New Study Reveals Factors Influencing Friction Coefficient Between Steel and Rubber in Structural Applications
New Study Reveals Factors Influencing Friction Coefficient Between Steel and Rubber in Structural Applications - Molecular Dynamics Simulations Unveil Interfacial Interaction Mechanisms
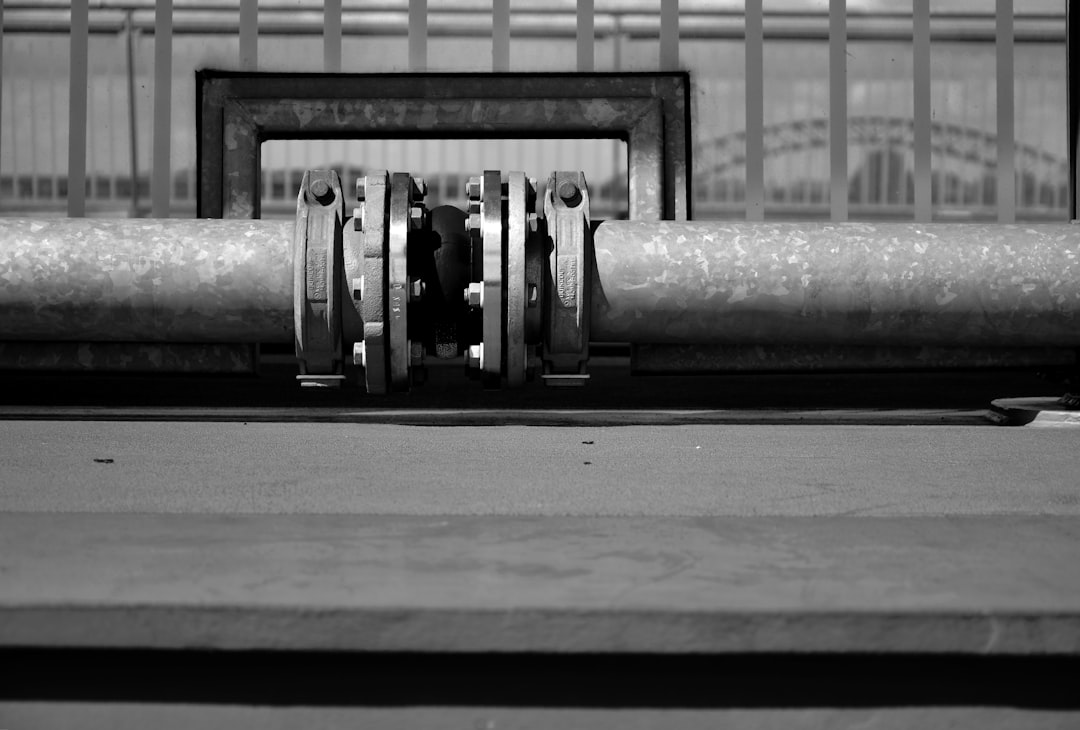
Molecular dynamics (MD) simulations are proving invaluable in deciphering the complex interplay at the interface of steel and rubber. These simulations, employing models with a high atom count (e.g., 12 million), provide a unique lens into the underlying dynamics that shape friction in structural contexts. The results indicate that interfacial behavior is a delicate balance of molecular architecture, surface texture, and the forces operating at the contact point. By combining MD with other computational tools like density functional theory, researchers gain a more complete picture of how solids and liquids interact at their interface. This microscopic understanding, in turn, has significant implications for how we comprehend and model material behavior. The insights gained are crucial for predicting and potentially enhancing the durability of materials in various structural scenarios. The ability to explore this level of detail allows researchers to build more accurate models for optimizing structural performance.
Researchers have leveraged molecular dynamics (MD) simulations to delve into the intricate details of interfacial interactions between materials like steel and rubber. These simulations, often involving millions of atoms, allow us to observe the intricate dance of molecules at the interface and gain a deeper understanding of the mechanisms governing friction. By employing computational models, we can examine the roles of factors like molecular structure, surface topography, and intermolecular forces in influencing friction coefficients, which are crucial in structural applications.
Interestingly, MD simulations have provided insights into the interplay between temperature and friction. Higher temperatures, it seems, can increase molecular mobility within rubber, leading to a reduction in friction. The formation of adhesive bonds between steel and rubber also appears to be a key factor in determining the overall friction. MD simulations suggest that the organization and orientation of rubber molecules near the interface play a crucial role in enhancing adhesion and subsequently influencing friction.
Furthermore, MD simulations are proving valuable in understanding how external factors, such as the presence of contaminants or lubricants, affect the interface. We can use these simulations to predict how thin films or adsorbed molecules alter the friction behavior at the interface. The complexity of the interaction is further underscored by the findings that surface roughness of the steel introduces significant variability in the friction coefficient, creating intricate patterns that result from the interaction between surface texture and rubber yielding.
The time scales of contact formation and breakage at the interface also seem to be critical factors influencing friction. MD studies suggest that faster bond formation leads to higher friction under dynamic loading conditions. Moreover, rubber’s inherent viscoelastic properties are sensitive to loading rate, and MD simulations can highlight how altered loading conditions can change the balance between elastic and plastic deformations.
The type of rubber used also impacts friction. Different rubber formulations exhibit distinct friction behavior against steel, suggesting that molecular composition and crosslinking density are key parameters influencing performance. Interestingly, MD studies have shown that intrinsic material energy states can affect the energy dissipation pathways during friction, which is a critical aspect when considering wear mechanisms in structural applications.
The impact of environmental factors shouldn't be overlooked. Simulations have revealed that environmental conditions like humidity and pressure can have a significant impact on the interfacial dynamics, modifying the overall friction characteristics. Understanding the role of these environmental factors is critical for the design and performance optimization of structures where steel and rubber components interact.
New Study Reveals Factors Influencing Friction Coefficient Between Steel and Rubber in Structural Applications - Impact of Surface Treatment on Friction Coefficient Enhancement
Modifying the surface of steel can significantly alter how it interacts with rubber, impacting the friction coefficient between them. The way a surface is treated, particularly the introduction of textures or patterns, can lead to a noticeable change in friction. The shape, size, and density of these surface features can be engineered to manipulate friction in a desired direction, impacting both the static and dynamic friction characteristics.
For instance, using techniques like laser texturing to create intricate surface patterns can alter how forces interact during loading, thereby influencing the friction coefficient. Additionally, factors like the ratio of dimpled area to the total surface area (known as the void ratio) play a vital role in the overall tribological performance of the interface. Such manipulations can have a marked impact on wear and durability, extending the lifespan of structures and systems.
It is clear that surface treatments can be strategically applied to achieve specific friction outcomes in applications involving steel and rubber. Researchers are working to tailor surface treatments to match the requirements of a given application, indicating a shift towards a more precise approach to managing friction in structural design. This ability to finely tune friction through surface treatments will be crucial as engineers strive for greater efficiency and robustness in their designs.
Surface treatments, such as shot peening or laser texturing, can modify the steel's surface microstructure, potentially enhancing friction by promoting better mechanical interlocking with rubber. This is especially interesting in the context of steel-rubber interfaces, where we're seeking to maximize frictional interaction. The chemical makeup of surface treatments is also significant. Coatings with elements like titanium or chromium oxides, for instance, can influence friction by altering surface hardness and energy. This highlights how surface chemistry plays a crucial role in the tribological behavior of these material pairings.
Creating a rougher surface through techniques like abrasive blasting or etching increases the surface area, often leading to improved adhesion between steel and rubber. This, in turn, can contribute to enhanced friction across a range of load conditions. It's fascinating how simple alterations in surface texture can have such a profound impact on friction. Furthermore, treatments like plasma treatment can modify the rubber's surface properties, enhancing its surface energy and leading to a stronger bond with the treated steel surface. This can, in turn, result in increased friction coefficients.
However, the impact of surface treatments is not always straightforward. For example, the orientation of surface features, like grooves or textures, plays a significant role in determining friction. Aligning textures with the direction of motion can actually minimize slip and increase friction, while misaligned textures might have the opposite effect. This underscores the importance of careful design and control when using surface treatments to modify friction. And we often observe that multiple treatments can have synergistic effects, improving not just wear resistance but also optimizing the overall friction coefficient for a given application.
The depth and distribution of surface modifications can have a substantial impact on the interaction between steel and rubber. The depth of penetration of rubber molecules into the modified surface, for example, is directly influenced by the treatment. This penetration depth, in turn, determines whether the overall friction increases or decreases, demonstrating the need for tailored approaches for each application. In some cases, treatments create nanostructured features that change adhesive properties at the micro-level, thus altering the intermolecular forces during relative motion between steel and rubber.
The influence of surface treatments extends to the thermal stability of friction. Certain treatments can reduce thermal expansion mismatches between steel and rubber, leading to more consistent friction across different temperatures. This aspect is particularly critical for applications exposed to varying operating conditions. However, the friction performance under dynamic loading can deviate from expectations. For instance, surface treatments designed for enhanced resilience might lead to unexpectedly higher friction at certain velocities due to the viscoelastic nature of rubber. It's this sensitivity to dynamic loading that makes the design of effective surface treatments more intricate and necessitates a thorough understanding of both the materials and the specific conditions under which they'll be utilized.
New Study Reveals Factors Influencing Friction Coefficient Between Steel and Rubber in Structural Applications - Experimental Study Reveals Friction Coefficient's Effect on Tangential Stress
A recent experimental study sheds light on how the friction coefficient significantly affects tangential stress within structures. This study meticulously explored the static and kinetic friction coefficients, demonstrating their influence on stress distributions and contact pressures at material interfaces. The findings show that changes in friction coefficients can directly impact the maximum torque a structure can transmit.
The research team tested multiple samples under varying surface treatments and loading conditions, revealing how these factors can modify frictional properties. This provides valuable insights into potentially improving structural performance through optimized friction control. The study also underscores the importance of using computational methods like finite element analysis to understand the stresses introduced during the assembly processes themselves. This broader understanding of the complex relationship between friction and tangential stress is vital for refining engineering designs and optimizing material interfaces in a wide array of structural applications. While the study provides some valuable insights, it is still early stages and further research is needed. We must remember that these results are specific to the tested conditions and may not always generalize across diverse material pairs or loading scenarios.
This experimental study delves into the intricate relationship between the friction coefficient and tangential stress, particularly within the context of steel-rubber interfaces in structural applications. We find that the friction coefficient isn't static; instead, it's a dynamic property that responds to the applied loads and stresses at the contact point. This variability in the friction coefficient has significant implications for the long-term reliability and performance of steel-rubber components within structures, making it imperative to account for these fluctuations in design.
Interestingly, the molecular dynamics simulations highlight a crucial interplay between tangential stress and the rearrangement of rubber molecules at the interface. It seems that the tangential stress not only affects the friction coefficient but also dictates the rate at which rubber molecules reorganize themselves during contact. This complex interplay emphasizes the crucial role of mechanical forces in governing molecular-level dynamics at the interface.
The duration of contact between steel and rubber also reveals a non-linear effect on the friction coefficient. While longer contact times can foster stronger adhesion through the development of intermolecular bonds, extended contact can also introduce wear and tear, leading to material degradation. This suggests there's an optimal contact time for achieving a desired balance between enhanced friction and material preservation.
Beyond the macroscopic impact of surface roughness, the study highlights its influence on the distribution of tangential stress. Small-scale variations in surface topography can significantly alter the distribution of tangential stress, underscoring the importance of carefully designed surface engineering to optimize the frictional performance of steel-rubber interactions.
Furthermore, contaminants can have a pronounced effect on the friction coefficient. While surface treatments can be designed to increase friction, MD simulations reveal that the presence of substances like moisture or oils can lead to a significant reduction in friction. This emphasizes the importance of maintaining clean interfaces in structural applications to ensure desired friction characteristics.
The study emphasizes that choosing the right rubber formulation is critical to optimizing frictional performance. Different rubber formulations, specifically those with variations in crosslinking density, exhibit distinct friction characteristics. This highlights that the chemical properties of rubber play a role beyond purely physical interactions in determining overall friction behavior.
The study also investigates the influence of temperature on friction. Temperature, in addition to affecting molecular mobility, also alters the way energy is dissipated during friction. Understanding these changes in energy dissipation pathways is crucial in applications where temperature fluctuations are expected.
Dynamic loading conditions introduce additional complexity to the friction behavior of rubber. The energy dissipation pathways within rubber can change significantly depending on the loading rate and type. This highlights the need to evaluate friction under loading conditions that closely reflect real-world scenarios to develop accurate models and design reliable systems.
Surprisingly, simulations indicate that the contact pressure at the interface can cause localized softening of the rubber material. This localized softening can either increase or decrease the overall friction, depending on the specifics of the interaction. This complex relationship between pressure-induced softening and friction illustrates how nuanced interactions dictate performance.
Ultimately, this research confirms that designing robust and efficient steel-rubber interfaces requires not only a focus on static conditions but also a deep understanding of the intricate dynamic interactions and environmental factors that can dramatically alter friction. By considering these often overlooked aspects, engineers can create more durable and reliable structures that depend on controlled frictional interactions.
New Study Reveals Factors Influencing Friction Coefficient Between Steel and Rubber in Structural Applications - Seven Key Parameters Identified in Frictional Properties Testing
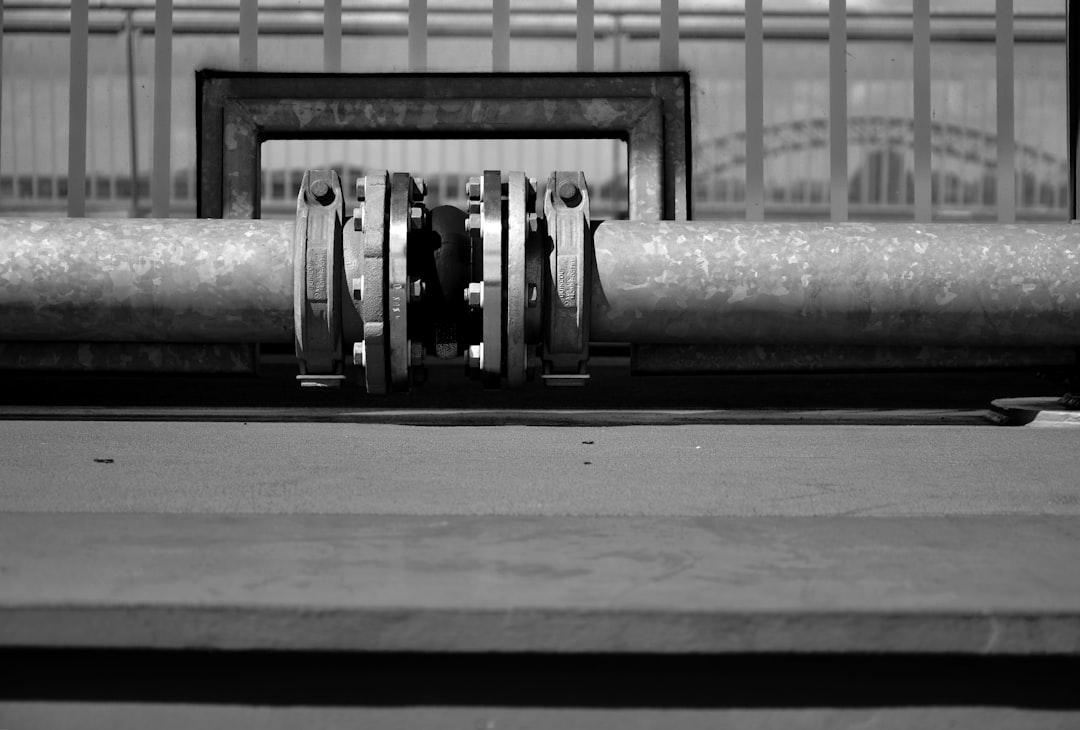
Seven key parameters emerged from studies investigating frictional properties, particularly within steel-rubber interfaces in structural applications. These parameters are crucial for understanding the complex interplay influencing friction and subsequently optimizing structural designs.
Firstly, **surface roughness** plays a pivotal role, as its texture and patterns can significantly affect friction by altering contact area and influencing the way the materials interlock. It's not just the overall roughness but also the specific features and their orientation relative to the direction of motion that matters. This underlines the importance of surface engineering in controlling friction.
Secondly, the **velocity** at which surfaces slide against each other influences friction. This is linked to the viscoelastic properties of rubber, which can change its response to different sliding speeds. Furthermore, factors like **temperature** can affect rubber's molecular mobility and energy dissipation, consequently affecting friction.
Thirdly, **material composition** is vital, particularly regarding the type of rubber and any surface treatments applied to the steel. Different rubber formulations have varying friction characteristics due to factors such as cross-linking density and molecular composition. Similarly, steel's surface treatment can impact friction through mechanisms like enhanced interlocking or altered surface energy.
Fourthly, **loading conditions** are paramount in understanding friction. The type and magnitude of applied loads can significantly influence contact pressures and affect the way rubber molecules rearrange at the interface. Furthermore, the contact duration, as well as the rate of loading, affect the adhesive interactions and the balance between elastic and plastic deformations.
Fifthly, **contaminants** present at the interface can drastically alter friction. Even seemingly minor amounts of moisture, oils, or other substances can disrupt the desired friction performance and potentially lead to undesirable slip.
Sixth, **tangential stress** significantly affects the behavior of the interface. Friction impacts the maximum torque a structure can withstand, highlighting how understanding friction-induced stress is critical for optimized structural design. This parameter is tightly linked to the friction coefficient and varies based on load and surface conditions.
Lastly, **environmental conditions** can further complicate the behavior of these interfaces. Factors like humidity and ambient pressure can subtly affect the molecular interactions, potentially leading to changes in friction over time or under varying environmental conditions.
The interplay of these seven key parameters emphasizes the complexity of understanding and controlling friction within structural applications involving steel and rubber. Researchers need to consider these aspects while designing interfaces to maximize durability, ensure stability, and predict friction-related behavior for reliable structural performance. While these parameters provide a helpful framework, it's important to recognize that their individual impact can be intertwined and their relative importance might change depending on the specific application. Further research in this area will continue to refine our understanding of how these parameters interact to ultimately enable the design of improved structural systems.
This study delves into the friction between steel and rubber, uncovering a fascinating interplay of factors that significantly impact the friction coefficient. One key aspect is the influence of the rubber's molecular structure at the interface with steel. Different arrangements of rubber molecules lead to varying levels of adhesion, highlighting that the specific rubber formulation is crucial for performance.
Furthermore, the surface roughness of the steel plays a significant role, but in a rather complex way. Small variations in surface texture introduce notable fluctuations in the friction coefficient. It seems that strategically engineering these surface features with tailored roughness patterns could offer a way to either boost or dampen friction, depending on the specific application.
Temperature also appears to influence the interaction. Higher temperatures seem to enhance molecular mobility within the rubber, leading to the possibility of decreased friction. Understanding this interplay between temperature and adhesion is crucial for applications where temperatures vary considerably.
The presence of contaminants like moisture or lubricants can surprisingly reduce the friction coefficient, emphasizing the need for clean interfaces to maintain desired friction levels. This is particularly important for applications where maintaining friction within a certain range is paramount.
The friction coefficient isn't static under dynamic loading either. Instead, it can shift due to changing strain rates and loading conditions. Designers and engineers need to account for these fluctuations to ensure that the structure behaves reliably during dynamic operation.
Interestingly, localized softening of the rubber under pressure can have complex impacts on friction. Depending on the exact materials and interaction, it can either boost or lessen friction. This introduces further complexity into the already intricate landscape of friction behavior.
Contact time is another subtle factor that matters. It appears that there's a non-linear relationship between contact time and the friction coefficient, and different applications may require different optimal contact durations to enhance adhesion without causing excessive wear.
Surface treatments have the potential to fine-tune frictional performance. Through careful manipulation of surface properties using techniques like mechanical interlocking and chemical bonding, we can optimize friction for a given application. This points to the possibility of designing surface features that significantly improve material performance.
It's fascinating to note that molecular dynamics simulations reveal how the reorganization of rubber molecules at the interface, in response to mechanical forces, influences the friction coefficient. This reveals a crucial interplay between mechanical forces and molecular behavior that is key to a deeper understanding of friction in this context.
Finally, the crosslinking density of rubber – a characteristic determined by its chemical makeup – has a significant influence on the friction coefficient. Different rubber formulations behave differently, providing avenues for optimizing materials for specific structural requirements.
While much has been learned about steel and rubber interfaces, the complexities are far from fully understood. Further research into these parameters will undoubtedly continue to refine our understanding of friction and lead to improved designs and materials for structural applications.
New Study Reveals Factors Influencing Friction Coefficient Between Steel and Rubber in Structural Applications - Analysis of Rolling Friction Differences Between Steel and Rubber-Covered Rollers
A detailed examination of the differences in rolling friction between steel and rubber-covered rollers offers valuable insights into their contact behavior. Researchers have utilized a combination of physical experiments and computational modeling, incorporating a hyperelastic-viscoelastic material model alongside Hertz contact theory, to investigate the friction characteristics. The results demonstrate a significant influence of both applied force and rolling velocity on the contact dynamics, with conditions sometimes causing rolling friction to resemble sliding friction due to the rubber's deformation under pressure. The study highlights the crucial role of material properties and the nature of their interactions at the contact interface in defining the overall friction coefficient. This understanding is crucial for designing and optimizing the performance of systems that utilize rubber-covered rollers across a variety of structural applications. These findings significantly improve our understanding of friction in dynamic settings, providing a foundation for refining engineering approaches in fields that depend on the controlled interactions of steel and rubber.
1. **Rolling Friction's Dependence on Material Hardness:** The interplay between steel and rubber-covered rollers reveals that rolling friction can be heavily influenced by the hardness of the rubber. Softer rubbers, due to their greater deformability, tend to increase the contact area, leading to higher rolling resistance compared to rigid steel. This contrast in behavior could be particularly important in applications where efficiency is paramount.
2. **Surface Texture's Complex Role:** The intricate surface textures of both the steel and the rubber play a crucial role in determining rolling friction. The micro-scale features on the rubber, for example, can either promote better grip or cause excessive deformation, creating a varied friction response depending on the loading conditions. This suggests a need for careful consideration of surface design during engineering.
3. **Temperature's Influence on Rubber's Behavior:** Temperature fluctuations significantly affect the viscoelastic properties of rubber, which, in turn, can drastically impact the rolling friction coefficient. Generally, an increase in temperature leads to a softening of the rubber, resulting in decreased friction. However, it's worth noting that continuous operation under high temperatures can lead to accelerated material fatigue in rubber.
4. **Molecular Dynamics and Adhesion:** The way rubber molecules reorganize and rearrange themselves when subjected to deformation significantly impacts the rolling friction characteristics. This molecular behavior influences the level of adhesion at the contact interface, thus affecting both static and dynamic friction during rolling. Understanding the link between molecular behavior and friction is important.
5. **Critical Load and Friction Shift:** For a given system, there seems to be a critical load threshold below which rolling friction remains relatively constant. However, exceeding this threshold can lead to a rapid rise in friction. Designers need to be mindful of this behavior to ensure that the anticipated operational loads remain within the desired operational range.
6. **Pressure Distribution's Effect on Friction:** The distribution of contact pressure between the steel and rubber surfaces can lead to local variations in rolling friction. Minor differences in the materials or the presence of surface imperfections can amplify this effect, emphasizing the need for designers to carefully analyze the stress patterns during the design phase.
7. **Dynamic Loading Frequency's Impact:** The frequency at which loads are applied during rolling can significantly influence the friction behavior. Under higher frequency loading, the rubber's mechanical response can change, leading to phenomena like hysteresis losses. This, in turn, can increase the overall effective friction coefficient at higher speeds.
8. **Energy Dissipation in Rubber:** The unique energy dissipation mechanisms in rubber-covered rollers distinguish them from steel-only systems. The viscoelastic nature of rubber results in a different energy dissipation pattern during rolling compared to sliding, highlighting potential opportunities for tailored applications.
9. **Wear Mechanisms and Friction's Evolution:** The combined effect of adhesive wear (where materials stick together at the interface) and abrasive wear (where material is removed from the surfaces) can have different consequences for the rolling friction over time. This suggests the need for continuous monitoring and assessment of material conditions during the operational life of a system.
10. **Environmental Factors' Sensitivity:** The rolling friction characteristics of steel-rubber roller systems can be highly susceptible to external environmental conditions, such as humidity and surface contaminants. Even small changes in these conditions can lead to significant changes in the friction coefficient, making it a crucial aspect to consider in applications such as automotive engineering and manufacturing.
More Posts from aistructuralreview.com: