Essential Skills and Tools for Modern Structural Inspectors A Technical Equipment Proficiency Guide
Essential Skills and Tools for Modern Structural Inspectors A Technical Equipment Proficiency Guide - Advanced Structural Analysis Software Tools Including Computer Aided Design Applications
Modern structural analysis has been transformed by specialized software tools, including computer-aided design (CAD) programs. These tools allow engineers to realistically model and simulate a wide range of physical forces, such as impacts, thermal changes, and vibrations. This capability significantly increases the precision and safety of designs. The complexity of contemporary structures necessitates sophisticated analysis software to ensure designs adhere to industry standards and regulations. For structural inspectors, comprehending advanced analysis and design techniques – and being able to interact with programs like SOFiSTiK and STAAD – is now crucial. The speed and accuracy of design and detailing stages have been improved due to these software applications, offering faster project turnaround and more precise analyses. In the continuously evolving construction landscape, incorporating these advanced tools is no longer optional but vital for preserving the safety and integrity of buildings and structures. It is important that inspectors gain the knowledge required to interpret and validate the results provided by these advanced analytical tools. However, it's crucial to recognize that reliance on software does not eliminate the fundamental need for rigorous design principles and appropriate material selection. The future of structural integrity relies on effectively integrating these digital tools into a broader understanding of structural principles and construction practices.
Sophisticated structural analysis programs offer the ability to simulate intricate loading situations, leading to far more precise predictive models. This is vital for thoroughly evaluating the structural integrity of designs under a wide range of stress conditions, something that was not easily achievable before the widespread adoption of these tools.
The integration of CAD applications fosters real-time collaboration amongst engineering and architectural teams. This means changes made by one party are immediately visible to the others involved, which has the potential to greatly diminish the incidence of design oversights.
Many contemporary analysis tools employ finite element analysis (FEA) methodologies. This involves breaking down complex structures into smaller, manageable components to solve for stresses and strains. This approach often exposes insights that may have been missed using traditional calculation methods.
Some advanced software programs incorporate machine learning techniques to forecast possible points of failure based on historical data. This can contribute to more effective preventative maintenance, reducing disruptions and unexpected downtime.
CAD applications with parametric modeling features provide the ability to dynamically modify design aspects. This streamlined approach enables fast-paced design revisions, leading to more creative and effective structural solutions.
The rise of cloud-based platforms for structural analysis allows engineers access to powerful computing capabilities remotely. This broadens access to advanced tools that previously required substantial local infrastructure investment.
Modern software tools often have multi-disciplinary integration capabilities. This means structural, acoustical, and thermal properties can be simultaneously analyzed within a single unified model, facilitating a comprehensive assessment of building performance.
A growing number of structural analysis programs now offer augmented reality (AR) features. This provides a visual, 3D representation of complex data sets, improving the clarity and overall understanding of the design during reviews.
The relentless pace of software upgrades poses challenges for inspectors who must continuously adapt to new features and functionalities. This can create knowledge gaps for those who haven't actively kept up with the latest versions.
Some advanced analysis tools incorporate automated reporting features, simplifying the documentation process. This allows inspectors to quickly generate comprehensive reports with minimal manual input, boosting both efficiency and accuracy.
Essential Skills and Tools for Modern Structural Inspectors A Technical Equipment Proficiency Guide - Digital Measurement Equipment From Laser Scanners to Ground Penetrating Radar Systems

Modern structural inspections increasingly rely on digital measurement tools, ranging from laser scanners to advanced ground penetrating radar (GPR) systems. These tools provide inspectors with a more comprehensive understanding of a structure's condition and hidden elements. GPR, for instance, has matured considerably since its development in the late 1980s and early 1990s. Inspectors now have access to equipment with varying configurations, allowing them to adapt to the specific depth and resolution needed for particular assessments. Whether looking for buried utilities or mapping underground infrastructure, GPR's capacity to detect both metallic and non-metallic materials proves incredibly useful. It's important to note that GPR systems often come with user interfaces designed for ease of use and quicker interpretation of the scans, which has definitely sped up the analysis phase of inspections. However, there's always the question of choosing the correct type of GPR system for a given task, as various companies provide a wide array of equipment, each with its own strengths and limitations. It is clear that the integration of these digital tools is becoming essential for structural inspections. These advances, paired with the inspector's understanding of traditional methods, are vital in achieving a more thorough and accurate analysis of structural integrity. The future of ensuring safe and sound structures will depend on an adept inspector's ability to combine these advanced digital capabilities with core knowledge of structural mechanics and materials.
Ground Penetrating Radar (GPR) uses a range of techniques, with the equipment's frequency and setup tailored to specific inspection needs. While single-frequency systems can produce decent results, dual-frequency systems offer more flexibility, using a lower-frequency antenna to scan deeper and a higher-frequency antenna for shallower scans. The rise of GPR in the late 1980s and early 1990s made it a go-to method for inspecting concrete, providing valuable imaging data on the internal structure. It's a versatile tool for detecting various materials, from non-conductive materials like PVC pipes to metal pipes, proving quite useful for pinpointing utilities.
Finding an electromagnetic (EM) locator can range from about $800 to $5,000, while renting one might cost between $700 and $1,500 a month. The Proceq GP8000 is an example of a portable GPR device that aims to make concrete inspections easier and faster using SFCW technology. It's touted for its ability to penetrate deeply and offer high-resolution scans.
However, GPR often works best when combined with other methods. Structural inspectors frequently use it alongside video pipe inspection, leak detection, and 3D laser scanning for a more comprehensive view. GPR is increasingly used in a variety of situations, such as assessing underground infrastructure, helping inspectors to visualize structures that are otherwise hidden. Many GPR systems are designed with user-friendly interfaces to help streamline concrete inspections.
Companies like GSSI offer a wide range of GPR and electromagnetic induction equipment, highlighting the importance of selecting the right tool for each specific inspection. This diversity in equipment choice emphasizes that there's no single, one-size-fits-all solution when it comes to understanding the subsurface using these techniques. Choosing the appropriate GPR system is critical, as it's crucial to get the right balance of penetration depth, resolution, and accuracy for the specific requirements of each inspection. While the technology is improving, we still need a good understanding of the limitations of each method and be thoughtful in choosing the appropriate technology for each inspection situation. It is important to always critically evaluate the outputs of GPR and combine the data with other inspection methods to arrive at the best overall conclusion about the structural integrity of the object being inspected.
Essential Skills and Tools for Modern Structural Inspectors A Technical Equipment Proficiency Guide - Drone Technology and Aerial Photography Equipment for Remote Building Assessment
Drone technology has become increasingly important for structural inspections, especially when conducting remote building assessments. These unmanned aerial vehicles, equipped with high-quality cameras and sensors, provide detailed aerial imagery and data that helps inspectors understand the condition of a structure. The lightweight construction of drones, often using materials like carbon fiber or plastic, contributes to their maneuverability and ability to access hard-to-reach areas, making inspections safer and more efficient. The application of drones is transforming the construction industry, facilitating the use of aerial views for various stages of project development and management. For structural inspectors, knowing how to use these small Uncrewed Aerial Systems (sUAS) for remote sensing and aerial imaging is now a critical skill. While drones offer many advantages, inspectors must be aware of their limitations and ensure data obtained from them is interpreted within the larger context of a structural assessment. The growing adoption of drone technology underscores the need for structural inspectors to adapt their skillset to stay current with industry best practices and ensure the integrity of structures.
Drones, particularly those outfitted with high-resolution cameras, are increasingly employed in construction monitoring and structural assessment. The ability to capture images with very fine detail – down to a centimeter in some cases – significantly enhances the visual data available for inspection, offering a level of detail that was previously challenging to achieve. This advancement has led to a reduction in on-site inspection time, potentially decreasing it by up to 80% compared to conventional methods. This efficiency gain allows engineers to conduct a greater number of inspections within a shorter timeframe.
Beyond standard visual inspection, some drones are equipped with thermal imaging capabilities. This feature allows inspectors to detect otherwise invisible issues, including heat loss, water damage, and electrical faults, further enhancing building diagnostics. The integration of GPS in drone technology facilitates the accurate georeferencing of images, which is essential for constructing comprehensive digital models and monitoring structures over time. Furthermore, drone flights can be automated using pre-defined flight paths, enabling repeatable inspections and aiding in long-term structural monitoring.
However, safety and regulatory considerations are crucial. The use of drones can significantly reduce human exposure to hazardous conditions, such as working at heights or around unstable structures. This increased safety factor is a significant benefit. But current regulations, especially those set by the FAA, can limit drone operations in certain areas, such as near airports or in congested urban environments. This requires a thorough understanding of the regulatory landscape to ensure compliance.
Drone-captured data often involves remote sensing techniques like photogrammetry or LiDAR, leading to the generation of 3D structural models. These models give detailed insight into the geometry and volume of the structures, improving the accuracy of assessments. However, the performance of drones can be significantly affected by environmental factors like wind. Strong winds can impact flight stability and image quality, potentially leading to oversights during assessments. Drone operators must have a solid understanding of weather conditions and flight techniques to mitigate these risks and ensure optimal results.
The integration of artificial intelligence (AI) in drone-based analysis is an emerging area of research. AI-powered software could automatically analyze aerial images to identify structural defects or abnormalities, shifting the role of inspectors from primarily data collection to more strategic assessment and evaluation. While the current limitations of AI in this area still require careful scrutiny, the potential for enhanced structural evaluation is immense and worth close monitoring.
Essential Skills and Tools for Modern Structural Inspectors A Technical Equipment Proficiency Guide - Mobile Data Collection Devices and Documentation Software for Field Reports
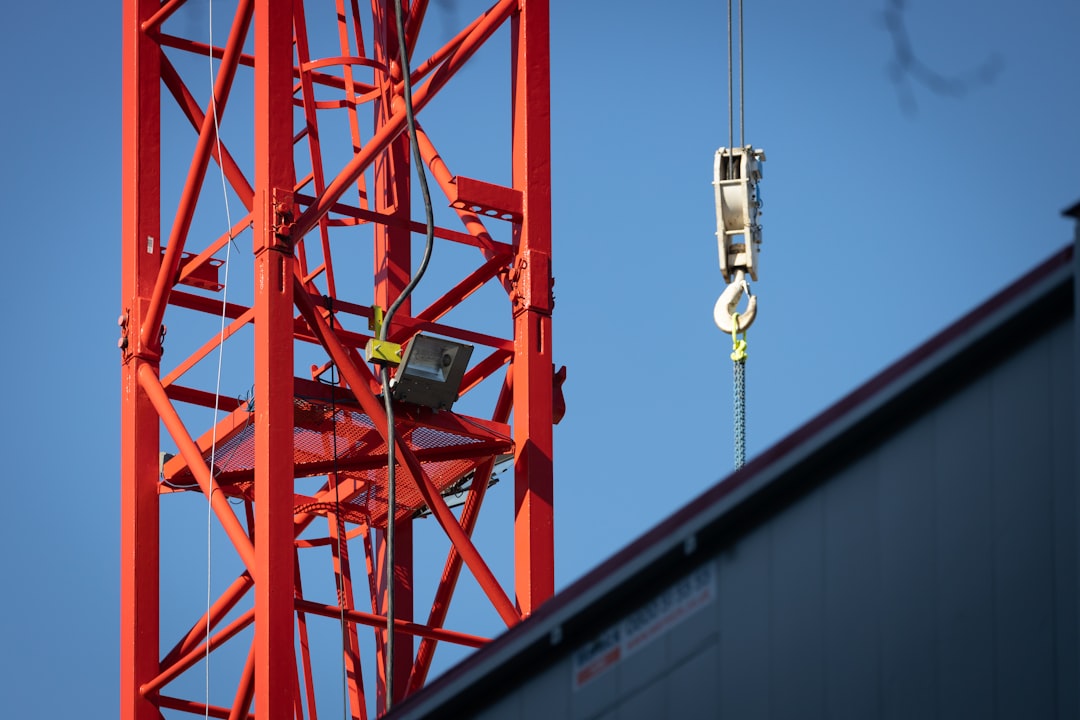
Modern structural inspection practices are increasingly reliant on mobile data collection devices and specialized software for producing thorough and efficient field reports. Mobile applications, like those based on Open Data Kit (ODK), offer inspectors streamlined data capture during on-site assessments. Features like form-based data entry in applications such as Esri Collector or Survey123 simplify the recording and organization of findings. Inspectors can leverage user-friendly tools, like Fielda, to create customized checklists without any programming, making field data gathering more efficient for diverse inspection scenarios.
The shift toward mobile technology has not only made documentation more efficient but has also improved communication and collaboration among inspection teams. Software solutions can facilitate data sharing and collaboration, leading to a more consistent and data-driven approach to assessments. While these advancements clearly enhance the efficiency of inspections, it's imperative that structural inspectors maintain a focus on the fundamental principles of structural integrity. The incorporation of digital tools must never replace the need for a thorough understanding of traditional methods and critical evaluation of findings. The challenge for the modern inspector is to seamlessly integrate these new digital tools while simultaneously adhering to established inspection procedures and ensuring the highest standards of structural safety. As the field evolves and new technologies emerge, inspectors will need to adapt, striking a balance between the ease and speed of mobile platforms and the fundamental principles of sound structural practices.
Mobile data capture devices and associated software are fundamentally changing how structural inspections are documented. These tools, often accessed through smartphones or tablets, enable quick and efficient data entry directly in the field, reducing the reliance on cumbersome paperwork. Some applications, like Esri's Collector and Survey123, focus on streamlined data entry using forms, making them well-suited for routine inspections. Others, like SurveyCTO based on Open Data Kit (ODK), offer a more robust feature set aimed at researchers and professionals seeking more control over data types and organization.
Apps like Fielda prioritize ease of use, letting individuals create customized checklists and forms without needing to learn any coding. These simplified interfaces streamline field operations, enhancing speed and consistency during installations or asset checks. The wider availability of this type of technology reflects a growing need for quality and safety improvements in inspections, which is seen as essential to fostering a higher level of customer satisfaction. However, the reliance on mobile data collection also needs to be considered alongside more traditional methods.
Platforms like Magpi allow web-based form creation for deployment across multiple devices, supporting diverse data types, including imagery, GPS location, barcodes, and signatures. This capability is particularly useful when you need to capture a diverse array of details in your inspections. These mobile field technologies improve communication and boost the overall efficiency of inspection teams, contributing to enhanced safety procedures through more effective data management in the cloud. This also can lead to improvements in decision-making, as teams can use the data from the field to refine their inspection strategies and improve operations.
Mobile devices, with their integrated software, are helping inspectors transition from relying on aging paper-based methods towards streamlined digital systems. Specialized asset management applications are further streamlining this transition, capturing and documenting data efficiently, optimizing inspection workflows. These capabilities can be very effective, but it is also important to be aware of the implications for data storage and security, as reliance on mobile devices shifts a lot of inspection data to the digital realm.
Further enhancing inspection methods, tools like ODK and Teamscope are tailored for specific inspection demands, giving researchers and professionals a solid foundation for managing large datasets across various environments. While offering great potential, the sheer variety of apps on the market can be overwhelming, and careful consideration is needed to select the most appropriate option for your specific needs. The constant introduction of new features and capabilities in these platforms emphasizes the need for continuing education, as it is imperative for structural inspectors to keep up with new developments. Understanding how to use these tools and effectively integrate the collected information within the broader framework of a structural assessment is a developing field and deserves attention. It is quite clear that the future of inspection is inextricably tied to the continued evolution of mobile data capture systems and associated software.
Essential Skills and Tools for Modern Structural Inspectors A Technical Equipment Proficiency Guide - Non Destructive Testing Equipment Including Ultrasonic and Thermal Imaging Tools
Modern structural inspectors increasingly rely on non-destructive testing (NDT) equipment to assess the integrity of materials and components without causing damage. This is a critical aspect of ensuring structural safety and performance. Methods like ultrasonic testing (UT) have become essential for detecting subsurface flaws, proving useful in fields like aerospace and manufacturing where internal component integrity is crucial. UT allows for volumetric inspections that can reveal potential defects not visible on the surface. Furthermore, the use of thermal imaging tools is expanding. These tools leverage the detection of infrared radiation to identify temperature variations, providing valuable clues about potential problems like water intrusion or inadequate insulation.
While NDT offers considerable advantages, its effectiveness heavily depends on the skills of the person using the equipment and the quality of the tools themselves. This means that inspectors need to be properly trained and have access to well-maintained equipment if they are going to generate reliable and informative data. The field of NDT is continually evolving with new technologies and techniques being introduced. Staying up-to-date on these developments will be important for inspectors to ensure they can conduct comprehensive and accurate inspections as the industry progresses. Staying informed and skilled in the proper use of this type of testing is crucial for any inspector who wants to maintain a high level of professional competence and help ensure structures are safe for their intended use.
Non-destructive testing (NDT) equipment offers a fascinating array of tools for evaluating the integrity of materials and components without causing any harm. Ultrasonic testing (UT), for instance, leverages high-frequency sound waves to uncover hidden flaws within materials, like tiny cracks or internal structural weaknesses. This technique is remarkably sensitive, capable of detecting defects as small as a tenth of a millimeter. Its ability to 'see' into materials makes it ideal for applications like inspecting welds in metal structures, a critical safety concern in many industries.
Thermal imaging equipment offers a different perspective, using infrared technology to map temperature variations across surfaces. With a sensitivity to detect temperature changes as small as a tenth of a degree Celsius, inspectors can identify a wide range of anomalies, from heat loss in building envelopes to overheated electrical components in machinery. This non-contact method is incredibly useful in predictive maintenance, allowing engineers to spot potential issues before they lead to more significant problems.
Beyond simply finding flaws, ultrasonic technology can also be employed to accurately measure the thickness of materials with high precision—often within one-hundredth of a millimeter. This is especially important for inspecting components prone to corrosion or erosion, where understanding the rate of material degradation is vital for maintaining safety. Moreover, the development of digital signal processing in newer UT instruments has led to better noise reduction and significantly improved defect detection capabilities.
Modern ultrasonic and thermal imaging devices frequently incorporate real-time data visualization features, which streamlines on-site inspections. Inspectors gain immediate access to results, enabling prompt decisions regarding necessary maintenance or repairs. This quick turnaround can considerably minimize downtime on projects, especially in production environments. Thermal imaging also has unexpected applications such as fire hazard detection, as it can quickly identify areas of overheating that could potentially lead to dangerous situations.
However, each technique has its limitations. While thermal imaging provides valuable insights into temperature distributions, it cannot, on its own, determine the underlying structural integrity of a material. Similarly, in ultrasonic testing, achieving the best results requires careful consideration of the frequency used. Lower frequencies are better suited for thicker materials, while higher frequencies offer better resolution but have a shorter penetration depth. This trade-off highlights the importance of using the right tool for each inspection.
The evolution of NDT has not only increased the sophistication of the technology but also simplified its application. Modern NDT devices tend to be much more compact and user-friendly. Several thermal imaging cameras, for example, are now designed to integrate seamlessly with smartphones, simplifying data sharing and documentation. This portability and simplified usability further expand the accessibility of these inspection tools. The future of NDT equipment appears to be one of continued innovation, leading to ever-more sophisticated and portable tools that streamline the process of inspecting and maintaining structures and critical components across a vast range of industries. The ability of inspectors to integrate this technology into their skill sets and apply it effectively is increasingly crucial for ensuring structural integrity and safety in our ever-more complex built environment.
Essential Skills and Tools for Modern Structural Inspectors A Technical Equipment Proficiency Guide - Material Testing Equipment for Concrete Strength and Steel Property Analysis
Assessing the strength and properties of concrete and steel is fundamental to modern structural inspections, and this relies heavily on specialized material testing equipment. Concrete testing is crucial for confirming that materials meet stringent quality standards and are fit for purpose within the construction context. It's essential to ensure that concrete performs reliably throughout the life of a structure, and this can be accomplished through a variety of testing methods. Notably, non-destructive testing methods allow inspectors to evaluate the concrete's condition without causing any damage to the material itself, providing immediate feedback and insights during the inspection process. This is valuable when quick on-site decisions are required. The advent of portable field testing equipment has revolutionized the way inspections are performed, allowing inspectors to conduct analyses directly at the job site, streamlining the process and ensuring that the construction project remains on track and compliant with relevant quality control measures. Beyond basic concrete assessments, advanced material testing systems are now available that can analyze a broad range of construction materials, including concrete, various types of cement, soils, roadbeds, and structural steel. This expanded range of capabilities emphasizes the importance for structural inspectors to be knowledgeable about the use of these sophisticated tools in order to guarantee the safety and integrity of the structures they evaluate. While inspectors rely on their visual inspections and training in traditional assessment methods, modern technology significantly aids in achieving a more robust and informed understanding of material behavior.
1. **Concrete's Strength and Curing**: The strength of concrete can vary significantly depending on how it's cured, with optimal curing potentially boosting strength by as much as 50%. This highlights how important proper curing methods are throughout a building's construction to ensure the structure is sound.
2. **Steel's Yield Strength Variation**: The yield strength of steel isn't fixed; it can change depending on factors like heat treatments and how much carbon is in it. This means that inspectors can't just rely on the material's specifications but need to consider the testing methods and processing conditions the steel went through.
3. **Non-Destructive Testing's Impact**: Tools like the Schmidt hammer can measure concrete strength with a simple surface impact, providing quick feedback on the material's condition without having to damage it. This is particularly useful when assessing the integrity of existing structures before making any changes to them.
4. **Ultrasonic Testing's Depth**: Ultrasonic testing can reveal flaws within concrete and other solid materials, potentially showing inconsistencies several meters below the surface. It's interesting how the speed of ultrasonic waves changes with the material's density, providing crucial insights into the material's quality.
5. **Thermal Imaging's Temperature Sensitivity**: Thermal imaging tools are very sensitive to temperature differences, as small as 0.1°C, making them valuable for finding thermal anomalies that might signal structural problems like insulation issues. However, inspectors need to be properly trained to interpret these readings because environmental factors can influence the data.
6. **Understanding Load Capacity**: While concrete's resistance is often discussed, a lesser known fact is that standard brick can withstand up to 1400 psi of pressure. This type of knowledge emphasizes how important material selection is in load-bearing applications.
7. **Digital Advancements in Ultrasonic Testing**: Digital signal processing within modern ultrasonic testing equipment has significantly improved flaw detection by reducing noise. This enhanced clarity and accuracy leads to more reliable assessments and helps inspectors avoid overlooking potential problems.
8. **Concrete Density's Role**: The density of concrete has a considerable influence on its strength—lightweight concrete can be as low as 1200 kg/m³ compared to typical concrete at about 2400 kg/m³. The choice of concrete type, especially its density, affects its performance in earthquake-prone areas, making it critical to select the appropriate density for each scenario.
9. **Steel Alloying and Corrosion**: Not all steel is made the same. Adding alloying elements, like chromium, greatly improves a steel's corrosion resistance, often exceeding the basic requirements for structures in harsh environments.
10. **Real-Time Data for On-Site Decisions**: The improvement in NDT tools means inspectors can see results on-site in real-time. This accelerates the decision-making process in time-sensitive situations. It's a big step forward in the inspection workflow, enabling quicker maintenance interventions when necessary.
More Posts from aistructuralreview.com: