Code Compliance Challenges Navigating Plumbing Installation in Exterior Walls
Code Compliance Challenges Navigating Plumbing Installation in Exterior Walls - Understanding Local Building Codes for Exterior Wall Plumbing
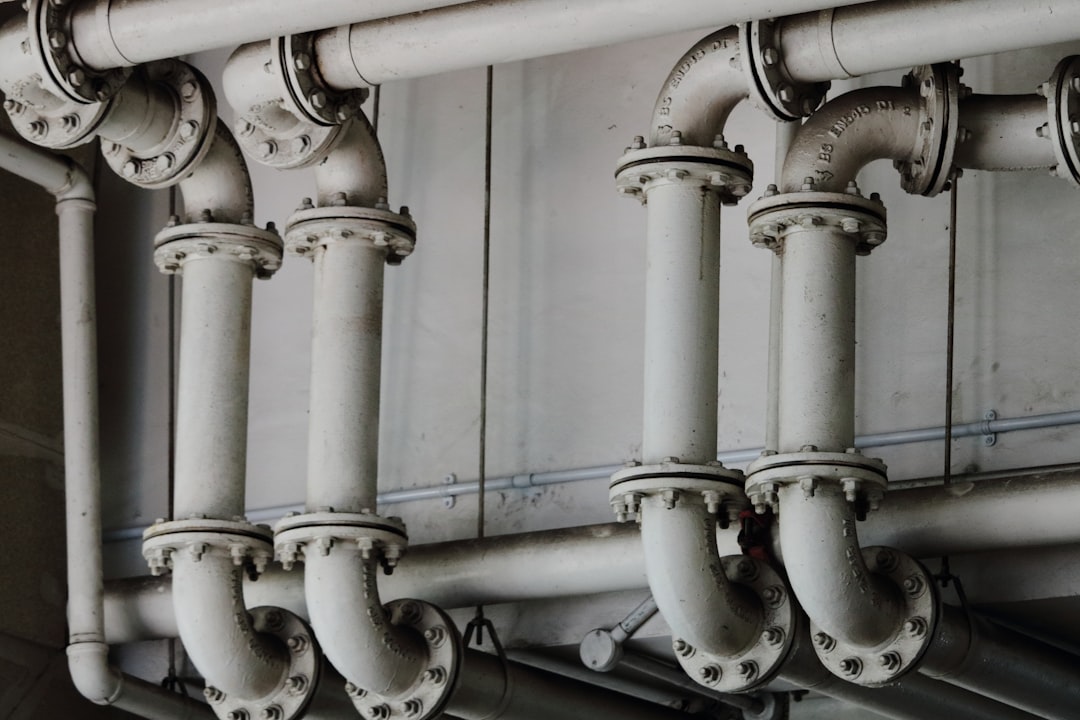
Installing plumbing in exterior walls can be tricky, and understanding local building codes is essential. The placement of pipes in exterior walls presents unique challenges, especially in climates with freezing temperatures. Building codes provide specific guidelines for protecting pipes from freezing, often requiring insulation or heat tracing. Beyond preventing damage, code compliance helps ensure plumbing systems function effectively and efficiently, while also safeguarding builders from legal issues that arise from non-compliance. Ultimately, local building codes act as a safety net, ensuring that plumbing installations in exterior walls meet minimum standards of safety and functionality.
Navigating local building codes for exterior wall plumbing is like deciphering a regional dialect - nuanced rules and regulations that vary depending on the local climate and past experiences. While building codes often focus on public safety and functionality, when it comes to exterior wall plumbing, the intricacies of regional weather conditions, past construction failures, and even local noise sensitivities come into play.
For example, in regions with frigid winters, plumbing codes dictate freeze protection measures for pipes running through exterior walls, to prevent costly damage from frozen pipes. This can involve specific insulation requirements or the use of heat tracing cables, depending on the local code. Another interesting aspect is the use of insulated chaseways in some areas, aimed at mitigating thermal bridging and maintaining comfortable temperatures within buildings. This highlights the broader impact that exterior wall plumbing can have on energy efficiency.
Furthermore, codes often specify the spacing and sizing of pipes, ensuring adequate water pressure throughout the system, especially for longer runs or elevation changes. This underscores the importance of understanding hydraulic principles when designing and installing plumbing in exterior walls. Interestingly, local regulations also can limit the types of materials used due to fire safety considerations, sometimes banning certain plastics or requiring fire-resistant components, making it crucial to consult the specific requirements for each project.
It's worth noting that the minimum cover depth for pipes installed in exterior walls is not merely for aesthetics. It's often dictated by codes to protect against physical damage and facilitate safe inspections, a factor that can influence design choices and construction costs.
However, navigating these code requirements can be tricky, as inspection protocols for exterior wall plumbing can vary significantly. This often reflects historical construction failures or specific concerns in a region, leading to a patchwork of compliance challenges for contractors and engineers.
Adding to the complexity, some codes mandate the use of backflow prevention devices for exterior wall plumbing connections to protect potable water supplies, a critical requirement that often goes overlooked. Finally, in areas with seismic activity, unique provisions regarding anchoring and bracing techniques for exterior wall plumbing systems are common. This emphasizes the need for specialized knowledge regarding earthquake resistance in these regions.
It seems local plumbing codes have become more inclusive, addressing even noise transference through exterior walls, with some localities requiring soundproofing techniques to maintain comfort levels in residential settings. Ultimately, understanding the nuanced complexities of local plumbing codes, which are constantly evolving to accommodate new technologies and methods, is paramount for professionals. It's a field that requires ongoing education and attention to detail to ensure compliance and prevent potential pitfalls.
Code Compliance Challenges Navigating Plumbing Installation in Exterior Walls - Weather-Resistant Envelope Requirements for Concrete and Masonry Walls
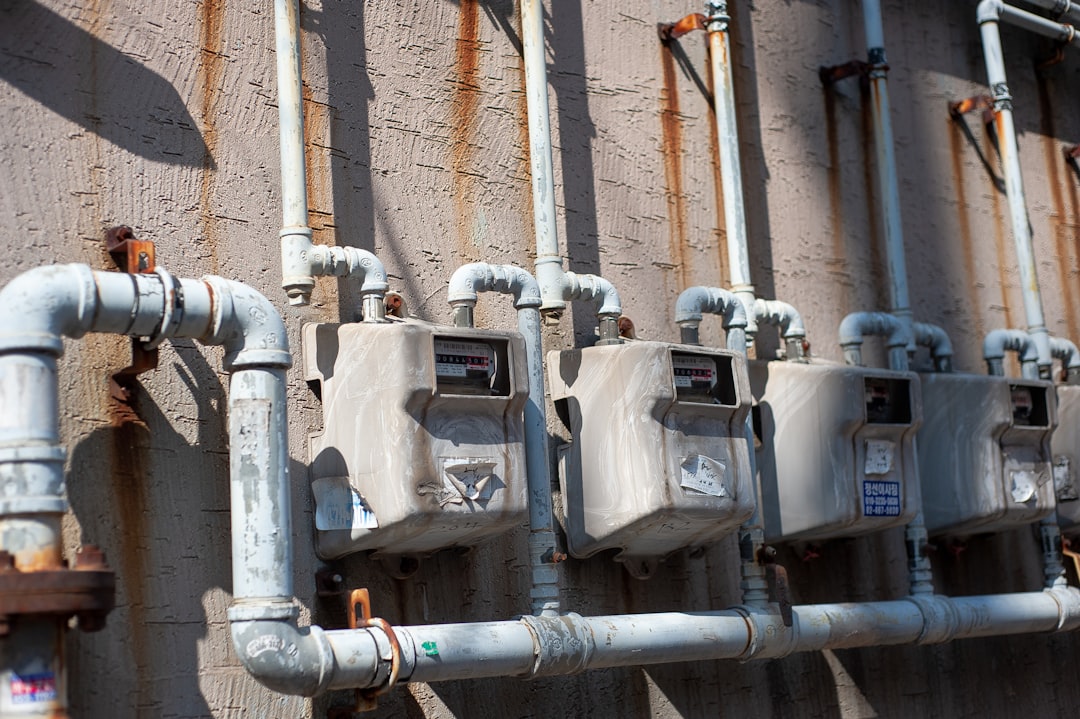
Building codes often require exterior walls to be weather-resistant, but there are exceptions. Concrete and masonry walls, when designed and tested according to specific code sections, may not need an additional weather-resistant envelope. However, this exemption complicates plumbing installation in these walls.
The codes typically demand resistance to wind-driven rain, and while this may be achieved through testing, it can clash with the need for concealed drainage and insulation for plumbing systems. Further, code provisions vary widely depending on location, adding another layer of complexity for plumbing installers. To ensure compliance and proper installation of plumbing in concrete and masonry walls, it's essential to thoroughly understand these weather-resistant envelope standards and their application in different jurisdictions.
The interaction between weather-resistant envelopes and concrete/masonry walls presents a complex web of considerations for designers and builders. While concrete and masonry are generally seen as durable materials, their inherent porosity and potential for thermal bridging make them susceptible to moisture intrusion. This means proper detailing and material selection are crucial for ensuring long-term performance.
Code requirements can seem contradictory at first glance. While some codes exempt these wall types from specific weather resistance requirements when designed according to established standards, others still insist on specific testing procedures. The seemingly contradictory nature of these codes begs further investigation into how these provisions ensure the long-term integrity of the building envelope, especially given the susceptibility of concrete and masonry to water penetration.
For example, in regions prone to extreme weather, codes may require additional layers of protection, including waterproofing membranes and the use of specific types of flashing. However, even these measures can be rendered ineffective if the detailing of the wall assembly is compromised. The emphasis on meticulous attention to detail, such as proper sealing of joints and the use of thermal breaks, becomes critical to maintain the desired level of protection. This highlights the need for skilled labor and the value of ongoing research into more robust solutions.
The use of specific types of insulation can greatly impact the thermal performance of these walls, minimizing heat loss and reducing the potential for condensation within the wall cavity. This, in turn, can reduce energy consumption and increase the overall comfort of the building. However, proper insulation placement and the choice of vapor retarders must align with local climate conditions to avoid moisture buildup and potential deterioration.
Interestingly, existing masonry structures often face unique challenges when attempting to upgrade or modify their weather-resistant envelopes. The need to balance preservation with modern building standards can lead to conflicts between existing construction methods and current code requirements, presenting a tricky situation for architects and contractors.
These considerations demonstrate that the challenges of integrating plumbing systems into concrete and masonry walls go beyond simply avoiding frozen pipes. They involve a delicate balance of structural integrity, material selection, and meticulous installation techniques. Understanding these complex interactions is crucial for ensuring building performance and preventing future costly repairs. The ongoing evolution of building codes and the increasing focus on sustainable design will continue to shape the way designers and engineers approach these intricate challenges.
Code Compliance Challenges Navigating Plumbing Installation in Exterior Walls - Testing and Drainage Provisions for Wind-Driven Rain Resistance
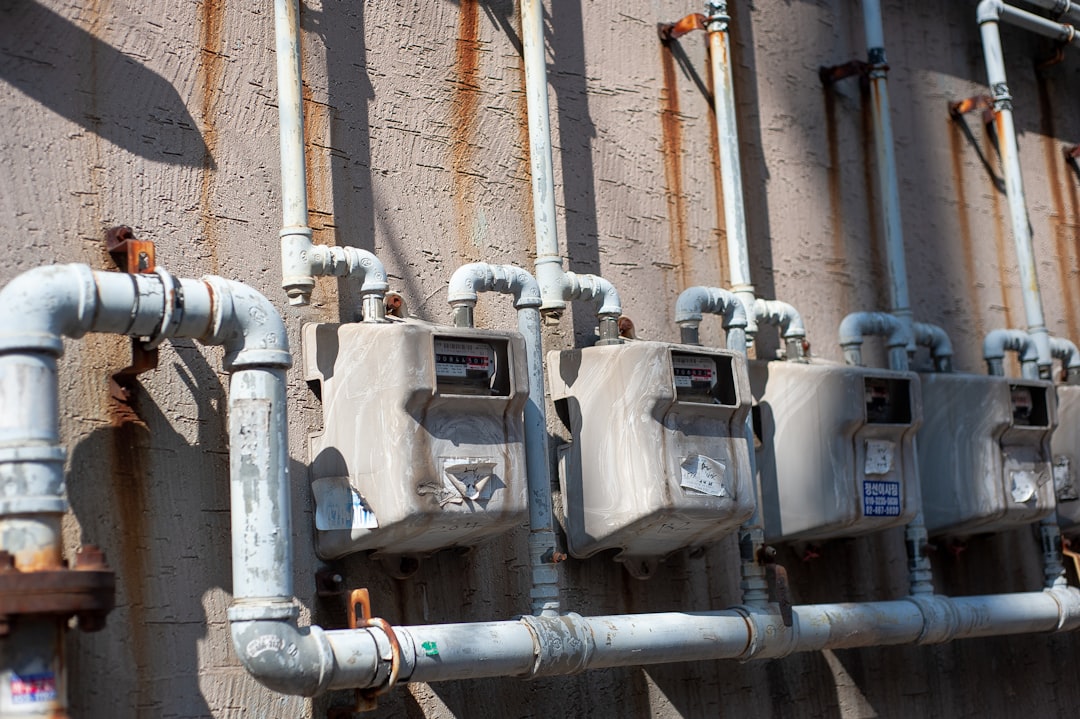
Testing and Drainage Provisions for Wind-Driven Rain Resistance introduces an interesting twist to the world of building codes. Essentially, if your exterior walls can prove they're resistant to wind-driven rain through testing, you may be able to skip some of the more complex drainage requirements. This sounds like a shortcut, but it comes with a caveat. While the International Building Code (IBC) allows for this exemption, the possibility of moisture intrusion remains a significant concern. It's easy to see why, as removing drainage provisions could increase the chances of water damage within the wall assembly. The burden falls on architects and builders to ensure that rigorous testing and careful attention to design detail are employed to prevent problems.
The challenge lies in the nuances of effective moisture management. It's not just about passing a single test, but about designing structures that can withstand the relentless onslaught of wind-driven rain over the long term. And as cities like Seattle and Florida adapt similar provisions to the IBC, we see a growing need for expertise in these areas. The real issue isn't just about the letter of the law, but the art of building structures that will stand the test of time, even in the face of extreme weather conditions.
Wind-driven rain is a significant threat to building envelopes, as it can penetrate with surprising velocity, often exceeding design pressures by a considerable margin. Testing for wind-driven rain resistance is a crucial step in ensuring a building's structural integrity and longevity, but the complexity of these tests can pose challenges.
The tests themselves are standardized, involving simulated rainfall at high pressure to evaluate the performance of wall assemblies under extreme conditions. However, different localities often specify unique testing protocols based on their unique weather patterns. This creates a patchwork of requirements, making it difficult for engineers and builders to navigate these diverse standards.
Drainage plays a vital role in mitigating the impact of wind-driven rain, as water can travel through porous materials through capillary action. Effectively managing this means designing drainage systems that account for these properties. Interestingly, research indicates that the angle of the rain relative to the building's surface impacts water penetration significantly, making it essential for architects to consider the local weather patterns when designing building facades.
Water-resistant barriers, while effective, are not foolproof. Improper installation can lead to moisture accumulation within wall cavities, highlighting the importance of skilled labor for achieving proper weather-resistance. It's interesting to note that not all materials used in plumbing systems are equally resistant to moisture; certain plastics can degrade when exposed to specific climates, which presents challenges in achieving code compliance.
Regions experiencing frequent seismic activity require additional considerations for drainage provisions to withstand lateral forces. This necessitates rethinking design strategies for both plumbing systems and drainage paths to ensure the resilience of the building envelope.
Water penetration in masonry walls poses a particularly difficult challenge due to the hygroscopic nature of many masonry materials. This requires meticulous design and installation practices for both drainage and ventilation to preserve structural integrity over time.
Finally, it's important to note that code compliance for wind-driven rain resistance is not just about preventing water from entering the building, but also about effectively managing it. This requires a dynamic approach, as static solutions may not be sufficient to address the intense forces of wind-driven rain during storms.
Code Compliance Challenges Navigating Plumbing Installation in Exterior Walls - Proper Support and Alignment of Plumbing Pipes in Exterior Walls
Properly supporting and aligning plumbing pipes within exterior walls is a critical aspect of building construction, ensuring system integrity and compliance with local building codes. Supporting pipes adequately prevents sagging and misalignment, which can lead to expensive repairs and potentially dangerous situations. Proper spacing and support systems, tailored to the specific type of pipe, are crucial to accommodate expected thermal expansion and contraction. Furthermore, in colder climates, insulation methods require careful attention to mitigate the risk of pipes freezing. Ultimately, understanding and implementing code requirements related to plumbing pipe support not only ensures effective system performance but also reinforces overall building safety.
Installing plumbing within exterior walls presents a complex set of challenges, especially when considering the nuances of local building codes. While the previous sections delved into the impact of climate on these installations and the unique demands of specific wall materials, it's important to also examine how plumbing codes influence the design and installation of pipes themselves. This goes beyond simple placement; it delves into material choices, thermal considerations, and the interplay of various physical forces.
For instance, choosing the right pipe material is more than a simple matter of cost. While certain plastics offer ease of installation and lighter weight, they often behave unpredictably under fluctuating temperatures. Metal pipes, like copper, expand and contract with temperature changes, demanding meticulous attention to expansion loops and flexible connections. Failure to properly account for these differences can lead to leaks, structural issues, and potential damage to the wall assembly itself.
The impact of temperature gradients is another critical aspect. Pipes located near cold exterior walls can experience a significant drop in water temperature, leading to condensation and the growth of mold within the wall cavity. Proper insulation becomes essential for preventing these issues, especially in colder climates. This ties into the broader concept of thermal bridging – when pipes act as conduits for heat transfer, compromising the energy efficiency of the building. Adherence to insulation standards specified in the code is crucial to maintain comfortable indoor temperatures and reduce energy consumption.
Plumbing systems also face the limitations of the surrounding structure. The placement of pipes must not overburden the wall's load-bearing capacity, often necessitating additional support systems to prevent collapse. This is particularly important in earthquake-prone regions, where codes require seismic compliance measures like bracing and anchoring, complicating routine installations.
Even the layout of the pipes themselves must be carefully considered to ensure efficient water flow. Excessive bends, valves, and fittings too close together can create turbulence and pressure drops, impacting system efficiency. These factors are governed by hydraulic design principles, further underscoring the need for expert knowledge during the planning and installation process.
The presence of mechanical systems can add another layer of complexity. Vibrations from these systems can put strain on pipe joints, leading to premature wear and potential leaks. It's not enough to just account for static loads; the dynamic forces must be considered when designing support systems for plumbing pipes.
Navigating these intricacies is vital for successful installations. It requires a deep understanding of not just the letter of the code but the reasoning behind its requirements. Ultimately, proper planning and execution can ensure plumbing systems function efficiently, contributing to the long-term safety and sustainability of the building itself.
Code Compliance Challenges Navigating Plumbing Installation in Exterior Walls - Thermal Insulation Strategies to Prevent Pipe Freezing
Protecting pipes from freezing, particularly those situated within exterior walls, demands a careful approach to thermal insulation. The most effective strategy involves insulating both hot and cold water supply lines, which minimizes the risk of condensation and ice formation, ensuring water flow during even the coldest months. When pipes must be placed within exterior walls, it's crucial to provide substantial insulation to mitigate the impact of freezing temperatures. In many areas, continuous insulation, often exceeding minimum energy code requirements, not only enhances building performance but also addresses the concern of thermal bridging, where pipes act as a conduit for heat loss. Proper insulation not only protects plumbing systems but also contributes to energy conservation and reduces the associated noise, underscoring its multifaceted value in modern building practices.
Preventing pipes from freezing in exterior walls is a crucial aspect of building design, especially in regions with frigid winters. While codes often provide general guidelines, the complexities of insulation are rarely discussed. To effectively insulate pipes and prevent freezing, a deep understanding of heat transfer, insulation materials, and code variations is essential.
The effectiveness of insulation is quantified by its R-value, which measures its resistance to heat flow. Insulation materials commonly used for exterior plumbing include fiberglass, spray foam, and rigid foam board. Each material possesses different thermal properties, with rigid foam offering continuous insulation that minimizes thermal bridging.
It's crucial to consider heat transfer mechanisms, including conduction, convection, and radiation, to design effective insulation strategies. In high-humidity areas, vapor barriers are critical to prevent condensation within wall cavities, which can lead to freezing and structural damage. Proper insulation placement around pipes is vital, with full wrapping crucial to prevent cold air contact. Misaligned insulation can create significant temperature differentials, increasing the risk of freezing.
Introducing thermal breaks in areas where plumbing is embedded in exterior walls can minimize heat loss. For particularly at-risk pipes, heat tracing systems can be employed, which utilize electric heating cables to maintain temperatures above freezing regardless of ambient conditions.
Interestingly, proper insulation not only prevents freezing but also significantly enhances a building's overall energy efficiency. Inadequate insulation results in increased energy consumption due to heat loss. However, local code requirements regarding pipe insulation vary greatly, with some mandating continuous insulation and others offering more flexible recommendations.
It's important to remember that insulation is not a one-time installation. Regular inspections are vital to ensure continued protection against pipe freezing, as insulation can degrade or be compromised over time, particularly in long-run applications. This demonstrates the dynamic nature of insulation strategies, requiring ongoing maintenance and adaptation to changing environmental conditions.
Code Compliance Challenges Navigating Plumbing Installation in Exterior Walls - Balancing Energy Code Compliance with Plumbing Installation Needs
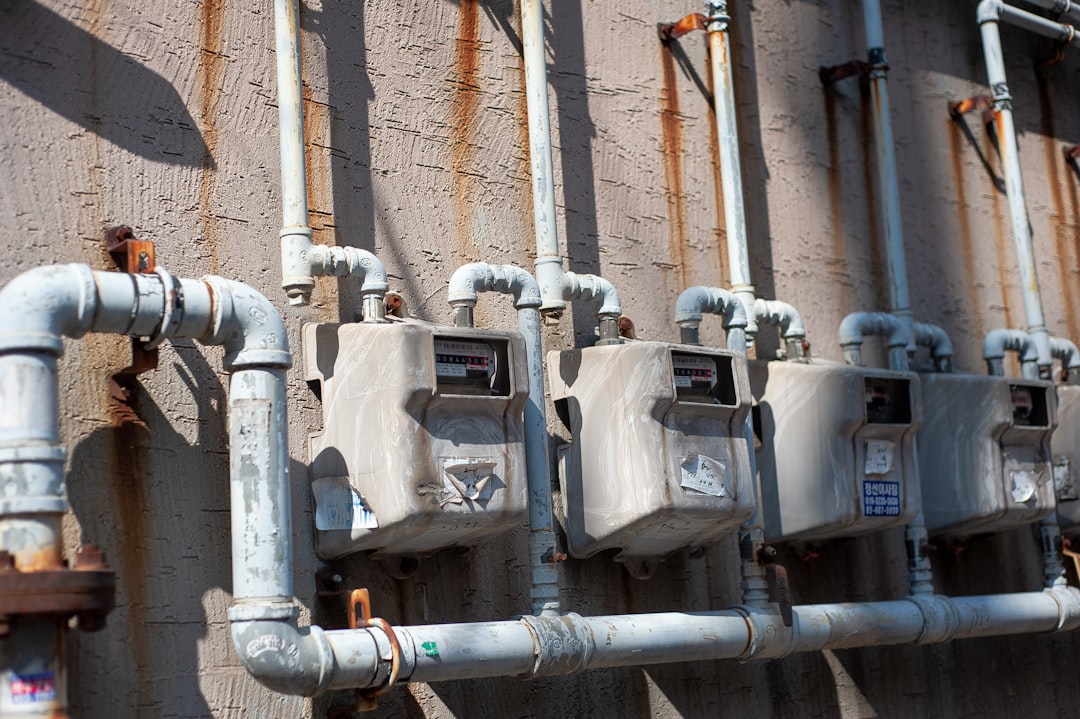
Balancing energy code compliance with plumbing installation needs is becoming increasingly complex. While modern energy codes strive for greater efficiency, their stringent requirements often clash with the practical needs of plumbing systems, particularly when installed within exterior walls. For instance, the International Energy Conservation Code (IECC), aimed at promoting energy efficiency, may require insulation levels that hinder traditional plumbing installation methods, especially in colder climates where pipe freezing remains a major concern. Achieving a balance between compliance with local plumbing codes and meeting energy efficiency standards demands constant education and a keen understanding of local regulations, especially as they evolve with advancements in technology and construction practices. This delicate interplay between plumbing and energy mandates underscores the complexity that builders and engineers face in today's construction landscape. They must navigate these conflicting demands to ensure both functionality and sustainability in modern buildings.
Building codes are a constant work in progress, and plumbing in exterior walls is no exception. While older codes might have simply addressed pipe freezing, newer ones push for continuous insulation, a measure driven by the high cost of frozen pipe damage and the inefficiency of older systems. But, there are nuances. Vapor barriers are often hailed as essential to keep moisture at bay, but a wrong installation can trap humidity, ironically increasing freezing risk. It's a fine balance to master. The type of pipe material is another point of contention. PEX tubing is known for its flexibility and thermal properties, potentially requiring less insulation than copper, but codes might still mandate redundant measures, throwing a wrench into installation choices. Furthermore, research demonstrates that plumbing pipes can act as thermal bridges, contributing to substantial heat loss in colder climates. This phenomenon has led codes to emphasize thermal breaks and proper insulation to curb energy waste.
Seismic activity in certain areas adds its own layer of complication. Codes for these regions often incorporate seismic bracing requirements, forcing engineers to juggle safety and performance. A simple plumbing installation in these areas becomes a balancing act. Fluid flow dynamics within plumbing systems are also very sensitive to pipe alignment and fittings. Codes regarding spacing and routing have a direct impact on pressure consistency and system efficiency, demanding meticulous planning.
The issue of noise transfer has also made its way into codes. Now, soundproofing for plumbing pipes is a requirement in some places to ensure residential comfort. It's yet another hurdle for engineers to overcome as they navigate the ever-growing list of demands. Wall assemblies can add to the complexity. A poorly designed assembly might actually exacerbate condensation issues, creating more challenges for code compliance.
Condensation, which is a serious concern, particularly in varying humidity levels, is addressed through specific insulation strategies in some codes, ensuring the longevity of plumbing systems. Finally, inspection protocols vary drastically depending on the locality. These variances often reflect the area's experience with plumbing failures. It's a clear reminder that local regulations are a must-know to confidently navigate code compliance.
More Posts from aistructuralreview.com: