Exploring the Yield Strength of 304 Stainless Steel A 2024 Update on Material Properties and Applications
Exploring the Yield Strength of 304 Stainless Steel A 2024 Update on Material Properties and Applications - Understanding the Composition and Basic Properties of 304 Stainless Steel
304 stainless steel, also known by its UNS designation S30400, is a widely used alloy due to its composition, primarily 18% chromium and 8% nickel. This blend contributes to its austenitic structure, a key factor in its overall performance. In addition to the main constituents, 304 stainless steel typically contains small amounts of other elements, such as carbon, manganese, and silicon, within specific limits. Its face-centered cubic (FCC) crystal structure is integral to its mechanical behavior.
The mechanical properties of 304 stainless steel are notable, exhibiting a yield strength typically around 205 MPa and a tensile strength near 515 MPa. Its density is approximately 7.93 g/cm³, indicating a good balance of strength and weight. The high melting point, spanning from 1400°C to 1450°C, underscores its ability to withstand high temperatures in various applications.
Corrosion resistance is a hallmark feature of 304 stainless steel, particularly against oxidation, especially at moderate temperatures. However, in harsh corrosive environments, particularly when welding is involved, the formation of carbides can reduce its effectiveness. In such situations, 304L, a low-carbon variant, offers better resistance. Lastly, the material is generally non-magnetic in its annealed state, although this property can shift with processes like cold working, which can induce a degree of magnetism. This aspect requires careful consideration when designing for applications where magnetic properties are important.
304 stainless steel, also known by its UNS designation S30400, is a widely employed alloy primarily due to its composition. It typically contains around 18% chromium and 8% nickel, these elements are key in conferring its desirable corrosion resistance and elevated-temperature capabilities. Beyond the main constituents, 304 also incorporates trace amounts of other elements such as carbon, manganese, silicon, and nitrogen, each with a specific role in influencing the final properties. These minor constituents can, however, sometimes impact the steel's performance in specific applications.
The crystal structure of 304 is face-centered cubic (FCC), classifying it as an austenitic stainless steel. This FCC structure greatly contributes to its ductility and formability, key characteristics often explored in the design and manufacturing stages. As a consequence of its composition and structure, it typically exhibits a yield strength around 205 MPa and a tensile strength around 515 MPa. These values can change due to factors such as cold working and heat treatment, and thus are often viewed as an initial indication of its strength characteristics.
304's density is approximately 7.93 g/cm³, which is a reasonably common density for a stainless steel alloy. Its high density could be a design consideration for applications focused on weight-sensitive components or structures. Further, it has a melting point range between 1400°C and 1450°C. This relatively high melting point makes it suitable for high-temperature applications, particularly when combined with its corrosion resistance at elevated temperatures. However, understanding the exact melting point variation depending on the specific composition and impurities is often a crucial consideration during the melting and casting process.
One interesting property of 304 is its ability to resist oxidation, especially at higher temperatures. It can withstand intermittent service up to 870°C and continuous service up to 925°C. This oxidation resistance is a result of the chromium-rich surface layer that forms naturally when exposed to oxygen. Yet, this property is often subjected to degradation depending on the environmental conditions and surrounding atmosphere.
In situations demanding high corrosion resistance, especially when welding is involved, a variant known as 304L (low-carbon 304) is generally preferred. This is because lower carbon content in 304L helps mitigate the risk of carbide precipitation during welding, which could potentially compromise corrosion resistance.
Finally, 304 is generally non-magnetic when annealed, meaning it's not attracted to magnets in its softened state. However, the application of cold working can induce a slight magnetic response. It is essential to keep in mind that any changes in magnetic properties introduced by cold working should be carefully considered, especially in applications involving electromagnetic fields or sensors.
Exploring the Yield Strength of 304 Stainless Steel A 2024 Update on Material Properties and Applications - Yield Strength Improvements Through Ultra-Strength Reinforcement Processing
Recent research into ultra-strength reinforcement processing (USRP) has shown that it can significantly improve the yield strength of 304 stainless steel. Through USRP, the yield strength of 304 stainless steel has been boosted from around 310 MPa to as high as 659 MPa, representing a substantial 113% increase. This strength gain is notable, especially considering that the material retains a high level of elongation at 36%, suggesting that its ability to deform before fracture is not overly compromised.
Interestingly, some variations of the process, like a modified version called USRP700, can result in a slight decrease in yield strength. However, even these variations still yield a strength that is greater than standard 304. This illustrates the sensitivity of the process parameters and highlights the importance of controlling the variables to achieve desired material properties.
The exploration of USRP methods for 304 stainless steel aligns with wider trends in materials science. Researchers and engineers are consistently searching for ways to create stronger, lighter materials capable of handling extreme loads and energy absorption. In many modern engineering fields, especially aerospace and automotive, there is a growing demand for advanced materials that deliver exceptional performance while keeping weight to a minimum. It appears that USRP shows some promise in helping to meet these challenges for 304 stainless steel. The potential for USRP to expand the use of 304 stainless steel into demanding environments and engineering applications is promising.
Recent research has shown that we can significantly boost the yield strength of 304 stainless steel through innovative processing methods like Ultra-Strength Reinforcement Processing (USRP). For instance, we've seen yield strength jump from its typical 310 MPa up to 659 MPa – a remarkable 113% increase. It's quite fascinating how this enhanced strength can be achieved. While a strong increase in yield strength is observed, it's noteworthy that the material retains a high level of elongation at 36%, which is rather impressive.
Interestingly, experimenting with modified versions of USRP, such as USRP700, suggests a slight trade-off. While we still see an improved yield strength over standard 304, it's not quite as high as the initial results. This highlights the importance of carefully controlling the processing parameters to optimize the desired properties. We've also witnessed improvements in other stainless steel variants. For example, additively manufactured 316L has shown exceptional yield strength, along with good tensile elongation, making it a potential candidate for particular applications where strength and toughness are desired.
However, the search for ever-stronger steels continues. Engineers are increasingly looking for advanced high-strength steels capable of reaching yield strengths above 2 GPa. These materials are envisioned for structures where lightweight designs and substantial energy absorption are needed, especially in challenging environments.
There are other exciting developments in stainless steel. Research on repaired 316L samples illustrates that repair processes can result in stainless steel with high yield and ultimate tensile strength, although some ductility may be lost in the process. A new, ultrahigh-strength maraging steel has also been developed, reaching a yield strength of 2200 MPa. This impressive strength has been attributed to innovative nano-scale precipitation strengthening techniques.
Beyond these advancements, we see a promising direction in lightweight stainless steels (LWSS). These innovative materials boast ultrahigh strengths exceeding 1 GPa, while maintaining a considerable elongation of over 35%. What's particularly interesting about LWSS is that they exhibit a lower density compared to traditional steels. Laser Powder Bed Fusion (LPBF) techniques are also demonstrating their usefulness in manufacturing stainless steels with a desirable combination of ultimate tensile strength and elongation, addressing the challenging issue of balancing strength and ductility.
Finally, a recently developed multiphase stainless steel shows an extremely low yield ratio of 0.36 and exceptional ductility, reaching a tensile strength of roughly 1114 MPa with a total elongation of approximately 21.73%. These results offer a new pathway to materials that combine high strength and ductility.
All these developments paint a hopeful picture for the future of stainless steels. While the search for optimal processing and microstructural design is ongoing, these promising trends suggest that we are continually developing innovative stainless steel alloys with remarkable properties, pushing the boundaries of what we can achieve with these materials.
**Disclaimer:** This information is for educational and discussion purposes and does not constitute endorsement of any specific material, product, or process.
Exploring the Yield Strength of 304 Stainless Steel A 2024 Update on Material Properties and Applications - Magnetic Characteristics and Cold Working Effects on 304 Stainless Steel
304 stainless steel, in its typical annealed state, is generally considered non-magnetic. This is largely due to its austenitic structure and the specific mix of elements in its composition, notably chromium and nickel. However, the application of cold working techniques like rolling or other processes involving plastic deformation can introduce a subtle magnetic response. This change occurs because cold working strains the atomic lattice, altering the material's microstructure and leading to a weakly magnetic state.
The extent of this magnetic response can vary based on the specific cold working conditions and the exact alloy composition of the steel. The amount of nickel, for example, plays a role in the magnetic behavior. It's important to remember that the induced magnetism is generally weak compared to other magnetic materials. Still, this change in magnetic properties should be considered when designing applications where magnetic fields or sensors are involved.
Interestingly, while cold working does induce a degree of magnetism, it also leads to an increase in the hardness of the 304 stainless steel. However, it's worth noting that even with significant cold working, up to 50% deformation, the increase in hardness is comparatively small, generally around 7%. This suggests that there's a limit to the hardening that can be achieved through cold working alone. Therefore, understanding the interplay between cold working, magnetic properties, and mechanical strength is crucial when selecting or applying 304 stainless steel for various engineering applications.
304 stainless steel, generally considered non-magnetic in its original state, can develop magnetic properties when subjected to cold working processes like rolling or stretching. This magnetic transformation is mainly attributed to the strain-induced formation of a different crystal structure, which affects its behavior in magnetic fields. The level of magnetism induced is influenced by the severity of cold working, with even moderate deformation causing noticeable magnetic changes. This characteristic is worth considering in applications like enclosures where magnetic interference might be an issue.
The nickel content plays a role in influencing magnetism in 304 stainless steel, as do other alloying elements. We see variations in how different 300 series stainless steels behave magnetically, depending on their specific composition. Understanding the interactions between these elements and the structural changes that occur during cold working is important to predict how a material will behave in a magnetic field. However, while the hardness increases with cold working, we only see minor improvement – about 7% with up to 50% cold work. It appears that cold working primarily affects the magnetic and mechanical properties instead of drastically boosting hardness.
Interestingly, the mechanical performance, including tensile characteristics, is impacted by the plastic deformation introduced during cold rolling. The extent of cold working influences how the material behaves under stress, which is crucial for proper design. The chemical makeup of 304, which notably includes around 0.058% carbon along with chromium and nickel, is linked to its initially non-magnetic nature. These elements contribute to its austenitic structure. But cold working, by altering the atomic structure, particularly the grain structure, can lead to a magnetic transformation.
Maintaining its austenitic phase even when cooled is a critical part of 304 stainless steel's inherent non-magnetic nature. However, when cold worked, the structure alters, creating different magnetic behavior. The effect of magnetic fields on tensile strength at very low temperatures (4 Kelvin) has been investigated and suggests that while there is no large impact on tensile characteristics, some minor effects might still be present. Researchers also acknowledge that the material's mechanical and magnetic traits are crucial in various applications, particularly in structural and manufacturing contexts.
Researchers have studied the interplay between processing conditions and resulting properties. The effects of cold work, along with the broader impact on mechanical behavior, have been researched under different processing parameters. These studies reveal how these parameters, such as cold working or specific heat treatments, directly relate to material characteristics. This area continues to be important to improve 304 stainless steel in various industrial applications, especially as we see a growing interest in exploring its use in more complex environments where strength and other properties become more important. Overall, understanding the link between processing conditions and the resulting magnetic and mechanical properties will enable engineers to design and manufacture 304 components that perform reliably in demanding applications.
Exploring the Yield Strength of 304 Stainless Steel A 2024 Update on Material Properties and Applications - Ductility and Fabrication Advantages in Industrial Applications
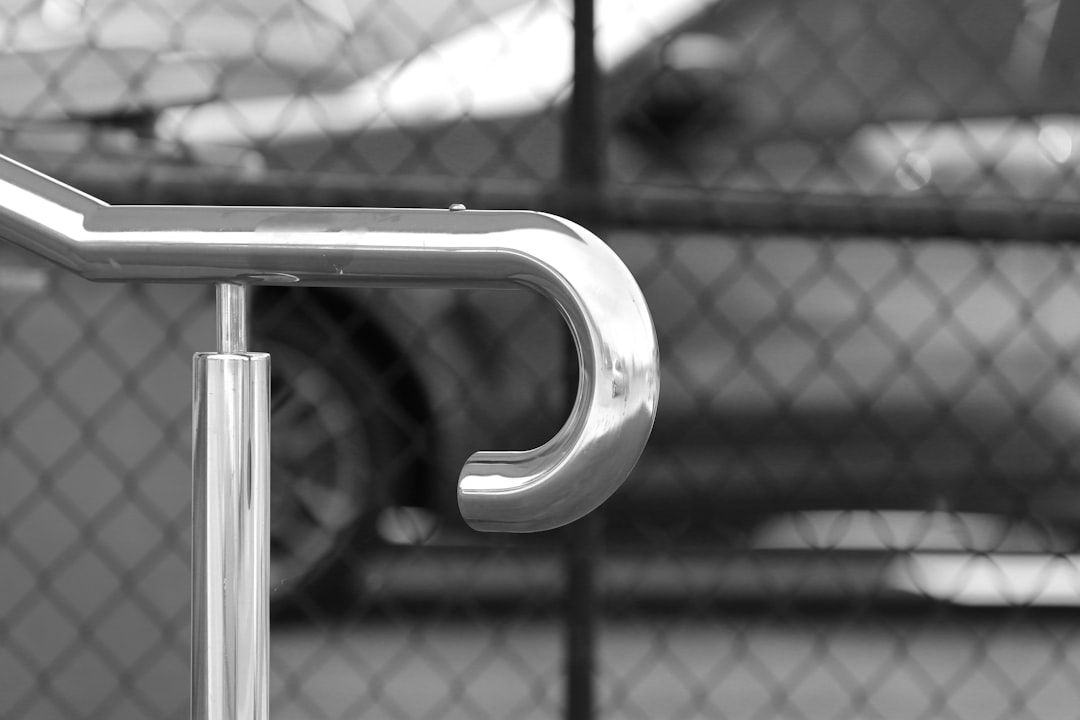
The ability of 304 stainless steel to deform significantly before fracturing, a property known as ductility, is a key factor in its usefulness for industrial fabrication. This malleability allows it to be readily shaped into a wide variety of forms needed in applications across industries, including aerospace, food and beverage, chemicals, and machinery. The capacity to draw this alloy into thin sheets or intricate shapes becomes critically important for components experiencing high stress while requiring dimensional stability. While modern techniques like Ultra-Strength Reinforcement Processing (USRP) can boost yield strength considerably, they don't appear to severely diminish ductility, making 304 a promising material for tough applications. However, finding the right balance between enhanced strength and the capacity for forming is important for industrial processes. Manufacturing needs vary, and optimizing the process parameters is crucial to ensure that the desired strength and formability are achieved for each specific application.
The inherent ductility of 304 stainless steel, a consequence of its face-centered cubic (FCC) crystal structure, is a significant advantage in numerous industrial applications. This ductility allows for a wide range of forming and shaping techniques without experiencing excessive cracking or fracture, crucial for producing intricate components. Its cold workability, where strengthening occurs without severely compromising ductility, further expands its processing flexibility. This is especially relevant when processes like bending and stretching are required during manufacturing.
The ability of 304 stainless steel to undergo substantial deformation prior to fracturing is especially valuable in processes such as welding and machining. When components are welded or machined, the material must readily yield to the tools and stresses involved, leading to better weld integrity and improved machinability. However, it's worth noting that this property can have some less desirable aspects, such as the tendency for localized necking and deformation in certain conditions, a phenomenon known as "piping." This effect highlights the need for precise control in fabrication techniques to prevent the creation of unexpected weaknesses in the final product.
Furthermore, the synergy of strength and ductility in 304 stainless steel makes it suitable for applications where energy absorption during impacts is vital. For example, in automotive parts, where safety under varying loads is paramount, the ability to deform and absorb impact energy is essential to mitigate damage. This is an area where its ductility offers a considerable advantage compared to some other materials.
It is important to recognize that the relationship between processing and mechanical properties isn't always straightforward. While cold working can effectively improve hardness, it can also reduce ductility to a degree. Engineers must carefully consider these trade-offs, opting for processes that provide the ideal balance of strength and ductility based on the specifics of each application. This illustrates the complex relationship between processing techniques and the final mechanical properties of the steel.
Moreover, the material's ductility can be enhanced by post-weld heat treatment. This process helps relieve residual stresses in the material and creates a more uniform microstructure. This benefit is particularly important for ensuring the integrity of welded joints in structural applications. Additionally, the ductility of 304 stainless steel is highly temperature-dependent. For example, at elevated temperatures, the material's ductility tends to increase further, making it suitable for hot forging.
Interestingly, the inclusion of specific alloying elements like molybdenum or higher nickel can also lead to an enhancement of ductility beyond what's typically observed in standard 304 stainless steel. This allows the material to operate more effectively in more challenging environments and applications that demand enhanced formability.
Finally, we must also acknowledge that processing plays a dominant role in determining the overall ductility of 304 stainless steel. Different rolling or shaping techniques can yield significant differences in the final material characteristics. Therefore, a thorough understanding of the fabrication techniques employed is essential to ensure optimal performance of 304 stainless steel in the intended applications. This knowledge is fundamental for ensuring the proper selection and utilization of this widely applied material.
(As of October 10th, 2024)
Exploring the Yield Strength of 304 Stainless Steel A 2024 Update on Material Properties and Applications - Corrosion Resistance Limitations in Chloride-Rich Environments
304 stainless steel generally offers good corrosion resistance, but its performance can be significantly compromised in environments rich in chloride ions. While it performs acceptably when chloride concentrations are under 200 parts per million (ppm), its resistance declines as levels increase. This issue becomes particularly pronounced when chloride concentrations are between 200 and 1000 ppm, where localized corrosion becomes more probable. Moreover, chloride ions can promote pitting and stress corrosion cracking (SCC), even at relatively low temperatures. The potential for SCC and pitting corrosion, which can weaken the material, can be a significant concern, especially when temperatures exceed 60°C. While specialized treatments and alloy modifications, like increasing molybdenum content or novel passivation approaches, can improve corrosion resistance, it is vital to consider how these techniques interact with specific environments to avoid unintended negative effects. The ability to handle chloride environments effectively is influenced by several factors, including the specific manufacturing process used to shape the steel. Thus, a careful evaluation of the environment's chloride levels and the impact of processing on the material is essential when selecting 304 stainless steel for chloride-rich applications.
In environments where chloride concentrations are high, 304 stainless steel faces significant challenges in maintaining its corrosion resistance. While generally suitable for environments with chloride levels below roughly 200 ppm, its performance becomes questionable at levels between 200 and 1000 ppm, highlighting a clear limitation. This is especially troubling in marine settings or areas exposed to salt spray where chloride concentrations are frequently elevated.
The pitting resistance equivalent number (PREN) provides a useful gauge for evaluating a stainless steel's ability to withstand chloride-induced corrosion. For example, 316 stainless steel, with a PREN of 25, exhibits better pitting resistance than 304 (PREN of 20) because of molybdenum's inclusion in 316. This suggests that alloy composition plays a crucial role in determining how a stainless steel will fare in chloride-rich environments. While 304 generally demonstrates good overall corrosion resistance, it remains susceptible to localized corrosion, particularly when exposed to environments containing halide ions like chloride and bromide.
A concerning issue is stress corrosion cracking (SCC), which can initiate at surprisingly low temperatures like 20°C in austenitic stainless steels like 304. The cracking rate rises considerably above 60°C, especially in chloride-rich settings. This behavior implies that the presence of tensile stresses in combination with chloride ions poses a substantial threat to structural integrity, potentially leading to unexpected failure.
While efforts have been made to improve 304's pitting resistance, such as a novel duplex passivation treatment involving both chemical and electrochemical steps, it's important to acknowledge that these methods don't fundamentally address the material's inherent limitations in chloride-rich environments. This is further emphasized by the research conducted on high-strength stainless steels (HSSSs), including austenitic and duplex grades. Cyclic potentiodynamic polarization (CPP) tests have shown their behavior in simulated alkaline environments, but understanding their performance in various chloride-rich environments is still necessary.
Furthermore, it appears that fabrication processes like machining can influence 304 stainless steel's susceptibility to SCC, demanding careful attention to manufacturing procedures when chloride exposure is anticipated. This issue underscores the importance of considering the interplay between processing methods and material behavior in designing applications that involve chloride-containing environments.
Chloride-induced stress corrosion cracking (ClSCC) poses a critical concern across many industries, especially in the oil and gas sector. This has driven the investigation of mitigation strategies and the need to better understand how chlorides influence the materials' performance, leading to the conclusion that further study is needed in this area.
The presence of aggressive ions, particularly chlorides, can substantially diminish stainless steel's localized corrosion resistance. It's important to realize that this degradation can vary depending on specific factors and may not be fully understood for specific applications. Therefore, in environments where aggressive chloride ions are present, it's wise to select a stainless steel alloy that has a higher PREN and is more resistant to pitting and SCC.
The effectiveness of stainless steel in chloride-rich environments is heavily contingent upon the alloy's specific composition and the concentration of alloying elements. While optimizing alloy composition can improve corrosion resistance and mechanical properties, it’s important to carefully assess the specific requirements of the intended application and consider whether 304 stainless steel is the most suitable choice.
(As of October 10th, 2024)
Exploring the Yield Strength of 304 Stainless Steel A 2024 Update on Material Properties and Applications - Temperature Tolerance and Oxidation Resistance of 304 Stainless Steel
304 stainless steel demonstrates a notable ability to withstand high temperatures, a crucial factor in determining its suitability for various applications. Its resistance to oxidation allows for intermittent use at temperatures as high as 870°C and continuous operation up to 925°C. This capability is largely due to the formation of a protective chromium oxide layer that shields the underlying metal from further oxidation. However, continuous operation within a specific temperature range, from 425°C to 860°C, can have an adverse effect on its corrosion resistance, particularly in situations where exposure to moisture is a concern. This behavior underscores a common preference for 304L in applications requiring both high-temperature exposure and resistance to corrosion in humid or aqueous conditions. The temperature sensitivity of corrosion resistance highlights the importance of thoughtful selection of 304 stainless steel for high-temperature applications, recognizing the impact of environmental factors on its performance.
304 stainless steel demonstrates a wide temperature tolerance, handling both cryogenic temperatures down to -196°C and continuous service up to approximately 925°C. This makes it suitable for applications ranging from extremely cold environments to those involving considerable heat. However, maintaining its integrity at the higher end of this range requires careful consideration.
The excellent oxidation resistance that 304 displays comes from the chromium oxide layer that forms naturally on its surface. This protective layer helps shield the steel from further oxidation and corrosion, but it begins to falter at higher temperatures, particularly beyond 870°C. Extended exposure at these temperatures can lead to the eventual deterioration of this protective barrier and, subsequently, a decline in the material's overall performance.
Unfortunately, 304's inherent resistance to oxidation can be significantly compromised by the presence of impurities like sulfur and phosphorus. At high temperatures, these contaminants can greatly accelerate the process of oxide formation and related degradation mechanisms, thus reducing the overall effectiveness of the material in these challenging conditions.
Interestingly, elevated temperatures appear to enhance some of 304's mechanical properties, particularly in scenarios that involve repeated heating and cooling cycles. It performs well in situations where it's exposed to thermal stresses and strains. However, it's important to keep in mind that sustained stress at elevated temperatures can cause the material to undergo relaxation, where it loses some of its stored energy and associated strength, potentially leading to structural or dimensional changes.
The grain structure of 304 stainless steel, like many metals, is susceptible to growth when exposed to sustained high temperatures. While this process doesn't necessarily lead to immediate failure, the changes in the grain structure can alter the yield strength and fatigue resistance of the material. This property needs careful consideration in any application where the material is exposed to prolonged thermal cycling or elevated temperatures.
When 304 is subjected to repeated heating and cooling cycles, particularly after welding, the risk of intergranular corrosion becomes a significant concern. This type of corrosion preferentially attacks the grain boundaries, creating areas of weakness within the material. If not considered and mitigated through post-welding heat treatments, intergranular corrosion can lead to premature failure in structural components or applications where material integrity is vital.
Cold working, a process commonly used to improve yield strength by increasing material hardness, might seem like a straightforward way to enhance the material's performance. But, this process can also negatively impact its oxidation resistance. The distorted microstructures resulting from cold work aren't as effective in forming the necessary protective oxide layers needed to shield the surface from oxidation.
In environments containing sulfur, 304 becomes vulnerable to a specific form of corrosion known as sulfide stress corrosion cracking (SSCC). This phenomenon can occur even at relatively moderate temperatures. This illustrates that temperature tolerance needs to be considered in combination with the chemical nature of the surrounding environment.
As temperature increases, the yield strength of 304 initially increases, but after a certain point, it starts to decrease. This highlights the need for careful evaluation of the intended service temperatures when designing components that will experience elevated temperatures. Determining the exact temperature threshold where yield strength starts to decrease is crucial in achieving the intended performance and functionality of the components.
The thermal conductivity of 304 stainless steel is relatively low compared to many other metals. This seemingly minor detail can become a significant consideration in certain applications, especially those involving heat transfer. In thermal management systems such as heat exchangers, the low thermal conductivity of 304 can create a bottleneck, limiting the material's ability to transfer heat efficiently. Understanding and mitigating this constraint is crucial in specific applications.
In summary, while 304 stainless steel is a highly versatile material suitable for a wide range of temperatures and applications, a comprehensive understanding of its properties and limitations within specific environmental conditions is essential for ensuring its optimal performance.
(As of October 10th, 2024)
More Posts from aistructuralreview.com: