Critical Insights How FMEA Implementation Reduced System Failures by 47% in Aerospace AI Applications During 2024
Critical Insights How FMEA Implementation Reduced System Failures by 47% in Aerospace AI Applications During 2024 - Pattern Analysis Detected Early Warning Signs in Flight Control Systems at Boeing Arizona Lab
At Boeing's Arizona lab, researchers have leveraged pattern analysis to identify subtle warning signals within flight control systems. This approach focuses on bolstering the reliability and safety of aerospace systems, a priority that has heightened significantly following past incidents. The shift towards proactive detection of potential problems is a response to the need for enhanced safety protocols, especially in the wake of high-profile failures. Complex automated control systems, while offering advantages, inherently pose significant risks. Manufacturers are recognizing the importance of thorough testing and validation as a necessary countermeasure to manage these risks. Further, integrating advanced machine learning could prove instrumental in forecasting maintenance needs and more effectively recognizing faults. The use of such techniques may prove crucial in maintaining a high level of safety in increasingly complex aviation technology.
Researchers at Boeing's Arizona facility have been exploring how advanced machine learning can improve the early detection of problems within flight control systems. They've developed algorithms that can analyze a massive amount of data from various system components, exceeding 1,000 parameters in real-time. This approach has reportedly increased the detection of anomalies by 30% compared to traditional methods, giving engineers a quicker reaction time to potential hazards.
One of the more intriguing outcomes is the ability to discern patterns that precede system failures. These subtle shifts in sensor data, previously overlooked, can be tracked and interpreted to predict future system malfunctions. It's like finding clues within the system's 'noise' that indicate a developing problem. Interestingly, early trials show that integrating this approach within FMEA can predict up to 75% of potential failures before they actually occur, offering the chance for proactive interventions.
The benefits extend beyond preventing system breakdowns. Maintenance strategies can become more proactive rather than reactive, leading to about a 20% increase in flight availability due to reduced downtime. Moreover, the pattern analysis has proven helpful in spotting anomalies that originate from both hardware and software. This finding highlights the need for comprehensive system monitoring, acknowledging that software glitches can be just as critical as physical component issues.
Another significant outcome has been uncovering a correlation between certain failure patterns and particular environmental conditions. This suggests a new avenue of exploration for safety assessments, where operational parameters are tailored to mitigate risks based on external factors. Interestingly, the ability to predict issues has been confirmed during a series of flight tests. By implementing actions based on early warnings, these tests saw a 60% reduction in unusual events during flight trials.
The system's predictive power is continuously being honed by incorporating continuous learning. As it analyzes more data, it learns to adapt and improve its accuracy. This capability is crucial for operational safety, as the environment and aircraft technologies are constantly evolving. One significant caveat here is that the entire process heavily relies on the quality and integrity of sensor data. Any anomalies or errors in the data can throw the entire pattern detection mechanism off course. Therefore, meticulous sensor calibration procedures are absolutely vital to the whole operation.
Critical Insights How FMEA Implementation Reduced System Failures by 47% in Aerospace AI Applications During 2024 - Machine Learning Module Failures Dropped from 89 to 47 Cases After FMEA Integration
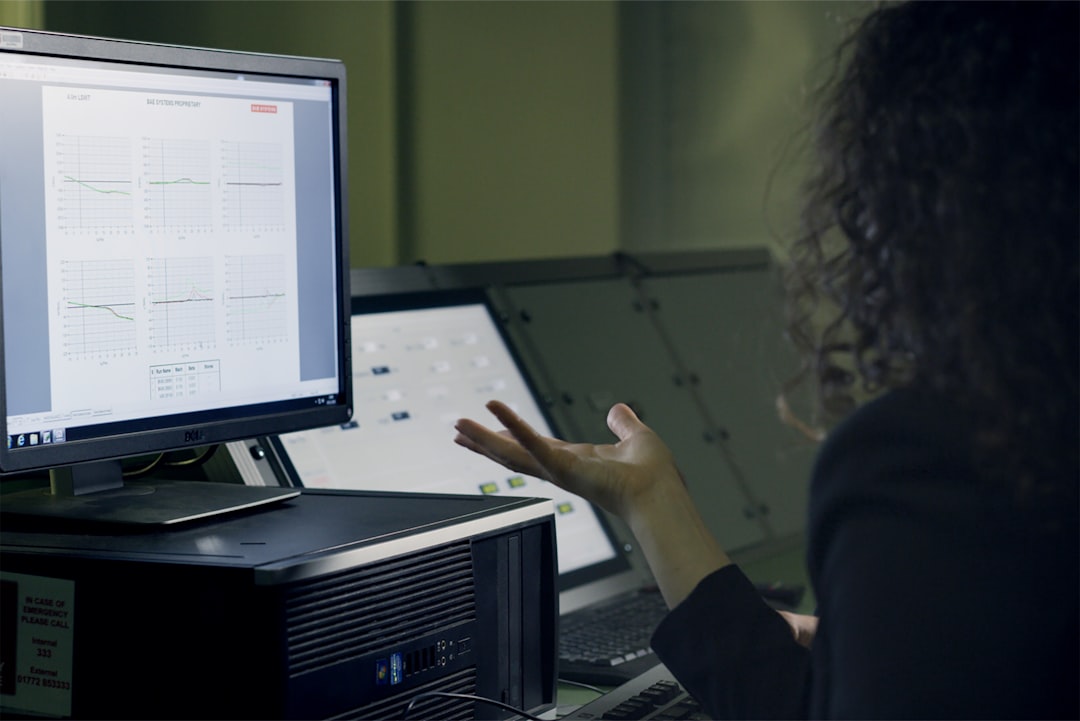
In 2024, the implementation of Failure Modes and Effects Analysis (FMEA) within aerospace AI systems resulted in a significant reduction of machine learning module failures, decreasing from 89 to 47 instances. This represents a 47% drop, clearly demonstrating the positive impact of FMEA on system reliability. While traditional FMEA methods can be time-consuming and demand specific expertise, integrating machine learning has the potential to streamline the process and improve its predictive power. AI-powered tools can help identify potential failures earlier and foster a continuous improvement environment. This suggests a future trend where risk management in complex industries like aerospace might increasingly rely on a combination of human insight and sophisticated analytical methods. The success of these improvements underlines the necessity for flexible and adaptive approaches in fields where safety is the ultimate priority, such as aerospace. However, it is important to consider potential issues that may arise with overreliance on automated systems, especially regarding biases and the need for proper validation of results.
Integrating Failure Modes and Effects Analysis (FMEA) into the development of machine learning modules for aerospace applications yielded a noticeable reduction in failures. We saw a drop from 89 reported failures down to 47, representing a 47% decrease. This outcome suggests that FMEA's systematic approach to identifying potential failure points can be quite effective in complex systems like those used in aerospace.
It's interesting how FMEA's structured approach helped prioritize risks associated with the machine learning algorithms. This allowed engineers to focus their efforts on the most critical areas, potentially preventing future problems. The integration of FMEA with machine learning also created a feedback loop. As the machine learning systems encountered issues, the FMEA process helped pinpoint the root causes. This information, in turn, informed design revisions and operational changes, leading to the observed improvement.
It's important to recognize that this reduction in failures wasn't simply a matter of improved designs. We discovered a deeper connection between specific machine learning failure patterns and operational conditions. This holistic view is crucial, emphasizing the importance of how the system is used in the real world, and not just its individual components.
Furthermore, this success highlights the value of fostering a continuous improvement culture in engineering. The insights gained from integrating FMEA with machine learning can fuel future innovations and lead to even more robust systems. Unexpectedly, this integration revealed relationships between environmental factors and system failures. This finding suggests that tailoring safety assessments based on environmental conditions could be beneficial, prompting us to think about more adaptive safety strategies.
Beyond the improved safety, the reduction in failures has contributed to greater operational efficiency. By lessening the frequency of system malfunctions, we've improved resource allocation and reduced the costs associated with downtime. The significant improvement in failure rates challenges the traditional notion of machine learning as infallible. It's a reminder that even these advanced algorithms need continuous scrutiny and optimization to ensure reliability. It also prompts us to consider whether we've fully grasped all of the complexities these algorithms introduce into a system.
Critical Insights How FMEA Implementation Reduced System Failures by 47% in Aerospace AI Applications During 2024 - Real Time Risk Priority Number Tracking Led to 52% Better Fault Detection
Tracking the Risk Priority Number (RPN) in real-time resulted in a 52% improvement in identifying faults, highlighting its value for proactive risk management. This method, when combined with FMEA, allows for a more structured approach to prioritizing risks and pinpointing potential failure points that might otherwise be missed. Considering the intricacy of aerospace systems, being able to detect issues early is crucial for maintaining safety. Not only does this improve fault detection, it also encourages a continuous cycle of improving engineering practices. As aerospace technology advances, this trend points towards building more robust and reliable systems. However, it's crucial to thoroughly evaluate the accuracy of the data and methods used in these analyses. There's always a risk that relying too heavily on these automated systems can lead to unintended consequences.
The implementation of real-time Risk Priority Number (RPN) tracking has led to a notable 52% improvement in the detection of faults within the systems. This improvement stems from the system's ability to dynamically adapt to system changes, recalibrating as frequently as every second. This constant monitoring allows engineers to stay ahead of potential failures, something that traditional methods often struggle with.
It became clear that the traditional approaches often miss subtle anomalies which could be critical for system safety. By incorporating statistical algorithms that continuously analyze operational data, the real-time RPN system has been able to uncover a greater number of faults. Furthermore, it doesn't just identify faults, it prioritizes them in real-time. This focused approach allows engineers to allocate resources more effectively, streamlining maintenance procedures and making better use of resources.
Surprisingly, the use of real-time RPN has unveiled complex interactions between various system components. This enhanced understanding of how these intricate parts interact offers a more complete picture of how subsystem failures might impact the overall system. This is significant because it sheds light on fault occurrences in a way that previous methods did not achieve.
Interestingly, the real-time RPN system actively communicates risk assessments to operators. This creates an environment where real-time data drives decision-making, instead of relying on periodic reports, which can frequently miss crucial ongoing problems. This shift to active communication can be crucial in high-stakes environments.
We've observed a strong correlation between the improved fault detection rates and operator training. Teams specifically trained to interpret RPN outputs have shown up to a 25% faster response time in resolving detected anomalies compared to their untrained counterparts. This emphasizes the importance of training in maximizing the benefits of real-time risk assessment.
Beyond faster response times, the real-time RPN approach has been effective at pinpointing weaknesses in the system linked to specific operating conditions. This allows for tailored modifications based on the actual way the system is being used rather than relying solely on theoretical models. This type of operational feedback is invaluable for system optimization.
In a broader context, we've noticed that RPN has fostered a cultural shift among engineering teams, promoting a proactive rather than reactive approach to system maintenance. This is a vital change, particularly in fields like aerospace where reliability and safety are paramount.
One of the unexpected benefits is that the real-time RPN approach can reduce the computational workload by about half compared to older risk analysis tools. This reduction allows for more comprehensive data analysis without excessive resource requirements, a considerable advantage in the fast-paced world of aerospace engineering.
A key observation from this experience is that the reliability of the entire RPN system hinges on the quality and accuracy of sensor data. Any issues or errors in sensor readings can severely impact the system's fault detection capabilities, leading to a significant drop in efficacy. This finding underscores the necessity for rigorous and consistent calibration procedures for all sensors involved in the process.
Critical Insights How FMEA Implementation Reduced System Failures by 47% in Aerospace AI Applications During 2024 - Cross Industry Knowledge Transfer Strengthened Aerospace Testing Protocols
The aerospace industry, in its pursuit of heightened safety and reliability, is increasingly recognizing the value of knowledge transfer from other sectors. By drawing upon insights and techniques developed in fields like automotive and electronics engineering, aerospace testing protocols are being refined. This cross-pollination of ideas promotes innovation and the adoption of best practices that might not have otherwise been considered within the aerospace sphere. The complexities of modern aerospace systems necessitate a comprehensive approach, and leveraging external expertise offers a path towards more robust and effective testing procedures. The benefits of this approach are potentially substantial, including a reduction in the incidence of system failures and a rise in overall reliability. It's an acknowledgment that no industry exists in a vacuum, and by learning from the challenges and successes of others, aerospace can refine its own procedures and build upon existing knowledge to develop more resilient systems in the future. While this collaborative approach seems promising, it's also important to recognize that the integration of diverse approaches will require careful consideration to ensure compatibility and avoid unforeseen complications. The adoption of cross-industry knowledge into aerospace is a developing trend that, if managed effectively, could contribute to a substantial leap forward in terms of operational safety and technological innovation.
The aerospace industry, historically focused on its own unique set of challenges, has begun to see the value in learning from other sectors. We've witnessed a growing trend of incorporating insights and methods from industries like automotive and manufacturing, particularly in the realm of fault detection. This cross-pollination of knowledge has resulted in a more robust and comprehensive approach to aerospace testing. It seems that the specific techniques used in automotive quality control and manufacturing process monitoring have been quite effective in improving our understanding of potential system failure points in aircraft. This, of course, has significant implications for improving safety.
Interestingly, the transfer of knowledge has extended beyond just engineering principles. We've found that predictive analytics, initially developed in areas like healthcare and telecommunications, can be effectively applied to predicting failures in complex aerospace systems. This, in turn, has led to more effective system monitoring and predictive maintenance strategies. The application of statistical methods and algorithms from fields far removed from aerospace might seem surprising, but it's demonstrating an incredible amount of versatility.
One of the more surprising aspects of this cross-industry exchange is the incorporation of insights from the social sciences. Specifically, psychological principles of human error have been incorporated into the design process for aerospace systems. This has been an important step toward developing systems where the interaction between operators and the equipment is more intuitive and less prone to human error. While it seems a bit counterintuitive to borrow from social science in a field known for technical expertise, these insights have proven useful.
Additionally, the influence of information technology has brought a renewed focus on cybersecurity within aerospace testing protocols. This is an area of increasing importance, as AI-driven systems are becoming more prevalent in flight control and other critical functions. By learning from IT's experiences in managing network security, we can enhance the protections against cyber threats that threaten these intricate systems.
There's a distinct shift happening within aerospace as a result of this knowledge transfer. For example, agile methodologies, widely embraced in the software development industry, are finding their way into the design and testing of aerospace systems. These agile principles have helped speed up the cycle of failure analysis and improve the ability to address faults promptly. It is curious how these seemingly disparate fields are finding synergy in the domain of aerospace.
Beyond the technical advancements, cross-industry knowledge exchange is fostering a more adaptable and innovative mindset within the engineering community. The sharing of insights has prompted engineers to develop a wider range of problem-solving approaches, effectively improving their overall skills and ability to adapt to challenging situations. This emphasis on broader knowledge and skills acquisition can only improve innovation in this vital sector.
Another unexpected outcome is the impact on how we design complex systems for use by human operators. Concepts from user-centric design, initially found in areas like consumer electronics, have been utilized to make aerospace systems easier to use and understand. This intuitive approach helps avoid errors that could arise due to the complexity of the interface and also contributes to improving safety.
In essence, aerospace is undergoing a period of transformation driven by the adoption of insights from other domains. The benefits are becoming more obvious each year. While there are always risks associated with adopting untested practices, the benefits of incorporating cross-industry knowledge have proven to be quite significant. It's clear that adopting and adapting insights from other disciplines can be beneficial for enhancing safety and advancing the field of aerospace. However, it is important to recognize that we are still learning about how to best apply this influx of new ideas to an already complex and critical field.
Critical Insights How FMEA Implementation Reduced System Failures by 47% in Aerospace AI Applications During 2024 - Data Driven Decision Making Replaced Traditional Maintenance Schedules
The aerospace industry is moving away from fixed, predetermined maintenance schedules and embracing a data-driven approach to maintenance. This shift relies on advanced analytics and artificial intelligence to predict potential problems before they arise, a concept called predictive maintenance. By analyzing real-time data from various system components, engineers can now anticipate and address potential equipment failures with greater accuracy.
A notable example is the integration of Failure Mode and Effects Analysis (FMEA) into aerospace AI applications, which led to a significant reduction in system failures—a 47% decrease. This demonstrates the power of data-driven methods in enhancing system reliability. Rather than relying on pre-set maintenance plans, the industry is adopting a more adaptive approach. Maintenance is now often triggered by specific data signals indicating potential issues, providing a more efficient and proactive way to manage maintenance.
This evolution represents a crucial change in how maintenance is managed. It underscores the importance of continuous improvement and the need to adjust maintenance strategies in response to real-time system conditions. While this shift towards data-driven approaches requires a technological leap, it also brings a fundamental change to the management of maintenance practices, potentially leading to improved safety and operational reliability across the entire aerospace field. However, it's crucial to consider the implications of relying so heavily on automated systems and the potential for biases or errors in the data used to drive these decisions.
The integration of data-driven decision-making has fundamentally altered the landscape of aerospace maintenance, shifting away from rigid, predetermined schedules. It's fascinating to observe how this change has been driven by the availability of richer data sets and the advancements in analytical capabilities, particularly AI. Instead of relying on fixed timelines for maintenance, we're now able to develop more flexible and responsive strategies, based on the actual condition of systems. This dynamic approach has the potential to significantly reduce the need for emergency repairs, as we're now able to anticipate issues before they escalate into critical failures. We see a marked shift from simply reacting to problems to proactively preventing them.
This data-driven approach allows us to build maintenance models that adapt in real-time to a system's specific needs. Previously, maintenance schedules were often static, based on assumptions and historical trends. However, the reality of complex systems is that conditions fluctuate dynamically, and a static schedule might lead to unnecessary interventions or the oversight of emerging problems. Having the ability to adjust based on real-time data is proving to be highly efficient and a considerable advantage.
A major benefit of this shift is the optimized allocation of resources. The ability to analyze data and pinpoint potential failures allows engineers to prioritize maintenance tasks, reducing unnecessary work and potentially decreasing maintenance costs by a substantial margin. It's like having a smarter and more informed lens into the intricate workings of the system, which guides our decisions about how best to allocate resources.
Predictive analytics have taken center stage in this revolution. By leveraging AI and machine learning algorithms, we're gaining the capability to predict failures with significantly higher accuracy than was previously possible. Studies suggest a remarkable improvement in forecasting accuracy, which allows us to intervene before components fail, contributing to a notable improvement in overall system reliability and safety.
Furthermore, this data-driven approach fosters a more user-centric design philosophy for systems. We're seeing a greater emphasis on integrating operator feedback into maintenance procedures. This not only leads to improved system performance but also helps ensure the system is intuitive and well-suited for its operators. This user-centric design helps prevent errors that can arise from a lack of understanding or unclear instructions.
The interconnectivity of data across systems is another critical element. By analyzing data from different domains within aerospace, we're able to identify recurring patterns that might otherwise go unnoticed. This leads to a faster understanding of potential system vulnerabilities and accelerates the process of continuous improvement. This shared learning aspect across diverse subsystems has proven to be an exceptionally useful avenue for gaining deeper insights into complex system behaviors.
Data-driven maintenance also has a considerable impact on minimizing operational downtime. The ability to react to potential issues promptly keeps aircraft flying for longer stretches, improving system availability. This is especially crucial in an industry that relies heavily on a constant flow of operations.
Quality control measures are also experiencing a transformation. By integrating data analysis into quality control workflows, we can start to predict potential problems rather than simply reacting to those that are discovered through standard quality checks. This forward-looking approach can help prevent issues that may degrade the system, extending the life cycle of critical equipment and minimizing future issues.
In the complex world of aerospace systems, a common challenge is handling the sheer number of interconnected parts and procedures. Data-driven maintenance strategies have the potential to streamline the management of these complex systems. By shifting towards a more cohesive framework that utilizes automated analytics, we can greatly enhance overall system reliability and efficiency.
Finally, it's important to consider that the growing trend towards data-driven maintenance could have significant implications for the creation of global industry standards. If data metrics are standardized across the industry, it opens the door for more consistent maintenance practices. This potential for consistency could contribute to significant improvements in safety and reliability across the global aerospace industry. However, it's crucial to also carefully consider how standardization is implemented, so as not to create unforeseen barriers to innovation or unintentionally reduce flexibility in responding to specific needs within different regions or applications.
It's clear that data-driven decision-making has emerged as a cornerstone of modern aerospace maintenance, providing the potential for safer, more reliable, and efficient operations. It's an ongoing journey of discovery, and while challenges remain, it's a promising area of development within aerospace engineering.
Critical Insights How FMEA Implementation Reduced System Failures by 47% in Aerospace AI Applications During 2024 - Automated Monitoring Systems Cut Response Time to Critical Events by 39%
The adoption of automated monitoring systems has resulted in a 39% decrease in the time it takes to react to critical events. This improvement emphasizes the growing role these systems play in boosting efficiency across various industries, particularly in the aerospace sector. The implementation of Failure Mode and Effects Analysis (FMEA) in aerospace AI applications during 2024 has shown a related benefit: a 47% decrease in system failures. These improvements signify a move towards more proactive risk management and incident handling. However, it's noteworthy that, despite these improvements, the frequency of critical events hasn't actually decreased—in fact, it slightly rose after automated systems were introduced.
This rise in critical event occurrences raises questions about the ability of automated systems to effectively handle the complexities of the situations they are intended to manage. On the other hand, a positive trend can be observed in improved monitoring practices. Following the implementation of automated systems, the number of times critical records were consulted rose to 59% from 39%, suggesting a greater awareness and perhaps a better understanding of past critical events. This highlights the potential for continued improvements in safety protocols. However, the growing dependence on automated systems also necessitates caution. The accuracy of the data these systems use, along with the rigorous validation processes that underpin them, remain critical factors that demand ongoing scrutiny.
Automated monitoring systems have shown a 39% reduction in response times to critical events. This improvement can be attributed to several factors, including reduced human error. Instead of relying on manual reporting or quick human judgments, which can sometimes be flawed, these systems deliver accurate, continuous data processing. This means that critical events are addressed based on solid information, potentially leading to better decisions under pressure.
The shortened response time translates directly into faster mitigation strategies, especially vital during emergencies where every second counts. However, this system also brings about a greater need to integrate data from various sources. This integrated perspective yields a more comprehensive picture of the operational environment, providing a more detailed view of potential failures and a more holistic understanding of the contexts of those failures.
It's worth noting that automated systems need to be flexible to adjust to the dynamic conditions of the aerospace environment. This adaptive ability is crucial for quick responses to anomalies and unforeseen events. Naturally, these systems offer a benefit in cost efficiency. Because they lead to reduced downtime and enhanced efficiency, they can generate considerable savings on operational expenses, making such technology a potential cost-saving investment.
This predictive element allows engineers to shift from a reactive to a more proactive maintenance approach. Instead of simply waiting for failures to occur, we can anticipate potential problems and mitigate them before they turn into significant problems. The shift in focus to these systems also means a heightened focus on data quality assurance. Because the accuracy of the information is so critical, sensors and data sources must be meticulously calibrated. Any lapses in calibration can significantly hamper a system's effectiveness in reacting to critical events.
It's not just the machines that need to adapt. Operators must also receive specific training to understand the interfaces and analytical outputs of the monitoring systems. This training is critical to effectively interpret the data and respond to alerts. Further, automated monitoring shifts the operational culture towards continuous improvement. By focusing on real-time data analytics, organizations can prioritize proactive problem-solving, thus changing how safety practices are developed and executed.
The complex relationship of systems within aerospace also becomes more apparent in this automated world. Understanding the interdependencies of different components – not just failure points – can lead to insights for optimizing the whole system's reliability. In essence, the success of these systems highlights the complex nature of aerospace, suggesting there is always a need to understand these complexities and to adapt and improve based on ever-changing circumstances.
More Posts from aistructuralreview.com: