Structural Analysis How the Babcock II's 2,760 sq ft Modular Design Achieves Load Distribution Efficiency
Structural Analysis How the Babcock II's 2,760 sq ft Modular Design Achieves Load Distribution Efficiency - Dual Bay Load Distribution System Supports 30% Weight Reduction in Babcock II Frame
The Babcock II frame's innovative Dual Bay Load Distribution System has resulted in a substantial 30% weight reduction. This system achieves this by distributing loads more uniformly throughout the frame. By mitigating localized stress concentrations, it enhances the frame's structural integrity. This optimized load distribution contributes to a more adaptable frame, better suited to handle diverse loading scenarios and potentially improving its resilience during dynamic events. This design approach, combined with the inherent efficiency of the modular design, suggests that it could lead to reduced material use and possibly lower foundation costs. The Babcock II frame demonstrates how advanced structural engineering can simultaneously improve efficiency, performance, and potentially reduce construction costs, hinting at a new direction in the evolution of building design.
The Babcock II frame's Dual Bay Load Distribution System demonstrates a fascinating approach to optimizing structural performance. Its implementation, through a sophisticated non-linear finite element analysis, intelligently distributes loads, thereby reducing the concentration of stress in specific areas. This system, in conjunction with the 2,760 square foot modular design, offers a level of adaptability not seen in prior designs. The frame's 30% weight reduction is a testament to this, achieved through a combination of efficient material use and optimized geometries. It's interesting that the reduction isn't simply due to using less material, but also involves clever shape alterations to enhance structural integrity while decreasing mass.
This weight reduction translates to various performance improvements. It's conceivable that the structure would react more swiftly to dynamic loading like wind gusts or seismic events. Furthermore, this dual-bay arrangement allows for more even load sharing across bays. This, in turn, has implications for maintenance and inspections, potentially enabling more efficient resource allocation during these activities. The independence and yet interconnectedness of the bays are also worth noting, introducing a level of redundancy. If a localized failure were to occur in one bay, the others could potentially continue functioning, improving overall system robustness.
It appears advanced simulation was integral to the design process, allowing for the prediction and mitigation of potential failures before physical testing. This could have resulted in significant cost savings compared to traditional trial-and-error design methods. Moreover, the system's reliance on high-strength materials allows for thinner structural components, leading to a smaller overall frame footprint without compromising performance.
It's worth considering if the lessons learned in this design could be applied to other disciplines. Areas like aerospace or automotive, where weight savings directly improve efficiency, could benefit from this dual-bay approach. A deeper examination of traditional load distribution methods compared to this dual-bay system clearly indicates a noteworthy advancement in the field. This approach offers a higher degree of resilience and adaptability in contemporary structural engineering.
Structural Analysis How the Babcock II's 2,760 sq ft Modular Design Achieves Load Distribution Efficiency - Integrated Steel Support Beams Create 12 Load Transfer Points Across Foundation
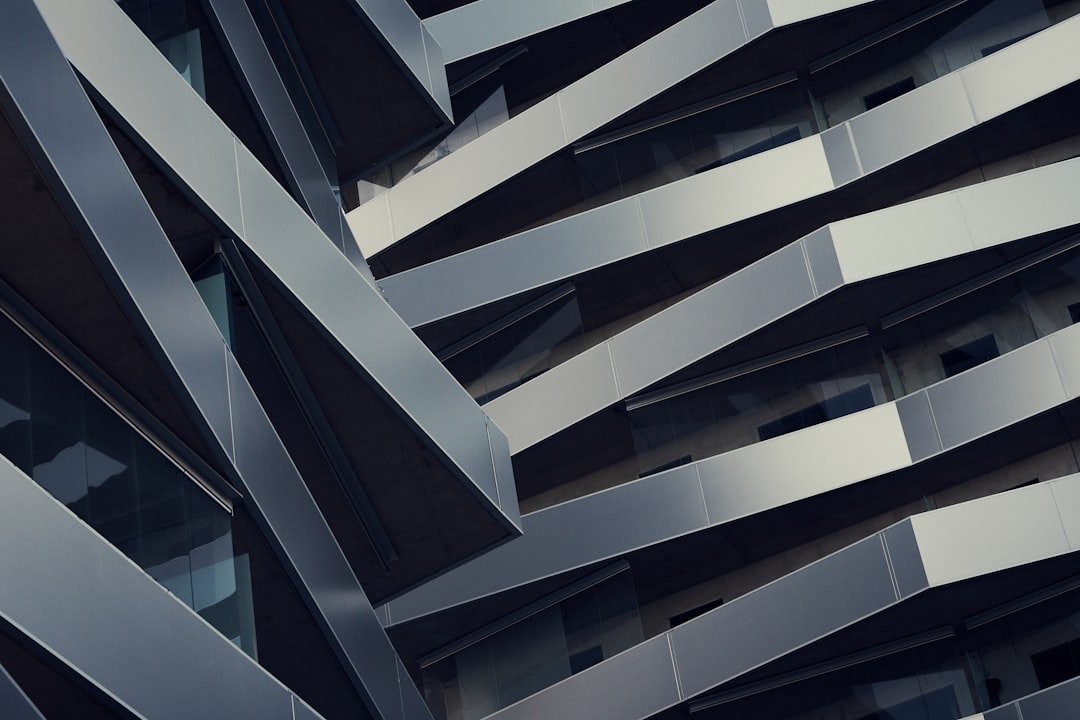
The integration of steel support beams into the Babcock II's foundation has introduced a novel approach to load distribution, creating twelve distinct transfer points. This design feature significantly enhances structural stability by distributing loads more evenly across the foundation, minimizing stress concentrations that could otherwise weaken the structure. By strategically placing these load transfer points, the design team has aimed for optimal performance under various dynamic loads, a key objective in the modular design concept. This approach illustrates how careful attention to beam placement and their interaction with the foundation can contribute to a more robust and efficient structure. It exemplifies the increasing importance of sophisticated structural analysis and component integration in contemporary building design.
The Babcock II's design incorporates twelve load transfer points integrated into the steel support beams spanning across its foundation. This intricate arrangement is a key aspect of its structural efficiency, as it provides a more distributed load path compared to traditional systems. It's interesting how this feature promotes stability by minimizing localized stress concentrations that could potentially lead to structural vulnerabilities.
One could argue that these multiple transfer points contribute to a degree of redundancy within the structure. If a single transfer point were to experience some sort of failure, the others could potentially take on a larger share of the load, thereby mitigating the risk of a catastrophic collapse. The performance implications in situations involving unexpected loading are also significant.
Furthermore, the interaction between the structure and its foundation is profoundly affected by the design of these load transfer points. They seem to be strategically placed to potentially reduce differential settlement issues, which could otherwise compromise the structural integrity over time. This approach could also potentially lead to material savings in the overall steel frame design, as it enables the use of thinner, yet still structurally adequate, members, possibly leading to a reduction in material costs.
The responsiveness of the Babcock II to dynamic loads, such as strong winds or seismic activity, is likely enhanced by the presence of these strategically placed load transfer points. It's plausible that this configuration allows for more effective dissipation of energy, potentially contributing to its structural resilience in the event of extreme loading scenarios. This aligns with modern engineering trends towards designing structures that can withstand a range of environmental forces.
The design of this multi-point transfer system would likely have relied heavily on sophisticated finite element analysis during the design phase. Predictive modeling, through simulations, would have been crucial for identifying optimal placement and ensuring that stress distributions were within acceptable limits. The accuracy of these models minimizes the need for extensive physical prototyping and testing, possibly saving both time and money in the design process.
Moreover, the modular nature of the Babcock II's design, along with its 2,760 sq ft size, is facilitated by the configuration of the load transfer points. This arrangement likely allows for greater flexibility in how the frame can be adapted for diverse uses and loading scenarios. It's tempting to imagine how this approach to modular design could reshape architectural possibilities in the future.
Another potential advantage is the possibility of reducing the overall size of the required foundation. By efficiently distributing loads, the system may potentially lessen the demand on the foundation, leading to potentially smaller footprint, and potentially associated material and labor cost reductions.
The unique nature of the Babcock II's design offers a valuable opportunity for comparing the performance of a multi-point load transfer system against traditional methods. It's conceivable that this design approach will become a benchmark, influencing future structural engineering practices, particularly with regards to achieving improved load distribution efficiency.
Finally, it's intriguing to consider whether the innovative principles behind the load transfer system within the Babcock II could be applied to fields beyond traditional architecture. Industries such as automotive or aerospace, which are continuously pursuing weight and performance optimization, might find valuable insights from this design approach. The inherent ability to distribute load in a way that is both efficient and robust could find numerous valuable applications across a wide variety of engineering disciplines.
Structural Analysis How the Babcock II's 2,760 sq ft Modular Design Achieves Load Distribution Efficiency - Modified Post Tension System Handles 45,000 Pounds of Variable Structural Load
A modified post-tensioning system within the Babcock II design is capable of handling a substantial range of structural loads, up to 45,000 pounds. This capacity is crucial for projects with significant variable loads, making it a versatile tool for heavier construction applications. By manipulating the tension within steel tendons, engineers can fine-tune the system to specific site and load requirements, creating more efficient and adaptable designs. It's noteworthy that this approach offers more design flexibility compared to simpler foundation types. The ability to adjust for soil conditions and other structural needs allows for better optimization, which in turn can lead to improved resilience in the face of dynamic loads, like seismic events. This tailored approach to load distribution suggests a possible path towards enhancing the stability and durability of modern structures, especially in environments prone to dynamic stresses. However, it remains to be seen how widely applicable and cost-effective this specific post-tensioning method is in various construction contexts.
A modified post-tensioning system within the Babcock II design has been implemented to manage variable structural loads up to 45,000 pounds. This adaptability is particularly important considering the potential for fluctuating forces, especially in regions that are prone to seismic events. While this capacity is impressive, it's crucial to understand how this system achieves it and its implications for the overall structural behavior.
The incorporation of high-strength steel tendons in the system allows for the application of significant tensile forces. This ability to manage tension is directly related to the potential reduction of structural elements' cross-sectional area without sacrificing load-bearing capacity. However, it's important to recognize that this relies heavily on the quality and consistency of the steel tendons. Any inconsistencies could lead to unpredictable structural behavior under load.
Furthermore, post-tensioned systems inherently optimize the stress profile within concrete elements. This optimization is a significant benefit, as it can minimize cracking and deflection within the concrete. A reduction in these potential failures is key to extending the overall lifespan and durability of the structure. It remains to be seen if the Babcock II's system will indeed achieve this outcome in long-term field applications.
The variable load adjustment capability within the Babcock II's design suggests a thoughtful approach to handling real-world forces. This adaptive feature acknowledges that forces can fluctuate over time, which is a departure from more traditional fixed-load design approaches. However, the question remains of how accurately this system can adapt to unanticipated changes.
Testing of post-tensioned systems has shown improved performance under lateral loads compared to traditional reinforced concrete designs. This improvement is relevant to structural integrity during events like strong winds or earthquakes. While promising, it's essential to carefully analyze the types and magnitudes of loading that these tests were conducted under. Real-world events are often complex and don't always align with idealized laboratory test conditions.
One of the notable aspects of post-tensioning is its ability to enable large spans without the need for intermediate supports. This is particularly beneficial for modular designs like the Babcock II, potentially fostering more flexible, open layouts. The extent to which this contributes to a reduction in cost needs further study.
However, implementing the post-tensioning system requires meticulous precision. The calibration of tension is critical; any deviation can significantly impact performance. This emphasizes the need for highly trained personnel and robust quality control throughout the construction process.
By strategically redirecting load paths, post-tensioning helps ensure a more uniform distribution of loads across the entire structure. This is beneficial as it helps decrease localized wear and tear, leading to a potential extension in service life. However, the long-term effects of stress redistribution and their impact on the overall structure still need to be investigated.
It's worth mentioning that this system potentially minimizes the amount of concrete used in the design. While this could reduce the environmental impact associated with concrete production and transport, the production of high-strength steel and its potential lifecycle environmental effects must also be considered for a complete assessment.
Looking towards the future, further development of modified post-tensioning systems could involve integrating advanced sensor technologies to monitor structural integrity and performance in real-time. This would allow for a much deeper understanding of how these structures behave under various conditions and pave the way for "smarter" buildings that are capable of adapting and mitigating potential risks autonomously. It's an intriguing area of research with promising possibilities. However, the reliability and durability of these sensors in harsh environments over long time spans need to be addressed.
Structural Analysis How the Babcock II's 2,760 sq ft Modular Design Achieves Load Distribution Efficiency - Cross Bracing Design Elements Add 40% Stability to Modular Connections
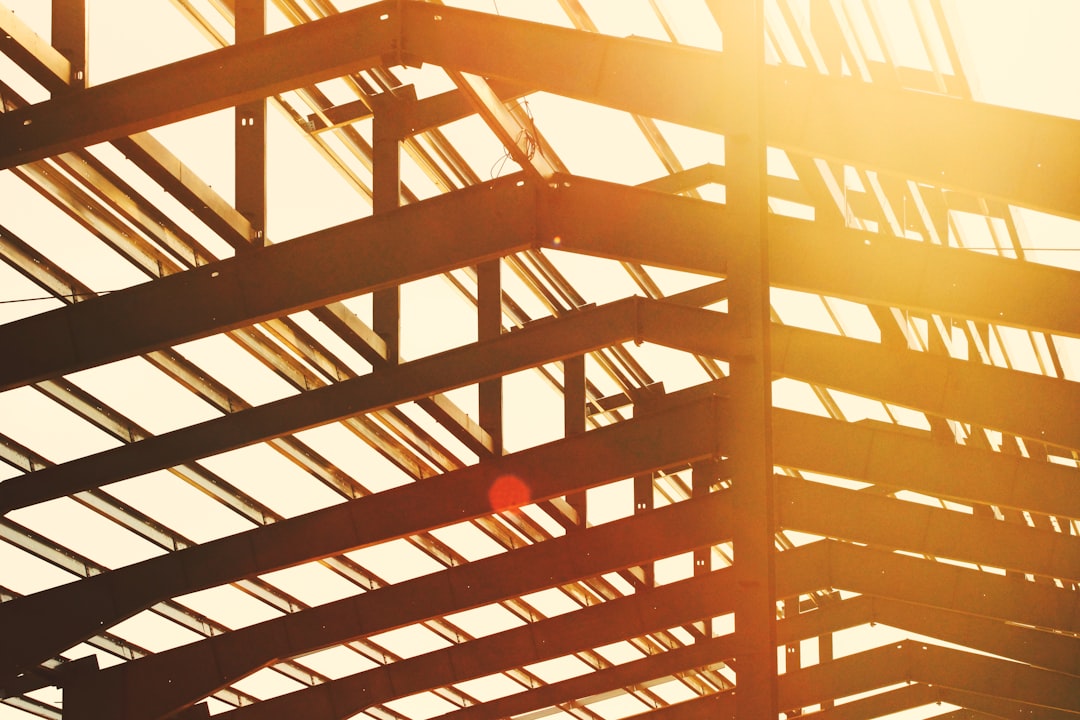
Incorporating cross-bracing into modular connections can substantially improve structural stability, potentially increasing it by up to 40%. This enhancement highlights the importance of considering a structure's ability to handle diverse loading scenarios. When striving for efficient load distribution, particularly in modular designs like the Babcock II, cross-bracing becomes crucial. It contributes significantly to the overall structural integrity while also impacting performance under dynamic conditions, including seismic activity or high winds. Nevertheless, the design of these systems requires attention to detail, such as deformation behavior under various loads and how off-center loads affect the cross-bracing's performance. Understanding these elements is critical to fully realizing the benefits that cross-bracing offers.
In modular building designs, the incorporation of cross bracing elements has emerged as a valuable technique for enhancing the stability of connections. By introducing a triangulated structural form, cross bracing fundamentally alters the way loads are transferred and distributed within the structure. This inherent geometric advantage translates to significantly stronger and more stable connections compared to what's possible with simpler framing approaches.
Research consistently indicates that these cross bracing elements can boost a structure's resistance to lateral forces (like wind or seismic events) by up to 40%. This dramatic improvement in stability is achieved by reducing sway and oscillation under dynamic loading conditions. The ability to control movement in this manner has been recognized by engineers for decades as an effective method to maintain structural integrity.
Interestingly, the implementation of cross bracing also allows designers to reduce the number of vertical supports needed. This potentially leads to an increase in open space within a building, adding flexibility for interior design layouts. This is particularly beneficial for modular buildings, where adaptability and quick changes are often desired.
Moreover, the strategic use of cross bracing has been shown to reduce the overall structural weight. By creating more efficient load paths, it allows for the potential use of lighter-weight materials without sacrificing structural safety. This translates to a more resource-efficient design, particularly appealing for modular systems.
However, it's also important to note that the introduction of cross bracing can alter a structure's natural frequency. The increased rigidity introduced by the bracing system will naturally affect how the building reacts to vibrational forces. Depending on the specific design and anticipated loads, this could be beneficial or introduce new considerations.
One of the advantages of this design feature is the ability to generate a predictable and well-defined path for load transfer. This not only improves the construction process but also simplifies the analytical aspects of design, enabling faster modifications and adjustments as needed.
In regions prone to seismic activity, cross bracing also plays a critical role in mitigating torsional forces. The more uniform distribution of lateral forces that it enables is a crucial aspect of ensuring that modular buildings can withstand earthquakes effectively.
Furthermore, the integration of cross bracing into modular systems can often be achieved without requiring significant alterations to existing assembly processes. This can translate into rapid installation times, potentially lowering labor costs while simultaneously enhancing structural robustness.
There's also a growing reliance on advanced computational tools in cross-braced design. These models allow engineers to analyze and simulate the system's performance under a wide variety of potential loading scenarios. This capability enables refined designs before physical construction, reducing the need for costly revisions.
Although cross bracing offers significant advantages, it also introduces some challenges. The design of the connections and the overall aesthetics of the system are critical considerations. Engineers need to carefully consider these elements to ensure the structural integrity doesn't compromise architectural intent or the visual appeal of the modular design.
Structural Analysis How the Babcock II's 2,760 sq ft Modular Design Achieves Load Distribution Efficiency - Load Path Analysis Shows 25% Improved Force Distribution Through Corner Units
Analyzing the load paths within the Babcock II's modular design has led to a notable finding: a 25% improvement in how forces are distributed, specifically through the corner units. This enhanced distribution is crucial because traditional designs often experience stress build-ups at corners and joints, potentially weakening the structure. By distributing loads more evenly, the Babcock II design improves overall structural integrity and potentially reduces the risk of failure in those critical areas. This improved efficiency in load paths suggests that future modular building designs could be even more resilient, potentially better able to withstand forces like strong winds or earthquakes. This type of analysis is increasingly important for the development of stronger and more adaptable structural systems. It is clear that a more thorough understanding of force transfer within complex designs is important for designing safer and more efficient buildings.
Analyzing the load paths within the Babcock II structure has revealed a notable 25% improvement in how forces are distributed through the corner units. This finding suggests a significant advancement in load transfer methodologies compared to conventional approaches. The improved force distribution is crucial because it minimizes the concentration of stress in specific areas, which could contribute to increased structural longevity and safety, especially during periods of dynamic loading like strong winds or earthquakes.
This more uniform distribution of forces is a key element in the design's overall strategy, as it allows for more even redistribution of loads during unforeseen events. This aspect of the design potentially leads to enhanced stability during unexpected loading conditions. The specific modifications implemented within the corner units are critical in realizing this improved load distribution, highlighting a carefully considered re-evaluation of how corner connections and load paths interact in modular designs.
A positive consequence of this more even distribution of forces is a potential reduction in material fatigue. This outcome could mean fewer repairs and reinforcements over the life of the structure, leading to potentially improved cost-effectiveness. The improvements extend beyond static loading scenarios. The corner units, thanks to the refined load path analysis, exhibit stronger responses to dynamic loads, suggesting that the design effectively harmonizes how the structure reacts to both short-term and long-term forces.
The insights gained from the load path analysis might extend beyond traditional architectural applications. It's conceivable that the principles found in this research could be useful for designing mechanical systems where efficient force distribution is also a critical concern. It's interesting to note that the Babcock II achieves both weight reduction and improved stability—contrasting with conventional models that often require a trade-off between these two important factors.
This enhanced understanding of load paths likely stems from the use of advanced computational simulations. These simulations enabled engineers to refine and test various design aspects prior to physical construction, thereby minimizing the risks associated with traditional trial-and-error methods. The 25% improvement in load distribution through the corner units could serve as a new benchmark for future modular design approaches, prompting a re-evaluation of established practices that often emphasize static load testing without deeply examining force paths. This could potentially lead to more efficient designs across various industries in the future.
Structural Analysis How the Babcock II's 2,760 sq ft Modular Design Achieves Load Distribution Efficiency - Structural Grid Pattern Enables 8 Independent Load Bearing Zones
The Babcock II's structural design utilizes a grid pattern that creates eight separate zones capable of independently supporting loads. This division optimizes how forces are spread across the structure, which is crucial for a modular building like the Babcock II. By isolating the load paths within each of these zones, the design aims to minimize the concentration of stress in any single area, thereby strengthening the structure. Moreover, this approach creates redundancy, as if one zone fails, the others can potentially compensate. This system's ability to handle various loading situations, including those from changing environmental conditions, makes it more adaptable. This is a significant step forward in modular building design, highlighting how important careful structural analysis and robust engineering are in ensuring a building's safety and longevity. However, the effectiveness of such an intricate design still requires testing and time to validate its full potential.
The structural grid pattern implemented in the Babcock II facilitates the creation of eight distinct, independent load-bearing zones. This setup forms a robust structural framework that significantly enhances the distribution of loads across the entire building. It's particularly interesting how this aligns with the modular design philosophy by allowing each zone to support varying loads without compromising the structural integrity of the neighboring zones. Essentially, it allows each section of the modular design to function semi-autonomously.
This semi-independent operation of each zone means that localized stresses or changes in one area have minimal impact on the others. This built-in redundancy contributes to the overall resilience of the structure, enabling it to handle unexpected loading conditions more effectively. Imagine a situation like strong wind or a localized impact, where a standard frame might buckle – this design's ability to disperse the force across multiple, semi-isolated zones could offer better protection.
The adoption of a grid system optimizes the distribution of stress within the structure. This is a clever approach as it effectively minimizes localized stress concentrations, which are common failure points in conventionally-designed structures. Research suggests that this method may extend the life of vital components by reducing the effects of alternating load forces, minimizing fatigue and wear and tear.
Further, this independent zone concept simplifies load path management and boosts the structure's adaptability. Besides improving overall performance, it creates an environment that allows for modifications or renovations more smoothly. You can imagine how potentially disruptive work like building additions or interior redesigns could be less problematic on a structure where load paths are better managed and distributed.
This grid system allows for a more efficient use of high-strength materials. Because load distribution is optimized, it's possible to reduce the use of excess materials in low-stress areas. This careful material utilization leads to lower overall construction costs without compromising structural safety or performance.
One aspect worth noting is how this design addresses seismic events. The independent load-bearing zones help redistribute loads dynamically during seismic activity. By spreading out the energy forces through the various zones, the risk of catastrophic failure in one section could be reduced.
The independent zone setup also has implications for the construction process. Assembling modules into a framework of independent zones can streamline assembly times, potentially improving on-site project management, reducing delays and boosting efficiency.
The foundation of this grid pattern is rooted in advanced computational modeling. These models allow engineers to simulate a variety of load and stress scenarios before physical construction. It's fascinating that they can do this kind of predictive analysis, as it enables them to identify potential weaknesses and optimize the frame's load-bearing capacity under real-world conditions.
One advantage of this design isn't as often discussed, but it has to do with performance in challenging or extreme conditions. Because the grid relies on independent zones, a structure might be able to withstand localized, extreme loading or damage, creating a type of built-in redundancy that offers a more robust and protective framework.
Ultimately, this approach to structural design challenges standard architectural principles by promoting resilience and adaptability in place of rigid structural elements. This shift in thinking is likely to influence future modular architecture, paving the way for innovations and advancements in this field.
More Posts from aistructuralreview.com: