New Safety Protocols Hydrogen's 585°C Auto-Ignition Temperature in Structural Engineering
New Safety Protocols Hydrogen's 585°C Auto-Ignition Temperature in Structural Engineering - Understanding Hydrogen's 585°C Auto-Ignition Temperature
Hydrogen's 585°C auto-ignition temperature is a crucial factor in understanding its safety profile, particularly within the context of structural engineering. This temperature represents the point at which hydrogen ignites in air without an external spark, highlighting its relatively low ignition threshold when compared to fuels like methane. It's important to recognize that this temperature can fluctuate based on surrounding conditions, like pressure, underscoring the need for stringent safety measures in any structural designs utilizing hydrogen.
While the higher auto-ignition temperature can benefit certain engine designs, the exceptionally low energy needed to initiate hydrogen combustion poses significant safety challenges. This inherent volatility demands careful consideration in the development of structures and systems incorporating hydrogen. A comprehensive understanding of hydrogen's auto-ignition characteristics is therefore crucial to minimize the risk of incidents and ensure responsible integration of this energy source in structural engineering.
Hydrogen's 585°C auto-ignition temperature, while seemingly high, represents a critical safety parameter that engineers must fully grasp. It's the temperature at which hydrogen ignites on its own, without needing a spark or flame. While the value itself is relatively consistent, reported as around 585°C at atmospheric pressure, some variability exists, with ranges documented between 520°C and 585°C, depending on factors like the surrounding environment. Interestingly, even though it's higher than some other fuels like methane, hydrogen's ignition is significantly easier to trigger, due to its incredibly low minimum ignition energy. This lower energy requirement implies that much less external energy is needed to get it burning.
The concept of auto-ignition highlights a critical distinction; hydrogen doesn't simply ignite – it undergoes a time-dependent process, with an ignition delay period. It's not an immediate event. Though we know the temperature trigger, there's a brief period before the reaction speeds up significantly. Furthermore, even though moderate pressure changes don't drastically alter its auto-ignition temperature, other aspects like concentration or presence of catalysts can significantly impact the energy needed for ignition. It's worth noting that while 585°C might seem high in everyday terms, it is readily achievable within various industrial settings, especially processes involving heat, making cautious design practices essential. Considering hydrogen's unique characteristics when establishing safety protocols is paramount to avoid potentially severe consequences. Ultimately, recognizing the autoignition temperature as a cornerstone of safety procedures in hydrogen-related engineering systems is crucial for preventing accidents stemming from a lack of understanding of these ignition characteristics.
New Safety Protocols Hydrogen's 585°C Auto-Ignition Temperature in Structural Engineering - Comparison with Methane AIT in Structural Design
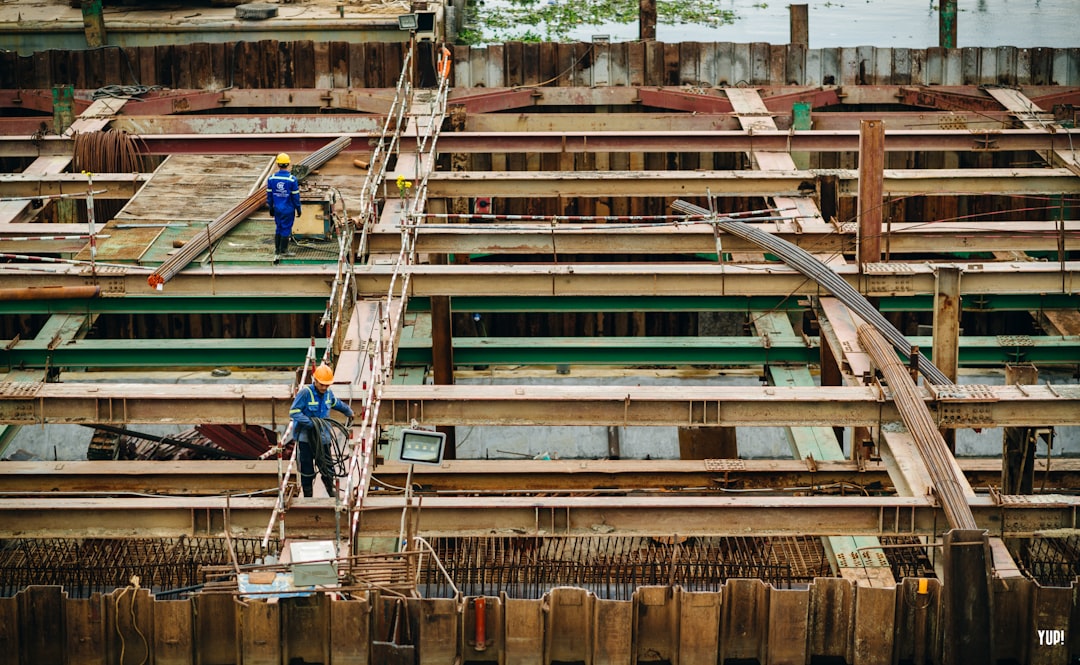
Hydrogen's auto-ignition temperature (AIT) of 520-585°C is notably lower than methane's AIT, which is around 600°C. This difference in ignition threshold has significant implications for structural design, as hydrogen presents a unique set of safety concerns. It's crucial for engineers to recognize that hydrogen ignites more easily, necessitating specific safety measures within any structure incorporating it.
Adding to the complexity is the fact that methane's AIT is sensitive to pressure changes. This means that the ignition temperature of methane can vary depending on the surrounding environment. This variable behavior isn't seen as strongly with hydrogen, but adds another facet to safety considerations. Beyond the lower AIT, hydrogen's high diffusion rate and extremely low ignition energy are important factors to consider. Hydrogen's rapid dispersal and the small amount of energy needed to initiate combustion introduce the potential for fast-spreading flames.
Effectively managing hydrogen's inherent flammability necessitates a clear understanding of these characteristics. The lower AIT compared to methane, coupled with the other factors mentioned, highlights the unique design challenges and safety protocols required when using hydrogen as a fuel or energy source in structural contexts. Thorough analysis of these factors is critical to minimize risks and ensure safe and responsible implementation of hydrogen in structures.
When comparing hydrogen's behavior to methane within a structural design context, several key differences emerge. While hydrogen's auto-ignition temperature (AIT) of 585°C is slightly lower than methane's (~600°C), its ignition energy is remarkably lower at about 0.02 mJ compared to methane's 0.28 mJ. This means hydrogen ignites much more readily, demanding careful consideration in structural designs.
Moreover, hydrogen boasts a significantly higher flame speed, reaching 2.3-3.0 m/s versus methane's 0.3-0.4 m/s. This translates to faster and potentially more intense combustion in confined spaces, thus impacting safety protocols. However, the AIT isn't static. It can shift based on factors like pressure and gas concentration, underscoring the need to consider these aspects during design.
Furthermore, hydrogen's combustion results in a higher heat release rate compared to methane, indicating a more rapid and significant temperature increase in fire scenarios. Structural designs must account for this higher risk. Additionally, hydrogen's extremely low density and high diffusion coefficient lead to rapid dispersion in the atmosphere. While this can aid in dilution, it also poses a risk of accumulation in confined spaces, requiring careful consideration of ventilation strategies.
The challenges don't end there. Hydrogen's flame is nearly invisible, making it difficult to detect and combat. Coupled with a broader flammable range (4-75% in air compared to methane's 5-15%), this highlights the need for robust safety systems and vigilant engineering design. Though hydrogen offers a higher energy content by weight, it presents a lower energy density by volume at standard conditions. This poses particular issues for storage and distribution in structures.
Interestingly, while pressure increases can enhance hydrogen's storage potential, they also increase safety complexity due to the heightened risk of ignition from potential leaks. The fact that hydrogen has a shorter ignition delay time under certain conditions emphasizes the need to thoroughly understand these dynamics when designing safety systems. It's also important to note that research continues on methods such as using artificial neural networks to better predict and understand AIT's contributions to flammability risk for hydrogen and other compounds. This area is especially critical for environmental impact assessments, as accurately predicting AIT is paramount for managing risks associated with potential accidents. The interplay of these factors makes hydrogen's safety profile quite distinct from that of methane and necessitates a comprehensive understanding of its unique characteristics to ensure safe implementation within the framework of structural engineering.
New Safety Protocols Hydrogen's 585°C Auto-Ignition Temperature in Structural Engineering - Low Ignition Energy Implications for Building Safety
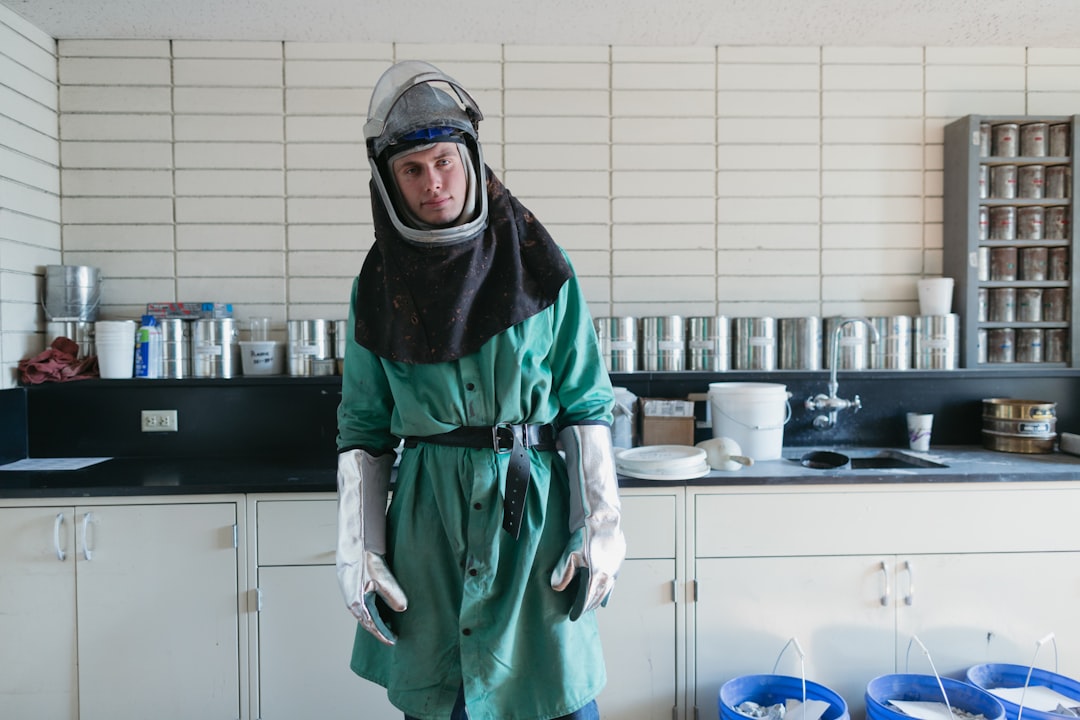
Hydrogen's remarkably low minimum ignition energy (MIE) of 0.02 millijoules makes it exceptionally easy to ignite, presenting a significant safety hurdle for building designs incorporating this fuel. This contrasts sharply with conventional fuels like hydrocarbons, which require substantially more energy to ignite. The ease with which hydrogen ignites, especially when considering its typical high-pressure storage (1000-1500 psi), significantly increases the potential for hazards. Adding another layer of complexity, hydrogen's auto-ignition temperature of 585°C, while seemingly high, combined with the low MIE, can lead to rapid and intense combustion, particularly in confined spaces.
Further complicating the safety picture are hydrogen's inherent characteristics. Its high diffusion rate and flame speed create challenges for engineers seeking to prevent accidents. As we move towards broader use of hydrogen in buildings, developing comprehensive safety protocols becomes critical. These protocols must be tailored to hydrogen's unique properties to ensure safe and reliable implementation without compromising building safety. The need to acknowledge and address these specific safety challenges is paramount as we navigate the integration of hydrogen into our built environment.
Hydrogen's ignition is remarkably easy to trigger, requiring only 0.02 millijoules (mJ) of energy, a value far lower than hydrocarbons like methane, which need about 0.28 mJ. This stark difference highlights the crucial need for heightened safety protocols in any structure utilizing hydrogen.
The speed at which hydrogen combusts is also a significant concern. Its flame can travel between 2.3 and 3.0 meters per second, a rate substantially faster than methane's 0.3 to 0.4 meters per second. This rapid combustion presents a greater risk of intense fires, especially within enclosed spaces.
While hydrogen's auto-ignition temperature (585°C) is seemingly high, it's not entirely fixed. Relatively minor shifts in the surrounding environment, such as pressure variations, hydrogen concentration, or the presence of certain catalysts, can dramatically alter this temperature, making hydrogen's safety profile more nuanced and complex.
Further adding to the safety challenges, hydrogen combustion produces a higher heat release rate compared to common fuels. This means a more rapid temperature increase during fire incidents, which structures must be designed to withstand without catastrophic failure.
The near-invisibility of hydrogen flames in daylight poses a significant obstacle for early detection. It forces a re-evaluation of standard fire safety protocols, necessitating innovative engineering solutions and specialized sensors for effective risk management.
The rapid diffusion of hydrogen into the atmosphere is another factor demanding careful consideration. While beneficial in open areas for dilution, this property also means that hydrogen can accumulate unnoticed in confined spaces, creating potential hazards.
Hydrogen's flammability range is significantly wider than that of methane, extending from 4% to 75% in air. This broad range requires extremely precise control systems and careful monitoring to maintain safe operating environments.
It's important to understand that the risk of ignition isn't solely dependent on temperature. The specific mixture of hydrogen and air also plays a crucial role. The possibility of explosive mixtures over a broad range of concentrations further complicates safety management in structural designs.
Excitingly, there's ongoing research into how machine learning might be used to predict how changes in the environment affect hydrogen's auto-ignition temperature. This area is a promising pathway towards developing more advanced, data-driven safety protocols for hydrogen-related technologies.
Finally, engineers must acknowledge the implications of hydrogen storage. Pressurization, while boosting storage capacity, introduces higher risks associated with potential leaks and subsequent ignition. Therefore, the design and continuous monitoring of storage systems are crucial for maintaining safety within any structure using hydrogen.
New Safety Protocols Hydrogen's 585°C Auto-Ignition Temperature in Structural Engineering - High Latent Heat of Combustion Considerations
Hydrogen's remarkably high latent heat of combustion, at 141.6 MJ/kg, underscores its potential as a potent energy source. However, this very characteristic presents major challenges, especially within structural engineering and safety protocols. The sheer energy released during hydrogen combustion is significantly higher than that of conventional fuels, demanding careful consideration of how structures and systems are designed and operated. The concern arises from hydrogen's relatively low auto-ignition temperature, at 585°C, coupled with an extremely low minimum ignition energy, making it exceptionally easy to ignite. This combination can lead to rapid and intense combustion, especially within confined spaces, if not properly controlled. Furthermore, hydrogen's high diffusion rate and tendency to form easily ignitable mixtures in enclosed environments necessitates the implementation of robust, hydrogen-specific safety protocols. As hydrogen adoption grows within energy infrastructure, a deep understanding of its combustion behavior and associated risks becomes increasingly vital for ensuring safe integration into structural design and applications.
Hydrogen's high energy content, while advantageous, presents a unique set of challenges due to its low density. This means that while it packs a lot of energy per unit of mass, it has significantly less energy per unit of volume compared to heavier fuels like gasoline or diesel. This characteristic makes storage and efficient application more complex and necessitates careful consideration in structural designs.
Hydrogen flames are known to be almost invisible in daylight, making it challenging to visually detect during fires. This poses a severe safety risk as early detection is crucial for swift mitigation. Consequently, relying solely on standard fire safety practices will be inadequate; engineers must explore the use of advanced detection and suppression technologies specifically designed for hydrogen.
Compared to fuels like methane, hydrogen burns at a dramatically faster rate, with flame speeds reaching 2.3 to 3.0 meters per second. This high velocity significantly increases the potential for rapid and intense combustion events, particularly within enclosed structures. Building designs must accommodate these flame characteristics and incorporate strategies to control or mitigate the risks associated with swift fire spread.
During combustion, hydrogen releases heat at a faster rate than many other fuels, leading to a more dramatic and abrupt temperature increase. Structures must be designed and constructed with materials capable of tolerating these higher temperatures to prevent catastrophic failures during fire incidents. Structural components like beams, columns, and protective layers need specific attention to avoid collapse due to intense heat.
The ease of igniting hydrogen, with a minimum ignition energy of only 0.02 millijoules, stands in stark contrast to other fuels. This incredibly low energy requirement means that accidental ignition can occur under various circumstances, including stray electrical sparks or even minor heat sources that would not ignite conventional fuels. This aspect underlines the importance of establishing very stringent safety protocols, including those related to electrical equipment and potential heat sources in hydrogen-related applications.
While often quoted as 585°C, hydrogen's auto-ignition temperature (AIT) is susceptible to variations in surrounding conditions. Pressure, the concentration of hydrogen in air, and the presence of certain materials, known as catalysts, can significantly influence the temperature at which hydrogen spontaneously ignites. This highlights the importance of continually monitoring operational conditions and designing safety systems that can adapt to these fluctuations.
Hydrogen has a remarkably broad flammable range compared to many other fuels, encompassing concentrations from 4% to 75% in air. This wide range means that ignition can occur over a much wider array of mixture ratios of hydrogen and air, expanding the possible scenarios that pose a risk of fire or explosion. For structural engineers, this signifies the importance of employing precise controls over gas concentrations in any system that incorporates hydrogen to avoid creating hazardous conditions.
Hydrogen's exceptionally high diffusion rate leads to rapid dispersion when released into open air, which can, in principle, dilute any concentrated hydrogen cloud and reduce the likelihood of a significant ignition event. However, in enclosed environments, this same rapid diffusion can lead to quick accumulation of hydrogen, especially in poorly ventilated areas. Therefore, ensuring that appropriate ventilation systems are incorporated into building designs is a critical aspect of safety in structural applications involving hydrogen.
Under certain conditions, hydrogen can undergo decomposition into simpler molecules before combustion, leading to a complex chain of chemical events that are difficult to predict. The formation of these intermediate products can influence the timing and characteristics of ignition, making it harder to fully anticipate its behavior during various scenarios. Further research is required to understand and model these dynamic decomposition pathways for improved safety protocols.
The application of machine learning is showing promise as a means of accurately predicting how environmental conditions like pressure and gas concentration will affect hydrogen's AIT. With the development of advanced AI algorithms trained on real-world data, it may become feasible to develop predictive safety systems capable of adapting in real-time to subtle changes in the surrounding environment, thereby offering more responsive and effective hydrogen safety solutions for structural engineering applications.
New Safety Protocols Hydrogen's 585°C Auto-Ignition Temperature in Structural Engineering - Cryogenic Properties and Storage Challenges
Hydrogen's utilization in structural engineering necessitates a deep understanding of its cryogenic properties and the challenges associated with storage at extremely low temperatures. Operating at temperatures as low as 77 Kelvin (-196°C) requires specialized materials like carbon fiber composites and aluminum liners to contain the hydrogen. However, the cyclical temperature variations that storage systems undergo pose a durability challenge, demanding research into materials that can withstand these extreme fluctuations. The production and maintenance of such cryogenic environments introduce complexities and significant cost factors that must be addressed by innovative engineering solutions. Furthermore, while high-pressure gaseous storage is a prevalent method due to its maturity and lower cost, it also presents safety challenges, particularly concerning temperature management. This is especially critical due to hydrogen's auto-ignition temperature of 585°C, necessitating strict safety measures within any structure incorporating it. The interplay between cryogenic properties and storage demands meticulous attention from engineers to develop safe and reliable hydrogen-based systems for structural applications.
Cryogenic hydrogen storage, operating at temperatures as low as -253°C (77 K), necessitates the use of specialized materials like resins, carbon fiber composites, aluminum, and stainless steel liners to withstand such extreme conditions. Maintaining these frigid temperatures presents a significant challenge, especially when considering the thermal stresses caused by the constant expansion and contraction of materials during operational cycles.
Storing hydrogen in its liquid form at cryogenic temperatures offers a higher density compared to gaseous storage, which is attractive for applications where space is limited, like spacecraft or certain industrial settings. However, this advantage comes with increased complexity in terms of handling, transport, and safety protocols. Maintaining the cryogenic state during transit and preventing rapid vaporization (boil-off) are key challenges, as the potential for pressure buildup within storage tanks is a serious concern.
One of the most striking properties of cryogenic hydrogen is its massive volume expansion upon warming to ambient conditions. It can expand roughly 800 times its original volume, which highlights the importance of robust pressure relief systems within storage tanks and transfer lines. If not accounted for, these sudden pressure spikes can pose significant risks during operational procedures.
The choice of materials in cryogenic systems is critical. Heat transfer, or the flow of thermal energy, can significantly impact the efficiency and effectiveness of these systems. Engineers must select materials that minimize heat flow while maintaining structural strength at extremely low temperatures. This balance between insulation and structural integrity is essential for achieving both efficient storage and long-term operational reliability.
Cryogenic hydrogen presents an intriguing aspect – ice formation. Exposure to even trace amounts of moisture can lead to the formation of ice within the storage or transport system, which can potentially cause blockages and impede operations. Maintaining very low humidity levels within the storage environment is crucial to prevent such incidents.
The extreme low temperatures used in cryogenic storage can cause embrittlement in some metals. This means that materials normally quite strong can become brittle and fracture easily at such cold temperatures. A thorough understanding of material properties at cryogenic conditions is required to choose the right materials for long-term durability and prevent structural failure in tanks and related equipment.
The specific heat capacity of liquid hydrogen, representing the amount of energy needed to raise its temperature, is comparatively low. While this might seem beneficial for reducing heating energy requirements, it demands careful consideration during system design to ensure that any heating needs are precisely managed.
Factors like surrounding temperature and atmospheric pressure can influence the evaporation rate of liquid hydrogen. Effectively managing these environmental influences is essential to optimize the storage and transfer processes. Engineers must ensure that their designs incorporate adaptability to these external conditions to ensure that cryogenic hydrogen remains in a stable, usable state.
Preventing accidents and managing potential risks associated with cryogenic hydrogen requires robust safety systems. Rapid leak detection and containment are of paramount importance. This is achieved through specialized sensors and automated shutdown protocols, all of which need to be designed to operate effectively in the extreme temperatures and pressures prevalent in these systems.
Liquid hydrogen is a compelling fuel source for rocketry and other aerospace applications because of its high energy content and low mass. However, the challenges of cryogenic storage and handling must be carefully addressed to ensure safe transportation and operation within these specialized environments, where failure is not an option. The future of this technology depends on developing systems and protocols that can reliably manage the complexities of extremely low-temperature environments.
New Safety Protocols Hydrogen's 585°C Auto-Ignition Temperature in Structural Engineering - Dispersion Characteristics in Structural Ventilation Systems
Within the realm of structural ventilation, understanding how hydrogen disperses is critical, especially in the event of a leak. Hydrogen's low molecular weight and rapid diffusion rate mean it can build up quickly in confined spaces, leading to potential safety issues. Research shows hydrogen concentrations can reach hazardous levels remarkably fast, making proper ventilation a key element of safety. The specific design of ventilation systems, including nozzle configurations and airflow patterns, significantly impacts how well hydrogen disperses. This emphasizes the need for systems tailored to specific scenarios to prevent excessive build-up and minimize the risk of a hazardous event. Further advancements in engineering and the use of computational modeling are promising paths toward developing safer structures that utilize hydrogen.
Hydrogen's rapid dispersal in still air, at a rate of 0.61 meters per second, is significantly faster than methane. This rapid movement means that the location of potentially ignitable hydrogen concentrations can change quickly within a building, posing a challenge for predicting and managing safety risks.
The range of hydrogen and air mixtures that can ignite is much wider than for methane, spanning 4% to 75% compared to methane's 5% to 15%. This broader range presents a greater variety of scenarios where an explosive environment can form, which adds complexity to the safety protocols needed during design.
When evaluating the thermal impact of hydrogen combustion on building components, it's crucial to remember that its flame temperature can surpass 2,000°C. This intense heat can cause rapid thermal fatigue in structural materials, often more rapidly than with other common fuels, making material selection and structural design very important.
Hydrogen's auto-ignition temperature isn't a fixed value. It can actually decrease in certain situations, such as when confined or mixed with other flammable substances. This sensitivity requires that safety protocols are adaptable and continually monitored within buildings where hydrogen is present.
A rapid release of hydrogen during an explosion can lead to a large fireball. This fireball can result in devastating structural damage, underscoring the need for engineers to focus on designing structures that can withstand potential overpressure effects.
When storing hydrogen at high pressure or during transfer, the venting of gas can create flammable clouds if not carefully managed. Engineers must create effective venting strategies that prevent the buildup of hydrogen in poorly ventilated areas of a building.
Hydrogen has the potential to cause embrittlement, particularly in high-strength steels and nickel alloys. Careful material selection is critical to prevent potential structural failures within storage or distribution systems, which could have disastrous consequences.
Since hydrogen flames are nearly invisible in daylight, standard flame detection systems may be ineffective. This necessitates the incorporation of advanced detection technologies, such as infrared sensors, into safety protocols to ensure a quick response in case of leaks or fires.
Interestingly, it's sometimes possible to identify hydrogen leaks through acoustic emission, which measures changes in sound waves due to gas flow. The integration of this technique into building monitoring systems could enhance real-time leak detection capabilities.
Due to the significant volume increase that hydrogen undergoes when it transitions from liquid to gas, the design of robust pressure relief systems is crucial. If these pressure changes are not managed effectively, dangerous situations could develop in confined spaces within buildings.
More Posts from aistructuralreview.com: