Comparative Analysis Strength-to-Weight Ratio of Lightweight vs Normal Weight Concrete in Modern Structures
Comparative Analysis Strength-to-Weight Ratio of Lightweight vs Normal Weight Concrete in Modern Structures - Density Comparison LWC vs NWC

The density difference between Lightweight Concrete (LWC) and Normal Weight Concrete (NWC) is a defining characteristic. While NWC typically weighs in at around 2400 kg/m³, LWC exhibits a significantly lower density, ranging from 1400 kg/m³ to 2000 kg/m³. This density reduction is primarily due to the integration of lightweight aggregates into the concrete mix. Interestingly, this use of lighter materials doesn't necessarily compromise structural strength. In fact, when engineered properly, LWC can achieve strength comparable to NWC, especially when utilizing recycled or waste materials as part of the aggregate.
The development of High-Strength Lightweight Concrete (HSLWC) underscores a trend towards pushing the boundaries of LWC. This advanced material type offers a combination of low density with enhanced characteristics like superior durability, better thermal insulation, and improved resistance to fire. Although LWC's mechanical response differs from NWC under stress, specifically in its stress-strain behavior, these differences can potentially be advantageous for certain structural designs. In conclusion, LWC's advantageous strength-to-weight ratio presents a compelling case for its wider adoption in construction, leading to the potential for lighter and more efficient structural components in contemporary buildings.
When comparing the density of Lightweight Concrete (LWC) and Normal Weight Concrete (NWC), a notable difference emerges. LWC, achieved by incorporating lightweight aggregates, exhibits a density ranging from roughly 1400 to 2000 kg/m³, while NWC typically falls around 2400 kg/m³. This density reduction is a key characteristic that can influence the design and performance of concrete structures.
Interestingly, achieving similar strength levels to NWC with LWC is possible through careful selection of lightweight aggregates, including waste materials when appropriate. This has led to the development of high-strength lightweight concrete (HSLWC), promising a blend of low density, high strength, and enhanced durability. It's also worth noting the potential benefits in thermal insulation and fire resistance offered by HSLWC compared to NWC, although further research is always needed to confirm performance in diverse conditions.
The lighter nature of LWC significantly reduces the self-weight of structural components, presenting advantages in applications where minimizing weight is paramount. However, engineers must understand that the mechanical behavior under bending can differ from NWC, particularly in stress-strain relationships and deformation capabilities. While compressive strength tests have shown LWC can achieve comparable strength to NWC, a meticulous design approach is required.
Research efforts, such as those evaluating the long-term behavior of lightweight aggregate concretes (LWAC) under various environmental conditions, are crucial to fully understanding the implications of LWC use in diverse climates. These investigations aim to clarify the durability aspects and strength development over time, particularly in demanding conditions like coastal environments. Ultimately, the promising strength-to-weight ratio and the potential to reduce overall building material quantities make LWC an intriguing avenue to explore in future structural designs, but only if its long-term performance can be assured across a wider variety of application conditions.
Comparative Analysis Strength-to-Weight Ratio of Lightweight vs Normal Weight Concrete in Modern Structures - Impact on Structural Design and Dead Load
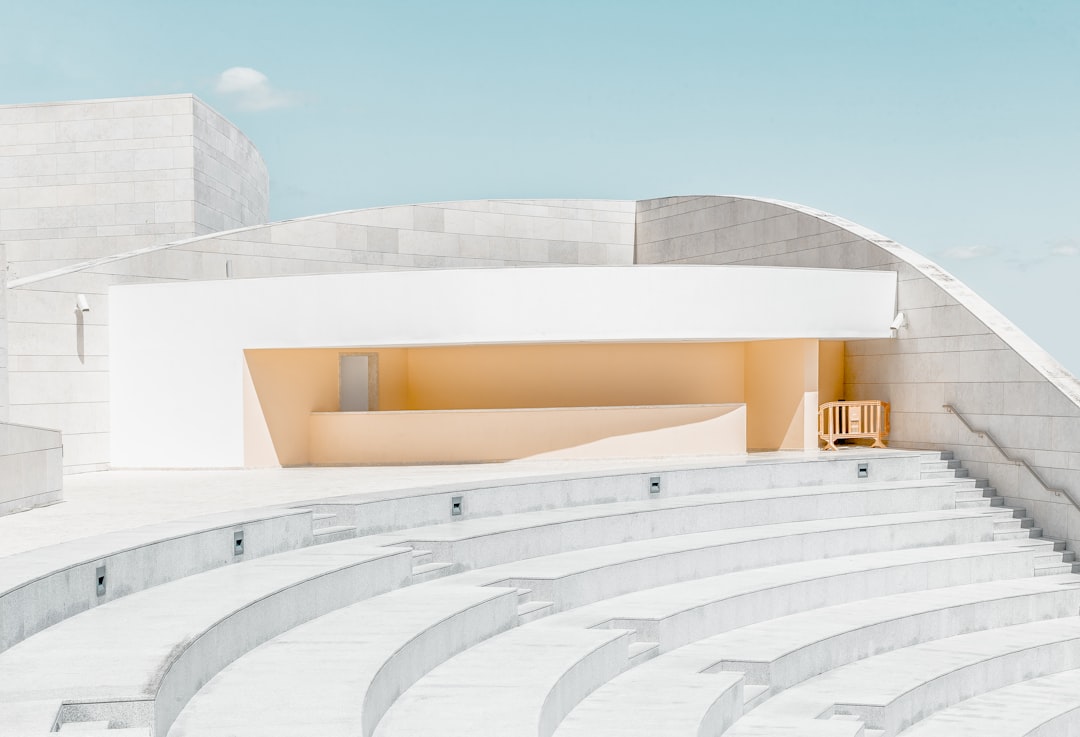
The use of lightweight concrete (LWC) significantly alters structural design considerations, primarily because of its impact on dead load. Since LWC has a density roughly half that of normal weight concrete (NWC), ranging from 1400 to 2000 kg/m³ versus NWC's 2400 kg/m³, structural elements can be lighter and smaller. This translates into decreased loads on beams, slabs, and foundations, often requiring less reinforcing steel. The reduced dead load from LWC is especially beneficial in seismic zones, where the lighter weight of the building lessens the impact of earthquake forces. Further, integrating LWC into composite structures like sandwich panels demonstrates its flexibility in optimizing structural performance by combining material properties. It's worth noting, though, that using LWC might mean needing more cement to achieve the target strength, which can complicate the design process and requires careful planning to maximize the advantages of weight reduction while addressing material trade-offs.
The decreased self-weight of Lightweight Concrete (LWC), typically ranging from 1400 to 2000 kg/m³ compared to Normal Weight Concrete's (NWC) 2400 to 2500 kg/m³, significantly impacts structural design by reducing dead loads. This reduction can translate to smaller, less massive beams and columns, potentially leading to lower construction costs, especially for foundations.
Furthermore, in tall buildings, the reduced mass of LWC structures could potentially lessen the impact of seismic forces during earthquakes, potentially enhancing their overall performance. However, the inherent differences in dead loads between LWC and NWC necessitate a thorough design approach. Lighter structures might enable longer spans and less material usage, yet they also require careful consideration of how loads are transferred and how lateral stability is maintained.
The lighter aggregates in LWC can influence thermal performance, potentially reducing the overall thermal mass of a building. This can impact energy efficiency but also alters how heat is distributed and retained within a structure, requiring a different perspective during design. It's worth noting that while High-Strength Lightweight Concrete (HSLWC) can achieve high strength, its modulus of elasticity can sometimes be lower than NWC, which influences the way deformation under load is managed during design.
While reducing dead load is clearly beneficial, relying on LWC without a deep understanding of its long-term behavior under various loading conditions can potentially lead to unexpected deflections or problems with how the structure performs over time. The vibrational properties of LWC structures are also altered, which can improve performance in cases where dynamic loading is a concern. However, engineers must adopt new strategies in their vibration analyses when designing with LWC.
LWC's lighter weight can potentially enable more inventive architectural designs, with thinner structural elements. However, this necessitates rigorous analyses of the structure's integrity to ensure that it can safely handle unexpected loading patterns. The chemical interactions between different lightweight aggregates and cement can differ significantly from traditional mixes, so a cautious approach to mix design is crucial. Extensive testing is required to confirm compatibility and performance.
The reduced weight can introduce a design challenge – balancing stability and load distribution. Lighter structures might be more susceptible to issues with stability and how loads are distributed, potentially requiring sophisticated modeling to verify the performance of all components under expected loading. It's clear that despite the many potential advantages, LWC necessitates a nuanced approach to design, analysis, and material selection to fully exploit its benefits. Ongoing research into the long-term performance of LWC in varied climates and under differing conditions is needed to fully understand its implications for future construction practices.
Comparative Analysis Strength-to-Weight Ratio of Lightweight vs Normal Weight Concrete in Modern Structures - Strength-to-Weight Ratio Analysis
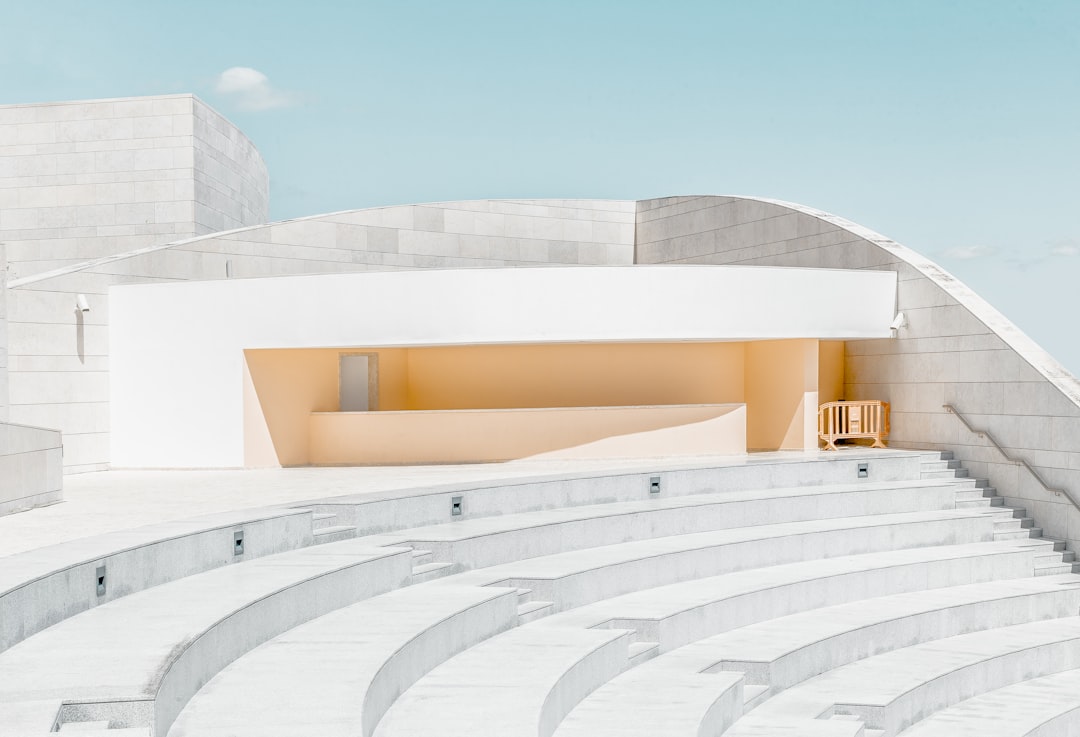
Understanding the strength-to-weight ratio is vital for making informed decisions in structural design, especially when choosing between concrete types. Lightweight concrete (LWC) stands out because it generally has a better strength-to-weight ratio than normal weight concrete (NWC). This benefit comes from using lighter aggregates in the concrete mix. The lighter weight of LWC leads to reduced loads on the structure, which can result in smaller, less massive components and potentially lower material costs. There are also potential benefits in areas like energy efficiency and seismic performance due to the lower mass.
However, the advantages of LWC don't come without challenges. The way it behaves under load is different, and the long-term durability of different types of lightweight aggregates can vary under different conditions. Engineers have to carefully balance the potential benefits of lower weight with the need to ensure the structural integrity and long-term performance of any design using LWC. Ultimately, the use of LWC needs to be thoughtfully considered within the context of a particular project and its specific requirements. It's a matter of understanding the material's unique characteristics and properly incorporating those characteristics into the design process.
Lightweight concrete (LWC) presents a unique stress-strain profile compared to its normal weight counterpart (NWC). While compressive strength can be similar, the increased flexibility of LWC might influence how structures behave when subjected to dynamic forces, leading to different deformation patterns under loads. Interestingly, LWC can sometimes exhibit a 20% improvement in strength-to-weight ratio compared to NWC, when proper aggregate selection is applied. This suggests that LWC could be a viable solution for structural components that need to carry considerable loads without adding significant dead weight. However, understanding these specific stress-strain curves and how loads are transferred through the concrete under these conditions is critical in structural design.
LWC also stands out in its lower thermal conductivity, compared to NWC, meaning it can offer improved thermal insulation within building elements. This attribute can influence the overall energy performance of a structure and needs to be taken into consideration during the design process. While seemingly beneficial, there are potential complications. For instance, LWC often gains a large percentage of its ultimate strength in a shorter timeframe than NWC. While this could be useful for certain projects with tight construction schedules, it also necessitates a very precise understanding of the material during the early stages of the build.
Furthermore, LWC's shear strength can sometimes be a challenge, particularly at lower densities. Engineers must carefully consider if extra reinforcement might be needed to meet safety requirements in crucial applications. This challenge highlights the significance of the size and type of lightweight aggregates used in LWC. Finer aggregates can produce smoother finishes, which is aesthetically appealing, yet can impact compressive strength if not managed properly.
Ongoing research is focused on better understanding the long-term properties of LWC, specifically concerning its resilience to water absorption and temperature changes. These are critical factors affecting its performance over time, especially given the increased drying shrinkage observed in LWC relative to NWC. These considerations are essential for ensuring a structure's longevity. This understanding is vital because LWC is a very versatile material, suitable not only for structural applications but also in precast components and decorative elements within the building design itself.
However, when we consider strain capacity, this is often significantly different in LWC than NWC. This difference can cause unexpected behavior in service conditions. For engineers to achieve the best possible design with LWC, a careful assessment of strain and potential deflections under a range of potential conditions needs to be completed. Understanding these complexities and how they impact the structure's overall integrity throughout its lifetime is important. These are all considerations that researchers and engineers need to account for when working with lightweight concrete.
Comparative Analysis Strength-to-Weight Ratio of Lightweight vs Normal Weight Concrete in Modern Structures - Production Methods for Lightweight Concrete
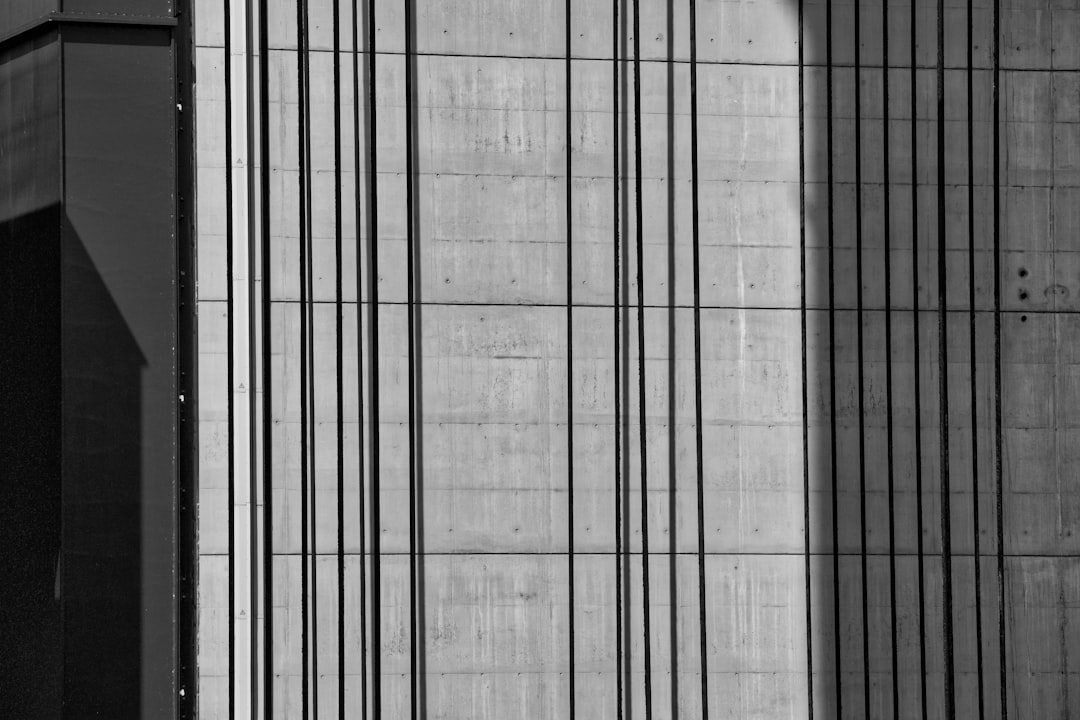
Lightweight concrete (LWC) production relies on a few key methods to achieve its reduced weight while retaining sufficient strength. One common approach is the use of lightweight aggregates. These materials, like expanded clay, shale, or even volcanic rock like pumice, replace some or all of the traditional, heavier aggregates used in normal weight concrete. The choice of lightweight aggregate significantly affects the properties of the resulting concrete, impacting both its strength and how it holds up over time.
Another way to create LWC is by incorporating chemical "expanding agents" directly into the concrete mix. These agents generate tiny air bubbles within the concrete, essentially creating a foam-like structure that reduces overall density. However, the creation of these air voids can alter other properties, for instance, influencing the way the concrete handles stresses and strains. The size and shape of the lightweight aggregates and the efficiency of the expanding agents are crucial factors in determining how well the LWC will perform in a structural setting.
Current efforts in LWC production focus on improving the strength and overall durability of the concrete while preserving its key advantage: a favorable strength-to-weight ratio. The specific properties of each production method and aggregate type are highly relevant to meeting design requirements and performance expectations in a wide array of building applications. As LWC finds more use in contemporary buildings and structures, researchers are exploring improved production techniques to address questions regarding long-term durability and structural integrity, particularly under diverse climate conditions and loads. This research and development aim to push the limits of what can be achieved with LWC in construction, making it an even more viable alternative in modern building design.
Lightweight concrete (LWC), with its density typically ranging from 1400 to 2000 kg/m³, offers a compelling alternative to traditional normal weight concrete (NWC) which weighs in at about 2400 to 2500 kg/m³. This weight reduction stems from the use of various lightweight aggregates like expanded clay, pumice, or even recycled materials such as expanded polystyrene (EPS). The ability to tailor properties using a wide range of aggregates can be beneficial for streamlining material procurement and logistics in certain construction situations.
Interestingly, some high-strength LWC mixes can rival the compressive strength of NWC, with values exceeding 50 MPa in some cases. This challenges the common assumption that lighter materials necessarily imply a compromise in structural integrity. The specific size and grading of the lightweight aggregates play a crucial role in determining the concrete's workability and performance. For instance, using finer aggregates can lead to smoother surfaces, enhancing aesthetics, but may also reduce strength if not carefully managed during the mixing process.
Beyond structural performance, LWC exhibits lower thermal conductivity compared to NWC, making it attractive for energy-efficient buildings. This reduced thermal conductivity fundamentally alters the way heat is stored and released within a structure, which needs to be accounted for in energy models used in building design. Additionally, LWC shows a distinctive stress-strain behavior compared to NWC, especially under tension, where it demonstrates higher deformability. This characteristic could prove beneficial in earthquake-prone regions as it allows the structure to absorb more energy before failure, offering a potentially more resilient approach to building design in such contexts.
One aspect to consider with LWC is its rapid strength gain. Unlike NWC, LWC can reach a significant portion of its ultimate strength remarkably quickly, as much as 90% within the first two weeks. This rapid hardening can accelerate construction timelines but requires careful handling during early stages to avoid premature application of loads. Furthermore, the reduced weight of LWC unlocks design possibilities that were not previously feasible. Thinner structural elements become possible, opening doors for innovative architectural designs. However, rigorous structural analyses are essential to ensure the integrity and stability of these lighter structures.
Researchers have observed an increased tendency towards drying shrinkage in LWC compared to NWC, leading to a greater likelihood of cracking, especially in environments where moisture fluctuations are common. This heightened risk of cracking is a factor that must be incorporated into the design process. Achieving the desired performance with LWC mixes can be more involved than with NWC due to the diverse interactions between aggregates and cementitious materials. Experimentation with different mix designs is typically required, adding complexity to the design process.
Lastly, the altered mass characteristics of LWC result in different vibration responses compared to NWC. Engineers need to revise their analytical models to correctly capture these changes. This could involve refining damping strategies for buildings designed for higher performance under dynamic loads. The interplay of all these factors – rapid strength gain, shrinkage tendencies, design complexities, and vibrational characteristics – underscores the importance of a thorough understanding of LWC's behavior for successful applications in modern structures. Ultimately, although promising, LWC necessitates a meticulous design approach, rigorous testing, and a deep understanding of its intricacies to maximize its benefits in diverse construction scenarios.
Comparative Analysis Strength-to-Weight Ratio of Lightweight vs Normal Weight Concrete in Modern Structures - Seismic Performance Advantages
Lightweight concrete (LWC) offers several benefits when it comes to seismic performance in modern structures. Its reduced mass, compared to normal weight concrete, significantly lessens the overall seismic loads a building experiences during an earthquake. This translates to potentially less damage and improved structural integrity during seismic events. Additionally, LWC exhibits lower variations in bending moments and shear forces under earthquake-like conditions. These characteristics, along with its ability to absorb more energy before failure, suggest LWC structures might be more resistant to seismic forces.
The lower weight of LWC also makes it an attractive material for structures in areas with low seismic activity, where lighter buildings might be preferred for economic or architectural reasons. Moreover, innovative techniques like retrofitting existing structures with LWC and using materials like carbon fiber fabrics to strengthen these buildings show promising improvements in seismic resilience. However, the differences in material properties compared to traditional concrete, like elastic modulus and shear strength, necessitate careful design and analysis during seismic engineering. A thorough understanding of these nuances is crucial to ensure the advantages of LWC are fully leveraged and potential risks are mitigated when utilizing it in seismic design.
Studies have shown that lightweight concrete (LWC) can potentially offer advantages in seismic performance compared to normal weight concrete (NWC) due to its lower mass. This reduced mass, resulting from the use of lightweight aggregates, leads to a decrease in inertial forces that act on a structure during an earthquake, potentially enhancing energy dissipation. The resulting change in the structure's fundamental period of vibration can also improve how a building reacts to seismic waves, potentially reducing the resonance effects that can amplify earthquake damage.
While LWC demonstrates a different stress-strain response compared to NWC, this difference can translate to improved flexibility, allowing structures to deform more under seismic loads without necessarily causing immediate structural failure. The lower weight of LWC structures also minimizes the overturning moment during an earthquake, which is particularly important for the stability of taller structures. It's interesting to note that some research suggests LWC may achieve higher load factors in seismic design, suggesting a potential to better withstand dynamic loading.
The decreased dead load of LWC translates to lower lateral loads during earthquakes and wind events, which can lead to more efficient and smaller structural elements without sacrificing safety. This also lessens stress on the building's foundation, potentially simplifying the design and potentially lowering costs. There's evidence that LWC might have some inherent resistance to critical cracking because of its deformation characteristics under stress. The porous nature of certain LWC aggregates might also offer better moisture management than NWC, contributing to better long-term performance and resilience during seismic events.
The versatility of LWC is also an important consideration. Engineers have the ability to customize the mixture during production, potentially tailoring it for improved seismic resistance by integrating specific additives that enhance the concrete's strength or ductility. It's crucial to consider, though, that these observations are still subject to further testing and deeper research to understand the full range of LWC's potential in seismic applications. This field is dynamic, with research continuously uncovering new aspects of LWC and how it performs in a range of conditions. It remains to be seen how effectively these potential benefits translate to real-world scenarios and how design codes will evolve to fully leverage these characteristics.
Comparative Analysis Strength-to-Weight Ratio of Lightweight vs Normal Weight Concrete in Modern Structures - Bond Behavior and Design Code Considerations
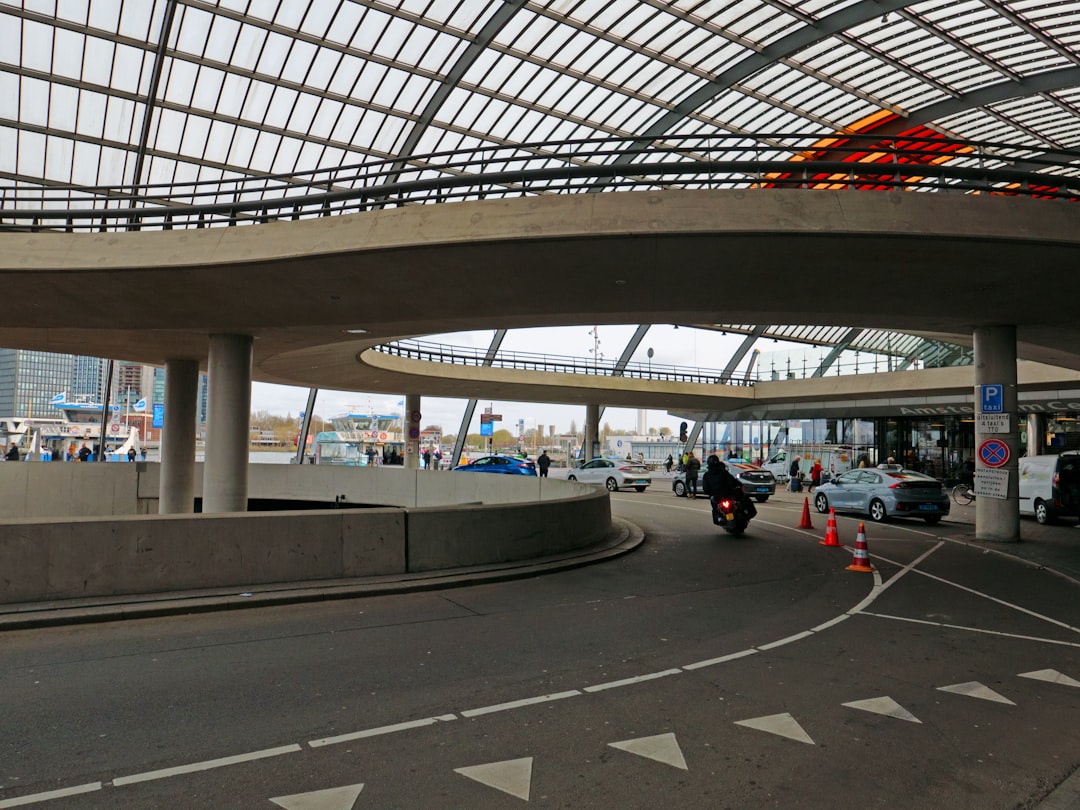
The connection between reinforcing steel and concrete, referred to as bond behavior, plays a significant role in how concrete structures perform, especially when considering the differences between lightweight concrete (LWC) and normal weight concrete (NWC). The way the reinforcing steel interacts with the concrete influences the overall behavior of the structure and can significantly impact its safety and integrity.
Current design standards, however, may not fully capture the bond strength characteristics of LWC, particularly for high-strength mixtures. This suggests that design codes might be underestimating the bond strength in certain situations. Understanding the factors that affect bond strength in concrete is important for safe and successful designs. These factors include the texture of the reinforcement bars and the characteristics of the concrete itself (like the type of LWC being used).
As LWC becomes a more commonly used material in modern structures, the need to evaluate and potentially modify current building codes to address the unique bond behaviors of LWC becomes crucial. Engineers need to ensure that designs meet all safety standards while effectively leveraging the advantages offered by lightweight concrete. A thorough understanding of bond strength in LWC is essential to both optimize design and minimize the risk of bond failure in structures.
Lightweight concrete (LWC), with its lower density achieved through the use of lightweight aggregates, presents interesting challenges and opportunities when considering bond behavior in reinforced concrete structures. The bond between concrete and reinforcing steel is fundamental for structural integrity, but the properties of LWC, notably its altered stress-strain response and different thermal expansion characteristics compared to normal weight concrete (NWC), can significantly influence this bond strength.
The type of lightweight aggregate used plays a major role in how well the concrete bonds to the steel. Some aggregates might not provide the ideal surface texture for strong mechanical interlock, leading to potential reductions in bond strength relative to traditional aggregates in NWC. Careful selection and testing of aggregate types are therefore crucial for LWC design.
Moreover, the interface between the LWC and the reinforcement can experience differing shrinkage and thermal expansion behaviors, potentially leading to bond degradation over time. This highlights the importance of considering local environmental conditions and adjusting mix designs to mitigate these effects. It's also important to note that current design codes are often based on NWC properties, making it difficult to directly apply these standards to LWC applications. Engineers often need to adapt existing guidelines creatively, or even develop entirely new ones, to account for LWC's unique properties like bond stress and shear capacity, especially in high-strength LWC mixes.
Interestingly, the size and shape of lightweight aggregates can also affect the bond behavior. Finer aggregates can sometimes enhance bond strength due to an increase in surface area contact, potentially providing a better mechanical interlock, while larger aggregates might introduce weak points in the bond due to the uneven surface texture.
During construction, it's crucial to ensure the reinforcement is accurately placed and secured without jeopardizing the bond. The lower density of LWC can sometimes result in variations in compaction, requiring stricter construction procedures to maintain bond integrity and prevent voids or weak spots around the rebar.
Temperature fluctuations during the curing process can also have a noticeable impact on LWC bond strength. Elevated temperatures can significantly impact the hydration process and concrete properties. Therefore, it's vital for engineers to manage curing temperatures carefully to prevent any negative consequences on bond strength and overall LWC performance.
Traditional bond strength tests sometimes fall short in fully capturing the complex interactions found in LWC. Newer testing methods, such as those based on non-destructive evaluation techniques, are actively being developed to better understand the behavior of LWC and steel interaction.
The lower mass and unique stress-strain response of LWC can change the stress distribution within structural components, affecting both the flexural and shear capacities of the concrete. Designs must be able to accommodate these shifts in stress patterns to maintain safety and ensure satisfactory performance.
External environmental factors, like fluctuations in humidity and temperature over time, can have a significant impact on bond performance in LWC. Engineers need to consider these influences when developing designs to ensure that the expected performance is maintained across various weather conditions and over the long-term.
Lastly, incorporating different chemical admixtures to enhance LWC properties may unintentionally alter the bond behavior. Careful consideration must be given to the interaction between these admixtures and lightweight aggregates to maintain optimal bonding conditions and prevent any compromise in overall structural integrity.
These intricacies reveal the importance of conducting thorough research and development into bond behavior in LWC. Understanding these complexities is vital for refining design standards and construction practices. While LWC presents many exciting advantages for various applications, a comprehensive and rigorous understanding of its bond behavior under different conditions is crucial for its successful and safe implementation in a wide range of structural designs.
More Posts from aistructuralreview.com: