Ensuring Structural Integrity for Underground Gas Pipelines
Ensuring Structural Integrity for Underground Gas Pipelines - Identifying the Usual Suspects Common Threats to Pipeline Walls
Understanding the principal dangers that compromise the physical structure of underground gas pipelines is fundamental. The usual suspects include material degradation, primarily corrosion in its many forms eating away at the metal, alongside significant mechanical forces, whether from ground movement, seismic activity, or external impacts. Internal operational pressures also exert constant stress on the pipe walls. A critical aspect often overlooked is how these individual threats rarely act alone; they frequently interact, accelerating damage and making identification more challenging than a simple checklist approach might suggest. Ultimately, these factors degrade the pipeline wall's integrity, reducing its capacity to withstand operating conditions and external loads. Proactively identifying and thoroughly assessing these complex and often interacting threats is essential to preempt structural failure and ensure the pipeline remains reliable for the long term.
As engineers and researchers probing the factors that compromise the very walls of underground gas pipelines, we recognize several recurrent issues. Understanding the nuances of these degradation mechanisms is critical, as they are far from simple textbook cases:
Corrosion driven by microbial activity (MIC) is often underestimated because it doesn't always behave like atmospheric rust. Certain types of bacteria thriving in oxygen-depleted environments, perhaps trapped moisture under disbonded coating or saturated trench backfill, can produce corrosive compounds like highly reactive sulfides. This results in intensely localized pitting, sometimes accelerating material loss in unexpected areas, even where external coatings appear intact.
Stress Corrosion Cracking (SCC) is another insidious mechanism. It typically involves the formation of multiple, fine crack networks, often oriented parallel to the pipe's axis, and requires the unfortunate confluence of tensile stress, specific environmental conditions (like certain soil chemistries), and a susceptible steel material. These cracks can initiate and propagate slowly, sometimes remaining below detection thresholds during routine inspections until a critical point is reached.
Mechanical damage isn't limited to dramatic excavation hits that cause immediate leaks. Even seemingly minor scrapes, dents, or gouges that don't fully penetrate the pipe wall are concerning. They locally deform the steel, introducing significant residual stresses and microscopic damage that fundamentally alters the material structure in that spot. This compromised area can then become a prime initiation site for future cracking mechanisms like fatigue or SCC, potentially manifesting failure decades after the original incident.
The presence of hydrogen within the steel lattice is a serious issue, often arising from certain corrosion processes or, less commonly, from overprotection during cathodic protection. Hydrogen atoms are small enough to diffuse into the steel's crystal structure, particularly at grain boundaries and defect sites. While not causing direct material loss, its presence can severely reduce the steel's ductility, its ability to deform slightly before breaking, making it prone to sudden, brittle fractures under tensile loads – a phenomenon we refer to as hydrogen embrittlement.
Finally, the operational reality of pressure fluctuations cannot be ignored. The pipeline system breathes, experiencing cycles of pressure increases and decreases. While seemingly benign on a robust pipe, these cycles provide the driving force for fatigue crack growth. Any existing small discontinuity, whether a microscopic flaw in a weld, a minor mill defect, or indeed the micro-damage from past mechanical interference, can act as a stress concentration point where tiny cracks initiate and grow incrementally with each pressure cycle, gradually eroding the structural margin over the pipeline's service life.
Ensuring Structural Integrity for Underground Gas Pipelines - Assessing Pipe Condition What the Standard Methods Reveal
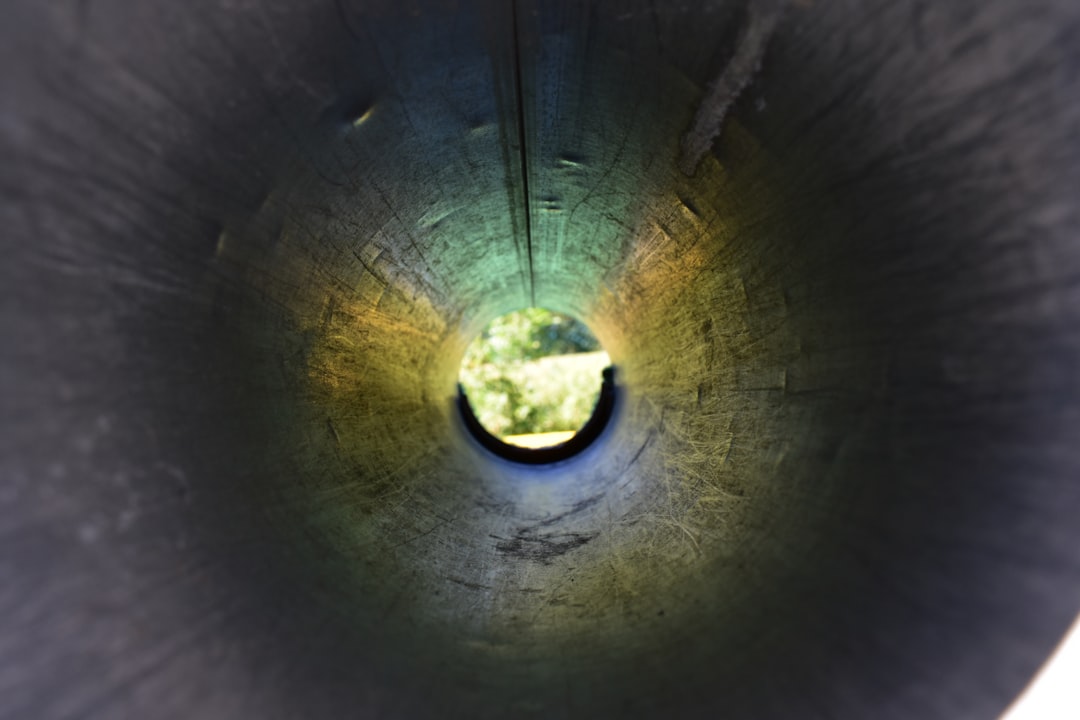
Determining the structural health of underground gas pipelines is a foundational element for maintaining their integrity and averting potential failures. Conventional assessment techniques, including approaches like engineering critical assessments and pressure testing, are routinely employed to gain understanding. These methods typically aim to detect and evaluate conditions such as material loss from corrosion, physical deformations, and certain types of cracking phenomena. While serving essential compliance functions, the true value of these evaluations lies in their role in proactive risk management, informing critical maintenance decisions, and upholding safe operational standards. Nevertheless, it's crucial to acknowledge that no single standard method is exhaustive; they may not always capture the full spectrum of degradation, particularly subtle issues or those developing under complex environmental or operational stresses.
When we apply the array of standard techniques available for probing the state of pipeline infrastructure, the picture isn't always as straightforward as simply mapping defects. What these methods truly reveal involves navigating some fundamental challenges in translating raw data into a complete understanding of structural health.
It's important to acknowledge that even advanced in-line inspection tools, combining multiple sensing principles, can struggle with the nuances of certain types of damage. Accurately distinguishing and characterizing closely spaced pitting or finely networked stress corrosion cracks, particularly when masked by internal deposits or tightly adhering scale, remains a significant hurdle, sometimes resulting in incomplete or misleading assessments of the actual threat.
Furthermore, the effectiveness of detecting certain anomalies using standard tools isn't always static. Factors like fluctuating internal pressure or subtle shifts in pipeline temperature can temporarily alter the geometry of a defect or the sensor's interaction with the pipe wall, potentially influencing detectability and leading to conditions being missed during a specific inspection run.
We rely heavily on automated algorithms to process the vast amounts of data generated by techniques like magnetic flux leakage or ultrasonic testing. However, these algorithms, and the subsequent interpretation required by experienced personnel, involve making critical judgments to classify signals and estimate defect dimensions. This interpretation step isn't immune to variability and requires careful validation, highlighting that the assessment isn't purely objective measurement.
The physical condition of the pipe surface itself plays a surprisingly critical role. The presence and type of external coatings, internal residues, or even minor surface roughness can significantly attenuate or distort signals from various non-destructive testing methods. This can directly impact their ability to penetrate the material or accurately sense changes within the pipe wall, potentially obscuring critical flaws.
Perhaps most fundamentally, the standard tools primarily give us a snapshot of the *outcome* of degradation – a measurement of metal loss, a crack dimension, a strain profile. They typically don't directly quantify the intricate *interactions* occurring between multiple degradation mechanisms (like corrosion influencing SCC initiation) that are often the real drivers of accelerated damage rates and complex failure paths.
Ensuring Structural Integrity for Underground Gas Pipelines - Managing Integrity Through Defined Programs and Practices
For underground gas pipelines, maintaining their long-term performance and safety hinges critically on establishing clear, structured approaches to managing their physical condition. This means moving beyond reactive fixes to actively defining systematic efforts aimed at heading off potential problems before they become critical.
Such formalized initiatives prioritize continuous oversight and evaluation, deploying available methods and technologies to identify signs of degradation, such as material loss, physical deformation, or certain types of cracking, while they are still in their earlier stages. The goal is to understand potential vulnerabilities well before they lead to failure.
However, it's crucial to approach this with realism: no single method or technological solution can definitively detect every conceivable threat. Moreover, the complex ways different forms of damage can interact and accelerate each other often makes comprehensive tracking and remediation through a defined process more intricate than a straightforward checklist approach might suggest.
Ultimately, ensuring the enduring physical strength of these vital pieces of infrastructure requires a strategy for managing integrity that is both thorough in its scope and keenly aware of the inherent complexities and potential blind spots.
Managing the structural well-being of underground gas pipelines effectively hinges on implementing defined programs and established practices. This isn't merely about reacting when a problem is found, but about proactively managing the complex lifecycle of the asset. From a researcher's vantage point, several aspects stand out regarding how this is approached:
It's intriguing how these programs attempt to weave together incredibly granular historical data, like mill certifications for the steel or detailed weld logs from initial fabrication, with vast, ongoing external observations – things like localized land subsidence rates monitored over decades or shifts in groundwater chemistry impacting cathodic protection effectiveness. The aim is essentially to build a dynamic, virtual representation – a digital twin of sorts – of each pipeline segment, where historical context continuously informs current risk assessments. The critical challenge here is ensuring the consistency, quality, and relevance of data collected across vastly different methods, timescales, and historical standards, and then getting it to genuinely *inform* current structural behavior predictions, not just reside in a database.
A significant pivot is the move towards predictive analysis, largely driven by complex probabilistic modeling frameworks. Instead of simply cataloging defects found during an inspection, these models try to simulate thousands of potential future outcomes, considering various degradation rates and interaction pathways based on the accumulated data. This sounds powerful – aiming to forecast where and *when* future problems are most likely to manifest across an entire network – but it inherently relies heavily on the accuracy and completeness of the input data and the assumptions baked into the models themselves. Translating these probabilities into actionable, justifiable maintenance schedules across extensive infrastructure remains a formidable task.
The integration of environmental data is becoming increasingly sophisticated, extending far beyond routine geotechnical surveys. Continuous monitoring of subtle shifts in soil moisture potential, changes in nearby drainage patterns affecting backfill saturation, or even capturing low-level ambient vibration/micro-seismic activity – these dynamic inputs are being fed directly into integrity risk models. The goal is dynamic risk adjustment: for instance, identifying areas where changing ground conditions might suddenly accelerate corrosion threats or increase susceptibility to geohazards. The complexity lies in establishing reliable, actionable correlations between these subtle environmental changes and specific pipeline degradation processes.
A truly critical, though perhaps less visible, element is the closed-loop learning process. Every assessment finding, whether a confirmed defect requiring repair or even a non-critical observation, along with data from maintenance activities and any operational anomalies or incidents, needs to be meticulously fed back into the integrity management system. This constant influx of real-world performance data is what iteratively refines the algorithms, improves the accuracy of predictive models, and ideally, helps optimize future inspection methodologies and frequencies. Without this robust feedback loop, the whole system risks becoming static and less representative of the actual, evolving pipeline condition.
These programs often attempt to frame necessary interventions within a comprehensive life-cycle perspective, looking out not just years, but potentially decades – aligning with the intended service life of 50, 80, or even 100+ years for these assets. This requires complex forward planning, attempting to balance near-term safety requirements with the long-term sustainability and economic implications of different maintenance and rehabilitation strategies. It's a daunting planning horizon, necessitating assumptions about future operating conditions, regulatory landscapes, material science advancements, and the long-term efficacy of chosen remediation methods, which collectively adds a significant layer of uncertainty to the long-term projections.
Ensuring Structural Integrity for Underground Gas Pipelines - Ongoing Monitoring and the Next Steps for Operators
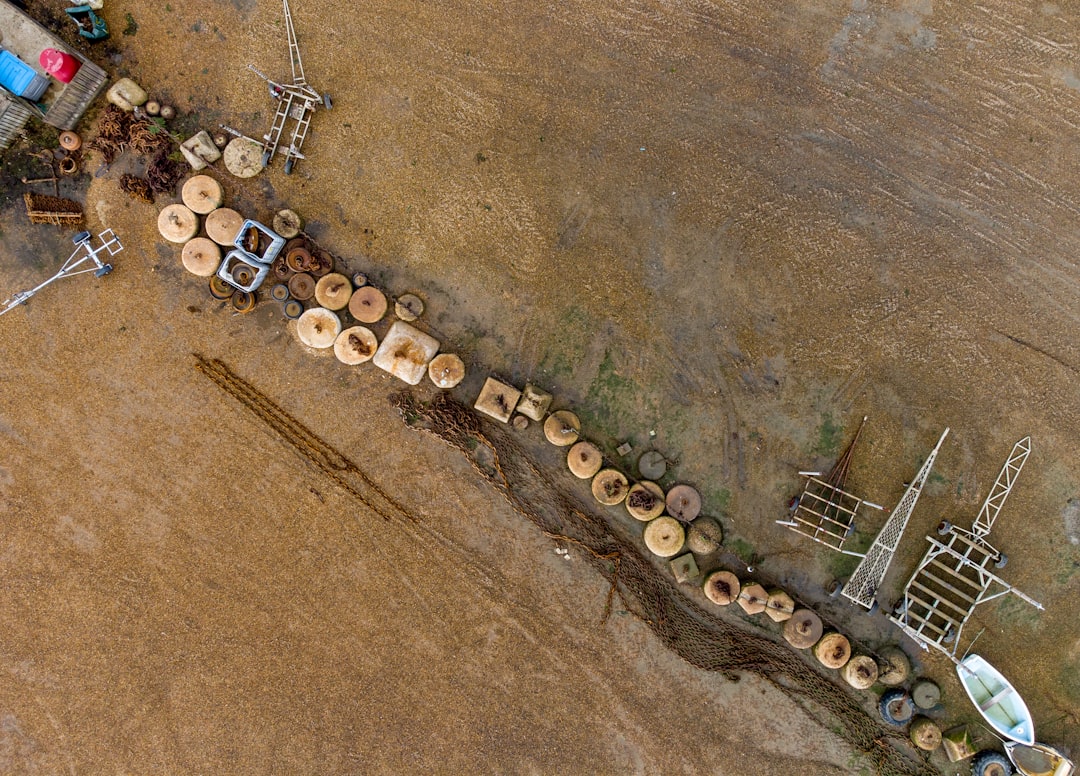
Ensuring structural integrity for underground gas pipelines fundamentally requires ongoing attention, moving past periodic checks towards continuous oversight. For operators, this translates to leveraging a combination of established assessment techniques and incorporating more dynamic monitoring capabilities. The goal is to obtain direct, evolving insights into the pipeline's condition and the influence of its surrounding environment, including factors like potential geohazards. While advancements offer the potential for more autonomous systems providing constant feedback, the central challenge remains the effective analysis and interpretation of potentially immense data streams. Translating this wealth of information into concrete, justified steps for intervention or future planning is the critical task operators face, demanding a sophisticated understanding to guide necessary actions amidst the inherent complexities of subsurface infrastructure.
Stepping beyond traditional periodic assessments, the ongoing surveillance of underground gas pipelines is increasingly moving towards real-time, nuanced analysis. It's clear that maintaining structural integrity necessitates a continuous watch, adapting to ever-changing conditions.
A significant trend involves deploying increasingly sophisticated algorithms, often drawing on artificial intelligence principles, to sift through continuous streams of sensor data. The aim here isn't just identifying known defect signatures, but detecting extremely subtle deviations or patterns that might signal damage initiating or accelerating *before* it registers on standard inspection thresholds. This pushes the envelope towards anticipating future issues rather than merely reacting to present conditions.
Novel monitoring systems are being integrated directly onto or alongside the pipeline infrastructure. Technologies like distributed fiber optic sensing can pick up minute acoustic events or small strain changes along vast distances, providing almost instantaneous alerts and precise location information that conventional methods might miss entirely or only capture during a later inspection cycle.
Furthermore, the true power emerging lies in correlating information from diverse sensor types – linking operational data like pressure and temperature fluctuations with environmental factors and real-time monitoring outputs. The objective is to construct a dynamic picture, ideally allowing for a localized, data-driven estimate of how quickly degradation is actually progressing at specific points along the line.
Remote sensing capabilities are also playing a greater role. High-resolution satellite radar, for instance, offers the ability to spot very small shifts in ground elevation over extensive pipeline corridors. This provides a crucial layer of oversight for identifying areas potentially vulnerable to geotechnical hazards like subtle land subsidence or soil instability that could subject the buried asset to unforeseen stresses.
Ultimately, the ambition extends to analytically connecting these varied data points to better model and potentially anticipate the complex interplay between different degradation processes – understanding, for example, how subtle changes in local soil chemistry picked up by sensors might be accelerating corrosion in conjunction with tensile stresses already present. This moves towards a more holistic understanding of the true structural condition.
More Posts from aistructuralreview.com: