Temperature Relief Valve Design and Structural Safety Scrutiny
Temperature Relief Valve Design and Structural Safety Scrutiny - Designing for Thermal Extremes Material Selection and Fatigue Considerations
In the evolving landscape of critical infrastructure design, especially for components like temperature relief valves, the imperative to manage thermal extremes continues to drive innovation. As of mid-2025, the focus in designing for these environments has shifted notably beyond traditional material charts. We are now seeing a significant push towards computational materials discovery, where sophisticated simulations and machine learning are accelerating the identification of novel alloys and ceramic composites capable of withstanding unprecedented thermal shocks and prolonged high temperatures. This permits a more nuanced understanding of microstructural stability and the nuanced pathways of thermal fatigue crack initiation and propagation. Alongside this, advancements in additive manufacturing are beginning to allow for geometrically complex designs that can better distribute thermal stresses, though challenges persist in ensuring consistent material properties and validating long-term performance for these intricate structures. The discourse is increasingly centered on integrated material-design approaches, demanding a more holistic view of a component's lifecycle under thermal duress, rather than just its initial specification.
The intricate interplay between extreme temperatures and material behavior in valve design presents a fascinating, yet challenging, landscape for researchers and engineers alike. Here are some observations that underscore the complex realities we navigate:
One often underestimates the subtle creep deformation that materials can exhibit under sustained thermal load. It's not about immediate failure, but a slow, irreversible 'sagging' or dimensional shift over extended periods, even when stresses are well below the material's nominal yield strength. This insidious behavior critically compromises the precise clearances and sealing surfaces essential for a relief valve's long-term operational integrity, demanding rigorous analysis beyond static strength models.
The sudden application or removal of heat can generate profound thermal gradients within a component. These aren't just surface effects; they can induce intense internal stresses as parts of the material expand or contract at different rates, essentially trying to tear themselves apart from within. This 'thermal shock' can lead to rapid crack propagation or surface spalling, especially in materials with inherently low ductility or those that don't easily dissipate stress through plastic flow.
Designing with dissimilar materials, while often necessary for performance, introduces inherent weaknesses. When materials with varying Coefficients of Thermal Expansion are rigidly joined, every temperature fluctuation turns the interface into a battleground. This constant tug-of-war creates localized stress concentrations that, over repeated thermal cycles, can initiate interfacial delamination or fatigue cracks long before the bulk material shows any sign of distress.
Thermal cycling itself, even in the absence of significant external mechanical loads, can be a potent source of damage. When a material is constrained from freely expanding or contracting due to temperature changes, it's forced into cyclic plastic deformation. This 'strain-controlled' fatigue, particularly low-cycle fatigue, can lead to crack initiation and propagation through an accumulation of microscopic damage, highlighting that the absence of high nominal stress doesn't equate to immunity from fatigue.
Beyond merely altering mechanical properties, prolonged exposure to elevated temperatures can instigate fundamental metallurgical transformations or accelerate environmental degradation. For instance, in certain stainless steels, extended thermal exposure can lead to the formation of brittle 'sigma phase' particles. This microstructural change dramatically reduces the material's ductility and toughness, rendering it susceptible to sudden, brittle fracture under conditions it was originally designed to withstand. Such aging effects often remain undetectable until a catastrophic event occurs.
Temperature Relief Valve Design and Structural Safety Scrutiny - Assessing Structural Robustness Analytical Tools and Testing Regimens
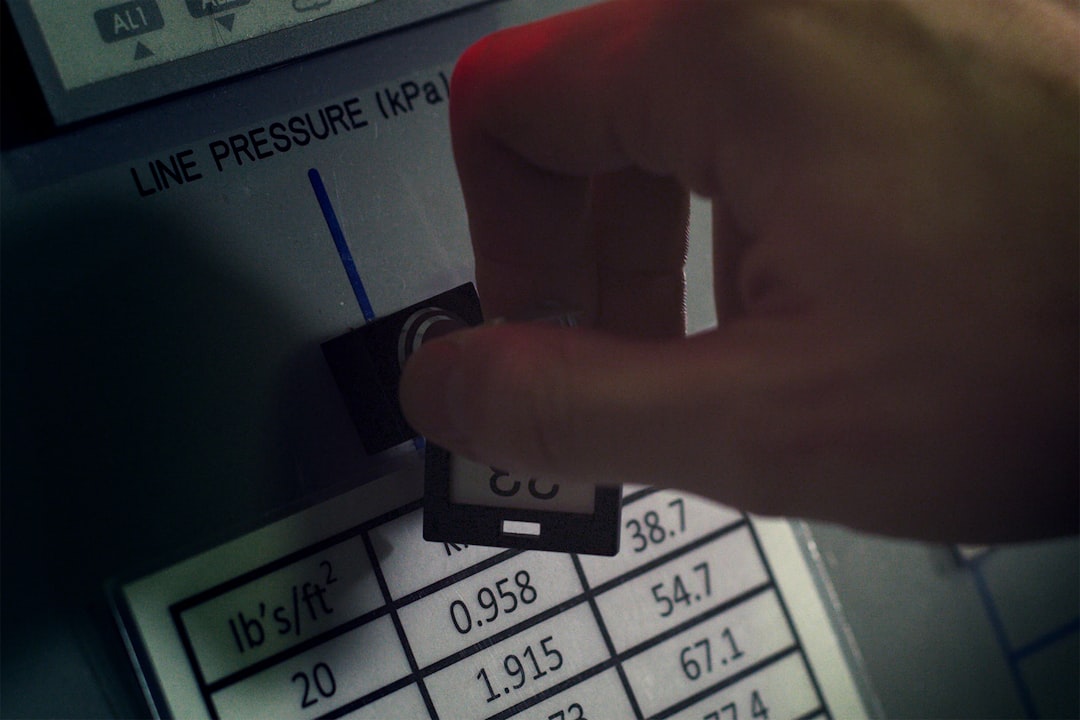
As of mid-2025, the contemporary focus in assessing the structural robustness of critical components like temperature relief valves has sharpened considerably, extending beyond conventional finite element analysis and isolated laboratory tests. A significant shift is observed in the evolution of analytical tools, with a growing emphasis on truly predictive, multi-scale computational models that aim to simulate the complex, interconnected degradation pathways rather than just individual failure modes. This increasingly involves integrated probabilistic analysis, moving towards predicting a likelihood of failure under various operational profiles, though the inherent quality and breadth of input data remain critical constraints. Concurrently, testing regimens are transforming, with a drive towards hyper-accelerated and multi-modal testing environments. These advanced rigs combine extreme thermal cycles with varying pressures, mechanical loads, and even corrosive agents to compress decades of potential service life into far shorter durations. The challenge, however, lies not just in executing these complex tests, but in effectively processing and interpreting the vast quantities of real-time sensor data they generate, ensuring that advanced data analytics keep pace with experimental capabilities. Furthermore, the very definition of a 'robust' test protocol is being re-evaluated for the novel material systems and intricate component designs now entering production, necessitating a more dynamic and less prescriptive approach to certification.
Our ongoing exploration into the resilience of critical components like temperature relief valves reveals a fascinating evolution in how we analytically and experimentally scrutinize their structural integrity. It's no longer sufficient to simply declare a design "safe"; rather, we strive for a deep understanding of its limits and likelihood of failure, especially under the unpredictable thermal loads often encountered.
One particularly compelling shift has been the widespread adoption of probabilistic fracture mechanics, often intricately linked with multi-scale material models. This moves us decisively beyond simplistic deterministic pass/fail criteria, instead yielding a nuanced probability of failure for valve components across their projected thermal cycles. While this adds a layer of statistical complexity, it provides engineers with a more realistic risk assessment, acknowledging the inherent uncertainties in material properties and loading conditions, ultimately improving confidence in long-term operational integrity.
Accompanying these analytical strides, the realm of high-fidelity digital twins is truly transforming our ability to assess structural robustness. These sophisticated computational counterparts to physical components allow for continuous, dynamic monitoring and prediction of a valve's remaining useful life and potential failure modes under real-time thermal and mechanical stresses. They prove invaluable for exploring component performance under conditions that are either too dangerous, expensive, or simply impossible to replicate in traditional physical testing, though the ongoing challenge remains in ensuring these digital representations maintain perfect fidelity with their real-world counterparts throughout a component's extended service life.
On the experimental front, advanced techniques such as Digital Image Correlation (DIC) at elevated temperatures are revolutionizing the validation of complex thermo-mechanical models. By capturing full-field, micro-level strain maps during actual thermal cycling, DIC provides an unprecedented resolution for observing and correlating localized deformation and stress concentrations. This direct observation capability is absolutely critical, as it bridges the gap between theoretical predictions and actual material response, allowing us to pinpoint areas of concern that might be missed by sparser measurement techniques, though setting up and conducting such experiments at high temperatures presents its own demanding set of technical hurdles.
Furthermore, Physics-Informed Neural Networks (PINNs) are rapidly emerging as potent analytical tools. These networks embed fundamental physical laws directly into their architecture, allowing them to significantly accelerate and refine simulations for complex phenomena like non-linear thermal stress redistribution and crack propagation. Compared to traditional purely computational methods, PINNs promise faster and often more accurate predictions, especially valuable when exploring a vast parameter space. However, as with many machine learning approaches, understanding their generalization capabilities and potential "blind spots" outside of their training data remains an area requiring diligent investigation by curious researchers.
Finally, a significant shift in industry and regulatory thinking is evident in the increasing mandate for "beyond design basis" robustness assessments for critical valve components. This pushes engineers well past routine operational parameters, compelling them to employ advanced scenario-based simulations that explore failure pathways under truly extreme, even improbable, thermal transients. The goal is to fully comprehend the safety margins, even for events far exceeding routine operational parameters, forcing us to consider contingencies for the most challenging and unexpected conditions a valve might encounter in its lifetime.
Temperature Relief Valve Design and Structural Safety Scrutiny - Field Inspection Methodologies and Compliance Verification
As of mid-2025, field inspection methodologies and compliance verification for critical components like temperature relief valves are undergoing a fundamental transformation. The emphasis is now squarely on leveraging operational data and advanced field technologies to understand a valve’s real-world behavior. Inspections are moving well beyond simple visual checks, increasingly incorporating miniaturized, non-intrusive sensors and portable analytical tools that can detect sub-surface anomalies and material degradation in situ. This shift facilitates a more proactive approach to integrity management, moving away from interventions based purely on time. For compliance, the focus is increasingly on the establishment of a robust digital thread, providing an immutable ledger of a valve's lifecycle performance, including every field inspection and maintenance action. This aims to streamline regulatory oversight, but it also demands unprecedented rigor in data capture and security. While these advancements promise enhanced safety and reliability, integrating such complex data streams from varied field environments remains a substantial challenge, often creating new layers of complexity that demand equally advanced human expertise for proper interpretation.
Observing the current trajectory of field inspection for critical components like temperature relief valves, it's fascinating to note how far methodologies have evolved beyond simple visual checks.
* Contemporary field assessments frequently leverage advanced non-destructive modalities, notably Phased Array Ultrasonic Testing (PAUT). This isn't just about finding obvious cracks; PAUT now provides intricate internal structural maps, enabling us to pinpoint subtle pathways of material degradation, such as the insidious effects of hydrogen on ductility or the precise location of thermal disbonding, even within complex geometries and across varying wall thicknesses. It offers an unparalleled internal gaze, though the meticulous interpretation of such high-resolution data remains a significant undertaking for the inspecting engineer.
* Autonomous robotic systems, equipped with an array of optical and thermal imaging sensors, are undeniably redefining the efficiency of field inspection. These platforms can tirelessly scan critical valve surfaces, utilizing integrated artificial intelligence algorithms to meticulously identify minute surface anomalies or unusual thermal signatures that might precede a structural issue. While promising remarkable consistency and speed compared to human observation, a keen researcher can’t help but ponder the robustness of their anomaly detection models when encountering truly novel failure modes or unforeseen environmental interferences.
* The increasing integration of 'smart valve' technology, featuring embedded Micro-Electro-Mechanical Systems (MEMS) sensors, heralds a profound shift in how we approach compliance verification. These miniature devices provide a continuous stream of real-time operational intelligence—everything from minute temperature fluctuations across internal surfaces to subtle changes in vibration patterns. This constant influx of live performance data empowers dynamic structural integrity assessments, moving the paradigm beyond merely scheduled check-ups towards a perpetually informed, if not truly predictive, understanding of a valve's health, though the sheer volume and fidelity of data often present their own analytical challenges.
* It's becoming increasingly clear that the lessons learned from post-failure forensic analysis are indispensable for refining proactive field inspection strategies. Rigorous metallurgical examination of retrieved valve components, scrutinizing fracture surfaces and detailing microstructural degradation mechanisms, provides critical empirical feedback. This invaluable data allows us to precisely calibrate and tune our non-destructive inspection techniques, enabling them to specifically hunt for the earliest, most subtle precursors of known failure modes, thereby significantly boosting the reliability of our detection capabilities in the field.
* High-precision optical methods, including laser scanning and structured light projection, are now routinely employed during field inspections. These sophisticated techniques allow for the meticulous verification of critical dimensional integrity, particularly concerning the tight clearances and sealing surfaces essential for a relief valve's functionality after extended service or exposure to thermal extremes. They can resolve sub-millimeter deformations resulting from phenomena like creep or localized thermal fatigue, providing a quantifiable assessment that ensures the valve's mechanical tolerances remain within safe operational parameters, though the practicalities of deploying such precision tools in varied industrial environments are not insignificant.
Temperature Relief Valve Design and Structural Safety Scrutiny - Operational Performance Data and Continuous Improvement Pathways
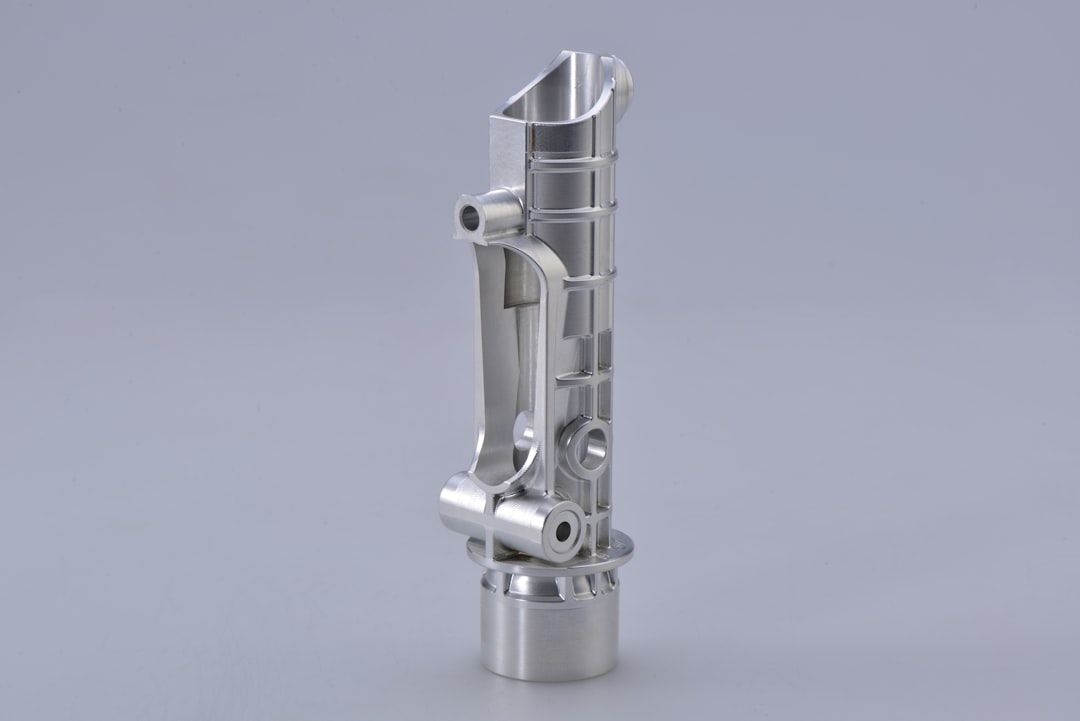
The integration of operational performance data with continuous improvement pathways represents a critical shift in how temperature relief valves are conceived and maintained. Moving beyond mere scheduled inspections or isolated design iterations, the current focus is on establishing a dynamic feedback loop: real-world operational insights directly informing subsequent design refinements. This isn't just about spotting impending failures but systematically extracting lessons from the subtle ways valves degrade under extreme thermal and mechanical duress. By analyzing performance telemetry, engineers aim to uncover previously undetected wear patterns or stress concentrations that eluded initial models. However, this ambitious approach faces significant hurdles. The immense volume of generated data is often compromised by quality issues like noisy sensors or missing context. Transforming this raw information into actionable engineering intelligence requires robust analytics, and effectively integrating these insights back into established design workflows and stringent regulatory frameworks remains an arduous task. The promise of continuously evolving, data-driven valve designs demands a fundamental re-evaluation of traditional validation processes and a disciplined approach to interpreting empirical evidence.
It's fascinating how data gathered from a valve's daily operation, when combined with broader lifecycle considerations, is now used to pinpoint the ideal moment for maintenance or replacement, aiming for not just component longevity but also a reduced environmental footprint, fostering an ongoing evolution in overall system stewardship.
We're beginning to see relief valve systems that are truly 'intelligent,' using live performance feedback to autonomously fine-tune their own behavior—things like modifying pressure set-points or flow rates. This allows them to spontaneously adapt to fluctuating temperatures or changes in fluid dynamics, a compelling step towards consistently optimized operation, though the complexities of such autonomous control warrant rigorous scrutiny.
A particularly powerful application emerging is the feeding of real-world operational insights into what we call "digital material twins." This allows the underlying material models – the constitutive equations that describe how materials behave – to be constantly updated and improved based on actual in-service stress and thermal histories. This dynamic feedback loop provides engineers with an unparalleled empirical basis for refining future valve designs, pushing the boundaries of material selection and robustness, assuming the data quality is impeccably maintained.
Handling the torrent of data pouring from instrumented valves has led to the widespread adoption of "edge computing" — processing information right where it's collected, at the operational site. This bypasses the need to send everything to a central cloud, enabling immediate, localized analysis and rapid, subtle adjustments. It's a critical enabler for truly dynamic optimization, though the security and resilience of these distributed nodes become paramount concerns.
A fascinating frontier is the application of unsupervised machine learning to operational data, which is now adept at uncovering incredibly subtle 'fingerprints' of impending issues. These algorithms can identify the unique pre-failure signatures of specific degradation modes—perhaps the faintest whisper of intergranular corrosion or a tiny vibrational shift indicating early stress relaxation—long before any visible or conventionally detectable damage appears. This enables a level of predictive maintenance that's almost surgical in its precision, though validating the reliability of these 'whispers' against false positives remains an ongoing analytical challenge.
More Posts from aistructuralreview.com: