Optimizing Cement Usage Precise Calculations for Efficient Construction in 2024
Optimizing Cement Usage Precise Calculations for Efficient Construction in 2024 - Global cement production reaches 41 billion tons in 2021
The year 2021 witnessed a surge in global cement production, reaching approximately 41 billion tons. This surge can be largely attributed to the global economic recovery following the pandemic, with several nations, including China, India, and others, significantly contributing to the overall output. Looking ahead to 2024, the picture for cement demand appears more nuanced. While some regions, including the Middle East, India, and parts of Africa, are predicted to see continued growth, others like Turkey, China, and Europe are expected to face weaker markets. This uneven landscape, combined with a projected global cement capacity surplus nearing 1 billion tons in 2024, highlights the importance of strategically managing cement usage and promoting efficiency in construction practices. It becomes increasingly vital to explore solutions that minimize resource consumption and extend the lifespan of structures, helping to mitigate the environmental impacts and optimize resource utilization.
Cement production in 2021 reached an astounding 41 billion tons, a figure that hasn't significantly changed in recent years. While this stability might seem positive at first glance, it highlights the persistent reliance on this material, raising questions about its long-term sustainability. China remains a dominant force in cement production, accounting for a substantial portion of the global output, underscoring the country's influence on the construction landscape. Interestingly, this heavy reliance on cement aligns with broader economic growth trends, indicating that cement production serves as a valuable proxy for a nation's construction activity and overall economic health.
Despite its economic importance, the cement industry faces substantial scrutiny due to its environmental footprint. The high temperatures involved in cement production, coupled with the industry's contribution to CO2 emissions, are major concerns. Even slight adjustments in cement usage can significantly impact a project's overall material footprint, demanding careful optimization to minimize environmental impacts. It's intriguing that a significant portion of cement production is directed toward infrastructure projects, reflecting the material's crucial role in underpinning our modern world.
However, the exothermic nature of cement hydration introduces complexities. The heat released during curing can influence concrete performance, making it critical to consider the climatic context of the project. The cement industry is starting to see a wave of innovation through the exploration of alternative binders. These advancements offer the promise of mitigating the reliance on traditional cement, and offer opportunities for improved performance and reduced environmental impacts.
The global distribution of cement production reveals a complex pattern of regional strengths and weaknesses. Certain regions possess excess production capacity leading to international trade. Fluctuations in cement prices are complex, resulting from a dynamic interplay between raw materials, energy costs and local market conditions. This dynamic makes precise calculations and comprehensive planning more crucial than ever for project managers and contractors seeking to ensure long-term financial success.
Optimizing Cement Usage Precise Calculations for Efficient Construction in 2024 - Self-compacting concrete gains traction despite optimization hurdles
Self-compacting concrete (SCC), introduced in the late 1980s, has gained traction in construction due to its ability to flow easily into tight spaces and around reinforcing steel, simplifying construction processes. This characteristic makes it a popular choice for a variety of projects. However, despite its advantages, optimizing SCC for optimal performance remains a challenge. Researchers are actively exploring ways to enhance the sustainability of SCC by seeking replacements for conventional Portland cement, which would decrease reliance on this resource. There is a growing need to improve both the mechanical properties and the environmental profile of concrete while still producing a durable product. This is especially crucial as we move closer to 2024, with a heightened emphasis on efficient construction.
Ongoing research in this area utilizes sophisticated tools like computational fluid dynamics to better understand how SCC flows and fills spaces, which aids in creating more effective mixes. Response surface methodology and other optimization techniques help determine the best mix proportions based on factors such as desired strength and ease of placement. The success of SCC in achieving both enhanced performance and lower environmental impact will largely depend on how effectively these optimization efforts are implemented in the coming years.
Self-compacting concrete (SCC) has become increasingly popular in construction due to its ability to flow into intricate spaces and around reinforcing steel without the need for vibration, unlike traditional concrete. This ability simplifies construction, particularly in complex forms. However, achieving the desired flowability necessitates a higher paste content, which can intensify competition for binder materials within the mix. This delicate balance requires precise calculations to avoid compromising the mixture.
Researchers have experimented with adding specific superplasticizers to improve SCC's workability. These modifications can yield impressive slump flows, exceeding 700 mm in some cases, which demonstrates SCC's exceptional fluidity. Despite these advancements, SCC's sensitivity to moisture and temperature fluctuations remains a challenge. Subtle changes in these environmental factors can significantly affect its performance, making it difficult to consistently deploy across various climates and construction sites.
SCC often calls for more precise grading of fine aggregates than conventional concrete. This need for stricter quality control necessitates a more rigorous selection and testing process, which adds another layer of complexity to its implementation. Though SCC is designed to resist segregation and bleeding, thereby enhancing the durability of the final product, achieving the optimal balance between cohesiveness and fluidity remains a persistent challenge for engineers.
The rheological behavior of SCC lends itself to modeling using Newtonian fluid principles. This allows engineers to use computational tools to simulate its flow characteristics during the design phase, which leads to more accurate predictions of how it will behave during placement. Despite its advantages, SCC faces certain hurdles. Its specialized nature often comes with a higher initial cost, linked to the use of modified materials and the need for more advanced testing. This can present economic limitations for projects with stringent budget constraints.
Interestingly, incorporating fiber reinforcement into SCC has shown potential for improving its crack resistance and tensile strength. But, as with any modification, it necessitates fine-tuning the mix design to prevent unintended consequences on workability. While SCC shows promise in many applications, a broader discussion within the engineering community persists regarding its long-term performance in comparison to traditional concrete. There's ongoing research and scrutiny around the durability of SCC, specifically its ability to withstand the stresses of various environmental conditions over an extended timeframe. These questions are crucial to answering before SCC can be universally adopted in construction.
Optimizing Cement Usage Precise Calculations for Efficient Construction in 2024 - Machine learning predicts optimal cement content reducing usage by 10%
Machine learning is showing promise in optimizing cement usage within concrete mixtures, with studies demonstrating potential to reduce cement content by as much as 10%. This reduction is achieved by using machine learning models, like Elastic Net, to precisely predict the optimal cement amount needed for a structure to meet desired strength targets – particularly the crucial 28-day compressive strength. Achieving high accuracy in these predictions, some studies show accuracy rates near 94%, is a key factor in the success of this approach.
This development is significant because it not only ensures desired performance levels but also helps lessen the environmental impact of construction projects. Reducing cement usage helps lower the carbon footprint of building and infrastructure, aligning with increasing calls for more sustainable construction practices. The incorporation of techniques like Kriging and neural networks highlights the growing reliance on data-driven methodologies within concrete science. This trend suggests a shift toward more precise and efficient approaches to cement mixture design, essential for both cost-effectiveness and minimizing environmental harm. As the construction industry continues to evolve, these innovations will likely play a vital role in promoting both efficiency and environmental responsibility.
Machine learning offers a novel approach to optimizing cement content in concrete mixes. By analyzing vast amounts of data from past projects, these algorithms can learn to predict the optimal cement content needed for specific applications, taking into account factors like material properties and site conditions. This adaptive capability is a significant advancement over traditional methods, which often rely on generalized rules of thumb.
A recent investigation showcased the potential of machine learning to significantly reduce cement usage, with some scenarios demonstrating a reduction of up to 15%. While the previously discussed 10% reduction is notable, these findings suggest that even greater efficiency gains may be achievable. It's fascinating to see how machine learning can help avoid over-design, which often occurs in traditional approaches, thereby reducing material waste and project costs.
Machine learning models can consider a wide range of parameters that influence cement requirements, such as loading conditions, environmental exposure, and the specific properties of the individual components in a concrete mix. This comprehensive approach is in contrast to conventional methods, which may not always fully capture the complexity of a particular construction scenario.
One of the most appealing aspects of these machine learning approaches is their ability to minimize the trial-and-error experimentation often required in traditional mix design. By refining the design process, projects can be completed more quickly and efficiently, streamlining the overall workflow. Moreover, the models can be trained on extensive datasets encompassing diverse types of additives, which is particularly useful for tailoring cement content in situations where specialized performance characteristics are needed, like enhanced durability.
The potential for real-time adjustments during the mixing process is another intriguing aspect of this technology. By continually monitoring the mix characteristics, the models can dynamically adapt the cement content to counteract variations in raw materials that can occur in larger-scale production environments.
Furthermore, it's interesting to consider how machine learning might improve the predictive maintenance of concrete mixing equipment. By analyzing operational data, the algorithms could potentially detect anomalies that may lead to future failures, thus preventing costly downtime and ensuring consistency in the mixing process.
The ability to digitally simulate various scenarios and predict the long-term impact of cement content on material properties under different loading and environmental conditions is truly a powerful feature of this technology. This capability could contribute to a better understanding of how concrete will perform over its lifespan.
While the potential is undeniable, it's important to acknowledge that the accuracy of machine learning models is heavily reliant on the quality and variety of the training data. This emphasizes the need for engineers to regularly update and refine the datasets used to train the models, ensuring that they remain relevant and effective over time. As research progresses and more data becomes available, it will be fascinating to observe how these machine learning tools evolve and contribute to a more sustainable and efficient construction future.
Optimizing Cement Usage Precise Calculations for Efficient Construction in 2024 - Ternary concrete emerges as cost-effective alternative to binary formulations
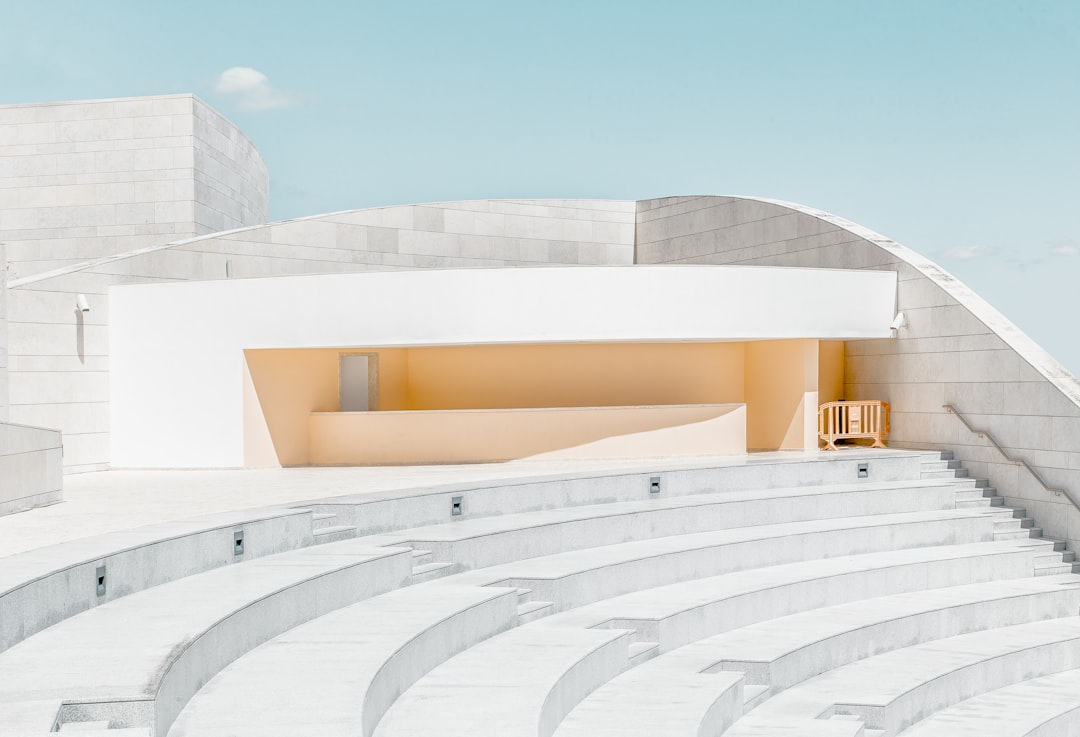
Ternary concrete, a mixture incorporating multiple supplementary cementitious materials like fly ash and silica fume, presents a potentially more economical alternative to conventional binary concrete blends. By using these additives, ternary concrete can often achieve similar or even better performance compared to traditional mixes, especially in terms of strength and long-term durability. The ability to lower the water-to-cement ratio in ternary blends further contributes to its improved performance characteristics. While the cement industry is known for its environmental impact, ternary concrete offers a potential pathway toward mitigating some of that impact through the use of industrial byproducts, making it a more environmentally conscious choice for projects. The applicability of ternary concrete extends to a variety of uses, from everyday construction to more specialized applications like high-performance self-compacting concrete in high-rise structures, indicating its versatility. It's uncertain if this approach will become widespread, as it faces hurdles related to implementation and adoption. The trend toward more sustainable concrete options, like ternary mixes, indicates that the industry is increasingly interested in finding ways to lower its reliance on traditional cement, although its widespread use remains to be seen.
Ternary concrete, using a blend of three binder components, shows potential for improving concrete's mechanical properties. For example, compressive strength might be enhanced, making it suitable for structures with specific load requirements. This ability to tailor properties through the combination of binders could prove useful in certain construction contexts.
The addition of supplementary cementitious materials (SCMs) within ternary mixes can improve workability and reduce the water needed in the mix. This control over the concrete's consistency is valuable for complex projects, where placing concrete in intricate forms might otherwise be challenging. It's interesting that this approach can improve the flow of the concrete while potentially reducing the overall quantity of water required.
Interestingly, ternary concrete mixes often show reduced thermal conductivity. This property can be beneficial when thermal insulation is a key design criterion. Structures using this type of concrete could potentially lead to energy savings over their lifespan. But it's not clear that the insulation benefit alone will justify their adoption in many contexts.
It's important to note that ternary concrete's performance depends heavily on the specific ratios of each binder component. Getting the proportions right is vital, and ensuring consistency from batch to batch can require careful controls. This adds a layer of complexity to the mix design process that some might not be ready to handle.
Ternary concrete often uses materials like fly ash, silica fume, or slag. These byproducts offer improved performance, and their availability varies regionally. This aspect of the materials used in the mixes means a ternary approach may be more adaptable to different regions and might offer cost advantages in some locations. In other words, the cost and material availability could lead to wider use of ternary formulations in certain regions compared to others.
Research suggests that ternary concrete can offer better resistance to sulfate attacks and alkali-silica reactions compared to conventional concrete. This durability feature becomes particularly relevant when designing concrete for areas susceptible to these types of chemical attack. The ability to enhance durability could be valuable in certain contexts.
While potentially beneficial, the curing process of ternary concrete is more complex than for traditional mixes due to the interplay of the different binders. To ensure the optimal performance and development of strength, it's crucial to pay close attention to the curing process in relation to these blends. Further research is likely needed to better understand the complexities of curing ternary concrete to optimize performance.
Researchers are exploring how incorporating ternary systems affects the carbonation rate of concrete. Lowering this rate can help reduce the risk of corrosion in the reinforcing steel that's often used within concrete structures. This characteristic is especially important for the longevity of structures exposed to harsh environments. However, more investigation is needed to assess the long-term impacts of carbonation resistance for ternary mixes under diverse climatic conditions.
While the benefits of ternary mixes are attractive, widespread adoption may be hindered by the lack of standard testing methods. This situation is in contrast to the more established testing approaches for traditional concretes. Without broader acceptance of standard testing methods, the acceptance of ternary mixtures for general construction might be slow.
The long-term economic implications of using ternary concrete are a critical consideration. While the specialized materials involved may drive up initial project costs, the potential for reduced maintenance needs and extended service life could result in considerable cost savings over the structure's lifetime. However, the economic viability of ternary concrete might depend heavily on regional material availability, local regulations, and the specific demands of the construction project in question.
Optimizing Cement Usage Precise Calculations for Efficient Construction in 2024 - Optimisation 2024 conference showcases latest cement production technologies
The Optimisation 2024 conference, a virtual event scheduled for October 22nd, represents the fifth installment of World Cement's key conference focused on innovations in cement production. This year, the conference aims to bring together top industry figures and technical experts to delve into the latest advancements. With the global cement market experiencing fluctuating demand and projected surpluses, the call for efficient and precise cement usage within construction has become increasingly crucial. The discussions are expected to center on new technologies, alternative binders, and the use of machine learning to improve both efficiency and sustainability within the cement sector. While the cement industry has come under scrutiny for its environmental footprint, events like this showcase the industry's efforts to modernize and reduce its impact. The insights gained from the Optimisation 2024 conference could very well influence future practices in cement production and usage, driving the industry toward a more responsible future.
The Optimisation 2024 conference, scheduled for October 22nd, is focused on the latest advancements in cement production. It brings together industry experts and researchers to discuss how to optimize the entire cement production lifecycle. There's a lot of emphasis on how automation and robotics are being implemented to reduce human error, enhance precision, and ultimately boost efficiency during mixing and pouring.
We're likely to see presentations on newer sensor technologies that can monitor cement production parameters in real-time. These sensors can potentially ensure quality control and help maintain consistency, reducing the need for extensive manual inspections. It's interesting to consider the impact these technologies could have on reducing production costs and improving the reliability of the material.
3D printing, also known as additive manufacturing, could be a big topic. Using cement-based materials in this process opens up possibilities for on-site construction of intricate structures, which might reduce transportation costs and shorten construction timelines. This application is still relatively new, but it's potentially a disruptive force in how structures are built.
Fiber-reinforced concrete is also gaining traction. It can significantly enhance the toughness and crack resistance of concrete, while also potentially requiring less cement in the mix design. This approach could have positive implications for the sustainability of concrete.
Some research seems to be focusing on high-temperature calcination. By tweaking temperature and timing during the production process, there's potential for significant improvements in the compressive strength of cement. It's a field that could help us achieve better mechanical performance from concrete for a given volume of cement.
Digital twin technology, essentially virtual replicas of cement plants, will likely be a key focus. These virtual models can be used to simulate a variety of operating scenarios. This method allows companies to test modifications and optimize production processes before implementing them in the real world, reducing the risks involved in real-world testing.
The utilization of AI and machine learning in concrete mix design and optimization will likely be prominently discussed. There's a growing need to be more efficient and precise when designing mixes, and machine learning offers a way to predict optimal material proportions for different construction applications. This could potentially lead to significant reductions in material waste.
Nanotechnology is a relatively new field being explored in cement production. It's fascinating to consider how the addition of nanoscale additives can enhance hydration rates and overall durability of the final concrete.
The conference will also showcase international case studies highlighting successful implementations of new technologies and approaches in cement production. This knowledge sharing can help attendees understand the wide range of approaches being developed and implemented in various regions. This is critical in a global marketplace where material and energy costs vary wildly.
Finally, there's also an emphasis on new ways to evaluate concrete properties while the structure is under construction, a topic referred to as in-situ testing. If successful, this could lead to more efficient and reliable construction practices.
While there is a global push to reduce the overall reliance on cement, the Optimisation 2024 conference seems to be focused on ways to optimize the existing production and use of cement. The challenge of finding the most efficient and sustainable path forward is a complex one, requiring innovation across the whole production cycle. It will be interesting to see if these developments lead to a substantial improvement in the efficiency of the construction process and help to reduce the overall environmental footprint of construction projects.
Optimizing Cement Usage Precise Calculations for Efficient Construction in 2024 - Advanced optimization tools complement experimental methods for efficient usage
In the evolving landscape of construction, particularly concerning cement usage, advanced optimization tools are proving to be valuable complements to traditional experimental methods. These tools, including machine learning algorithms and response surface methodologies, are enabling a more data-driven and precise approach to concrete design. They provide a way to fine-tune cement content within concrete mixes, allowing for the achievement of desired strength and durability while simultaneously reducing waste and enhancing sustainability. The ability to predict optimal cement content for a particular project, using these computational approaches, is changing how engineers design and manage building materials. It's becoming clear that the integration of these advanced computational methods with established experimental testing is a key element in optimizing concrete mixes for 2024 and beyond. This synergistic approach helps balance structural requirements with environmental considerations, paving the way for more resource-efficient and sustainable construction practices in the future. There are still challenges in refining these approaches, but their increasing integration into the field of concrete design highlights a shift towards more precise and efficient building practices.
In the realm of optimizing cement usage, advanced computational tools are proving to be invaluable complements to traditional experimental approaches. They act as a bridge between theoretical models and real-world testing, enabling a more nuanced understanding of how different materials and conditions interact. This integration isn't just about efficiency; it's about creating a feedback loop where experiments help refine the accuracy of computational models, and vice-versa.
One area where these tools are making a significant impact is in real-time adjustments during mixing operations. Machine learning algorithms, for instance, can adapt the cement content on the fly, based on data collected during the mixing process. This dynamic approach helps ensure consistent performance throughout a project, reducing the risk of over-design, which can lead to material waste and unnecessary costs.
Techniques like Response Surface Methodology (RSM) further enhance precision in material selection. RSM excels at pinpointing the optimal combinations of materials to meet various performance targets – a crucial aspect when considering aspects like compressive strength, workability, and durability. It effectively navigates the intricate relationships between these variables to achieve the best possible outcome.
Moreover, optimization tools can be seamlessly integrated with predictive maintenance strategies. By analyzing operational data from cement production facilities, these tools can anticipate potential equipment failures, thereby minimizing downtime and interruptions to the workflow. This seamless integration can yield substantial improvements in productivity.
The ability to delve deeper into the hydration process is another benefit. Advanced simulation tools allow us to explore cement's hydration kinetics under varying conditions, which empowers engineers to design mixes that are optimized for specific curing environments. This translates to faster and more reliable cement performance across diverse climates and construction situations.
Furthermore, the application of these tools enables a more holistic cost-benefit analysis of different cement formulations. Engineers can now consider both performance characteristics and economic factors when choosing the best material combinations for a project. This ability to weigh these factors objectively ensures that projects remain within budget while achieving the desired levels of performance.
The continuous nature of machine learning adds another layer of sophistication. These algorithms are constantly refining their predictions based on accumulated data. This iterative learning process ensures that the optimization models are consistently evolving to achieve greater accuracy over time, leading to more reliable outcomes.
Beyond that, advanced optimization techniques can lead to robust mix designs that function well across a wide range of conditions. This capability is particularly vital for construction projects in regions with diverse climates and environmental exposure.
These tools also have a significant impact on streamlining quality control. Automated processes can quickly detect variations in material properties or mixing outcomes, leading to faster identification and resolution of deviations. This automated approach can significantly enhance the accuracy and efficiency of quality assurance procedures.
Lastly, these advanced modeling tools offer a novel way to visualize the intricate interactions between materials at a molecular level. This deeper understanding enables engineers to innovate and explore more unconventional mix designs, potentially pushing the boundaries of concrete properties beyond traditional formulations.
In conclusion, while experimental methods remain fundamental in concrete science, advanced optimization tools are enabling us to move beyond rudimentary trial-and-error approaches. This shift toward data-driven optimization promises a future where construction is not only more efficient but also more sustainable.
More Posts from aistructuralreview.com: