Structural Integrity When Replacing Windows With Sliding Doors
Structural Integrity When Replacing Windows With Sliding Doors - Evaluating the Existing Wall Structure
Assessing the structural condition of the existing wall is a critical first step before replacing a window with a sliding door. This requires more than a cursory look; it involves a detailed inspection of the current framing elements, checking for any pre-existing damage, water ingress, or structural deficiencies. Since installing a sliding door often means creating a significantly larger opening than the existing window, this alteration fundamentally changes how loads are borne by the wall structure. Simply cutting a larger hole without understanding or compensating for this load redistribution can compromise the wall's integrity. Proper planning and reinforcement are vital. Obtaining a professional structural assessment provides the necessary expertise to ensure that the planned modifications preserve the building's stability and contribute to its continued safe performance.
Here are some points to consider when undertaking the critical task of assessing the existing wall structure before introducing a large opening like a sliding door:
* It's vital to understand that the wall section originally occupied by a smaller window contributes significantly to resisting horizontal forces from wind and potential seismic events; replacing this with a much larger opening drastically diminishes this inherent shear capacity unless a robust compensatory load path is meticulously engineered.
* Even walls that appear sound on the surface can conceal underlying issues; hidden structural decay within wood members or unseen corrosion of metal supports, often resulting from past water leaks that were never fully addressed, can significantly compromise the wall's load-carrying capability in ways not immediately obvious during a visual inspection.
* Creating a large opening fundamentally redirects how the wall carries structural loads, concentrating forces that were previously distributed across a wider area onto a new supporting element above the opening. This requires careful evaluation of how these rerouted stresses impact the surrounding wall framing, critical connections, and the foundation system below.
* Existing conditions such as minor building settlement or subtle historical structural movement within the wall can introduce complex challenges; integrating a new, relatively rigid door frame into a wall with existing movement patterns can potentially create differential stresses that exacerbate hidden weaknesses or induce new cracking patterns elsewhere in the structure over time.
* The point where the original wall fabric meets the new door frame and its supporting structure is a key area for long-term performance. Inadequate attention to sealing and flashing details at this critical interface can create subtle pathways for moisture entry, leading to progressive, unseen deterioration of structural components within the wall cavity adjacent to the new opening.
Structural Integrity When Replacing Windows With Sliding Doors - Planning for the Opening Size Increase
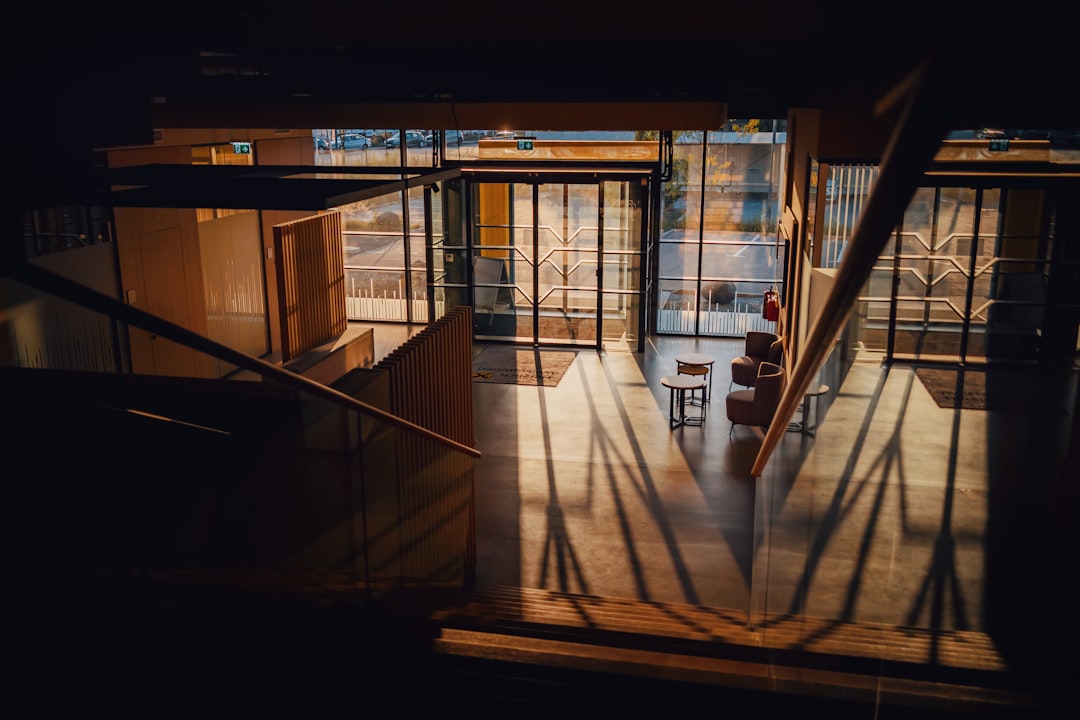
Enlarging an existing window opening to accommodate a sliding door introduces specific structural considerations that demand careful upfront planning. Beyond just cutting a bigger hole, this modification fundamentally alters the load paths the wall was designed to manage. The simple fact of removing a larger section of wall material, particularly in load-bearing walls, significantly reduces the wall's inherent capacity to resist vertical loads from above and lateral forces like wind. Adequate structural support must be meticulously calculated and installed above the new, wider opening. Furthermore, the larger cut exposes more of the existing wall structure, potentially revealing hidden weaknesses or inconsistencies that were less critical with a smaller opening but become significant under the redistributed stresses. Integrating the new, larger door frame precisely into this altered structure requires careful measurement (allowing for necessary fitting space) and attention to how the new frame interacts structurally with the old, particularly if the original wall has experienced any settlement or movement. Without thorough preparation and potentially professional input to address these magnified structural challenges, simply upsizing an opening risks compromising the long-term integrity of the building envelope.
Digging into the specifics of accommodating a larger opening size reveals several points critical to structural performance that might initially seem counter-intuitive or simply overlooked during preliminary planning:
The new structural element spanning the enlarged space – commonly termed a header or beam – isn't just a piece of lumber or steel chosen casually. Its required dimensions and material strength demand precise calculation, factoring in the span length and the cumulative structural loads it will predictably carry from floor levels, the roof system, and potentially snow or wind pressures above. Failing to size this element correctly, even slightly, can introduce excessive deflection over time or, worse, lead to sudden brittle or ductile failure modes under peak loading scenarios.
Crucially, the substantial loads intercepted by this new beam don't simply vanish; they are concentrated and transferred downward specifically through the vertical framing elements directly supporting the beam's ends (often called trimmer or jack studs). This creates highly focused point loads at the base of these supports. A failure to ensure these studs are adequate for the task, or that the structure *below* them – floor framing, foundation, or slab – possesses sufficient bearing capacity at these precise points, risks localized crushing or differential settlement, subtly undermining the integrity of the wall and potentially impacting finishes elsewhere.
Furthermore, removing a significant portion of wall material drastically diminishes the building's inherent capacity to resist forces acting parallel to the wall surface, such as those imposed by high winds or minor seismic events. This wall segment, acting like a stiff plate (or 'shear wall'), originally contributed significantly to the building's overall lateral stability. Replacing it with a large, flexible opening necessitates a deliberate strategy to compensate for this lost shear capacity, often involving the introduction of new bracing elements – potentially dedicated shear walls or moment frames – located elsewhere within the structure to re-establish a continuous, robust load path for these lateral forces.
Beyond the capacity of the structural members themselves, their stability is paramount. The vertical support studs carrying the concentrated header load are particularly susceptible to buckling – a form of failure under compression where the member bows outward before its material strength is fully reached. This stability depends heavily on the stud's slenderness (its height relative to its cross-section) and whether it is adequately braced along its length to prevent lateral movement. Overlooking this potential failure mode, especially with taller openings or when using less rigid materials, represents a significant planning blind spot.
Finally, even if the header and its immediate vertical supports are theoretically sufficient, the interfaces where these components connect to each other and tie back into the existing structure are critical vulnerabilities. These connections must reliably transfer the concentrated forces. Underestimating the loads at these joints or using improper fasteners, connection types, or insufficient bearing surfaces is a common pathway to failure, where loads bypass the intended path. Engineered connectors or specific nailing/bolting patterns are often required, demanding careful detailing during the planning phase to ensure these structural "handshakes" are robust enough for the long term.
Structural Integrity When Replacing Windows With Sliding Doors - Designing the Required Header and Framing
Crafting the header and surrounding frame demands precise engineering, moving beyond potentially outdated rule-of-thumb sizing. While standard double or triple lumber headers remain prevalent, contemporary practice and building codes offer alternative materials and assemblies that can enhance structural performance, improve thermal efficiency by minimizing bridging, or fit tighter wall depths. The necessary dimensions for a header are not arbitrary but calculated based on the specific loads from above and the span of the new opening; miscalculation invites problematic deflection or even outright failure over time. Framing the opening involves stout vertical members – king studs running full height, paired with jack or trimmer studs directly supporting the header ends. For the significant weight transferred by wider sliding door headers, employing multiple jack studs to bear the load downward onto the wall plate is a standard requirement. Crucially, the header itself needs lateral support to prevent buckling, which can be overlooked but is critical for beam stability under load. Careful assembly of multi-ply headers using proper fasteners ensures they perform as intended. Additionally, the precise placement of the header sets the opening height, directly impacting the clearance needed for the sliding door system, underscoring the interplay between structural needs and door functionality.
Accommodating differential thermal expansion, particularly when integrating materials with disparate properties like steel headers within traditional timber framing, necessitates meticulous detailing to manage long-term movement and prevent stress concentrations at connections. The cumulative effects of wood's inherent hygroscopic behaviour – its subtle cycles of shrinkage and swelling driven by moisture content changes over the building's life – can gradually alter the intended load distribution path around the header assembly, potentially introducing unforeseen stresses on adjacent elements. Beyond straightforward load-carrying requirements, building code mandates or specific wall assembly specifications often dictate a required fire resistance rating for the header itself, influencing material selection or requiring protective coverings, a design constraint independent of purely structural capacity. Ensuring the header's lateral stability at its bearing points is a critical, sometimes overlooked, detail; insufficient bracing at these ends can permit the header to twist or rotate under load, a distinct failure mode that compromises the assembly's integrity regardless of its vertical capacity. Designing for serviceability, specifically limiting deflection under typical loads, is as crucial as ensuring ultimate strength; excessive bending, even within theoretical safety margins, can cause undesirable aesthetic issues like cracked drywall or poorly operating doors elsewhere in the structure.
Structural Integrity When Replacing Windows With Sliding Doors - Ensuring Compliance with Local Building Codes
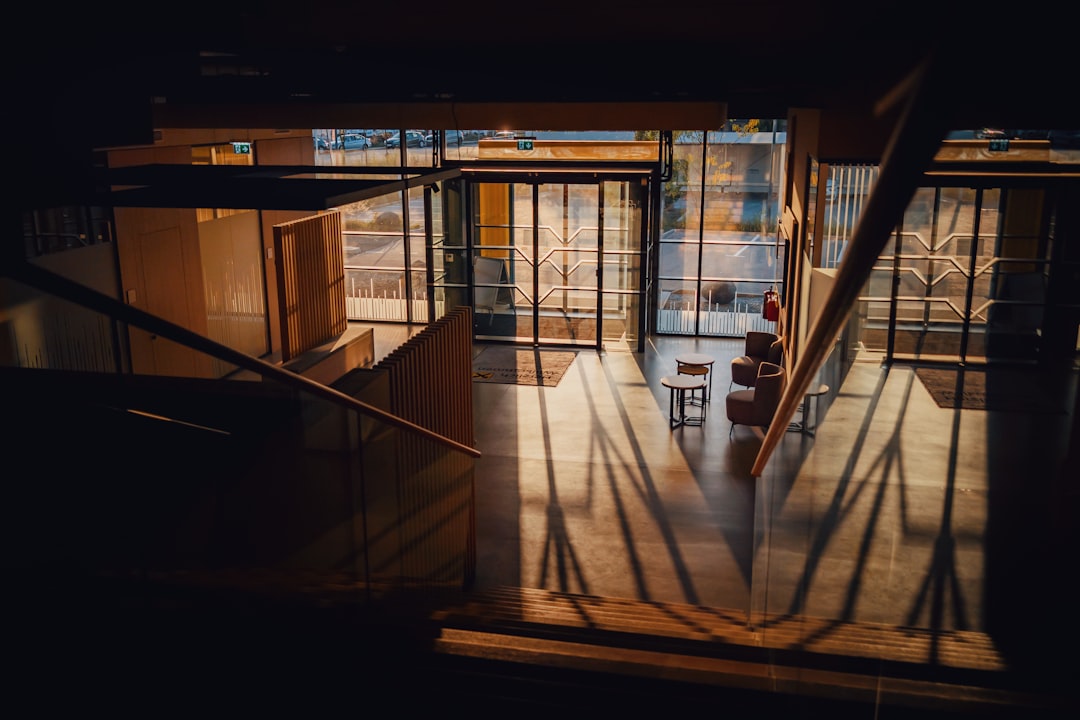
Navigating local building codes when installing sliding doors in place of windows is non-negotiable. These regulations, often complex and specific to your region's environmental nuances and structural demands, serve as the baseline for ensuring safety, maintaining structural integrity, dictating acceptable materials, and specifying installation practices. Disregarding them isn't merely a bureaucratic oversight; it actively risks incurring significant financial penalties, enduring frustrating project delays, and critically, potentially compromising the building's stability itself. While energy efficiency standards are often part of the mix, the structural mandates surrounding altering load-bearing elements for larger openings are particularly critical in this context, though details vary. A failure to diligently verify and adhere to the specific code requirements applicable to the project location, rather than assuming general knowledge suffices, is a critical planning error that can have lasting repercussions on the building's performance and longevity.
Ensuring compliance with local building codes for structural modifications like introducing a larger opening for a sliding door introduces several layers of complexity and practical considerations.
The foundational challenge in achieving code compliance for such modifications lies in the inherent jurisdictional variability; codes aren't uniform nationwide or even statewide, with neighboring towns often adopting different editions or incorporating local amendments reflecting micro-climates, specific soil conditions, or historical practices. Navigating this fragmented landscape requires granular research specific to the project's exact location, as assumptions based on general knowledge or nearby projects can easily lead to non-compliance.
It's perhaps a pragmatic truth that building codes primarily establish a baseline for safety under defined design loads and conditions, rather than dictating parameters for peak performance or extended resilience beyond these calculated thresholds. Meeting code guarantees a structure should withstand specific anticipated forces, but it doesn't necessarily assure resistance against outlier events or long-term degradation mechanisms not explicitly modeled, leaving a subtle gap between code compliance and potential longevity or exceptional performance.
Building codes are dynamic documents, not static rulebooks carved in stone. Their periodic revisions are crucial, often prompted by hard lessons learned from structural failures following natural disasters or informed by advancements in material science and engineering analysis techniques. Relying on outdated code versions isn't merely a bureaucratic misstep; it risks omitting safeguards designed to address vulnerabilities identified in recent history or failing to utilize current best practices for structural detailing and assembly.
The path to final compliance invariably passes through the local building official's review and field inspections. While design documents represent the theoretical intent and code application, the practical execution on site must align with the code requirements as interpreted and verified by the authority having jurisdiction. This process can introduce subjective elements or require specific documentation to satisfy the inspector's criteria, highlighting that compliance involves not just technical adherence but also procedural navigation and communication.
The required level of structural scrutiny and the specific code provisions applicable aren't solely dictated by the type of modification (like installing a sliding door) but are fundamentally tied to the building's purpose and occupant load. Designing for a single-family home falls under a different set of code parameters, including load factors and safety coefficients, than modifications to a multi-unit residential building, a commercial property, or a structure with high public occupancy, underscoring the need to correctly classify the building's use early in the planning phase.
Structural Integrity When Replacing Windows With Sliding Doors - Considering Long Term Structural Performance
Considering the lifespan of a building means looking well beyond the immediate aftermath of converting a window opening into one for a sliding door. This seemingly straightforward alteration isn't a temporary fix; it's a permanent change that must align with the structure's intended longevity. Thinking long-term involves recognizing that the materials used and the quality of the workmanship during installation directly influence how the new opening, and the wall around it, will withstand decades of environmental exposure and structural load variations. Shortcuts in assessing the original structure, inadequate preparation, or choosing substandard components based purely on upfront cost can introduce subtle weaknesses that compound over time, leading to issues like premature material fatigue, compromised weather sealing, or load path inconsistencies that only become apparent years down the line. True structural integrity for this modification lies in a foresightful approach, ensuring the adapted structure remains robust and performs consistently throughout the building's service life, integrating seamlessly into the building's overall resilience rather than becoming a point of failure.
Considering the long-term performance horizon introduces challenges that extend well beyond merely meeting immediate code requirements or ensuring initial load capacity. Structures don't simply exist; they subtly interact with their environment and internal forces over decades, and a significant alteration like substituting a large opening for a window shifts these dynamics. Here are aspects warranting scrutiny from a longevity perspective:
The continuous, albeit minor, cycles of temperature and moisture variation experienced by the wall assembly cause subtle expansion and contraction. When diverse materials like wood framing, steel connectors, glass, and aluminum door frames are rigidly joined at a new large opening, these differing thermal and hygroscopic responses generate cumulative stresses at the interfaces, potentially leading to fastener fatigue, sealant failure, or gradual loosening of connections over years.
Even under typical service loads below material yield strength, components like wood framing can exhibit creep – a slow, time-dependent deformation. Around a concentrated header load, this gradual yielding might cause the beam or its supports to deflect imperceptibly year after year, subtly altering how loads are distributed across the opening and onto adjacent original framing members in ways the initial static analysis may not fully capture decades later.
Introducing a large, relatively flexible opening significantly diminishes the wall's inherent capacity to act as a monolithic unit resisting lateral forces. This reduction in system redundancy means that minor localized deterioration, perhaps unforeseen moisture ingress impacting a critical connection, or an unanticipated overload event years down the line, has a potentially more pronounced impact on the overall stability of that wall section than in the original, stiffer configuration.
The long-term durability of the weather seal and flashing system around the new door opening is paramount. While installed correctly initially, the effectiveness of sealants and tapes degrades over decades due to UV exposure, cyclic movement, and material aging. Should these critical barriers fail subtly, chronic moisture intrusion into the modified wall cavity can lead to hidden structural decay and corrosion long before any signs become visible on the exterior or interior finishes.
Diagnosing structural issues related to the new opening years post-installation can be difficult. Slow-onset problems like subtle creep deflection, progressive connection degradation, or hidden moisture damage often manifest first as non-specific distress in finishes – hairline cracks in drywall, sticking door panels, or localized paint bubbling – which might be dismissed as cosmetic until significant underlying structural change has occurred.
More Posts from aistructuralreview.com: