Comparing Steel and Aluminum Understanding the 25x Strength Differential in Structural Applications
Comparing Steel and Aluminum Understanding the 25x Strength Differential in Structural Applications - Defining The 25x Factor Material Density Difference Between Steel and Aluminum
A core distinction between steel and aluminum lies in their substantial density difference. Aluminum possesses a density approximately a third of steel's, leading to steel being roughly 25 times denser when comparing equal volumes. This fundamental density contrast impacts more than just the weight of structural components. It also shapes how each material is applied in construction projects. Aluminum's lower density offers a compelling strength-to-weight ratio, making it a prime option for applications requiring lightweight structures. However, the greater tensile strength and inherent density of steel make it the superior choice in contexts demanding unwavering durability and ultimate structural integrity. While aluminum's usage is expanding in industries like automotive and aerospace, emphasizing weight reduction, steel continues to be the preferred choice in conventional construction projects, particularly when the focus is on robust strength.
Aluminum's density, roughly 2.7 g/cm³, is considerably lower than that of steel, which falls between 7.8 and 8.1 g/cm³. This translates to steel being about three times heavier than aluminum for the same volume. This inherent weight advantage of aluminum is driving its adoption in applications where mass reduction is crucial.
While possessing lower density, aluminum can achieve tensile strengths that rival or surpass certain types of steel, particularly when specific alloying elements like copper, magnesium, or silicon are introduced. This highlights that the relationship between composition and material performance is complex and not solely dependent on density.
The widely mentioned 25x factor for steel's strength advantage is most relevant when comparing practical yield strengths. However, this difference can be significantly altered by alloying and treatment processes, making it crucial to carefully consider specific material choices in a given application.
Steel tends to demonstrate ductile failure under load, while aluminum, at lower temperatures, can be more prone to brittle failure. These distinct failure behaviors must be factored into material selections, especially in applications subject to wide temperature fluctuations.
Aluminum's notable corrosion resistance offers advantages in terms of maintenance costs and durability, particularly in environments where moisture or chemical exposure are concerns. This long-term advantage might outweigh some of the initial cost considerations favoring steel.
Aerospace applications frequently prioritize aluminum over steel, driven not only by the weight savings but also by its superior fatigue resistance. This is especially crucial in high-cycle loading scenarios like those encountered in aircraft.
Steel's widespread availability and affordability are significant factors in its selection. However, aluminum processing methods, such as extrusion and die-casting, offer potential cost savings through design flexibility. This can translate to quicker assembly times and more complex shapes due to the material's lower weight.
The superior thermal and electrical conductivity of aluminum compared to steel makes it preferable in applications where heat dissipation or electricity transmission are essential. This widens the scope of considerations beyond simple strength comparisons.
Though offering significant fuel-efficiency benefits in automotive design, aluminum's high strength-to-weight ratio is sometimes overshadowed by the well-established track record and performance of steel. There is a lingering preference for steel in many of these applications.
It's essential to acknowledge that aluminum's lower density does not always translate to superior performance across all applications. Its specific modulus, signifying stiffness relative to weight, doesn't guarantee better performance in situations requiring high rigidity and minimal deformation. This underscores the necessity of careful consideration and analysis for each unique application.
Comparing Steel and Aluminum Understanding the 25x Strength Differential in Structural Applications - Load Bearing Analysis Steel at 500 MPa vs Aluminum at 90 MPa
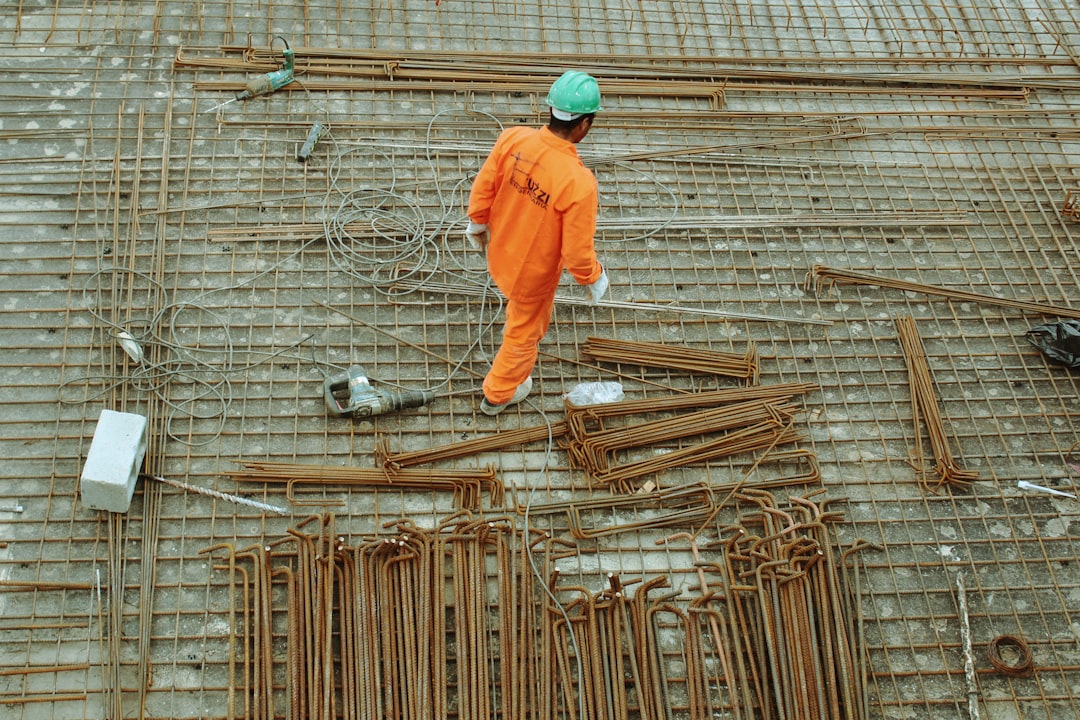
When analyzing load-bearing capabilities, a clear distinction arises between steel and aluminum. Steel, with its typical tensile strength of 500 MPa, significantly surpasses aluminum's 90 MPa. This substantial strength difference, particularly in compressive strength where steel is 5 to 6 times stronger, makes steel the preferred material for applications requiring high structural integrity. While certain aluminum alloys, through the addition of elements like copper or magnesium, can achieve tensile strengths approaching those of some steel grades, they still don't match the raw strength that structural steel provides. Therefore, while aluminum offers advantages in lightweight design and resistance to corrosion, its comparatively lower inherent strength necessitates cautious evaluation in situations demanding robust load-bearing performance. Engineers and designers must fully understand this disparity when selecting materials that effectively meet the specific demands of the structure they are creating.
While standard structural steel typically boasts a tensile strength around 500 MPa, aluminum's inherent strength is considerably lower, usually around 90 MPa. However, this doesn't tell the whole story. Certain aluminum alloys, particularly those enhanced with copper or magnesium, can achieve tensile strengths that rival or even exceed 600 MPa. This highlights how material composition significantly influences the final performance, a crucial factor to consider when making material choices.
The way steel and aluminum fail under stress differs. Aluminum, depending on temperature and alloy, can experience ductile tearing followed by a more brittle failure. This contrasts with steel, which usually shows a more predictable yielding response before failure. This distinction makes failure analysis and the design of structures that incorporate aluminum potentially more complex.
Steel's greater yield strength enables engineers to utilize leaner structural members in certain designs. While this cuts down on material usage, it presents challenges with temperature-related expansion and contraction. This must be accounted for when designing systems that are exposed to varying temperatures.
Aluminum's susceptibility to fatigue failure under repetitive loading is a significant concern, especially in applications where stress levels are high. Steel, conversely, has a generally superior endurance limit, suggesting that it might be a better choice in such situations.
When dealing with seismic events, steel's capacity to absorb and redistribute energy is superior to aluminum's. Steel's higher ductility allows it to withstand the forces involved better than aluminum, which could fail more readily under similar circumstances.
To maintain aluminum's corrosion resistance, often coatings or anodizing are required, adding complexity to its long-term maintenance and life-cycle considerations. This stands in contrast to steel, where simple galvanization can be effective.
Analyzing the overall cost of a structure demands considering the full life cycle, not just the initial costs. Aluminum might seem initially cheaper because of its lighter weight, aiding transportation and assembly. But, the potential for more frequent repair or replacement due to fatigue issues could diminish these initial savings over time.
Aluminum's transition temperature is a factor in determining its overall performance. At colder temperatures, its ductility tends to reduce, potentially leading to brittle failures, a critical consideration for applications operating in cold environments.
Electromagnetic interference can sometimes be a concern in specific applications. Steel's lower conductivity offers some advantages in these cases as it's less susceptible to electrical disruptions than aluminum, highlighting a less-discussed element in material selection.
The connection between the strength and ductility of aluminum alloys is intricate. Factors such as heat treatment and tempering can greatly impact these characteristics. This highlights that the simplistic comparisons often associated with materials are not always sufficient when looking for the best fit for a specific application.
Comparing Steel and Aluminum Understanding the 25x Strength Differential in Structural Applications - Weighing Structural Applications Heat Dissipation and Corrosion Resistance
When evaluating structural materials like steel and aluminum, factors beyond just strength, such as heat dissipation and corrosion resistance, become crucial. Aluminum demonstrates superior corrosion resistance, making it well-suited for environments where oxidation is a concern. This inherent property can translate to reduced long-term maintenance costs, a significant benefit in many applications. Furthermore, aluminum's exceptional thermal conductivity allows it to dissipate heat efficiently. This is particularly valuable in scenarios requiring rapid temperature changes, like those found in transportation sectors like aerospace and automotive.
However, this advantageous profile is balanced by aluminum's generally lower tensile strength when compared to steel. In situations demanding high structural integrity and durability, steel remains the dominant choice, holding its own against the potential advantages aluminum offers. Consequently, while aluminum possesses qualities that are beneficial in specific application contexts, a thorough evaluation of the intended use and its specific performance requirements is critical before final material selection is made. The optimal material choice ultimately hinges on balancing the required performance characteristics with the specific application needs.
When considering structural applications, it's not just strength that matters, but also how materials handle heat, and resist corrosion. Aluminum, with its notably high thermal conductivity, around 205 W/m·K compared to steel's 50 W/m·K, excels in situations demanding quick heat dissipation. This makes it a natural choice for applications like electronics cooling where overheating is a major concern. While steel can be protected with coatings, aluminum intrinsically forms a protective oxide layer that resists further corrosion, reducing the need for maintenance in harsh conditions. This self-repairing characteristic is a significant advantage, especially in environments prone to oxidation and chemical exposure.
However, the story of corrosion resistance isn't entirely straightforward. While steel may need regular coating maintenance, aluminum's oxide layer can repair itself under atmospheric conditions, potentially leading to lower long-term maintenance. This also impacts the overall cost of using each material throughout its life cycle.
While aluminum shines in thermal management applications due to its high thermal conductivity, the difference in thermal expansion between the two metals is important. Aluminum expands about 2.5 times more per degree of temperature change compared to steel, which necessitates cautious consideration in designs where significant temperature fluctuations are anticipated. Failure to account for this can lead to significant structural issues caused by thermal stress.
Aluminum's resistance to pitting corrosion, a common problem in steel structures, especially in salty or chemically aggressive environments, makes it preferable for coastal or industrial settings. But, aluminum's structural performance in highly stressed environments can be tricky, making careful design crucial. This becomes even more critical when considering dynamic or impact loading situations.
The fatigue behavior of aluminum, which can be greatly influenced by alloying and processing, complicates things further. While it is often considered less fatigue resistant than steel, some aluminum alloys can outperform certain steel grades under repeated loading conditions, challenging conventional wisdom about material limitations.
Another important factor is galvanic corrosion. It's a greater concern when using aluminum with incompatible metals, requiring careful material selection to prevent premature failure. Steel, on the other hand, tends to be less susceptible to this issue, increasing its reliability in mixed-material applications.
While weight reduction is a primary reason for using aluminum in structures, its strength can diminish considerably at elevated temperatures compared to steel. Steel retains its strength much better under high heat, a vital factor for situations where fire exposure is a potential concern.
These are only a few of the many considerations that come into play when choosing between steel and aluminum. Each application requires a comprehensive evaluation of material properties, anticipated environmental conditions, and structural performance needs to ensure that the chosen material optimally meets the demands of the structure.
Comparing Steel and Aluminum Understanding the 25x Strength Differential in Structural Applications - Understanding Material Costs Raw Material to Final Installation
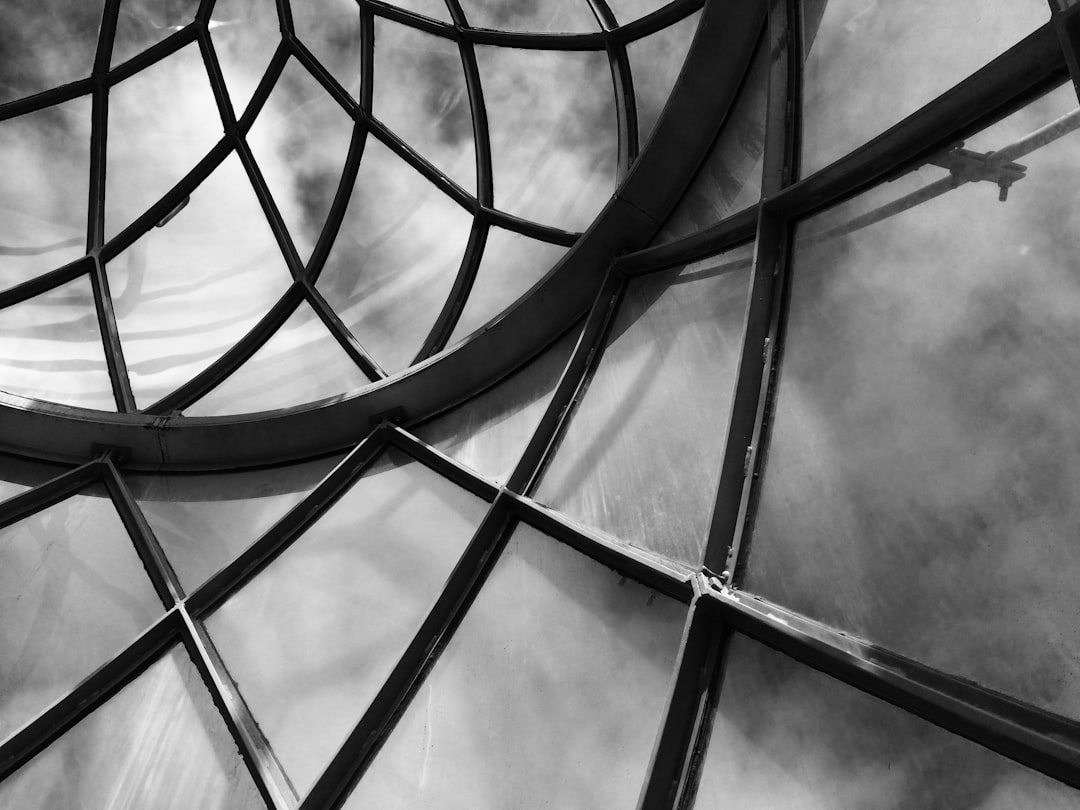
When comparing steel and aluminum, understanding the costs associated with each material from its raw state to the final installation is essential due to their different properties and economic implications. Aluminum typically starts with a higher price per kilogram compared to steel. However, its lower density can lead to cost savings during transport and construction phases. But aluminum's propensity for fatigue and the requirement for protective coatings throughout its lifespan can complicate the long-term cost picture, making its overall cost-effectiveness questionable. Steel, although its raw material costs can vary based on market conditions, tends to be less expensive initially. This, combined with steel's inherently greater strength and durability, makes it a preferred choice for applications demanding robust performance. Ultimately, the choice between the two hinges on a careful evaluation of both immediate and long-term costs, factoring in the performance requirements within the specific structural context of the project. It's a complex interplay of immediate expenses and potential future upkeep that influences the optimal material decision.
The cost of materials, from the initial raw state to the final installation, is a crucial factor in comparing steel and aluminum for structural applications. Steel typically boasts a lower initial raw material cost compared to aluminum. This stems from the readily available iron ore reserves and generally lower extraction costs. However, steel prices can fluctuate based on global market conditions and potential tariffs.
Interestingly, aluminum's processing can significantly increase costs. Its production requires a substantially greater energy input compared to steel, about ten times more, impacting the overall budget. This energy-intensive nature of aluminum processing needs to be factored into any cost analysis.
Post-processing also presents cost differences. While steel is frequently welded, aluminum often requires more specialized welding methods like TIG or MIG, leading to higher labor and material costs during installation. Aluminum's inherent characteristics can also necessitate specialized tooling and techniques, which can drive up fabrication costs.
The shapes and thicknesses of aluminum components can be more complex to achieve a desired level of performance. This complexity often leads to higher fabrication costs due to the requirement for more elaborate designs.
Aluminum's pricing volatility, influenced by global market conditions and manufacturing costs, can be a drawback compared to steel, whose price tends to remain relatively more stable. This fluctuating aluminum price can complicate financial forecasting in longer-term construction projects.
While known for its excellent corrosion resistance, aluminum often requires protective coatings for applications exposed to harsh environments. These coatings add a significant maintenance cost to the long-term lifespan of the material, sometimes challenging its perceived cost-efficiency.
Installation speed can be a factor, with aluminum's lighter weight facilitating quicker handling and potentially lowering labor costs on site. However, these potential labor savings may not always offset the higher material and specialized labor costs.
Aluminum's recyclability provides a pathway for lower material costs for recycled aluminum. However, the production of high-quality aluminum from raw materials still comes at a higher price point than steel, which can heavily influence cost decisions.
For specific, demanding applications like aerospace, where custom aluminum alloys are needed, the cost can significantly exceed that of comparable steel, requiring a careful assessment of performance and expense.
Lastly, the expertise required for aluminum's final installation can drive up project costs. Specialized skills and knowledge are needed to work with the specific properties of aluminum, potentially leading to higher contractor bids.
In summary, while aluminum offers compelling advantages in some applications, it's important to carefully consider the complete cost picture, encompassing both initial material expenses and the associated costs of processing, fabrication, installation, and maintenance when choosing between aluminum and steel. It becomes evident that the 25x strength differential alone doesn't fully capture the multifaceted cost considerations involved in these two widely used structural materials.
Comparing Steel and Aluminum Understanding the 25x Strength Differential in Structural Applications - Stress Strain Behavior The Yield Point Distinction
When exploring the mechanical differences between steel and aluminum, a key distinction lies in their unique stress-strain behaviors and how they exhibit yield points. Unlike hot-rolled steel, which shows a clearly defined yield point on a stress-strain curve, aluminum alloys present a more gradual, rounded response. This means aluminum doesn't have a distinct point at which it transitions from elastic to plastic deformation. This difference is a significant factor when assessing the overall strength of each material, as aluminum typically has a lower yield strength compared to steel. This characteristic contributes to the widely discussed strength differential between the two, and it's why engineers often cite a 25x strength factor in favor of steel.
Further complicating the matter, aluminum possesses an elastic modulus roughly one-third of steel's. This lower stiffness means that aluminum components, when subjected to stress and then relieved, will "spring back" more than comparable steel parts. This property needs to be carefully considered during the design phase of structural projects. Recognizing these differences in stress-strain behavior and yield point characteristics is critical for engineers and designers when deciding between steel and aluminum for particular applications, as the choice impacts a structure's overall performance and the types of design considerations required.
Aluminum and steel exhibit different behaviors when subjected to stress, specifically concerning the yield point. Steel often displays a clear yield point, meaning it undergoes a noticeable deformation before failing. This allows engineers to predict its behavior and design accordingly. However, aluminum's yield strength can be significantly influenced by temperature, leading to unexpected failures in structures exposed to varying temperatures. It's like trying to build with a material whose strength isn't always consistent.
Unlike steel, where the difference between yield strength and ultimate tensile strength is more pronounced, aluminum's yield point often falls closer to its ultimate strength. This smaller margin for error means aluminum has less flexibility before failure, presenting a challenge for design. It's a bit like a tightrope walk for engineers: a small misstep could be disastrous.
Steel's yield point is often characterized by a specific pattern in stress-strain curves – a plateau that helps predict material behavior. Aluminum, however, lacks this regularity in its stress-strain response. This inconsistency makes it more challenging to design applications that depend on predictable behavior under stress. You can think of it like designing a bridge with materials of varying strengths – it's hard to guarantee the structure's integrity.
When loads are repeatedly applied, known as cyclic loading, aluminum's fatigue limit often sits closer to its yield strength. This makes aluminum more prone to failure over time compared to steel, which generally possesses a higher endurance limit. It's like constantly bending a paperclip: eventually, it breaks. Steel seems to handle such stresses far better.
Because of these differences, aluminum structures may require more conservative design choices, like increased sizing and safety factors to account for the inherent lower and less consistent yield characteristics. This conservative approach can affect overall design efficiency, highlighting a trade-off that must be made when using aluminum.
Interestingly, certain treatments can enhance aluminum alloys to achieve yield strengths exceeding some mild steels. Yet, the lack of a distinct yield point can still pose challenges in environments with repeated loads. It's a bit of a double-edged sword – improved strength in one aspect, but risk in another.
Steel's yield point is generally more dependable across varying stress levels. Therefore, it's often the preferred material in situations where constant load-bearing is essential, for example, in structures designed to withstand earthquakes. It's a more predictable and reliable choice when consistency is key.
Aluminum's susceptibility to temperature fluctuations can reduce its yield point and ductility in cold environments. Engineers must meticulously consider this behavior when choosing aluminum for structures in cold climates or those subjected to wide temperature variations. Failing to factor this in could lead to unexpected structural consequences.
While aluminum's higher elasticity enables lighter designs, a key advantage, this must be weighed against the increased risk of fatigue failure when the material experiences repeated loads. It's a constant balancing act between weight savings and performance risk.
Understanding the nuances of yield strength versus tensile strength is paramount in structural engineering. While aluminum can satisfy certain design needs, its yield behavior demands careful scrutiny. We must be mindful that simply assuming its strength is adequate could lead to issues in load-bearing applications. The strength difference between steel and aluminum is very real and needs careful consideration.
Comparing Steel and Aluminum Understanding the 25x Strength Differential in Structural Applications - Practical Applications Where Each Material Shows Superior Performance
When engineers and designers choose between steel and aluminum for structural applications, the decision often comes down to where each material shines. Aluminum's lightweight nature and inherent corrosion resistance make it a favored choice in areas like aerospace and automotive engineering, where reduced weight and enhanced durability are paramount for performance and fuel efficiency. In contrast, steel, with its substantially greater strength and toughness, remains the go-to material in many construction and heavy machinery scenarios. This is particularly true when structures require high load-bearing capabilities and the ability to withstand extreme forces. While aluminum excels when the goal is a lightweight structure with a good strength-to-weight ratio, steel's superior raw strength makes it ideal in applications where robust structural integrity and resistance to high stresses are the primary concerns. Ultimately, the selection between these materials boils down to a meticulous evaluation of each project's specific performance goals, the anticipated environmental conditions, and the overall cost considerations associated with each option.
In scenarios demanding high temperatures, steel's significantly higher melting point (around 1370-1450°C compared to aluminum's 660°C) makes it a superior choice. Aluminum's structural integrity degrades at elevated temperatures, limiting its applicability.
When structures face potential impacts, steel's inherent ductility allows for substantial deformation prior to fracture, absorbing a considerable amount of energy. Conversely, aluminum tends to fracture more abruptly under high impact loads, posing a potential challenge for designing structures that ensure safety in such events.
In environments with consistently cold temperatures, aluminum's tendency to become brittle becomes a notable concern. It loses the ability to effectively absorb energy before failing, unlike steel, which retains its ductility and toughness in cold conditions. This difference makes steel more suitable for structures located in harsh climates.
When dealing with very large-scale structures, such as bridges, while the lighter weight of aluminum seems attractive, the amount needed to achieve the same strength as steel often negates any significant weight savings. This factor might seem counterintuitive at first glance, but it is important to consider in the design process.
Steel's lower coefficient of thermal expansion, approximately 11 µm/m·K, is half of that seen in aluminum (roughly 23 µm/m·K). This difference in how each material responds to temperature changes requires careful design consideration to manage thermal stress in structures exposed to varying temperatures. The consequence of failing to consider this discrepancy in design can result in structural problems.
Steel's greater density provides a distinct edge in sound insulation compared to aluminum. In applications like buildings where noise reduction is a priority, steel emerges as a more effective sound barrier. This aspect is significant in residential or commercial environments where controlling noise transmission is important.
While standard aluminum is weaker, specific heat-treated aluminum alloys can achieve tensile strengths that exceed those of several types of steel. As a result, a close examination of material properties and selection is crucial for getting the desired performance from each structure.
Welding aluminum necessitates specialized techniques like TIG welding due to its thermal conductivity and lower melting point. In contrast, steel is welded with relative ease and using less specialized equipment, simplifying the construction process. It’s one of the reasons why steel construction is often considered more straightforward for many projects.
Creep, which is a material's tendency to permanently deform under sustained loading, is a more prominent issue for aluminum, particularly at elevated temperatures. This aspect restricts its use in structures exposed to long-term loading in warm environments, where high-strength steels demonstrate better performance.
Steel has greater dimensional stability than aluminum and deforms less under loads. This characteristic can lead to more reliable and accurate construction tolerances, a vital factor in structures requiring precise assembly and fit. This detail might appear minor at first, but it is critical in many types of industrial applications.
More Posts from aistructuralreview.com: