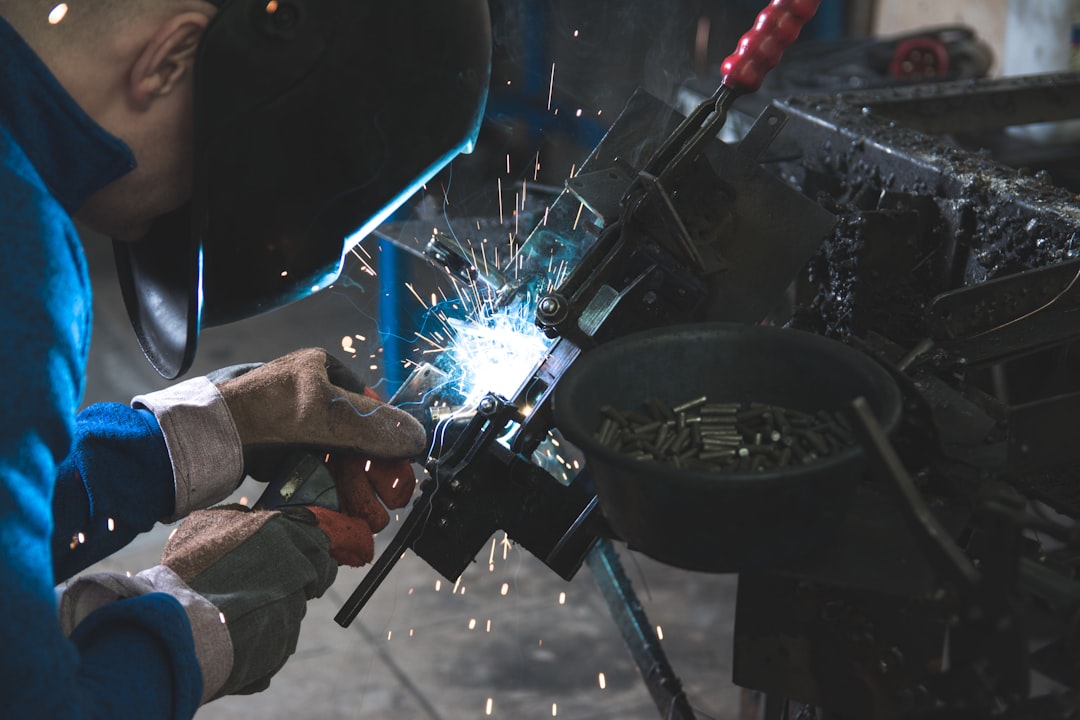
Non-destructive testing (NDT) plays a vital role in verifying the quality of welds, particularly in identifying defects like lack of fusion. This type of defect, a planar discontinuity, can be difficult to detect using traditional methods, making advanced NDT techniques like ultrasonic testing and radiography especially valuable. As welding processes become increasingly complex, involving diverse materials and advanced welding procedures, the need for accurate and reliable NDT grows. The evolution of image fusion and the combination of different NDT methods is improving the reliability and precision of defect detection, especially for smaller, harder-to-find flaws. Developing and using a robust NDT strategy is important for ensuring the long-term safety and structural integrity of welded components. Ultimately, the effectiveness of NDT is crucial for advancing quality control measures in welding and bolstering confidence in welded structures.
In the realm of structural welding, understanding the complexities of phase transformations during the cooling phase after welding is critical. Rapid cooling can lead to a martensitic transformation, potentially causing brittleness and weakening the weld joint. This emphasizes the need for carefully controlled cooling rates to optimize the weld microstructure and minimize the chances of fusion defects.
While ultrasonic testing is a valuable NDT tool, it has limitations when it comes to detecting lack of fusion. These defects often occur at the weld interface, making it difficult to reliably distinguish between acceptable and unacceptable fusion levels. The signal interpretation becomes challenging, which may lead to missed defects or misinterpretation of the data.
The thickness of the oxide layer on the base metals can also interfere with NDT results. An excessive oxide layer can significantly impact the accuracy of ultrasonic readings, potentially masking actual fusion issues. Careful surface preparation before welding is essential to minimize these complications and ensure reliable NDT results.
Multi-pass welding presents additional challenges in detecting lack of fusion. Each weld layer can affect the temperature distribution of the preceding layer, complicating the inspection process. Poor control over interpass temperatures can result in incomplete fusion during subsequent passes, potentially leading to hidden defects. These complexities necessitate comprehensive and precise NDT strategies.
Although radiographic testing is good at finding voids or inclusions, its application in detecting lack of fusion has limitations. It's difficult to differentiate between incomplete fusion and acceptable weld structures with similar density profiles. The use of radiography to check for fusion in some materials may not be practical and it may be challenging to interpret the radiographic image.
Maintaining the correct thermal profiles during welding is paramount in avoiding lack of fusion. Carefully controlling the heating and cooling phases prevents the development of temperature gradients that impede bonding. Accurate temperature calibration is crucial in preventing variations that can compromise fusion.
NDT methods need to be tailored to the specific materials and welding process. For instance, magnetic particle testing is not effective for non-ferrous materials. Choosing the appropriate NDT method for a particular welding situation is crucial for maximizing the chance of detecting defects.
Lack of fusion can lead to unexpected crystal structure alterations at the weld interface, potentially generating stress concentrations that initiate cracks under load. These localized structural variations often require more advanced NDT imaging to be revealed.
The design of the welded joint itself can influence the effectiveness of NDT methods. Certain joint configurations can hinder access and prevent a clear view of the weld, making it challenging to detect lack of fusion. It's best if the weld joint design takes into account the anticipated welding process and chosen NDT methods.
Training is paramount in preventing lack of fusion and ensuring proper weld integrity. Welders and inspectors need proper training and knowledge in welding and inspection techniques to be able to identify fusion issues and implement effective NDT methods. Skill in interpreting the data produced by the NDT methods is critical to minimize human errors and increase the accuracy of the defect detection process. The lack of trained inspectors and weld technicians is an issue across many industries where welding plays a crucial role in the construction of manufactured components.
Understanding and Preventing Lack of Fusion in Structural Welding A Critical Analysis - Preventing Lack of Fusion in High Strength Steel Welding
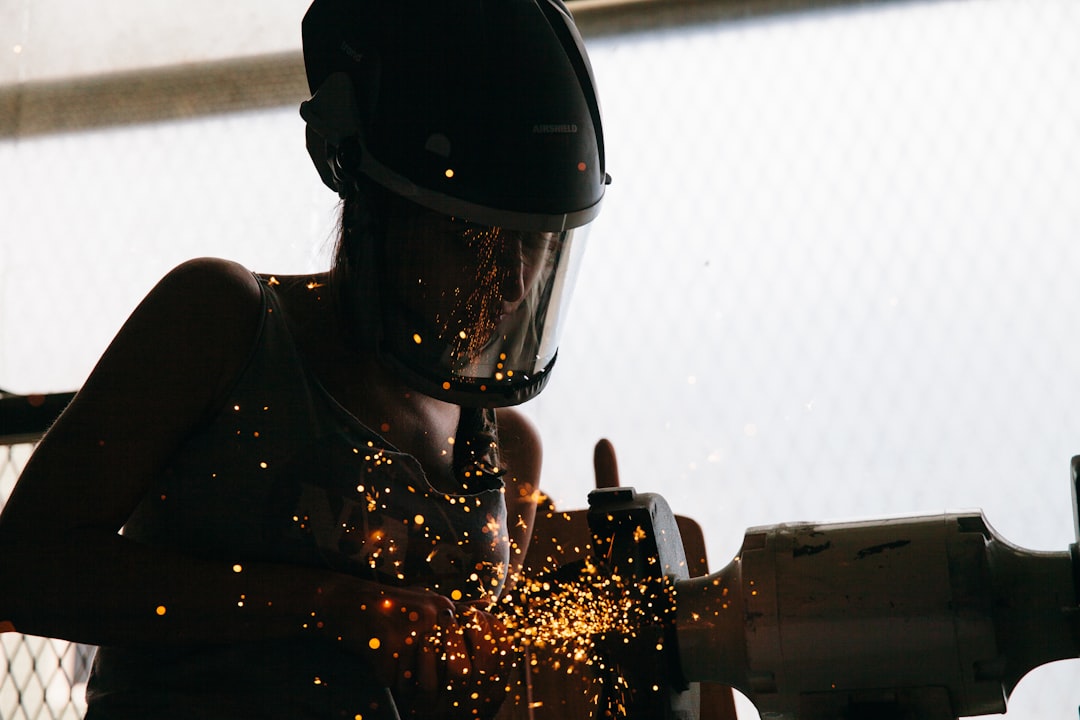
High-strength steel welding demands meticulous attention to prevent lack of fusion, a defect that severely compromises structural integrity. Achieving optimal fusion in these materials requires careful consideration of welding techniques and parameters. Incorrect heat input, for instance, can be particularly detrimental, leading to incomplete bonding of the weld to the base metal. Furthermore, using incompatible filler materials can worsen the issue, making it harder to achieve a strong bond.
Certain techniques, such as employing metal-cored arc welding with a rotating electrode, can help address challenges related to thick sections of steel, allowing for consistent heat distribution and deeper penetration. Innovative approaches like ultrahigh-power laser welding can offer solutions for specific high-strength steel types, particularly when dealing with thicker sections.
Thorough surface preparation is also non-negotiable in preventing fusion issues. Impurities and contaminants, such as rust, present on the steel surface can impede proper bonding. Removing these impurities before welding is essential for ensuring that the molten weld metal can adequately intermix with the base metal.
Continuous monitoring and adjusting of welding procedures throughout the process can also be beneficial for maximizing the likelihood of a quality weld. This involves adjusting parameters in response to any deviations that may occur during welding. The goal is always to achieve complete fusion, reducing the potential for structural failures later on. Without proper attention to these critical aspects, high-strength steel structures can be left vulnerable, risking failure under load.
High-strength steels present unique challenges when it comes to preventing lack of fusion during welding. Their sensitivity to heat input means that excessive heat can soften the heat-affected zone (HAZ), making it harder for the weld metal to form a robust bond and increasing the likelihood of incomplete fusion. Furthermore, the cooling process after welding can induce significant thermal distortion in these steels, leading to the formation of voids or gaps at the weld interface. This highlights the importance of carefully controlling cooling rates to minimize these issues.
The presence of even a thin oxide layer on the surface of the steel can act as a barrier, significantly impacting fusion. Thorough surface preparation, removing oxides and impurities, is crucial for achieving proper fusion, especially when dealing with high-strength steels. The design of the weld joint also has a major role in fusion quality. Joints that restrict access or are inherently complex can lead to incomplete penetration and fusion issues, particularly in hidden or multi-pass welds.
Maintaining consistent interpass temperatures is critical for multi-pass welds. A drop in temperature between passes can hinder the fusion of subsequent weld layers, increasing the chance of incomplete fusion and potential defects. Welding speed also plays a crucial role. Rapid welding speeds often don't allow enough time for the weld metal and base material to bond adequately, particularly in high-strength steels, where precise control over travel speed is necessary to prevent problems.
While nondestructive testing (NDT) methods like ultrasonic testing can help identify defects, they can struggle to accurately detect lack of fusion, especially those occurring at the interface between the weld and base metal. Skilled interpretation is crucial to minimize misdiagnosis and ensure reliable defect identification. The specific chemical composition of a high-strength steel has a direct impact on its welding behavior. Variations in alloying elements can affect melting characteristics and lead to a greater possibility of incomplete fusion. Therefore, careful material selection is paramount.
Post-weld heat treatment can sometimes improve or correct instances of incomplete fusion but needs to be performed with a detailed understanding of the specific steel. Applying heat incorrectly can actually make matters worse, underlining the importance of matching the treatment to the steel's specific properties. Finally, the quality of the base materials used can directly affect fusion outcomes. Variations in steel properties from suppliers can lead to unexpected welding challenges, highlighting the importance of consistent quality assurance throughout the supply chain, right from material procurement.
It seems clear that high-strength steels present a complex set of issues when attempting to achieve proper fusion, particularly as the steels become stronger and more alloyed. The range of factors affecting the final weld is broad, and it remains a challenge to ensure high quality welds without advanced planning and knowledge.
More Posts from aistructuralreview.com: