Comparing Mixing and Diverting Valves Key Differences in Flow Control Applications
Comparing Mixing and Diverting Valves Key Differences in Flow Control Applications - Operating Principles of Mixing and Diverting Valves
Mixing and diverting valves operate on distinct principles, which are fundamental to their respective applications. Diverting valves, as the name suggests, direct the flow of a fluid to different outlets. This process necessitates maintaining pressure on both sides of the valve to effectively switch between these outlets. In contrast, mixing valves are designed to combine fluids from two different sources. These valves only require pressure on one side to function, allowing them to blend the two inlets in a controlled manner.
The internal mechanism of each valve type also differs. In a diverting valve, the valve element shifts to a specific position to block one outlet and direct the flow to the other. Mixing valves, however, employ a design that allows for both inlets to be connected to the outlet simultaneously. The valve element controls the degree to which each inlet is mixed into the outlet.
Interestingly, three-way valves offer a certain degree of flexibility. Depending on their configuration, they can perform either mixing or diverting tasks. Their design, particularly the arrangement of their ports, determines which function they primarily serve. It's this versatility that makes three-way valves attractive in various applications where the need may shift between mixing or diverting fluid flow.
Understanding how these valves function, particularly the distinctions in their operation and design, is a critical part of selecting the correct valve for a specific application. Choosing the appropriate valve is necessary not only for ensuring that the valve performs as desired but also for optimizing the overall performance and efficiency of a given system.
1. Diverting valves act as flow switches, rerouting a fluid stream between two or more destinations. This contrasts with mixing valves, which combine different fluid streams into a single, blended output. This ability to switch flow paths makes them ideal for applications like managing fluid flow to different parts of a hydraulic system.
2. The operation of a diverting valve hinges on maintaining pressure differentials across both sides of the valve. If one side experiences a loss of pressure, the switching capability is compromised. Conversely, mixing valves require pressure primarily on one side to facilitate blending of the two fluids.
3. The core difference in valve mechanics lies in the movement of the internal valve plug. In a mixing valve, the plug is positioned to allow both inputs to blend, creating a mixture. In a diverting valve, the plug shifts to one extreme position or the other to completely block flow from one inlet.
4. Three-way valves are versatile, serving as both mixing and diverting devices depending on their design and internal construction. The porting and actuator design can be customized to control how the valve manages flow paths.
5. With three-way mixing valves, the valve plug's intermediary positions can modulate the flow from all three ports, providing finer control of the flow blend. This allows for gradual adjustments of the output mixture compared to a simple on/off diverting action.
6. Diverting valves, typically with one inlet and two outlets, operate most efficiently when the pressure differences between the outlets are kept below a specific threshold, usually around 0.6 bar. Exceeding this limit can lead to unstable and erratic valve operation.
7. The application needs dictate the choice of a mixing or diverting valve. Mixing valves are commonly found in temperature control systems where precisely blending fluids is crucial. Diverting valves are used in situations where you want to route fluid to different locations or components.
8. In heating and cooling applications, three-way diverting valves can improve efficiency by bypassing a coil or heat exchanger once the target temperature is met. This can help to minimize energy use by redirecting flow away from unneeded components.
9. Electric actuators are often the preferred choice for diverting valves due to their ability to provide more precise and stable control compared to pneumatic ones. This is especially important in applications where fast and accurate flow switching is needed.
10. While both valve types help manage fluid flow, their core function differs. Mixing valves aim to create a blended mixture, while diverting valves primarily focus on redirecting the flow to various locations based on the operational requirements. Their distinct design and operational features cater to different control needs within fluid systems.
Comparing Mixing and Diverting Valves Key Differences in Flow Control Applications - Pressure Requirements for Optimal Valve Performance
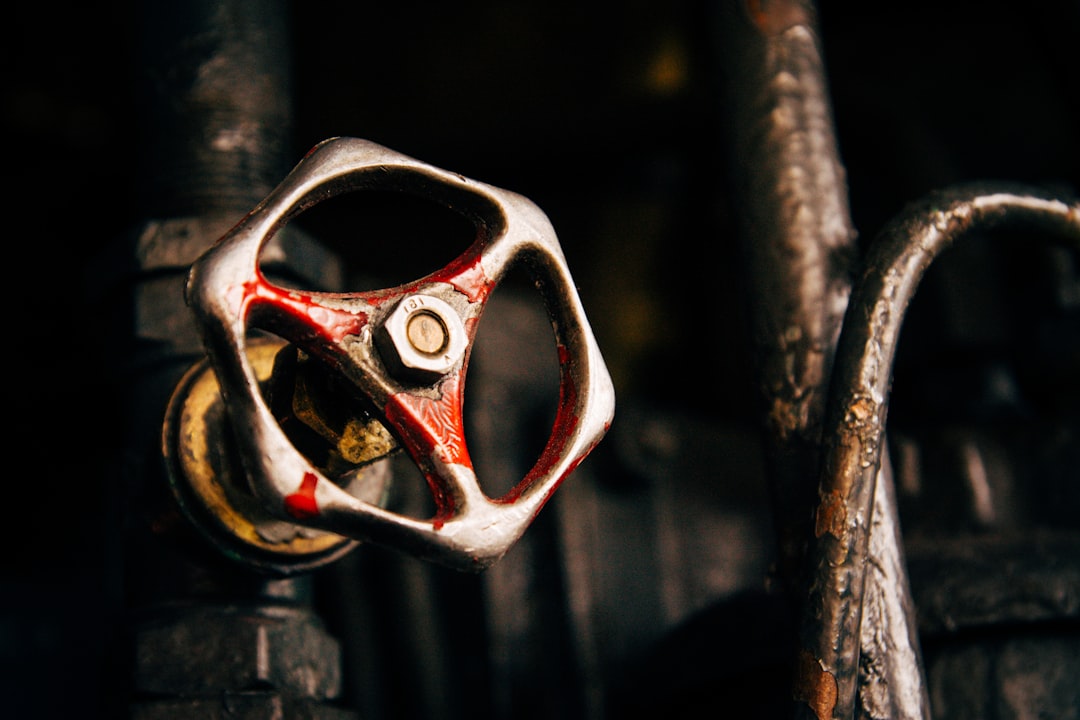
The performance of mixing and diverting valves is significantly impacted by pressure. Diverting valves, needing to switch flow between outlets, critically rely on maintaining pressure on both sides of the valve for reliable operation. If pressure drops on either side, their ability to switch flow paths effectively is compromised. In contrast, mixing valves, which blend fluids from multiple sources, primarily need pressure on one side for optimal function. The pressure drop across the valve, in both cases, affects how the valve is sized and influences its overall efficiency within a given system. The pressure requirements for both types of valves, therefore, play a key role in determining their suitability for different flow control scenarios. It's imperative to understand these pressure dynamics when selecting valves for specific applications, ensuring optimal performance within the particular system. While seemingly a minor detail, this can be a crucial aspect for the stability and long-term health of the overall system's fluid management.
Maintaining appropriate pressure is vital for achieving optimal performance from mixing and diverting valves. It's generally understood that a pressure differential of about 15-20% of the valve's maximum rated pressure can help extend its operational lifespan and minimize wear. However, if pressure differentials are not properly managed, it can lead to undesirable flow turbulence, particularly in diverting valves. This turbulence can manifest as valve chatter, a rapid oscillation that could damage internal parts.
Fluid temperature also plays a role in pressure requirements. Changes in temperature alter fluid viscosity, and generally, higher temperatures result in lower viscosity, making it possible for valves to operate more smoothly under lower pressure. It's interesting to note that diverting valves can show non-linear flow patterns in response to pressure variations. This makes implementing effective pressure control systems crucial for achieving a more linear and predictable valve performance, especially in intricate piping networks.
The position of the valve's actuator can also become a source of variability, impacting performance. Changes in actuator pressure can lead to suboptimal valve behavior, which underscores the need for meticulous actuator tuning based on the system's unique pressure profiles. When working with fluids of higher viscosity, pressure loss across the valve can become significant. This necessitates the use of larger valve openings or larger valves to ensure system efficiency isn't compromised.
A valve's maximum operating pressure isn't just limited by the materials it's constructed from; it's also influenced by potential pressure surges within the system. Understanding these pressure surge dynamics is essential to minimizing the chances of costly valve failures. Multi-port diverting valves have the potential to balance pressure across different outlets, but without proper design and control, they can introduce pressure imbalances, which adds complexity to system dynamics and performance.
Different valve materials naturally have different pressure requirements. For instance, plastic valves generally have lower pressure ratings than those made from metal, impacting their use in high-pressure applications. Choosing the right material is critical to ensuring the valve's longevity and proper operation in its intended working environment. Interestingly, the field of valve technology has seen advancements with the introduction of smart pressure sensors. These sensors can monitor pressure in real-time, enabling adaptive control strategies that can refine the responsiveness and overall reliability of mixing and diverting valve systems.
Comparing Mixing and Diverting Valves Key Differences in Flow Control Applications - Common Applications in Industrial Flow Control Systems
Industrial flow control systems rely heavily on valves to manage fluid movement, and mixing and diverting valves are frequently employed in a wide range of applications. Mixing valves prove crucial in scenarios that necessitate precise temperature control, like heating, ventilation, and air conditioning systems, or chemical processing where consistent fluid blends are paramount. Their ability to combine fluids from different sources helps achieve desired output temperatures or create consistent chemical compositions. In contrast, diverting valves are integral in directing fluid flow to various locations, commonly seen in hydraulic systems where multiple actuators or components need independent fluid delivery. This switching function is vital for tasks such as directing flow to different sections of a system or for safety features that redirect flow away from compromised parts.
Three-way valves demonstrate unique flexibility due to their adaptability for either mixing or diverting functions depending on the specific configuration of their ports and the flow direction required. This inherent versatility makes them desirable in processes where flow management needs might shift, eliminating the need for multiple valves in certain circumstances. However, choosing the right valve for the job can be challenging. Proper valve selection is crucial for ensuring effective system operation, minimizing the risk of costly errors, improving efficiency, and ultimately, maximizing the reliability of industrial processes. The choice of valve type significantly impacts a system's ability to consistently meet operating parameters, showcasing the critical role valve selection plays in optimizing industrial processes across a wide array of sectors. While seemingly a simple mechanical component, their functionality forms the foundation of complex fluid management and control systems in many industrial environments.
Industrial flow control often involves managing fluids under extreme conditions, with temperatures potentially reaching over 200 degrees Celsius or dropping below -50 degrees Celsius. This necessitates the use of materials capable of withstanding such harsh environments. Rigorous testing, like high-cycle endurance tests, are vital for ensuring the durability and reliability of valves used in high-demand industrial systems. Some valves can withstand over a million cycles in these tests without failing, a testament to their robustness in demanding applications.
Understanding the flow characteristics within diverting valves is crucial. Factors like the Reynolds number significantly influence the flow, determining whether it's laminar or turbulent. This knowledge has implications for energy efficiency and the overall wear and tear on valve components. Incorporating variable frequency drives (VFDs) alongside valve systems presents an opportunity to optimize energy usage. VFDs can dynamically adjust pump speeds based on system demand, reducing the reliance on solely valve throttling for flow control.
Mixing valves aren't confined to handling just water-based fluids. They are also effective at managing viscous fluids or slurries. However, specialized designs are often required to minimize clogging and ensure proper mixing of these more complex fluids. While seemingly a simple task, precise calibration of mixing valves can have significant consequences for downstream processes and product quality. In sensitive industries such as pharmaceuticals and food production, where consistent ingredient blending is paramount, accurate calibration is crucial.
The way valves are installed can also influence their performance. For example, diverting valves generally perform optimally when installed horizontally to minimize pressure drops caused by gravity. Integrating flow measurement devices into valve systems offers real-time data on fluid dynamics. This can provide engineers with previously unavailable insights into system performance, improving monitoring and control. The selection of actuators for both mixing and diverting valves is a significant consideration. Pneumatic actuators excel at quick response times, while electric actuators offer higher precision. Thus, choosing the appropriate actuator depends on the system's specific operational requirements.
In larger, complex systems, employing multi-port diverting valves can streamline the overall design. These valves can often replace multiple individual valves, simplifying maintenance procedures and reducing installation costs. It's interesting to note that this cost-saving aspect is often overlooked in initial valve selection processes, highlighting the importance of considering the overall system implications.
Comparing Mixing and Diverting Valves Key Differences in Flow Control Applications - Temperature Regulation vs Flow Routing Functions
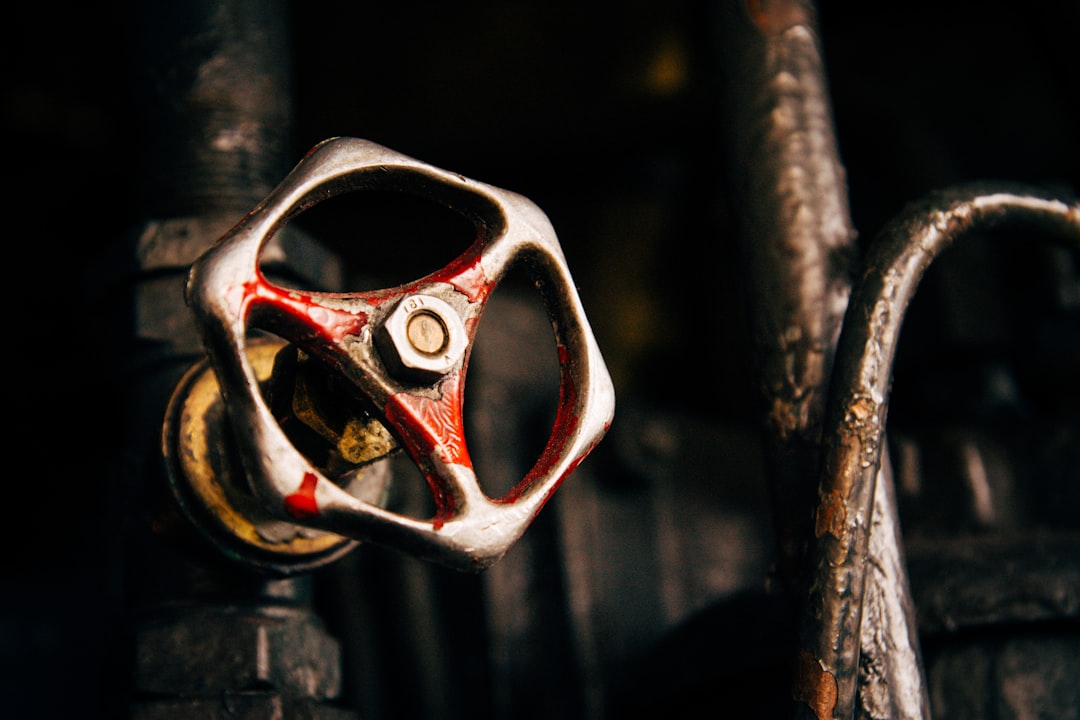
Within the domain of fluid control, understanding the difference between regulating temperature and routing flow is fundamental to achieving optimal system performance. Mixing valves specialize in blending fluids to achieve a specific temperature, which is crucial in applications like heating, ventilation, and air conditioning, or in chemical processes where precise mixtures are vital. In contrast, diverting valves excel at guiding fluid flow along different paths, proving valuable in applications requiring flexible fluid distribution, like those found in complex hydraulic systems.
Although both types of valves can be integrated into various control schemes, their operational principles are distinct. Mixing valves work by adjusting the ratio of different fluids to reach a desired output temperature. Diverting valves, on the other hand, emphasize maintaining pressure balance and switching fluid flow between different outlets without manipulating the temperature or composition of the fluid itself. Recognizing this core difference is critical for system designers and operators to select the valve type that best matches the unique demands of their fluid system, leading to improved efficiency and reliability in the long run. It's about making conscious choices for the right valve to optimize a specific system and application.
1. Mixing valves excel at temperature regulation, often achieving very precise output temperatures, such as variations within ±0.5°C in critical applications like pharmaceutical processes. This highlights their ability to finely manage thermal conditions.
2. It's a misconception that diverting valves don't affect fluid temperature. In reality, rapid flow switching can create thermal shocks, potentially leading to unexpected temperature changes and alterations in the fluid's properties.
3. The materials used in mixing valves are frequently designed to account for thermal expansion. This helps maintain consistent performance, even during temperature variations, as they manage how the fluids blend.
4. While diverting valves primarily manage flow direction, they can also indirectly influence fluid thermal stability. Poorly controlled temperature differences can lead to thermal shocks over time, potentially jeopardizing system integrity.
5. Studies suggest that the temperature of combined fluids in mixing valves can significantly impact the viscosity of the final blend. This affects flow rate and overall system performance, emphasizing the importance of precise temperature control.
6. A mixing valve's performance isn't solely reliant on flow rate, but also the temperature of incoming fluids. Higher temperatures can lead to lower viscosity and more efficient mixing. However, excessive temperatures can negatively affect the valve's seals.
7. Recent developments in diverting valve design now incorporate thermal monitoring, allowing for real-time temperature assessment across different flow paths. This innovation enables enhanced control and proactive maintenance approaches.
8. Mixing valves can be susceptible to thermal stratification, where temperature differences create distinct layers of fluid. If left unaddressed, this can cause inconsistent outputs, illustrating the complex relationship between temperature management and flow dynamics.
9. Interestingly, the turbulence caused by diverting valves rapidly switching between outlets can generate heat, particularly at high speeds. This affects the fluid's thermal profile and poses challenges in precision applications.
10. The inclusion of temperature sensors, particularly within mixing valve systems, is a major step forward. It allows for dynamic control strategies that optimize performance, seamlessly linking temperature regulation and flow routing.
Comparing Mixing and Diverting Valves Key Differences in Flow Control Applications - Port Configurations and Flow Path Design
The way the ports are arranged and how fluids flow through a valve (flow path design) is crucial for how well a mixing or diverting valve manages fluids. For example, valves with a T-shaped port layout (T-port) allow for blending fluids from all three ports at once, ideal for mixing applications. On the other hand, valves with an L-shaped port layout (L-port) are designed to redirect the fluid flow at a 90-degree angle, making them suitable for switching flow paths. The internal shape of the valve (bore design) directly affects how the fluid moves and mixes within the valve, ultimately impacting the system's performance. It's important to recognize that selecting the correct valve type isn't just about picking the right part—it profoundly influences how reliable and efficient a system is, particularly across a variety of different applications where flow control is vital.
1. How the ports are arranged in flow control valves can significantly affect the amount of turbulence created when fluids move through them. This turbulence can lead to energy loss and uneven flow distribution, potentially harming equipment and reducing system efficiency. It's a constant tradeoff that designers grapple with.
2. Multi-outlet diverting valves can be cleverly designed to intentionally change flow rates. By making the ports different sizes or shapes, engineers can create preferred flow paths, making the system more adaptable to specific tasks. It's an interesting approach to optimization.
3. The internal channels in mixing valves are often engineered to minimize areas where the fluid might stagnate. This is important for ensuring that fluids are blended thoroughly, which is crucial in things like chemical or food processing where specific mixes are critical.
4. When looking at how fluids move, we need to consider the impact of port design on the chances of cavitation happening. If ports aren't designed well or if there are sudden changes in flow direction, the pressure can drop and create cavitation, which can damage the valve and nearby parts over time.
5. The angle at which fluid enters a diverting valve's ports can have a surprisingly large effect on how the fluid flows. Small changes in the angle can significantly alter the flow behavior and how fast the fluid is moving. This shows how careful the design process has to be.
6. Some more advanced mixing valves have flow meters built into the ports, allowing for real-time adjustments to how the fluids are blended. This innovation ensures that the output mixtures meet precise specifications and reduces variability, which is beneficial in applications where precision is critical.
7. The idea of perfectly even flow distribution in three-way valves can be misleading. Differences in fluid viscosity and density can make the distribution uneven. This means that accurate design and modeling are necessary to ensure the system works as planned.
8. The material used in the valve body doesn't just matter for how long it lasts, but also how the fluid moves. For example, smooth surfaces can lessen friction, leading to more consistent flow and pressure drops. This factor is often overlooked in materials selection and has a direct impact on valve performance.
9. Contrary to what some people might think, having multiple ports can actually simplify a system instead of making it more complex. It can streamline how the flow is managed and often reduces the total number of parts needed, making maintenance and repairs easier.
10. Engineers are increasingly using computational fluid dynamics (CFD) simulations to design port configurations. These simulations help them see and optimize how the fluid flows, ensuring that the valve designs meet their performance goals before actual physical prototypes are built. This approach is a great example of leveraging technology to address complex engineering challenges.
Comparing Mixing and Diverting Valves Key Differences in Flow Control Applications - Efficiency Considerations in Valve Selection
When considering the efficiency of valve selection, it's essential to understand the unique roles of mixing and diverting valves within fluid control systems. Mixing valves excel at temperature control by blending fluids, while diverting valves direct flow to various outlets. The selection of the right valve type not only directly impacts immediate fluid handling but also influences long-term system reliability and maintenance expenses. Optimizing valve selection by carefully considering system demands significantly improves operational efficiency. Choosing the wrong valve can lead to control problems, accelerated wear and tear, and potentially, system breakdowns. As industrial practices and fluid management systems evolve, understanding and improving these efficiency aspects of valve selection will remain crucial in various fluid control applications.
1. The materials a valve is made of can significantly influence its efficiency. For example, using valves with ceramic linings in harsh environments where particles are present can greatly reduce wear and tear. This helps to keep the flow consistent and lowers the need for frequent repairs and maintenance over time.
2. Mixing and diverting valves can sometimes exhibit unpredictable flow patterns under certain operating conditions. This can make controlling the system difficult and might necessitate using complex programming within PLCs to achieve the best results.
3. Studies show that using swirl flow technology in mixing valves can make them blend fluids more effectively. This results in faster mixing and less energy use compared to traditional mixing valve designs.
4. The type of actuator used to control a valve has a significant effect on overall efficiency. Choosing between pneumatic and electric actuators impacts not only how quickly the valve reacts but also the overall energy use of the flow control system.
5. The pressure drop across a diverting valve is a crucial consideration. Even a 10% pressure drop can cause a considerable reduction in flow rate and system efficiency. This highlights the importance of selecting valves that are perfectly suited for the specific application.
6. In high-speed fluid systems, "choking flow" can create substantial efficiency losses, especially when diverting valves are used. If a diverting valve isn't sized correctly, it can restrict the flow path and increase backpressure, potentially impacting system performance.
7. The angle at which fluid enters a valve can affect how stress is distributed across the valve's components. Optimizing these entry angles during the design phase can enhance the valve's durability and efficiency, especially in settings with high turbulence.
8. Using computer models to simulate fluid flow around valve ports can reveal opportunities to recover energy from the system. For instance, it might be possible to harness the energy from turbulent flow created by diverting valves to generate power in certain industrial settings.
9. Modern valves with built-in diagnostic capabilities and performance monitoring tools have shown the potential to increase the lifespan and efficiency of fluid systems. Engineers can use this data to predict and prevent valve failure through strategic maintenance routines, maximizing the operating life of the entire system.
10. Mixing valves may become less efficient if not properly calibrated for the specific properties of the fluids they handle. It's crucial to ensure a good match between the valve's design and the fluid characteristics to avoid issues like excessive turbulence and incomplete mixing, both of which impact overall system performance.
More Posts from aistructuralreview.com: