UG NX 2019 Analyzing Key Enhancements in Generative Design and Structural Optimization
UG NX 2019 Analyzing Key Enhancements in Generative Design and Structural Optimization - Generative Design Revolutionizes Traditional Design Process in UG NX 2019
UG NX 2019 introduces generative design, a paradigm shift in the conventional design process. This new approach leverages AI algorithms to produce and assess a vast array of potential designs, pushing the focus towards achieving optimal performance. Instead of the traditional sequence of modeling followed by analysis, designers now start by defining desired outcomes and limitations. This "goals-first" mindset encourages exploration and creativity during the initial stages of design.
By shifting the focus, generative design empowers engineers to explore a wider field of design choices in a shorter timeframe. This optimization isn't simply about speeding things up; it's about fundamentally changing how design constraints are understood and managed. The capability to incorporate intricate performance specifications from the outset streamlines the design journey and allows for a broader range of possibilities. The tools within UG NX 2019, specifically designed for generative design, seamlessly integrate with the established workflow, making this revolutionary approach more accessible. This integration suggests a move towards a more performance-driven approach to design, requiring engineers to adjust their methodologies for an industry landscape undergoing rapid transformation. While the concept holds promise, it remains to be seen how readily it will be adopted and integrated into design processes across various sectors.
UG NX 2019's generative design feature uses artificial intelligence to explore a vast number of potential designs, going beyond what human designers might conceive. Instead of starting with a specific shape and then assessing its performance, this approach prioritizes the desired outcome from the very beginning, defining goals and limits.
This shift in perspective, evident in the NX Topology Optimizer, emphasizes performance over rigid design limitations. Consequently, engineers can quickly explore numerous design variations, significantly streamlining the design process. The traditional "design and then analyze" cycle is disrupted, replaced by a process that initially clarifies the design space and aims.
Generative design serves as a powerful companion for topology optimization, expanding the range of available design options. It incorporates physics-based simulation and analysis tools to guarantee that design performance aligns with requirements. Siemens NX provides a unified set of generative design tools, seamlessly integrating them into the design workflow.
During the preliminary design phases, designers can readily experiment with numerous design iterations thanks to generative design. This is crucial for exploration and concept refinement. While promoted as a forward-looking engineering solution, generative design has profoundly changed traditional engineering methods, leading to a new era in design. It prompts a critical evaluation of how designs are conceived and implemented. The potential of the approach to significantly reduce design time while allowing for designs to incorporate multiple disciplines raises fascinating questions on the future of design in many fields.
The ability to rapidly iterate and optimize designs using simulations—tasks that once took days now reduced to minutes or seconds—is a notable achievement of NX 2019. Further, designs can incorporate a range of analyses from structural to thermal and fluid flow. Notably, it often generates designs that push conventional aesthetic norms, demonstrating its ability to create designs beyond human intuitive expectations. The software's evolving capacity to learn from user interactions provides further refinements to designs over time. However, this evolution of engineering design brings with it the question of what future roles will be for traditionally trained engineers, as the software provides a platform for users to create viable designs, requiring less specific engineering skills than before. This development prompts contemplation on the dynamic balance between computational power and the human aspect of innovative design.
UG NX 2019 Analyzing Key Enhancements in Generative Design and Structural Optimization - Topology Optimization Sets NX Apart in Structural Simulation
Within the realm of structural simulation, NX distinguishes itself through its topology optimization capabilities. This feature automates the process of improving structural designs, aiming to reduce weight while maximizing performance. NX's integration of advanced generative design features further enhances the power of topology optimization. These features allow engineers to efficiently eliminate excess material from designs while staying within defined constraints for load and weight.
This integrated approach is designed to support iterative studies, allowing engineers to explore "what if" scenarios and develop more efficient designs aligned with desired functions. The user interface has been improved, simplifying the comparison and analysis of the results from these studies, making it easier for engineers to refine designs.
The ongoing development of NX's topology optimization and generative design capabilities underscores their potential to significantly alter traditional design practices. As these tools become more powerful, they raise questions about the changing role of engineers in a design environment increasingly reliant on sophisticated software.
NX's inclusion of topology optimization within its structural simulation capabilities offers a noteworthy advancement. It provides a platform for conducting various study types through the Optimization Navigator, allowing researchers to delve into a range of design possibilities. The integration of AI and generative design within recent updates has significantly boosted the functionality of topology optimization, a trend that's been shaping many CAD tools.
Within NX, generative design is effectively linked to topology optimization, enabling the removal of unnecessary material while strictly adhering to defined load and weight parameters. This ability has become more streamlined through what Siemens describes as convergent modeling, seen in NX 12, and provides for a unified approach to 3D modeling. The Topology Optimizer effectively enables "what-if" scenarios, empowering engineers to design based on specific functional criteria.
One of topology optimization's core strengths is its ability to automate the design enhancement process, especially beneficial in early design stages by reducing weight and maximizing performance. However, training is often required, with offerings such as the NX Topology Optimization course, a five-day program aiming to bolster the user's skills in leveraging this design optimization technique.
NX uses finite element analysis within its iterative topology optimization process, allowing it to assess loading conditions and generate design recommendations. The interface in more recent versions has been refined to simplify the process of comparing various study results within the topology optimization function, making result interpretation more straightforward.
It's notable that the software's generative design approach, incorporating tools like topology optimization, is becoming increasingly popular in engineering practices. Its potential for efficient material utilization and improved performance is driving adoption in a wide range of applications. Though promising, there is ongoing discussion as to how readily these methods will be implemented across industries. It's interesting to see how effectively the approach will be used for designing in fields outside of automotive or aerospace. It may prove to be particularly useful for products that have many, complex moving parts where optimization could dramatically change performance. The ability to optimize designs to suit the intended manufacturing method, particularly additive manufacturing, is noteworthy.
While these tools are valuable, the question remains whether the rapid advancement in software design optimization might change the landscape of engineering itself. As software takes over some of the more traditional tasks of engineering, it's worth questioning how this evolution in engineering may require adaptations in how we educate and train engineers.
UG NX 2019 Analyzing Key Enhancements in Generative Design and Structural Optimization - Convergent Modeling Technology Enhances 3D Capabilities
Siemens NX's incorporation of Convergent Modeling represents a notable leap forward in 3D modeling. This technology streamlines the design process by enabling the unification of different geometry types—facets, surfaces, and solids—within a single model without needing data conversions. This is especially valuable when dealing with 3D scanned data, which often arrives as facets, significantly enhancing 3D modeling capabilities. The ability to directly work with facet-based geometry also contributes to increased design efficiency, as demonstrated by productivity gains achieved with features like the 'Combine' command.
Further, tools like Draft Analysis, now able to consider convergent bodies, and streamlined reverse engineering workflows illustrate the practical benefits of convergent modeling. While these improvements are undoubtedly helpful, it's crucial to consider the potential impact of this technology on the design workflow and how engineering professionals integrate these tools into their standard practices. It remains to be seen how widely Convergent Modeling will be embraced and how it will reshape design methodologies in various industries.
Siemens NX's convergent modeling technology offers a way to blend facet, surface, and solid models within a single design space. This capability eliminates the need for data conversion during the design process, promoting a smoother workflow. It's particularly helpful when incorporating scanned 3D data, which often comes in a facet-based format. Introduced with NX 11, this approach allows for direct manipulation of facets, leading to noteworthy efficiency gains.
A new Combine command within NX 1101 adds further flexibility, letting users mix analytic and convergent bodies during modeling. This improves how engineers can create complex designs by providing options to combine different geometric types. Moreover, the enhancements in Draft Analysis now allow convergent bodies as targets for analysis, a step forward in evaluating these hybrid models. The simplification of reverse engineering, especially for scanned models, highlights one of convergent modeling's key advantages. It streamlines working with different geometric representations, simplifying a task previously prone to errors.
Convergent modeling aligns well with the overarching trend of generative design, where design goals are established upfront and then optimized to meet those criteria. Its integration with generative design helps to broaden the range of design possibilities within the optimization process, leading to a faster exploration of different options. This technology isn't just beneficial for generative design, though; it enhances NX's already strong suite of features related to topology optimization and 3D printing. These tools form a core part of Siemens' push towards an integrated design and manufacturing environment. In fact, the technology has been recognized within the CAD industry for its potential to significantly reshape how product design evolves. It remains to be seen, though, how readily designers and engineers will incorporate it into their workflows given the shift in required skills. It could possibly require a shift in how we train engineers, moving away from more traditional approaches to CAD. This presents an interesting question as to how the development of software will shape the future of engineering, and its broader implications on the industry. One interesting area of concern revolves around the fact that as computational power increases, we rely more and more on software to take on the human tasks, and there is a potential risk that engineers lose critical design thinking capabilities. The potential for a disconnect between the theoretical aspects of design and the reliance on black-box automated tools warrants further investigation. Despite the powerful advancements in CAD, we should always take steps to retain the critical analysis skills of design teams.
UG NX 2019 Analyzing Key Enhancements in Generative Design and Structural Optimization - Multiple Design Alternatives Explored Through Generative Design
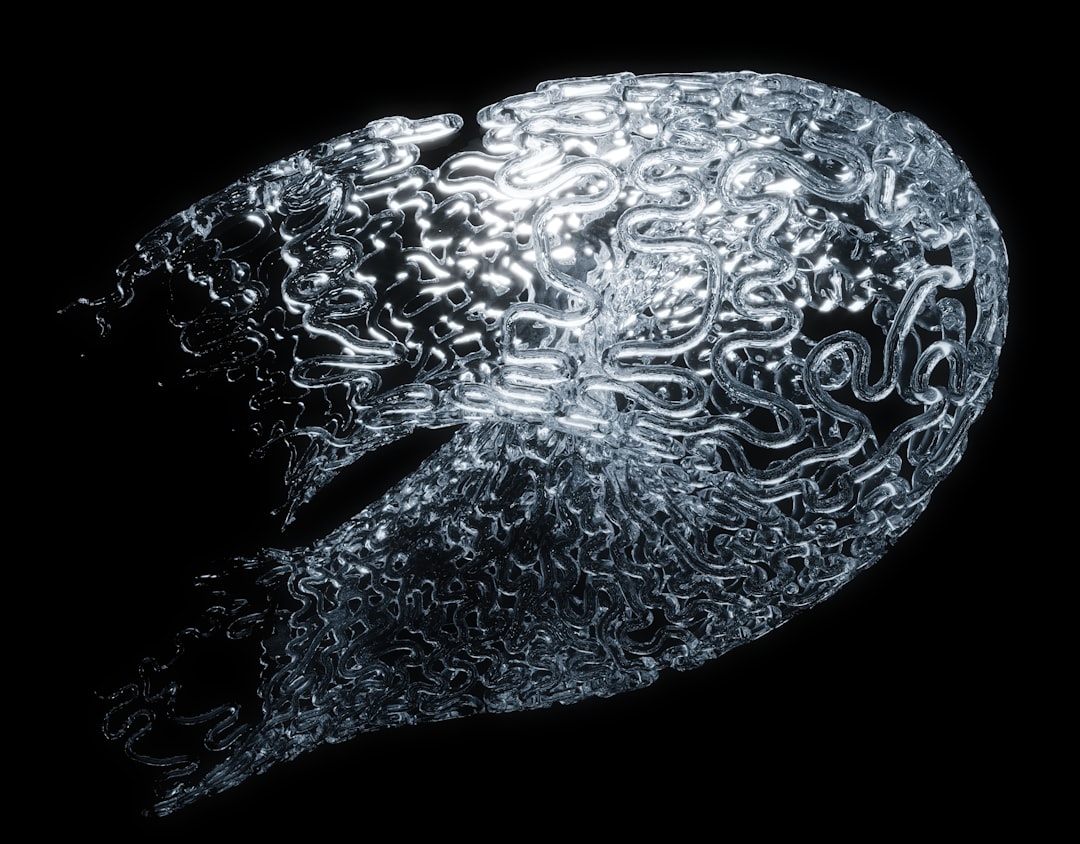
UG NX 2019's generative design capability introduces a new way to explore a much wider range of potential designs compared to conventional methods. Unlike topology optimization, which focuses on a single optimized solution, generative design explores numerous design variations based on predefined criteria. This ability to consider multiple options, informed by performance targets, offers designers a richer understanding of the design space. Furthermore, generative design opens up possibilities for creating more complex shapes, especially when paired with additive manufacturing technologies. This combination allows for the production of intricate designs that may not be achievable with traditional manufacturing processes. However, adapting to the often complex output of these generative design processes can be challenging for many existing CAD software packages. Many systems struggle with handling the facets generated during the optimization process and struggle to make modifications. Therefore, properly leveraging this technology necessitates strong training to ensure engineers can efficiently incorporate and manipulate the resulting designs while maintaining design integrity within the constraints of the current CAD systems and the wider engineering process. The potential, while powerful, also emphasizes the need for ongoing education and skill development in the field of design and engineering.
Generative design in UG NX 2019 allows engineers to explore a vast range of design possibilities, potentially thousands, exceeding the scope of traditional design methods. This broadened design space encourages creativity and innovation, unveiling design solutions that might not be readily apparent through human intuition alone. The underlying algorithms utilize mathematical optimization approaches like genetic algorithms and gradient-based optimization to hone designs towards optimal performance and material efficiency. This often results in designs with unusual, yet functional, shapes.
By incorporating simulations across various disciplines—such as structural, thermal, and fluid flow—generative design promotes interdisciplinary collaboration. This allows engineers with diverse expertise to contribute valuable insights into a design's multifaceted performance requirements. Following design generation, feasibility analyses assess not only performance but also practical aspects like manufacturability and cost, offering a more holistic approach to design evaluation.
Generative design grants fine-grained control over design parameters, such as load paths and material distribution, which was previously difficult to achieve through traditional techniques. This level of detail facilitates the creation of customized solutions tailored to specific applications. The seamless integration of generative design within UG NX allows for real-time feedback loops. Modifications made to design criteria are instantly reflected in the design output, enabling continuous adaptation and exceeding the capabilities of traditional design workflows.
Though generative design frequently results in complex geometries, it also reveals opportunities for structural simplification by pinpointing and eliminating redundant material. This has the potential to reshape our understanding of "over-engineering," leading to designs that are simultaneously stronger and lighter. With the automation of some aspects of the design process, the role of engineers might shift towards a more strategic oversight function. They could be responsible for defining design goals and interpreting results rather than performing routine calculations, enhancing the strategic value of their contribution.
Moreover, machine learning algorithms are increasingly being incorporated into generative design systems within UG NX. These systems learn from past design projects to refine the search for optimal solutions in future endeavors. This learning capability continuously enhances the system's design generation ability.
However, the increasing reliance on generative design raises questions about the importance of fundamental engineering skills. The possibility of relying too heavily on automated systems could potentially diminish critical thinking abilities in design. The optimal approach likely involves a careful balance between leveraging technological advancements like generative design and maintaining the development of core engineering thought processes. While we continue to explore the exciting potential of generative design, ensuring the preservation of core design thinking is crucial in navigating this new era of design.
UG NX 2019 Analyzing Key Enhancements in Generative Design and Structural Optimization - User-Friendly Interface Reduces Learning Curve for New Features
UG NX 2019's enhanced user interface makes it easier for users to learn and apply new features, fostering a smoother and more positive experience. Features like the Adaptive UI cater to individual preferences and working styles, potentially boosting efficiency. The design consistency across the interface reduces mental strain, promoting intuitive interaction and a quicker grasp of new tools. This is especially important given the complexity of engineering software, where user engagement can sometimes be a challenge. As generative design and structural optimization become more integrated into design processes, the improved interface helps users fully exploit the power of these tools. However, it's worth considering whether the focus on user-friendliness might lead to a simplification that hinders the development of advanced skills and deeper understanding. The long-term implications of a streamlined, intuitive interface for training and skill development are important aspects to watch as these technologies mature.
The user-friendly nature of UG NX 2019's interface is notable in how it reduces the time it takes to become proficient with new features. It appears they've designed the interface with the idea that usability directly impacts how quickly engineers can adapt to the software's capabilities, potentially leading to a faster adoption rate of new functions. It's interesting to consider how this approach might change how engineers engage with new software releases, leading to less resistance and a smoother transition to new workflows. However, there is always the question of whether simplifying the user interface sacrifices some control or flexibility for the user in the process.
Improvements to the interface seem to prioritize streamlining the design process. Features like a more logical arrangement of tools, potentially requiring fewer steps to access commonly-used functions, might contribute to engineers spending more time designing and less time navigating menus. This focus on usability can also contribute to reducing cognitive overload—the mental effort needed to use a system. The idea behind this approach is that reducing the mental effort spent on learning the interface can free up mental resources for more complex design tasks.
It's worth considering if the introduction of Adaptive UI is effective in personalizing workflows. The ability to tailor the interface to a user's context and specific needs is a feature that could enhance productivity if implemented successfully. While seemingly beneficial, one wonders if personalization features create a fragmented learning experience across engineering teams, potentially leading to knowledge silos or inconsistencies in design methodologies. This trade-off between individual customization and standardization across projects is an interesting consideration for those deploying and utilizing these tools.
The introduction of features like a 'Linked Feature' column in the WAVE Interface Linker illustrates how subtle changes can impact user experience. While seemingly minor, the fact that linked entities can be visualized without needing to interact with a specific feature can help in troubleshooting and design validation. This is a good example of how even small updates to the interface can result in productivity gains and a better understanding of what's happening within the software.
Changes introduced since NX 11 seem to indicate a focus on refining usability without resorting to drastic interface overhauls. The fact that core elements like the ribbon and menus have been left untouched while improving functionality behind the scenes is an interesting approach. This approach of iterative improvements, rather than drastic revamps, might allow users to smoothly adopt new functionality while maintaining familiarity with the software's core elements. It remains to be seen whether this conservative approach is universally beneficial or if a larger-scale overhaul of the user interface would have a more positive impact.
Consistency across the user interface seems to play a key role in simplifying how users interact with the software. The idea that users can predict how features will behave based on past interactions is key in allowing for quicker adoption of new capabilities. This relates to a concept often discussed in the field of human-computer interaction where consistency between elements of the interface can lead to a reduction in errors and a smoother learning curve. However, the question remains whether relying on consistency can sometimes be detrimental if it prevents incorporating new paradigms and potentially valuable interactions.
The introduction of over 350 enhancements in NX 12 shows that Siemens continues to prioritize improving the software's capabilities. These kinds of incremental improvements, in conjunction with focusing on a user-friendly interface, are expected to translate to better software for the end users. However, it also raises the question of whether a software with so many potential enhancements and different functionality can remain manageable and user-friendly.
The challenges that poor interfaces pose for user engagement is worth acknowledging. In an environment where engineering software needs to facilitate highly complex tasks, the importance of well-designed user interfaces is clear. One wonders whether this emphasis on user-centered design is permeating throughout the engineering industry at the rate necessary to improve overall productivity and innovation. It's an important consideration as we transition to an era where reliance on highly sophisticated tools is expected.
The focus on continuous UX/UI improvements in industrial engineering software like NX points to the importance of usability in maintaining user satisfaction and minimizing errors. The idea that consistent visual and functional elements contribute to a positive experience is something that designers of any type of software should keep in mind. How this emphasis on uniform elements affects the overall look and feel of the interface across different versions of NX will be interesting to observe. There is a potential for a homogenization of design across products within the Siemens software platform which can help ensure consistency.
UG NX 2019 Analyzing Key Enhancements in Generative Design and Structural Optimization - Additive Manufacturing Drives Advancements in Optimization Tools
Additive manufacturing is significantly changing how we design and optimize products, especially within the context of Industry 4.0. Tools like topology optimization and generative design are becoming increasingly important, helping engineers create unique, lightweight parts specifically designed for additive processes. By incorporating advanced simulation methods, designers can explore a wider range of design options, often resulting in shapes that traditional manufacturing can't produce. However, as these technologies improve, standard CAD systems struggle to fully leverage additive manufacturing's potential. This highlights a growing concern about how engineering practices and the skills needed by designers will evolve. While the move towards designing for performance is exciting, it also raises concerns about relying too much on complex software while neglecting core engineering principles. Finding a good balance between advanced computational tools and foundational engineering knowledge will be crucial as additive manufacturing continues to mature.
Additive manufacturing (AM) is significantly impacting the development of optimization tools, particularly within the context of Industry 4.0. This impact is so profound that we're seeing projections of a substantial increase in the market value for this type of technology. Structural optimization, including methods like topology optimization (TO), has long been a cornerstone of creating efficient and sustainable product designs.
Generative design (GD) and TO are key methods in design for additive manufacturing (DfAM), enabling engineering approaches that prioritize performance. GD allows for comparisons between design outcomes for intricately shaped aerospace components like blades or airfoils, pushing beyond traditional constraints. Integrating complex lightweight designs into AM processes improves the design workflow by using multiscale simulations to maximize the advantages of the technology.
Currently, we are seeing the limitations of older CAD systems as the capabilities of TO and GD tools for AM become better recognized. Cellular structures, for example, which are easily created with AM, demonstrate benefits like high strength-to-weight ratios and energy absorption while reducing material waste.
TO is a mathematical approach that finds the optimal arrangement of material within a design by considering loads and boundary conditions. AM's capability to fabricate complex shapes not feasible with traditional methods underscores its importance for driving innovation. Enhanced design procedures for AM require designers to integrate advanced optimization techniques into the workflow to truly take advantage of the potential.
It's interesting to see how much AM has changed our understanding of design. It has the potential to push design boundaries in a way that might challenge established methods and the role of the engineer in the process. There are many questions yet to be answered, though, about the effect of software and the resulting designs on the engineering community. It's interesting to see how engineers adapt to the changing design landscape.
More Posts from aistructuralreview.com: