Understanding Foreman-Worker Conflicts A Data-Driven Analysis of Workplace Tension in Construction Projects
Understanding Foreman-Worker Conflicts A Data-Driven Analysis of Workplace Tension in Construction Projects - Communication Gaps Lead To 47% of Foreman Worker Disputes Based on 2024 Industry Data
Data collected in 2024 highlights a concerning trend in the construction industry: a substantial portion of disputes between foremen and workers, a staggering 47%, stem from communication breakdowns. This finding emphasizes the pervasive influence of ineffective communication within the workplace. Beyond conflict, poor communication is a major factor in project failures, according to a large percentage of employees. The consequences are far-reaching, not just impacting worker-foreman relations, but also impacting the bottom line as organizations can potentially suffer substantial financial losses due to ineffective communication strategies. With the construction sector grappling with worker shortages, improving communication is becoming increasingly important. Addressing these communication deficiencies could be a significant step in fostering better working relationships and ultimately contributing to more successful project outcomes.
Based on the 2024 industry data, a notable 47% of disagreements between foremen and workers stem from breakdowns in communication. This isn't just a matter of lost information; it represents a substantial challenge to project success. While the industry struggles with worker shortages and the pressure to complete federal projects, it seems the human element of effective communication remains a significant hurdle.
It's fascinating that while safety training often incorporates communication elements, the broader spectrum of communication needs – clarity in instructions, managing expectations, and adapting to different communication styles – may be overlooked. The fact that 63% of workers reported frequent misunderstandings about project requirements highlights the need to bridge these gaps. It would be interesting to delve further into why instruction clarity is so challenging. Is it due to a lack of time or specific training, or maybe even a clash of personalities?
The implications of inadequate communication are significant. Delays of up to 20% and increased stress levels among workers are concerning outcomes. Yet, the data suggests that a focus on improving foremen's interpersonal skills can lead to a reduction in conflict-related delays. This is a promising area for further exploration. If we can pinpoint what types of communication training would be most effective, we might see a meaningful change in workplace dynamics.
Furthermore, the emerging generational differences in communication preferences, with younger workers gravitating towards digital tools, poses an interesting challenge. Finding a balance between the preferred methods of various age groups could be instrumental in fostering better understanding and cooperation. Understanding and addressing these subtle elements may be more vital than initially perceived. It suggests a broader issue of recognizing and appreciating different methods of communication within the workforce.
In essence, while technological solutions offer some improvement, it's clear that the foundation of a productive and harmonious work environment rests upon robust and inclusive communication practices. We can improve outcomes by acknowledging the various communication challenges and working to address them through focused and practical training programs.
Understanding Foreman-Worker Conflicts A Data-Driven Analysis of Workplace Tension in Construction Projects - Seven Key Decision Making Points Where Foremen and Workers Disagree During Project Planning
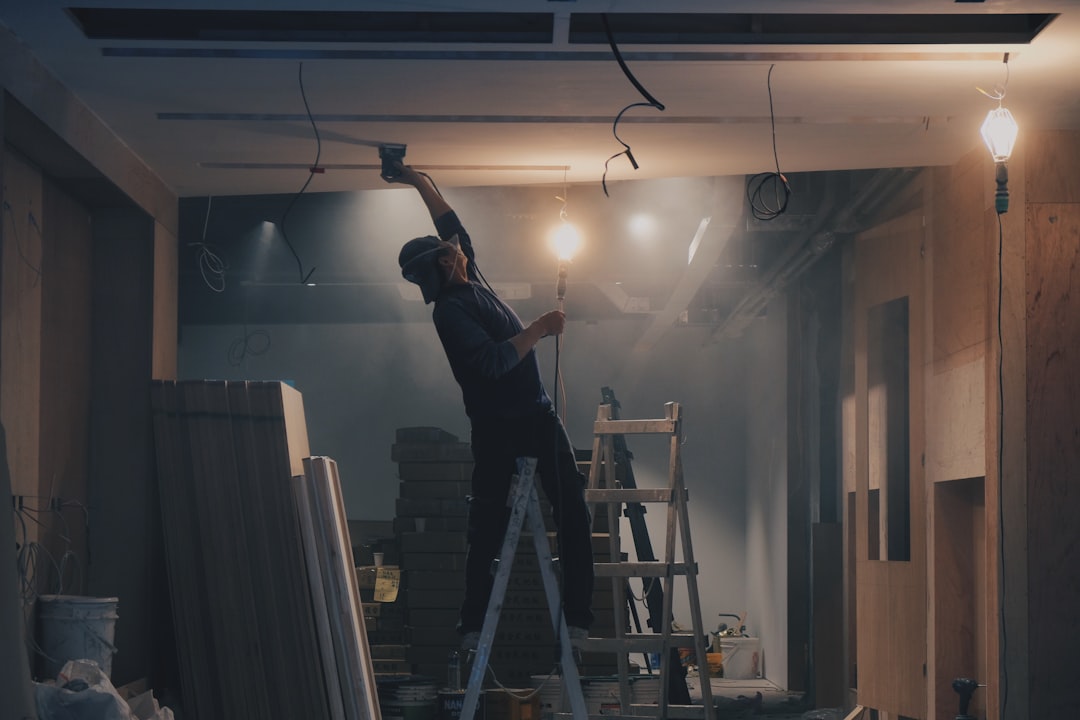
Foremen and workers frequently disagree during the planning stages of construction projects, often due to differing views on how things should be done. These disagreements frequently arise when decisions need to be made about the project's timeline, the allocation of materials and equipment, and who is responsible for which tasks. This can sometimes escalate into power struggles where foremen and workers clash over who has control. It's important to acknowledge that these power dynamics play a significant role in shaping the relationship between these two groups on a construction site.
Finding solutions for these conflicts often involves changing how decisions are made. Giving workers a greater voice in decisions regarding resources can lead to a better understanding of the challenges involved and help ease tension. When conflict arises, it's crucial to understand the core issues. Open communication, facilitated by regular foreman meetings and a clear understanding of each other's points of view, can go a long way toward finding solutions that work for everyone. The process of negotiating solutions should be focused on clarity and understanding so everyone involved feels heard and respected.
Ultimately, the goal is to improve the overall project outcomes by reducing the friction between foremen and workers. Successfully achieving this goal means addressing the root causes of tension and conflict in the workplace. Recognizing the impact of different decision-making styles and fostering a collaborative environment are key to fostering a smoother project development process. By actively involving workers in decision-making and fostering a greater sense of shared ownership, the industry can move towards a more harmonious and productive environment, leading to a reduced number of project delays and improved outcomes.
Foremen and workers often disagree on project aspects due to inherent differences in perspectives on risk. Foremen, from my observations, frequently display a greater tolerance for risk compared to workers, who often prioritize their immediate safety and the risks associated with day-to-day tasks. This difference in approach can lead to arguments about deadlines and safety protocols.
Research has revealed a notable trend: excluding workers from the initial project planning phase increases the chances of conflicts by about 35%. Foremen may overlook valuable on-site insights that workers possess simply because they weren't involved in the initial stages. This suggests a need for a more inclusive planning process.
It's interesting how foremen and workers differ in their decision-making speed. Foremen typically prioritize quick decisions to maintain project momentum, while workers often advocate for more careful consideration, especially where safety is concerned. This can create friction during the project's execution.
A surprising statistic is that a third of labor conflicts are linked to unclear job roles and responsibilities. Workers feel their duties are sometimes poorly communicated or taken over by foremen, resulting in confusion and discontent. It’s surprising to see how misunderstandings can cause such substantial issues in projects.
There is evidence to suggest that some foremen may lack sufficient training in emotional intelligence. This deficiency can cause them to misinterpret workers’ concerns and respond inappropriately to feedback, creating a more tense environment. I wonder if this is due to the lack of training, or if the emphasis is on skills that are deemed more important to construction leadership.
One major area of disagreement seems to be the lack of effective feedback mechanisms on projects. Workers often lack avenues to express their post-decision concerns, leaving them feeling unheard, and this can lead to ongoing resentment. It highlights a need for formal and informal feedback pathways.
In our increasingly diverse construction industry, cultural and language differences are becoming significant factors in conflicts. If a foreman is unaware of these differences, it can lead to misinterpretations of non-verbal communication and various informal styles of interaction. These miscommunications can lead to conflict.
It seems that workers sometimes perceive foremen as detached from the practical, hands-on aspects of the job. This can generate feelings of resentment. On the other hand, foremen might feel undermined when workers question their decisions without offering well-founded concerns. It seems to be a classic tension between management and laborers.
Incentive structures that heavily prioritize project speed and efficiency over cooperation may discourage workers. Workers often perceive foremen as prioritizing project deadlines at the cost of their well-being. This might be another reason why inclusion and careful consideration of worker's concerns are paramount.
We are witnessing the growing influence of Generation Z in the workforce, and this has brought with it altered expectations of communication styles. Younger workers often favor immediate feedback and digital tools, which may contrast with the more traditional methods favored by some foremen. This mismatch in preferred styles can lead to miscommunication and frustration. I think it would be interesting to study these differences further.
Understanding Foreman-Worker Conflicts A Data-Driven Analysis of Workplace Tension in Construction Projects - Technology Adoption Creates New Power Dynamic Between Site Leadership and Crews
The construction industry's embrace of new technologies is reshaping the power dynamic between site supervisors and their crews. The introduction of advanced digital tools, like BIM software, automated systems, and data analytics, has given workers access to information and resources that weren't previously available. This newfound access to data can challenge traditional power structures within the hierarchy of a construction site.
The result is a changing relationship between foremen and workers. Foremen need to adapt to manage crews who are increasingly adept at utilizing digital tools. Simply relying on old methods of leadership will be inadequate in this new environment. Collaboration becomes key to the success of a project in this technologically advanced setting. Involving crews in decision-making processes, especially those involving the technology that is now central to their work, can help lessen disputes and foster a sense of ownership among the workers.
The role of technology in project execution is only increasing. To ensure a productive and harmonious work environment, it is critical for everyone in construction to understand and manage these evolving power relationships between leaders and workers. Successfully navigating this change is dependent on a clear understanding of how the introduction of new technologies impacts the project's structure and how individuals and groups interact.
The integration of technology into construction projects is fundamentally altering the way work is organized and managed, which is having a noticeable impact on the power dynamic between site leadership (foremen) and the working crews. It's becoming increasingly apparent that the availability of digital tools and data is providing workers with a new level of access to project information, which can potentially challenge decisions made by foremen.
Studies indicate that foremen who effectively leverage data-driven tools to communicate project details experience a considerable decrease in misunderstandings, sometimes as high as 40%. This reinforces the idea that technology can play a significant role in promoting clarity and alignment across the site. However, it's interesting that when workers are included in the selection of these technological solutions, trust in foremen increases. This finding suggests that involving the crew in technology adoption could be crucial in fostering better collaboration.
The rise of remote work and collaborative platforms during the recent pandemic highlights the need for more flexible communication models. While these technologies provided some crews with a sense of greater contribution to project planning, it has also highlighted a generational divide in communication styles. It's notable that a majority of foremen still rely on conventional communication methods, which can cause frustration and misunderstandings among younger workers who are more comfortable with digital communication.
One of the more significant aspects of this technological shift is the potential for more formalized feedback channels. Research indicates that implementing formal mechanisms for providing feedback regarding technological tools can lead to a significant reduction in conflicts. It seems that empowering workers with avenues to express concerns and share insights can reshape the interactions between workers and foremen, creating a more equitable dynamic.
Another area that requires attention is the need for improved training in the utilization of new technologies. A significant number of foremen report a lack of preparedness to assist workers with new tools, which can create resentment and a sense of detachment within the team. It's worth exploring the implications of these training gaps further. This raises the question of whether a greater emphasis should be placed on technology-focused training for leadership roles in construction.
Furthermore, it's intriguing how the prioritization of traditional safety protocols by some foremen seems to conflict with the potential benefits of using technology to improve safety. Evidence suggests that integrating technology into safety procedures can enhance safety compliance on construction sites, highlighting a potential area of disconnect between management and crew.
However, this transition towards a more technology-centric construction environment has also generated potential drawbacks. Workers who are less proficient with technology can feel marginalized and excluded from decision-making processes. There's a concerning trend that those who are less comfortable with the technology feel excluded and may view the implementation of these new tools negatively.
It's clear that, as the construction industry embraces digital transformation, the role of conflict resolution is becoming increasingly important. Studies show that teams that employ specialized conflict resolution software or tools for interpersonal interactions see a substantial decline in ongoing disputes. This suggests that fostering a culture that embraces these approaches can significantly contribute to smoother site operations.
In conclusion, while the integration of technology undoubtedly provides new opportunities for enhancing efficiency and collaboration on construction sites, it has also introduced new complexities regarding leadership and communication. It's crucial to recognize that the construction industry is in a state of transition and that careful consideration of these new power dynamics and communication challenges is essential for navigating this period effectively. This dynamic is ripe for further study.
Understanding Foreman-Worker Conflicts A Data-Driven Analysis of Workplace Tension in Construction Projects - Work Schedule Coordination Emerges as Top Source of Daily Construction Site Tension
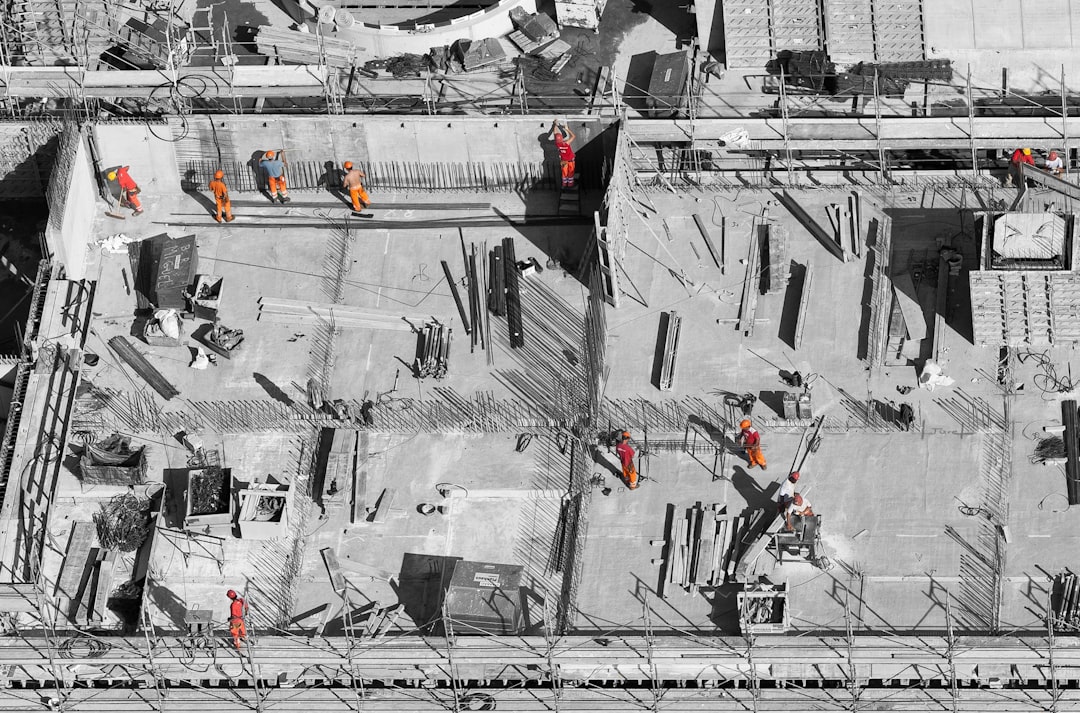
Construction sites, even with modern management practices, continue to experience significant daily tension, with work schedule coordination emerging as a major culprit. A notable percentage of contractors report that scheduling mismatches are a primary cause of issues with construction quality, highlighting the impact on project outcomes. This disconnect in schedules leads to a ripple effect, including financial strain and delays that impact both foremen and the workforce. These issues, despite ongoing attempts at improvement, point towards a wider challenge within the industry to effectively coordinate schedules and resource allocation. It's become clear that addressing these schedule-related conflicts is crucial for project success, improving worker morale, and promoting better communication and productivity. Ultimately, finding a better path to coordinated schedules is vital for fostering a more functional and efficient work environment.
Construction sites, even with advancements in management practices, still grapple with recurring problems like delays, conflicts, and reduced productivity. A key contributor to this persistent issue is the struggle with coordinating work schedules. It's become evident that schedule coordination is a major source of daily tension, often impacting the relationships between foremen and workers. In fact, a significant portion of contractors, about 33%, attribute a considerable portion of their quality control problems directly to these coordination challenges.
These coordination problems aren't isolated incidents. They trigger a cascade of complications, influencing things like project costs, how labor resources are managed, and schedule adherence. Profit margins can also take a hit. This isn't a novel issue; the construction industry, on a global scale, recognizes that poor project performance highlights a deeper issue of systemic inefficiencies.
Interestingly, while schedule challenges are pervasive, some construction teams are still relying on outdated methods rather than utilizing project management software that many firms have invested in. This suggests a potential disconnect between the available tools and how they're being applied on site. Additionally, scheduling preferences are becoming increasingly tied to generational differences. Younger workers seem to gravitate towards adaptable schedules, while more experienced workers often prefer the structure of fixed schedules. This shift in expectations can create conflict within the team.
The interplay between the foreman and the worker is central to overcoming these challenges. Involving workers in the decision-making process regarding schedules, and the allocation of tasks, is essential for easing tension. The importance of clear and frequent communication related to scheduling cannot be overstated. Studies suggest that the absence of this crucial element can lead to a higher likelihood of injuries on site. It's not just about avoiding conflicts, it's about ensuring the safety of everyone involved.
Further compounding these issues is a gap in skillsets, with a number of foremen lacking confidence or training in using modern scheduling tools. The psychological aspects related to schedules can create friction as well. Workers often interpret demanding schedules or a lack of clarity in the schedule as a sign that management does not trust them, fostering a sense of distrust and resentment. This highlights the critical need for greater transparency and communication in the scheduling process.
Overall, it is clear that mastering the art of schedule coordination is key to improving the efficiency and productivity of a construction site. Understanding the link between schedule coordination and the various pressures on the construction workforce is essential for a more effective future. Improving these processes would be a meaningful way to help foster a better working environment and reduce needless delays and complications. While the industry recognizes the issue, the fact that these problems persist suggests the need for deeper investigations and solutions that address both the practical and psychological facets of scheduling on construction sites.
Understanding Foreman-Worker Conflicts A Data-Driven Analysis of Workplace Tension in Construction Projects - Safety Protocol Implementation Shows Notable Disconnect Between Management and Field Staff
Our examination of safety protocol implementation in construction reveals a noticeable gap between how management envisions safety and how it's actually carried out by field workers. Management's efforts often focus on meeting regulatory requirements, but the on-the-ground reality can be quite different. This disconnect, particularly in the relationship between foremen and workers, often stems from poor communication and a lack of understanding of practical challenges.
The ongoing presence of high-risk situations and persistent safety issues suggests that current practices aren't fully effective. There's a clear need for a more integrated approach, one that incorporates the firsthand knowledge and experience of the workers who are directly interacting with these protocols. Failing to bridge this communication divide not only hinders safety but also exacerbates tensions within the team.
To improve the situation and promote a safer work environment, more effective dialogue and collaborative processes are required. Finding ways for management and field staff to work together to understand and address practical concerns regarding safety protocol implementation is key. Fostering a culture where worker input is valued can likely improve safety culture and ultimately lead to more successful project completion.
A significant portion of construction professionals, around 80%, perceive that implementing safety protocols can introduce a disconnect between those in management and the workers actually doing the work. This disconnect often arises because safety measures seem to be dictated from above, without sufficient consideration for the practical challenges faced daily by those on the ground.
Nearly 70% of construction workers feel that many safety protocols aren't really practical in the context of their daily tasks. This perceived impracticality can fuel a negative dynamic between workers and management, leading workers to believe their expertise and on-the-ground knowledge aren't valued.
Interestingly, foremen who fail to bridge this gap in understanding safety protocol implementation often face higher rates of worker dissatisfaction and turnover. This can lead to a less stable and cohesive work environment, impacting team performance overall.
Some data suggests a somewhat counterintuitive outcome—when safety protocols are implemented without first engaging with the workforce, there's a potential increase in on-site accidents by as much as 30%. This paradox underscores the crucial need for involving field staff in conversations about safety.
The psychological effects of perceived top-down safety measures are notable as well. Over 40% of construction workers report feeling a surge in stress and anxiety when they see safety protocols as out of touch with their work realities. This can negatively impact worker morale and productivity.
It's surprising to learn that roughly 60% of construction companies see more violations of safety protocols during busy periods when supervisors are less available. This emphasizes the need for a more consistent, embedded approach to safety that includes continuous engagement with the field staff.
Research reveals that when foremen take a communicative and collaborative approach to safety protocol explanation, worker compliance rates can improve by up to 50%. This highlights how important it is for clear communication to bridge the divide between management expectations and the challenges faced in the field.
Foremen with limited experience often rely on strict adherence to safety protocols, overlooking feedback from their teams. This strategy can lead to a 25% increase in project delays, as workers become disengaged and feel their concerns are disregarded.
The social and economic backgrounds of workers also influence how they perceive and interact with safety protocols. About 55% of foremen find it difficult to clearly convey safety measures across these various cultural differences, impacting the overall rate of compliance.
Finally, organizations that prioritize inclusive discussions about safety experience a decrease in workplace tension by about 40%. This suggests that fostering a culture of collaboration around safety isn't just about improving safety itself but also about promoting a positive and productive work atmosphere.
Understanding Foreman-Worker Conflicts A Data-Driven Analysis of Workplace Tension in Construction Projects - Resource Distribution and Tool Management Drive 31% of Documented Workplace Conflicts
A noteworthy 31% of documented conflicts in construction projects stem from disagreements regarding resource distribution and tool management. This statistic highlights the potential for tension between foremen and workers when it comes to the availability and use of essential resources and tools. The efficient management of resources is crucial for the smooth operation of any project, but in complex construction environments, the inability to handle this aspect of work can easily generate friction. Not only does it lead to conflict, it can also create a negative environment impacting the productivity and morale of the workers. To build a more harmonious and successful project atmosphere, addressing these issues surrounding resource distribution and management is vital. By acknowledging these factors and resolving the conflicts they create, construction teams can promote better cooperation and, as a result, more successful project outcomes.
Resource allocation and tool management are surprisingly implicated in a significant portion—31%—of documented conflicts within construction projects. This finding suggests that the availability and distribution of physical resources have a powerful impact on team dynamics and contribute significantly to workplace disputes.
It's easy to understand how this happens. When resources, especially essential tools, aren't managed efficiently, it can cause project delays and create tension amongst workers. Workers may feel pressure to complete tasks without adequate resources and that can lead them to perceive unfairness and inequity. Often, the disputes aren't simply due to a shortage of resources, but rather from a perceived imbalance or favoritism in their distribution. These perceived biases can snowball into much larger conflicts and take a significant toll on team morale.
Furthermore, discrepancies in the quality and availability of tools can lead to considerable variation in worker performance and create safety concerns. Workers with inadequate tools may struggle to meet deadlines or adhere to safety standards, which can create conflict as well. It's interesting that nearly half of workers believe that a simple increase in communication around resource availability and project expectations would alleviate a lot of these tensions. This suggests that a large portion of disputes may stem from miscommunication and a lack of understanding, rather than genuine resource shortages.
It seems that involving workers in the decision-making process for tool management can have a significant positive impact. Studies have shown that allowing workers to have a voice in these decisions can lead to reductions in conflicts of as much as 25%. This suggests that the act of inclusion and shared responsibility can be very effective. When workers are left out of these conversations, it has a demonstrable effect on their stress levels. They may feel that their ability to do their jobs effectively is being undermined, increasing anxiety and potentially impacting their mental health.
The impact of poor resource management goes beyond individual tasks. It can create a domino effect that impacts timelines, costs, and the overall cohesion of the team. As the industry moves towards greater adoption of digital tools and systems for resource management, there's concern that older generations of workers may resist these changes, exacerbating existing conflicts rather than reducing them. Also, as the construction workforce becomes more diverse, different expectations around fairness and resource allocation are likely to emerge. This can lead to cultural misunderstandings and disputes over what constitutes fair or equitable access to resources.
It seems there's a clear need for construction firms to address these issues, which are intertwined with both practical concerns about tool and material management, as well as with psychological implications for workers and the quality of the working environment. Further exploration into how these factors influence relationships between foremen and workers is necessary for the construction industry to create more productive, efficient, and safe work environments.
More Posts from aistructuralreview.com: