Critical Temperature Thresholds in Cast Iron Welding How to Stay Below 1400°F for Optimal Results
Critical Temperature Thresholds in Cast Iron Welding How to Stay Below 1400°F for Optimal Results - Temperature Control Strategies to Maintain Cast Iron Below 1400°F During Welding
Successfully welding cast iron hinges on keeping the material's temperature below 1400°F. This prevents the formation of cracks, a common issue when cast iron exceeds this critical threshold. To achieve this, careful management of temperature throughout the process is crucial.
Preheating the cast iron before welding is a fundamental step. A preheat temperature range of 600°F to 700°F is often recommended. This gradual heating helps to reduce the thermal shock the material experiences during welding, lowering the chances of cracking. During the welding process itself, concentrating the heat input into a narrower, deeper weld zone minimizes distortion.
The cooling phase after welding is equally vital. Slow, controlled cooling is paramount to avoiding the stresses that can lead to cracks. Rapid cooling methods like water or compressed air quenching should be avoided entirely. Further, the condition of the metal's surface before welding plays a significant role. Proper preparation, including techniques like gouging and chamfering, is key to a successful weld. Ignoring surface preparation can set the stage for unwanted cracking later on. By employing these careful temperature control measures, you can improve your chances of achieving a strong, durable weld in cast iron.
Maintaining cast iron below 1400°F during welding is paramount, as exceeding this point can drastically compromise the material's strength and resilience. This temperature range is crucial for preserving the beneficial graphite structure within cast iron. When temperatures soar beyond the threshold, the graphite's morphology can shift, leading to a brittle microstructure that makes the iron more susceptible to cracking under stress.
Preheating the cast iron before welding is a common technique that aims to regulate the temperature profile during the process. Carefully managed heat input helps minimize the likelihood of localized overheating and supports consistent temperature distribution. Strategically employing heat sinks, like copper blocks, can absorb some of the heat generated during welding. This acts as a temperature buffer, ensuring the base metal remains within the desired temperature range for optimal welding outcomes.
While post-weld heat treatments can potentially address residual stresses and restore some material properties, their implementation needs careful consideration. Improper heat treatment can unintentionally introduce new microstructural alterations that compromise the iron. It's worth noting that the selection of filler metal can influence the overall welding temperature. Using filler alloys with lower melting points can facilitate better control of the temperature during the welding process.
Cast iron's distinct carbon content dictates its thermal expansion, setting it apart from steel and highlighting the need for unique welding temperature control strategies. Environmental factors, such as humidity and airflow, can impact cooling rates post-weld. Accounting for these influences during the design and implementation of cooling protocols is critical in preventing unexpected cracking or distortion. Using insulating coverings or blankets over the weld area is another approach that can help manage heat dissipation, preventing overly rapid cooling, and potential problems associated with that.
Real-time temperature monitoring using thermal imaging offers engineers a visual representation of the weld’s temperature profile. This visual data enables them to fine-tune the welding parameters on the fly and ensure the cast iron remains within its optimal temperature window, improving weld quality and reducing the chance of failure. As our research continues, hopefully these methods will provide more precise control of welding parameters and lead to more consistent results in this challenging material.
Critical Temperature Thresholds in Cast Iron Welding How to Stay Below 1400°F for Optimal Results - Measuring Heat Distribution with Digital Thermometers and IR Temperature Guns
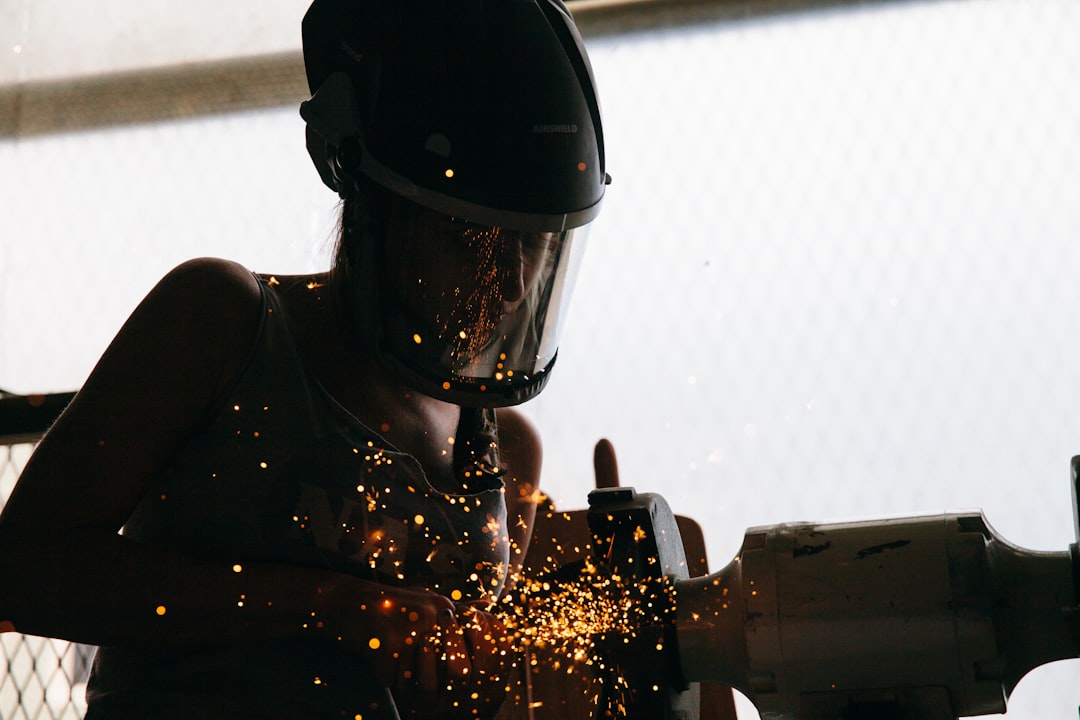
Precisely gauging heat distribution is paramount in cast iron welding, where keeping temperatures under 1400°F is vital for preserving the material's structural integrity. Digital thermometers and infrared (IR) temperature guns are useful for this purpose, able to measure temperature ranges relevant to cast iron welding, although their accuracy can vary. The material's emissivity—which is high in cast iron—has a notable impact on how IR thermometers perform, making it important to understand how these tools function properly.
IR temperature guns work by measuring the infrared radiation emanating from a surface, providing a snapshot of the temperature distribution—if aimed correctly. A key consideration when using IR thermometers is the distance-to-spot ratio, which dictates the size of the area measured from a particular distance. To achieve reliable readings, it's essential to calibrate these instruments. Without proper calibration, the risk of inaccurate readings can lead to suboptimal welding results and potential flaws in the final product. It's crucial to use these tools with awareness of their limitations to prevent potential issues.
1. **Remote Temperature Sensing with Infrared Guns:** Infrared (IR) temperature guns offer a valuable way to measure surface temperatures without direct contact, especially beneficial in situations like cast iron welding where proximity to heat can be hazardous. This non-contact approach can make measuring the heat near molten metal much safer and more practical than traditional contact methods.
2. **Cast Iron's Emissivity and IR Accuracy:** The accuracy of IR temperature readings relies heavily on the material's emissivity, a measure of how well it emits infrared radiation. Cast iron, having an emissivity near 0.85, generally yields decent IR readings. However, surface treatments like paints or coatings can alter emissivity and necessitate adjustments for accurate measurements. Understanding this nuance is vital for obtaining reliable temperature data.
3. **Mapping Heat Patterns with Temperature Sensors:** Both digital thermometers and IR guns offer the potential to pinpoint temperature variations across a weld area. By capturing these localized temperature changes, engineers can potentially identify hotspots that might otherwise go unnoticed. This fine-grained temperature mapping can help optimize heat distribution during welding and enhance the overall integrity of the weld.
4. **Thermal Imaging as a Preventive Tool:** Utilizing thermal imaging during the welding process can be quite helpful in preventing issues before they manifest. For instance, if insufficient preheating or cooling is occurring, thermal imaging can potentially highlight these deficiencies in real-time. This immediate visual feedback can allow for on-the-spot adjustments, potentially reducing defects like cracking.
5. **IR Thermometer Limitations: Reflective Surfaces:** IR thermometers face challenges when dealing with reflective surfaces, like shiny spots or metal splatter, which can interfere with accurate temperature measurements. In these cases, the reflected temperature might be captured instead of the actual temperature of the area of interest. This can lead to potentially inaccurate measurements and highlights the need for careful aiming and understanding of the limitations of IR thermometers in certain situations.
6. **Time Lag in Temperature Response:** The speed with which an IR thermometer, and indeed any thermometer, responds to temperature changes can lead to a lag between the actual temperature and the displayed value. This can be more of a concern in high-speed welding operations where real-time feedback is paramount. Researchers may need to carefully account for this lag when interpreting temperature readings in dynamic environments.
7. **Ambient Conditions and Their Influence:** Factors like ambient temperature, airflow, and humidity can all impact thermometer accuracy. In environments with significant temperature fluctuations or uncontrolled airflow, any thermometer reading might be skewed. Researchers conducting these measurements should be aware of these potentially confounding influences and take steps to account for them, especially in outdoor settings.
8. **Alternative to Digital and IR: Bimetallic Thermometers:** While digital and IR thermometers offer a level of precision, traditional bimetallic thermometers might be a suitable option in some cases. Bimetallic thermometers often withstand high temperatures and harsh conditions better and can be a robust alternative where extreme durability is prioritized, even if the level of precision isn't as critical.
9. **Temperature Gradients and Optimized Welding**: By measuring temperature gradients in a weld area, engineers gain a deeper understanding of how heat is distributed. This knowledge allows them to potentially adjust welding techniques to create a more uniform heating profile. Minimizing significant heat variations in the weld zone can potentially mitigate thermal stress concentration, lowering the risk of weld cracking.
10. **Connecting Temperature with Phase Changes:** Understanding the phase transitions of cast iron as it nears 1400°F, where it goes from solid to liquid states, is vital. By carefully monitoring temperature, it's possible to guide these phase changes within acceptable boundaries. This knowledge is critical to prevent exceeding critical temperature limits during phase changes, thus preventing the microstructural failures that can compromise the integrity of the weld.
Critical Temperature Thresholds in Cast Iron Welding How to Stay Below 1400°F for Optimal Results - Proper Preheating Methods Using Electric Blankets and Ceramic Heating Elements
When welding cast iron, maintaining a temperature below 1400°F is paramount for optimal results. To achieve this, preheating the cast iron before welding is a key strategy, and electric blankets and ceramic heating elements offer effective methods for achieving this preheat.
Electric blankets, in particular, can distribute heat evenly across a large surface area, while ceramic heating elements provide greater control and allow for precise temperature adjustments. This ensures the cast iron reaches the desired preheating range (often 600°F to 700°F) gradually, minimizing the thermal shock that can cause cracking during the welding process. However, one must remain vigilant during these preheating stages to avoid uneven heating, as this can lead to increased stress within the material and affect the weld quality negatively.
It's essential to emphasize the importance of integrating accurate temperature monitoring throughout the process when using these methods. This enables real-time feedback, helping to ensure the cast iron stays below 1400°F while preventing any undesirable temperature variations. These methods, in conjunction with monitoring, contribute significantly to a successful cast iron weld, maximizing strength and durability. Without careful management of temperature during all stages of the process, the risk of cracking and other defects increases, significantly impacting the reliability of the final product.
When it comes to preheating cast iron before welding, achieving the right temperature uniformity is crucial to avoid cracking and ensure a strong weld. Electric blankets, due to their ability to cover large areas, can help in achieving consistent heat throughout the workpiece. This consistent heat application can help to mitigate the risk of localized overheating, a common cause of cracking in cast iron welds.
Ceramic heating elements offer a different approach to preheating. Their rapid heating response is a desirable feature when quick adjustments to the heating process are needed. However, while quick to respond, it's vital to ensure these heating elements are properly controlled and not allowed to overheat any specific area of the casting. Modern electric blankets often come equipped with built-in thermostats, offering a greater level of control over the preheating temperature. This reduces the risk of exceeding the crucial 1400°F limit, which can have detrimental effects on the cast iron's structure.
It's worth noting that the thermal conductivity of cast iron itself impacts how effectively it absorbs heat. While the surface might heat quickly, the core can lag behind. This difference in heat transfer needs to be considered when designing the preheating process, especially with methods like electric blankets. The ability to combine electric blankets with ceramic heaters provides a more dynamic heat management approach. This dynamic strategy is particularly useful when aiming for a very specific and uniform preheat temperature across the entire casting.
However, it's crucial to emphasize that safety is always paramount when working with electrical equipment. Electric blankets, if not carefully monitored and maintained, can pose fire risks, especially when in environments with flammable materials. The preheating strategies explored here – electric blankets and ceramic heaters – are not limited to just cast iron welding. Industries like aerospace also benefit from these technologies for precise temperature control during the fabrication of parts under demanding standards.
Further, it's important that engineers have the ability to customize the heating process based on the specific type of cast iron being welded. Fortunately, many electric blankets provide adjustable settings that cater to these varying compositions. This level of flexibility is invaluable in achieving the desired preheat temperatures for a wide range of cast iron alloys.
The effect of these heating methods on the post-weld cooling phase is also worth mentioning. Insulating blankets, such as electric blankets, can extend the cooling process, promoting a slower, more gradual transition within the cast iron's structure. This slower cooling helps to minimize thermal stresses and, therefore, the probability of cracking after welding. The more we understand the interaction of different heating techniques and cast iron's behavior at different temperatures, the closer we get to consistently creating robust, reliable welds in this challenging material.
Critical Temperature Thresholds in Cast Iron Welding How to Stay Below 1400°F for Optimal Results - Cooling Rate Management Through Insulation and Controlled Environment
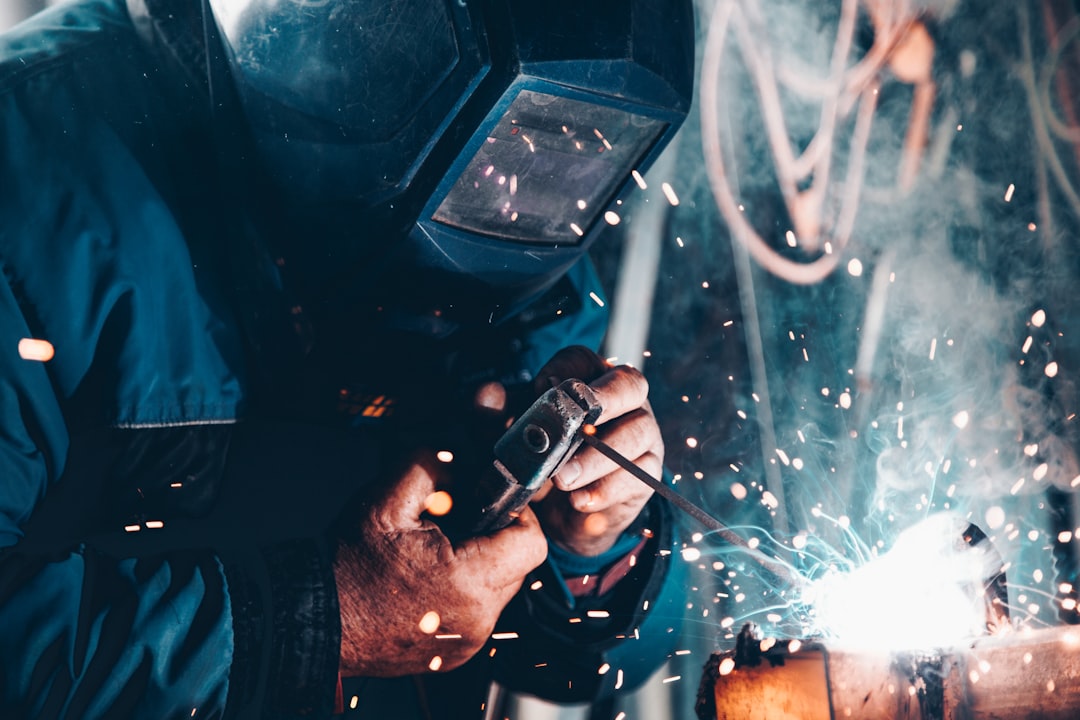
Managing the cooling rate after welding cast iron is crucial, particularly when aiming to stay below the critical 1400°F temperature. This involves using insulation and controlling the environment surrounding the weld. By slowing down the cooling process through insulation, such as using blankets or covers, the material experiences a more gradual temperature shift. This controlled cooling reduces the risk of developing undesirable microstructures that can lead to cracks and brittleness. Further, maintaining a controlled environment minimizes external influences like humidity or air currents that can cause uneven cooling, potentially introducing stress and distortion. The ability to carefully manage the cooling phase helps achieve optimal mechanical properties in the welded joint, minimizing the likelihood of cracking and ensuring the resulting weld is as strong and durable as possible. While challenging, it is possible to achieve desirable outcomes through this deliberate control of cooling.
Managing the cooling rate during cast iron welding is crucial for achieving the desired mechanical properties and preventing cracking. This is particularly important when trying to maintain temperatures below 1400°F. The way we insulate the weld area plays a significant role in how quickly or slowly the cast iron cools. Using effective insulation materials can slow down the heat loss, leading to a smoother, more gradual cooling phase, which is better for minimizing the risk of cracks.
Furthermore, the surrounding environment in which the welding is conducted can also have an impact. Maintaining a consistent and controlled environment – for example, keeping the ambient temperature stable and reducing variables like drafts and humidity – can help create more consistent and predictable cooling rates. This helps to avoid inconsistencies that can sometimes lead to undesirable changes in the cast iron's microstructure.
How thick the cast iron piece is also matters when we consider how it cools. Thicker sections will naturally cool more slowly than thinner parts. Recognizing this is critical when planning how to insulate and manage the cooling process, ensuring consistent temperatures across the entire weld area.
It seems intuitive that a slower cooling rate is preferable for promoting beneficial changes in the material's structure, allowing the microstructure to transform in a way that enhances its strength. However, it's not simply a case of just slowing things down as much as possible. The cooling needs to be carefully controlled to ensure the appropriate phase changes happen in a gradual way for optimal results.
The precise placement of insulation materials can significantly influence the temperature profile of the welded part. The ability to create targeted temperature gradients using insulation can be very helpful in managing the internal stresses that develop in the cast iron during cooling, potentially lessening the risk of cracking.
Understanding the different ways heat can escape from a body is crucial. We're dealing with three key heat loss mechanisms: convection (heat transfer via fluids), conduction (heat transfer via direct contact), and radiation (heat transfer through electromagnetic waves). Knowing these mechanisms is key for improving the effectiveness of the insulation and maximizing its ability to control temperature.
The significant temperature changes during the welding process can cause cast iron to expand and contract, which can stress the material. Well-designed insulation can help regulate this expansion and contraction, particularly during the cooling phase, ultimately minimizing the likelihood of cracking caused by uneven shrinking.
The specific filler metal used during welding also influences the temperature characteristics of the weld pool, affecting the subsequent cooling rate. Insulation and cooling strategies need to consider this. Using filler metals with different melting points might require different cooling management.
We're starting to see some intriguing advancements in insulation technology, including novel materials like aerogels and vacuum panels. These materials have extraordinarily low thermal conductivity, which might provide better control over cooling rates than traditional insulation methods. It'll be interesting to see how they're implemented in the welding world.
Finally, to ensure our approaches are effective, we can use thermal imaging and temperature monitoring tools to measure and record temperature changes during cooling. This data can help us quantify the impact of our insulation strategies, refine our understanding, and adjust our methods as needed to optimize our approach to cooling rate management.
Critical Temperature Thresholds in Cast Iron Welding How to Stay Below 1400°F for Optimal Results - Heat Input Calculation Methods for Cast Iron Welding Projects
Successfully welding cast iron hinges on carefully managing the heat introduced during the process. This is particularly crucial for cast iron, as exceeding a critical temperature of 1400°F can lead to significant structural weaknesses, including cracking. Calculating and controlling heat input is a key part of this process, and a number of methods are used to do this.
The most common method for calculating heat input involves a relatively straightforward formula that considers the welding current, voltage, and travel speed. This formula, usually expressed in kJ/in, allows welders to make adjustments to their technique in order to achieve optimal results. Tools that utilize this formula are also available and make the job of maintaining control over the heat input easier. Beyond this standard approach, there are other methods for indirectly controlling heat input. For example, understanding the type of electrical current being used—whether it's AC or DC—can influence how the heat input affects the weld. The volume of weld metal being deposited also plays a role in the overall heat input, and can be used as another way to gauge and adjust the heat input.
The reason these adjustments are so important is that heat input has a profound effect on the properties and structure of the weld zone. This means controlling heat input directly influences the strength and integrity of the finished weld. In the specific case of cast iron, with its unique thermal properties and susceptibility to cracking, precise heat management is essential for creating welds that meet the design requirements. Using accurate heat input methods are essential to help minimize risks of defects and achieve the desired weld quality in the challenging environment of cast iron welding.
1. **Heat Input's Role in Cast Iron Welding:** Calculating heat input during cast iron welding is crucial, as it's a major factor in determining the final properties of the weld. We can calculate it with the formula: Heat Input (kJ/in) = (60 x Amps x Volts) / (1000 x Travel Speed). While seemingly straightforward, understanding how factors like amperage, voltage, and travel speed interplay with the heat input becomes essential for keeping the weld within the desired temperature range.
2. **Microstructure Modification**: One of the most concerning aspects of exceeding 1400°F in cast iron is the potential shift in its microstructure. The graphite within the material, which influences its strength and ductility, can transition from a preferred flake shape to a less desirable spheroidal shape. Understanding how heat input relates to these microstructural changes is fundamental for preserving desirable properties.
3. **Localized Heat Input Control:** Rather than treating the entire weld area uniformly, it's often beneficial to employ localized heat management strategies. This could involve using different welding techniques or altering the welding parameters in different areas. This approach provides more control over the heat distribution and makes it easier to maintain the temperature below the critical threshold, reducing the risk of issues like cracking.
4. **Cooling Rate and Post-Weld Structure:** The rate at which the weld cools after it's made impacts the resulting microstructure, which significantly affects mechanical properties. A rapid cooling rate can lead to undesirable phases like martensite, which can make the weld brittle. A controlled, gradual cooling process allows the cast iron to transform into a more desirable tempered structure, increasing its toughness and ductility. Managing the cooling phase helps ensure the weld joint can perform optimally.
5. **Filler Metal Choices Impact Heat Input:** The filler metal we use plays a major role in the heat input calculations. Materials with a greater concentration of alloying elements tend to have higher thermal conductivities. This influences how heat travels through the weld zone, requiring adjustments in welding parameters or techniques to manage heat properly. Failing to consider these effects could lead to excessive heat input.
6. **Welding Technique and Heat Input**: Different welding techniques impact the amount of heat delivered to the weld area. Gas tungsten arc welding (GTAW, or TIG) and gas metal arc welding (GMAW, or MIG) can both weld cast iron, but MIG generally leads to higher heat inputs due to its speed and the nature of the process. This distinction becomes crucial when welding intricate cast iron parts, where excessive heat can easily be concentrated in localized regions, exceeding the critical 1400°F point.
7. **Real-Time Temperature Monitoring is Vital:** To precisely control heat input, real-time temperature monitoring throughout the welding process is essential. Data loggers provide engineers with continuous, detailed temperature readings. This allows for immediate adjustments to welding parameters or techniques, if needed, safeguarding against exceeding the critical temperature and ensuring a smooth process.
8. **Thermal Cycling's Cumulative Impact:** Cast iron's response to multiple thermal cycles during the welding operation is crucial to understand. Each heating and cooling cycle causes changes to the material's microstructure, and it's essential to assess how the cumulative effects of these cycles impact the material's overall performance.
9. **Cast Iron Thickness Matters:** When welding thicker pieces of cast iron, the cooling process takes longer compared to thinner ones. This calls for adapting preheating and cooling strategies to account for different sections of the weld. Thorough understanding of how heat flows in different thicknesses of cast iron is vital for creating a uniform temperature profile and avoiding unexpected consequences.
10. **Harnessing the Power of Simulation**: Modeling heat distribution during welding using computer simulations is becoming more common. These tools enable engineers to anticipate potential problems before they occur by visualizing temperature changes and identifying areas prone to overheating. This advanced technique helps refine the approach to welding cast iron without trial and error, ultimately contributing to more robust welds that stay within critical temperature thresholds.
Critical Temperature Thresholds in Cast Iron Welding How to Stay Below 1400°F for Optimal Results - Temperature Monitoring Systems and Documentation Requirements for Quality Control
Temperature monitoring systems are increasingly important for maintaining quality in many fields, including welding. In cast iron welding, keeping track of temperatures is critical to prevent the material from exceeding 1400°F, a temperature that can cause cracks and weaken the metal. These systems often use modern technologies like wireless sensors and thermal imaging cameras to provide continuous temperature data, allowing for swift adjustments to maintain the correct temperatures during the welding process. It's crucial that these systems are used in a way that complies with industry regulations and that comprehensive records of the temperature readings and system performance are maintained. This documentation helps to ensure that the process is both consistent and meets quality control requirements. To get the best results from welding cast iron, you need a well-planned temperature control strategy, and this includes implementing systematic testing of the temperature monitoring system itself. This multifaceted approach is vital to maximizing the chances of achieving a high-quality weld while minimizing the risk of defects.
1. **Real-time temperature monitoring systems** are becoming more integrated with welding equipment, automatically adjusting welding parameters as temperature readings change. This continuous feedback loop helps keep the cast iron within the desired range below 1400°F, which is crucial for avoiding defects.
2. **Calibration of temperature sensors** is essential for ensuring the accuracy of the data collected during welding. Even minor inaccuracies can lead to problems, as it can mean the difference between a successful weld and one that fails due to overheating. If we can't trust the data we're getting, we can't make good decisions about welding processes.
3. **Documenting the temperature data** is a critical part of quality control in welding. Not only does it help ensure compliance with industry standards (if applicable), but it also provides a record of the temperature history that can be useful when troubleshooting problems with welds in the future.
4. **Analyzing historical temperature data** can help identify trends and patterns that might be contributing to defects or failures in welds. This type of analysis allows engineers to adjust their welding techniques or process parameters, leading to an improvement in the overall quality of the welds over time. It gives a historical overview of what has worked and what hasn't.
5. **Surface conditions of the cast iron can impact temperature measurements**. Oil, rust, or other contaminants on the surface of the cast iron can act as insulation, leading to inaccurate readings from the sensors. This can result in an area getting hotter than anticipated, potentially leading to overheating during the welding process.
6. **Automated alert systems** in some temperature monitoring setups can send a warning to the welder if temperatures get too close to the critical 1400°F limit. This rapid notification provides a chance to make adjustments and prevent damage to the weld or the cast iron before it happens, reducing risk to the process. It's another step towards a more proactive and safer process.
7. **The link between temperature and the cast iron's microstructure** can be quite complex. Observing how the temperature changes during welding allows us to see how the microstructure of the cast iron is being influenced. Understanding this connection can help us design welding procedures that lead to desirable microstructures (or avoid ones that create problems). This adds yet another dimension to the complexity of this process.
8. **Data visualization tools** can be very helpful in providing real-time graphical representations of the temperature data during welding. The visualization tools can reveal potentially problematic hotspots and allow the welder to make immediate adjustments to ensure the weld is under control. It helps give a more complete picture of the entire area being welded, which is harder to do with a single point measurement.
9. **Artificial intelligence (AI) is starting to play a role** in some more advanced temperature monitoring systems. These systems can use AI techniques to predict future temperature changes based on historical data from past welding procedures. This capability can make welding operations even more responsive, further improving quality control. While this is a newer area, it has the potential to further refine our control of welding parameters.
10. **Following documentation requirements is not just about compliance.** It's also a key part of a quality assurance system for any welding operation. By properly documenting and archiving the temperature data, we can develop a robust roadmap for continuous improvement in welding practices. It helps create a culture of learning and a way to systematically improve overall welding quality.
More Posts from aistructuralreview.com: