The 2018 Mechanical Code: Essential Insights for Structural Engineers
The 2018 Mechanical Code: Essential Insights for Structural Engineers - Where Mechanical Systems Demand Structural Attention
Addressing the interplay between mechanical systems and the buildings that house them, this portion focuses on where the 2018 Mechanical Code specifically necessitates attention from structural engineers. It highlights the critical need for timely cooperation between the mechanical and structural design disciplines from the project's outset. Failure to coordinate early can lead to significant issues, particularly when accommodating substantial mechanical elements like expansive ductwork within spaces sensitive to their appearance, such as areas designed with open ceilings. These integration challenges are not merely aesthetic; they inherently involve structural considerations regarding support, load paths, and space allocation, directly impacting the building's safety and overall functionality. The mechanical code sets forth requirements that define these interfaces, underscoring why structural engineers must grasp its implications to ensure that proposed systems can be safely and practically incorporated into the structure. This mutual understanding and early engagement are fundamental to avoiding conflicts and achieving integrated, resilient designs.
Within the realm of structures and the guidelines like the 2018 Mechanical Code, it becomes clear that seemingly distinct mechanical elements can pose significant challenges demanding a structural engineer's focus.
1. Heavy mechanical plant, think large chillers or air handlers, represents concentrated point loads. These aren't always distributed neatly across supporting members and can impose intense localized stress, potentially beyond a member's original design capacity. Over time, without proper detailing and reinforcement, this can lead to unintended deflection, cracking, or even threaten structural integrity.
2. Operational vibrations from machinery are more than just an annoyance; they can be a dynamic force. If not adequately isolated at the source or along the path, these vibrations can excite resonant frequencies in structural elements. This amplification can significantly increase stress cycles, accelerating fatigue damage in connections or members, which is a subtle but critical form of long-term deterioration.
3. Creating openings in structural components for running ductwork, pipe runs, or conduits inherently reduces the effective cross-section. A penetration, even if it appears minor, particularly when situated within a region of high bending moment or shear stress, can substantially diminish the load-carrying capability of a beam or wall compared to its solid state. This necessitates careful analysis beyond simple area reduction.
4. Long runs of piping and ductwork, subject to temperature fluctuations, undergo thermal expansion and contraction. If these movements are restrained by rigid connections to the structure without provisions like expansion loops or joints, considerable forces can be transmitted. These thermal loads can induce stresses on supports, anchors, or adjacent structural elements, potentially leading to unanticipated localized stresses, cracking, or displacement.
5. Mechanical units positioned on the exterior, notably rooftop HVAC units, become significant surfaces subjected to wind pressure. The resulting uplift and lateral loads must be effectively transferred down through the building's structural frame. Underestimating these wind-induced forces and failing to ensure adequate bracing and connection design can challenge the roof structure and the building's overall lateral load resisting system in significant ways during high wind events.
The 2018 Mechanical Code: Essential Insights for Structural Engineers - The Code Interface Points Mechanical Meets Structural
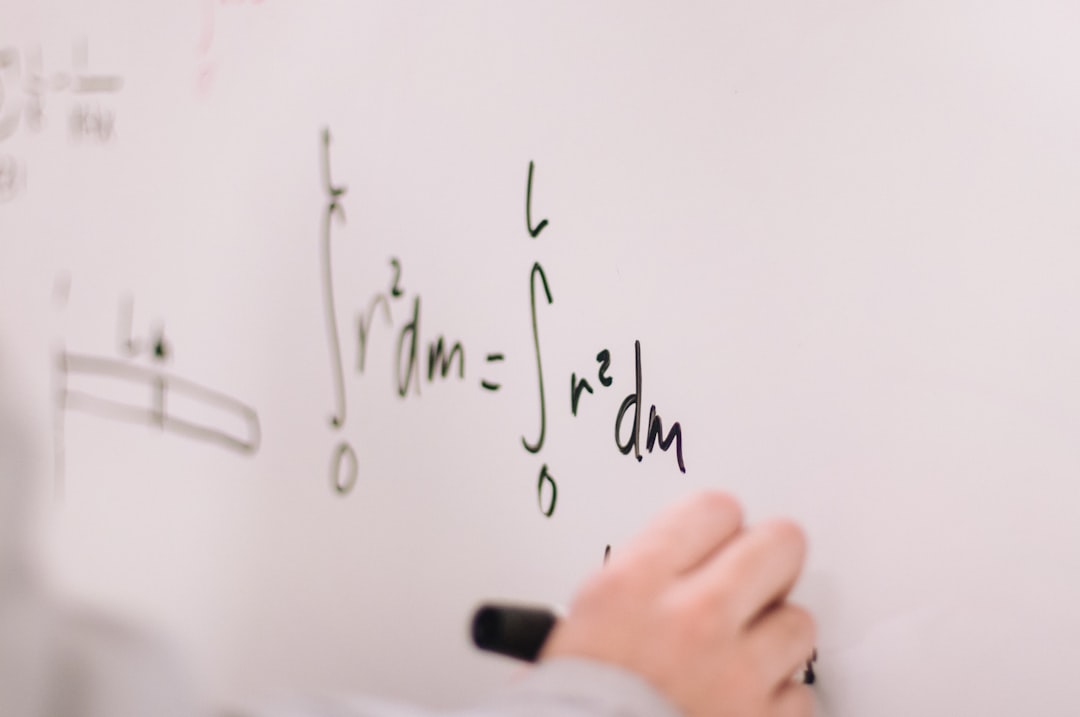
The junction where mechanical systems integrate with the structure is a key area within the 2018 Mechanical Code that directly concerns structural engineers, underscoring how these installations influence overall building integrity. The structural implications arise as components like substantial equipment and ductwork introduce significant forces onto the supporting framework, necessitating careful evaluation to mitigate potential issues stemming from load concentrations or dynamic effects. Furthermore, modifying structural members to accommodate pathways for mechanical services requires specific analysis to account for how such alterations might affect load paths and member capacity. The code also implicitly requires consideration for stresses induced by forces like thermal movement in piping and ductwork. Ultimately, navigating these intersections defined within the mechanical code proactively and with informed judgment is fundamental to crafting resilient and functionally sound building designs.
Here are some specific aspects governed by the 2018 Mechanical Code where mechanical systems intersect with structural considerations, often in ways less immediately obvious than main load-bearing requirements:
1. Certain mechanical equipment installations, particularly those with asymmetrical layouts or operational characteristics like pumps or fans, can induce twisting moments or uneven forces on their supporting structure. Effectively transferring these sometimes dynamic and potentially torsional loads requires a more nuanced structural detailing than simply accounting for gravity weight, posing a challenge if not addressed early in design integration.
2. While individual ductwork sections may seem light, the cumulative mass across an entire floor or building becomes a significant component of the building's total dead load. Furthermore, the added weight of insulation, internal linings, reinforcing elements, and even the settled dust and debris over years of operation contributes to a static load that, if underestimated in the support system design, can lead to excessive deflections or stresses on supporting members or connections.
3. Provisions within the mechanical code for condensate drainage systems, essential for managing moisture from cooling coils or other sources, necessitate careful thought regarding routing and discharge relative to structural elements. Uncontrolled water leakage or failure in these systems poses a chronic threat, potentially leading to moisture-induced deterioration, including corrosion of steel members or rebar within concrete, which can subtly undermine long-term structural integrity if not adequately planned for and protected against.
4. The operating environment created by some mechanical equipment, such as high-temperature exhaust systems or areas with rapid temperature cycling, can directly influence the behavior of adjacent structural materials. Elevated temperatures, even locally, can affect material properties like the yield strength of steel or increase creep susceptibility in concrete elements, potentially altering their performance and load-carrying capacity over time under sustained or repeated loading scenarios.
5. Mandatory fire-resistance requirements for certain ductwork, particularly in systems like kitchen exhausts or hazardous exhaust, create complex interactions where these systems must penetrate fire-rated structural assemblies. Ensuring that the required fire-stopping and support methods for such ducts maintain the integrity of the structural fire compartmentation, without introducing new load paths or weakening the structure at the point of penetration, demands precise coordination between the mechanical and structural fire protection designs.
The 2018 Mechanical Code: Essential Insights for Structural Engineers - Highlighting Key Changes in the 2018 IMC for Structural Engineers
Looking back at the adoption cycle, the 2018 International Mechanical Code introduced several key updates directly pertinent to structural engineering considerations. Revised mandates concerning ventilation and exhaust systems, detailed in various chapters like 4, 5, and 6, weren't just about airflow rates; they frequently required different ducting configurations or larger equipment, posing new challenges for support layouts and load path integration within the building structure. The code's increased clarity around accommodating dynamic aspects within duct and piping systems subtly reinforces the structural engineer's responsibility to account for operational forces and expansion effects, even if the previous code implied such necessities. Furthermore, the inclusion of explicit requirements for components like pollution control units highlighted the evolving demands on mechanical systems, bringing potentially significant new loads – whether static weight or from operational forces – into the structural design equation. While often perceived as purely mechanical, these changes in scope and specification within the 2018 IMC underlined an increasing complexity in the systems structural engineers must physically integrate and support, requiring diligent review beyond just identifying major equipment pads. Keeping abreast of these shifts in mechanical requirements was, and remains, fundamental for anticipating their spatial and load implications on the structural framework.
Let's delve a bit deeper into some specific areas governed by the 2018 IMC that might not immediately jump out as structural concerns, yet significantly influence how we approach the design of supporting structures:
Acoustic isolation systems, while intended to mitigate operational noise and vibration transmission, are themselves structural components influencing load paths and dynamic behavior. Properly designing supports for equipment resting on spring mounts or elastomeric pads requires understanding how these isolators distribute forces and interact with the structure's natural frequencies. If not done with precision, the very solution meant to control vibration can, in certain scenarios, introduce undesirable swaying motions or unintended stress concentrations.
Consider the impact of evolving environmental regulations driving changes in mechanical equipment design. The 2018 IMC implicitly aligns with broader environmental goals, including those affecting refrigerant use. This isn't merely a plumbing issue; newer, less environmentally harmful refrigerants often require larger or heavier compressors and heat exchangers to achieve comparable performance. This means that equipment packages delivering equivalent heating or cooling capacity to older models can impose increased dead loads on supporting roofs or floors, a detail crucial for structural calculations that might rely on historical weight assumptions.
The trend towards distributed mechanical systems, replacing large central plants with numerous smaller units scattered throughout a building or across a roofscape, presents a different structural challenge. Instead of a single, massive load at one location, we're now contending with multiple smaller loads, often in closer proximity than anticipated. The cumulative effect and localized concentration of these distributed units can create demands on specific structural bays or members that differ significantly from supporting a single heavy load, requiring careful assessment of load sharing and local capacity.
Energy recovery ventilators (ERVs), increasingly mandated or encouraged by codes like the 2018 IMC for improved building energy efficiency, are becoming ubiquitous. These units, housing complex heat exchange matrices, filters, and fans, add substantial weight to duct runs or floor areas. Supporting these relatively bulky components, often located in congested service zones or retrofitted into existing structures with limited capacity, requires careful structural planning for concentrated loads and clear spans, moving beyond simple duct hanger calculations.
Finally, the growing integration of diverse building systems, such as building-integrated photovoltaics (BIPV) linked with mechanical systems like solar air collectors, introduces novel structural considerations. These combined elements, while serving energy or architectural functions, represent integrated loads encompassing dead weight, wind forces on exposed surfaces, and potentially thermal expansion effects from the solar components. Assessing the structural impact of these hybrid systems demands a holistic view, recognizing that what might appear as an electrical or architectural element inherently carries structural consequences governed partly by the requirements for its mechanical interfaces.
The 2018 Mechanical Code: Essential Insights for Structural Engineers - Designing Structural Elements for Mechanical Loads and Penetrations
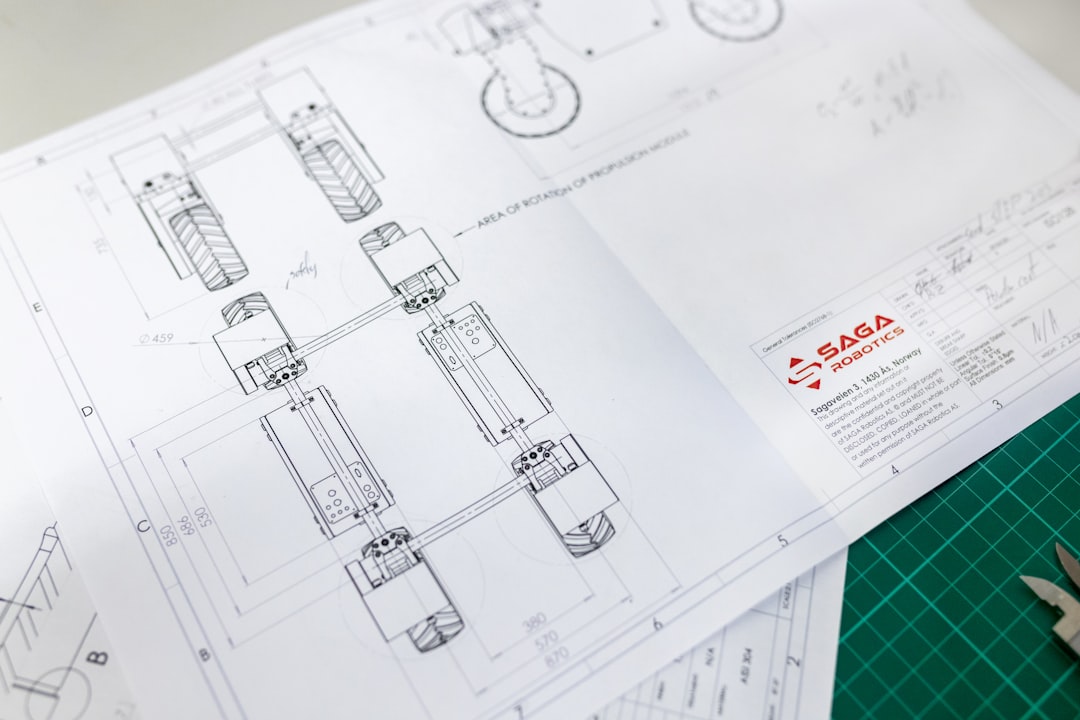
Delving deeper into how structural engineers navigate the 2018 Mechanical Code reveals layers of subtlety beyond the readily apparent requirements for supporting substantial equipment. It compels us to think about less intuitive ways mechanical systems interact with the structure.
For instance, consider the phenomenon of "ice loading," not from external weather, but internally. Large duct systems, particularly in environments with significant temperature differentials and humidity, are susceptible to condensation. If not meticulously insulated or sealed, this trapped moisture can accumulate, and in colder operational cycles or climates, freeze. The resulting ice isn't negligible; it adds substantial weight, often distributed unevenly along duct runs. Curiously, this internal accumulation can impose localized loads on supporting hangers and the primary structure that might creep beyond the original design assumptions, posing an interesting challenge for long-term structural resilience.
Another less common consideration arises with certain specialized mechanical equipment requiring protection from electromagnetic interference. Think about chillers associated with sensitive medical or research equipment like MRI machines. The shielding demanded often involves significant quantities of dense materials such as copper or lead lining the enclosures or pathways. From a structural viewpoint, this shielding represents a considerable, often localized, additional dead load that must be rigorously assessed. It's a structural consequence driven purely by an operational mechanical requirement, highlighting the diverse sources of load.
There's a less discussed potential pitfall concerning acoustic treatments. While intended to mitigate noise and vibration – issues certainly relevant to structural performance – certain applications of sound dampening materials or wraps around mechanical components or ductwork can inadvertently affect the thermal conditions of adjacent structural elements. If improperly designed without adequate ventilation paths, these treatments could potentially lead to localized heat buildup. Elevated temperatures, even if not extreme, can subtly alter the properties of materials like steel or concrete over time, raising questions about potential localized reductions in capacity or increased creep effects under sustained load, a seemingly benign acoustic fix having unintended structural repercussions.
When we think about seismic events, the focus is rightly on lateral force resistance and overall building stability. However, the differential movement or drift between floors during an earthquake presents a specific challenge for mechanical penetrations through structural walls or slabs. If ductwork, piping, or conduits pass through these elements with insufficient clearance or without appropriate, flexible connections, the rigid system can effectively become an unintended diagonal strut or tie. This can introduce significant shear forces or bending moments at the penetration point, potentially damaging the mechanical system itself, compromising the fire rating of the penetration, or, critically, inducing unanticipated stresses in the surrounding structural element, potentially impacting its integrity.
Finally, a frequently overlooked load is the "legacy load" imposed by abandoned or decommissioned mechanical systems. In renovations or analyses of older buildings, we might encounter ductwork runs, capped off piping, or disused equipment that were never fully removed. While no longer operational, their physical mass remains. This residual weight contributes to the building's overall dead load. When evaluating the capacity of existing structural members for new system installations or changes in use, accounting for this 'phantom' load is crucial. Ignoring it could lead to an underestimation of the cumulative stress state, potentially impacting the available capacity for new mechanical loads or other structural modifications. It serves as a reminder that a building's history, in terms of its installed systems, leaves a lasting structural footprint.
The 2018 Mechanical Code: Essential Insights for Structural Engineers - Exploring Alternative Compliance Paths in the IMC
While not always the first consideration, the 2018 International Mechanical Code includes avenues for pursuing alternative compliance methods, a provision pertinent for structural engineers when prescriptive code requirements for supporting mechanical systems prove impractical or hinder design innovation. This capacity allows for justification of non-standard solutions for unique equipment supports, complex routing requiring atypical structural modifications, or performance-based approaches to dynamic loads or thermal effects. The application process and the level of detail required for demonstrating equivalent safety and performance through analysis may have seen subtle shifts or increased application in the 2018 cycle, requiring engineers to be prepared to provide robust technical substantiation. Engaging with these alternative paths demands thorough structural analysis to confirm proposed deviations maintain or exceed the intended level of safety and avoid introducing unforeseen issues into the building's structural integrity.
Moving beyond the prescriptive requirements of the code sometimes becomes necessary, or simply offers potentially better integrated solutions. Navigating these alternative compliance paths within the International Mechanical Code, specifically the 2018 edition we're considering, introduces a different set of considerations, particularly from a structural perspective. It's less about the direct loads from specific equipment types, which we've touched upon, and more about how the *methods* of demonstrating compliance require structural input and verification.
1. Opting for performance-based design, as the IMC permits, necessitates a rigorous demonstration that the proposed mechanical system achieves equivalent or superior levels of safety and functionality compared to the prescriptive code routes. For the structural engineer, this shifts the burden; we aren't just checking against standard tables and limits. We must deeply understand the mechanical system's operational parameters under various scenarios, including potential failure states, and collaborate to define precisely what constitutes "equivalent safety" when dynamic or interconnected system behaviors dictate performance. It forces a less siloed, more integrated risk assessment of the combined mechanical-structural entity.
2. Leveraging computational simulations, such as Computational Fluid Dynamics (CFD), to validate things like ventilation effectiveness under alternative designs offers a powerful tool. However, for these simulations to be meaningful for structural considerations, they demand an accurately modeled physical environment defined by the building structure. The boundaries and internal partitions of the simulation space are inherently structural elements. Ensuring the structural model used for planning or checking clearances is sufficiently detailed and representative of the as-built conditions to support a valid CFD analysis becomes a critical, though perhaps unexpected, link between disciplines.
3. Applying formal risk assessment methodologies to evaluate novel or alternative mechanical designs is a logical step towards quantifying potential outcomes. While these frameworks help identify failure modes and estimate probabilities and consequences for the mechanical system itself, a crucial part involves rigorously assessing the *structural* consequences of mechanical failures (e.g., unexpected forces from system malfunctions) or the *mechanical* consequences of structural issues (e.g., how minor deflection affects system alignment or performance). Successfully implementing this requires a shared language and a deep understanding of the interdependencies, which isn't always straightforward to quantify.
4. Exploring alternative materials that might serve multiple functions, like insulation integrated with stiffening properties to support ductwork or acoustical treatments that also offer limited load resistance, presents an interesting structural challenge. While potentially innovative, these materials often lack the long-term performance data under combined loading (e.g., thermal cycling simultaneously with sustained mechanical load) that traditional structural materials possess. Verifying their durability and ensuring they maintain their structural contribution over the building's life requires careful scrutiny and perhaps a degree of caution until more robust data or specific test standards emerge.
5. Increased prefabrication of mechanical systems, often incorporating their own support frames designed off-site, fundamentally changes the structural engineer's task regarding support design. Rather than detailing piece-by-piece hangers, the focus shifts to verifying the integrity of the prefabricated support structure itself and, critically, designing robust and perhaps complex interfaces where these pre-built assemblies connect to the primary building structure. Furthermore, considering the temporary stresses imposed on these integrated support systems during lifting, transport, and installation becomes a specific structural assessment requirement, quite different from analyzing static operational loads.
More Posts from aistructuralreview.com: