Understanding Continuous Feature Requirements in GD&T Impact on Aircraft Component Design
Understanding Continuous Feature Requirements in GD&T Impact on Aircraft Component Design - Understanding CFZ Basic Geometry Rules for Aircraft Turbine Components
Understanding the fundamental geometric rules within the context of Continuous Feature Zones (CFZ) is crucial for designing safe and reliable aircraft turbine components. These rules establish precise alignment and tolerance requirements, a necessity given the extreme operating conditions these parts endure. The Continuous Feature symbol within GD&T becomes particularly important here. It dictates that separate, or disjointed, features should be treated as a single, unified element when considering geometric controls, significantly influencing how turbine component geometry is managed. Moreover, the growing use of variable geometry turbines introduces an additional layer of complexity. These design changes, intended to optimize performance dynamically, must be aligned with the established CFZ rules. This is critical as turbine components, like rotors and casings, need to withstand operational stresses far exceeding their typical design parameters, often up to 115% of their rated speed. Designers must meticulously account for the potential for plastic deformation and fatigue life under such conditions. Failure to adhere to these geometric principles could have serious consequences, highlighting the importance of a thorough understanding of CFZ rules for ensuring safe and effective turbine operations.
Continuous Feature Zones (CFZ) within turbine components aim to enforce consistency in intricate shapes, which is critical for enduring the high-stress environments they operate in. Maintaining this consistency is paramount for the longevity of vital engine parts. These geometrical rules governing CFZ demand that parts maintain strict tolerances because even small deviations can cause significant performance problems, such as increased vibrations or efficiency losses during operation.
The connection between CFZ and GD&T is vital as GD&T acts as a standard language to convey design intent and desired functionality to the manufacturers. Understanding this link allows for more precise design and manufacturing. In turbine blades, CFZ concepts assist in improving aerodynamic effectiveness, influencing thrust production and fuel consumption. It is important that these blade geometries can withstand extreme temperatures while managing airflow.
CFZ guidelines frequently use finite element analysis (FEA) to model how components will react to environmental stresses, assisting in predicting possible failure points before physically testing the part. When many components are assembled, tolerance stacking can significantly impact the overall assembly and thus emphasizes the need for precisely defined CFZ. The result of poor tolerance management is often assembly challenges and compromised structural integrity.
Engineers must consider thermal expansion in CFZ because temperature shifts during flight can impact part dimensions. If not managed properly, variations in temperature can negatively impact turbine performance. Newer manufacturing processes like additive manufacturing are prompting a re-evaluation of traditional CFZ standards, requiring engineers to adapt their approach to geometry given these newer production methods.
By leveraging aerodynamic principles to optimize shapes and sizes, CFZ implementation can lessen turbine component weight without sacrificing strength. Lastly, incorporating CFZ rules into the early design phase often results in lower manufacturing costs by minimizing rework and adjustments during machining, which are a consequence of a precise understanding of tolerance constraints.
Understanding Continuous Feature Requirements in GD&T Impact on Aircraft Component Design - Impact of Surface Continuity Requirements on Wing Panel Design
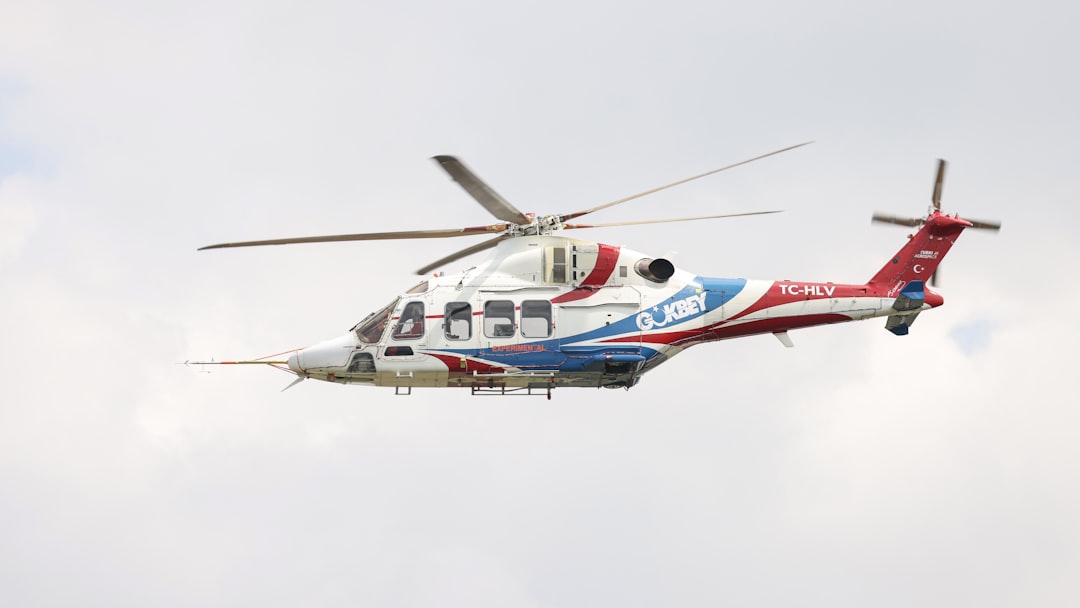
The design of wing panels is significantly influenced by the need for continuous surfaces. This requirement for continuity is crucial for maintaining structural integrity and ensuring optimal aerodynamic performance. Wing panels, being critical aircraft components, must meet precise geometric specifications to effectively manage stress distributions and prevent failures like buckling. However, advancements in manufacturing, particularly with techniques like additive manufacturing and the use of composite materials, introduce complexity into how surface continuity is achieved. This is because these newer methods create challenges related to the continuous flow of surfaces in unique ways.
Furthermore, the design of wing panels using composite materials requires a meticulous focus on how the layers (or plies) are arranged. This aspect, known as ply continuity, can have a substantial impact on a wing panel's weight and its operational effectiveness. As the aerospace industry continues to push boundaries with innovative designs, the ongoing evolution of manufacturing technology requires a careful integration of surface continuity requirements into these novel design processes. Successfully integrating these requirements is key to maximizing wing panel functionality and achieving the desired levels of durability for various aircraft applications.
The pursuit of surface continuity in aircraft wing design isn't merely about achieving a pleasing aesthetic; it's intrinsically tied to aerodynamic performance. A smooth, uninterrupted surface minimizes air turbulence, boosting lift and curtailing drag, which translates into improved flight efficiency. This pursuit of smoothness, however, can be a double-edged sword. The precision demanded by GD&T tolerances for achieving surface continuity can lead to accelerated tool wear and extended machining times, potentially impacting production timelines and cost.
Fortunately, the evolution of CAD software has enabled engineers to more readily simulate surface continuity under diverse loading conditions, allowing them to predict and potentially mitigate design flaws earlier in the process. This proactive approach, in contrast to addressing issues after production, promises a more efficient design cycle. However, the need for surface continuity must be balanced against other critical design requirements. For instance, in high-stress regions of the wing, structural integrity may necessitate deviations from a perfectly smooth surface, creating intricate design trade-offs.
Additive manufacturing (AM) is reshaping our understanding of surface continuity in wing design. AM's capacity to create complex geometries could lead to a departure from traditional flat-panel approaches, demanding new standards for evaluating surface continuity. Furthermore, the surface continuity specifications dictated by GD&T can pose assembly challenges. If wing panels don't adhere to these specifications, aligning them during assembly can be problematic, potentially compromising the overall structural integrity of the wing.
Our observations show that even subtle variations in surface continuity can significantly impact aerodynamic forces acting on wing panels, potentially resulting in suboptimal performance. This reinforces the critical importance of adhering to GD&T principles. To guarantee adherence to these principles, technologies such as laser scanning are gaining traction in the aviation industry for verifying surface continuity. This technology allows for the detection of minute deviations that might escape traditional inspection methods, ensuring components fall within the desired tolerance ranges.
Intriguingly, failure to meet surface continuity standards for a wing panel can trigger a cascade effect, potentially requiring a comprehensive redesign of the entire wing structure. This highlights the deeply interconnected nature of design elements and emphasizes the importance of a holistic design philosophy. The impact of surface continuity requirements extends beyond the wing panel itself. They influence the overall weight distribution and center of gravity of the aircraft, directly affecting its stability and handling characteristics during flight. Understanding these interdependencies is vital for crafting safer and more efficient aircraft.
Understanding Continuous Feature Requirements in GD&T Impact on Aircraft Component Design - Feature Control Frame Applications in Landing Gear Manufacturing
Landing gear, with its intricate components and critical role in aircraft operation, relies heavily on Feature Control Frames (FCFs) to establish and communicate essential tolerance requirements. These frames, using the language of Geometric Dimensioning and Tolerancing (GD&T), are vital for ensuring proper component alignment and integration during assembly. Deviations from these tolerances can have significant consequences for aircraft safety and functionality.
Crucially, the concept of continuous features is often incorporated within these FCFs. This means that even when a feature is made of multiple, disjointed parts, GD&T dictates that they be treated as a single, unified entity. This approach is vital for managing tolerances and ensuring reliable performance in landing gear systems.
Additionally, evolving GD&T standards, particularly regarding composite positional tolerances, allow for more flexibility in design while maintaining stringent control over orientation parameters. This offers designers more freedom in creating efficient landing gear designs, but it also demands careful consideration and adaptation by manufacturers to ensure parts meet the rigorous functional needs of modern aircraft. The evolving application of these principles highlights the importance of remaining current with GD&T standards to ensure that landing gear systems meet the highest possible performance and safety requirements.
Feature Control Frames (FCFs) play a crucial role in landing gear manufacturing, where even minuscule deviations from specified dimensions can have significant, even catastrophic consequences during landing or takeoff. Essentially, FCFs, using the language of Geometric Dimensioning and Tolerancing (GD&T), provide a blueprint for allowable variations in manufactured features. The Continuous Feature symbol within GD&T is especially relevant in this context, as it emphasizes treating groups of disjointed features as a single, continuous entity when applying tolerances.
Understanding how to interpret these frames is critical, including the leader arrows that pinpoint the specific feature being controlled and the geometric symbols and control types within the frame itself. This knowledge is further amplified by standards like ASME Y14.5-2018, which defines composite positional tolerances – scenarios where we prioritize precise orientation over strict location. Notably, the differences between composite and multiple single segment FCFs are revealed in their base frameworks. In essence, composite FCFs are focused on refining a part's orientation and location relative to other features.
Within landing gear design, we see FCFs are crucial for setting tolerances and ensuring consistency in how parts are assembled and interact. This precision is important due to the complexity of landing gear assembly; multiple geometric tolerances are often simultaneously considered. The intricate interplay between individual part tolerances and the whole system's performance is crucial for designers to grasp, as tolerance stacking can quickly amplify errors.
Furthermore, engineers often leverage finite element analysis (FEA) for simulating how the landing gear responds to dynamic stresses it experiences during operation. FEA allows for the identification of potential weak points in the design, making the design process less prone to physical prototyping errors. The choice of materials, like high-strength aluminum alloys or titanium, is another important aspect where FCFs impact performance. They directly influence how these materials respond to manufacturing processes, impacting their ultimate strength and durability.
It is important to consider that even seemingly small variations can impact landing gear functionality over time. This wear can occur due to repetitive stresses, and GD&T provides the means to monitor and plan for these changes. It also helps in predictive maintenance, which in turn keeps systems ready to perform when needed.
The advent of additive manufacturing adds a new layer to this challenge. The unique geometries possible with 3D printing present challenges to traditional GD&T principles, necessitating a more detailed evaluation of feature continuity and alignment. In essence, engineers are working on developing new methods to ensure parts manufactured with AM meet design intent and safety standards.
The landing gear system, especially the hydraulic actuator portion, depends on very precise feature control for safe and reliable operation. Any deviation can lead to either poor performance or the failure of the gear to deploy or retract correctly, posing significant safety risks. Additionally, FCFs can impact aerodynamic performance by shaping the landing gear's geometry when it is extended. Optimization of these features can help reduce drag, contributing to improved fuel efficiency.
However, the complexities don't stop there. Landing gear design must pass stringent certification processes, highlighting the critical nature of compliance with established GD&T standards. Any failure to adhere to these guidelines can lead to delays and substantial redesign efforts. This is particularly true in the interconnected nature of landing gear with other aircraft systems, including braking and steering mechanisms. If feature control in one component is not as specified, the ripple effect can cascade through the system. Therefore, GD&T's impact extends far beyond individual parts and emphasizes the interconnectedness of the aircraft systems and the necessity for a holistic approach to aircraft design.
Understanding Continuous Feature Requirements in GD&T Impact on Aircraft Component Design - Position Tolerance Zones for Continuous Features in Engine Mounts
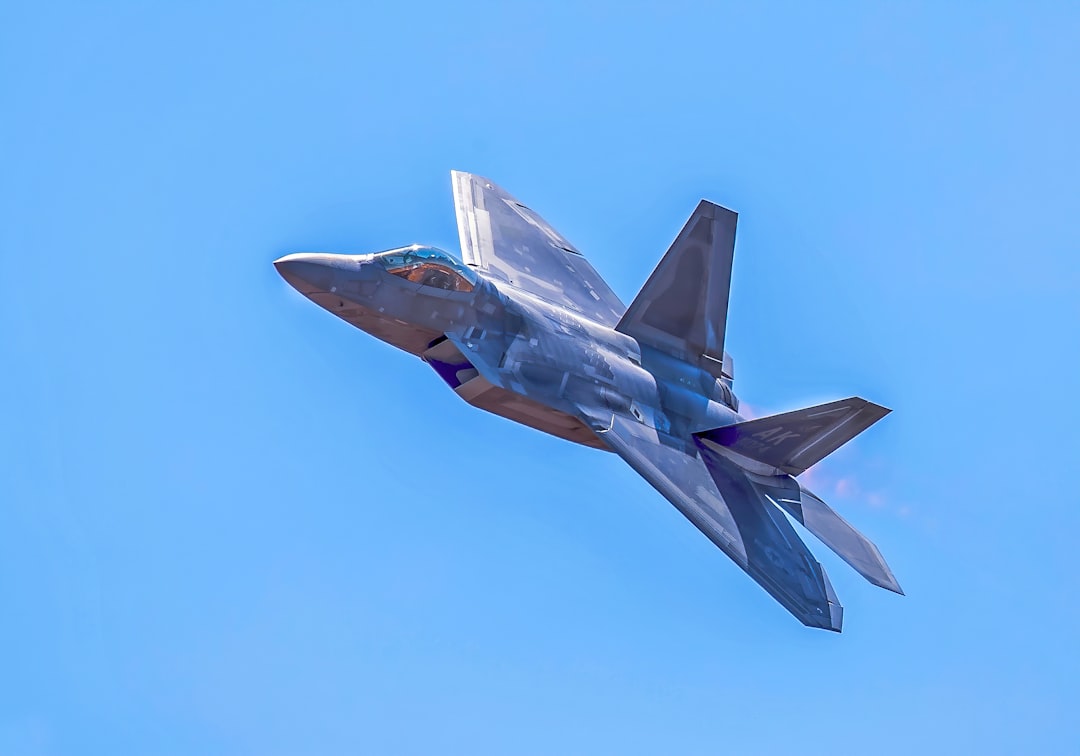
Engine mounts rely heavily on the correct positioning of continuous features, and understanding how position tolerance zones are applied is vital for ensuring reliable aircraft operation. The concept of True Position, often visualized with a crosshair symbol, becomes especially important here. It dictates the ideal location of a feature relative to established datums. The tolerance zone itself, typically a cylinder in this context, defines the permissible range of variation around that ideal location. This is critical for ensuring proper engine attachment and preventing stress concentrations during operation, which are key to ensuring engine mounts can safely secure the engine to the aircraft.
The application of these zones becomes more complex with the evolving design standards and manufacturing techniques used in aircraft development. Newer GD&T standards and the adoption of processes like additive manufacturing require a reevaluation of traditional approaches. This is further complicated as these position tolerances must consider not only the individual component, but also the overall assembly and how tolerance stackup could impact performance or reliability. It's not enough to just understand the specific features of a mount – understanding how they contribute to a larger, integrated system is increasingly vital. This requires engineers to be increasingly aware of how changes to position tolerance zones for continuous features can impact not just the mount, but the entire system it's a part of, which is crucial for ensuring aircraft structural integrity and flight safety in challenging environments.
Continuous feature tolerance zones within engine mounts are essential for ensuring proper assembly and functionality within the stringent dimensional constraints of aircraft design. Even slight deviations from these zones can lead to assembly problems or even component failure during dynamic operations, underlining the critical role of precise manufacturing in aircraft engine design.
Engine mounts experience substantial dynamic loading during flight, often exceeding their typical design parameters. Understanding how these positional tolerance zones for continuous features accommodate not only the static dimensions but also the dynamic changes due to engine vibrations and aerodynamic forces is paramount for their safe and reliable operation.
The emergence of advanced manufacturing techniques, like additive manufacturing, has prompted a reevaluation of traditional tolerance specifications. Additive manufacturing's ability to create complex geometries can challenge standard design practices, pushing engineers to adapt how they apply GD&T specifically for these newer production methods.
The cumulative impact of positional tolerances within continuous features can greatly influence the overall performance of assembled engine components. Engineers need to understand tolerance stacking, the phenomenon where small errors in multiple features compound, creating larger misalignments and potentially impacting performance and safety.
The choice of material for engine mounts significantly impacts how the positional tolerance zones are maintained and interpreted. Materials with varying coefficients of thermal expansion can exhibit different expansion or contraction under temperature changes, making the selection process critical for satisfying GD&T requirements.
Finite element analysis (FEA) is a valuable tool for evaluating continuous feature tolerance zones and simulating component responses to various stress conditions. FEA allows engineers to identify potential failure points during the design stage, before manufacturing, enhancing component reliability and safety.
Continuous features operating under high stress can undergo "flexural fatigue," a phenomenon where suboptimal tolerances lead to deformation under repeated loading cycles. This emphasizes the importance of implementing robust GD&T specifications within the design phase to address these potential failure modes.
Following tolerance zones for continuous features influences not just the initial design but also maintenance schedules. Components remaining within the specified tolerances can lead to reduced wear, longer operational lifespans, and lower long-term operational costs.
Failing to maintain positional tolerance zones can result in not only performance degradation but potentially also structural failures. Within the extreme operating conditions encountered by engine mounts, even small deviations can compromise the integrity of the entire engine assembly, leading to catastrophic events.
Compliance with GD&T standards and continuous feature tolerances is not just a technical matter but also a regulatory one. Aircraft components are subject to rigorous safety certifications, and any failure to meet the established tolerance requirements can result in significant delays or even rejection of the certification process.
Understanding Continuous Feature Requirements in GD&T Impact on Aircraft Component Design - GD&T Pattern Requirements for Multiple Fastener Locations
When designing aircraft components, accurately defining the locations of multiple fasteners is critical for ensuring the structure's integrity and proper function. GD&T pattern requirements provide a structured approach for specifying the dimensions and tolerances of these fastener arrangements. This is important because even small deviations in the alignment or spacing of fasteners can negatively impact how parts fit together and ultimately, how the component performs. The goal is to minimize the chances of misalignment during assembly and prevent operational problems or failures.
Applying GD&T to fastener patterns helps streamline manufacturing processes and reduces errors. This can lead to significant cost savings by minimizing the need for rework or scrap. However, the field of manufacturing is constantly evolving, with newer techniques like additive manufacturing coming into play. This means engineers must continuously adapt their understanding of GD&T to accommodate the complexities of novel materials and designs. It's a reminder that clearly defining fastener dimensions and tolerances is crucial for all types of components and across all manufacturing methods. By continuing to follow these standards, we can enhance the safety and extend the operational life of aircraft parts.
Geometric Dimensioning and Tolerancing (GD&T) is a cornerstone of engineering design, especially for aircraft components, as it ensures accuracy and consistency during manufacturing and assembly. The ASME Y14.5 standard provides a common language for interpreting these specifications. When dealing with multiple fastener locations, the application of GD&T pattern requirements is particularly vital. This is because slight misalignments can severely impact load distribution and potentially lead to fatigue failures, especially in areas experiencing significant stress during flight.
The choice of whether to use circular or rectangular patterns within a GD&T scheme can influence both machining processes and tooling requirements, ultimately impacting efficiency. It’s important to consider how these choices link to optimal manufacturing methods. When multiple fasteners are involved, tolerance stack-up becomes a critical consideration. The accumulation of small tolerances from each fastener hole can lead to larger errors in the final assembly. This potential for compounding errors makes careful analysis essential for complex assemblies.
Interestingly, GD&T allows for patterns to be replicated based on symmetry, which simplifies inspection and assembly procedures. This ability can be a real boon in production, making quality control more manageable. Furthermore, understanding how the manufacturing process impacts GD&T pattern requirements is key. Traditional machining techniques differ significantly from additive manufacturing, which allows for complex, intricate designs that require different GD&T approaches.
Datum references play a crucial role in ensuring proper alignment. Without precise datum definitions, there’s a higher risk of misaligned parts, which can damage the structural integrity of the overall assembly and lead to safety hazards during operation. Advanced technologies like 3D laser scanning are revolutionizing how we verify that GD&T specifications for multiple fastener locations are met. This approach allows for incredibly precise measurements, often identifying discrepancies that might be missed by older, more conventional inspection techniques.
Dynamic loading is another important aspect to consider. Fastener patterns must account for the stress changes components experience during flight, which can be complex and challenging to design for. Designers must be mindful of the interrelationship between fastener locations and other systems or components on an aircraft. Changes in one area might necessitate adjustments in related areas. This underscores the interconnectivity of aerospace design and the need for a comprehensive, holistic approach.
Examining the historical evolution of GD&T standards provides insight into how the field has progressed. As our technology has advanced, so has our understanding of material behavior. The shift towards sophisticated pattern requirements from simpler tolerancing methods reflects the increasing complexity of aircraft designs. It’s a testament to the field of engineering being in a state of continual development and highlights the importance of engineers adapting to new knowledge and methods.
Understanding Continuous Feature Requirements in GD&T Impact on Aircraft Component Design - Manufacturing Implications of Profile Tolerancing for Continuous Surfaces
"Manufacturing Implications of Profile Tolerancing for Continuous Surfaces" explores the challenges of achieving and maintaining surface smoothness in aircraft component design, especially within the framework of Geometric Dimensioning and Tolerancing (GD&T). Profile tolerancing is a core aspect of this, establishing the acceptable limits of surface shape deviations, and thus directly impacting the manufacturing process and the quality of the final part. The introduction of new symbols, like "all over", improves how tolerance requirements are communicated, but simultaneously adds hurdles for manufacturers to consistently achieve those high-precision standards in critical applications. Furthermore, the evolution of production technologies, with additive manufacturing being a prime example, requires us to rethink and revise traditional GD&T approaches, especially when dealing with more complex shapes. This is crucial as the failure to properly implement profile tolerancing can cause a wide range of performance issues and safety risks. It's clear that rigidly adhering to GD&T is essential when manufacturing continuous surfaces in the aerospace industry.
Applying continuous feature tolerancing fundamentally shifts how engineers approach design, especially for complex structures. Deviations that might seem small on individual parts can lead to significant misalignment in the assembled system, potentially compromising structural integrity. This emphasizes the importance of a holistic understanding of how all parts interact.
Within GD&T for continuous surfaces, the adherence to positional tolerance zones doesn't just control individual features; it also shapes how the entire system performs during assembly. Engineers need a thorough grasp of how each component reacts under loads.
Advanced manufacturing methods, like additive manufacturing, are challenging conventional GD&T practices. This means engineers must adapt how they use profile tolerances to embrace new design possibilities and performance needs. This shift raises questions about how we apply established standards in innovative ways.
The distinctive nature of continuous features necessitates specific evaluation approaches. For example, laser scanning technology is becoming vital for checking tolerances. This technology is more sensitive than traditional methods and can uncover subtle discrepancies that might be missed otherwise.
Interestingly, the complexities of thermal expansion in continuous features mean that material choice and testing must be taken seriously. Variations in material behavior can cause unforeseen problems if not addressed in the initial design phase.
Using continuous profile tolerances can reduce the likelihood of fatigue failures in aircraft parts. Understanding how stresses are distributed throughout these features allows engineers to create optimized designs and extend the service life of crucial parts.
Effectively using continuous feature tolerances can save a lot of money during manufacturing. Reducing rework and scrap due to manufacturing issues leads to greater efficiency and better use of resources.
The interplay between different GD&T standards and continuous features can lead to confusion. Engineers must have a firm understanding of the most up-to-date regulations and technical innovations to meet the changing needs of the aerospace industry.
A small oversight in defining profile tolerances can create a ripple effect. Failing to meet specifications in one area can result in significant redesigns across several components and delay projects considerably.
Continuous surface requirements are inherently connected to aerodynamic performance. Maintaining these tolerances isn't just about structural integrity; it directly impacts lift and drag, which emphasizes the complex role of GD&T in aerospace design. This points to the interconnectivity of aircraft design.
More Posts from aistructuralreview.com: