Understanding Clinker Formation The Critical Phase in Modern Cement Production at 1400-1600°C
Understanding Clinker Formation The Critical Phase in Modern Cement Production at 1400-1600°C - Raw Material Composition and Temperature Control in Modern Cement Kilns
The performance of modern cement kilns hinges on the careful balancing act between raw material composition and precise temperature control. Achieving optimal clinker formation, a crucial step in cement production, relies heavily on managing temperatures throughout the kiln's various stages. This is especially true during the formation of key components like alite and belite, where specific temperature ranges are needed. Finding the right balance between these temperatures directly impacts energy consumption and ultimately, the environmental impact of cement production.
The chemical makeup of the raw materials themselves plays a significant role. By modifying elements like the lime saturation factor, it's possible to potentially improve the energy efficiency of the process and reduce the amount of CO2 released into the atmosphere, issues of paramount importance today. Improvements in automation and process control technologies are continuously changing how these kilns operate. We now see kilns with customized temperature profiles designed to achieve specific clinker characteristics. As the demand for cement changes and evolves, so will the challenges and innovations involved in maintaining a sustainable approach to clinker and cement production, demanding a deeper understanding of the interplay between raw materials and kiln temperatures.
The composition of the raw materials, primarily limestone, clay, and iron oxide, directly influences the clinker's behavior within the kiln. Slight variations in the chemical makeup can significantly affect how these materials react at high temperatures. For instance, the reactivity of the mix, ultimately impacting the quality and properties of the final clinker, is tied to the initial chemical balance.
Maintaining a precise temperature profile throughout the kiln is essential for not only driving the clinkerization reactions but also for guiding the formation of specific mineral phases, like alite, belite, and tricalcium aluminate. Each of these minerals significantly affects the performance of the cement, particularly its strength development. Achieving the desired balance of these phases is largely dictated by temperature control.
The temperature gradient inside the kiln creates distinct zones, where different chemical reactions are favored. The critical 'burning zone', around 1400-1600°C, is where decarbonation and the formation of the key mineral compounds predominantly occur. This is where the complex interplay of temperature and raw material chemistry culminates in the creation of clinker.
While fossil fuels have traditionally provided the heat necessary for clinkerization, the industry is exploring alternative fuels and pre-calciners to enhance energy efficiency. These innovations could potentially improve temperature control within the kiln, reduce reliance on traditional fossil fuel sources, and optimize the clinker formation process overall.
Interestingly, the degree of pre-homogenization of the raw materials, before entering the kiln, plays a vital role in the clinkerization process. A homogeneous raw material feed provides a more uniform and consistent chemical environment throughout the kiln. This helps to avoid temperature swings and localized hot or cold spots during firing, potentially leading to improved energy efficiency and more predictable clinker quality.
The presence of sulfur in the raw materials is another factor that can subtly alter clinker chemistry. It can impact the formation of compounds like calcium sulfoaluminate, thereby influencing the final cement's hydration properties. Thus, it's important to consider the sulfur content during the raw material selection and preparation stages.
The reactions that lead to clinker formation are governed by chemical kinetics, which is heavily influenced by temperature. For instance, the creation of alite, a crucial component for cement strength, requires a very precise temperature profile for optimal transition from intermediate compounds. If these temperature parameters are not maintained, the alite formation process might be hindered, ultimately affecting the final product.
Modern cement production leans on advanced kiln technologies, often employing rotary kilns with artificial intelligence-driven controls. These sophisticated systems allow for real-time monitoring and adjustments of temperatures within the kiln, leading to better consistency in clinker formation. The ability to dynamically react to changes in the kiln environment enhances the overall quality and predictability of clinker production.
Temperature variations throughout the kiln can unfortunately induce thermal stresses in the clinker itself. These stresses may promote the formation of unwanted mineral phases or undesirable microstructures within the clinker. These unexpected changes can negatively influence the structural integrity of the final cement product.
As clinker formation relies so heavily on the raw material feed and kiln temperature control, consistent monitoring of the raw material composition becomes paramount. Even small variations in the chemical composition can have a significant effect on the thermal behavior and overall efficiency of the clinker formation process. Therefore, strict quality control of the raw materials is crucial for maintaining both production consistency and clinker quality.
Understanding Clinker Formation The Critical Phase in Modern Cement Production at 1400-1600°C - Chemical Transformation from Limestone to Clinker at 1450°C
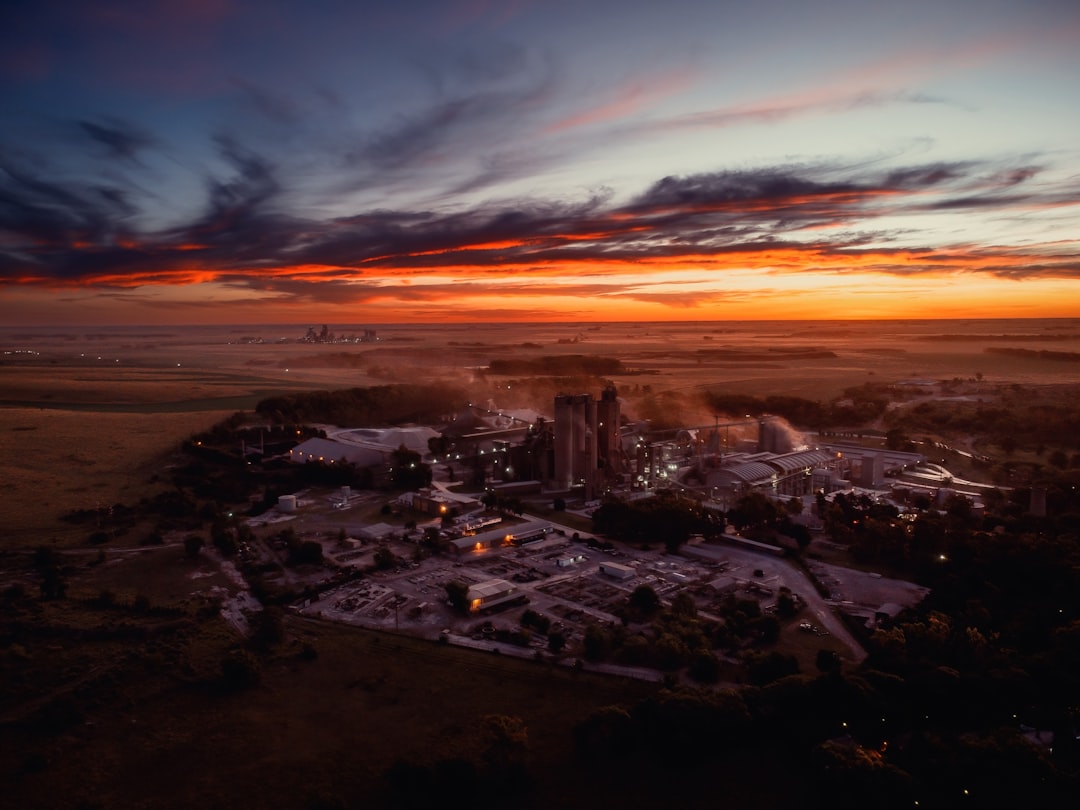
Within the high-temperature environment of a rotary kiln, around 1450°C, limestone undergoes a significant chemical transformation to become clinker. A key reaction in this process is the breakdown of calcium carbonate (CaCO3) into calcium oxide (CaO), a fundamental step in the formation of the various clinker phases. The kiln's intense heat triggers a series of chemical reactions resulting in a specific clinker composition, a crucial aspect of producing Portland cement clinker. Maintaining the desired clinker quality relies on precise temperature management and consistent raw material properties. Even small changes in the raw materials can lead to noticeable alterations in the final clinker's characteristics and performance. As the cement industry strives for improved efficiency and environmental responsibility, understanding this high-temperature transformation of limestone to clinker is becoming increasingly important for optimizing the entire production process.
The transformation of limestone into clinker at 1450°C is a fascinating chemical journey involving a cascade of reactions. The initial and crucial step is the decomposition of calcium carbonate (CaCO3) into calcium oxide (CaO) and carbon dioxide (CO2), a process that starts around 900°C but continues and is followed by the sintering step at higher temperatures.
The formation of alite (tricalcium silicate, C3S), a key compound responsible for the cement's strength, is highly sensitive to temperature. Maintaining the correct temperature range is essential, as even slight deviations can lead to the creation of less desirable compounds, jeopardizing the mechanical properties of the final cement.
The melting points of the raw materials are critical factors, with some components needing to reach their melting point for proper sintering. High proportions of silica, for example, can lower the overall melting point of the mix, impacting the clinkerization process and possibly enabling the formation of other minerals.
Iron oxide plays a dual role in the mix. While it aids in the formation of beneficial compounds, it also acts as a temperature stabilizer within the kiln. Iron oxide reactions lead to compounds like iron aluminate, which in turn can modify the viscosity of the melt, potentially affecting clinker production energy efficiency.
Maintaining the precise temperature profile within the kiln is vital, but it also presents a challenge due to the potential for "hot spots"–localized temperature variations. These variations can cause inconsistent material behavior and unwanted phase formation, highlighting the difficulty of maintaining a uniform heat distribution.
Interestingly, the clinker formation process can generate its own heat through exothermic reactions. This self-sustaining heat can be advantageous, but managing it is crucial to avoid overheating and destabilizing the desired phases.
The timing of raw material introduction is important as well. Limestone, in particular, must be introduced at the right intervals to ensure the remaining components react properly without interfering with the burning process.
The formation of dicalcium silicate (C2S) occurs at slightly lower temperatures than tricalcium silicate, providing a mechanism to tailor a mix of early- and long-term strength components. This illustrates the need for precise control over the thermal journey within the kiln.
The clinker mineral interactions with the kiln atmosphere can lead to the formation of volatile compounds that alter the overall clinker composition. Alkalis, for example, can unexpectedly reduce the formation of certain key phases, making it critical to carefully consider their presence during the raw material preparation stages.
The advancements in kiln operation and process controls are notable. Data-driven analytics and artificial intelligence allow kiln operators to predict and respond to real-time changes with greater precision. These technological improvements are revolutionizing clinker production by enabling the optimization of these high-temperature chemical processes with unprecedented control.
Understanding Clinker Formation The Critical Phase in Modern Cement Production at 1400-1600°C - Role of Aluminum and Iron Oxides in Clinker Mineral Formation
Aluminum and iron oxides play a crucial part in shaping the clinker's mineral composition, ultimately influencing the cement's performance. The presence of aluminum within the clinker's structure, particularly in alite, alters its hydration characteristics. This alteration can potentially enhance the cement's strength development, though it's important to understand how these interactions affect the overall mix design.
Iron oxides act as a sort of catalyst, or flux, in the clinker formation process. They promote the formation of essential clinker minerals like tricalcium silicate (C3S) and dicalcium silicate (C2S) which influence the cement's properties. The clinker melt, or liquid phase, is highly impacted by the presence of these oxides. This melt's viscosity and surface tension are significantly altered, affecting the effectiveness of mineral formation.
Managing this complex interplay between aluminum and iron oxides is essential for optimizing the overall clinkerization process, particularly within the kiln environment. However, it's not a straightforward endeavor. Maintaining the balance is crucial as these minerals directly impact the resulting clinker's composition and the cement's final properties. Ultimately, a better understanding of how aluminum and iron oxides interact in the high-temperature clinkerization process can pave the way towards improved cement quality, energy efficiency, and potentially more sustainable cement production methods.
Aluminum and iron oxides play multifaceted roles in the formation of clinker minerals, significantly impacting the final properties of cement. Aluminum's presence, for example, can influence the formation of calcium aluminate compounds, which contribute to the overall strength and durability of the resulting cement. This highlights the importance of carefully controlling the aluminum content in the raw materials to optimize clinker quality.
The interplay between iron and aluminum oxides is particularly interesting. Iron oxides can alter the viscosity of the clinker melt during the high-temperature process, affecting how various mineral phases interact and crystallize. It's a delicate dance of chemical interactions that impacts the efficiency of clinker formation.
Both aluminum and iron oxides act as fluxes, which essentially means they help lower the melting point of the raw materials. This leads to a more fluid melt, facilitating the formation of the core clinker minerals, especially at high temperatures. This fluxing behavior is critical to the clinkerization process.
The oxidation state of iron—whether it exists as ferrous iron (Fe²⁺) or ferric iron (Fe³⁺)—has a notable influence on the formation of silicate phases within the clinker. This emphasizes the importance of managing the oxidation environment within the kiln to ensure the desired clinker composition.
Reactive alumina can significantly boost the formation of aluminate phases. This enhances cement hydration kinetics, which essentially influences how quickly cement gains strength. This is crucial for construction projects requiring fast setting times.
Aluminum oxide content can also impact the clinker sintering process. While the effect can vary depending on the concentration, optimally, it can lower both the sintering temperature and duration, making the process more energy-efficient.
The ratio of silica to alumina and iron, often termed the silica modulus, controls the proportions of various mineral phases like belite and alite. Balancing these oxides is critical to achieving the desired final cement properties.
Iron compounds are relatively stable at high temperatures, yet, this stability can sometimes be a double-edged sword. Uncontrolled, it could lead to the formation of unwanted phases that might compromise clinker quality. Continued monitoring during production is crucial for consistency.
There's a complex network of reactions between iron and aluminum oxides within the clinker. These interactions are critical and heavily influence the final mineralogy of the clinker. Understanding and controlling these interactions are essential for optimization.
Lastly, aluminum and iron oxides also significantly impact the viscosity of the clinker melt. Higher viscosity can hinder the necessary rearrangement and reactions of minerals, hindering the formation of high-quality clinker. Maintaining a suitable viscosity, then, is a crucial factor in optimizing clinker production.
In essence, these two oxides play a crucial role in clinker formation, impacting its properties and ultimately, the performance of the final cement. Their intricate interplay underscores the need for meticulous control over the chemical composition of the raw materials and the conditions within the kiln. It's a fascinating example of how subtle changes in the chemistry can dramatically impact the engineering of materials like cement.
Understanding Clinker Formation The Critical Phase in Modern Cement Production at 1400-1600°C - Kiln Atmosphere Effects on Clinker Quality and Composition
The atmosphere inside the cement kiln significantly influences the quality and composition of the resulting clinker, especially within the crucial temperature range of 1400-1600°C. The levels of oxygen and any volatile compounds present can directly affect the formation of key mineral phases like tricalcium silicate and dicalcium silicate, which are crucial for the cement's performance. These interactions can lead to the development of undesirable compounds that negatively impact the clinker's properties and the final cement's mechanical strength.
As the cement industry explores innovative solutions for reducing carbon emissions, including technologies like carbon capture and oxyfuel combustion, understanding the impact of the kiln's internal environment becomes even more critical. This knowledge is vital for creating the best possible clinker while enhancing energy efficiency. A greater understanding of the kiln's atmosphere and its effects on clinker formation is essential for improving both the sustainability and quality of modern cement production. This understanding can lead to better choices for both the kiln design and operation, ultimately helping cement production evolve in a more sustainable direction.
The formation of specific clinker phases is strongly tied to the kiln's temperature profile. For instance, alite, a crucial component for cement strength, forms most readily in a narrow temperature band around 1450-1550°C. Departing from this optimal range can lead to increased formation of other phases like belite, which has a different set of strength characteristics. This reinforces the importance of maintaining precise temperature control for achieving the desired clinker properties.
The kiln atmosphere, a mixture of gases generated from fuel combustion and other sources, can significantly influence the behavior of iron oxides during clinkerization. Specifically, the oxidation state of iron, whether it's Fe²⁺ or Fe³⁺, can vary based on the gas composition, directly impacting the mineral makeup of the clinker. Effectively managing the combustion conditions, therefore, is key to ensuring clinker quality.
Unexpected water vapor present in the kiln atmosphere can throw off the clinkerization process by influencing the reactions occurring and potentially leading to the creation of undesirable hydrates. Controlling humidity levels within the kiln presents a considerable challenge for maintaining consistent clinker quality.
Sulfur compounds present in the kiln's gas environment can contribute to the formation of calcium sulfoaluminate. This compound, while not inherently detrimental, can impact the cement's mechanical performance, emphasizing the need for careful monitoring of sulfur content in the kiln environment and feedstock.
The presence of alkalis within the kiln atmosphere can alter the raw materials' melting behavior, potentially leading to unintended consequences in the clinker formation process. For example, they might suppress the formation of key phases like alite while promoting less desirable phases, making control efforts more intricate.
The kiln's geometry plays a role in the uniformity of heat distribution during clinkerization. If a kiln design doesn't create a uniform temperature profile, this can lead to inconsistent clinker quality. Careful design and engineering are thus necessary to ensure consistent clinker formation.
The cooling phase following clinker formation significantly impacts its mineral structure and stability. If clinker cools too quickly, certain mineral phases may get trapped in metastable states, potentially affecting the cement's long-term performance. Therefore, controlled cooling is a factor in optimizing the final product.
The variability inherent in raw materials can pose a challenge for maintaining consistent clinker quality. The chemical makeup of different batches of raw materials, even from the same source, can vary, leading to variations in behavior under the same kiln conditions. Adaptable controls and rigorous testing can help manage this variation.
The interplay of various oxides in the clinker formation process creates a highly intricate chemical environment. Fully comprehending these interconnected reactions is vital for optimizing the final cement's quality and functionality.
While modern technology has improved monitoring of kiln conditions, ensuring consistent compliance with desired parameters is challenging. Variables outside the direct control of operators, like fuel quality or ambient conditions, can lead to fluctuations in the kiln environment. It underscores the need for engineers to remain vigilant and actively manage these dynamic systems.
Understanding Clinker Formation The Critical Phase in Modern Cement Production at 1400-1600°C - Cooling Rate Impact on Final Clinker Properties and Cement Performance
The way clinker cools down significantly influences its final characteristics and how well the resulting cement performs. A fast cooling process can interfere with the formation of certain beneficial clinker phases like a specific form of dicalcium silicate (g-type C2S), which is generally desired due to its positive contribution to cement's hydration. This limitation in phase formation then affects the overall reactivity of the clinker, which is essential for proper strength development in the final cement product.
Because of this, fine-tuning clinker cooling systems is vital. It not only improves energy efficiency but also ensures that the mineral phases that contribute to cement's performance (like tricalcium silicate and dicalcium silicate) are formed and remain stable. The specific way air flows over the clinker and other cooling strategies are particularly important. They influence the clinker's mineral makeup in a big way. All of this emphasizes that we need to very carefully control and regulate clinker cooling processes during cement production to achieve desired outcomes in terms of the quality and performance of the cement we eventually use in construction.
The way clinker cools down significantly impacts its internal structure and how it behaves later on. If cooled too rapidly, it can end up with less stable phases, kind of like a rushed crystallization process. These unstable phases might not revert to their normal form even if reheated, which could make the cement perform less than ideally.
A quicker cooling process also tends to produce smaller clinker particles, affecting the surface area available for interactions during hydration. This change in surface area plays a key role in determining how quickly and strongly the final cement develops its strength.
Temperature variations during cooling can create internal stresses within the clinker, somewhat like thermal shock. These stresses can lead to cracks or undesired shifts in mineral composition as it solidifies. This highlights the need for controlled and even cooling methods.
Complicating things further, certain elements found in the raw materials, such as magnesium, can make the effects of cooling rates more difficult to predict. Different levels of magnesium change how stable the clinker's phases are as they cool. This reinforces the importance of maintaining consistent quality of the raw materials used to make the clinker.
The way various minerals crystallize is also affected by cooling rates. Each mineral might crystallize at a different rate as it cools, which influences the overall performance of the cement. This includes both the early and later stages of strength development in concrete.
We can try to control the cooling rate by using techniques like air or water sprays. This helps us fine-tune the process, but it adds another layer of complexity and cost to the operations.
Different clinker compositions behave differently in response to cooling rates. For instance, clinker with a higher proportion of belite might perform better with a slower cooling process to let its crystals grow properly. This suggests a need for more specialized cooling techniques tailored to the specific clinker being produced.
The cooling rate can also influence the internal structure of the clinker. It affects factors like porosity and how easily water can move through it. These are significant factors when using cement in various engineering applications.
One rather unexpected finding is that rapid cooling can increase the amount of alkali compounds that leach out of the cement as it hydrates. If not managed carefully, this leaching can impact the concrete's long-term durability.
Finally, research indicates that finding the best cooling rate can make the clinker more reactive in specific environments. This helps control the hydration process and potentially reduces the amount of cement needed in applications, making the overall cement use more efficient in some instances.
More Posts from aistructuralreview.com: