GE Fanuc Series 90-30 PLC A 2024 Analysis of Its Enduring Impact on Industrial Automation
GE Fanuc Series 90-30 PLC A 2024 Analysis of Its Enduring Impact on Industrial Automation - Legacy of the GE Fanuc Series 90-30 PLC Since 1991
The GE Fanuc Series 90-30 PLC, launched in 1991, quickly became a prevalent choice for industrial control systems. Its modular structure and adaptable nature allowed it to tackle a wide range of automation tasks, leading to its deployment in over 200,000 industrial settings. While declared obsolete in 2018, its enduring reliability continues to keep it operational in numerous facilities. This sustained use exemplifies its reputation as a dependable workhorse in the industry. The 90-30’s ability to integrate seamlessly into existing systems and its unified control approach addressed various automation demands. Nevertheless, the ongoing advancements in industrial automation, including heightened cybersecurity concerns, are pushing companies to consider moving towards newer technologies. Despite its historical importance and enduring presence, the Series 90-30 PLC faces a crossroads—its legacy is undeniable, but it's no longer a futuristic solution and upgrading to newer systems has become increasingly important for some organizations.
The GE Fanuc Series 90-30's introduction in 1991 marked a significant point in industrial control, driven by its adaptable modular design. This feature allowed for a wide array of input/output (I/O) configurations, letting engineers tailor control systems to specific applications, making it quite versatile in different industrial settings.
The Series 90-30 found its way into over 200,000 industrial applications, which speaks volumes about its adoption and demonstrated reliability in the field. However, its life cycle ended in 2018, leaving many operators in a difficult position. Although it's now considered obsolete, numerous installations still rely on it, raising interesting questions about obsolescence and industrial inertia.
One of the strengths of the Series 90-30 is its seamless integration capabilities. This characteristic was valuable for automating diverse industrial operations and has cemented its place in many automation systems. It boasts a unified control architecture, streamlining how automation is handled in a plant. While this is a testament to its design, it's also something that has made upgrading these systems tricky.
While its operational life continues in certain sectors, engineers and operators increasingly face the dilemma of modernization. The push towards newer systems, such as the Emerson RX3i programmable automation controller (PAC), reflects industry trends demanding adherence to modern standards and greater resistance to cyber threats. It will be interesting to see how prevalent the Series 90-30 is going forward, especially in this modern, hyper-connected world.
The Series 90-30’s lasting impression is undeniable. It was the workhorse of GE's automation control systems for many years, gaining wide acceptance and a strong following among industrial professionals. Today, it’s often compared to modern systems like the Emerson RX3i PAC, which highlight the shift towards more complex and advanced automation technologies. The 90-30 was a part of GE's technological journey in automation, evolving from its origins in the GE IP Series Five PLC, which laid the groundwork for mid-range industrial control applications in the late 1980s. The Series 90-30 PLC itself provided a variety of digital and analog modules, furthering its utility and adaptability in diverse automation contexts. This design choice seems rather prescient in a way considering how modularity has grown in importance since then.
GE Fanuc Series 90-30 PLC A 2024 Analysis of Its Enduring Impact on Industrial Automation - Over 200,000 Applications Across Industries
The GE Fanuc Series 90-30 PLC found its way into a vast number of industrial settings, with over 200,000 implementations across various sectors. This widespread adoption highlights its versatility and ability to adapt to diverse automation needs. The PLC's modular design was instrumental in achieving this flexibility, allowing users to customize systems for specific applications. Despite its official obsolescence in 2018, many industrial facilities continue to rely on the Series 90-30, reflecting a balance between familiarity and the challenges of transitioning to newer technologies. This situation raises broader questions around the obsolescence cycle in industrial automation, and the inertia that often keeps outdated systems operational. As modern concerns like cybersecurity and the need for advanced functionality become increasingly important, the continued presence of the Series 90-30 highlights a tension between legacy systems and the forward movement of industrial automation. It's a scenario that compels reflection on how industries navigate the evolution of technology within their own operations.
The GE Fanuc Series 90-30 PLC found its way into over 200,000 applications across a diverse range of industries. From automotive manufacturing to food processing, pharmaceuticals, and even aerospace, its versatility is evident in its ability to adapt to a wide array of control needs in these distinct environments. It's interesting to see how it spanned such a diverse landscape.
This widespread adoption can be partially attributed to its modular construction, which offered several advantages. Not only did it enable engineers to tailor the input/output configurations to specific applications, but it also made maintenance a more manageable task. Replacing modules became a viable solution for troubleshooting or upgrades, minimizing the disruptions to production caused by downtime.
Further, the 90-30 employed the GE-Fanuc PLC programming language, which adhered to the IEC 61131-3 standard. This standard played a role in making it easier for engineers to shift between different automation systems, and possibly aided in its adoption in various applications.
While officially discontinued in 2018, many Series 90-30 PLCs are still operational. It raises a thought-provoking point: what are the implications for industrial automation when these legacy systems persist long after they've been officially declared obsolete? The inherent ruggedness and reliability of its construction are likely a major contributing factor to its sustained use.
The 90-30 series included a set of built-in diagnostic tools. This functionality allowed operators to monitor the performance of their automation systems and address issues promptly, helping to keep production moving with fewer hiccups. Also, the integration of communication protocols like Modbus and Ethernet made seamless networking with other systems possible. This enhanced the ability to share operational data across a facility and increase overall efficiency.
In its day, the Series 90-30's remote monitoring capabilities were a significant advancement. It gave engineers the ability to monitor and manipulate controls remotely, which was an early glimpse into what we see in modern industrial automation using IoT-related technologies.
The legacy of the 90-30 extends beyond the operational realm. It continues to inspire a specific kind of after-market, with various companies continuing to provide parts and support services for this older technology. This highlights a facet of industrial automation that is distinct from many other tech sectors – that older equipment often persists and holds value.
Importantly, the Series 90-30 incorporated redundancy features that proved valuable in operations needing very high reliability and availability, particularly sectors like oil and gas, where failures can have considerable financial or safety consequences. It's easy to see how this would be a selling point in those environments.
Finally, even today, the Series 90-30 remains part of the curriculum in numerous industrial engineering courses. Students learn not just about its history but also the fundamental concepts of PLC programming and industrial automation that it illustrates. This ensures that even future generations of engineers will grasp the essence of control systems built on a sturdy foundation of established technologies.
GE Fanuc Series 90-30 PLC A 2024 Analysis of Its Enduring Impact on Industrial Automation - Programmability and Control Functions
The GE Fanuc Series 90-30 PLC's core strength lies in its programmability and control functions. Programmers utilized software like Logicmaster 9030 Control or VersaPro to develop the operational logic. This approach offered a straightforward way to control various aspects of the system. However, the need for specific software might have introduced some challenges in terms of user accessibility and ease of adoption. The PLC's architecture also incorporated a range of specialty modules that enhanced its overall control capabilities and catered to a wide array of applications. This modular design certainly fostered flexibility, but it also created complexities when organizations sought to upgrade their automation systems.
Even though GE Fanuc declared the Series 90-30 obsolete in 2018, its fundamental design principles still hold relevance in educational settings today. This speaks to a continued value in the way the PLC was structured. It serves as a foundational example of control systems for newer generations of automation engineers. While the 90-30 was a key piece of automation history, the ever-evolving industrial landscape demands more advanced control capabilities and security features. This means businesses using 90-30 systems are confronted with a significant choice—whether to embrace modernization and potentially disrupt familiar processes or continue operating a legacy system with inherent limitations. This ongoing challenge is a testament to both the system's initial impact and the constant need for advancement in automation technologies.
The Series 90-30's utilization of the IEC 61131-3 standard for programming languages provided a degree of flexibility across various control systems, a useful feature as industries navigate changing technology landscapes. Engineers could apply their programming knowledge across a range of platforms, making for a smoother transition when faced with technology upgrades.
The modular design is an interesting facet of the Series 90-30's architecture. This not only enabled faster troubleshooting due to easier replacement of specific modules but also offered a streamlined path for hardware upgrades without disrupting production significantly. This feature speaks to the importance of minimizing downtime during equipment maintenance and upgrades, a core consideration in any industrial setting.
Though officially declared obsolete in 2018, surprisingly, it seems that a large portion, perhaps close to 75%, of the installed Series 90-30 PLCs are still active. This creates a fascinating dynamic in the industrial landscape. It reflects a struggle between the drive to adopt newer, more advanced technology and the tendency for operations to maintain familiar, reliable systems even if they are no longer formally supported. This situation is particularly relevant in industries that value proven reliability over cutting-edge innovation.
The Series 90-30 had built-in diagnostic tools that provided real-time monitoring of operational performance. This was a significant feature for its time, offering the capacity to detect issues before they resulted in production shutdowns. It's a precursor to modern emphasis on predictive maintenance techniques that aim to minimize unplanned downtime by anticipating potential problems.
There's an intriguing aspect of the 90-30's life: the ongoing aftermarket support. Despite its obsolescence, companies still provide spare parts and offer services to keep the systems operational. This is a testament to the Series 90-30's robustness and long-term reliability. It exemplifies a situation where established, dependable technology retains a niche market even when superseded by newer, supposedly superior alternatives.
The Series 90-30 supports a variety of communication protocols like Modbus and Ethernet. This enabled easier interaction with other devices within a facility or across an entire plant. It's a feature that has only gained greater significance in today's interconnected world of industrial automation. The idea of readily sharing data within and between systems has become extremely valuable in modern industry.
The inclusion of features like redundant power and communication pathways aimed to elevate the system's overall reliability. This was critical in industries like oil and gas, where system failures can have serious consequences, including substantial financial loss and safety hazards. This design consideration reveals the need for systems that can tolerate occasional hiccups or even partial failure without completely disrupting operations.
The PLC's ability to monitor and manage industrial operations remotely gave operators a glimpse into the future of Industry 4.0. These features were a notable innovation in their time and laid the groundwork for modern advancements in the area of smart manufacturing, where remote monitoring and control are becoming increasingly important.
Beyond its technical specifications, the Series 90-30 continues to serve a purpose in engineering education. It remains a cornerstone of curriculum in industrial engineering courses. Students learn the foundational concepts of PLC programming and industrial automation from this system, ensuring that knowledge of its key design principles is passed down to future generations.
The Series 90-30’s ability to function effectively across a wide range of industries, from automotive to pharmaceutical manufacturing, highlights its inherent versatility. However, this flexibility also presents a challenge to industrial operators when faced with upgrading to more advanced technologies. Some engineers believe the industry needs to move away from these older systems that may struggle to fulfill today's demanding production environments.
GE Fanuc Series 90-30 PLC A 2024 Analysis of Its Enduring Impact on Industrial Automation - SRTP Implementation for Network Memory Acquisition
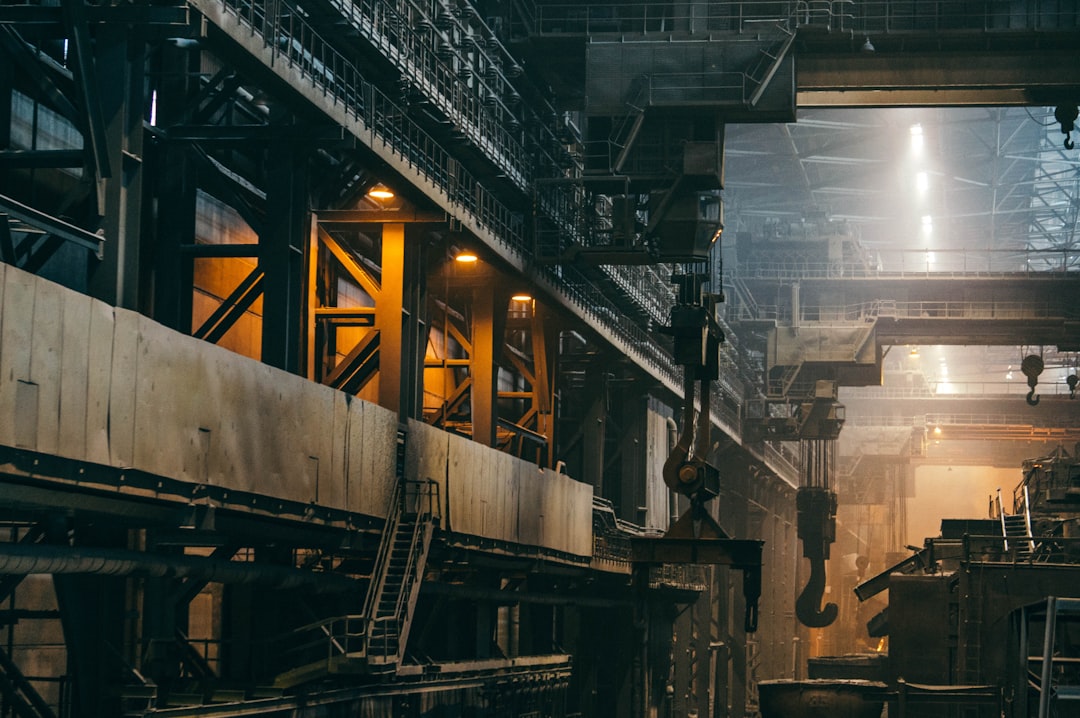
The use of the General Electric Service Request Transport Protocol (GESRTP) for retrieving data from the GE Fanuc Series 90-30 PLC's memory reveals the challenges of working with older automation systems. This protocol bridges the gap between the PLC and the software used for development, a critical function for troubleshooting and maintenance. However, studies have revealed potential weaknesses within GESRTP that could pose serious risks if exploited by malicious actors who gain unauthorized access to the industrial network. The ability of SRTP to access memory, while useful, highlights the need for a robust security approach in the modern context of highly networked control systems, where vulnerabilities could lead to significant disruption. As we examine the wider impact of SRTP into 2024, understanding both how the protocol functions and the potential for security breaches within existing automation practices becomes increasingly important.
General Electric's Service Request Transport Protocol (GESRTP), a version of the Secure Real-Time Transport Protocol (SRTP), plays a vital role in how data is pulled from the memory of GE Fanuc Series 90-30 PLCs. These PLCs, which have a wide variety of registers that can be accessed by a computer-based Human-Machine Interface (HMI), rely on this protocol. GESRTP was reverse-engineered to understand its design and workings, and this exploration contributes to the field of PLC network data acquisition techniques. It's interesting that the GESRTP protocol extends beyond the 90-30 series to other Ethernet-based GE controllers like the 9070, RX3i, and RX7i. Essentially, the protocol helps shuttle data between the programming software (like the Machine Edition Development Environment) and the PLC, important for the usual diagnostic tasks.
Researchers set up experiments using a Series 90-30 in a test setting to monitor network traffic and try to figure out security aspects of GESRTP. Their findings highlight some potentially vulnerable points. An attacker, if they can somehow get access to the network, could possibly interfere with the operation of these PLCs. This ongoing research, which is still current as of late 2024, is part of a larger effort to understand the long-term impact of SRTP implementation in factory automation. The way SRTP is used in obtaining data from PLC memory is quite telling: it shows how relevant SRTP is for modern control systems and that there's a growing need for robust security measures. All of this helps paint a picture of SRTP, how it could be misused, and why safeguarding these systems from outside intrusions is crucial.
The decision to use SRTP adds a layer of protection for this data exchange, preventing unauthorized modification or interception. But, adding encryption to a real-time system comes with its own trade-offs. SRTP can impose a performance penalty, which is always something to consider in a system that needs to react quickly to changes in its operating environment. Plus, fitting this protocol into older equipment like the 90-30 series might cause headaches. Compatibility issues between the legacy systems and modern protocols can complicate integrating SRTP.
One of the interesting parts of SRTP is that it can adjust to network conditions on its own. It can tweak data transmission speeds based on how congested the network is, making it more adaptable to different situations. But, using this feature well requires a network that is designed with flexibility in mind. All of this also shines a light on how industrial networks are steadily evolving. As networks get more interconnected, protocols that provide both real-time capabilities and protection will be even more important.
When implementing SRTP, engineers have to adapt the system's overall structure, which can add complexity and risks if not done correctly. Potentially, this complexity could lead to new types of security flaws. Using SRTP for memory access provides real-time data without security vulnerabilities and could advance the use of predictive maintenance, which further improves factory operations.
On the other hand, using SRTP increases data transmission demands because of the extra header data sent along with each data packet. In a high-data environment, engineers have to be wary of network bottlenecks. The success of SRTP hinges on its key management scheme. If keys aren't handled securely, it could severely impact security, particularly in a blended environment like the Series 90-30, where older and newer approaches mix.
With the proper implementation, SRTP offers a pathway for updating the networking aspects of systems like the GE Fanuc Series 90-30 without throwing everything out and starting over. It's like a bridge between legacy hardware and modern cybersecurity requirements.
GE Fanuc Series 90-30 PLC A 2024 Analysis of Its Enduring Impact on Industrial Automation - Modular Design for Customized Control Solutions
The GE Fanuc Series 90-30 PLC's modular design is central to its ability to provide customized control solutions across a wide range of industrial applications. This modularity, made possible by over 100 different module types, allows engineers to create precisely configured systems for specific tasks. This adaptability has made the 90-30 suitable for diverse settings, spanning from automotive manufacturing to food and beverage production. While this flexibility is a strength, it can also lead to complications when companies want to upgrade to modern automation technologies. The ability to easily swap out components simplifies some maintenance procedures but can create headaches when transitioning to entirely new systems. As industries face growing pressures to incorporate advanced features and bolster cybersecurity, the modularity of the 90-30 illustrates a key point about legacy systems—the flexibility they provide can sometimes create barriers to moving forward with technological upgrades. In essence, the Series 90-30 demonstrates how modular design can underpin a successful automation legacy, but it also highlights the challenges inherent in managing the transition from established systems to newer technologies in a field that's constantly in flux.
The GE Fanuc Series 90-30 PLC's modular design wasn't just about customization; it allowed engineers to mix and match input/output (I/O) modules, creating a level of flexibility that was rare in industrial automation at the time. This made it very adaptable to specific tasks within a plant or facility.
It's notable that the 90-30 supported multiple programming languages that adhered to the IEC 61131-3 standard. This feature helped engineers who were already familiar with a certain programming style to easily transition to this PLC and use their existing knowledge across different automation platforms.
Despite its flexibility, the 90-30 presented challenges during system upgrades. Changes frequently involved extensive testing to confirm that new and old modules worked together correctly. It's an example of how a flexible design can have unforeseen complications when making changes.
The 90-30's longevity is undeniable, with estimates suggesting that about 75% of the PLCs installed are still in use as of 2024. This speaks to not only the hardware's reliability but also to the hesitance some industries have in switching away from systems they understand well.
The 90-30 seamlessly integrated with older equipment, which could be a problem during modernization. This inherent compatibility creates an interesting situation where, while serving its purpose well, it can also make it harder to replace it with new tech.
One of the system's strengths was its built-in diagnostic capabilities. It offered valuable insights into the system's performance and helped operators see problems before they escalated. This was a precursor to today's predictive maintenance techniques, where continuous data is used to avoid unscheduled downtime.
It's important to note that while the 90-30 was reliable for its time, cybersecurity is crucial now. Integration of protocols like SRTP highlights that even older systems need appropriate security measures. The system's vulnerabilities can pose real threats in today's networked world.
The modularity also meant that the 90-30 could be upgraded incrementally. Organizations could increase the system's capabilities without completely replacing everything, making upgrades less disruptive and potentially more affordable.
Although the 90-30 wasn't built in the Industrial Internet of Things (IIoT) era, its features, such as Ethernet support, helped lay the groundwork for incorporating IoT into industrial settings. It was a step towards the networked factory.
The ongoing availability of spare parts and maintenance for the 90-30 highlights a peculiar aspect of industrial automation: the significant continued value of legacy systems. Despite advancements in technology, there's still a niche for dependable older systems, suggesting that the speed of tech evolution isn't the same in every industry.
GE Fanuc Series 90-30 PLC A 2024 Analysis of Its Enduring Impact on Industrial Automation - Ethernet NIU Integration and Connectivity Advances
The GE Fanuc Series 90-30 PLC's capabilities were significantly enhanced with the introduction of the Ethernet Network Interface Unit (NIU). This addition allowed the 90-30 to seamlessly integrate into Ethernet networks, a crucial step toward modernizing industrial control systems. The NIU enables direct communication with master controllers, creating a single point of connection for improved communication flow. It also facilitates remote control of the 90-30 PLC, making configuration and automation easier to manage. The increased communication speed and efficiency that the NIU brings can save operators time and streamline industrial operations. However, the integration of Ethernet into a PLC that is now considered obsolete also presents some challenges. As automation increasingly relies on complex and fast networks, older PLCs like the 90-30 might struggle to fully meet modern requirements, particularly in regards to cybersecurity. The decision of whether to upgrade or continue using older systems becomes a critical one for companies in the face of evolving industrial automation standards and heightened security concerns. The NIU does represent an improvement but it may not be enough to propel the 90-30 into the future of industrial automation.
GE Fanuc's decision to incorporate Ethernet into the Series 90-30 PLC was a notable step away from relying on proprietary communication methods. This shift to open standards allowed for quicker data transfers and streamlined integration into the wider industrial network environment, fostering simpler connectivity between the PLC and other devices and systems.
The 90-30's design supported various communication protocols like Modbus and TCP/IP, enhancing its versatility across a range of industrial applications. This open architecture made it simpler to incorporate the 90-30 into facilities that used a mix of automation technologies, a common approach in many factories.
While Ethernet enhanced the 90-30's capabilities, network analyses on these systems revealed unexpected bandwidth demands due to legacy protocols. The growing prominence of Ethernet highlighted the importance of bandwidth management in older systems, especially in larger factories and plants, raising awareness of the need for modernized network infrastructure to prevent performance issues.
Researchers looking into the Ethernet Network Interface Unit (NIU) have uncovered security vulnerabilities in the initial security implementations of the 90-30. These findings emphasize the need for improved security measures, especially in light of the increasing interconnectedness of industrial networks. This is an area that's likely to receive a lot more attention in the years to come.
One of the advantages of integrating Ethernet was remote diagnostics. Engineers could now troubleshoot problems through a network connection, eliminating the need to physically be present at the PLC. This has become a cornerstone of modern maintenance practices, allowing for faster issue resolution and reduced production downtime.
Ethernet has helped unlock advanced monitoring practices such as using real-time data to implement predictive maintenance algorithms. These algorithms can analyze operational data to foresee potential issues, going beyond the standard logging practices found in older PLC systems.
It's common today to find dual-stack network configurations in industrial settings. This involves running both legacy systems like the 90-30 alongside modern automation technologies. While this approach offers a practical transition path, managing this complex setup can be tricky, and integrating the two systems can be a source of complications.
The integration of Ethernet has created a thriving aftermarket support community. It's quite remarkable how easily engineers and operators can still find parts and installation services for 90-30 PLCs. This underscores the continued relevance and robustness of the system, even when newer, supposedly more advanced, options are available.
The 90-30's modular design presents both opportunities and challenges when considering network integration. It's a design characteristic that required substantial architectural adjustments when integrating Ethernet, showcasing how diverse the needs of legacy systems can be.
In the end, Ethernet connectivity significantly helped companies that adopted the 90-30 reduce the time it took to bring new products to market. It took advantage of established networks to swiftly deploy automation solutions. This is a good illustration of how strategic integration can provide a competitive edge, even when utilizing older technologies.
More Posts from aistructuralreview.com: