Choosing Structural Stainless 174 PH Or 304 A Review
Choosing Structural Stainless 174 PH Or 304 A Review - Assessing Mechanical Performance Beyond Standard Data Sheets
Evaluating how structural stainless steels like 17-4 PH and 304 will perform mechanically necessitates moving beyond simple reliance on standard material data sheets. While established test procedures provide fundamental values such as strength and yield limits, these numbers offer an incomplete picture of behavior under actual service stresses and environmental influences. The complex ways materials interact with their surroundings and applied loads in real structural use are often not fully captured by idealized lab tests. Contemporary understanding in material science continues to reveal more subtle aspects of steel behavior, suggesting that performance involves factors not traditionally listed on a standard sheet. Therefore, a thorough assessment demands a broader perspective, combining necessary empirical testing with critical analysis tailored to the intended structural role, acknowledging that the numbers on a sheet are merely a starting point, not the full story of a material's capability.
It's easy to focus on the headline numbers on a standard mechanical datasheet – yield strength, tensile strength, elongation from a simple tensile test. But real-world structural performance involves scenarios far more complex than a slow pull in a controlled lab environment. As engineers, we need to look deeper.
Consider dynamic loading or impact events; here, the rate at which strain is applied matters profoundly. Standard quasistatic tests don't reveal how material flow stress might increase under high strain rates, potentially altering deformation modes and perhaps surprisingly reducing the energy-absorbing capacity if ductility suffers.
Then there's fatigue, the insidious failure mechanism under repeated stress cycles. A datasheet might show impressive static strength, but it says nothing about how many times the material can be loaded and unloaded, even at stresses well below the yield point. Determining the true fatigue limit, that critical stress threshold for seemingly infinite life, requires extensive and costly cyclic testing – data rarely presented alongside basic static properties.
Temperature is another critical variable. While alloys like 304 are known for excellent low-temperature properties, even seemingly ductile materials can exhibit a transition where fracture behavior changes dramatically, becoming brittle at cryogenic temperatures. Room-temperature fracture toughness values or ductility figures don't necessarily predict this shift, posing a potential risk in certain applications.
Furthermore, structural fabrication often involves welding, and it's vital to recognize that the material in the heat-affected zone (HAZ) adjacent to a weld is not the same as the parent material. Microstructure is altered, residual stresses are locked in, and both mechanical properties (like toughness) and potentially even corrosion resistance can be significantly different from the datasheet values for the base metal alone.
Lastly, for grades like 17-4 PH, which rely on specific precipitation hardening treatments, the susceptibility to environmental factors like stress corrosion cracking isn't simply a function of listed strength or hardness. Different tempers can exhibit vastly different resistances in specific corrosive environments, and relying solely on standard strength data without considering the temper's interaction with the service environment is a significant oversight.
Choosing Structural Stainless 174 PH Or 304 A Review - Evaluating Corrosion Resistance Across Diverse Structural Exposures
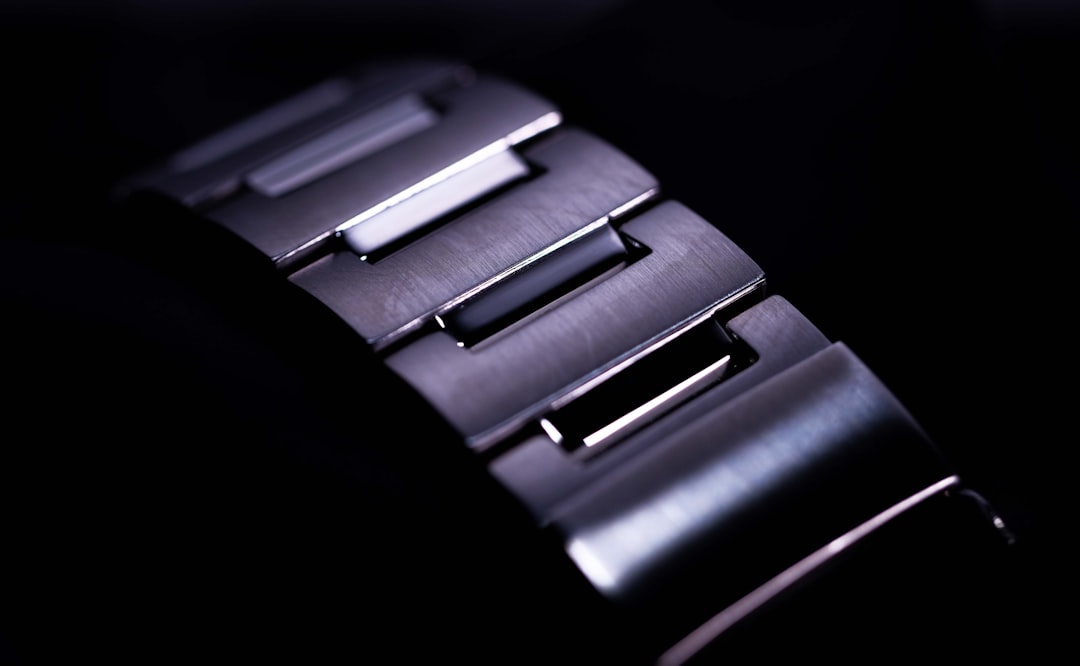
Assessing how structural stainless steels perform under the diverse environmental conditions they encounter is paramount for predicting their long-term reliability. Different service exposures present unique threats; for example, marine or industrial atmospheres laden with chlorides can aggressively challenge a material's resistance. The degree to which stainless alloys, including types like 17-4 PH and 304, withstand corrosion in these varied settings is highly sensitive to factors like their specific metallurgical state and the exact chemical and physical conditions of the environment. Comprehending the mechanisms governing the formation and maintenance of the passive film, as well as the initiation and propagation of localized attacks like pitting or crevice corrosion under these real-world exposures, is indispensable for appropriate material selection. This necessitates structural engineers go beyond generalized assumptions, integrating detailed understanding of specific exposure risks with material performance data derived under relevant conditions to make robust design choices.
Delving into the practical assessment of how stainless steels hold up against corrosion across varied structural settings quickly reveals layers of complexity beyond simple comparative charts. It turns out some phenomena are less intuitive and demand specific attention.
One often underestimated challenge is the risk of crevice corrosion. Within structural connections, under washers, or anywhere oxygen diffusion is restricted, a localized aggressive environment can develop. Even in conditions where the bulk surface remains passive and resistant, hidden zones can experience rapid attack. Evaluating this requires simulating these tight geometries, which isn't always part of standard broad-brush tests, leaving a potential vulnerability unexamined.
Furthermore, while general resistance categories are useful, specific atmospheric performance can defy simple rankings. It's interesting to note that a grade like 17-4 PH, often seen as less universally resistant than the standard 304 in immersed conditions, can sometimes perform quite acceptably or even surprisingly well in certain atmospheric exposures, depending on the unique blend of pollutants and humidity. This underscores that classifying 'corrosion resistance' needs context, tailored to the precise airborne or surface chemistry the structure will encounter.
Surface condition plays a disproportionately large role. Even with a highly corrosion-resistant alloy like 304, minor surface defects, embedded iron particles from tooling, or residual contaminants left after fabrication can act as initiation points for localized corrosion. A visually clean surface isn't necessarily passive; achieving the material's intended resistance often depends critically on meticulous post-fabrication cleaning and passivation, a step easily overlooked when focusing purely on bulk material properties.
Assessing galvanic corrosion risk in a structure made of multiple materials isn't as straightforward as just looking at a galvanic series table. The severity of potential attack on the less noble material depends heavily on the nature and conductivity of the electrolyte bridging the connection (is it rain, saltwater spray, condensation?) and the relative surface areas of the coupled metals. Without understanding these factors, a simple assumption based on contact could be misleadingly alarming or dangerously complacent.
Finally, stress corrosion cracking remains a particularly tricky failure mode to evaluate. It's not simply a matter of high stress in a corrosive environment. Instead, it's a complex synergy; a combination of stress, temperature, and perhaps surprisingly low concentrations of aggressive species (like trace chlorides) can interact in unpredictable ways to trigger sudden, brittle failure in alloys that would otherwise appear ductile. Pinpointing this critical threshold requires tests specifically designed to capture these combined effects, moving well beyond single-factor analyses.
Choosing Structural Stainless 174 PH Or 304 A Review - The Cost and Supply Landscape for High-Strength vs.
General Grades
Understanding the financial aspects of structural stainless steel selection involves navigating a varied market, where high-performance alloys sit distinctly from more common varieties. Grades engineered for high strength, such as those requiring precipitation hardening like 17-4 PH, typically incur greater costs. This is driven by the complexity of their alloying elements, the specialized manufacturing processes required to achieve their properties, and potentially less standardized production scales compared to widely used alternatives. On the other hand, ubiquitous grades like 304 benefit from high production volumes, established supply chains, and simpler compositions, which generally translates to lower material expense and easier availability. However, simply picking the cheapest option overlooks critical engineering requirements. A purely cost-driven decision fails to account for the necessary mechanical performance under specific loads, the resistance needed for particular environmental conditions, or the overall expected service life of the structure. Therefore, navigating the cost and supply landscape demands a careful balance, ensuring that initial material expenditure aligns realistically with the long-term functional demands and lifecycle value.
Here are some observations on the cost and supply differences often noted between high-strength stainless grades like 17-4 PH and more general structural types such as 304, looking at the situation around early July 2025.
1. One curious factor is how the fluctuating market prices of specific alloying elements seem to exert a greater proportional influence on the relative cost. For instance, the price swings in copper, critical for 17-4 PH's hardening mechanism, can shift its position against 304, whose cost is heavily tied to nickel prices. This means the cost advantage of one over the other isn't static but can be surprisingly dynamic based on global commodity markets.
2. Beyond the elemental recipe itself, a substantial chunk of the cost disparity seems rooted in the specific, technically demanding, and energy-intensive processing required for 17-4 PH. Achieving that high strength relies on precise precipitation hardening heat treatments. This thermal cycling requires specialized furnace capacity and control that isn't typically part of the standard production stream for structural 304, making that extra manufacturing step a significant cost contributor.
3. Looking at the supply side as of mid-2025, the sheer scale and widely distributed global production base for 304 stainless steel often appears to provide its primary material sourcing with a degree of stability. It's a ubiquitous alloy. In contrast, 17-4 PH production tends to involve more specialized, perhaps lower-volume facilities and supply chains, potentially making its raw material availability and associated costs more sensitive to localized disruptions or changes in demand peaks.
4. Interestingly, supply constraints for grades like 17-4 PH don't always boil down simply to the availability of the basic metals. Sometimes, the real bottleneck seems to be access to critical specialized processing capacity further along the line – think vacuum induction melting or those dedicated heat treatment facilities. This suggests that securing a supply of high-strength grades might hinge more on the capacity and scheduling of specific processors than the global availability of raw materials like ferrochrome or ferronickel which heavily influence 304.
5. Finally, considering the supply robustness involves acknowledging the reliance on less common elements that are key to certain grades. The sourcing reliability and market volatility of elements like Niobium, crucial for 17-4 PH's characteristics, introduce a different layer of supply risk compared to the more globally commonplace elements making up the bulk of 304. This adds a geopolitical or specialized mining dimension to the cost and availability equation for high-strength alloys.
Choosing Structural Stainless 174 PH Or 304 A Review - Matching Material Characteristics to Specific Structural Requirements
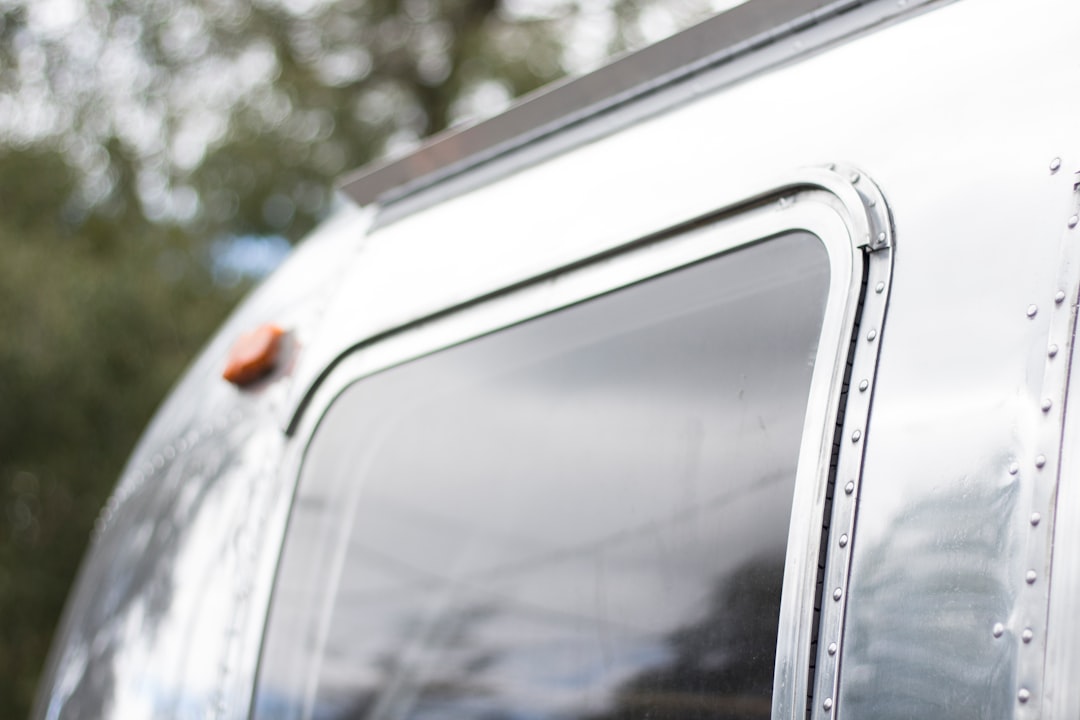
Selecting a material for a structural application fundamentally requires aligning its inherent capabilities with the specific performance demands the structure will face throughout its service life. For instance, when considering stainless steels like 17-4 PH and 304, engineers must look beyond simple designations to understand how each grade's specific characteristics – such as achievable strength levels or typical resistance to certain corrosive agents – align with the project's criteria. While 17-4 PH is often the default for requirements demanding high mechanical strength, and 304 is widely used for its balance of properties and cost-effectiveness in less demanding scenarios, a critical assessment necessitates evaluating the full spectrum of conditions, including anticipated stress profiles, potential temperature variations, and environmental exposures. Failing to conduct this thorough analysis, focusing only on one or two headline characteristics, risks misapplication and potential structural issues, underscoring that material choice must be a deliberate match to the holistic operational requirement, not just a single factor.
Moving past simply listing individual attributes, genuinely matching material capabilities to specific structural demands requires grappling with a more nuanced reality. It's less about picking a material with a high number for a single property and more about understanding how a complex set of characteristics interact synergistically under expected service conditions. For instance, it's often the intricate interplay between the material's inherent stress state, its microstructure (things like grain size, phase distribution, and inclusion content), and localized stress concentrations that dictates where and how a crack might initiate and propagate, rather than just its bulk tensile strength.
For structural applications where achieving zero defects is practically impossible or the consequences of failure are severe, the traditional focus on yield strength as the primary selection driver seems increasingly insufficient. A more pragmatic perspective frequently elevates fracture toughness – a material's inherent resistance to unstable crack extension when a flaw is present – to a more critical requirement than just how much stress it can withstand before yielding. A structure designed to tolerate pre-existing imperfections without catastrophic brittle failure often offers a higher degree of real-world safety than one simply optimized for maximum yield strength.
Furthermore, it's a curious finding that prolonged exposure to certain service environments can, over time, subtly alter a stainless steel's fundamental mechanical properties in ways not immediately apparent from initial testing. Consider the potential for absorbed hydrogen, perhaps introduced during processing or from electrochemical reactions in service, to diffuse into the material lattice, leading to a reduction in toughness or an increased susceptibility to cracking, even in environments not conventionally considered hydrogen-charging. This long-term environmental effect on mechanical performance adds another layer of complexity to material selection.
In some advanced structural design philosophies, matching requirements delve even deeper, extending beyond standard mechanical property ranges to specify desired microstructural features or grain size distributions. There's growing recognition that controlling these finer details of the material's internal architecture can have a profound and beneficial influence on its overall mechanical reliability, particularly in resistance to fatigue, fracture, or stress corrosion cracking. This pushes the boundaries of material specification well past simple compositional limits.
Finally, even within the ostensibly tight confines of an official material specification for a standard grade like 304, the permitted ranges for alloying elements, though seemingly small, can lead to non-trivial variations in properties critical for precise matching. For example, the allowed variation in chromium content within the 304 specification can influence its localized corrosion resistance, such as pitting, presenting a challenge when attempting to guarantee a consistent level of performance across batches from different suppliers without additional verification.
More Posts from aistructuralreview.com: