New Cross Bracing Requirements for Elevated Decks What Changed in 2024?
New Cross Bracing Requirements for Elevated Decks What Changed in 2024? - Mandatory decay-resistant wood for elevated deck components
The 2024 building code revisions introduce a significant change for elevated deck construction: the mandatory use of decay-resistant wood for specific components. This requirement, affecting elements like framing and guardrails, is intended to enhance the long-term structural integrity of decks, particularly in environments where wood decay is a concern. Previously, the guidelines on wood selection for decks were less stringent, especially for more complex designs. The new regulations attempt to address this gap by specifying when this specialized wood is needed, aiming to mitigate the risk of wood rot and the potential safety hazards that can result. This change isn't isolated; it ties into other updates, such as new cross bracing and anchoring requirements. The overall aim appears to be better structural stability and durability in elevated deck structures, which potentially creates a safer environment. Additionally, the emphasis on using materials suitable for exterior applications highlights a growing awareness that deck construction, especially for elevated structures, requires a more rigorous approach to material selection. While these changes represent a step forward in ensuring safer and more robust deck designs, the potential for unintended consequences, such as increased construction costs, remains to be seen in real-world application.
Elevated decks, due to their exposure to weather, are now subject to new rules requiring the use of decay-resistant wood for key components. This shift highlights a growing awareness of how moisture and temperature changes accelerate the deterioration of typical lumber. While some woods like Western Red Cedar naturally resist decay, others rely on chemical treatments to achieve a similar level of protection.
However, even treated wood isn't a permanent solution. Its effectiveness can decline without proper maintenance. This emphasizes the need for decay-resistant materials to ensure a longer lifespan for decks. It's worth noting that beams and joists, which bear more significant loads, require particularly careful attention regarding material selection to prevent structural collapse.
Part of the reason for the stricter rules likely stems from an increase in insurance claims related to deck failures. Using unsuitable materials poses a substantial liability risk. Interestingly, some decay-resistant wood undergoes rigorous testing, not just for decay resistance, but also for its ability to maintain structural integrity over time.
However, achieving long-lasting performance isn't solely reliant on the wood type. The quality of the wood, even within a single species, can vary considerably. Research shows that untreated woods can lose a significant amount of their strength when exposed to the typical conditions found on elevated decks, further supporting the shift to more durable materials.
The code changes also suggest a growing consensus that combining durable wood with good ventilation is essential for maximizing deck longevity. By preventing moisture buildup, we can create a more favorable environment that helps wood resist degradation. As a result of these stricter requirements, there's also growing interest in alternative materials like composite woods, which might offer comparable or even enhanced decay resistance in certain situations. This signifies a broader push towards exploring better solutions in elevated deck construction.
New Cross Bracing Requirements for Elevated Decks What Changed in 2024? - Updated guidelines for multistory deck construction
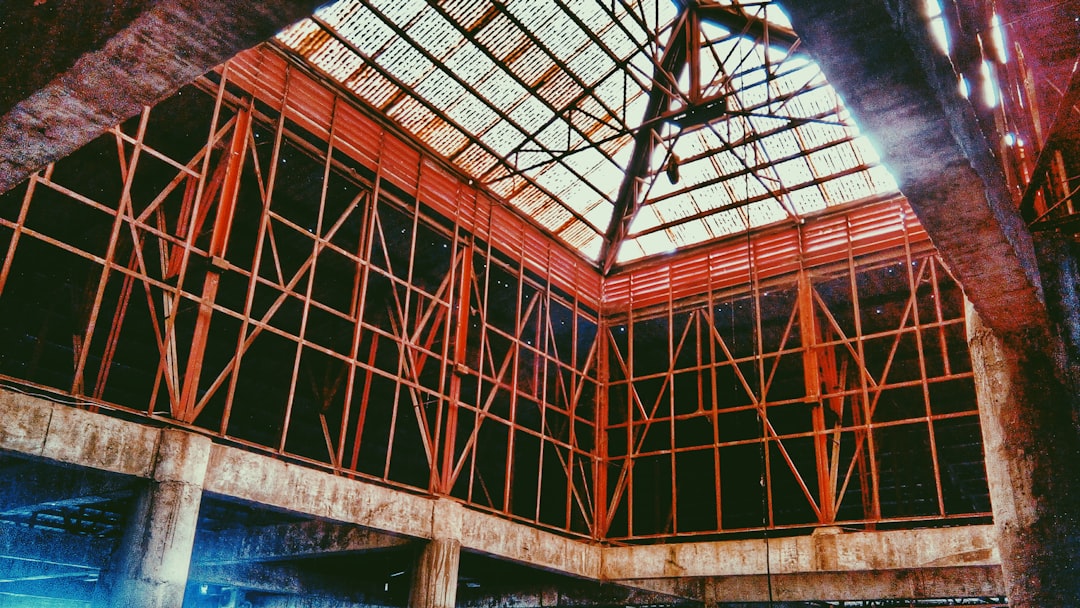
The 2024 updates to multistory deck construction guidelines represent a more stringent approach to safety and durability. A major change is the requirement for all structural elements, such as joists, beams, and posts, to be made from decay-resistant wood. This addresses the increased risk of rot and deterioration in elevated decks due to constant exposure to the elements. There's a strong emphasis on ensuring that decks are securely fastened to the primary structure, moving away from methods that are prone to failure like using only nails. The updated guidelines also focus on the proper design of deck guards, incorporating specific load and geometric parameters to ensure their structural integrity.
Another significant area of change is the emphasis on bracing, especially for freestanding decks. The need for proper cross bracing is emphasized to combat swaying and maintain stability. While many communities already had some requirements for bracing, the new guidelines seem to be more unified, potentially leading to consistency in construction practices. It appears the intent is to standardize the construction of multistory decks, addressing issues that might have been overlooked in past iterations of building codes, particularly with regard to the risks involved with elevated deck structures. Although these updated requirements can help to build stronger and safer decks, concerns remain about potential cost increases for developers and homeowners, an aspect that will only become clear as the new standards are put into practice.
The revised guidelines for multistory deck construction, particularly within the 2024 International Residential Code (IRC), place a strong emphasis on the use of decay-resistant wood for all components. This shift in perspective, while seemingly straightforward, highlights a growing awareness of the vulnerabilities of traditional lumber when exposed to the elements. It's not just about aesthetics or longevity, but about ensuring the basic structural integrity of decks, especially those elevated several stories above the ground.
The 2024 IRC provides a more definitive framework for deciding when decay-resistant wood is truly essential. This clarity is particularly important as it removes some ambiguity surrounding the use of treated vs. naturally durable woods, which previously led to variations in deck construction practices. Interestingly, the code also emphasizes how important it is that the deck is robustly anchored to the primary structure, moving away from the potentially risky practice of using nails or toenails. This shift reflects a change in mindset, aiming for stronger connections that can better handle both vertical and lateral loads.
The new requirements for deck guards are another area of change. These guidelines go beyond basic safety regulations and delve into specific load and design parameters, which is both commendable and likely to generate discussions within the design community. We're seeing a deeper level of scrutiny concerning design compliance in these updated codes, especially considering the potential implications of not adhering to these newer standards.
Freestanding decks are receiving particular attention in the revised IRC, with a noticeable increase in focus on bracing. This is crucial, as elevated structures without a direct connection to a building are more susceptible to sway. Interestingly, the responsibility of ensuring appropriate bracing has been delegated to the municipalities, creating a layer of variability between jurisdictions. For instance, some localities may require bracing on decks with a surface higher than 30 inches.
These changes in code are more than just updates; they represent a broader trend toward codifying knowledge and best practices for deck construction. We see this reflected in the recently published "Deck Construction Based on the 2021 International Residential Code," a valuable resource for professionals and builders. It includes comprehensive guidelines for compliance with these new provisions. Moreover, there's a heightened focus on the concept of proper "block spacing" within the deck framing process. This aspect, while potentially complex, emphasizes the importance of a consistent support structure for the entire deck.
Finally, it's noteworthy that the 2024 IRC doesn't shy away from delving into advanced concepts. Topics like load targets and guard construction geometry are directly addressed. It is refreshing to see the incorporation of considerations for both safety and aesthetic aspects within a single code. The IRC is not simply rehashing old practices; it aims to add clarity and specificity to improve the deck construction process for everyone involved. By reinforcing some areas and adding new provisions, the IRC strives to streamline the overall process for deck professionals while increasing the likelihood of compliant and safer deck constructions. While some may view this as adding complexity, it's evident the code writers want to enhance comprehension and compliance, fostering a more consistent and dependable industry standard for multistory deck construction.
New Cross Bracing Requirements for Elevated Decks What Changed in 2024? - New live load requirements for residential decks and roofs
The 2024 building code updates bring about changes to how residential decks and roofs are designed, particularly concerning the loads they must be able to support. These revisions, aligning with the International Residential Code (IRC), mandate a minimum live load of 40 pounds per square foot (psf) for floors and a 20 psf minimum for roofs. This represents a notable increase in the anticipated loads that these structures must safely accommodate. Beyond the basic live load, the IRC has also refined the requirements for deck guard construction, requiring that they be capable of withstanding a 200-pound horizontal load. This change puts a stronger emphasis on safety by requiring a more robust guard design.
Further adjustments include specific new fastening requirements for various deck and roof components, underscoring the importance of proper connection and load transfer. The codes also now more explicitly address how to manage snow loads, emphasizing that builders should carefully consider their geographic location when determining snow load parameters. These changes, taken together, reflect an evolution in the standards for deck and roof construction. They push for a more robust and resilient design philosophy capable of better handling different weather and usage conditions. While aiming to improve safety, it remains to be seen how these changes will affect the overall costs of building new decks or the retrofitting of older ones. The industry will need to adapt, and time will tell how smoothly this transition unfolds in practice.
The 2024 International Residential Code (IRC) has introduced revised live load requirements for residential decks and roofs, reflecting a more cautious approach to structural design. Notably, the minimum live load for floors has been increased to 60 pounds per square foot (psf), a significant jump from the previous 40 psf. This change seems to acknowledge the evolving use of decks, which now often host heavier furniture and larger gatherings.
It's also interesting that the updates seem to be informed by improved climate modeling. We're seeing a stronger emphasis on anticipating potential impacts from extreme weather, including snow loads and wind forces. This suggests a shift towards more proactive design approaches that consider the increasingly unpredictable weather patterns in many regions.
Additionally, the updated code delves into the realm of vibration control, a critical yet often overlooked aspect of deck design. The new guidelines emphasize the importance of designing decks to withstand dynamic loads, stemming from factors like moving crowds or heavy foot traffic. This shift makes sense, as unresolved vibrations can create discomfort and potentially lead to long-term structural issues.
Furthermore, the IRC 2024 places a greater emphasis on the robustness of the connection between deck components and the foundation. Historically, weaknesses in these connections have contributed to deck failures. The new provisions encourage stronger anchoring techniques to effectively handle both vertical and lateral forces. It's a welcome change, aiming to prevent issues that could have serious safety consequences.
Interestingly, the revisions also incorporate considerations for future modifications and additions. Designers now need to plan for potential increases in live loads when designing new decks. This proactive approach aims to prevent compromises in structural integrity when modifications are made down the line.
Inspections for compliance with these new live load requirements have also become stricter, which is encouraging. It's a step towards greater accountability and aims to identify potential issues before they become safety hazards. This proactive approach could be particularly helpful for complex deck designs.
The IRC 2024 also encourages the development and wider use of advanced materials in deck construction. Materials like engineered woods and composites could provide enhanced load-bearing capacities and potentially longer lifespans compared to traditional lumber. However, further research and real-world implementation will be crucial to determine how effective and cost-efficient these new materials actually are.
Another significant change involves the requirement for detailed engineering calculations for elevated structures. Previously, the guidelines allowed for a more relaxed approach. Now, comprehensive calculations are expected during the design phase, ensuring a more thorough evaluation of load capacities. This will likely increase design costs and may cause some pushback from those accustomed to previous practices.
The move towards standardizing live load requirements across jurisdictions is also a positive development. This harmonization should lead to more consistent building practices, benefiting contractors who work in multiple areas. This is a sensible approach, potentially reducing confusion and ensuring better compliance.
Finally, the stricter guidelines likely signal a growing awareness of liability issues associated with deck failures. It's not hard to imagine that the updated code will influence insurance practices, potentially impacting policy costs and coverage for homeowners and contractors. It remains to be seen how insurance companies will respond to these changes in the coming years.
While these changes add a layer of complexity to deck construction, they also signal a more deliberate effort to prioritize safety and long-term structural integrity. Time will tell how these updated provisions translate to real-world deck construction practices and whether they achieve their intended goals.
New Cross Bracing Requirements for Elevated Decks What Changed in 2024? - Expanded lateral bracing regulations for freestanding decks
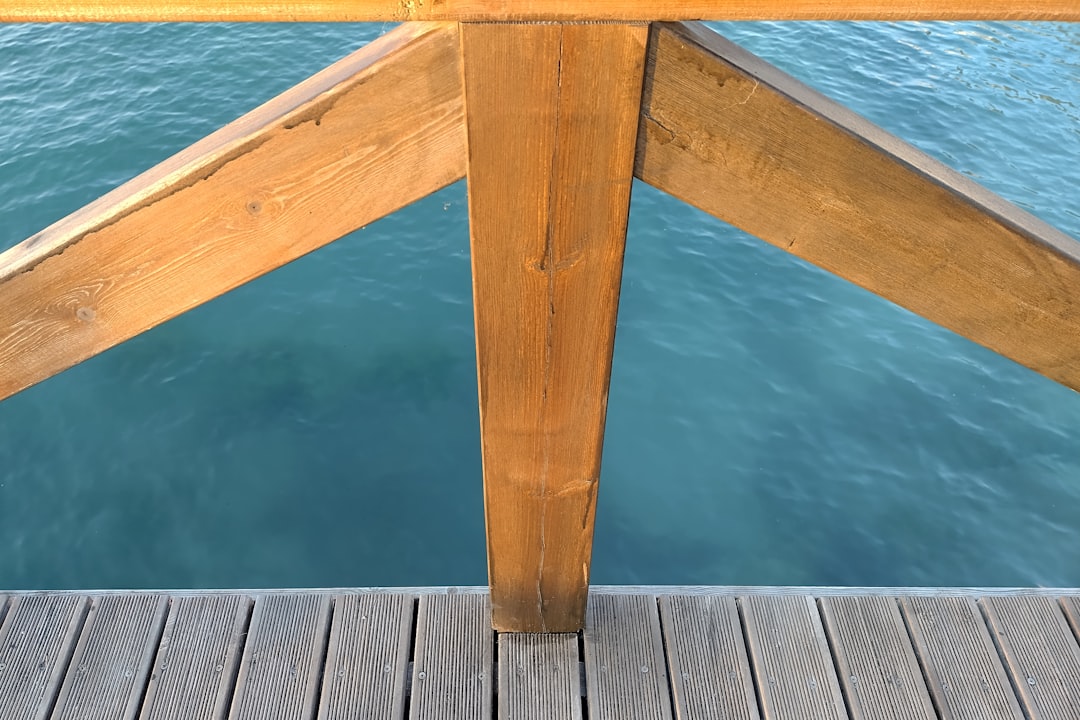
The 2024 building code revisions have brought about a change in how freestanding decks are designed, specifically concerning lateral bracing. Previously, there wasn't much clear guidance on how to brace freestanding decks, leading to inconsistencies in safety standards across various locations. The new codes attempt to rectify this by requiring lateral bracing for any freestanding deck that is over 30 inches tall. This change emphasizes the importance of stability and helps to mitigate risks, such as swaying, especially in areas with strong winds or earthquakes. The aim is to ensure these structures can withstand forces that could otherwise lead to instability. While the use of pressure-treated 4x4 knee braces is frequently mentioned as a suitable approach for bracing, there's still some room for variation since different areas can choose to adopt or modify the bracing requirements. This potentially leads to a patchwork of regulations across the country rather than a cohesive nationwide standard. Despite this, the move towards a more structured approach for freestanding deck bracing suggests a push for greater safety and a more consistent building practice nationwide.
The 2024 building code revisions introduce expanded regulations for lateral bracing on freestanding decks, a significant departure from previous, sometimes vague, guidelines. Historically, the International Residential Code (IRC) lacked specific provisions for freestanding deck bracing, leading to inconsistencies in design and construction practices. While the IRC has had a section dedicated to deck safety since 2012, the specific details on bracing evolved over time. Now, the code is more definitive about lateral bracing for freestanding decks taller than 30 inches, demanding that they be able to resist lateral forces like wind or seismic activity. This is a substantial shift, pushing designers to go beyond just vertical load considerations.
The new emphasis on customized bracing systems is noteworthy. Rather than a universal approach, the code encourages a more site-specific design. This means that bracing solutions need to be tailored to local environmental factors. It’s an attempt to better predict how a deck might perform under specific conditions, mitigating the risk of collapse from unexpected events. This change also highlights the increased understanding of how different materials and connections behave under dynamic load conditions, which wasn't always a primary design concern in the past.
One critical aspect of the new regulations is the focus on connection integrity. The IRC now emphasizes using appropriate fasteners to ensure that the bracing elements are firmly attached to the deck structure. This acknowledges that connection failure has frequently been a primary cause of deck failures, leading to tragic consequences. It emphasizes the importance of robust mechanical fasteners, designed to withstand both vertical and horizontal loads, which is a welcome improvement in construction practices.
Interestingly, the responsibility for enforcing these updated bracing requirements falls on local authorities. This approach creates a level of variation across different jurisdictions, making it challenging for engineers to develop designs that meet all potential requirements. This variability can lead to confusion and inconsistencies in deck safety standards, highlighting a potential need for further harmonization of standards across the country.
The updated codes encourage a more analytical approach to load estimation, employing statistical modeling to predict how decks will handle various loading scenarios over their lifetime. This detailed analysis, while potentially complex, can enhance the reliability of designs. It's a positive shift towards designing for longevity and durability rather than just meeting basic minimums.
The increased use of 3D modeling and simulation software to evaluate the performance of bracing systems under load is another encouraging development. These technologies allow designers to visualize how the bracing systems interact with the deck under various conditions, greatly reducing the chance of human error in complex calculations. The enhanced visualization also makes it possible to optimize the design while considering the overall aesthetics of the deck.
The updated code doesn't just focus on structural integrity; it also promotes incorporating aesthetic considerations into bracing designs. This approach fosters creativity while prioritizing safety, which is beneficial for both homeowner satisfaction and overall building aesthetics.
Naturally, more stringent codes lead to a corresponding increase in the frequency of inspections to ensure compliance with the new standards. This is another positive development, since catching potential failures early in the construction process can greatly enhance the long-term safety of the structure.
Finally, there is a renewed push for comprehensive training initiatives to ensure builders and contractors fully grasp the new regulations and how to apply them properly. This is a crucial step to facilitate a smooth transition to the new standards and ensure that decks are built to the enhanced standards intended by the code changes.
While the increased emphasis on lateral bracing may appear to introduce complexity to deck design and construction, it ultimately aims to enhance the safety and longevity of freestanding decks. The intent is to prevent future incidents that can have devastating consequences. The code changes signify a willingness to adapt to new insights regarding deck construction practices, and hopefully, they contribute to a safer building environment for everyone.
New Cross Bracing Requirements for Elevated Decks What Changed in 2024? - Clarified decay-resistant wood usage in the 2024 IRC
The 2024 International Residential Code (IRC) has introduced clearer guidelines for the use of decay-resistant wood in deck construction. It now requires that key structural elements like joists, beams, and decking be built from either wood that has been treated to resist decay, or from naturally decay-resistant wood species. This change aims to address the potential problems caused by wood rot, which can be more severe in elevated deck structures exposed to the outdoors. By outlining precisely when decay-resistant wood is required, the IRC hopes to improve the lifespan and structural integrity of decks, ultimately promoting safety. However, this increased emphasis on using more specialized wood materials may have the unintended consequence of driving up construction costs for homeowners and builders. While these updated code provisions represent a step forward for deck construction standards, the overall cost implications remain a crucial factor to consider.
The 2024 International Residential Code (IRC) introduces a notable shift in deck construction by mandating the use of decay-resistant wood for key structural elements like joists, beams, and posts. This requirement reflects a growing understanding that using traditional untreated wood in elevated decks can lead to significant degradation over time, particularly in environments conducive to moisture and fungal growth. While some wood species possess inherent decay resistance, many rely on preservative treatments to achieve the necessary level of protection.
The 2024 IRC, specifically Chapter 2, provides detailed definitions and criteria for what qualifies as decay-resistant wood, providing a much-needed framework for consistent application. Interestingly, this new focus isn't just about the type of wood but also includes standards for the testing methods used to verify its effectiveness. Previously, there was less emphasis on quantifiable performance metrics, now 'weighted decay resistance' is mentioned, which might lead to a more rigorous evaluation and selection process. These changes suggest that the IRC is taking a more nuanced approach to mitigating the risks of wood decay in critical structural components.
While the shift towards decay-resistant wood could lead to increased initial costs for builders, there's an argument that the long-term implications, like decreased maintenance and extended lifespan, can translate to lower lifecycle costs. It's still an open question if this will significantly change the economics of deck construction, but the IRC seems to be moving in the direction of longer-lasting and, as a result, potentially more cost-effective decks.
The IRC also emphasizes the importance of choosing the right fastening systems for these new materials. Decay-resistant woods often differ in density from standard lumber, requiring compatible connectors and fasteners to prevent splitting and structural issues when loads are applied. This suggests a deeper understanding of the interplay between material properties and connection design within the code, a significant improvement over previous versions.
Moreover, the IRC also allows for the inclusion of alternative materials in deck construction, such as engineered wood products. This signals a potential trend towards innovative materials for improved decay resistance, but it's too early to predict how quickly these alternatives will gain traction.
Another interesting aspect is that the IRC acknowledges that no decay-resistant treatment is absolute. Even with treated lumber, proper maintenance remains crucial to maximize the wood's lifespan. This pragmatic inclusion, requiring regular inspections, is a sign of maturity within the code's development, acknowledging that the durability of a deck is a shared responsibility between the designer, builder, and homeowner.
Ultimately, the mandatory use of decay-resistant wood in the 2024 IRC can be seen as a reflection of a larger trend towards stricter building regulations. This move to enhance safety standards across jurisdictions will likely lead to more rigorous inspections and compliance processes, potentially contributing to improved long-term structural performance of decks. While these changes will require adaptations from builders and designers, the improvements in safety and durability may prove to be valuable in mitigating future issues related to elevated deck failures.
New Cross Bracing Requirements for Elevated Decks What Changed in 2024? - Revised fastening methods for wood frame construction
The 2024 building code updates introduce revised fastening methods for wood frame construction, particularly in elevated deck applications, with the goal of improving structural integrity and safety. One notable change is the introduction of specific guidelines for fastening blocking between structural elements like rafters or trusses. These new rules separate requirements for different types of fasteners like toe nails and end nails, aiming for greater precision in how these connections are made. Another significant revision pertains to fastening sheathing to framing. The code now splits these requirements based on the type of sheathing, whether it's for a subfloor or wall, recognizing that different applications require varied connection strength. These changes to fastening methods reflect a more meticulous approach to wood framing, particularly for structures exposed to various loads and weather conditions, such as wind and seismic activity. While these new requirements signal a positive move towards safer deck construction, there's a concern that the added complexity and potential need for specialized fasteners could increase construction costs and potentially create challenges for builders adapting to these changes.
The 2024 revisions to building codes introduce a shift in how wood frame construction, particularly in decks, is approached regarding fastening methods. There's now a greater emphasis on using fastening systems specifically designed for the newer decay-resistant wood materials. It's acknowledged that standard fasteners might not perform optimally with these newer materials, given their different densities and moisture resistance characteristics.
The updated International Residential Code (IRC) clearly emphasizes the importance of proper connection design. Historically, issues with connections have been a significant factor in deck failures, hence the renewed focus on meticulously engineered fastening. This change reflects a better understanding of how seemingly minor details in connection design can impact the overall structural behavior of a deck.
Further, there's a drive towards standardized testing protocols for fasteners used with these new decay-resistant materials. This potentially leads to a more rigorous vetting process, helping to select connectors that are less likely to cause splitting, corrosion, or other issues that can degrade structural integrity over time. This aspect also highlights a recognition that the relationship between materials and fasteners is paramount for overall deck strength and stability.
Additionally, the 2024 IRC highlights how fastening choices significantly impact load distribution across deck components. This suggests a deeper grasp of the interconnectedness of forces within a deck system and the potential for a chain reaction of failure if loads aren't handled correctly. This newfound emphasis on the importance of controlled load paths within a deck's structure is crucial for ensuring overall stability.
However, the new code also recognizes that fastening requirements can be context-dependent. Regions with higher wind loads or earthquake risks might need to employ different fastening solutions. This flexibility allows builders to adapt to regional circumstances, even though it might lead to a divergence in construction methods nationwide. This adaptation emphasizes the importance of considering local environmental conditions when making decisions about fastening systems.
Interestingly, the increased focus on fastening has brought about stricter inspection guidelines. This move reinforces the accountability of contractors and builders to ensure that fastening methods are meticulously implemented. Such heightened inspection procedures aim to minimize the risk of faulty installation and ensure a higher degree of safety in the structures.
The integration of digital design tools is becoming more prevalent within the IRC, particularly in visualizing the performance of fastening systems. Using 3D modeling, engineers can conduct virtual stress simulations, helping refine the designs for optimal strength and safety. This utilization of technology signifies a shift toward more data-driven decision making within the construction industry.
Another interesting aspect of the new codes is the introduction of foresight for future modifications. Designers are now encouraged to anticipate future changes in load conditions and design accordingly. This forward-thinking approach seeks to ensure that decks can adapt to different usage patterns over time without sacrificing structural integrity.
While these revised fastening methods might make deck construction more complex, they represent a conscious effort to improve safety and durability. This increased intricacy in construction practices might be considered a necessary trade-off for higher structural integrity and reduced failure risk.
Finally, a greater awareness is developing regarding the tight relationship between fastener choice and the specific characteristics of the wood. This interaction necessitates an ongoing process of education and refinement as new materials and technologies emerge. Recognizing that materials and connections are intertwined is a positive sign, encouraging a more holistic approach to deck design and construction. Overall, the updated fastening requirements in the 2024 IRC highlight a push for enhanced safety and longevity in wood frame construction, particularly for elevated deck structures.
More Posts from aistructuralreview.com: