New Study Reveals Optimal Surface Preparation Techniques for Slip-Critical Connections in Steel Structures
New Study Reveals Optimal Surface Preparation Techniques for Slip-Critical Connections in Steel Structures - Blast Cleaning Emerges as Top Surface Preparation Method
Recent studies have underscored the importance of meticulous surface preparation for the reliable performance of steel structures, particularly in applications like slip-critical connections. Within this landscape, blast cleaning stands out as a preferred method. Its ability to efficiently remove contaminants, including rust, paint, and other debris, from steel surfaces makes it highly effective in creating a suitable foundation for coatings. The technique, which encompasses various approaches like sandblasting, utilizes abrasive materials to achieve a desired surface profile. Adherence to established industry standards, ensuring consistent levels of surface cleanliness, is paramount to achieving the intended outcomes. The selection of the appropriate abrasive media and careful control of the blasting process are critical factors influencing the quality of surface preparation. Ultimately, the aim is to create a uniformly roughened surface that promotes excellent coating adhesion and enhances the long-term integrity and protection of the steel infrastructure.
Blast cleaning, a technique rooted in Tilghman's 1870 patent, has evolved into a cornerstone of surface preparation, particularly for applications like steel structures. Originally seen in sandblasting, a dry abrasive method, its appeal stems from its ability to rapidly and effectively clean steel. The need for optimal surface preparation, particularly in slip-critical connections, is paramount for achieving desired coating performance. Standards like ISO 8501 and SSPC guidelines provide frameworks, specifying various methods including different levels of abrasive blasting (SSPC SP 5, SP 6, and SP 10) and chemical treatments like pickling.
While the selection of suitable paints for slip-critical connections is crucial, the actual preparation process can be broken into three steps: initial liquid cleaning, followed by mechanical cleaning techniques like blasting, and final dusting. However, achieving optimal blast cleaning requires a careful understanding of variables, including the abrasive material itself—be it steel grit, glass beads, or aluminum oxide. The properties of the abrasive directly influence the achieved surface texture. These different blast cleaning methods and their specific outcomes are meticulously documented in various technical standards.
Ultimately, the effectiveness of blast cleaning hinges on its ability to completely remove rust, loose and even bonded coatings, as well as any contaminants that might hinder paint adhesion. Achieving a consistent, uniformly roughened surface is critical for both the adhesion and longevity of the applied coatings. It's intriguing how a specific surface profile can be attained by carefully controlling factors like blasting pressure and abrasive velocity. This tailored surface isn't merely cosmetic; it can impact the fatigue life of the structure. It also raises concerns about the considerable dust created during the process, necessitating robust safety controls. While the focus is often on the surface profile, the impact angle of the abrasives also plays a role, possibly affecting the underlying microstructure, which becomes crucial under dynamic loads. The increasing use of automated systems offers improved consistency and safety compared to manual cleaning practices, highlighting a trend in modern surface preparation.
New Study Reveals Optimal Surface Preparation Techniques for Slip-Critical Connections in Steel Structures - Impact of Coating Thickness on Slip Resistance Performance
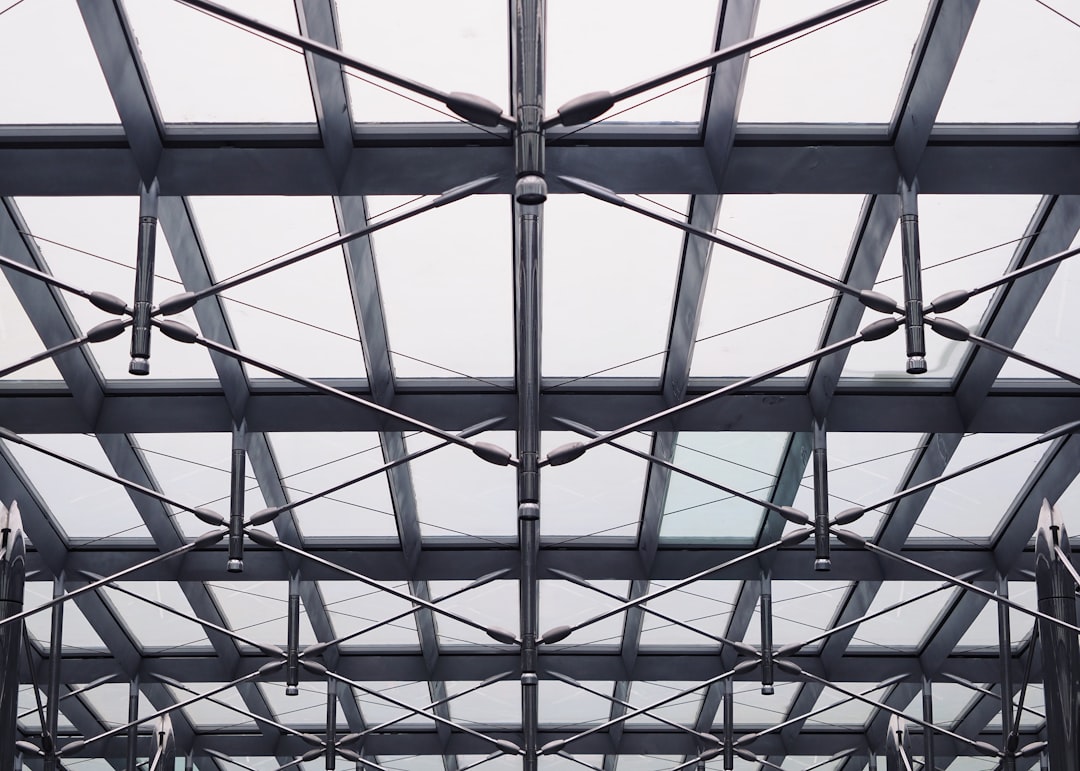
The thickness of a coating applied to steel surfaces in slip-critical connections has a notable impact on how well they resist slippage. Thicker coatings tend to improve slip resistance. However, the connection's performance is also deeply affected by the clamping force generated when bolts are tightened. This clamping force can lessen over time due to factors like material creep, ultimately impacting the effectiveness of the coating in preventing slippage. Moreover, it's crucial to recognize that the methods used to prepare the steel surface before coating application are equally important in ensuring the joint's overall strength and long-term behavior. There's a clear relationship between the thickness of a coating and the surface preparation techniques that can lead to more resilient and safer steel structures. Recognizing and optimizing this interplay is vital in ensuring the durability and safety of these structures. Some aspects remain a challenge. For example, current industry standards often do not provide clear, actionable guidance in the realm of designing connections, especially in relation to the durability under dynamic and long-term load scenarios. Further investigation on the combined effect of coating and surface preparation is warranted.
The influence of coating thickness on slip resistance in steel connections is a complex topic. Generally, thicker coatings can enhance slip resistance, but this relationship isn't always straightforward. There appears to be an optimal thickness, as exceeding it can potentially decrease traction. This is likely due to how thicker coatings can alter the surface texture and roughness, which are essential for friction.
It's fascinating how the type of coating material itself plays a role. Different coatings, like epoxies or polyurethanes, might respond differently to increases in thickness, indicating that a one-size-fits-all approach is unlikely to be ideal. Temperature also seems to be a factor; thicker coatings appear to make the performance more susceptible to temperature changes, possibly because of altered material properties.
Beyond surface properties, the coating's impact extends to the underlying steel. Changes in thickness can lead to alterations in the steel's microstructure, which could affect the strength of the bond between coating and steel, and overall joint performance. This is especially relevant for high-stress applications where even small variations could be problematic.
The way we test slip resistance also plays a role in interpreting results. Different testing methods—such as static versus dynamic—may lead to different ideal coating thickness ranges for optimal performance. Furthermore, we need to consider the impact of coatings on the surface's water-repelling qualities (hydrophobicity). Thicker coatings might make it more difficult for water to drain, which in turn could negatively impact slip resistance under wet conditions.
While thicker coatings offer the advantage of improved initial slip resistance, they can also have downsides. The risk of cracking or delamination under mechanical stress seems to be higher with thicker layers, affecting their long-term wear resistance. However, properly managed coating thickness can also reduce maintenance costs, since properly coated joints can potentially last longer.
Precise measurement of coating thickness is essential, as even slight differences can drastically change slip resistance performance. This emphasizes the importance of reliable and carefully controlled application techniques. Future research might explore how the optimal coating thickness range differs depending on specific coating material, temperature, and intended application. Understanding the complexities of these interactions will be vital for designing and constructing reliable and durable steel structures, especially those with slip-critical connections.
New Study Reveals Optimal Surface Preparation Techniques for Slip-Critical Connections in Steel Structures - Bolt Preload Optimization for Enhanced Connection Stability
Ensuring the stability of steel structures, particularly those employing slip-critical connections, hinges on optimizing the preload applied to high-strength bolts. Preload loss, a common occurrence, can significantly weaken connections, especially when subjected to dynamic loads like vibrations. Research indicates that limiting preload loss to within 5% during slip is vital for robust connection performance. This underscores the importance of carefully considering factors like bolt arrangement and the overall design of the connection. Additionally, achieving optimal slip resistance is influenced by surface preparation techniques and the thickness of any coatings applied. The interrelationship between these elements is significant for ensuring the long-term safety and resilience of steel structures. Innovative design strategies, combined with advanced monitoring tools capable of assessing bolt preload in real time, offer promising avenues for improving the performance and longevity of bolted connections. However, the complex interplay between these factors necessitates a more comprehensive understanding to fully realize these benefits, which could be further studied.
Bolt preload plays a crucial role in the stability of connections, particularly in slip-critical situations. Maintaining the right clamping force at the joint interface through optimized preload is paramount for preventing slippage and ensuring structural integrity. Research suggests that achieving the desired bolt tension is often more influential than the connection's material properties alone.
It's interesting that achieving the desired preload isn't just about the torque applied. The friction between the bolt threads and the nut significantly influences preload. Variations in this friction coefficient can lead to inconsistencies in preload levels, underscoring the importance of careful torque control.
Furthermore, optimal preload not only influences slip resistance but also affects the fatigue life of connections. Maintaining preload within certain limits can minimize the detrimental effects of cyclic loading, extending the lifespan of connections in dynamic environments.
Unfortunately, contaminants like lubricants can drastically reduce the effective preload in a slip-critical connection. Therefore, employing advanced surface preparation techniques to remove these contaminants before final assembly is crucial for achieving optimal performance.
The bolt material and its properties extend beyond influencing preload; its mechanical characteristics, like yield strength and stiffness, affect how the preload translates into joint stability when loads are applied.
Experimenting with novel bolt designs, such as those incorporating serrated or keyed surfaces, has revealed that these features can improve the ability to maintain preload, enhancing their utility in slip-critical applications.
Temperature fluctuations during the service life of a structure can lead to variations in bolt preload, potentially causing a loss of clamping force over time. Incorporating engineering solutions that account for thermal expansion into connection design is critical for safeguarding structural integrity.
Traditionally, bolt torque methods have been the standard, but acoustic or ultrasonic measurement techniques are gaining traction as a means of accurately assessing actual bolt preload in real-time. This shift in quality assurance practices in steel construction could lead to improved accuracy and safety.
Direct tension indicators offer a visual confirmation of the correct preload levels during assembly, contributing to safety and performance assurance. This represents a step forward in ensuring that the right clamping force is achieved before the connection is fully assembled.
Finally, the design of the bolted connection, specifically the number of bolts used and their arrangement, plays a significant role in the distribution of loads. Achieving an optimal bolt configuration can minimize the necessary preload while still maximizing connection stability. This is a factor that deserves closer consideration in designs. There is still a need for further research on this and many other aspects of bolted connections, as standards may still not be enough to cover the increasing complexities of steel structures and connections.
New Study Reveals Optimal Surface Preparation Techniques for Slip-Critical Connections in Steel Structures - New High-Performance Surface Coating Outperforms Traditional Options

A new study has shown that a high-performance surface coating, often derived from bio-based sources like lignin, can surpass traditional coatings in several aspects. This newer coating is particularly notable for its improved ability to repel water compared to older, synthetic types. The research also highlights its enhanced resistance to physical wear like abrasion, and staining caused by environmental factors like prolonged exposure to UV radiation. These characteristics make it a compelling alternative for use in construction and potentially other industrial projects.
Interestingly, the research also underscores that the success of any surface coating, especially for a challenging application like slip-critical steel connections, depends greatly on how the underlying surface is prepared. It suggests a clear connection between the specific methods of cleaning and preparing the surface before applying a coating and the ultimate performance of that coating. This is a reminder that achieving a desired outcome requires more than simply applying the latest materials.
Given the growing body of evidence surrounding this new type of coating and its interplay with surface preparation, it's worth revisiting traditional assumptions about both materials and practices. Perhaps there are more opportunities for improvement than we have previously considered. As we push for enhanced performance and safety in steel structures, it seems we must also examine the underlying basics of how we prepare surfaces and consider what new technologies may improve this facet of the design process.
Recent research has unveiled a new class of high-performance surface coatings that surpass traditional options in various aspects. These advanced coatings employ novel adhesion mechanisms, fostering a stronger bond with steel substrates compared to conventional coatings that mainly rely on mechanical interlocking. This enhanced bonding appears to be linked to their molecular structure, offering a potentially more robust and durable solution.
Interestingly, these new coatings often have a wider operational temperature range, remaining effective at temperatures exceeding what many conventional options can handle. Some of these advanced coatings function optimally at over 200°C, whereas traditional coatings may begin to degrade around 120°C. This characteristic may prove invaluable in applications where extreme temperatures are encountered.
Moreover, these coatings are specifically engineered to resist environmental stresses such as saltwater and industrial chemicals, promising a significant extension of the coated surfaces' lifespan. While many standard coatings suffer from corrosion under these conditions, the new generation appears to provide greater protection, opening up possibilities for use in harsh environments.
The surface preparation method before coating application still appears to be crucial, with the roughness of the blasted surface playing a surprisingly significant role in these new coatings. Achieving a suitable surface texture is critical to enhancing the load-bearing capacity and overall structural integrity. This emphasizes the need for precise surface preparation for optimum coating performance.
Some of these newer coatings incorporate nanoscale modifications, leading to intriguing self-repairing properties. Under certain conditions, they seem to be able to close up minor surface damage, a capability that is not found in typical coatings. This is a potential advantage that could improve durability in certain situations.
While the initial materials for high-performance coatings might be more expensive than conventional alternatives, their ease of application and reduced need for maintenance could lead to lower lifecycle costs in the long run. This warrants a thorough cost-benefit analysis to properly understand this aspect, which often is not considered in the initial stages of projects.
One of the significant advantages of these newer coatings is their improved performance under dynamic loads. Their flexible polymer compositions can absorb and mitigate stress, making them less susceptible to cracking compared to their more rigid predecessors. This property is crucial in environments with frequent vibrations or cyclical stress.
These new coatings also tend to maintain adhesion in humid environments, unlike several traditional coatings that struggle under those conditions. This attribute is especially beneficial in coastal or highly humid regions where maintaining adhesion under wet conditions is important for structural integrity. How well this is sustained long-term still needs to be assessed with further research.
In addition, these high-performance coatings exhibit predictable aging patterns under stress. This predictability allows engineers to develop more accurate maintenance schedules, minimizing unexpected failures. Traditional coatings often degrade in a less predictable manner, necessitating more frequent inspections or replacing them more frequently.
Finally, several of these coatings are designed with compatibility in mind for use with newer sensing technologies and structural health monitoring systems. This integration potential could offer continuous real-time data about the health of a steel structure, potentially improving the reliability and safety of these components. These advancements could profoundly impact the field of structural monitoring, but extensive evaluation is needed to ensure that this potential is realized.
While these new coatings hold a lot of promise, the field is still developing. It is likely that a more sophisticated understanding of these materials and their optimal applications will continue to emerge with further research and development.
New Study Reveals Optimal Surface Preparation Techniques for Slip-Critical Connections in Steel Structures - Fretting Fatigue Considerations in Long-Term Connection Durability
The long-term durability of bolted connections in steel structures, especially those designed for slip-critical applications using high-strength steel, can be significantly impacted by fretting fatigue. This phenomenon involves the repetitive microscopic movement at the contact surfaces of bolted joints under cyclic loading, which generates localized stresses. While increased bolt preload can improve fatigue life, the complex interaction of various factors related to fretting damage makes it difficult to predict and design for its effects. Fretting fatigue can be a primary cause of failure in these types of connections, often surpassing other potential failure modes. A deeper comprehension of the mechanics of fretting fatigue is necessary to develop solutions that extend the lifespan and reliability of these structural elements. Further research is needed to refine design practices and mitigate fretting fatigue to ensure that slip-critical connections meet the demanding requirements of modern steel structures.
Fretting fatigue, a type of material failure, arises at the contact points within structural connections. It's driven by tiny movements between surfaces under load, leading to wear and a decline in the material's ability to withstand repeated stress. This process can significantly shorten the lifespan of a connection, making it crucial to address in design.
Blast cleaning's creation of surface roughness can influence fretting fatigue. A rougher surface might enhance the interlocking between the joining components, but it can also concentrate stress, posing a design challenge in finding a balance between optimal surface texture and fatigue resistance.
The abrasive action of blast cleaning doesn't just change the surface; it can also modify the underlying structure of the steel. These alterations, which might include smaller grain size or changes in internal stresses within the metal, can modify fatigue characteristics and affect the connection's durability.
Corrosion and fretting fatigue are intertwined. If corrosion occurs, the resulting byproducts can act like abrasive particles, worsening fretting wear, and potentially leading to serious issues, especially in slip-critical connections, where even minor slippage can have major consequences. It highlights the need for effective surface preparation and protective coatings.
Dynamic loading conditions amplify the interaction between fretting and fatigue. Research suggests that even minor variations in the bolt tension can significantly impact fretting behavior, reinforcing the necessity for precise bolt installation techniques and consistent preload.
Temperature fluctuations can also impact material behavior and joint interface adhesion. For example, heat can soften adhesives or coatings, making the connection more susceptible to fretting, underscoring the importance of material choices suited to the environment the connection will be in.
While certain coatings aim to reduce friction and improve performance, unsuitable lubrication can actually exacerbate fretting. Grasping the relationship between lubrication, coatings, and friction is essential for designing high-performing slip-critical connections.
The application of advanced monitoring methods like acoustic emissions or vibration analysis allows for the early identification of fretting fatigue signs. This proactive approach, through immediate inspection, can potentially extend the connection's operational life.
Slip-critical connections that use high-strength bolts often present fretting fatigue issues. Optimal bolt design and careful management of preload are crucial to mitigating risks by efficiently distributing the loads and maintaining tension within acceptable parameters.
The choice of coating material significantly influences fretting fatigue resistance. Certain polymer-based coatings have demonstrated better fatigue performance than traditional materials, suggesting that material innovation could change established practices in slip-critical applications. This provides more opportunities for further research in the field.
New Study Reveals Optimal Surface Preparation Techniques for Slip-Critical Connections in Steel Structures - Seismic Zone Applications Highlight Importance of Proper Preparation
Seismic zones demand that steel structures are exceptionally robust and resilient, especially where slip-critical connections are used. A recent study highlights the crucial link between how surfaces are prepared and how well a steel structure withstands seismic activity. If proper surface preparation isn't done, it can significantly weaken the structure during an earthquake. This study reveals that we still don't fully grasp how surface preparation affects structures at the microscopic level, and this gap in knowledge is a potential vulnerability in design. Further, it suggests that strategies based on optimization principles related to earthquake engineering could pave the way for developing more resilient structures. Steel structures in seismic zones are constantly being re-designed and refined to handle earthquakes. This study emphasizes how important it is to apply what we've learned from past earthquake events to current building practices. Essentially, this research calls for a more thorough understanding of surface preparation to make sure these critical structures remain safe and reliable for years to come.
Seismic zones present a unique set of challenges for steel structures, especially when considering the performance of slip-critical connections. Research indicates that maintaining consistent bolt preload is critical, as even minor reductions under dynamic loads, like vibrations, can increase the risk of slippage. This finding highlights the importance of not only the initial tightening of bolts but also ongoing monitoring to ensure connection stability.
While we typically think that creating a rough surface improves how well parts lock together, overzealous surface preparation techniques can create excessively rough surfaces. These overly rough surfaces can cause stresses to concentrate in specific areas of high-strength steel joints, leading to a reduction in fatigue resistance. Finding the right balance between surface texture and fatigue life is a vital design consideration.
The phenomenon of fretting fatigue is complex. Not only is it impacted by the initial bolt preload, but also environmental factors like humidity and temperature can alter how effectively a coating performs, making the design of slip-critical connections even more challenging.
The surface preparation process can unintentionally alter the steel's internal structure. For example, blast cleaning can alter the grain size of the steel. These changes can lead to either improvements or declines in the steel's ability to withstand fatigue. This is an area where further research can provide critical insights for designers.
Interestingly, research shows that even minor changes in bolt preload during dynamic loading have a significant effect on how fretting fatigue behaves. This points to a need for carefully managed tightening procedures and a clear understanding of preload and torque tolerances during assembly of slip-critical connections.
Corrosion can play a significant role in connection performance. Corrosion products can act like abrasive particles, making fretting fatigue worse. This means that optimal surface preparation is just one part of the solution; we also need effective corrosion prevention strategies to prevent early failures.
The prospect of incorporating real-time monitoring systems is exciting. Sensors could allow us to detect the signs of fretting fatigue early on. If this development matures, it could completely change how we maintain steel structures and their components.
The choice of coating material can have a dramatic influence on the long-term performance of connections. There are newer polymer-based coatings that show a lot of promise in terms of reducing fretting fatigue. These newer materials could shift how connections are designed and assembled in the future.
We need to better understand how temperature influences the adhesion of various coatings. While some coatings perform better under high temperatures, excessive heat can weaken bonds and increase the likelihood of fretting fatigue. It's critical to select materials that match the specific environment of the structure.
Although higher performance coatings may initially be more expensive, they can ultimately be more cost-effective over a structure's lifetime. This is because they can potentially last longer and reduce the need for maintenance, thus lowering overall costs. This leads us to think that including a life-cycle cost analysis in the initial stages of design is more critical than before.
More Posts from aistructuralreview.com: