Laminar and Turbulent Flow Structural Effects
Laminar and Turbulent Flow Structural Effects - Pressure Field Variance Under Laminar and Turbulent Conditions
When considering the pressure landscape within a fluid flow, the fundamental distinction between laminar and turbulent regimes is stark. Laminar flow, characterized by its smooth, layered movement, typically presents a pressure field that is relatively stable and predictable, reflecting the underlying orderly nature of the fluid particles. Conversely, turbulent flow is a dynamic, chaotic state marked by significant, rapid fluctuations in both pressure and velocity across space and time. This inherent variance in the turbulent pressure field introduces complexities absent in laminar conditions. The transition from a laminar to a turbulent state, or the presence of turbulence itself, dramatically alters the pressure distribution acting upon surrounding structures. This shift in pressure dynamics is directly relevant to the structural response, potentially inducing varying levels of stress and strain on components interacting with the flow. Grasping the nature and magnitude of this pressure field variance is therefore crucial for accurate analysis and robust design in engineering scenarios where diverse flow conditions, particularly the unpredictable aspects of turbulence, must be accommodated. Accurately capturing this variability remains a significant challenge in flow modeling.
Exploring the characteristics of pressure fields under vastly different flow conditions, one might find a few points particularly noteworthy:
For instance, consider the sheer scale: the dynamic fluctuations in pressure observed within a turbulent flow regime can readily reach levels many thousands of times greater in amplitude than any comparable unsteady variations encountered under strictly laminar conditions. This highlights the fundamental difference in the energetic nature of the flow's interaction with boundaries.
Then, there's the spatial signature: rather than a truly random scattering of pressure points on a surface beneath turbulence, we often see patterns. These spatial pressure maps appear correlated to the scale and transient movements of the larger, more coherent (or perhaps 'less incoherent' is more accurate) eddy structures within the bulk flow just above the surface.
Furthermore, while the time-averaged pressure value might not differ dramatically between the regimes, focusing solely on the mean or even the root-mean-square (RMS) variation misses the crucial detail: instantaneous peak pressure excursions in turbulence can momentarily surge to values several times the RMS level. These short-duration, high-magnitude spikes are disproportionately important for predicting dynamic structural response and potential fatigue.
From a frequency perspective, the pressure variance in turbulent flow isn't concentrated in a narrow band but is spread broadly across many frequencies. This broadband energy spectrum means the turbulent pressure fluctuations can potentially excite a variety of different natural vibration modes within an adjacent structure, unlike the often quasi-steady or slowly varying pressures typical of laminar flow.
Ultimately, unlike the predictable, smoothly evolving pressure fields in laminar flow which often reflect geometry or steady forcing, the dynamic pressure variations in turbulence are fundamentally self-generated. They arise directly from the complex, non-linear internal dynamics of the turbulent velocity field itself, the swirling, stretching, and colliding motions of the fluid creating pressure variations from within the flow fabric.
Laminar and Turbulent Flow Structural Effects - Convective Heat Transfer Dissimilarities and Thermal Stress
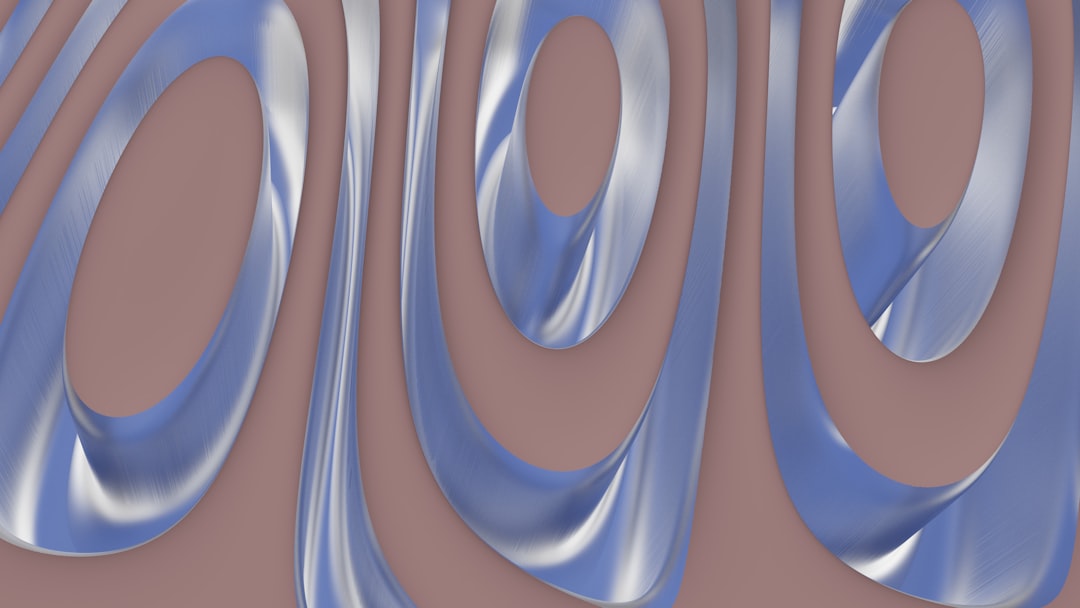
When considering how heat moves from a fluid to a surface, the fundamental nature of the flow—whether smooth and layered (laminar) or chaotic and swirling (turbulent)—creates profound differences in convective heat transfer, directly impacting the thermal stress on adjacent structures. A standard measure for this effectiveness, the Nusselt number, clearly shows that turbulent flow conditions are far more efficient at transferring thermal energy than laminar ones. Engineers frequently exploit this by encouraging turbulence or integrating flow modification techniques like internal fins or specific channel geometries specifically to boost heat transfer rates in systems requiring effective cooling or heating. However, this enhanced heat transfer is rarely uniform; variations in local flow structures, even within a turbulent field, can lead to significant differences in heat flux across a surface. These non-uniform heat transfer rates result in differential thermal expansion or contraction within materials, generating internal stresses that can challenge structural integrity in ways that the comparatively gentle heat transfer of laminar flow typically does not. Accurately predicting these thermal stress landscapes, particularly under the dynamic and spatially varying conditions of turbulence, represents a persistent challenge in structural design and requires careful consideration beyond simple averaged properties.
Moving our focus from the force landscape to the thermal interplay, the behavior of convective heat transfer and its implications for structural integrity also differ profoundly between laminar and turbulent flow regimes.
Consider the sheer capacity: turbulent flow can strip heat from a surface, or dump it into one, many tens or even hundreds of times more effectively than its laminar counterpart operating under comparable conditions of speed and temperature difference. This massive amplification in thermal transport capability fundamentally alters the thermal state of adjacent components, subjecting materials to significantly higher net thermal loads and, perhaps more importantly, much steeper temperature gradients concentrated near the surface.
It's fascinating to note the primary engine driving this enhanced heat transfer in turbulence isn't simply the bulk velocity fluctuations, though those play a role. The critical factor appears to be the turbulent flow's relentless agitation and rapid renewal of the exceptionally thin thermal boundary layer that clings to the surface. This continuous mixing essentially short-circuits the relatively slow process of pure conduction across a static or slowly changing thermal layer, effectively pulling heat away from (or driving it into) the material's interior far more quickly. This mechanism intensifies temperature gradients right where the fluid meets the solid.
Furthermore, unlike the often steady or slowly varying temperature distributions seen under stable laminar convection, turbulent flow imposes heat transfer conditions that fluctuate rapidly and substantially in both magnitude and location. These dynamic thermal inputs create transient temperature fields within the material, inducing thermal stresses that are inherently time-varying. These aren't the steady mechanical stresses from average pressure loads; they are distinct stresses arising purely from differential thermal expansion driven by temperature changes, and they contribute directly to fatigue mechanisms, independent of pressure-induced loads.
Just as with pressure, relying solely on time-averaged values for heat flux or temperature can be misleading. Instantaneous measurements under turbulent conditions reveal local heat transfer rates that can momentarily surge far beyond the average, leading to fleeting but intense hot or cool spots on the surface. These localized temperature excursions, albeit short-lived, drive peak thermal stresses that can be considerably higher than what one might calculate based on mean heat transfer coefficients alone – a critical detail easily missed in simplified analyses.
Finally, the temporal variability of temperature fields imposed by turbulent flow isn't confined to a single frequency; it exhibits a broadband spectrum. This means the material is subjected to thermal expansion and contraction cycles occurring across a wide range of frequencies simultaneously. Such broadband thermal loading carries the potential to excite various material responses and could conceivably resonate with characteristic material timescales, such as its thermal diffusivity, potentially accelerating damage processes like thermal fatigue through a complex interplay of thermal cycling across diverse temporal scales.
Laminar and Turbulent Flow Structural Effects - Wall Shear Stress Effects on Structure Surface Durability
Wall shear stress, acting tangentially along a surface exposed to fluid flow, represents a key force influencing its material endurance, particularly as flow conditions transition from smooth laminar motion to chaotic turbulence. Under a laminar regime, this tangential stress tends to be comparatively steady and follows predictable patterns based on geometry and mean flow. However, within a turbulent flow, the nature of wall shear fundamentally changes; it becomes intensely irregular and complex, varying significantly over both space and time. These rapid fluctuations in wall shear are not merely academic; they translate directly into dynamic, localized stresses imposed on the surface material. The continuous, chaotic buffeting from these fluctuating shear forces can contribute substantially to processes like surface fatigue and cumulative damage over time. Designing structures meant to withstand turbulent flow environments necessitates grappling with the complex, often non-uniform, distributions and intense fluctuations of wall shear stress. Accurately characterizing and predicting the long-term structural response to this dynamic tangential loading, especially its localized peaks and spatial variations driven by the turbulent flow structures just above the wall, remains a persistent analytical and computational challenge for ensuring surface longevity. Ignoring these complexities, or oversimplifying the turbulent wall shear environment, risks underestimating potential degradation pathways.
Moving beyond the forces acting normal to a surface—the pressures—and the complexities of heat transfer, it's crucial to consider the tangential force exerted by the fluid: the wall shear stress. This often-overlooked aspect represents the friction-like drag on a structure's boundary and plays a pivotal role in determining surface durability through mechanisms quite distinct from pressure or thermal loads. Understanding the nature of wall shear stress, especially how it behaves differently under laminar and turbulent conditions, is essential for anticipating material wear, fatigue, and chemical degradation at interfaces.
It's worth considering how wall shear stress manifests and influences structure surfaces:
We observe that, even at comparable bulk flow speeds, the average wall shear stress can be significantly higher—easily an order of magnitude greater—in turbulent flow compared to laminar flow. This amplified tangential drag arises directly from the much steeper velocity gradients right at the wall, a consequence of the intense, small-scale mixing characteristic of turbulence relentlessly pulling fluid layers past each other near the surface.
Beyond the higher average, the wall shear stress in turbulent flow isn't steady; it undergoes rapid, substantial fluctuations. These momentary peaks can surge to values many times the average, exerting transient tangential tugs on the surface. It appears these intense, short-duration tangential forces are particularly effective at initiating surface cracks associated with fatigue and are potent drivers for dislodging adherent particles or stripping away protective coatings.
Interestingly, the interaction between the surface's physical texture and the wall shear stress forms a dynamic feedback loop. The shear stress itself contributes to wear mechanisms like erosion, altering the surface topography. In turn, these changes in surface roughness profoundly modify the local flow field and, consequently, the distribution and magnitude of the wall shear stress, thereby influencing subsequent wear and degradation patterns. This implies that the journey of durability is one of continuous interaction, not just dictated by the starting condition.
Furthermore, wall shear stress acts as a primary transport mechanism for solid particles flowing within the fluid. Higher shear stress zones are particularly effective at sweeping particles along the surface, increasing the frequency and force of their impacts. This direct link between the fluid's tangential pull and particle motion is fundamental to understanding and predicting erosive wear rates, concentrating abrasive action where the shear is strongest.
Lastly, wall shear stress doesn't operate in isolation from chemical processes. It significantly impacts electrochemical corrosion rates by enhancing the convective transport of reactive species towards the surface and, perhaps more critically, by mechanically disrupting or removing fragile passive films or loosely adhering corrosion products. This mechanical influence on chemical kinetics means fluid motion and its associated wall shear can dramatically accelerate material degradation even in environments that are only moderately corrosive.
More Posts from aistructuralreview.com: