New Study Reveals Key Factors Influencing Concrete's 50-100 Year Lifespan
New Study Reveals Key Factors Influencing Concrete's 50-100 Year Lifespan - Chemical Composition Impact on Concrete Longevity
The chemical makeup of concrete profoundly affects its lifespan and performance. Variations in the proportions of oxides like magnesium oxide (MgO), aluminum oxide (Al₂O₃), and silicon dioxide (SiO₂), among others, directly influence crucial properties such as the time it takes for the concrete to set and its ultimate strength. These properties are foundational to ensuring structures endure over time. Utilizing supplementary materials, such as Class C and Class F fly ash, during the concrete mixing process can positively impact both durability and the environmental footprint of concrete production by reducing carbon dioxide emissions. It's crucial to understand how certain chemical components influence the degradation processes that contribute to concrete deterioration. This knowledge allows us to develop strategies for bolstering concrete's resistance to these processes, leading to more sustainable practices that ultimately extend the service life of concrete infrastructure. Further research into historical materials, particularly the remarkably durable Roman concrete, might reveal insights applicable to modern concrete production, possibly informing new approaches to extend the longevity of concrete structures.
The chemical makeup of cement itself plays a significant role in the overall performance and longevity of concrete. For example, a higher concentration of tricalcium aluminate (C3A) can make concrete more vulnerable to sulfate attack, potentially accelerating deterioration. Maintaining a concrete environment with a pH above 13 is crucial for protecting embedded steel reinforcement. This high pH helps keep the steel in a passive state, preventing corrosion that can compromise the structure over time.
The emergence of alternative cementitious materials, such as fly ash and slag, presents promising possibilities for improving both the short-term and long-term strength of concrete. These materials can also influence the pore structure, making the concrete less susceptible to water ingress and freeze-thaw damage. The extent to which cement hydrates influences its long-term strength development. The presence of unhydrated cement particles, which can persist for many years, might impact durability if their use is not optimized.
Certain types of silica aggregates can initiate an alkali-silica reaction (ASR), leading to expansion and cracking. Using low-alkali cement can help mitigate this, emphasizing the importance of carefully selecting materials. The addition of fiber reinforcement, like steel or polypropylene fibers, can change the way cracks propagate within the concrete, thus improving the overall durability, especially under tensile loads common in many structural applications.
The water-to-cement ratio is a crucial factor, as higher ratios (above 0.5) contribute to a more porous concrete structure. This can lead to quicker degradation due to environmental exposure and shorten the structure's projected lifespan. The incorporation of chemical admixtures can noticeably alter the concrete's microstructure. For example, superplasticizers increase workability without negatively affecting strength, often resulting in a denser concrete product.
During the curing process, the heat generated from hydration can cause temperature variations that might lead to the formation of micro-cracks if not carefully controlled. This underlines the importance of controlled curing procedures for long-term durability. Studies indicate that higher chloride concentrations in the concrete mix can accelerate corrosion of embedded steel reinforcement, thus reducing the overall service life of the structure. This necessitates careful consideration of chloride levels in the mix design.
New Study Reveals Key Factors Influencing Concrete's 50-100 Year Lifespan - Environmental Factors Affecting Durability
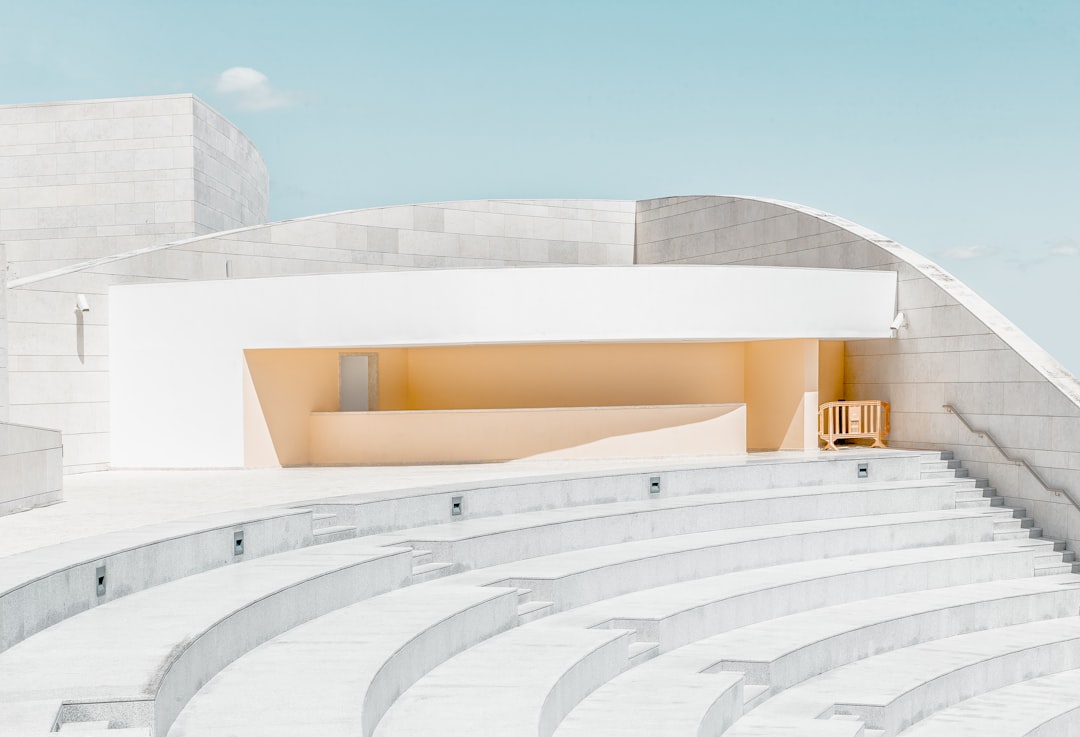
Environmental factors play a crucial role in determining how long concrete structures last, a factor critical when we consider their projected lifespan of 50 to 100 years. Exposure to harsh conditions like seawater, repeated freezing and thawing cycles, and exposure to aggressive chemicals can severely weaken concrete, causing damage and increasing maintenance needs. Concrete issues like alkali-silica reactions and sulfate attacks are particularly damaging, impacting not just the long-term performance of the structures, but also adding to the environmental cost of their existence. It's become clear that improving concrete's resistance to these environmental stresses is paramount. This can be achieved through careful material selection and structural design. Improving durability leads to more sustainable infrastructure, which ultimately plays a part in our attempts to reduce climate change's impact on our built world. By better understanding and addressing these environmental challenges, we can create concrete that produces more resilient and long-lasting structures.
Concrete's durability, while often estimated to last between 50 and 100 years, is significantly influenced by a range of environmental factors. These environmental pressures play a critical role in the long-term performance and longevity of concrete structures, underscoring the importance of understanding how they affect the material's degradation processes. The recent research highlighting the potential to reduce up to 50% of CO2 emissions through extended concrete lifespan underscores the need for a more holistic approach to design and construction. Concrete production, which currently accounts for roughly 10% of global anthropogenic CO2 emissions, primarily due to the high carbon footprint of Portland cement production (8-10% of global CO2 emissions), necessitates this focus on durability.
Beyond the internal chemical makeup of concrete itself, the external environment interacts with concrete in a number of ways that can accelerate degradation and ultimately shorten the lifespan of infrastructure. For instance, exposure to acidic environments can lead to a loss of calcium carbonate within the concrete matrix, weakening its overall structure. The presence of water within concrete pores, subjected to freeze-thaw cycles, can cause internal stress due to the expansion of ice. This stress frequently results in surface deterioration, including spalling and scaling, which can dramatically affect a structure's performance. Furthermore, UV radiation exposure can degrade surface treatments and protective coatings, creating paths for moisture penetration and further degrading the internal structure of the concrete.
Coastal and other saline environments can contribute to the rapid corrosion of embedded steel reinforcement, accelerating structural deterioration. Similar effects are observed when de-icing agents containing brine are used. In these instances, engineers may consider alternative reinforcing materials to improve the longevity of infrastructure. Fluctuations in moisture levels can also create expansion and contraction within the concrete matrix, leading to crack formation. While additives can be employed to mitigate this, their application must be carefully calibrated. In regions close to industrial operations, concrete is exposed to both acidic pollutants and corrosive chemicals, both of which can influence the long-term durability of the concrete by altering its chemical makeup and accelerating the degradation of binding components.
The thermal expansion and contraction of concrete and reinforcing materials can cause differential stresses, especially if not accounted for during the design phase, leading to structural cracks. Likewise, biological factors, including microorganisms and fungal growth, can lead to acid production, accelerating concrete degradation and highlighting the importance of protective coatings. Airborne pollutants, such as sulfur dioxide, contribute to the formation of sulfuric acid when combined with water, which speeds up degradation through mechanisms such as sulfate attack. Finally, the chemical composition of groundwater, including high sulfate or chloride levels, has a significant impact on the concrete's long-term health. Understanding the local environment, including the chemistry of groundwater, is essential to inform the design process and achieve optimal long-term performance of structures.
By focusing on these environmental factors and implementing mitigation strategies, such as optimizing mix designs and utilizing alternative materials, we can extend the service life of concrete structures. This not only ensures the longevity of built infrastructure, but also helps to minimize the environmental impacts of the construction sector and potentially improve sustainability efforts by mitigating the impacts of climate change on our built environments.
New Study Reveals Key Factors Influencing Concrete's 50-100 Year Lifespan - Reinforcement Design and Corrosion Prevention
Reinforcement design and corrosion prevention are crucial considerations when aiming for a 50 to 100-year lifespan for concrete structures. A major concern for reinforced concrete is the potential for corrosion, particularly in environments rich in chlorides. These environments dramatically accelerate the deterioration of the steel reinforcement, leading to compromised structural integrity. Cracks in the concrete also play a role, providing pathways for moisture and oxygen to reach the reinforcing steel, fostering corrosion and weakening the bond between the steel and concrete. Therefore, design decisions related to material properties, such as adjusting the water-to-cement ratio and incorporating protective layers, are essential to minimize corrosion and maximize the life of the structure. Moreover, monitoring and evaluation techniques are vital for understanding and addressing degradation processes, thereby helping prevent costly repairs or infrastructure failures down the line. It's important that engineers and designers stay vigilant about this aspect in order to make structures truly last the projected 50 to 100 years.
Reinforced concrete, while a robust material, is vulnerable to corrosion under specific conditions, which can significantly degrade its structural integrity and lead to premature failure. The interplay of environmental factors, the quality of the materials used, and the design itself contribute to the rate and extent of this deterioration. Chloride-containing environments, for example, are particularly aggressive, promoting corrosion of the steel reinforcement bars embedded within the concrete. This is particularly problematic because even small cracks can allow water and oxygen to reach the steel, leading to a weakening of the bond between the steel and the concrete, increasing the likelihood of corrosion.
Interestingly, research has shown that the intensity of corrosion can stabilize after a short initial acceleration period, roughly 12 days. This acceleration phase is critical, as the corrosion processes are at their most impactful during this timeframe. A critical factor influencing concrete's vulnerability to corrosion is its permeability, largely determined by the water-to-cement ratio. Higher ratios, in essence, create a more porous structure, which increases the chances of reinforcement corrosion due to increased moisture intrusion. Experimental data suggests that using a lower water-to-cement ratio, around 0.40, significantly delays the onset of corrosion compared to higher ratios like 0.55, emphasizing the importance of mix design.
Corrosion, particularly when involving iron and chloride ions, is a complex process involving a cascade of chemical reactions that ultimately lead to the degradation of the reinforcement. These reactions lead to further deterioration, making the issue a continual and worsening cycle unless mitigated. Consequently, understanding the factors leading to corrosion is critical for predicting a structure's longevity. Effective monitoring techniques and methods for assessing concrete degradation are essential for planning maintenance strategies and predicting the long-term service life of structures. Neglecting this issue can have significant financial repercussions, with corrosion of infrastructure costing the United States an estimated $276 billion annually. This substantial figure underscores the need for proactive and comprehensive strategies that address corrosion at all stages of planning, design, and maintenance to enhance the lifespan and performance of our infrastructure.
It's clear that concrete degradation is a multifaceted issue demanding a holistic approach in construction. Simply focusing on strength isn't enough. It's equally important to focus on concrete's long-term resistance to degradation in the various environments it might encounter. These aspects, when effectively integrated, can substantially contribute to concrete's ability to deliver its expected service life and minimize the considerable economic and environmental repercussions of premature failure.
New Study Reveals Key Factors Influencing Concrete's 50-100 Year Lifespan - Mixing Techniques and Curing Processes
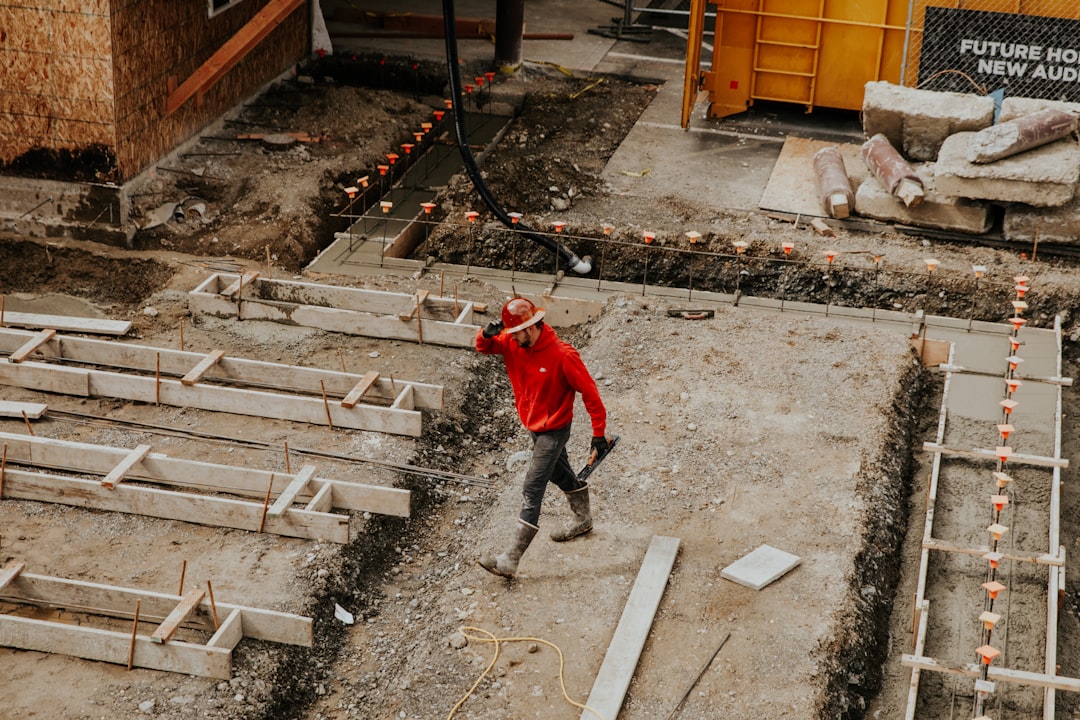
Mixing techniques and curing processes are fundamental aspects influencing the long-term performance and durability of concrete. The way concrete is mixed directly affects the final microstructure, a key factor determining its quality and long-term resistance to deterioration. The efficacy of the mixing process, coupled with the chosen curing method, plays a significant role in achieving desired compressive strength, which is crucial for a structure's intended lifespan.
Curing, in essence, is the process by which cement hydrates, influencing the development of the concrete's ultimate strength and durability. The effectiveness of curing is influenced by several variables, including the duration of the process, the availability of water, and the type of curing method implemented. Interestingly, new research on internal curing, where water is introduced within the concrete mixture itself using microcapsules, is exploring methods to enhance the process.
These processes are not without challenges. For instance, achieving optimal water distribution within a mixture or managing heat generated during hydration can be difficult, which is why effective control and monitoring of the curing process are critical. Optimization of these processes through innovation is critical. By understanding how different mixing and curing methods impact the microstructure and overall performance, we can design and implement strategies to mitigate degradation processes and prolong the service life of concrete infrastructure in diverse environmental settings.
Concrete's mixing techniques and subsequent curing processes are fundamentally linked to its long-term performance, a crucial factor when considering lifespans of 50 to 100 years. The water-to-cement ratio, for instance, plays a significant role in determining the final concrete's porosity. Higher ratios, above 0.5, contribute to a more porous structure, increasing the chances of damage from freeze-thaw cycles and other environmental stressors, essentially shortening the expected lifespan. Conversely, incorporating fiber reinforcement like steel or polypropylene can significantly alter how cracks propagate through concrete, enhancing its overall durability, particularly under tension, which is often encountered in structural applications.
The heat generated during the curing process, a byproduct of cement hydration, can cause micro-cracking if not carefully managed. Optimizing the curing schedule is crucial to control these temperature fluctuations and prevent long-term structural issues. We also see the impact of carbon dioxide on concrete. Exposure to it can lead to carbonation, a process that reduces pH levels and can trigger corrosion in reinforcing steel. This corrosion often proceeds subtly until significant damage occurs, highlighting the need for careful design and environmental consideration. The use of chemical admixtures, like superplasticizers, can improve the mixing process and workability without sacrificing strength, resulting in a denser microstructure with enhanced resistance to environmental degradation. This ties into the overall importance of pore structure. A carefully formulated mix, considering the chosen aggregates and mixing techniques, can lead to a less connected pore network, reducing water penetration and improving resistance to external deterioration.
However, concrete is not just susceptible to external factors, but also experiences changes over time from within. The risk of the alkali-silica reaction (ASR), which can cause substantial expansion and cracking, is greatly influenced by the type and reactivity of the aggregates used in the mix. Selecting low-alkali cement and carefully choosing the aggregates are essential steps in mitigating ASR. Unhydrated cement particles, often remaining within the concrete for years, can also affect durability if not managed correctly. Their potential for hydration over time influences long-term strength and resistance to environmental factors. Moreover, the curing environment itself—temperature and humidity—plays a substantial role in the rate and completion of hydration. Improper curing conditions can alter the microstructure of the concrete, potentially leading to higher porosity and reduced strength.
Further complicating the picture is chloride contamination, which is known to accelerate the corrosion of steel reinforcement. Even a small amount, about 0.1% by weight of cement, can start the degradation process. This reinforces the importance of rigorous mix design and considering the surrounding environment. It's clear that a complete understanding of how these factors interact is essential to designing concrete that performs as intended and lasts as long as we want it to. Further investigation into this complicated relationship could offer new ways of optimizing concrete mixtures for a variety of applications and environments, further extending the useful lifespan of this fundamental construction material.
New Study Reveals Key Factors Influencing Concrete's 50-100 Year Lifespan - Maintenance Practices for Extended Lifespan
To ensure concrete structures reach their projected 50 to 100-year lifespan, adopting a robust maintenance program is critical. This involves a spectrum of approaches, from routine preventive care to proactive interventions aimed at tackling potential problems before they escalate. A key aspect of this is consistent inspection, as early detection of issues allows for timely mitigation, which is essential for safeguarding the long-term health of concrete. Environmental factors like temperature swings and exposure to moisture can accelerate or impede degradation, underscoring the need to consider these influences when designing and maintaining concrete structures. Therefore, a comprehensive approach to maintenance—embracing regular checks, addressing emerging problems promptly, and proactively mitigating potential risks—is paramount in achieving the desired longevity of concrete infrastructure. While some maintenance methods are reactive, simply responding to problems as they emerge, the focus should be on preventative and predictive approaches to ensure concrete endures. Without such a multi-faceted maintenance strategy, it is unlikely to realize the projected lifespan of concrete structures.
Research suggests that achieving the projected 50- to 100-year lifespan of concrete structures hinges on adopting strategic maintenance practices. Optimizing the water-to-cement ratio is a primary concern, as lower ratios (below 0.4) create a less porous concrete, thus increasing resistance to environmental degradation and delaying corrosion. However, ratios above 0.5 can substantially increase the likelihood of structural issues stemming from increased porosity. Maintaining controlled curing temperatures is another key element. The heat generated during hydration, if not managed, can induce microcracks that can compromise long-term structural integrity. Interestingly, researchers are exploring internal curing methods, like incorporating microcapsules filled with water into the concrete mix, which holds potential for significantly improving hydration efficiency and strength.
The selection of materials significantly impacts durability. Avoiding reactive aggregates and using low-alkali cements can help prevent the dreaded alkali-silica reaction (ASR), a chemical process that leads to expansion and cracking. Understanding the progression of corrosion is also vital. While corrosion rates associated with chlorides can stabilize after an initial 12-day period, those first few days are critical in influencing the structure's long-term health. This underscores the need for rigorous monitoring and evaluation strategies to identify and address potential issues early. Furthermore, chemical admixtures, such as superplasticizers, can play a valuable role in increasing workability and creating a denser concrete matrix. The result of this denser matrix is a structure with enhanced resistance to harmful chemicals and water ingress.
In especially harsh environments, selecting alternative reinforcement materials, such as stainless steel or composite materials, could drastically extend the structure's longevity by reducing the impact of corrosion. Even small amounts of chloride contamination, approximately 0.1% by weight of cement, can initiate corrosion, further highlighting the need for precise mix design and a thorough understanding of the local environment. It's also crucial to acknowledge that unhydrated cement particles can persist in concrete for years, influencing long-term strength and resistance to environmental factors. Optimizing hydration practices during curing becomes vital in this context, as they can significantly impact the structure's ability to withstand the pressures of its surroundings over time.
Overall, proactive maintenance, including regular inspections and interventions, is key for preserving the integrity and longevity of concrete structures. Recognizing that the chemical composition of concrete and the surrounding environment play crucial roles in the long-term health of infrastructure allows us to implement more effective and durable designs. Continued research into these areas could potentially lead to significant advances in concrete technology, leading to more resilient and long-lasting structures.
New Study Reveals Key Factors Influencing Concrete's 50-100 Year Lifespan - Innovative Additives Enhancing Concrete Performance
Innovative additives are increasingly important in improving concrete's performance and lifespan. New developments include crystalline admixtures that reduce water penetration, which in turn, improves resistance to environmental damage and potentially increases the concrete's useful life. The exploration of nanomaterials in concrete and the use of carbon-based additives, like carbon black, are also showing promise in enhancing concrete's strength and adding features like the ability to monitor its own condition. These developments are not only about building stronger and longer-lasting concrete but also about making it more environmentally friendly by possibly turning it into a carbon storage material. However, it's crucial that the environmental impact of these new materials is carefully studied to ensure we don't inadvertently create misleading claims about concrete's environmental benefit when compared to other construction materials. It's all about finding a balance between achieving the desired performance and addressing sustainability concerns.
Current research delves into a variety of additive technologies that hold promise for dramatically improving concrete's durability and overall performance. These additives can help extend the operational lifespan of concrete structures well beyond the typical 50 to 100-year projections.
One area of interest involves polymers like polyvinyl acetate, whose inclusion can make concrete more flexible and resilient to stress, which is particularly relevant for regions prone to earthquakes. Another intriguing area is the use of nano-silica. By incorporating nano-silica particles into the concrete mix, researchers have shown that it can create a denser matrix with improved compressive strength and a greater resistance to water penetration.
The idea of self-healing concrete, where microscopic capsules containing repair agents are embedded, is capturing a lot of attention. The hypothesis is that upon crack formation and exposure to water, these capsules release the repair agent, initiating a natural healing process. This type of innovation could significantly improve concrete's long-term performance. Along similar lines, the addition of materials like graphene oxide shows promise in enhancing both the strength and resilience of concrete. However, while this research suggests improvements up to 30% in compressive strength by increasing the bond between the cement paste and aggregates, we need to look more closely at what effect, if any, it has on other concrete properties.
The concept of 'smart' concrete, incorporating sensors into the mixture, is fascinating. Fiber optic and piezoelectric sensors can provide continuous feedback on the structural integrity of the concrete, allowing for proactive maintenance. This sort of real-time monitoring could vastly extend the lifespan of concrete structures by enabling early detection and mitigation of problems before they become major issues.
Research into alternative aggregates is also being investigated. Expanded glass beads offer a promising possibility as a lighter-weight aggregate, reducing the density of concrete while also enhancing thermal performance. This could be a key element for construction projects in regions with large temperature variations.
Corrosion management within concrete structures is a major concern, leading researchers to explore a range of electrochemical methods. These innovative approaches could help mitigate steel reinforcement corrosion, especially in chloride-rich environments, by using controlled electrical currents.
The addition of hydrophobic agents can greatly increase concrete's resistance to water, which is important in regions with freezing temperatures. Reducing water penetration through the addition of hydrophobic agents helps decrease damage caused by freeze-thaw cycles.
Researchers are also exploring biological solutions. Microbial-induced carbonate precipitation (MICP) has shown some promise in improving the binding properties of concrete by using bacteria to fill voids and create a denser material. However, much more research is needed to understand if the benefits of MICP outweigh the potential risks, before applying it more widely.
Finally, researchers are working on additives that can better control thermal conductivity during the curing process. This could help to manage temperature gradients within the concrete, mitigating the possibility of cracking during the curing process, which improves overall strength and durability.
It's important to note that while these innovations show promise, we need to carefully evaluate their overall impact on concrete's properties. Some innovations may have unintended consequences that we are just beginning to understand. For example, we need to determine the long-term impact of these additives on the environment. Further investigation into each of these additive technologies is critical for advancing the understanding and optimal use of concrete within the built environment. It is through rigorous research and the validation of these concepts that the future of longer-lasting and more sustainable concrete solutions can be realized.
More Posts from aistructuralreview.com: