How Diffusion Bonding at 70-90% Melting Point Optimizes Metal Joint Strength in Aerospace Applications
How Diffusion Bonding at 70-90% Melting Point Optimizes Metal Joint Strength in Aerospace Applications - Process Parameters Behind Metal Joint Strength at 70-90% Melting Point
Achieving robust metal joints through diffusion bonding within the 70-90% melting point range hinges on precise control over several processing variables. Temperature, the duration of the bonding process (dwell time), and the pressure applied at the interface all play a crucial role in dictating the final joint strength. While higher temperatures can promote stronger bonding through enhanced atomic diffusion, they can also introduce a risk of joint brittleness. This highlights the need for a delicate balancing act when optimizing these parameters.
Furthermore, the deformation that takes place during the bonding process is frequently underestimated in its importance to joint toughness. This mechanical aspect is critical in influencing the final joint strength and shouldn't be overlooked. Techniques such as response surface methodology can aid in optimizing factors like temperature, pressure, and surface roughness, all of which can dramatically impact joint quality. These optimization methods are especially valuable for aerospace applications, where failure is not an option and joint integrity is critical.
It's important to recognize that achieving proper metal-to-metal contact, along with the development of suitable compositional gradients, are also critical factors in the success of diffusion bonding. These aspects, together with the precise control of the previously mentioned process parameters, pave the way for strong, reliable joints crucial for demanding applications.
The temperature employed during diffusion bonding, ideally within the 70-90% melting point range, significantly impacts joint strength. This temperature window fosters optimal atomic movement without compromising the base metal's structural integrity. However, it's important to note that simply increasing the temperature is not always beneficial. It's been observed that temperatures exceeding 450°C, while leading to enhanced shear and bonding strength in some cases, warrant careful consideration as it could potentially lead to undesirable consequences.
Time, often referred to as "dwell time" or "holding time," plays a pivotal role in determining joint strength. Extended bonding durations can, in some instances, lead to excessive grain growth and compromise material properties. Conversely, insufficient dwell times might impede complete atomic diffusion, leading to weak interfaces.
Furthermore, the pressure exerted during the process is a key parameter influencing joint density. It's important to find the right balance because excessive pressure can cause defects, while insufficient pressure can hinder the diffusion process and result in poor bonding. This pressure-density-strength interplay is particularly crucial in diffusion bonding.
Interestingly, the type of alloy chosen influences the bonding process itself. Some alloy combinations exhibit superior bonding capabilities due to favorable interactions between atoms. The research on various alloys and their bonding behavior is quite extensive, but there's still a large gap in the understanding of the nuanced behaviors in the 70-90% melting point regime. For example, while many studies examine the impacts of temperature, pressure, and time, a large percentage of the research has relied on examining the "average joint performance" rather than exploring the mechanisms that drive variations across different specimens. This makes it hard to optimize bonding parameters when we haven't figured out the fundamental factors driving variability.
Surface preparation is another factor that cannot be overlooked. Impurities or variations in the surface finish can significantly impact diffusion rates and hence, the joint quality. Furthermore, the post-bonding cooling process influences the microstructure. Rapid cooling can trap certain beneficial phases, whereas gradual cooling might promote negative microstructural changes. It is important to design the appropriate cooling strategy to avoid these negative outcomes.
Lastly, the challenges associated with optimizing diffusion bonding parameters in aerospace applications are considerable. In these demanding environments, the joint must reliably withstand cyclical thermal stresses and various operating conditions. Determining optimal bonding parameters that ensure consistent performance in the face of these challenges is an ongoing pursuit that will hopefully lead to better insights into this fascinating process. In effect, there is a push-and-pull at play. One seeks to achieve optimal atomic diffusion and strong bonds while remaining mindful of the materials' propensity to degrade as temperatures approach the melting point.
How Diffusion Bonding at 70-90% Melting Point Optimizes Metal Joint Strength in Aerospace Applications - Atomic Movement Analysis During High Temperature Diffusion Bonding
Understanding the atomic movements during high-temperature diffusion bonding is key to achieving optimal joint strength in metals, especially in demanding aerospace applications. When bonding occurs at temperatures between 70-90% of the material's melting point, atoms become significantly more mobile, which can dramatically improve the integrity of the joint. However, a careful balance needs to be struck. While higher temperatures encourage greater atomic movement and lead to stronger bonds, it's also critical to consider the potential negative impacts that excessive temperatures can have, including increased brittleness and undesirable changes to the material's microstructure. Additionally, the interplay between atomic movement and other variables such as applied pressure are significant. Each factor contributes to the success and long-term durability of the bond under the harsh conditions often seen in aerospace. By gaining a deeper understanding of the underlying atomic mechanisms driving this bonding process, researchers and engineers can more effectively optimize these parameters and achieve greater joint strength while mitigating the risks associated with high-temperature diffusion bonding. This detailed understanding is necessary for tackling the specific and challenging requirements found in aerospace components.
The core of diffusion bonding lies in the movement of atoms, primarily driven by the movement of vacancies—empty spaces within the crystal lattice. As the temperature rises closer to the melting point, this atomic dance becomes more frenetic, allowing atoms to shuffle around and fill in gaps more efficiently. However, pushing the temperature beyond about 90% of the melting point can lead to overly rapid grain growth, potentially harming the desired mechanical properties of the joined parts.
Temperature is a double-edged sword here. While it's essential for boosting atomic mobility and enhancing the bonding process, it’s crucial to maintain a careful balance. The pressure applied during bonding also plays a crucial role, working in tandem with the temperature to optimize the process. The pressure ideally encourages atomic movement without triggering unwanted phase changes that can negatively affect joint strength.
The elevated temperatures in diffusion bonding also affect the movement of dislocations, which are defects in the crystal structure. These dislocations are a key contributor to material strength and ductility, and under controlled high-temperature conditions, they can actually rearrange themselves, reducing their overall density. This can produce a more uniform grain structure, which is highly desirable for aerospace alloys that require exceptional tensile strength.
However, the atomic dance of diffusion can be significantly affected by the precise alloy composition. Certain elements can either slow down or speed up the diffusion process. This is a critical consideration as it affects the overall efficiency of bonding and influences the final properties of the joint. It's also worth noting that significant differences in atomic size between constituent elements can hinder diffusion, leading to unequal rates of atom movement and potentially undesirable joint structures.
Even tiny amounts of impurities on the bonding surfaces can act as roadblocks to atom movement, hindering the diffusion process and ultimately compromising the bond quality. The cooling process after bonding is equally important, impacting both residual stress and phase transformations within the microstructure. Managing the cooling rate helps ensure the formation of a microstructure with the ideal combination of properties.
Furthermore, the interplay of interatomic forces—the forces that hold atoms together—within the alloy system can result in non-uniform strain distribution during the bonding process. This unevenness can lead to variations in local microstructures, potentially affecting the joint’s overall strength.
The bonded interface is not a static structure. As atoms continue to rearrange themselves at elevated temperatures, finer-grained substructures can form. This can lead to improved joint toughness if the process is carefully managed. All in all, diffusion bonding is a fascinating process that holds significant promise for high-strength, reliable metal joints, but its complexity requires careful control and a deep understanding of the intricate interactions that occur at the atomic level.
How Diffusion Bonding at 70-90% Melting Point Optimizes Metal Joint Strength in Aerospace Applications - Impact of Temperature Control on Aerospace Grade Bond Formation
In aerospace applications, the influence of temperature control on the formation of high-quality bonds through diffusion bonding is paramount for achieving optimal joint strength. Maintaining the right temperature range is crucial because it directly affects how readily atoms move, enabling strong bonds to form without compromising the inherent strength of the materials being joined. However, striking a balance is essential. While higher temperatures can promote more atom movement and potentially stronger bonds, exceeding certain thresholds can cause increased brittleness and potentially unwanted changes in the material's microstructure. Equally important is the cooling process that follows the bonding procedure, as this stage influences the residual stresses and the transformation of the material's phases, which can negatively impact the bond strength. The ability to understand these temperature dynamics is absolutely crucial for optimizing the diffusion bonding process, particularly in high-performance aerospace applications where joint reliability is essential.
The impact of temperature on aerospace-grade bond formation through diffusion bonding is multifaceted and requires careful consideration. While elevated temperatures are essential for promoting atomic movement and enhancing bond strength, they can also lead to unforeseen consequences. For instance, specific temperature thresholds can trigger phase transformations in certain alloys, potentially resulting in less desirable microstructures and compromised mechanical properties. The optimal temperature-time relationship is not linear, with each alloy possessing its unique sweet spot that maximizes diffusion without excessive grain growth.
Furthermore, the dissolution of secondary phases, which can be beneficial in certain alloys, becomes a concern at higher temperatures. These phases might dissolve, potentially degrading overall material performance. Interestingly, even though higher temperatures accelerate diffusion, they can amplify the influence of surface roughness on bond formation. Surface irregularities can become more prominent, potentially creating weak points in the otherwise strong bond.
The variation in atomic size among different alloying elements can also significantly impact diffusion rates. If smaller atoms move faster than larger ones, it can lead to uneven element distribution, potentially affecting joint integrity, especially in applications requiring uniform strength. The increased mobility of grain boundaries at elevated temperatures can lead to coarsening of the microstructure, which might negatively affect the joint's mechanical properties.
The cooling rate post-bonding is critical for managing residual stress. Rapid cooling can induce stress concentrations, potentially leading to crack initiation or propagation, a critical concern in aerospace components. The flow of vacancies, crucial for atomic rearrangement, becomes more erratic at higher temperatures, increasing the risk of defect formation unless the temperature is carefully controlled. This high-temperature environment can also impact ductility, with excessive grain refinement possibly leading to increased brittleness.
Different fracture mechanisms might dominate at varying temperatures. This necessitates targeted testing to ensure reliable joint integrity across various temperatures. The temperature sensitivity of these mechanisms is crucial to understand for achieving robust and durable joints in the harsh environments faced in aerospace applications. These challenges necessitate a more nuanced approach to optimizing diffusion bonding parameters to maximize the potential of this powerful joining technique while minimizing the risks associated with high temperatures.
How Diffusion Bonding at 70-90% Melting Point Optimizes Metal Joint Strength in Aerospace Applications - Microstructural Changes in Metal Joints at Near-Melting Temperatures
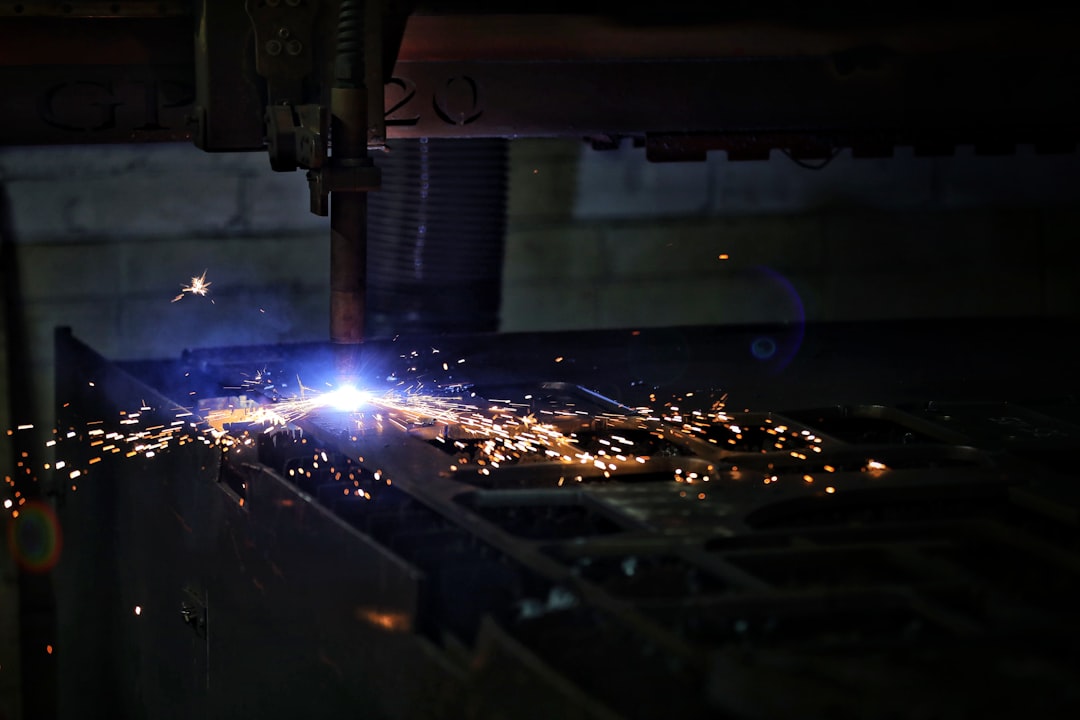
When metal joints are subjected to temperatures approaching their melting point (roughly 70-90%), notable microstructural changes take place, which are fundamental to achieving strong and reliable bonds through diffusion bonding. These changes can dramatically influence the overall strength and integrity of the joint, particularly in aerospace applications where component reliability is paramount.
One of the most significant alterations is the formation of intermetallic compounds (IMCs) at the interface between the materials being joined. The presence and characteristics of these IMCs can have a profound effect on the mechanical behavior of the joint, particularly in complex alloys such as tungsten-based composites. While IMCs can contribute to increased strength in some cases, they can also lead to brittleness, especially if their composition is unfavorable. The precise formation and distribution of these IMCs depend on a variety of factors, including the exact temperature, the time the materials are held at temperature (dwell time), and the applied pressure.
Another key area of interest is the evolution of the grain structure within the joint. At elevated temperatures, the atoms become significantly more mobile, leading to grain growth, which can potentially influence the joint's mechanical properties. If not carefully controlled, excessive grain growth can lead to a loss of ductility, a detrimental characteristic in aerospace applications where flexibility and fracture resistance are often critical.
The heat-affected zone (HAZ) surrounding the bonded interface is also impacted by near-melting temperatures. This area, affected by the thermal cycling of the bonding process, plays a critical role in how stress is distributed within the joint. In tensile testing, the HAZ can influence the location where fracture initiates, and therefore, its behavior is extremely important to understand. This reinforces the need for careful temperature control to minimize the risk of unexpected or premature failure.
Understanding and managing these microstructural shifts are critical steps in optimizing the strength and reliability of diffusion-bonded joints for demanding aerospace applications. The complex interplay of temperature, time, and pressure, combined with the specific characteristics of the alloys involved, makes the optimization process a constant challenge. Further research and analysis are likely to uncover additional insights into these complex interactions, and ultimately lead to the development of even stronger and more reliable joints.
During diffusion bonding near the melting point (70-90%), the metal's internal structure undergoes significant changes, influencing the strength and flexibility of the resulting joint. The movement of atoms becomes much more active due to an increase in the number of vacant spaces within the metal's crystalline structure. This enhanced atomic mobility is essential for strong bonding, but it's a double-edged sword. While it promotes better bonds, it can also lead to larger grains within the material, potentially reducing its strength. Finding the right balance between enhanced diffusion and the risk of excessive grain growth is a constant challenge.
The specific composition of the alloy used has a notable influence. Different alloys respond differently to high temperatures, potentially undergoing phase shifts that can change the material's properties. It's critical to understand these potential shifts to predict how the joint will behave in a specific application. Additionally, the interface formed between the joined pieces isn't simply a straight line; it's a dynamic zone where atoms actively rearrange themselves. This rearrangement can create a finer internal structure, which is desirable for increased toughness, but this refinement needs to be carefully managed.
The size of different atoms within the alloy mixture also affects how quickly they can move around. If there are considerable differences in atom sizes, some might move much faster than others, leading to uneven distribution of elements within the joint, potentially harming the joint's integrity. The condition of the bonding surfaces is another crucial factor. Roughness or contaminants on the metal surfaces can hinder the movement of atoms and degrade the bond quality, particularly at temperatures near the melting point where oxides and other impurities can interfere with diffusion.
The cooling process after bonding is equally important. How quickly or slowly the metal cools down can create internal stresses within the material. While both rapid and slow cooling have benefits and drawbacks, proper control of the cooling parameters is essential for achieving the desired final properties of the joint. The mechanisms by which a joint fails can change depending on the temperature used during bonding. This temperature sensitivity is something engineers need to consider to create robust joints that can withstand the rigors of aerospace applications.
Interestingly, even microscopic imperfections in the crystalline structure called dislocations can be influenced by elevated temperatures during bonding. Under controlled conditions, these defects can move and rearrange themselves, potentially leading to a more uniform grain structure within the joint. This reorganization is a potential pathway to improve joint toughness, but only if the temperature is managed carefully to prevent unwanted phase changes that could weaken the material. Navigating the complex interplay of temperature, alloy composition, and microstructural evolution is crucial for maximizing the potential benefits of diffusion bonding while mitigating the associated risks, especially in demanding applications like aerospace where component reliability is paramount.
How Diffusion Bonding at 70-90% Melting Point Optimizes Metal Joint Strength in Aerospace Applications - Material Selection Criteria for Optimized Diffusion Bond Strength
When aiming for optimized diffusion bond strength, especially within the critical aerospace sector, material selection plays a pivotal role. The choices made regarding alloy composition have a significant impact on the success of the bonding process and the eventual joint's performance, especially under the extreme conditions common in aerospace applications. The ability of an alloy to facilitate effective atomic diffusion while simultaneously avoiding excessive grain growth is crucial for ensuring joint strength. Factors such as temperature, pressure, and bonding time all influence this delicate balance, and the chosen materials must be able to withstand those conditions without compromising their properties.
It is also important to recognize the criticality of surface preparation in the selection process. Impurities, or inconsistencies in surface finish, can significantly hinder the ability of atoms to effectively diffuse across the interface, ultimately leading to weak and unreliable bonds. Understanding the relationship between the chosen materials, the bonding environment, and the desired mechanical properties is paramount for ensuring the integrity of the joint. The nuanced interactions between material characteristics and bonding parameters must be considered if a diffusion bond is to reliably perform in the complex, demanding, and unforgiving environment of an aerospace structure. In essence, optimized material selection is a core element of ensuring strong, dependable, and durable joints in high-stakes aerospace applications.
The success of diffusion bonding, particularly within the 70-90% melting point range, hinges on a thorough understanding of how different alloys behave during the process. Each alloy has its own unique characteristics when it comes to atomic diffusion—some promote rapid atom movement, while others hinder it. This variability significantly affects the final quality of the bond and emphasizes the importance of tailoring the bonding parameters to specific alloy systems.
The microscopic surface texture of the parts to be joined also plays a crucial role. A rougher surface can enhance mechanical interlocking at the interface, but it can also introduce stress concentration zones, which could negatively impact the bond's overall strength. It's a bit of a trade-off, with both benefits and potential drawbacks.
At the interface of the joint, intermetallic compounds (IMCs) often form. While these IMCs can contribute to increased joint strength, some can lead to brittleness, making the precise control of temperature during bonding even more important. It's a balancing act, optimizing the process to form beneficial IMCs while avoiding those that negatively impact the joint's performance.
The movement of vacancies—empty spaces in the crystal lattice—is another critical factor. While these vacancies facilitate atom movement, an overabundance of them can lead to increased defect formation, potentially compromising the bond's strength. It's a reminder that finding the sweet spot is a central challenge.
There's a specific temperature threshold to consider. While higher temperatures generally improve atomic diffusion and enhance bonding, going beyond around 90% of the material's melting point often leads to uncontrolled and rapid grain growth. This grain growth can seriously harm the desired ductile properties, which are critical for applications like aerospace where flexibility and resistance to fracture are paramount.
The rate at which the metal cools after bonding has a significant impact. Cooling too rapidly can induce harmful residual stresses, while excessively slow cooling can allow phase transformations that compromise performance. It's about carefully navigating the cooling process to optimize the final properties of the bond.
The grain size within the joint is a key variable affecting toughness. Finer grains generally contribute to enhanced toughness, while excessive grain growth can lead to a reduction in overall strength. Achieving the correct balance in grain size is a central aim of optimizing this bonding process.
Elevated temperatures during the bonding process can cause the movement and rearrangement of dislocations—defects in the crystal structure. This rearrangement, when carefully controlled, can contribute to a more uniform grain structure, potentially enhancing the mechanical properties of the joint.
Variations in the heat distribution during bonding can result in localized heating effects, which can lead to non-uniform bond characteristics. This non-uniformity can produce differing stress responses and create potential areas of weakness within the joint, underlining the importance of ensuring a consistent temperature profile.
Different temperatures can trigger distinct fracture mechanisms in the joined materials. It's crucial for engineers to understand how these fracture mechanisms shift at different bonding temperatures to design bonding processes that can withstand the specific environments encountered in aerospace applications. This knowledge is essential to maximizing the joint's long-term reliability.
These insights demonstrate the intricate and interconnected nature of the diffusion bonding process. It's clear that a deep understanding of the interaction of temperature, alloy composition, and the resulting microstructural changes is necessary to optimize the process for high-performance aerospace applications. There are many nuances, and researchers are continuing to work on the optimization of this complex process.
How Diffusion Bonding at 70-90% Melting Point Optimizes Metal Joint Strength in Aerospace Applications - Testing Methods for Evaluating Joint Integrity in Aerospace Applications
In the realm of aerospace, ensuring the reliability of joints created through diffusion bonding, particularly within the 70-90% melting point range, hinges on comprehensive testing. Various testing methods are crucial for evaluating the integrity of these joints, especially under the demanding conditions often encountered in aerospace operations. Traditional techniques like tensile and shear tests are essential for determining the strength and toughness achieved by the diffusion bonding process. They provide a direct measure of how the joint will withstand various stresses and strains. Fatigue testing is also vital for understanding how the joint will respond to repeated loading, which is a common scenario in many aerospace applications.
Furthermore, non-destructive testing methods are employed to detect any imperfections or flaws within the bonded area. Techniques such as ultrasonic and radiographic inspections allow engineers to assess joint quality without causing damage to the component. These methods are valuable in identifying potential weaknesses or discontinuities that might compromise the structural integrity of the joint.
The appropriate selection and application of testing methods are paramount for gaining a thorough understanding of the limits of diffusion bonded joints. The results of these tests are used to guide design decisions, predict component performance in specific environments, and develop more reliable and robust joints. Continued research into advanced testing techniques is crucial for optimizing joint integrity and performance in increasingly complex aerospace systems. It is through ongoing advancements in testing that we can continue to refine and improve the application of diffusion bonding in aerospace components.
Evaluating the integrity of joints in aerospace applications, especially those created through diffusion bonding, requires a rigorous set of testing methods. This is especially true given the extreme conditions these structures often endure. Real-time monitoring of temperature and pressure during the bonding process is crucial, allowing for adjustments to prevent defects. Techniques like thermography are beneficial in visualizing temperature variations and potentially guiding adjustments in real-time.
Non-destructive testing (NDT) methods like ultrasonic testing are commonly employed to assess the internal structure of the bonded joints without causing damage. These methods can detect flaws like voids and inclusions that could compromise a joint's integrity before they cause major problems.
Fatigue testing is a critical component in the evaluation process. Applying cyclic loads to the joint simulates the repeated stress experienced in real-world aerospace environments, helping us understand long-term performance and potential failure modes.
Analyzing failure modes is a fundamental part of understanding joint integrity. It's been observed that failure often arises from a complex interaction of factors including mechanical loading, environmental stressors, and microstructural characteristics of the bond. These observations emphasize that thorough assessment strategies are necessary for long-term reliability.
The cooling rate after bonding significantly impacts the quality of the joint. Rapid cooling can introduce residual stresses leading to cracking, while slow cooling might facilitate undesirable microstructural changes that reduce joint strength. There's always a need to find a balance between those two potential negatives.
Computational modeling is increasingly utilized to predict the behavior of joints under diverse operational conditions. Simulations using different material compositions and bonding parameters help us understand how the bond will likely perform in specific conditions. This is especially important for expensive materials and complex aerospace applications.
Many testing techniques are focused on the microstructural characteristics of the bond, including grain size and distribution. Techniques such as scanning electron microscopy (SEM) provide highly detailed analysis, helping us establish the correlations between microstructure and joint strength. This aspect is particularly important to ensure that the material selected for the diffusion bond aligns with the design requirements.
Recent advances have enabled the direct measurement of atomic diffusion during bonding using techniques like atom probe tomography. These advances are providing vital data that researchers can use to optimize bonding conditions for improved joint integrity in aerospace applications.
Detecting voids within the bond is vital since they can significantly weaken it. Newer X-ray computed tomography (CT) methods allow for the identification of microvoids that might be missed using conventional inspection methods. This development offers a powerful non-invasive way to assess potential weaknesses within bonded structures.
Intermetallic compounds (IMCs) that form at the interface are a bit of a double-edged sword. While IMCs can increase joint strength, if they form improperly or in excess, they can introduce brittleness. Thorough testing and analysis are necessary to understand the impact of IMCs on mechanical performance. The formation and behavior of IMCs are quite complex and is an area of continued research.
In conclusion, a wide range of testing methods is used to evaluate the integrity of diffusion bonded joints in aerospace applications. The importance of testing and understanding how temperature, pressure, and material selection impact bonding can't be overstated. We are continuously seeking new ways to optimize this critical process, leading to further improvements in the performance of aerospace structures and components.
More Posts from aistructuralreview.com: