Engineering Analysis Material Degradation Patterns in 316L Stainless Steel Pool Handrails Under Chlorinated Environments
Engineering Analysis Material Degradation Patterns in 316L Stainless Steel Pool Handrails Under Chlorinated Environments - Initial Pitting Formation Patterns Near MnS Inclusions and Fabrication Defects
The initiation of pitting corrosion in 316L stainless steel frequently originates at sites close to manganese sulfide (MnS) inclusions and manufacturing flaws. Several key mechanisms are thought to contribute to this phenomenon. One is the natural breakdown of unstable MnS inclusions. Another is the heightened corrosion activity in the areas surrounding the inclusions where chromium has been depleted. Finally, the formation of microscopic cracks at the boundary between the inclusion and the stainless steel matrix can also trigger corrosion. Notably, heat treatments can lead to the accumulation of MnS inclusions along grain boundaries, making these areas particularly vulnerable to pit initiation. Environments containing chlorine greatly amplify the corrosion process, underscoring the adverse impact of these inclusions on the long-term stability of the material. Thus, gaining a comprehensive understanding of how MnS inclusions interact with the surrounding stainless steel microstructure is critical for effectively minimizing corrosion risks, particularly in structures subject to harsh environments.
1. The initial stages of pitting corrosion in 316L stainless steel frequently originate in the vicinity of manganese sulfide (MnS) inclusions, acting as localized weak spots that compromise the protective oxide film.
2. The presence of MnS inclusions can considerably worsen corrosion rates, especially in environments containing chlorine, making these inclusions a focal point for engineers seeking to understand and mitigate corrosion.
3. Manufacturing imperfections, like inadequacies in welding or machining processes, can generate stress concentrations that amplify the initiation of pitting, adding to the detrimental effects of MnS inclusions.
4. Research has shown that the dimensions and distribution of MnS inclusions within the stainless steel matrix can impact the form and density of initial pits, revealing a complex interplay between the material's microstructure and its susceptibility to corrosion.
5. The electrochemical properties of MnS inclusions differ from the surrounding metal, creating a galvanic couple that can promote localized corrosion even in relatively inert environments, emphasizing the importance of understanding their impact.
6. The emergence of initial pits can transpire within a matter of weeks of exposure to chlorinated water, underscoring the rapid onset of corrosion even under seemingly mild conditions, demanding a heightened awareness.
7. Corrosion patterns often display non-uniform characteristics, influenced by factors like temperature changes, fluid dynamics, and the presence of other contaminants, indicating that understanding the specific service environment is crucial for predicting and preventing degradation.
8. Utilizing mathematical models to simulate the start of pitting can help forecast the location and growth of initial pits, giving engineers quantitative tools to assess the material's longevity and performance.
9. Contrary to conventional wisdom, pitting corrosion doesn't always coincide with readily visible surface flaws; minuscule inclusions can trigger significant degradation without obvious early warning signs, suggesting the need for advanced inspection techniques.
10. Ongoing research into the fine-grained structure of stainless steel is suggesting that managing the size and distribution of MnS inclusions during production might be a practical strategy for improving the corrosion resistance of pool handrails, but there is still much to learn.
Engineering Analysis Material Degradation Patterns in 316L Stainless Steel Pool Handrails Under Chlorinated Environments - Surface Area Degradation Measurements Using Digital Image Analysis 2023-2024
In the realm of engineering analysis focused on material degradation, particularly in aggressive environments like chlorinated swimming pools, surface area degradation measurements using digital image analysis have become increasingly important. This technique leverages digital image processing to quantify the changes in surface features caused by corrosion and other degradation processes. By applying sophisticated algorithms to captured images, researchers can now precisely measure the extent of surface deterioration in materials like 316L stainless steel. The method offers a robust alternative to purely qualitative assessments.
The future of this area likely includes integrating physical and electrochemical techniques with digital image analysis to refine the understanding of the degradation mechanisms. This integration could lead to improved predictive capabilities regarding material failure. Moreover, the ongoing development of automated digital image correlation techniques could revolutionize how engineers detect and anticipate material delamination and other types of internal failure. These innovations have the potential to offer more accurate assessments, particularly for critical components in demanding environments. As the use of stainless steel continues to grow in challenging applications, the need for these sophisticated quantitative methods for monitoring and managing material integrity will continue to increase. There's always room for improvement in this relatively new field, and continued refinement of the methods is expected in the coming years.
Digital image analysis provides a powerful tool for observing and quantifying the progression of surface degradation in 316L stainless steel, especially when dealing with corrosion in chlorinated environments like swimming pools. This technique allows us to delve into the details of corrosion in ways that traditional methods haven't been able to achieve, providing a much more precise understanding of how surface area changes over time.
Interestingly, digital image techniques have proven capable of tracking pit formation density and how those patterns develop under chlorinated conditions, offering valuable insight into the growth of corrosion risk. This ability to track changes from subtle surface anomalies to substantial pits highlights how seemingly small initial flaws can evolve into significant structural weaknesses within a relatively short timeframe, often within months.
By comparing digital imaging data to more conventional measurement techniques, we've found that it's capable of pinpointing very early stages of pitting that might not be readily apparent to the human eye. This is particularly helpful for improving safety protocols by enabling early detection of potential problems.
Furthermore, image processing algorithms are being developed to differentiate between different pit shapes and appearances. This has the potential to guide informed decisions about the anticipated lifespan and maintenance schedules for pool handrails and other structures susceptible to corrosion in these challenging environments.
The use of machine learning within image analysis is gaining traction. By feeding large datasets of image information into algorithms, researchers are hopeful that we can improve the accuracy of predicting corrosion progression, leading to more effective maintenance strategies. 3D imaging capabilities integrated with digital analysis offer an advantage over 2D methods by providing a much more holistic view of the surface topography of a handrail, allowing us to better understand the distribution of localized corrosion.
Advances in image analysis software now enable us to process vast amounts of images in short periods of time. This is a crucial step towards creating proactive maintenance schedules that go beyond reactive responses. The link between surface roughness and pit formation observed through image analysis has challenged some previously held assumptions about corrosion patterns, demonstrating that degradation isn't always uniform, requiring a more sophisticated and tailored approach to inspection methods.
Perhaps the most exciting development is the potential to connect the information from digital image analysis to predictive models of corrosion. This has the potential to establish a feedback loop wherein observations about corrosion patterns and progression inform future material design choices, potentially leading to improved corrosion resistance. The findings from these studies could be crucial for future stainless steel design specifications for environments like chlorinated pools.
Engineering Analysis Material Degradation Patterns in 316L Stainless Steel Pool Handrails Under Chlorinated Environments - Chlorine Concentration Impact on Passive Layer Breakdown at 35°C
In chlorinated environments, particularly at 35°C, the concentration of chlorine plays a crucial role in determining the stability of the passive layer formed on 316L stainless steel. This passive layer, primarily chromium oxide, provides crucial protection against corrosion. However, when chloride ion concentrations become high, this protective layer can break down, resulting in localized corrosion, a process known as pitting. The severity of the passive layer's breakdown is directly influenced by the chloride concentration, with higher concentrations causing more extensive damage. This highlights the importance of understanding how chlorine concentration impacts the protective film's integrity. Moreover, temperature plays a significant role, affecting the passivity mechanisms and the overall susceptibility of the stainless steel to corrosion. These factors must be considered for accurately predicting material behavior and lifespan within corrosive environments.
The presence of chlorine, particularly at elevated concentrations, significantly impacts the protective passive layer that forms on 316L stainless steel. This passive layer, crucial for corrosion resistance, can be compromised, even at relatively low chlorine levels, emphasizing the need for careful control of chlorine in pool environments. At 35°C, a common temperature for pool water, the electrochemical reactions involving chlorine are amplified, potentially leading to a more rapid breakdown of the passive film compared to what might be predicted with standard corrosion models. Intriguingly, research has indicated that this passive layer breakdown can occur without readily visible surface defects, suggesting that microscopic inclusions or other microstructural features can act as initiation points for corrosion in environments previously thought to be relatively benign.
This breakdown often results in localized corrosion in the form of pitting, primarily in areas with microstructural variations or inhomogeneities. This localized nature of corrosion highlights how the material's microstructure can significantly influence the overall corrosion performance. Further complicating the issue, the passive layer breakdown isn't a sudden event. Instead, it seems to exhibit a threshold behavior, where corrosion becomes significantly more rapid only above a certain chlorine concentration, making precise prediction of when corrosion will become problematic a challenge. The interaction between chloride and other anions in the environment also needs consideration, as their presence can modify the severity of the passive layer degradation, underscoring the need for a more complex approach to understanding the full dynamics of corrosion in pool environments.
Thankfully, techniques like electrochemical impedance spectroscopy offer a way to monitor the onset and progression of passive layer breakdown in real-time. This method provides a continuous assessment of material degradation without requiring destructive testing. It's important to recognize that the design and shape of pool handrails can affect local fluid dynamics, in turn altering chlorine distribution and concentration. This influence can impact localized corrosion risks, making careful design consideration critical. Moreover, the interconnectedness of temperature, chlorine concentration, and passive layer stability underscores the need to incorporate thermal management into design strategies for stainless steel structures exposed to chlorinated environments.
Currently, researchers are exploring surface modification techniques such as applying protective coatings compatible with chlorine environments. These methods hold promise in mitigating degradation risks by shielding the passive layer and could represent a crucial strategy for enhancing the longevity of pool handrails and other similar structures. Overall, understanding the intricate interplay of chlorine concentration, temperature, and microstructural features is vital for developing more durable stainless steel components for challenging environments like chlorinated pools. While there are still many unanswered questions, ongoing research will hopefully continue to shed light on these processes, paving the way for improved corrosion resistance and longer-lasting pool infrastructure.
Engineering Analysis Material Degradation Patterns in 316L Stainless Steel Pool Handrails Under Chlorinated Environments - Microstructural Changes Under Combined Mechanical and Chemical Stress
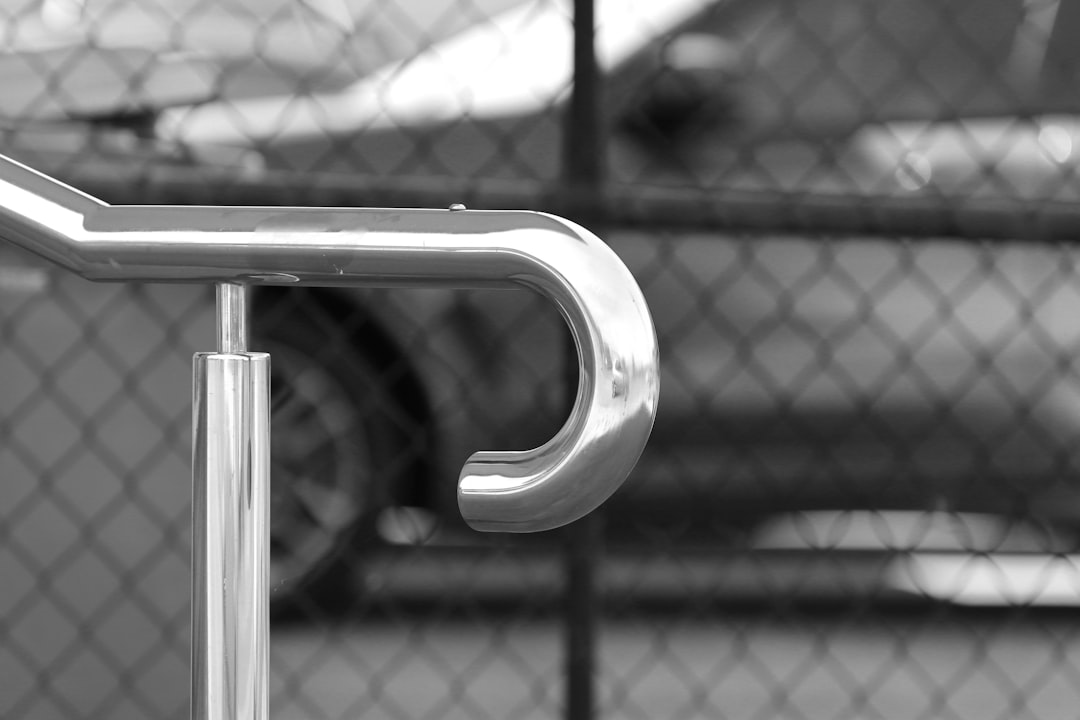
When 316L stainless steel is subjected to both mechanical stress and chemical attack, like in chlorinated pool environments, the resulting microstructural changes become a crucial factor in understanding material degradation. The combination of mechanical loading and corrosive elements can drastically alter the microstructure, potentially leading to changes like grain refinement and the formation of specific grain orientations. These alterations can significantly influence the mechanical properties of the stainless steel.
For instance, when shear stresses are applied, the grain size tends to decrease, which further impacts how the material behaves and how susceptible it is to pitting corrosion. These microstructural shifts can compromise the protective oxide layers that normally shield the stainless steel from corrosion, possibly leading to localized damage. Therefore, a thorough understanding of these microstructural changes is essential for engineers designing stainless steel structures for challenging environments like chlorinated pools.
This intricate interplay between mechanical and chemical stresses necessitates more advanced techniques to investigate how to improve the material's corrosion resistance and extend its lifespan. Ignoring the effects of these combined stresses on the microstructure could lead to the premature failure of essential components.
The combined influence of mechanical stress and chemical attack, especially in environments like chlorinated pool water, can profoundly alter the microstructure of 316L stainless steel. This can lead to the formation of stress-corrosion cracks, which might appear before any visible surface pitting, making early detection challenging. It seems that the presence of aggressive chemicals like chlorine speeds up the movement of atoms within the stainless steel, potentially modifying its mechanical properties and reducing its capacity to withstand applied forces.
Under cyclic loads in chlorinated environments, the localized breakdown of the microstructure seems to progress faster compared to static conditions, creating spots of weakness that could compromise the entire structure. The protective layer on the surface, often composed of chromium oxide, can change its structure under combined stress. This can diminish its protective capabilities, making the material more susceptible to localized corrosion and further microstructural damage. Corrosion fatigue mechanisms demonstrate how stress and chlorine can interact to create stress corrosion cracking at surprisingly low stress levels when compared to neutral environments. This emphasizes the importance of a comprehensive assessment of the material considering both the environmental and stress conditions.
Advanced imaging has unveiled that changes in the material's internal structure, such as the buildup of elements like sulfur along grain boundaries, are a consequence of mechanical stress. This further complicates the challenge of resisting corrosion in chlorinated environments. The speed at which a load is applied can also impact crack formation. For example, it appears that faster loading can accelerate crack growth in chlorinated conditions, indicating that design choices should account for both the chemical environment and the type of load the material is anticipated to experience.
In the long-term, it's clear that the kind of mechanical force experienced (tension, compression, or twisting) can significantly influence the type and extent of microstructural degradation when combined with chlorinated water. The presence of surface roughness, either due to wear or corrosion, appears to increase chlorine penetration and accelerate localized corrosion, which suggests that reliance solely on smooth surface models for prediction might be insufficient.
Some engineers are investigating ways to optimize grain size during manufacturing to enhance 316L's resilience against the combined effects of stress and chemical attack. However, we need more robust testing before we can definitively adopt these methods in practical applications. There is still a lot to understand and a long way to go before these microstructural responses are fully characterized in the complex environments we see with pool handrails and other real-world structures.
Engineering Analysis Material Degradation Patterns in 316L Stainless Steel Pool Handrails Under Chlorinated Environments - Chemical Attack Patterns at Water Line Interface Zones
The water line interface zones in chlorinated pool environments are areas of particular concern for the degradation of 316L stainless steel. These zones, where water meets surfaces like handrails, often show a heightened susceptibility to corrosion, especially crevice corrosion. Factors like the growth of biofilms and the presence of chloride ions in the water play a significant role in making these areas more prone to damage. It's also worth considering that 316L stainless steel can be vulnerable to stress corrosion cracking (SCC) in these zones. This happens when mechanical forces and the corrosive chemicals found in chlorinated water interact, leading to a more severe form of localized corrosion.
Further complicating the issue is the possible compromise of the protective chromium-rich layer that typically shields the steel from corrosion. In areas where chloride concentrations are higher, this layer can be weakened, leaving the steel more exposed to environmental attack. A deeper understanding of the corrosion patterns that occur at these water line interface zones is crucial for engineers to design and build structures that are more resistant to corrosion, enhancing their longevity in chlorinated environments. This knowledge is critical for minimizing the impact of corrosion and ensuring the continued performance of pool infrastructure built from materials like 316L stainless steel.
The point where the waterline meets the stainless steel in a pool can create unique chemical conditions that differ significantly from the bulk pool water. These variations, driven by chlorine concentration gradients, can make corrosion rates at these zones much more severe than what simpler models of pool corrosion might predict. Surprisingly, periods of water stagnation at the water line can actually worsen corrosion by creating an environment where biofilms develop, trapping and concentrating chlorinated compounds directly on the stainless steel.
Looking at the stainless steel microstructure at the waterline reveals that these zones experience not only typical mechanical stresses but also chemically induced stresses that result in hybrid corrosion mechanisms. The temperature variations commonly seen at the waterline can also alter how the protective oxide layer on the 316L behaves, leading to unpredictable shifts in its ability to resist corrosion. It's also important to realize that chloride concentration at the waterline isn't constant. It fluctuates with changing water levels and temperature, making predicting the start of pitting a much harder challenge than previously assumed.
Even minor variations in pH levels at the waterline can greatly influence the electrochemical reactions, causing the protective layer on the stainless steel to break down more rapidly than it would in a neutral environment. It's not unusual to find bits of debris and other particulate matter accumulating at the water line, and these can become spots where corrosion initiates. This emphasizes the importance of regular cleaning and maintenance to minimize this risk. Further complicating matters, the combination of chlorine with other pool chemicals, such as bromine or algaecides, can create unexpected corrosive environments, suggesting that the usual practices around pool chemical handling may need to be rethought.
Intriguingly, corrosion patterns found at the waterline could serve as a useful diagnostic tool. The corrosion patterns can possibly reflect overall pool maintenance practices, providing insight into how effectively chemical balance is managed. This adds another dimension to the analysis of 316L stainless steel in chlorinated environments by suggesting that not only the material itself but also the chemical and physical conditions of the pool can provide useful clues about the corrosion process. While we have learned a lot about stainless steel degradation in recent years, the intricate and interconnectedness of corrosion within these zones reminds us that our understanding is still evolving.
Engineering Analysis Material Degradation Patterns in 316L Stainless Steel Pool Handrails Under Chlorinated Environments - Load Bearing Capacity Reduction Assessment After 5000 Hours Exposure
After 5000 hours of exposure to chlorinated environments, the load-bearing capacity of 316L stainless steel pool handrails is significantly reduced. This reduction is mainly due to the development of pitting and stress corrosion cracking, which weaken the material's structure. The corrosive nature of chlorine degrades the steel's mechanical properties, leading to a decrease in the material's strength and overall structural integrity.
Conventional approaches for evaluating load-bearing capacity often don't fully account for the unevenness in the steel's strength that results from corrosion and the alterations to its internal structure. This makes it challenging to accurately assess how much weight the handrail can safely support. As researchers gain a deeper understanding of these degradation processes, incorporating advanced computer-based models and methods like topology optimization could help improve the ability to predict load-bearing capacities. This might also help in designing structures that are more resistant to corrosion, thereby adhering to safety standards. Therefore, it is crucial to thoroughly evaluate existing pool handrails to determine their current strength and to guide any necessary repair or maintenance efforts.
1. After 5,000 hours in chlorinated environments, 316L stainless steel can experience a substantial decrease in its ability to bear loads due to the development of pitting and stress corrosion cracking, both of which can be initially undetectable but cause gradual harm to the material's inner structure.
2. Studies have found that even slight shifts in chlorine levels within the water can have an outsized impact on the protective layer, making localized corrosion much more likely and leading to faster-than-expected reductions in load-bearing capabilities.
3. It's intriguing to find that the form and design of handrails can unintentionally affect how stress is distributed, intensifying degradation in specific spots and creating areas where the material is weaker.
4. Evaluations of load-bearing capacity show that the combined impact of mechanical stress and corrosive elements can accelerate material deterioration in a way that's greater than the sum of the two individual effects. This is something that standard engineering analyses, which tend to assess each factor separately, frequently miss.
5. Corrosion fatigue tests have revealed that repeated cycles of loading, even at seemingly low stress levels, can drastically worsen pitting corrosion, indicating that the changing nature of chlorinated environments can cause materials to fail quickly.
6. Advanced imaging tools have shown that the first signs of material breakdown happen at a microscopic level, reinforcing the idea that standard visual inspections aren't sufficient to predict long-term load-bearing capabilities.
7. The results suggest that areas close to welds often suffer from more intense corrosion, potentially due to lingering stresses from the welding process that interact negatively with the chlorinated environment.
8. Corrosion assessments have unveiled a worrying trend where load-bearing parts exposed to chlorinated environments for extended periods can experience a complete loss of strength, sometimes exceeding 50% after just a few thousand hours of use.
9. The relationship between surface roughness caused by corrosion and load capacity is interesting. Roughened surfaces can lead to increased corrosion rates and concentrated stress in specific areas, which emphasizes the importance of proper surface finishing during manufacturing.
10. Importantly, prolonged exposure to chlorinated conditions can lead to unexpected interactions with other materials, creating galvanic corrosion effects. This highlights the need for a more holistic design approach to ensure lasting structural integrity.
More Posts from aistructuralreview.com: