Cellular Glass Pipe Insulation A Comprehensive Analysis of Thermal Performance and Durability in Industrial Applications
Cellular Glass Pipe Insulation A Comprehensive Analysis of Thermal Performance and Durability in Industrial Applications - Thermal Performance Range of Cellular Glass Pipe Insulation
Cellular glass pipe insulation, like FOAMGLAS, demonstrates a significant operating temperature window, spanning from 450°F to 900°F (268°C to 482°C). This wide range allows it to effectively manage heat in a variety of industrial applications. The material's thermal conductivity, measured at 0.036, positions it competitively against other insulants such as mineral wool. This performance is attributed to the unique structure of the insulation – millions of hermetically sealed glass cells. This cellular structure also provides inherent advantages like moisture resistance and non-combustibility, crucial factors in safety-sensitive environments. Furthermore, adhering to industry standards like ASTM C552 ensures quality and reliability, a key concern when thermal performance is critical for process efficiency and safety. While achieving certain pipe insulation designs may necessitate specialized fabrication, the overall impact of this type of insulation is its ability to consistently deliver thermal performance even in high-stress industrial situations.
Cellular glass pipe insulation exhibits a noteworthy thermal performance range, spanning from cryogenic temperatures, as low as -268°C, to high-temperature industrial applications up to 430°C (or 800°F). This broad range opens up possibilities in diverse applications, from handling extremely cold liquids to environments where heat is a major consideration.
Its closed-cell structure is crucial in ensuring minimal water absorption, unlike some other insulants that may lose effectiveness when moisture gets into them. While moisture infiltration can significantly degrade thermal efficiency in some materials, cellular glass maintains consistent insulation performance.
The thermal conductivity of cellular glass tends to fall within a narrow band, usually between 0.035 and 0.060 W/m·K. This places it alongside more established insulants like mineral wool in terms of thermal resistance. It's interesting to observe how this aligns with other materials, raising questions about the potential advantages and disadvantages in specific situations.
A significant aspect of cellular glass is its thermal stability. In contrast to certain insulants that degrade over time or with consistent exposure to heat or temperature shifts, cellular glass exhibits excellent durability. It maintains its thermal efficiency even under rigorous conditions, indicating a promising characteristic for long-term insulation projects.
One of the significant benefits is its inherent non-combustibility. Since it's entirely inorganic and doesn't support combustion, cellular glass provides a reliable thermal barrier in settings where fire safety is paramount. Further, it doesn't release hazardous fumes when exposed to high temperatures, unlike some organic materials that can create harmful off-gassing.
Temperature fluctuations and cycles are often detrimental to certain insulating materials. However, cellular glass demonstrates remarkable resistance to dimensional changes, meaning it does not shrink or warp under changing temperatures. This consistency is valuable in applications where maintaining insulation effectiveness throughout a structure's service life is important.
The inherent lightness of cellular glass insulation is advantageous when considering installation. Its rigid structure means it requires less mechanical support, potentially streamlining and reducing the costs of installations, especially in large industrial applications.
Production methodologies influence the density of cellular glass, allowing manufacturers to adjust properties to suit specific engineering specifications. This ability to fine-tune thermal performance and mechanical strength is a key advantage when it comes to fitting the insulation to the exact needs of a given project.
The remarkably low thermal expansion coefficient of cellular glass offers advantages in situations with significant temperature variations. It is important to keep in mind that thermal expansion is critical in some designs, and this property can reduce or eliminate some mechanical challenges.
The initial purchase cost of cellular glass insulation might be higher compared to alternative materials. Yet, this is counterbalanced by its incredible longevity and minimal maintenance needs. This translates into reduced overall costs over a long period, making it a potentially attractive long-term insulation option for demanding industrial applications.
Cellular Glass Pipe Insulation A Comprehensive Analysis of Thermal Performance and Durability in Industrial Applications - Composition and Key Properties of Cellular Glass Insulation
Cellular glass insulation is a specialized material primarily designed for high-temperature industrial applications where both thermal efficiency and durability are critical. Its core structure is based on a network of sealed glass cells, forming a material with low thermal conductivity and a remarkable resistance to moisture. This closed-cell composition makes it ideal for environments with harsh temperature swings and potential exposure to moisture, which can degrade the effectiveness of other insulants.
Beyond its core thermal properties, cellular glass exhibits other advantageous characteristics. Its non-combustible nature and chemical resistance are key attributes in safety-sensitive industries where fire hazards and chemical exposure are prevalent. This also plays a role in overall energy conservation. The material is also relatively lightweight, which can make installation easier and faster, especially in large-scale industrial applications where handling and positioning large insulation pieces can be challenging.
While cellular glass offers numerous advantages, the initial cost can be higher compared to some alternative insulation options. However, this initial investment is balanced by the material's extremely long lifespan and negligible need for maintenance. In the long run, this translates into lower overall costs and reduced disruption from repairs or replacements, potentially making cellular glass a financially sound choice for applications demanding sustained thermal performance and reliability.
Cellular glass insulation is typically made from recycled glass that's melted and expanded into a distinctive closed-cell structure. This composition not only contributes to its thermal performance but also enhances its overall durability and resilience. The cells within the material are hermetically sealed, preventing water from entering and air from moving, resulting in stable thermal performance over time. This feature is particularly valuable in facilities where precise temperature control is crucial.
Interestingly, this type of insulation can withstand substantial compression loads, sometimes exceeding 350 kPa, making it suitable for high-pressure industrial uses. In fire situations, its behavior deviates from conventional insulants – it resists combustion and retains its structural integrity, creating a prolonged barrier against heat transfer. This is a critical attribute in safety-conscious industrial environments.
The resistance of cellular glass to a range of chemicals, including acids and bases, makes it a good option for applications like chemical processing plants. Its production process offers flexibility in controlling density and porosity, which gives engineers the ability to fine-tune the insulation for specific load-bearing needs while preserving desired thermal properties.
One intriguing observation is its ability to reduce noise. This is a valuable property in industrial facilities where both thermal and acoustic control are important. There's substantial evidence that cellular glass insulation can last for over 30 years, a testament to its resistance to deterioration from factors like rot, pests, and thermal degradation, unlike some organic insulants.
Despite its rigid and lightweight nature, this insulation can be readily cut and shaped in the field, making it adaptable to complex pipe configurations. It consistently maintains thermal conductivity across varying temperature ranges, guaranteeing dependable performance whether it's exposed to extremely cold or high-temperature conditions. This thermal stability is a critical factor in its ongoing effectiveness. While the initial costs might be higher compared to some alternatives, the long-term durability and minimal maintenance requirements can lead to overall cost savings over time. This is a crucial consideration for industrial facilities seeking a robust and enduring insulation solution.
Cellular Glass Pipe Insulation A Comprehensive Analysis of Thermal Performance and Durability in Industrial Applications - ASTM C552 Standards for High-Temperature Applications
ASTM C552 sets forth the standards for cellular glass insulation designed for high-temperature environments, specifically within the range of 450°F to 800°F (268°C to 427°C). This standard delves into aspects like the material's makeup, dimensions, and various physical attributes, all vital for achieving reliable insulation in demanding industrial contexts. It highlights the need for thermal performance and long-lasting durability, particularly important in high-heat applications. The standard's adoption by parts of the US Department of Defense suggests its significance in crucial settings. The specification also acknowledges that achieving certain pipe insulation designs within this temperature range may involve unique manufacturing approaches. The standard's continued development and revisions are key to ensuring cellular glass insulation remains a dependable choice for industrial processes where consistent and effective heat management is critical. This, in turn, helps maintain performance and safety within these demanding environments.
ASTM C552 sets the standards for cellular glass insulation designed for high-temperature applications, typically within the 450°F to 800°F (268°C to 427°C) range. This standard delves into the material's composition, size specifications, and key physical characteristics. It's worth noting that specialized fabrication techniques might be necessary when applying this insulation to pipes within the defined temperature range.
Interestingly, the US Department of Defense acknowledges and approves this standard. Its primary use case revolves around commercial and industrial systems, hinting at its broader relevance in these sectors. It's also crucial to understand that the ASTM C552 standard undergoes periodic revisions and reapprovals, ensuring it stays relevant to evolving industry needs and technological advancements.
The core focus of the standard is on essential properties like thermal performance and durability in high-temperature settings. The detailed physical property requirements within ASTM C552 guarantee effective thermal insulation and protection against demanding high-temperature environments. This makes it ideal for a variety of industrial applications where both safety and consistent performance are paramount.
Maintaining energy efficiency within industrial processes operating at elevated temperatures is critical. Cellular glass thermal insulation plays a pivotal role in this regard. The specified requirements in the standard help ensure that its performance will remain reliable over time, something that's vital when dealing with high-temperature operations. However, we also must acknowledge the evolving nature of this standard, given that it might be subject to future changes or updates as the industry learns more. There's a need to remain vigilant about the changes in the standard to ensure that any application follows the current recommendations. It will be interesting to follow how the standard evolves with continued research and practical applications in the coming years.
Cellular Glass Pipe Insulation A Comprehensive Analysis of Thermal Performance and Durability in Industrial Applications - Moisture Resistance Capabilities in Industrial Settings
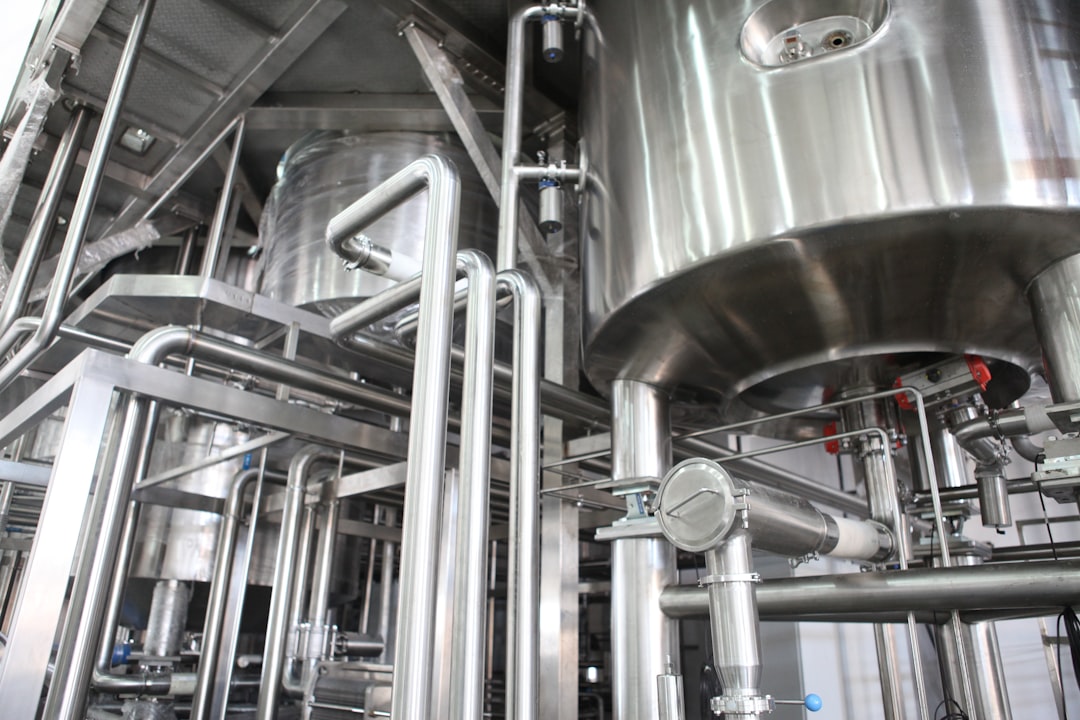
In industrial environments, the ability of insulation materials to resist moisture is crucial because moisture can severely reduce their effectiveness. Cellular glass insulation, due to its unique structure of countless, sealed glass cells, greatly limits water absorption. This means it can retain its thermal properties even when exposed to moisture, a common concern in many industrial applications. This makes it well-suited for situations where moisture exposure is likely, thus lowering the chances of insulation failure over the long run. Furthermore, adherence to standards like ASTM C552 ensures the quality and performance of this material, making it a desirable option for industrial applications that require both longevity and dependable heat management. The inherent moisture resistance of cellular glass contributes to its reputation as a durable, reliable insulation choice in challenging environments.
Cellular glass pipe insulation, such as FOAMGLAS, exhibits a remarkably low moisture absorption rate, typically less than 0.1%. This makes it an exceptional choice in industrial settings where high humidity is prevalent, as it effectively minimizes the risk of moisture-induced damage that can plague other insulation materials. Its unique structure, comprising millions of hermetically sealed glass cells, plays a crucial role in achieving this high level of moisture resistance. These sealed cells prevent water from penetrating the material, unlike many other insulants which are porous and susceptible to water infiltration.
In environments where moisture is a concern, such as refineries or chemical processing plants, cellular glass can prevent mold and mildew growth. These microorganisms not only degrade the insulation's performance but also compromise the quality of the surrounding air. The material's high compressive strength, capable of withstanding loads exceeding 350 kPa, adds another layer of protection. This robust structure ensures that the moisture barrier remains intact, even under severe physical stress, unlike other insulants which might become compromised under heavy industrial conditions.
It's noteworthy that cellular glass maintains its thermal performance even in the presence of moisture, unlike some traditional insulation materials which can experience a dramatic decrease in efficiency when exposed to water. This sustained performance is essential for industrial applications, ensuring reliable thermal control and energy efficiency throughout the material's operational lifespan. This characteristic stems from the material's non-hygroscopic nature, meaning it does not readily absorb moisture from the environment. This contrast with other more porous insulants is critical, as moisture absorption can lead to a decline in thermal conductivity and reduced performance.
Moreover, cellular glass insulation is designed to resist dimensional changes, like warping or shrinkage, even when exposed to moisture over extended periods. This resistance to dimensional instability is particularly important in industrial environments where temperature and humidity fluctuations are common. It also possesses inherent chemical resistance, which allows it to function effectively in environments with aggressive substances and moisture, thus offering protection against chemical degradation and physical damage.
The closed-cell structure of cellular glass does more than just prevent moisture intrusion – it also minimizes air movement within the insulation. This characteristic can be crucial in industrial applications where precise temperature control is required, effectively forming a stable and reliable thermal barrier. Interestingly, even when subject to high moisture environments, cellular glass has demonstrated minimal thermal loss. This preservation of thermal efficiency under moist conditions is a significant advantage over many organic insulation materials that experience substantial degradation under similar circumstances. This ability to maintain performance under adverse conditions highlights the suitability of cellular glass for industrial applications demanding dependable insulation in potentially challenging environments.
Cellular Glass Pipe Insulation A Comprehensive Analysis of Thermal Performance and Durability in Industrial Applications - Grades and Types of Cellular Glass Insulation
Cellular glass insulation demonstrates versatility through its different grades, each designed for specific industrial needs. Insulation like FOAMGLAS offers seven grades, each engineered to function within temperature ranges from 450°F to 900°F (268°C to 482°C). This adaptability is key for applications in diverse environments. The inherent strength and durability of cellular glass, a result of its unique closed-cell structure with millions of sealed glass cells, provide exceptional resistance to compression and moisture. This makes it suitable for demanding situations where other insulation materials might fail. Furthermore, adherence to standards like ASTM C552 verifies its performance in high-temperature settings. The ongoing development of specialized fabrication methods expands its applications, including pipe insulation, to meet ever-evolving industrial requirements. As industry demands shift, a thorough understanding of the different grades of cellular glass and their specific characteristics becomes essential for achieving optimal thermal efficiency and longevity in challenging settings.
Cellular glass insulation is a fascinating material, categorized into various grades based primarily on its density, typically ranging from 80 to 400 kg/m³. This density significantly impacts both thermal performance and its ability to withstand compressive loads. Interestingly, higher densities generally correlate with superior load-bearing capabilities, providing a degree of versatility across different applications.
Beyond thermal performance, the material's closed-cell structure contributes to exceptionally low gas permeability. This characteristic proves useful in applications needing an airtight seal, thereby minimizing heat loss through convection and enhancing overall energy efficiency. One notable grade often used in industrial applications is FOAMGLAS, which adheres to specific ASTM standards. This compliance ensures consistent and reliable performance across various demanding conditions, validating its use in these settings.
The chemical resistance of cellular glass is remarkable. It can withstand a range of aggressive substances common in industrial processes, including strong acids and bases, minimizing the risk of degradation over time, thereby enhancing its overall lifespan. Further adding to its robustness, cellular glass can sustain considerable compressive loads without significant deformation. Some grades can tolerate compressive loads beyond 350 kPa, making it ideal for high-pressure applications where maintaining structural integrity under stress is vital.
Another notable property is the extremely low thermal expansion coefficient, typically around 5 x 10^-6/°C. This means it resists warping or cracking during significant temperature fluctuations, vital for consistent insulation performance throughout varying operational conditions. While the moisture absorption rate for cellular glass remains low, usually below 0.1%, it's not simply about maintaining thermal efficiency. This property prevents the growth of microorganisms, like mold and mildew, which can negatively impact both insulation performance and indoor air quality.
The adaptability of cellular glass during production is quite intriguing. Manufacturers can adjust the material's density and thermal properties to meet specific engineering demands, offering a unique degree of customization to suit particular industrial applications. It's also notable that despite its generally inert composition, some grades achieve exceptionally low thermal conductivity, as low as 0.034 W/m·K. This outstanding performance makes it a leader among insulating materials, often surpassing traditional options in terms of thermal resistance.
The long-term durability of cellular glass is another compelling characteristic. High-grade cellular glass insulation can maintain its functionality for over 30 years, especially in challenging environments subject to high-temperature cycles. This longevity reinforces its value for industrial applications that rely on consistent and reliable performance over extended periods. While cellular glass has many strengths, a curious researcher must also examine any drawbacks, which could include the initial cost, the need for specific installation procedures in some instances, and the possibility of further performance and material understanding evolving over time. However, this material offers a compelling and promising solution to thermal management challenges across many industrial sectors, suggesting it's an area ripe for further study and innovation.
Cellular Glass Pipe Insulation A Comprehensive Analysis of Thermal Performance and Durability in Industrial Applications - Impact on Energy Efficiency and Cost Reduction in Industries
Cellular glass pipe insulation offers a compelling solution for improving energy efficiency and lowering costs in various industrial applications. Its exceptional thermal insulation capabilities minimize heat loss, a critical factor for industries seeking to curb their energy consumption and environmental footprint. As industries strive towards decarbonization, with projections suggesting substantial cost reductions in energy practices by 2030, the use of advanced insulation materials like cellular glass gains importance. While offering significant benefits, cellular glass often carries a higher initial cost compared to traditional insulants. Consequently, careful consideration of the long-term cost advantages – primarily driven by its remarkable durability and minimal need for maintenance – is necessary to ensure it aligns with the overall financial and energy efficiency objectives of an industrial facility. There's a balance to be struck between immediate expense and the potential for long-term savings, and understanding the nuances of this balance is key for adopting energy-efficient solutions effectively.
The use of cellular glass pipe insulation in industries can lead to considerable energy efficiency improvements, with potential cost reductions reported to be as high as 20%. This is primarily attributed to its low thermal conductivity, which minimizes heat loss, especially in high-temperature industrial processes. Furthermore, its exceptionally long lifespan, exceeding 30 years, significantly reduces the need for frequent repairs or replacements, translating to lower overall operational expenses.
Industrial energy efficiency measures are widely recognized as crucial for lowering carbon footprints. This is particularly true in sectors where high-temperature processes are prevalent. It's noteworthy that the UK's industrial sector alone accounts for a substantial portion of its overall energy use and greenhouse gas emissions, highlighting the urgency for adopting energy-saving technologies. Carbon dioxide remains the major greenhouse gas emitted from industrial operations. Therefore, improving energy efficiency is a critical part of any industrial decarbonization strategy.
While there's growing interest in advanced insulation materials, such as cellulose-based aerogels, a comprehensive evaluation of insulation materials highlights the critical role thermal performance plays in influencing both energy demands and environmental impact. This is particularly crucial for making informed decisions during the insulation selection process. The growing awareness of environmental challenges and the need for sustainable practices adds another layer of importance when choosing insulants.
The pursuit of greater industrial energy efficiency has also revealed promising avenues for cost savings. It's been estimated that about 1% of total U.S. industrial energy consumption could be saved through improved energy management. This is significant and highlights the economic potential of adopting efficient insulation technologies. While energy management practices and the introduction of smart technologies show great potential for achieving energy reductions and emissions limitations, there are certain physical limits inherent in some materials.
The introduction of high-temperature heat pipes also promises improvements in energy conservation in a wide range of industrial settings. The ability to customize cellular glass insulation to specific performance demands adds to its potential. During manufacturing, its density and load-bearing capabilities can be adjusted, ensuring the insulation perfectly aligns with specific industrial needs. In addition, cellular glass's exceptional resistance to moisture makes it particularly suitable for a range of environments, even those with high humidity, where other insulants might degrade. Unlike some materials, it's not susceptible to mold and mildew.
The robust nature of cellular glass makes it suitable for many industrial processes, including those where chemical exposure is prevalent. It withstands a range of harsh chemicals and does not deteriorate as a result of these exposures. The stability of the material in both temperature fluctuations and mechanical stress is critical, helping to ensure consistent performance over long periods. It maintains its integrity and does not suffer from shrinking or warping, which can often degrade thermal efficiency in other materials. Additionally, it has the benefit of helping to mitigate industrial noise, which is an interesting, and potentially useful attribute in many industrial settings. Overall, cellular glass insulation presents itself as a promising solution for enhancing energy efficiency, reducing costs, and minimizing the environmental impact of industrial operations. There are still open questions regarding the optimal use of this material and its performance across a wide range of industrial settings, and ongoing research will continue to inform decisions on its best applications.
More Posts from aistructuralreview.com: