Installing Perforated Pipe The Structural View
Installing Perforated Pipe The Structural View - Trench Excavation Effects on Surrounding Soil Stability
Creating an opening in the ground for utilities or drainage systems necessarily disrupts the existing equilibrium of the earth around it. For processes like installing perforated pipe, this excavation directly influences how the adjacent soil behaves structurally. The act of digging alters the distribution of pressures and the capacity of the ground to support loads, increasing the potential for instability, including differential settlement or sidewall failure. The specific concerns vary greatly depending on the soil type, the trench's dimensions, and what exists nearby. Adding water to the mix, either from groundwater or surface infiltration, typically exacerbates these issues by reducing soil strength. The successful integration of the perforated pipe structurally depends significantly on the quality of the interface and interaction between the pipe and the prepared soil zones around it, highlighting why thorough geotechnical assessment and appropriate ground support methods are often indispensable.
Here are five fascinating points worth considering regarding how trench excavation influences the stability of the surrounding soil mass, from a structural engineering perspective in mid-2025:
1. Simply digging a hole isn't merely removing volume; it fundamentally eliminates the *pre-existing geostatic pressure* that held the soil particles in their relatively dense, stable configuration. This sudden removal of confinement allows the adjacent soil to rebound or creep into the void laterally and vertically, often leading to a localized reduction in soil density and, crucially, a significant loss of peak shear strength right at the trench boundaries.
2. Creating a vertical or near-vertical trench wall introduces an unsupported *free boundary* to the soil mass. This boundary condition causes a drastic redistribution of stresses, typically inducing tensile stresses (which soils resist poorly, especially granular ones) near the ground surface adjacent to the trench face, and concentrating shear stresses deeper down. This altered stress regime creates distinct zones of potential failure mechanisms, even for relatively shallow digs.
3. Even when excavated well above the main groundwater table, a trench can compromise stability by disrupting the *capillary rise* zone. This layer of soil, held under negative pore water pressure (suction), contributes significantly to effective stress and apparent cohesion. Breaking this capillary connection or allowing air ingress can lead to a reduction in suction, a corresponding decrease in effective stress, and thus a loss of this 'bonus' strength, potentially triggering instability where it might not have been expected based on free water levels alone.
4. For cohesive soils like clays, the rapid unloading during excavation triggers an *immediate elastic rebound* that can be quite visible as 'heave' at the trench bottom or walls. However, the longer-term behaviour is often more problematic; the altered stress state drives pore water migration, potentially leading to *consolidation (settlement)* or, conversely, *swelling* and progressive strength degradation over time if moisture content changes significantly, making prediction challenging.
5. Perhaps most complex, the very act of excavation dramatically *rotates the principal stress directions* within the adjacent soil. In the undisturbed state, stresses are primarily vertical and horizontal. Near the trench face, these rotate, aligning potential failure planes (surfaces where shear stress is highest) in directions that were previously less critically stressed, effectively 'unlocking' new potential collapse mechanisms defined by the soil's shear strength parameters relative to these new stress orientations.
Installing Perforated Pipe The Structural View - Selecting Aggregate and Geotextile for Long Term Support
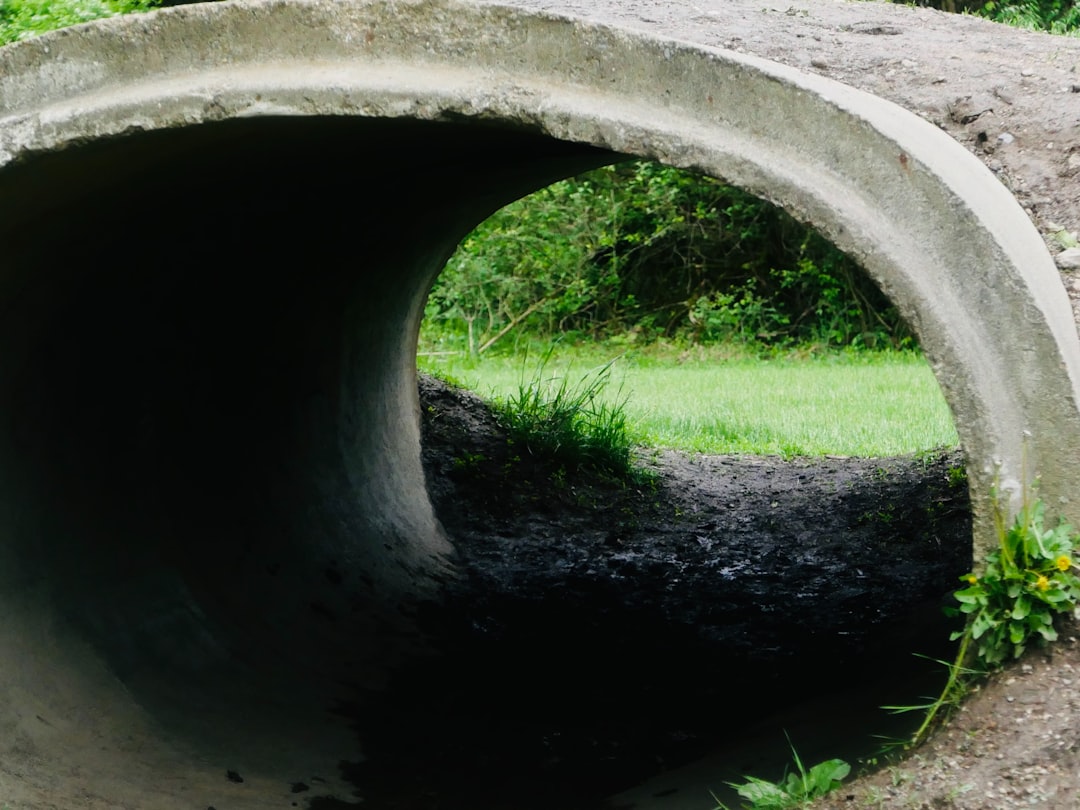
Ensuring the structural viability and continued function of perforated pipe drainage systems hinges significantly on the choice and proper placement of the surrounding aggregate and geotextile layers. The aggregate serves as the immediate structural backfill around the pipe, transferring loads and providing a stable bedding. Its ability to perform this role long-term relies heavily on achieving adequate compaction during installation. Simply filling the trench isn't sufficient; the aggregate needs to be consolidated, often through methods like repeated passes of equipment, to reach a density that resists future settlement or movement that could displace or damage the pipe.
Concurrent with aggregate, the geotextile functions primarily to maintain the purity and functionality of this aggregate envelope and the pipe itself. Positioned between the native or imported trench backfill and the selected drainage aggregate, its purpose is to filter out finer soil particles that would otherwise migrate into the aggregate pore spaces, leading to clogging and a loss of drainage capacity and structural support over time. The effectiveness of this filtration and separation is not solely about the presence of a fabric; it fundamentally depends on selecting a geotextile with appropriate material properties, including adequate permittivity and pore size distribution matched to the site soils, and critically, sufficient durability and creep resistance to survive the stresses of installation and the passage of years within the ground without degrading or allowing punch-through failures.
Installation is where the theoretical benefits of chosen materials are either realized or undermined. A durable, correctly specified geotextile offers no long-term protection if it is damaged during placement, improperly overlapped allowing soil bypass, or not correctly aligned to manage water flow paths. Similarly, aggregate provides little structural value if left loosely dumped in the trench. Therefore, the structural consideration extends beyond just the pipe itself to encompass this carefully constructed filter and support zone. Overlooking the nuances of material selection based on expected long-term performance under site-specific conditions, or neglecting strict installation protocols for compaction and fabric placement, creates inherent vulnerabilities in the system from day one, potentially leading to premature failure of the drainage function and, consequently, contributing to surrounding soil instability over time.
Here are five fascinating points worth considering regarding selecting aggregate and geotextile for long-term support in perforated pipe systems, from a structural engineering perspective in mid-2025:
1. Perhaps counterintuitively, securing sustained filtration often depends less on the geotextile's simple 'hole size' and more on the engineered *relationship* between the aggregate's gradation (often characterized by its D85 particle size) and the fabric's Apparent Opening Size (AOS). Get this D85/AOS ratio outside the accepted range, and you risk encouraging fine particles within the aggregate or from minimal external infiltration to prematurely form a low-permeability layer right against the filter fabric, rather than allowing proper self-filtration at the aggregate face.
2. Regarding the aggregate itself, the choice between rounded particles (like common drainage 'pea gravel') and angular, crushed stone presents a structural trade-off. While rounded stone might offer marginally higher initial void ratios for flow, the angular material's inherent particle *interlocking* capacity significantly enhances the bulk stiffness and shear strength of the backfill zone around the pipe. This increased rigidity is paramount for distributing overburden loads effectively and mitigating potential deformation or even structural collapse of the pipe itself over the decades, especially under traffic or significant surcharge.
3. Moving past its more commonly perceived role as solely a filter, the geotextile, when properly wrapped around the aggregate and pipe, contributes vital *tensile reinforcement* to the backfill zone. This creates a composite structure – the aggregate providing primary compressive and shear capacity, the geotextile providing essential tension – which significantly enhances the overall stiffness and load-spreading capability of the trench fill. This composite action is a fundamental requirement for resisting applied surface loads, particularly dynamic or cyclic ones, ensuring long-term structural integrity around the buried conduit.
4. While much attention is correctly given to preventing fine particles from the surrounding *native soil* from migrating into the drainage stone, a significant, and often overlooked, mechanism for long-term drainage inefficiency is the *self-clogging* caused by the migration and settlement of smaller particles *inherent within the chosen aggregate itself* over time. Selecting a 'clean' stone with a carefully controlled gradation, minimizing the percentage of deleterious fines (< 75µm) from the quarrying process, is arguably the single best defence against this internal blinding mechanism operating silently over decades of service.
5. Finally, the environment within the trench, particularly the chemistry and biological load of the water moving through the system, represents a distinct long-term threat to geotextile function, independent of soil particle filtration. Dissolved minerals can precipitate within the fabric structure as water chemistry changes or flows fluctuate, and microbial activity, including the formation of problematic iron ochre slimes, can progressively reduce pore space and permeability over time. These insidious processes can compromise the drainage system's effectiveness decades after installation, even if the geotextile was initially correctly specified for soil retention.
Installing Perforated Pipe The Structural View - Pipe Placement and Perforation Configuration for Drainage Performance
Getting the pipe into the ground isn't just about digging a trench; the specifics of where it sits and how its perforations are arranged dictate much of the system's ultimate success or failure. The precise pattern, size, and often overlooked orientation of the holes—whether deliberately directed upwards or downwards, for example—fundamentally governs how easily and effectively water can actually enter the pipe from the surrounding aggregate zone. This directly impacts the hydraulic efficiency. Likewise, the pipe's installed depth and consistent gradient are critical; a shallow pipe might miss the water table entirely, while an inconsistent slope can create unintended areas of stagnant water collection within the line itself, hindering flow and potentially leading to silting. Overlooking these seemingly minor details during installation represents a significant vulnerability, potentially compromising the drainage capacity precisely when needed most and, in turn, failing to protect the overall structural stability that the drainage system is intended to preserve over its design life.
The precise placement of the pipe within the trench profile and the deliberate configuration of its perforations are far from trivial details; they are fundamental engineering decisions dictating both the hydraulic function and the long-term structural viability of the drainage system. Overlooking these nuances can lead to systems that fail prematurely, either hydraulically through inefficient water capture and internal clogging, or structurally under the weight of overburden and applied loads.
Here are five fascinating points worth considering regarding pipe placement and perforation configuration for drainage performance, from a structural and hydraulic engineering perspective in mid-2025:
1. The structural implications of burial depth are often underestimated. Merely placing a pipe deeper for convenience or clearance overlooks the fundamental increase in static soil pressure it must withstand. Without rigorous consideration of the pipe's material strength, stiffness, and the load transfer through the surrounding fill (something standards like ASTM D2321 attempt to address), significant overburden can induce stresses leading to localized buckling or creeping deformation over the service life, rather than a simple collapse.
2. The seemingly counter-intuitive practice of perforating drainage pipes only along a specific arc of their circumference, typically limited to the lower portion (perhaps 120 to 180 degrees as sometimes specified, like Class 1 perforations found in standards referencing something like AASHTO M278), is a deliberate hydraulic strategy. This configuration forces a local water table to establish within the trench fill before inflow begins, enhancing capture from the lower, saturated zone and, perhaps more critically from a longevity perspective, acting as a rudimentary filter by preventing water (and suspended fines) from directly entering the pipe from unsaturated or less-controlled zones higher up.
3. Achieving and maintaining the minimum specified longitudinal gradient isn't just about ensuring flow; it's fundamentally about harnessing gravity to generate sufficient tractive shear forces along the internal wetted perimeter. These forces are the primary mechanism by which smaller particles that inevitably bypass filtration efforts are transported downstream, rather than silting up and progressively reducing the pipe's hydraulic capacity from the invert upwards. Insufficient grade means ineffective self-scouring.
4. The geometry of the perforations – their diameter, shape, and pitch – represents a delicate compromise between competing hydraulic and structural requirements. The aperture must be sufficient to permit the necessary inflow velocity from the surrounding filtered zone, essentially controlling the 'entrance head loss' into the conduit. Yet, these openings must simultaneously be constrained to reliably exclude particles from the carefully selected aggregate envelope (thinking of typical sizes like 8mm holes common in 150mm pipe as sometimes seen) that, if admitted, would contribute to internal pipe blockage. This requires careful coordination between aggregate gradation limits and perforation sizing standards.
5. The integrity of the installed pipe relies utterly on achieving truly uniform and continuous support from the underlying bedding layer along its entire length. Any discontinuity – an unexpected hard spot, a loose pocket, or differential compaction – creates stress risers. These imperfections transform what is ideally an evenly distributed bearing load into concentrated forces, introducing unpredictable bending moments and shear stresses in the pipe wall that can easily exceed localized material capacity, leading to structural failure mechanisms like cracking or joint separation that are not predicted by analyses assuming perfect support conditions.
Installing Perforated Pipe The Structural View - Backfill Method and Surface Load Capacity
Proper backfill material and its installation technique are fundamental to a perforated pipe drainage system's ability to withstand the loads applied from the surface. The soil envelope surrounding the pipe is the primary mechanism for transferring these loads from the ground surface down into the underlying foundation and past the pipe itself. Failure to achieve adequate backfill density or to select suitable materials means the load may not be distributed effectively, leading to concentrated stresses on the pipe or surrounding soil zones. This can result in unwanted settlement, deformation, or even structural compromise of the pipe or the trench itself over its operational life, underscoring the critical nature of this stage for managing surface-induced stresses.
Here are five fascinating points worth considering regarding backfill method and surface load capacity in perforated pipe systems, from a structural engineering perspective in mid-2025:
1. The manner in which backfill supports a buried pipe under load fundamentally differs depending on the pipe's inherent stiffness. For flexible pipes, the side fill's active and passive resistance is paramount; the pipe tends to deform slightly under vertical load, pushing outwards laterally. It's the compaction and strength of the adjacent backfill that prevents excessive deflection and mobilizes the pipe's ring compression capacity. Conversely, rigid pipes primarily rely on the bedding and haunch zones of the backfill to provide uniform support and distribute the vertical load to the trench bottom, with the backfill above primarily acting as overburden, although arching effects can still influence the net load.
2. Achieving uniform backfill density through controlled layer placement and compaction is not merely a quality control step; it is the direct mechanism by which load transfer paths and soil arching potential are established. Placing backfill in relatively thin lifts (typically 150mm to 300mm) and compacting each layer ensures that the material's shear strength and stiffness are mobilized consistently around the pipe. Failure to compact adequately, particularly in the haunch and side fill zones, leaves voids or loose areas that cannot provide the necessary passive resistance for flexible pipes or uniform bearing for rigid pipes, creating 'soft spots' where localized stresses concentrate under surface loads.
3. The concept of soil arching above a buried pipe, where a portion of the vertical load is transferred outwards onto the stiffer backfill columns at the trench sides rather than bearing directly down on the pipe, is a significant factor in load reduction. However, the effectiveness of this arching is entirely dependent on the quality and compaction of the backfill in the side zones relative to the material directly over the pipe. If the side fill is inadequately compacted, it cannot provide the necessary restraint or stiffness contrast, and the full 'prism load' (the weight of the backfill directly above the pipe) may indeed bear down, significantly increasing the stress on the conduit.
4. While flowable fill (like controlled low strength material or CLSM) might seem like an easy backfill solution due to its self-compacting nature, its long-term structural interaction with a flexible perforated pipe under surface loads warrants careful consideration. Unlike granular backfill that gains significant stiffness from inter-particle friction under load, flowable fill relies on its hardened matrix strength. This material might provide excellent uniform support initially, but its performance regarding mobilizing lateral passive resistance or facilitating load-reducing soil arching mechanisms in the same way as well-compacted granular fill might differ, potentially altering the expected long-term load transfer behavior.
5. The ultimate capacity of the backfilled trench and buried pipe system to support surface loads is inherently limited by the strength and stiffness of the weakest link, which is often the backfill material itself, especially if poorly placed or compacted. Even if the pipe material has adequate intrinsic strength, it relies entirely on the surrounding backfill to confine it, distribute applied loads, and prevent excessive deformation that could lead to connection failures or localized yielding. The variability of actual site soils used as backfill, combined with challenges in ensuring consistent, high-quality compaction across an entire trench length, introduces significant uncertainty into predicted load capacities.
Moving from simply installing the pipe and its immediate support, a fundamental aspect for structural integrity under live loads is the nature and execution of the bulk backfill above and around the crucial pipe zone. How this material is handled and densified directly dictates the system's ability to withstand pressures originating from the surface.
It's become evident through countless project observations that the capacity of trench backfill to support overlying traffic or other surface loads doesn't primarily stem from the passive weight of the soil mass or the depth of burial alone. Rather, it appears critically tied to the deliberate application of specific *compaction energy* to the backfill placed in carefully controlled lifts. This energy input facilitates the necessary particle interlock and bulk stiffness required to perform its structural function effectively.
A well-executed, adequately compacted trench backfill acts as a relatively stiff block within the softer native soil matrix. This stiffness difference is essential for promoting *stress arching*, a beneficial phenomenon where applied surface loads are preferentially transferred laterally towards the inherently stronger, undisturbed trench sidewalls rather than being channelled directly down onto the buried pipe. This mechanism is arguably the most significant factor in protecting the pipe structure from crushing under traffic.
Furthermore, the engineering properties and achieved density of the material placed in the bulk fill zone *above* the immediate aggregate envelope often prove more critical for long-term surface load performance than the structural rigidity of the pipe itself. This overlying backfill acts as a structural cushion and load distributor; its capacity to spread concentrated surface pressures over a wider area fundamentally dictates the stress magnitude that ultimately reaches the pipe zone.
Curiously, a backfilled trench that performs adequately under static conditions can exhibit distinctly problematic behaviour under dynamic or cyclic surface loads, such as repeated vehicle passes. The cumulative effect of fluctuating stresses can lead to a progressive breakdown of the backfill structure, causing pore pressure buildup or material fatigue, manifesting at the surface years later as noticeable rutting or differential settlement along the trench line.
Finally, the physical interface between the compacted backfill prism within the trench and the surrounding native soil represents a perennial structural discontinuity. Despite best efforts, the distinct mechanical properties at this boundary frequently lead to stress concentrations and differential strain paths under load, often expressing themselves visibly at the ground surface through the development of linear cracks or localized depressions directly aligned with the underlying trench edges.
Installing Perforated Pipe The Structural View - System Longevity and Adjacent Structure Protection
Achieving true system longevity and safeguarding adjacent construction are fundamentally tied objectives when installing perforated pipe drainage. The system isn't merely a conduit; it's an integrated element interacting dynamically with its underground environment. Its long-term functional duration and benign presence next to foundations or utilities depend critically on navigating the complexities inherent in disturbing ground and placing engineered components within it. Failures to anticipate these interactions – whether through material choices, installation procedures, or ignoring site-specific conditions – inevitably compromise the system's operational life, leading to issues like premature clogging or structural degradation. This functional failure, in turn, often translates directly into detrimental impacts on nearby built works through altered groundwater regimes or load transfer deficiencies. By mid-2025, the necessity for treating these installations as integrated geotechnical-structural undertakings, focused squarely on predictable, long-term performance, has become paramount, rather than simply focusing on getting pipe into the ground.
Addressing the long-term viability of these subsurface systems and safeguarding the stability of elements around them involves confronting processes that unfold gradually, sometimes insidiously, over many years or decades. The initial installation sets the stage, but sustained performance is challenged by dynamics far removed from day-one conditions.
Consider five specific points regarding the longevity of perforated pipe systems and their influence on surrounding structures:
The system's primary hydraulic function—capturing and removing water—can inadvertently trigger long-term settlement in neighbouring areas. By effectively lowering the local groundwater table, the drainage increases the *effective stress* borne by the soil skeleton beneath adjacent structures or pavements, potentially initiating a process of secondary consolidation in susceptible compressible soils that may continue for years, well after construction is complete, challenging the original foundation assumptions.
Biological interference poses a persistent, often underestimated threat. Plant root systems, particularly from mature vegetation nearby, are attracted to the more favourable moisture and aeration conditions within the backfilled trench. Their relentless search for water leads to physical root growth that can invade and disrupt the drainage aggregate, deform the pipe, damage the filter fabric, and exert significant pressure on the trench sidewalls and adjacent building footings or utilities over time.
Aggressive groundwater chemistry, extending beyond just suspended solids, introduces a different mode of long-term system degradation. Dissolved minerals, notably compounds containing iron and manganese, can precipitate out of the water and accumulate within the pore spaces of the drainage stone and geotextile fabric as flow occurs. This non-particulate clogging mechanism progressively reduces the hydraulic conductivity of the drainage envelope over decades, irrespective of how well the system initially filtered soil particles.
The distinct mechanical and thermal properties of the engineered backfill used in the trench, compared to the undisturbed native soil surrounding it, create a structural discontinuity with implications for overlying or adjacent structures. Differential thermal expansion and contraction due to cyclic temperature changes can induce cumulative stresses and strains at this interface, potentially leading to premature cracking in adjacent pavements or differential movement causing distress in nearby utilities aligned parallel to the trench.
Even without significant surface loads, the slow, viscous deformation of the soil and granular backfill material under sustained overburden pressure—known as creep—subtly alters the support conditions for the buried pipe over its service life. This gradual redistribution of stresses can change the bearing support along the pipe's length and circumference, potentially introducing unanticipated bending moments or local stress concentrations that were not factored into short-term elastic structural analyses, increasing the long-term risk of structural fatigue or deformation.
More Posts from aistructuralreview.com: