Identifying Contractor Red Flags for Building Structure Safety
Identifying Contractor Red Flags for Building Structure Safety - How a Contractor's Haste Impacts Foundations
A critical red flag to watch for with any contractor is an apparent rush to complete the foundation phase. This stage is non-negotiable for structural integrity, and prioritizing speed here often leads to serious compromises on building safety and longevity. When work is hurried, essential steps like adequate site preparation, careful placement and proper use of materials, and allowing sufficient time for curing are frequently neglected. These shortcuts, driven by the desire to move quickly to the next step, lay the groundwork for future problems. Property owners must recognize that this haste isn't efficiency; it's a warning sign that could result in foundational cracks, problematic settlement, or even dangerous structural failures over time. Insisting that the foundation is built meticulously and without undue haste is fundamental to preventing potentially catastrophic and costly issues later on.
Examining the fundamental steps of foundation construction reveals how deviations driven by a hurried schedule can subtly yet profoundly compromise long-term performance. From an engineering perspective, several critical processes are particularly vulnerable. Consider, for instance, the seemingly straightforward act of excavation; a contractor prioritizing speed might fail to dig precisely to the specified depth or, crucially, neglect to verify they have reached the intended load-bearing soil stratum identified during geotechnical investigation. Building on a weaker, more compressible layer than designed is a direct path to future excessive settlement. Moving to reinforcement, the accurate placement and securing of steel bars requires meticulous attention; haste often leads to inadequate concrete cover, allowing moisture and aggressive agents easier access to the steel, inevitably accelerating corrosion and weakening the critical tensile component of the foundation over time. Furthermore, the concrete itself relies on a specific chemical transformation – hydration – which requires time and careful curing. Rushing this stage by inadequate moisture management or premature loading prevents the full development of the cement matrix's strength and density, resulting in concrete that is more porous and less durable, susceptible to premature degradation. Finally, even the backfilling process surrounding the finished foundation is critical; hurried methods often neglect proper layer compaction, leaving hidden voids that will consolidate unevenly under load and environmental changes, contributing to differential settlement of the structure above. These are not minor shortcuts; they are procedural compromises at foundational stages that introduce long-term vulnerabilities difficult, if not impossible, to rectify later. Observing a contractor consistently pushing speed over procedural diligence across these steps serves as a significant indicator of potential structural issues down the line.
Identifying Contractor Red Flags for Building Structure Safety - Ignoring Permits and Plans Signs of Trouble Ahead
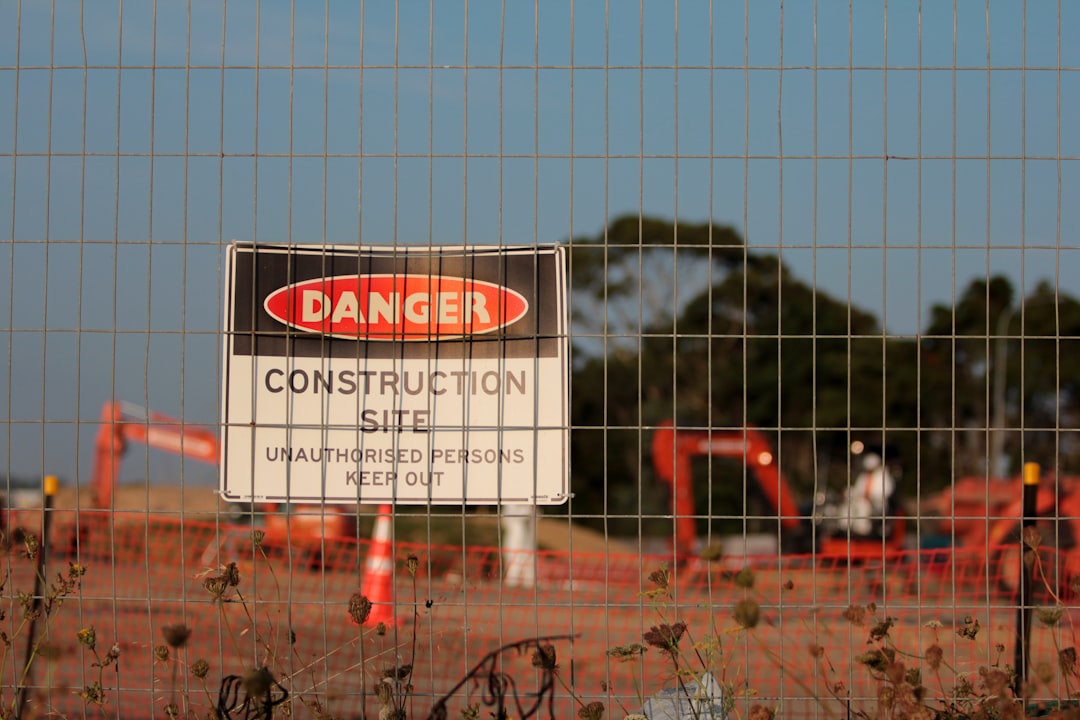
Sidestepping official permits and deviating from the agreed-upon, approved construction plans stands out as a significant warning sign for property owners focused on building structure safety. These governmental reviews and stamped plans serve as a fundamental layer of protection, confirming that the intended work aligns with established building codes and safety regulations designed for public welfare. A contractor who bypasses this essential process is effectively removing this independent oversight. This action frequently indicates potential problems such as unvetted changes to the structural design, the use of materials that were not specified or approved, or performing work without the required inspections intended to verify compliance at critical stages. Critically, it can suggest a contractor is operating without proper understanding of codes, or worse, deliberately cutting corners that would not pass standard checks. For the owner, the consequences can include a structure with hidden safety hazards, difficulty obtaining insurance or selling the property down the line, and potential legal mandates to rectify non-compliant work at great personal expense. Ignoring the requirement for permits and adherence to the plan is a deliberate choice that bypasses checks put in place for structural soundness and should be viewed as a critical indicator of potential trouble ahead for the integrity and safety of the building.
Skipping the formalized permit and plan review process isn't just cutting administrative tape; from a structural engineering perspective, it's bypassing critical technical safeguards. The approved plans embody the structural design, detailing how the building is meant to resist forces beyond just gravity – things like wind uplift and lateral seismic loads. They specify crucial elements, connection types, and bracing requirements. Ignoring these blueprints means these carefully calculated features designed for stability and resilience might be altered, misinterpreted, or omitted entirely on site, introducing significant, unplanned vulnerabilities into the structure.
Furthermore, neglecting to pull permits typically means foregoing mandatory inspections at various construction stages. These aren't mere bureaucratic hurdles; they are vital checkpoints where qualified eyes verify that critical structural components – the specific fasteners used for shear walls, the type and size of hold-down anchors connecting walls to the foundation, the splice lengths for rebar, the proper nailing patterns for framing – have been installed correctly according to the approved design. Without this independent third-party check, hidden installation errors or deviations that compromise the structure's ability to perform as designed can easily be built in, only becoming apparent later, often catastrophically.
The materials specified in the approved plans are integral to the structural calculations; they have defined strengths and properties. Diverting from these specifications without formal review, perhaps substituting lower-grade lumber, using undersized steel elements, or choosing fasteners with insufficient shear or withdrawal capacity, directly reduces the inherent safety margins the design relied upon. When permits and plans are ignored, the traceability and verification of installed materials against the design basis is lost, leaving the integrity of the load-carrying system open to significant, unquantified risk.
A structure's stability relies on an unbroken and appropriately strong path for loads to travel from where they are applied (like on the roof or floors) down through the walls and columns to the foundation and ultimately into the ground – the load path. The approved plans detail this critical path. When contractors disregard these plans or make unapproved changes because the process tied to permits is being circumvented, they can inadvertently disrupt this intended load path, potentially overstressing members or connections not designed to carry that burden. This can create points of premature failure under anticipated loads.
Lastly, while previous discussions may have focused on construction speed, bypassing the permit process often means the foundational design itself – its specific geometry, depth, reinforcement, and relationship to site-specific soil conditions derived from geotechnical reports – never received necessary engineering validation and approval through the building department. An unverified foundation design, even before considering construction quality, may be fundamentally inadequate for the actual loads and soil it must support, representing a foundational vulnerability that permits and plans are specifically intended to prevent by ensuring qualified review.
Identifying Contractor Red Flags for Building Structure Safety - When Cheap Materials Threaten Stability
Separate from rushing construction or bypassing necessary approvals, a serious warning sign can be found in the materials a contractor intends to use. Opting for substandard or cheap components to cut costs is a fundamental threat to structural integrity that may not be immediately obvious but can have severe long-term consequences. Utilizing lower-grade lumber, insufficient concrete specifications, or inadequate fasteners introduces inherent weaknesses into the structure's core framework. This practice, often motivated purely by increasing the contractor's profit margin, compromises the building's designed ability to withstand loads and environmental pressures. Such compromises are critical red flags because they lay the groundwork for premature failure, extensive deterioration, and pose direct risks to occupant safety. A focus solely on minimizing material expense suggests a disregard for the essential quality and durability required for a safe and lasting structure, which should be a clear concern for any property owner.
Beyond issues of process and planning, a more subtle, yet potentially catastrophic, red flag lies in the inherent quality – or lack thereof – of the raw materials themselves. At first glance, one piece of lumber or batch of concrete might look much like another, particularly to an untrained eye. However, hidden within lower-cost alternatives can be critical vulnerabilities that directly undermine the structural stability the design relies upon, manifesting their weaknesses only much later, sometimes years after construction appears complete.
Consider concrete, seemingly robust. Yet, cheaper mixes can sometimes incorporate aggregates (the gravel and sand within) that harbor chemical components, such as certain forms of silica, which can react slowly over extended periods with the alkaline cement paste, especially in the presence of moisture. This insidious Alkali-Silica Reaction (ASR) or Alkali-Carbonate Reaction (ACR) creates expansive gels *within* the concrete matrix. As these gels grow, they generate significant internal pressures – forces strong enough to micro-crack, then overtly fracture, and ultimately degrade the concrete from within. This isn't a surface issue; it's a fundamental disintegration of the material, compromising its compressive strength and ability to transfer load effectively, often causing patterns of map cracking on surfaces long after the structure is standing, a delayed threat born of material composition.
Moving to structural lumber, the visible grade stamps signify engineered properties, derived from limitations on strength-reducing characteristics. Cheaper lumber, potentially graded below standard or from sources with less stringent control, might superficially resemble compliant material but harbor larger or more numerous knots, significant diagonal grain, or other natural defects exceeding specified allowances. These features aren't just cosmetic; they act as stress concentrators and points of weakness, significantly lowering the lumber's predictable capacity to carry tensile, compressive, or bending loads compared to its ostensibly equivalent higher-grade counterpart. Relying on such material introduces unknown reductions in safety margins intended by the structural design.
Even the steel reinforcement embedded within concrete, critical for managing tensile forces, isn't immune to cost-cutting compromises. While typically assumed to have a certain resistance to environmental attack, the specific chemical composition or the nature of the mill scale or surface finish on lower-cost rebar can render it inherently more susceptible to corrosive agents like chlorides (from de-icing salts or marine environments) or attack facilitated by carbonation of the concrete cover. Should corrosion initiate and progress more rapidly due to these intrinsic material properties, the resulting rust expands, cracking the surrounding concrete cover, and more critically, reduces the effective cross-sectional area of the steel itself and degrades the essential bond between steel and concrete. This directly diminishes the composite section's ability to resist design loads over time.
Furthermore, a critical difference between certified, specified building materials and their cheaper, often unverified counterparts, lies in quality control and manufacturing consistency. Products from reputable sources undergo rigorous testing to ensure their properties – like strength, density, or stiffness – fall within a tight, predictable range. Conversely, cheaper materials may lack such stringent control, resulting in much higher variability. While the *average* tested property might seem acceptable, the presence of significant outliers – batches or pieces considerably weaker than the minimum expected value – creates unpredictable weak points anywhere within the load-bearing system. A single undersized piece of rebar or a section of concrete with poor matrix density can compromise the performance of an entire structural element under load.
Finally, even if the primary structural members like beams, columns, or walls possess adequate strength in isolation, the integrity of the load-carrying system hinges entirely on the connections transferring forces between them. Using non-certified, low-cost fasteners – be they nails, screws, bolts, or anchors – introduces a significant point of failure. These fasteners might appear correct visually but may be made from lower-grade alloys, lack proper heat treatment, or have insufficient geometric profiles. Consequently, their critical properties, such as shear strength (resistance to being cut) or withdrawal resistance (resistance to being pulled out), might be significantly below the values assumed in the structural design. Even if installed correctly according to pattern, these inadequate fasteners mean the critical joints designed to safely transfer forces could fail prematurely under design loads, initiating a chain reaction of instability throughout the structure. Recognizing a contractor's propensity for sourcing the least expensive materials, particularly without verification of their adherence to design specifications and relevant standards, is a potent red flag regarding the potential for long-term structural compromise.
Identifying Contractor Red Flags for Building Structure Safety - Spotting Contractors Who Skimp on Safety Standards
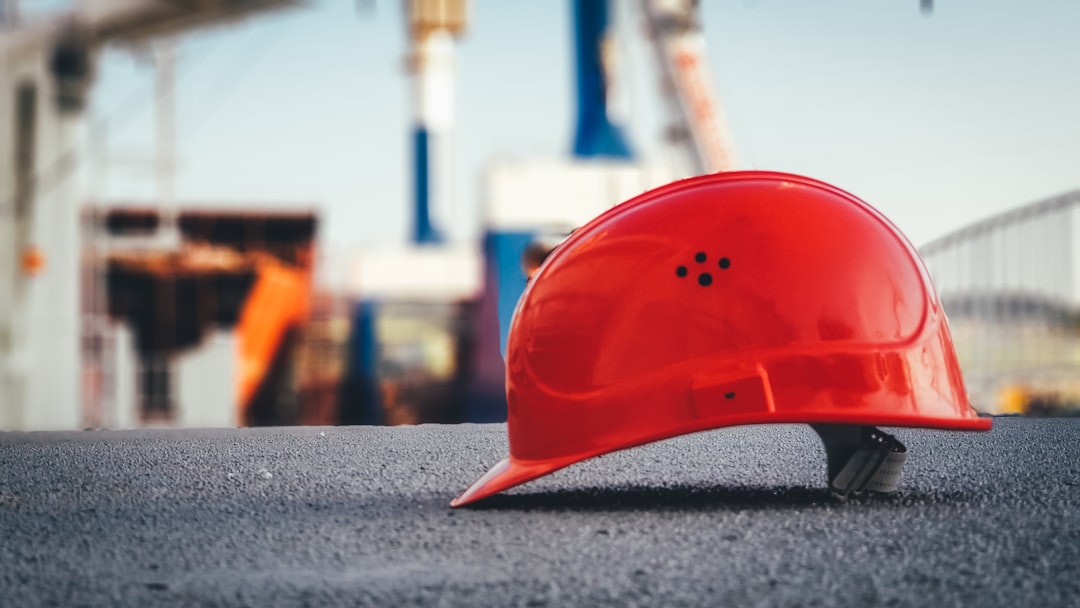
Beyond the foundational work, paperwork, and material selection, a significant indicator of a contractor potentially compromising structural safety lies in their observable approach to basic site safety practices. A contractor who overlooks the wellbeing of their crew often reveals a deeper disregard for established standards and attention to detail that can extend to the building itself. Signs like inconsistent or absent use of personal protective equipment (hard hats, safety glasses, proper footwear), inadequate fall protection on elevated work areas, or a general messy and unorganized work environment aren't just minor infractions; they signal a potential lack of rigorous process and risk awareness.
This negligence suggests that if a contractor is willing to gamble on the immediate safety of people on site, they may also be inclined to cut corners on less visible, but equally critical, aspects of structural construction. It reflects a culture where convenience or cost trumps careful adherence to protocol. Such an attitude can manifest in overlooked details during installation, improper sequencing of work, or a failure to implement necessary temporary bracing or support, all of which can introduce weaknesses into the structure. Observing a consistent lack of adherence to fundamental safety protocols should raise serious concerns about the overall conscientiousness and reliability of the contractor and their commitment to the total quality and integrity of the project, including the structural elements.
Beyond fundamental issues like rushing structural phases, sidestepping required reviews, or compromising on material intrinsic properties, there are other, perhaps less obvious, behavioral and procedural indicators that can signal a contractor's willingness to cut corners on safety standards, with potential repercussions for the finished structure's integrity.
Consider the excavation process, the initial interface between the structure and the earth. While the immediate risk of trench collapse to personnel is profound, a contractor's failure to implement proper shoring or sloping techniques also speaks to a disregard for soil mechanics adjacent to the planned foundation footprint. The resulting instability isn't just temporary; ground disturbance or collapse in this zone can alter the load-bearing characteristics of the surrounding soil, potentially leading to long-term differential settlement issues for the foundation above, a consequence far removed from just worker safety metrics.
Similarly, the period *during* construction, before a structural system is fully completed and capable of carrying its design loads, is critically vulnerable. Observing erected walls, beams, or columns standing without adequate temporary bracing reveals more than just a lapse in site organization. It indicates a fundamental underestimation or disregard for temporary loads—forces like wind gusts or incidental construction impacts—that the incomplete structure isn't yet designed to resist on its own. This is a visible gamble with acute instability, demonstrating a willingness to expose the partially built system to undue stress or even collapse before it achieves inherent stability.
Another operational flag, seemingly mundane, involves the placement of materials on site. The act of stockpiling heavy dense components—concrete blocks, bundles of rebar, or substantial lumber packages—on partially completed floor systems without first verifying that the structural elements (joists, temporary decking, formwork) possess the capacity to support these concentrated temporary loads points to a disregard for structural limits during the construction phase. Exceeding these temporary load capacities can induce plastic deformation or damage structural members even before the building is occupied, subtly compromising their long-term performance.
A more direct, observable red flag related to site practices involves the handling of tools and machinery. When workers are seen using power tools with safety guards removed or engineered interlocks bypassed, it suggests a deliberate circumvention of designed safety controls. While often discussed in the context of preventing immediate injury, this behavior can also lead to imprecise or damaging application to structural components—oversized or misaligned holes, unintended cuts, or surface damage—which can locally weaken the material or compromise crucial connections.
Finally, the most basic visible safety practices can serve as a proxy for a contractor's overall attitude. A consistent pattern of site personnel neglecting fundamental personal protective equipment—simple items like hard hats where overhead hazards exist, safety glasses during cutting or grinding, or appropriate footwear—suggests a broader, lax safety culture. If the most overt, easily followed safety protocols are routinely ignored, it raises serious questions about adherence to the more complex, less visible, but structurally critical standards related to proper installation techniques, material handling, or working within design constraints. These basic observations, while perhaps not immediately linked to complex engineering, offer a telling insight into the contractor's underlying respect for safety protocols in their entirety.
More Posts from aistructuralreview.com: