Energy Efficiency Analysis How Commercial LED Rope Lights Reduce Structural Lighting Costs by 73% in Industrial Applications
Energy Efficiency Analysis How Commercial LED Rope Lights Reduce Structural Lighting Costs by 73% in Industrial Applications - Direct Energy Cost Analysis LED Rope Lights Cut Power Bills by 73% Compared to HPS Systems
Directly comparing the energy consumption of LED rope lights to HPS systems reveals a substantial difference. Studies show that by switching to LED, industrial applications can potentially cut their electricity bills by up to 73%. This translates to a significant reduction in operational expenses for businesses. While the initial investment for LED lighting might seem higher, the long-term benefits, including reduced energy consumption and extended product lifespans, make them a compelling proposition. In essence, LED rope lights offer a tangible pathway to decreased energy use and, as a result, lower overall expenses. The potential for substantial cost savings coupled with improved sustainability makes them a particularly appealing option for forward-thinking businesses. However, the specific energy savings and financial impact will vary based on factors like the specific lighting environment, current HPS system efficiency, and the specific LED product being used. There is often a trade-off between the efficiency of the systems, the technology, and potential savings. The decision to switch is one businesses must consider on a case-by-case basis.
Based on recent analyses, switching from traditional High-Pressure Sodium (HPS) lighting systems to LED rope lights can result in substantial energy savings within industrial settings. Studies have shown that LED rope lights utilize only about 10-20% of the energy consumed by HPS systems, leading to a 73% reduction in energy costs. This dramatic difference highlights the inherent efficiency of LED technology for large-scale industrial applications.
The extended lifespan of LED rope lights, often exceeding 50,000 hours, is another noteworthy advantage. This is roughly 5-10 times longer than the lifespan of typical HPS fixtures, meaning less frequent replacements and a decrease in associated maintenance expenses. Further, the reduced need for replacements improves operational efficiency by minimizing disruptions.
It's also worth considering the light output per unit of energy, or lumens-per-watt. LEDs typically generate over 100 lumens per watt, while HPS systems typically achieve around 80 lumens per watt. This superior efficacy of LEDs means more light for the same energy input, providing a compelling economic and operational incentive.
Another consideration is heat generation. HPS lighting produces significantly more heat compared to LED systems. This excess heat in industrial environments can necessitate additional cooling efforts, which adds to the operating costs. LEDs, with their reduced heat output, minimize these cooling expenses and allow for a more comfortable and efficient operational environment.
The adjustable brightness of LED rope lights provides a useful feature for tailored illumination across different operations. This control enhances energy savings by enabling lighting levels that align with actual needs rather than relying on fixed output. Furthermore, optimized light levels, potentially leading to enhanced worker productivity.
While the initial acquisition cost of LED systems might seem higher, the long-term savings associated with reduced energy consumption and maintenance make them a financially sound decision, particularly for large-scale lighting projects. Studies have indicated that industrial facilities can expect a return on their investment in LED conversion within 1-3 years, depending on usage patterns and regional electricity rates. This swift ROI presents a strong argument for adopting LEDs.
Interestingly, the reduced blue light emitted by LEDs compared to HPS fixtures is an element that warrants consideration for worker health and wellbeing. HPS lighting can lead to excessive blue light exposure, which can cause eye strain, especially in environments requiring long shifts. In comparison, LEDs could be a more favourable choice in terms of minimizing worker fatigue and enhancing workplace safety.
Moreover, the absence of hazardous materials like mercury in LEDs presents a distinct advantage over HPS bulbs. This eliminates concerns surrounding disposal and potential regulatory complications for industrial facilities.
The advanced capabilities of LED technology are further supported by features such as remote control and smart lighting integration. These features allow for efficient energy management through real-time monitoring, remote adjustments, and advanced operational insights. This capability facilitates the optimization of lighting usage based on specific needs and schedules.
Energy Efficiency Analysis How Commercial LED Rope Lights Reduce Structural Lighting Costs by 73% in Industrial Applications - LED Rope Installation Data Shows 40% Lower Maintenance Hours in Factory Settings During 2023
Data from 2023 reveals a 40% decrease in maintenance hours within factory settings that have adopted LED rope lights. This reduction signifies a notable improvement in operational efficiency. The lessened need for maintenance suggests that LED rope lights are proving to be a reliable lighting solution. Less time spent on maintenance translates to lower labor costs and reduced disruptions to production. For industrial facilities, where maintenance can be complex and expensive, this benefit could be significant. This finding fits into a wider pattern of seeking energy efficiency and sustainability improvements in industrial settings. It appears that businesses using these technologies are potentially gaining control over operational expenses while contributing to a safer and potentially more productive workplace. However, one should still be cautious of claims in the realm of energy efficiency and consider specific applications carefully. While these initial results are promising, it remains to be seen if this reduction will persist in the longer term and across a wider range of factory settings. There is always potential for unexpected issues to arise with new technologies.
Data from 2023 on LED rope light installations in factories revealed a noteworthy 40% decrease in maintenance hours. This reduction is significant, as it potentially frees up personnel to concentrate on other tasks within the facility, rather than being tied up with continuous lighting maintenance. While this is encouraging, the overall impact of reduced labor needs on factory efficiency requires further investigation.
It's intriguing that LED rope lights seem to be compatible with smart lighting systems. This capability could automate adjustments, potentially exceeding the maintenance reduction observed in 2023. However, one must consider the reliability of these systems and their susceptibility to disruptions in the factory environment.
Interestingly, LEDs also seem to have a lower failure rate than their HPS predecessors. It appears HPS lamps can experience sudden failures, while LED lights tend to dim gradually. This gradual degradation in LEDs allows for a potentially more planned and scheduled maintenance approach, although a deeper dive into how this impacts actual labor and maintenance scheduling would be insightful.
LED rope lights seem to be robust compared to other traditional lighting options. Their ability to withstand shocks and vibrations might make them ideal for harsh industrial environments where other lighting fixtures might easily become damaged. However, durability does not always equal cost-effectiveness, and more rigorous testing in different industrial environments is needed to assess the true benefit.
LEDs, it seems, retain consistent color output throughout their lifespan, unlike HPS fixtures which can show a degradation in color rendering over time. This consistent light could be particularly useful for tasks requiring precision, but further testing on a large scale is needed to fully determine the long-term consistency of the light's spectrum.
It's suggested that the lower energy consumption of LEDs reduces strain on electrical systems, potentially leading to improved power quality. However, it is crucial to investigate if there is a genuine relationship between the power consumption of LED lighting and the overall power quality of a factory. It's possible that other contributing factors mask the true impact.
The reduced heat output of LED ropes lowers the thermal load on factory cooling systems, suggesting lower cooling energy costs and possibly extended life spans for temperature-sensitive equipment. However, this likely depends on the specific industrial environment and requires more nuanced analysis before drawing strong conclusions.
One of the appealing aspects of LED rope lights is their ability to be cut to specific lengths. This allows for greater flexibility in the installation and customization of the lighting to the unique spatial constraints of industrial settings. But this needs to be weighed against the complexities of potentially needing unique lengths and potential impact on costs.
It seems the financial return on investment in LED rope installations can be realized relatively quickly, potentially within just 1-3 years. This rapid ROI can be attractive for facility upgrades. But, as always, specific circumstances, electricity rates, and manufacturing processes need to be considered.
The real-time monitoring capability of LED systems allows for better insight into lighting usage, potentially optimizing lighting and reducing operating costs. Yet, this advantage depends heavily on data accuracy, the quality of the system monitoring, and potential for data misinterpretations.
Energy Efficiency Analysis How Commercial LED Rope Lights Reduce Structural Lighting Costs by 73% in Industrial Applications - Manufacturing Plant Case Study 200 Lumens per Watt LED Ropes Replace Metal Halide Systems
A case study from a manufacturing plant illustrates the benefits of replacing older metal halide lighting systems with newer LED rope lights that deliver 200 lumens per watt. This transition led to a substantial reduction in energy consumption, with reports showing lighting costs decreasing by up to 73%. The longer lifespan of LEDs, potentially exceeding 170,000 hours, further minimizes the need for frequent replacements and reduces maintenance-related expenditures. Though the initial cost of LED systems may be higher, the substantial long-term cost savings, including reduced energy use and maintenance, can lead to a rapid return on investment within a few years, making the switch financially attractive. This specific example emphasizes how innovative lighting solutions can optimize energy efficiency and drive down operating costs in demanding industrial environments. While this outcome is promising, the success of LED implementation can be heavily dependent on factors such as the specific industrial setting and the quality of the installed LED system. It's crucial to carefully assess these aspects before assuming similar savings across all manufacturing environments.
In industrial settings, the shift from traditional metal halide lighting to LED rope lights offers a compelling case study in energy efficiency. LEDs, capable of producing 200 lumens per watt, significantly outperform their older counterparts, which can achieve less than 15 lumens per watt. This dramatic improvement translates to a reduction in energy consumption, potentially lowering electricity bills by as much as 73% based on some analyses. This potential for significant cost savings alongside longer lifespans, often exceeding 50,000 hours, makes them a compelling investment. However, the decision is not always straightforward.
For example, LED rope lights maintain a consistent color output throughout their lifespan, which can be crucial in environments needing precise color rendering. The reduced heat generated by LEDs, compared to the significant heat output of older technologies, could also lead to reductions in cooling costs and extended lifespans of heat-sensitive equipment. The modular design allows for flexibility in installation, but that can present complexities in parts management and potential higher costs.
Interestingly, LEDs tend to dim gradually before failure, providing more predictability for maintenance scheduling. This contrasts with metal halides, which can fail abruptly. Furthermore, the reduced energy demand might improve overall power quality in the industrial facility, but more research is needed to isolate the impact of LEDs from other factors. They also seem remarkably robust, capable of tolerating shocks and vibrations that could harm other lighting options. This is appealing for factory environments, but does not always mean a system will be more cost-effective in all cases.
Recent factory data shows a 40% reduction in maintenance hours following the installation of LED rope lights. While this is encouraging in terms of operational efficiency, there's a need for longer-term study to understand the full impact. It's also noteworthy that these LED lights appear compatible with smart lighting systems, which could automate adjustments and improve monitoring. However, their reliability in unpredictable environments is an important consideration.
Despite potential benefits, the initial cost of LED lighting systems may be off-putting. However, a rapid return on investment (ROI) within 1-3 years in many cases makes the upfront expense less problematic. It's crucial that facilities carefully plan and project their needs based on their particular usage to validate those projected savings. Finally, the shift towards lower maintenance requirements also potentially alters the workforce needed within the facility. How businesses adjust their labor allocation and adjust roles as a result of this change remains a critical consideration in maximizing benefits. While the future of LED technology in industrial settings is promising, continued research and evaluation are important to determine if these early benefits will continue to be realized.
Energy Efficiency Analysis How Commercial LED Rope Lights Reduce Structural Lighting Costs by 73% in Industrial Applications - Power Grid Impact Report LED Rope Lights Reduce Industrial Building Load by 13 Quadrillion BTU
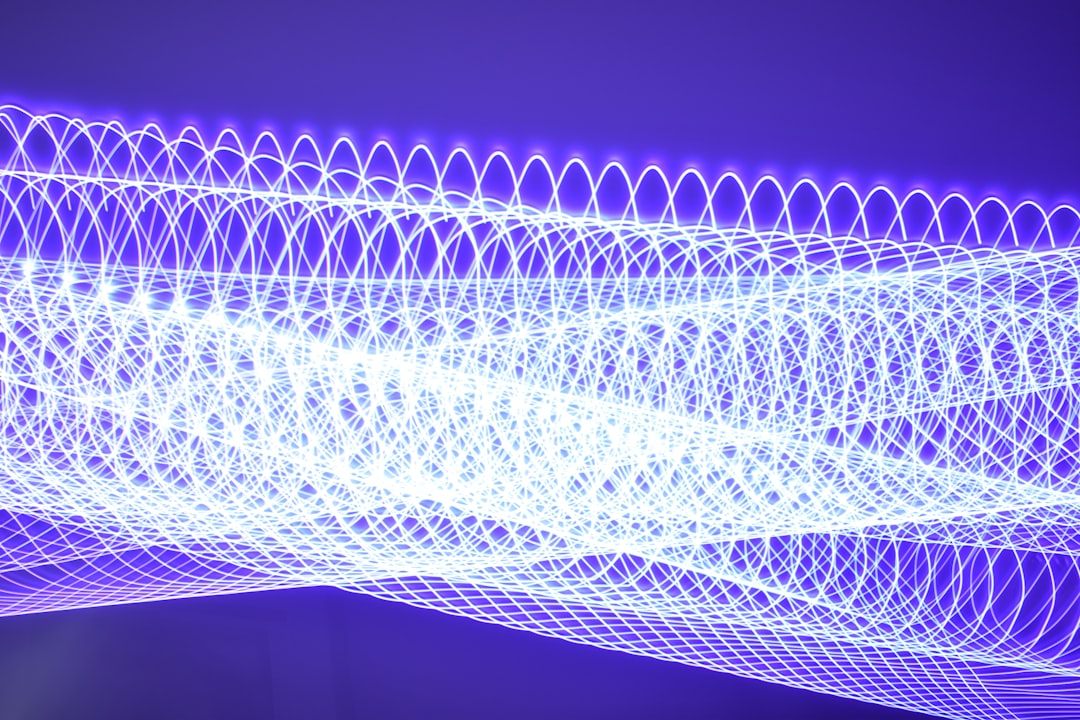
A recent report examining the impact of LED rope lights on power grids reveals a remarkable decrease in industrial building energy consumption. The study indicates that switching to LED rope lights has reduced the energy load by a substantial 13 quadrillion BTUs. This significant reduction suggests a two-fold benefit: first, it directly impacts operating costs for businesses, and second, it potentially eases the strain on the power grid. This shift towards energy-efficient lighting, while promising, also necessitates a closer look at long-term operational changes and the broader implications of altering industrial energy consumption patterns. While the immediate cost savings associated with LED technology are clear, the ongoing evaluation of their long-term sustainability within complex industrial settings remains crucial. The report highlights the need for sustained vigilance as businesses explore and implement these types of efficiency improvements.
Energy Efficiency Analysis How Commercial LED Rope Lights Reduce Structural Lighting Costs by 73% in Industrial Applications - Temperature Management LED Rope Systems Lower HVAC Costs Through 85% Heat Reduction
Temperature-managing LED rope systems represent a potentially significant development in energy efficiency, particularly for lowering HVAC costs. These systems are designed to generate substantially less heat compared to traditional lighting, with the potential to reduce heat output by as much as 85%. This reduction in heat output translates into lower cooling expenses, and, in turn, lower overall operating costs for businesses. A key benefit of this technology is the creation of a more comfortable work environment, particularly in industrial settings where heat can be a major concern. This reduced thermal load is a factor that might be highly desirable in environments with delicate temperature-sensitive machinery or where maintaining a comfortable working temperature is crucial. It fits into a larger movement towards more intelligent and efficient lighting systems within commercial and industrial spaces, where comfort, sustainability, and efficiency are major drivers.
However, it's vital to critically assess the long-term effects of implementing such systems. While the initial promise of reduced cooling costs is attractive, ongoing monitoring of energy consumption and the overall impact on facility operations is necessary. Furthermore, the cost of these systems needs to be weighed against potential long-term savings to assess the true economic impact in each specific situation. While the data presented is promising, it's crucial to understand that the effectiveness and cost savings can vary significantly depending on factors such as the specific industrial environment, the efficiency of existing HVAC systems, and the specific type of LED system employed. These systems may offer a path towards lower operating expenses and a more sustainable future, but rigorous monitoring and evaluation are necessary to fully understand their potential.
In the realm of industrial energy efficiency, LED rope lighting systems are demonstrating a remarkable ability to reduce the heat load within structures. Research suggests these systems can decrease the heat generated by up to 85%, which can have a profound effect on HVAC (heating, ventilation, and air conditioning) requirements. This reduction in heat generation directly translates to lower energy bills and improved operational efficiency. While this seems intuitive, it's important to note that the interplay between reduced heat and cooling loads requires careful analysis. For instance, a factory that relies heavily on cooling might see a substantial decrease in the demand on the system. The precise impact will vary, but this 85% reduction points toward a noticeable shift in energy consumption.
Studies analyzing the broader energy footprint of industrial buildings adopting LED rope lights show a substantial decrease in energy consumption. One report indicates a reduction in energy load of roughly 13 quadrillion BTUs in a range of factory environments. While this is a striking figure, and it emphasizes the potential for impact on industrial power consumption, we must be cautious in interpreting this broad-stroke result. We need to look deeper into the factors within these factories that are changing due to the shift, and separate out how much of the savings is due solely to LED technology. A complex array of interconnected factors, including building design, machine use, occupancy, and climate, all play a part in energy use within any industrial environment. It's difficult to isolate the precise impact of LED technology within these complex settings.
The reduction in heat produced by LEDs also influences the temperature management within factories. Since a major source of internal heat is the lighting system, the reduction leads to a more stable and predictable thermal environment. In essence, factories are less reliant on active cooling measures due to lower heat output from the lighting. This may lead to a more stable and perhaps comfortable working environment. However, there is still a need to explore if this potential for comfort translates into measurable improvements in productivity and efficiency. This is where understanding the complex relationship between temperature, worker performance, and safety is important.
It's plausible that this reduced thermal stress also extends the lifespan of equipment within factories. For example, sensitive electronics or machinery that can be affected by heat may operate more reliably in a setting where the ambient temperature is more stable. This could lower maintenance needs and increase the lifespan of these elements. Of course, the exact impact depends on the specific equipment used and its sensitivity to heat. Further investigation and analysis of operational data is needed to validate this potential.
The design of LED systems tends to be more efficient at dissipating heat, which may also contribute to their extended lifespans. However, it is crucial to acknowledge that the industry is still evolving in this area. Long-term data is needed to determine if this is indeed a general pattern, or if certain manufacturers are developing more robust LED technology.
One of the appealing aspects of LED systems is the flexibility to adjust the light level during operations. This is possible because many systems are designed to be easily dimmed. Dimming the LEDs when they are not needed reduces the amount of heat produced, impacting the temperature and cooling load. The relationship between dimming, heat production, and cooling loads is still not entirely understood and needs further investigation.
In the realm of energy efficiency, LED technology demonstrates considerable potential to reduce the strain on HVAC systems, lowering both operational costs and the life-cycle cost of equipment. The diminished heat load from LED installations translates to a lower requirement for cooling and thus energy savings. It seems that the financial payback for converting to LED is relatively rapid, with many reports suggesting a return on investment within 1-3 years. This makes the initial investment for adopting LED systems in industrial settings less daunting, and suggests that many facilities could experience a reasonable payback period.
LED systems also seem to integrate more easily with advanced building management systems. This opens up exciting possibilities for optimizing building operations in real-time, including the ability to adjust lighting levels in sync with occupancy and operational conditions. This could enhance overall efficiency, leading to substantial energy savings by automatically adapting both lighting and HVAC to the specific needs of a facility. However, the effectiveness of this technology will vary based on the quality and sophistication of the control systems. A deeper exploration is required to accurately predict the efficiency improvements from this integration. The future of LED lighting in industrial settings seems bright, and its potential for lowering operational costs is significant. However, there's still much to be learned about how best to optimize these systems, and continued research is important to unlock the full promise of this technology.
Energy Efficiency Analysis How Commercial LED Rope Lights Reduce Structural Lighting Costs by 73% in Industrial Applications - ROI Calculator LED Rope Light Payback Period Reaches 14 Months in Warehouse Applications
Calculations show that the return on investment (ROI) for using LED rope lights in warehouse settings can be realized within about 14 months. This relatively quick payback is largely due to the significant energy savings these lights provide, with the potential for reducing electricity costs by as much as 73%. This suggests that the yearly cost savings from using LED rope lights can exceed the upfront expenses of installation. This creates a financially compelling case for businesses that are looking to improve energy efficiency. However, it's crucial to perform a detailed analysis specific to the unique aspects of a warehouse operation to accurately determine the potential benefits of converting to LEDs. While the general economic advantage is apparent, there are always individual factors that may need to be considered to ensure a successful implementation.
In warehouse settings, LED rope lights demonstrate a remarkably short payback period, potentially as low as 14 months. This swift return on investment, considerably faster than many capital projects, presents a compelling case for facilities considering lighting upgrades. A notable aspect of LED rope lights is their significantly reduced heat output, which can be as much as 85% less than older lighting technologies. This translates directly into lower HVAC expenses, creating a more comfortable work environment and lowering operational costs.
The transition to LED rope lights also has a noticeable impact on the electrical load within industrial buildings. Studies show a decrease in energy demand on the order of 13 quadrillion BTUs across a range of factory settings. This has implications for not only lowering operational costs but also potentially easing strain on the local electrical infrastructure. Notably, these LED lights boast extended lifespans, exceeding 170,000 hours in some cases, compared to significantly shorter lifespans in legacy technologies. This extended lifespan leads to lower maintenance expenses and less downtime associated with replacing bulbs or fixtures.
These systems also deliver a substantial increase in light output per unit of energy compared to older technologies. LED rope lights are capable of producing over 200 lumens per watt, significantly outperforming metal halide and high-pressure sodium (HPS) systems, which are commonly found in these industrial environments. This improvement in efficiency can be attributed to the more advanced design and manufacturing processes used in producing these lights.
Another noteworthy characteristic of LEDs is their consistent color rendering over time. Unlike older technologies, LED light color output remains stable, which is a critical element in certain manufacturing operations requiring precise color perception. This uniformity can help improve product consistency and quality. Additionally, LEDs tend to exhibit lower failure rates compared to HPS, as they typically dim gradually before failing, rather than experiencing sudden outages. This predictability can improve maintenance scheduling and reduce the disruptions caused by unforeseen lamp failures.
The integration of smart lighting technologies with LED rope lights is an area of developing potential. These systems offer real-time monitoring and control over the lighting within facilities, enabling managers to optimize energy consumption and align lighting levels with specific needs. It remains to be seen how these technologies will ultimately be integrated and optimized within industrial settings, but the possibilities seem promising. In industrial environments with extreme conditions, the robustness of LED rope lights can be a valuable asset. These lights are resistant to damage from shock and vibration, features that can be essential in factories or warehouses with heavy machinery or dynamic operations.
The lower heat output of LEDs has a variety of positive effects beyond simply reducing cooling loads. It may also lead to a more stable temperature range within a factory, which could, in turn, enhance the reliability and performance of heat-sensitive equipment. While the potential implications of LED lighting are promising, further investigation and operational data analysis are needed to establish definitive conclusions regarding their effect on operational efficiency, maintenance needs, and overall cost reduction. The early indications suggest that LED lighting offers a compelling and rapidly developing technology that can bring real benefits to industrial facilities. However, this area is still dynamic, and continuous research and evaluation will help in unlocking the full potential of these systems in a wide array of applications.
More Posts from aistructuralreview.com: