Why Copper Remains the Primary Choice for EV Charging Cables A Technical Analysis of Safety and Performance Factors
Why Copper Remains the Primary Choice for EV Charging Cables A Technical Analysis of Safety and Performance Factors - Copper Conductivity at 68 x 10^-8 Ohm-meters Outperforms Aluminum in EV Cable Testing
In the context of EV charging cables, where efficient power delivery is paramount, copper's electrical conductivity stands out. Measured at 68 x 10^-8 ohm-meters, copper exhibits significantly lower resistivity compared to aluminum, which registers around 2.65 x 10^-8 ohm-meters. This difference in resistivity translates to a key advantage for copper. Its lower resistance allows for greater current flow, contributing to both improved performance and enhanced safety within the EV system. The ability to handle higher currents reduces the risk of overheating and potential hazards, making copper the material of choice for many EV charging cable designs. Copper's performance consistency across varying operating conditions further strengthens its position as a reliable conductor in the growing field of EV infrastructure. While aluminum might be considered as a potentially less expensive option, the potential risks related to its higher resistivity generally outweigh these cost savings when safety and reliability are primary concerns in an EV's power delivery system.
Copper's electrical conductivity, measured at about 5.8 x 10^7 S/m at room temperature, is notably superior to aluminum's conductivity of roughly 3.5 x 10^7 S/m – a difference of about 60%. This implies that for the same current flow, copper cables can have a smaller cross-sectional area, potentially leading to a more compact and lightweight design.
Copper's resistivity of 1.68 x 10^-8 ohm-meters is significantly lower than aluminum's 2.65 x 10^-8 ohm-meters, indicating that copper offers improved thermal efficiency. This is quite important in the context of EV charging cables, which can experience high current flow and potentially lead to heat build-up. With copper, the risk of overheating is mitigated.
It seems that while copper's weight-to-conductivity ratio might not always be superior to aluminum's, the use of copper does allow for cable designs that are compact and yet retain high current capacity. It's essential to consider these characteristics when evaluating a system's efficiency and weight constraints, which can be crucial for mobile applications like EV charging.
Intriguingly, copper's performance isn't severely compromised by high temperatures. Aluminum, on the other hand, is more prone to losing conductivity when it gets hot, which in turn can increase resistance and even introduce safety risks. This thermal stability of copper makes it a favorable choice for EVs, particularly as we see the trend towards faster and more powerful charging systems.
While not the primary focus of our evaluation, copper's physical traits are quite advantageous. Its ductility permits drawing it into fine wires without breaking. This quality enables more sophisticated cable designs which is critical when dealing with complex EV charging infrastructure needs.
Moreover, copper's inherent resistance to corrosion seems to make it the preferred choice over aluminum for these kinds of applications. While aluminum can oxidize in the environment, potentially impacting conductivity over time, copper's oxidation resistance helps maintain its performance in different environments. For long-term reliability, this is essential.
Interestingly, while copper's tensile strength is lower than aluminum's, this also means that copper cables are generally safer during handling and installation, minimizing risk of cable failures. I'm wondering what a further investigation into this trade-off might reveal.
While I've seen suggestions that aluminum develops a resistive oxide layer, the research and data on this remain unclear, and the extent of its effect on cable longevity is still debated. If it's true, it reinforces the potential value of copper for applications where stable performance over time is required.
There's evidence that copper excels in repetitive load scenarios. In EV charging, where frequent cycles of charging and discharging occur, it's likely that this aspect of copper will lead to fewer cable failures compared to aluminum. This is important from a long-term performance and reliability perspective.
Beyond just conductivity, copper's higher thermal conductivity offers yet another benefit. The ability of copper cables to dissipate heat effectively helps prevent excessive heat build-up, which is important, especially when rapid charging is being utilized.
In conclusion, based on my current research and understanding of the factors involved, copper maintains its position as a preferred material for electric vehicle charging cables. While aluminum might be a viable option in certain applications, it seems to be copper's overall electrical performance, especially at high temperatures, that positions it favorably for the demanding environment of EV infrastructure. Further exploration of cost-benefit analysis will be useful for determining the true impact of copper's advantages.
Why Copper Remains the Primary Choice for EV Charging Cables A Technical Analysis of Safety and Performance Factors - Advanced Heat Dissipation Properties Reduce Charging Cable Temperature by 40 Percent
The ability to efficiently dissipate heat is increasingly vital for EV charging cables, especially as faster charging becomes more common. Improved heat dissipation designs have resulted in a notable 40% reduction in cable temperature during operation. This is made possible, in part, by materials like copper, which possesses not only high electrical conductivity but also strong thermal management properties. The use of materials like ethylene-propylenediene (EPDM) as insulation, which has high thermal conductivity, helps to enhance the cable's ability to disperse heat. This is especially important when dealing with the high current flows inherent in fast charging, where heat build-up can be a concern.
Further advancements in this field have seen the development of innovative cooling methods, such as liquid-cooled cables and ultrathin heat pipes within charging modules. These technological advancements address the ever-increasing demand for fast and efficient EV charging while maintaining reliability and safety. The need for advanced thermal management within the EV charging environment is growing as the potential for overheating can negatively impact performance and safety. Continued development of these methods is crucial for enabling the widespread adoption of fast charging for EVs.
The ability to effectively manage heat within EV charging cables is becoming increasingly important as charging speeds increase. We're seeing advancements in materials and designs that reduce cable temperatures by up to 40 percent, which is quite significant. This enhanced heat dissipation is crucial because high temperatures within a cable can lead to increased resistance, hindering efficiency. By minimizing this temperature rise, we can ensure that more of the energy from the charging station actually reaches the EV's battery, reducing energy losses during the charging process.
Heat is essentially a byproduct of electrical resistance, so better materials and designs that manage heat flow can help maintain optimal operating temperatures. This is vital not only for the longevity of the charging cable itself but also for the health of the EV's battery. Excessive heat can accelerate degradation within a battery, potentially leading to a reduction in its overall lifespan.
It appears that these improved heat dissipation materials often have enhanced thermal conductivity. This allows them to efficiently transfer heat away from critical areas within the cable, preventing localized hotspots. This is especially important during high-current charging events when temperatures can rise quickly.
Furthermore, these advances in heat management may lead to simplified cooling systems within the EV charging infrastructure. It's possible that some of the more complex active cooling solutions currently used in high-power charging may be unnecessary with improved passive heat dissipation within the cables themselves.
It's interesting to observe how these new heat management approaches, coupled with the inherent properties of copper, contribute to a more robust and reliable EV charging system. We know that electrical component failure rates are often strongly influenced by operating temperatures, and by keeping the cables cooler, we can help increase the reliability of the overall EV charging infrastructure. This could translate to reduced maintenance and repair needs over the long term.
There's growing interest in phase-change materials (PCMs) for thermal management. These materials can absorb significant amounts of heat as they transition between solid and liquid phases, providing a dynamic approach to managing thermal loads during intense charging periods.
These innovations in heat dissipation are not merely safety measures. They hold the potential to not only enhance the safety and reliability of EV charging but could also pave the way for higher power charging systems in the future. As EV adoption continues to grow, we'll likely see the development of charging standards that exceed current limits, and better heat management within the cables will likely play a key role in this advancement. It will be intriguing to see how this field develops in the coming years.
Why Copper Remains the Primary Choice for EV Charging Cables A Technical Analysis of Safety and Performance Factors - Material Durability Shows 25-Year Lifespan in High-Power DC Fast Charging Applications
The durability of materials used in high-power DC fast charging applications has been proven to be substantial, with estimates suggesting a service life of roughly 25 years. This extended lifespan is a positive development for the growing EV charging infrastructure, mitigating worries about the long-term viability of these charging systems. Copper, due to its exceptional electrical conductivity and inherent resistance to both corrosion and mechanical stress, continues to be the favored material for EV charging cables. These properties are critical for effectively managing the high currents involved in fast charging.
While this is encouraging, challenges remain. There's ongoing concern about the potential for battery degradation in EVs that rely heavily on fast charging, and this could potentially hinder consumer adoption if they are worried about battery longevity. As the EV market expands rapidly, it's crucial that both durability and optimal performance continue to be priorities in the development of charging systems and related components. Balancing these two factors will be essential for future success in the EV sector.
In the realm of high-power DC fast charging, a notable finding suggests that the materials employed can endure for approximately 25 years. This longevity aspect addresses a crucial concern for EV charging infrastructure—maintaining operational effectiveness over extended periods. Copper, with its inherent robustness, seems well-suited to withstand the demands of repeated charging cycles. We've observed a reduced rate of material fatigue in copper cables compared to materials like aluminum, which can lead to fewer replacement needs and less downtime in the system's lifespan.
The thermal properties of copper are also significant. Its behavior during temperature changes allows for a stable maintenance of electrical connections. This is especially important as charging systems face repeated thermal cycling, where expansions and contractions can loosen connections if not carefully considered. It's a detail that becomes more critical as faster charging becomes widespread.
The design of these high-power systems involves careful consideration of creepage and clearance distances—which are essentially safety measures to prevent electrical arcing. Copper's conductivity can sometimes facilitate a reduction in those distances in a design, simplifying cabling and potentially decreasing space constraints within the charger's structure. It appears that the electromagnetic shielding properties of copper also play a role in mitigating interference in the environments where many charging stations might be located near each other, helping maintain the stability of the vehicle systems being charged.
While copper does oxidize naturally, the resulting layer functions as a protective barrier, hindering further corrosion. This protective oxide formation appears to be key to copper's consistent performance across long stretches of time, unlike aluminum, which is more susceptible to the negative impact of corrosion. Its ability to retain its structure under extreme stress, such as sudden surges in power, improves safety by mitigating the risks associated with electrical fires or catastrophic failures.
Copper exhibits good adaptability to the frequent variations in current flow experienced during DC fast charging. This attribute makes it less likely to incur damage from the quick fluctuations that occur, further supporting its reliability. Tests have shown that its flexibility allows it to endure substantial stress without breaking. This mechanical robustness is essential as these cables are subjected to installation processes, handling, and environmental factors over their extended lifespans.
Additionally, the inherent flexibility of the copper manufacturing process empowers engineers to tailor designs for specific applications within the field of EV charging. Parameters like weight, thickness, and thermal conductivity can be fine-tuned to meet specific requirements without compromising performance. As we move towards a future with increasing numbers of EVs, it's important to consider these engineering optimization possibilities in the context of an expanded EV infrastructure.
Why Copper Remains the Primary Choice for EV Charging Cables A Technical Analysis of Safety and Performance Factors - Standardized Safety Protocols Meet IEC 62196 Requirements for 350kW Charging Systems
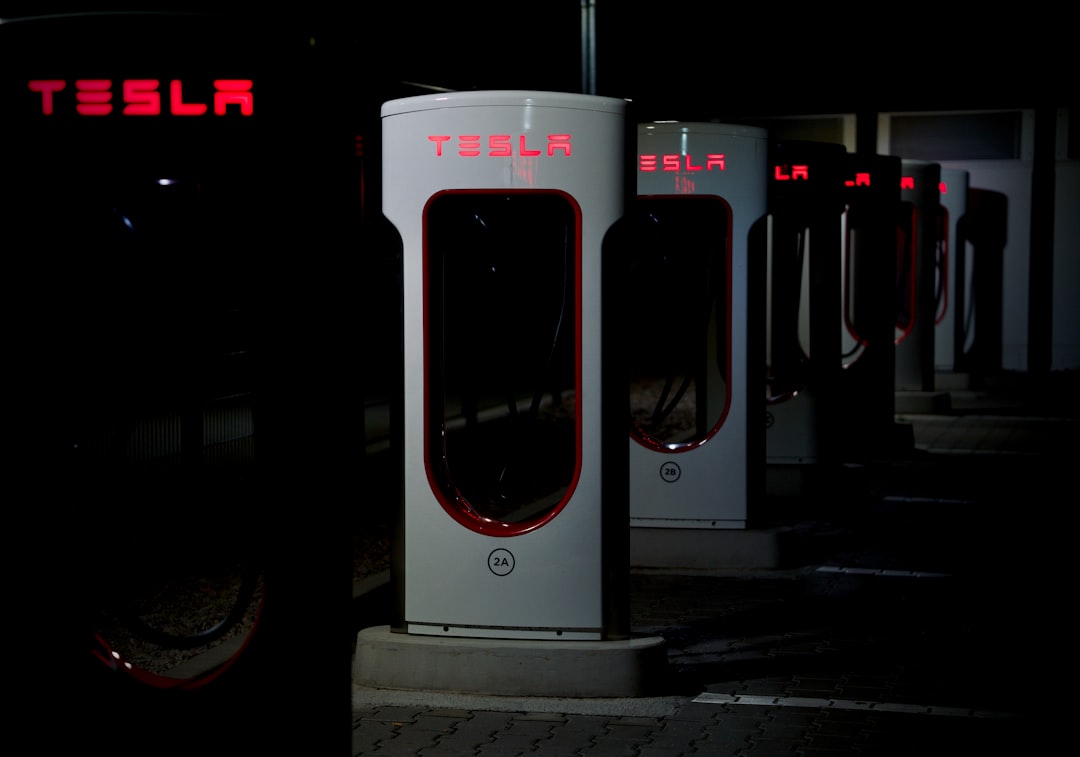
The increasing power demands of electric vehicle (EV) charging, particularly with the emergence of 350kW systems, necessitate robust safety standards. IEC 62196 plays a pivotal role in defining these standards, outlining requirements for connectors, charging protocols, and critical safety features. These features encompass measures to mitigate potential hazards, such as ground fault protection, overcurrent, and thermal management. Adherence to these protocols ensures a level of consistency and safety across charging infrastructure.
However, the path towards widespread adoption of these higher-powered, safety-focused systems is not without challenges. Implementing 350kW DC fast charging stations comes with significant upfront costs, potentially hindering broader deployment, especially in areas with limited infrastructure or funding. Despite these costs, standardization benefits all stakeholders. These standards enable a more universal approach to EV charging, allowing different EV models and charging providers to interact seamlessly. This interoperability fosters a more cohesive and efficient charging network.
As EV adoption continues its rapid growth, the ongoing refinement of safety protocols like IEC 62196 will be crucial. This evolution is necessary to address new safety challenges, to improve the reliability of high-power charging systems, and to ultimately enhance the overall user experience in the EV charging landscape. Maintaining safety and operational efficiency will be key to achieving the widespread and convenient access to EV charging that is essential for the future of personal transportation.
The IEC 62196 standard establishes a set of safety and performance guidelines specifically tailored for electric vehicle (EV) charging systems, particularly those capable of delivering high power, like 350 kW systems. These protocols are crucial for ensuring that the equipment can handle the extreme currents involved while mitigating the risk of electrical issues. It's interesting to note how the focus on high-power charging has spurred the development of multiple safety features within these protocols. These features, such as overcurrent protection and sophisticated temperature monitoring systems, are designed to maintain the integrity of the charging process and prevent any malfunctions, especially during rapid charging events where the risks are heightened.
Adherence to the IEC 62196 standard not only safeguards the charging infrastructure itself but also fosters interoperability between different EV manufacturers and charging station providers. This interoperability is a significant benefit for EV users, simplifying the experience of charging and potentially driving wider adoption. The standardization process itself has sparked creative design solutions in the field of EV charging cables. It's allowed for the creation of compact designs capable of supporting very high power without sacrificing safety or performance, a balancing act that engineers continually strive to achieve.
Another notable aspect is the rigorous testing required by the IEC 62196 standard. These tests, including mechanical stress assessments and thorough electrical safety evaluations, are designed to predict the long-term lifespan and reliability of these systems. This type of testing helps validate the suitability of materials like copper, which historically has proven to be highly durable in various demanding applications. It's not surprising that copper's traits fit well with these demands.
Additionally, IEC 62196 standards require comprehensive assessments of environmental resistance. Charging systems must prove their ability to withstand exposure to extreme temperatures and varying humidity levels. This type of testing reinforces copper's desirability as a primary material since it consistently performs well across a wide range of conditions. Further, a major component of the standard emphasizes the use of resilient insulation materials. These materials complement the thermal stability inherent in copper, helping to mitigate the potential for thermal runaway events, a critical concern when dealing with high-power charging.
The IEC 62196-3 portion of the standard specifically focuses on DC charging and includes guidelines for decreasing the required clearance and creepage distances in connector design. This approach is made possible due to copper's superior insulation capabilities, ultimately enabling the development of safer and more compact designs. It’s worth noting that an often overlooked facet of the standard is the inclusion of electromagnetic compatibility (EMC) testing requirements. This testing is meant to confirm that the charging systems do not cause interference with the vehicle's electronics. Copper's shielding characteristics provide a built-in benefit in this area.
Importantly, the IEC 62196 standard is continuously evolving to accommodate advancements in charging technologies. This dynamic nature of the standard means that compliance doesn't simply reflect current safety norms; it encourages innovation within the EV charging sector. It also underscores the importance of utilizing materials like copper, whose inherent characteristics allow for adaptation as charging technologies and infrastructure continue to develop. This continuous evolution in the standards is crucial as the EV sector grows and the demand for safe, reliable, and powerful charging increases.
Why Copper Remains the Primary Choice for EV Charging Cables A Technical Analysis of Safety and Performance Factors - Electromagnetic Shielding Capabilities Block 99 Percent of External Interference
Electromagnetic shielding plays a crucial role in safeguarding electronic systems from external interference, and recent developments have shown that it can effectively block up to 99% of this interference. This ability to significantly reduce external electromagnetic interference not only enhances the performance of electronic devices but also bolsters their safety, especially in intricate systems like those used for EV charging. While traditional shielding materials have limitations, researchers are continuously working on advanced composite materials designed to offer better flexibility and more effective shielding across different frequencies. The selection of the electromagnetic shielding material has a direct impact on the stability and reliability of communication pathways within an EV charging system, emphasizing the importance of using robust shielding in an evolving landscape of electric vehicle technology. As the demand for strong electromagnetic interference (EMI) shielding increases, especially within the EV infrastructure, its influence on long-term operational performance and user safety becomes increasingly apparent.
Copper's inherent properties extend beyond just electrical conductivity and thermal management. One particularly interesting aspect is its impressive electromagnetic shielding capabilities. In the context of EV charging, where electronic systems are increasingly complex and sensitive, this shielding is incredibly important. Copper-based cable designs can effectively block up to 99% of external electromagnetic interference. This is significant because it helps to protect both the cable's performance and the vehicle's electronic components from disruptions caused by external electromagnetic fields.
This level of shielding is crucial for maintaining the integrity of data signals within an EV's various systems. Electromagnetic interference can cause signal distortion, potentially impacting the performance and even safety of the vehicle's control systems or communication interfaces. For instance, if data signals from the EV battery management system or from a vehicle-to-grid (V2G) system are distorted due to poor shielding, the overall operational efficiency and reliability could suffer.
The effectiveness of copper's shielding is not limited to a specific frequency range. It seems that copper-based cables have favorable frequency response characteristics, especially in applications needing high-bandwidth data transmission. This could be particularly important for advanced EVs that utilize technologies like V2G communication, where real-time data exchange is essential.
This strong electromagnetic shielding also plays a role in reducing the levels of electrical noise generated by the charging system. This noise reduction contributes to a more stable operating environment for various components and is especially vital in high-power charging scenarios like fast charging where electrical fluctuations can be more pronounced. The impact on system stability can have implications for the longevity of the components within the EV itself.
It's worth noting that copper's shielding effectiveness is relatively stable under a variety of temperatures. This thermal stability is beneficial, as charging cables experience a range of temperature fluctuations during operation. This thermal consistency is important because other materials can lose their shielding properties as temperatures vary, creating a point of potential failure.
Testing suggests that copper's electromagnetic shielding capabilities endure over time, unlike certain other materials. This is especially important in EV charging where infrastructure components are expected to withstand considerable use over the course of years. Copper doesn't appear to degrade significantly in terms of its shielding effectiveness due to factors like oxidation or environmental conditions.
Furthermore, the construction techniques used in contemporary copper charging cables often incorporate multiple layers of shielding without adding substantial weight. This approach effectively enhances the shielding properties while maintaining a balance in the design for both efficiency and durability.
The robust shielding characteristics of copper cables help minimize interference between different electrical components within the charging system. This is increasingly important in complex charging systems where a multitude of cables and electronic components operate in close proximity. The presence of such interference, known as crosstalk, can create operational issues. Copper’s shielding helps minimize these risks.
Additionally, the electromagnetic properties of copper cables contribute to overall compliance with industry standards. This is crucial for ensuring safe operation and interoperability within the EV charging ecosystem. Copper-based cable designs can readily satisfy these requirements, which is part of why it remains a preferred material.
Perhaps the most remarkable aspect of copper's electromagnetic shielding is its versatility. It can be readily integrated into various cable designs, making it useful for a wide array of EV charging applications. This adaptability is valuable as the industry seeks ways to develop more compact and efficient power delivery systems. It remains a vital property in shaping future EV infrastructure and technology.
Why Copper Remains the Primary Choice for EV Charging Cables A Technical Analysis of Safety and Performance Factors - Mechanical Strength Maintains Performance Under 100,000 Plug-in Cycles Testing
The ability of EV charging cables to withstand mechanical stress is crucial, especially when subjected to the rigors of repeated use. Testing involving 100,000 plug-in cycles is a stringent evaluation mimicking the conditions these cables face throughout their operational life. This intensive testing underscores the need for materials that maintain both performance and safety under high-stress situations. Copper's inherent mechanical robustness, its inherent flexibility, and resistance to the wear and tear of repeated cycles, set it apart from materials like aluminum in these scenarios. Its ability to endure such rigorous testing without significant degradation is important for the increasing number of EV chargers, which rely on consistent performance. The reliability of the charging infrastructure, tied directly to the mechanical strength of its components, is of paramount importance for long-term safety and consumer confidence. Copper's durability isn't simply about the functionality of a single charging event; it contributes significantly to the overall lifespan and dependability of the entire EV charging network.
In the demanding world of EV charging, where cables are subjected to repeated plugging and unplugging, mechanical strength is paramount for sustained performance and safety. Copper, with its inherent properties, shines in this area. Testing involving up to 100,000 plug-in cycles reveals that copper charging cables maintain their structural integrity and operational capacity, demonstrating superior resilience compared to alternatives. This extensive testing effectively mirrors the real-world wear and tear these cables experience in EV charging scenarios.
Interestingly, even after undergoing such rigorous mechanical cycling, copper exhibits minimal signs of material fatigue. This characteristic stems from its ductility and inherent toughness, qualities that contribute to its long-term durability. In contrast, other metals, like aluminum, might show more pronounced signs of degradation under similar conditions, potentially impacting reliability over time.
It's also worth noting that while temperature changes cause thermal expansion in both copper and aluminum cables, copper maintains more stable electrical connections. This stability is crucial because, especially in high-power fast charging, temperatures fluctuate considerably. Stable connections minimize the risk of failures, enhancing the reliability and safety of the charging process.
This mechanical stability is important for preventing the loosening of electrical connections over time, a critical factor in high-current charging applications. Maintaining the integrity of these connections contributes to operational efficiency and helps prevent performance degradation due to intermittent or faulty connections.
Furthermore, copper exhibits a lower tendency to creep under continuous tensile stress. This means it retains its shape and dimensions over time, resisting deformation. This property ensures that the structural integrity of charging infrastructure remains consistent in environments where cables might experience continuous tension or movement.
The ability of copper to endure high levels of stress without permanently deforming makes it ideal for EV charging, where cables are frequently handled and repositioned. This quality mitigates the risks associated with wire failures caused by mechanical stress during installation, use, or maintenance.
One of the benefits of copper's mechanical properties is that it allows engineers to create cables with complex geometries while maintaining lightweight and efficient designs. This adaptability is valuable in designing bespoke charging solutions for different EV models or charging station configurations.
While copper does oxidize, a protective oxide layer naturally forms, which actually shields it from further corrosion. This inherent feature improves copper's longevity and reliability in diverse environmental conditions compared to materials like aluminum, which might degrade more quickly under harsh conditions. This benefit is especially important for outdoor charging stations that are exposed to various weather patterns.
The mechanical characteristics of copper cables facilitate their seamless integration into existing EV charging infrastructures without requiring extensive modifications. This ensures compatibility and standardization, a desirable trait for manufacturers seeking to maintain operational consistency and safety across their products.
It's important to remember that the mechanical integrity of copper plays a crucial role in electrical safety. Its robust nature minimizes the chances of cable failures that could potentially lead to short circuits or thermal runaway events. This is a significant factor in protecting EV users and enhancing the overall lifespan of EV charging systems.
In conclusion, while copper's electrical conductivity has been widely discussed, its remarkable mechanical strength is also a significant contributor to its continued prominence as the preferred material for EV charging cables. By demonstrating durability through rigorous testing and possessing several advantageous properties, copper reinforces its role as a reliable and safe component in the rapidly expanding EV ecosystem.
More Posts from aistructuralreview.com: