New ASME BPVC Section IX Updates Implications for Pressure Vessel Welding Certification in 2024
New ASME BPVC Section IX Updates Implications for Pressure Vessel Welding Certification in 2024 - Key Changes in ASME BPVC Section IX for 2024
The 2024 edition of ASME BPVC Section IX brings about a set of revisions that will become mandatory for new welding qualifications beginning in January 2024. These changes are primarily centered around welder, brazer, and welding machine operator qualifications and requalification procedures. A key theme of these updates is a tighter integration of welding qualification requirements with other sections within the BPVC code, specifically concerning manufacturing components. The revisions aim to improve the clarity surrounding welding procedure qualifications, which is vital for ensuring consistency in application. These adjustments appear to be driven by a combination of keeping pace with modern welding technologies and practices, as well as continuing efforts to enhance the overall safety of pressure vessel construction. While these modifications are presented as incremental improvements, they underscore the ongoing commitment to refining the code and adapting it to current industry standards. Whether the changes will be universally received as improvements remains to be seen, but they definitely highlight the evolving nature of pressure vessel manufacturing and its associated quality control measures.
ASME BPVC Section IX's 2024 edition, effective for new qualifications from January 1st, 2024, necessitates a closer look at how welding certification is handled. It appears the emphasis has shifted towards a more rigorous approach to welder, brazer, and welding machine operator qualifications. This includes an increase in the number of tests needed for some materials, which could potentially raise the bar for certification and the skill level of certified individuals.
The updates seem to be intertwined with the manufacturing requirements of other sections within the BPVC code, as they directly address welding, brazing, and fusing procedures. This creates a tighter connection between the various aspects of pressure vessel construction. It's fascinating to observe this renewed emphasis on procedure qualification, which has been a focus of these bi-annual revisions. The last major revision in 2023, along with these changes, signals a continuous improvement effort in the code.
The 2024 version reflects input from industry leaders, acknowledging that the field of pressure vessel construction is constantly evolving. The new Summary of Significant Changes books, designed for each section, are definitely useful for navigating the intricate details of the revisions. One of the aims is to enhance clarity within the code, potentially minimizing ambiguity regarding the necessary steps for procedure qualification. They've also attempted to ensure the code remains aligned with the latest technological advancements and common practices within the industry.
The overall impression is that they are trying to increase standardization and safety across the field of pressure vessel production. Considering that this code acts as a standard globally, including for nuclear facility components, the implications of these revisions are broad. It will be insightful to see how these changes impact practices in different sectors. Whether these revisions achieve their intended effect of increased safety and harmonized practices will be something to monitor over the coming years. It remains to be seen how readily these changes are integrated into the manufacturing procedures of the industry.
New ASME BPVC Section IX Updates Implications for Pressure Vessel Welding Certification in 2024 - Impact on Welder Qualification Procedures

The 2024 updates to ASME BPVC Section IX bring about notable changes influencing how welder qualifications are handled. One of the more significant revisions is the introduction of broader conditions under which welders can use any relevant Welding Procedure Specification (WPS). This shift suggests a potential for greater flexibility in the qualification process. Furthermore, the updates generally lean towards a more demanding set of testing requirements for welders. This could raise the bar for welder certification, potentially requiring a higher level of skill and knowledge from those seeking certification. These changes aim to elevate both safety and quality control within the field. It's also likely that the updates reflect the continuous development of new welding technologies and methods. The impact of these revisions on welding practices and how certifications are administered across various industries will be an interesting observation point going forward. The long-term implications of this shift on the field of pressure vessel construction and its safety standards will be worth monitoring.
The revised ASME BPVC Section IX, effective for new qualifications starting in 2024, introduces changes that could impact the timeframe of projects, particularly if more rigorous material-specific tests are needed for welder qualification. Interestingly, improvements in non-destructive testing appear to have influenced these updates, potentially requiring welders to demonstrate proficiency in identifying and interpreting previously undetectable defects. This suggests a shift towards more thorough quality control practices.
Another noteworthy adjustment is the introduction of new qualification tiers for specialized materials, like high-strength steels and nickel alloys, which were not as rigorously defined in earlier versions of the code. This increased specialization might create a temporary shortage of qualified welders, as existing personnel may need to recertify under the new, stricter requirements. It remains to be seen if the industry has sufficient workforce readiness for this transition.
The revised emphasis on procedure qualification highlights the need for better communication and coordination between engineering and production teams, which could ultimately improve the process. These changes align with a larger trend in engineering towards more holistic approaches, connecting design, manufacturing, and inspection in pressure vessel construction. This increased integration could lead to enhanced quality and consistency across the entire manufacturing process.
There's a possibility that these changes will also impact project costs, as companies may have to invest more in training and documentation to satisfy the increased standards. The clarifications provided regarding procedure qualification requirements suggest that regulatory compliance will become more systematic and involve significantly more documentation. Additionally, these alterations hint at a growing global awareness of variations in welding practices, leading to a potential future alignment of ASME standards with international codes. This could influence the landscape of global trade within the pressure vessel sector.
One of the more significant shifts introduced is the explicit requirement for continuous welder training and evaluation. Previously, certification often felt like a one-time event. Now, ongoing professional development is a focal point, suggesting a growing emphasis on maintaining and enhancing welder skills over their career. The long-term impact of these revisions on safety and industry practices is an area that bears close monitoring.
New ASME BPVC Section IX Updates Implications for Pressure Vessel Welding Certification in 2024 - New Requirements for Welding Documentation
The revised ASME BPVC Section IX, effective for new qualifications starting in 2024, significantly changes the requirements for welding documentation. These changes emphasize a more thorough approach to documenting welding procedures and welder qualifications. Specifically, there's a new focus on creating detailed Weld Procedure Specifications (WPS), Procedure Qualification Records (PQR), and Welder Performance Qualifications (WPQ). These documents must demonstrate compliance with the updated essential variables laid out in Table QW-2881, which cover various welding processes. The updated code also includes Appendix K, which is now mandatory, providing guidance on incorporating the requirements of Section IX into other standards and codes. These revisions are a response to advancements in welding technology and methods, aiming to increase consistency and improve safety in welding practices related to pressure vessel construction. The changes will necessitate a significant shift in how documentation is handled, with a focus on enhanced clarity and procedural rigor, likely impacting how welding certifications are obtained and potentially raising the bar for industry standards.
The 2024 revisions to ASME BPVC Section IX introduce several notable changes to welding documentation requirements, particularly impacting welder qualification procedures. One key shift is the increased emphasis on qualification testing, especially for materials like high-strength steels, which could lead to extended project durations due to the need for more frequent and detailed testing.
Interestingly, the new edition offers more latitude in the types of Welding Procedure Specifications (WPS) welders can utilize for qualification. While this can potentially improve workflow, it also necessitates a greater understanding of the range of WPS, potentially posing a new challenge for ensuring consistent application.
Furthermore, the code now features more specialized qualifications tailored to advanced materials such as nickel alloys. This level of material-specific qualification might create short-term workforce shortages if the existing pool of qualified individuals isn't adequately prepared for these stringent requirements.
Another substantial adjustment is the introduction of a requirement for continuous welder training and evaluation, a departure from previous, more static certification processes. This shift towards lifelong learning could fundamentally impact how organizations manage welder workforce development, shifting the focus from a one-time certification to a continuous professional development model.
The revisions also place a heavier emphasis on the use of non-destructive testing (NDT) techniques. This increased focus on NDT indicates a growing trend within the industry to enhance quality control by proactively identifying defects that may have been missed previously.
Companies may experience a notable impact on their operating costs due to increased requirements for detailed documentation around welding procedures and welder qualifications. Keeping track of this more extensive documentation will likely necessitate a significant increase in resource allocation.
These updates suggest an increasing alignment of US welding practices with international codes and standards. This step toward harmonization has the potential to smooth the path for global trade in the pressure vessel sector. However, it could also pose challenges for businesses that are accustomed to working within a solely US-centric set of regulations.
The revisions emphasize the importance of improved communication between engineering and manufacturing teams. This change could foster a more collaborative environment conducive to a greater emphasis on quality control. It remains to be seen whether this improved communication translates into a more efficient and effective workflow within pressure vessel manufacturing.
These stricter regulations might necessitate substantial upskilling or retraining for the existing welding workforce. This potential need for broader skills and competencies could lead to both a shortage of qualified individuals and an increase in wages for welders.
Finally, the overarching theme of these updates appears to be a heightened focus on quality control through thorough welding procedure qualifications. This heightened focus on procedural documentation and a culture of procedural adherence might lead to improved safety outcomes and a reduction in incidents in the pressure vessel sector. It will be interesting to see the long-term effects of these adjustments on industry practices and safety records.
New ASME BPVC Section IX Updates Implications for Pressure Vessel Welding Certification in 2024 - Alignment with Global Pressure Vessel Standards
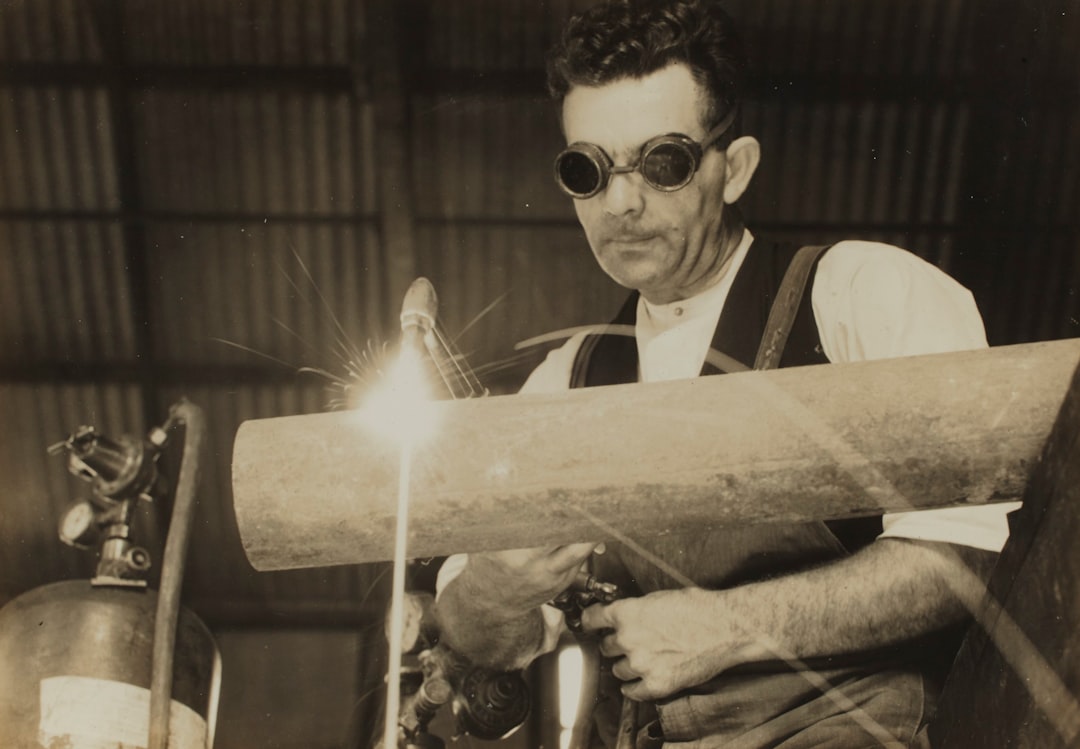
The latest revisions to ASME BPVC Section IX aim to better align pressure vessel standards with global practices. These updates emphasize stricter requirements for welding certifications and associated documentation, pushing for improved safety and consistency across the industry. The focus on ongoing professional development for welders reflects a worldwide trend of promoting continuous learning and updated skills. Furthermore, by creating more specialized certifications for advanced materials, the code seeks to address the diverse requirements of the modern industry. These changes aren't just about adhering to safety regulations, they are also designed to improve integration with global manufacturing processes, potentially changing how pressure vessels are both produced and certified internationally. While the intention is to harmonize standards, whether it will truly enhance the sector or lead to unintended complications remains to be seen. There is also a potential for resistance or challenges to adopting the new standards, given the potential impact on existing certification practices and the welding workforce. However, the drive towards uniformity is clear.
The 2024 ASME BPVC Section IX revisions seem to be strongly influenced by the push for greater global alignment in welding standards. This suggests a growing trend towards harmonizing welding practices across the globe, potentially impacting how pressure vessel construction is conducted worldwide. The revised standards, particularly for specialized materials like high-strength steels and nickel alloys, are introducing a level of detail and scrutiny that could dramatically change the manufacturing process for these materials. It's interesting to note that the updated code might lead to a substantial increase in qualification tests, potentially doubling or tripling the number of required tests for certain materials. This shift towards more frequent testing could significantly impact project timelines, potentially lengthening them due to increased testing and evaluation cycles.
Another fascinating change is the greater integration of non-destructive testing (NDT) into the welder qualification process. This signals a greater emphasis on proactively identifying potential weld defects, placing a higher premium on both the practical skills and theoretical knowledge of welders. The revisions also include a provision for broader WPS usage, which can provide greater flexibility, but also poses the risk of inconsistencies if there is insufficient training to ensure appropriate WPS application. This new focus on documentation is quite significant. The 2024 changes require a more rigorous approach to record-keeping, specifically in relation to PQRs and WPQs, which could add an administrative layer to existing processes. This increase in documentation will likely necessitate investments in both training and record management, potentially impacting resource allocation and project costs.
It's noteworthy that this revision shifts the paradigm of welder certification towards a continuous learning model. The focus on ongoing training and evaluation reflects a broader trend toward lifelong professional development. This is a substantial departure from traditional certification methods, which may reshape how organizations approach the management and development of their welder workforce. The shift towards stricter qualifications for specialized materials, however, might trigger a short-term labor shortage, especially if the current welder population doesn't possess the skills to meet the new requirements. Recertification under these stricter standards could pose a challenge to many experienced welders.
Increased documentation and qualification requirements will also likely translate into higher operational costs for businesses. The new standards mandate a more thorough and formalized compliance approach, potentially requiring investment in training, documentation tools, and changes to workflows. While these revisions aim to improve safety, it remains to be seen how effectively they translate into enhanced safety outcomes in the real world. Just because regulations increase doesn't necessarily mean safety automatically improves. The pressure vessel welding industry needs to carefully balance the increased compliance requirements with the practical application of the updated code to ensure that any potential gains in safety are truly realized.
New ASME BPVC Section IX Updates Implications for Pressure Vessel Welding Certification in 2024 - Training Needs for Industry Professionals
The revised ASME BPVC Section IX, effective for new qualifications starting in 2024, underscores the importance of ongoing training for those working in pressure vessel welding. The updated code introduces more stringent requirements, including expanded testing for specialized materials and a mandate for continuous welder training. This signifies a shift away from the idea of certification as a one-time event towards a more dynamic approach focused on ongoing skill development. This evolution is a direct response to the increasing sophistication of welding processes and a heightened emphasis on maintaining the highest safety and quality standards. To effectively meet the demands of these updated standards, professionals will need to adapt by participating in continuous learning programs and keeping their expertise current. The transition to these new standards may present challenges for organizations seeking to ensure their workforce is prepared, possibly leading to a temporary shortage of qualified individuals until they can bridge the skills gap. This evolving regulatory landscape necessitates a commitment to ongoing training and development in order to maintain competence and ensure compliance.
The recent updates to ASME BPVC Section IX, effective for new certifications starting in 2024, have introduced a number of changes that demand a closer look at the training needs of industry professionals. Notably, the concept of indefinite welding qualifications is gone, with certifications now needing periodic renewal. This emphasizes the necessity of ongoing professional development to maintain up-to-date skills in a rapidly evolving field.
These updates have also woven together welding qualifications with other manufacturing aspects, suggesting that professionals might need to branch out into related fields like materials science and non-destructive testing. This cross-disciplinary approach highlights the growing need for multi-skilled individuals in pressure vessel manufacturing.
However, this shift towards a broader skillset might not be entirely seamless. The stricter requirements for qualification testing, especially for specialized materials like high-strength steels and nickel alloys, will likely increase project lead times. The added time needed for rigorous testing procedures could disrupt current project timelines, adding new logistical challenges.
A major implication is the strong emphasis on continuous learning. Welder qualifications are no longer a one-time event, instead, they demand ongoing skills assessments, reflecting a move towards a more adaptive workforce. This is a clear response to the accelerating pace of technological advancements in welding.
Another challenge arises from the creation of specialized certifications for various materials. While these targeted qualifications enhance precision, they also risk creating a skills gap. Many currently certified welders might not meet the stricter standards, potentially creating short-term workforce shortages in specific areas.
The updated code significantly emphasizes meticulous documentation, with mandates for detailed WPS, PQRs, and WPQs. While this creates a robust trail of evidence and increases quality control, it also shifts a substantial administrative burden onto organizations, particularly smaller ones, who might struggle to maintain this level of record-keeping.
Additionally, the updates could lead to a marked increase in the frequency of testing, especially for specific materials. While this rigorous approach improves quality assurance, it potentially creates strain on existing testing facilities and their resources. It raises the question of whether existing testing facilities can handle this surge in demand effectively.
With a push towards aligning ASME BPVC standards with global norms, there's an inherent tension as organizations transition away from a US-centric framework to a more globally harmonized one. This will require a thoughtful adaptation process to manage the transition and potential resistance from those used to the existing regulations.
The updated standards might contribute to higher operational costs for manufacturers. Investments in new training programs, documentation tools, and administrative support will become crucial to ensuring compliance with these revised standards, leading to an overall increase in expenses.
Finally, the increased importance of non-destructive testing in welder qualifications signals a shift towards proactive defect identification. This puts more pressure on welders to not just execute welds, but also possess a critical eye for assessing the quality of their own work. This evolution in training and evaluation needs to be carefully managed.
In conclusion, the updated ASME BPVC Section IX calls for a significant overhaul in the training landscape for pressure vessel welding professionals. It introduces a new era of ongoing training and stricter certifications, leading to both increased safety and potential complexities. It's essential to carefully consider these changes and how best to navigate the training challenges ahead to ensure both a qualified and robust workforce and a smooth transition for the industry.
New ASME BPVC Section IX Updates Implications for Pressure Vessel Welding Certification in 2024 - Safety Enhancements in Pressure Vessel Manufacturing
The latest revisions to the ASME Boiler and Pressure Vessel Code (BPVC), specifically Section IX, represent a significant effort to enhance safety within pressure vessel manufacturing. These changes, effective for new certifications in 2024, prioritize stricter welder qualifications and a more rigorous documentation process, encouraging a continuous learning environment for professionals. This move towards higher standards is clearly a response to the ongoing evolution of welding technology and a desire for alignment with global best practices. The updates, however, don't come without potential challenges, as the increased integration of non-destructive testing could impact workforce preparedness and operational costs for companies. Despite this, the overarching goal is to bolster safety outcomes by ensuring that pressure vessel manufacturing methods remain reliable and adaptive within the current industrial landscape. It's uncertain if all of the new requirements will actually improve safety, but the intent is there.
The 2023 ASME Boiler and Pressure Vessel Code (BPVC) revisions, released in April 2023, particularly those affecting Section IX, highlight a fascinating shift in the landscape of pressure vessel welding. It seems that the use of advanced materials like high-strength steels and nickel alloys in pressure vessel construction has outpaced the existing welding qualification and techniques. This has led to the need for changes in qualification standards and welding methods to ensure safer manufacturing practices.
Interestingly, these changes are closely tied to the evolution of non-destructive testing (NDT) techniques. Welder qualifications are no longer just about welding proficiency; they now require a deeper understanding of these advanced inspection techniques, demanding that welders can effectively identify potential defects during production.
One of the more striking aspects of the revisions is the potential impact on the frequency of welder qualification testing. In some cases, especially for materials like high-strength steels, the new code could require twice or even thrice the number of tests. This will put considerable stress on existing testing facilities and might cause projects to take longer to complete as more testing and evaluation steps are added.
Further complicating matters is the move towards continuous welder training and evaluation. The days of earning a qualification and holding it indefinitely seem to be over. Instead, welders are now expected to be part of a continuous learning loop, with periodic assessments to keep their skills up to date and ensure continued compliance. This is certainly a departure from traditional certification practices.
This continuous learning requirement, coupled with the increased focus on meticulous record-keeping, adds another layer of complexity. The revisions mandate detailed Weld Procedure Specifications (WPS), Procedure Qualification Records (PQR), and Welder Performance Qualifications (WPQ), creating a more robust audit trail. While this certainly promotes quality control, it could place an undue burden on smaller companies with limited administrative resources.
It seems the ASME BPVC is also responding to a broader global push for harmonized welding standards. The updated standards demonstrate a notable shift towards aligning with international practices, potentially smoothing the path for increased global trade in pressure vessels. However, this also poses potential difficulties for companies that operate primarily within the U.S., requiring them to adapt to a more internationally focused standard.
The changes in the 2023 BPVC also indicate a push towards a more holistic approach to welding. Welders might need to expand their knowledge to encompass related disciplines like materials science. This cross-disciplinary trend implies that the ideal welder of the future will have a broader understanding of the entire process, from material properties to final inspection.
However, this shift could present some unforeseen consequences. For example, the stricter qualification requirements and specialized certifications might cause a short-term shortage of qualified welders, particularly those equipped to work with advanced materials. It remains to be seen if enough welders can adequately meet these new standards.
Another point of concern is the possible impact on businesses' operating costs. The necessity for continuous welder training programs, updated documentation practices, and perhaps even new technologies to maintain compliance with the updated standards could significantly affect a company's profitability. It's important to assess how these new costs will be absorbed by the industry.
Ultimately, the fundamental aim of the 2023 ASME BPVC revisions is to improve safety within the pressure vessel industry. The more detailed and standardized procedures, and the increased focus on continuous learning, are designed to minimize incidents. However, only through extended tracking of accident rates and other safety metrics over the coming years will it be possible to determine if these changes result in tangible improvements in safety outcomes. Whether these shifts in practice will significantly reduce incidents and contribute to a higher standard of safety across the industry remains a question to be answered over time.
More Posts from aistructuralreview.com: