7 Critical Engineering Innovations that Made the Brooklyn Bridge's Steel Wire System Revolutionary in 1883
7 Critical Engineering Innovations that Made the Brooklyn Bridge's Steel Wire System Revolutionary in 1883 - Wire Rope Manufacturing Method Using In House Steel Production at Roebling Mill
The Roebling Mill's wire rope production was groundbreaking for its time, integrating steel production directly into the manufacturing process. By controlling the entire process, from raw steel to the final rope, they achieved a level of quality control not previously seen. A key element of this method was a patented wire-spinning technique, which maintained even tension across all strands. This ensured the resulting ropes possessed unprecedented strength, outperforming the hemp ropes commonly used at the time. This internal control and innovation wasn't just vital to the Brooklyn Bridge's structural integrity. It fueled the growth of the American wire rope industry, driving applications across a range of industries, including shipping, railways, and elevators. Roebling’s implementation of advanced machinery and manufacturing practices within their mill reflected a critical shift in engineering practice, ultimately laying the groundwork for future advancements in infrastructure and transportation. The innovations at the Roebling Mill were, in essence, a paradigm shift, demonstrating the transformative power of controlled steel production in the context of late 19th-century engineering.
The Roebling Mill's approach to steel production was a game-changer. By controlling the steelmaking process internally, they could fine-tune the material's properties, a crucial step in achieving the high tensile strength needed for the Brooklyn Bridge's wire ropes. This in-house operation allowed them to manage steel consistency, which was paramount for the bridge's structural integrity.
Through a process known as "drawing," they were able to create wires of varying thicknesses, optimizing them for the different stresses and loads experienced throughout the bridge. This customization wasn't standard practice back then, highlighting their innovative engineering approach.
The steel created at the mill had a unique composition, containing a lower proportion of phosphorus than imported steel of the same era. This attribute gave their steel superior ductility, making it less prone to snapping under stress. This was a clever workaround, as it improved the strength properties of the steel needed for the wire rope, avoiding the brittle failures seen with other steels of the time.
Rather than just using a single thick wire, Roebling innovated by constructing their ropes from numerous strands of steel twisted together. This method not only improved flexibility, a practical consideration for a suspension bridge, but it also cleverly distributed load across a wider area, lessening the chance of a catastrophic failure in a single point.
It is fascinating that each of these critical components was rigorously tested to ensure the safety and reliability of the bridge. Some of the ropes had to withstand more than 25 tons of force in tensile tests, underlining how crucial each wire rope was to the bridge's structure. They weren't willing to compromise on the structural integrity of the bridge.
The Roebling Mill was an early adopter of "cold working" for their wires. This process strengthened the steel without needing additional heat treatment, a popular practice at that time. It is likely this process was faster and more effective, with less potential damage to the wires.
The level of control they had over the manufacturing process was remarkable. They were able to produce wire ropes with incredibly precise elongation under load, typically only a tiny fraction of a percent. This fine-tuning was vital for the bridge's stability, especially under dynamic forces like wind or the weight of passing vehicles.
They also arranged the individual wires in their ropes in a carefully considered pattern. This layering design not only enhanced the rope's ability to withstand twisting and bending but also contributed significantly to its fatigue resistance. This innovative approach extended the lifetime of each rope.
Because the production of the wire was kept within the mill, Roebling was able to quickly implement adjustments and new innovations. This was a significant advantage over their competitors, many of whom had to rely on external suppliers for their raw materials.
Most notably, Roebling decided to use steel instead of iron in the wire ropes, recognizing the benefits of steel's superior strength-to-weight ratio. This decision meant that they could maintain the structural capacity of the bridge with a reduced overall weight, optimizing the design for efficiency and safety. They made a bold and insightful choice.
7 Critical Engineering Innovations that Made the Brooklyn Bridge's Steel Wire System Revolutionary in 1883 - Parallel Wire Construction Technique Instead of Twisted Cable Design
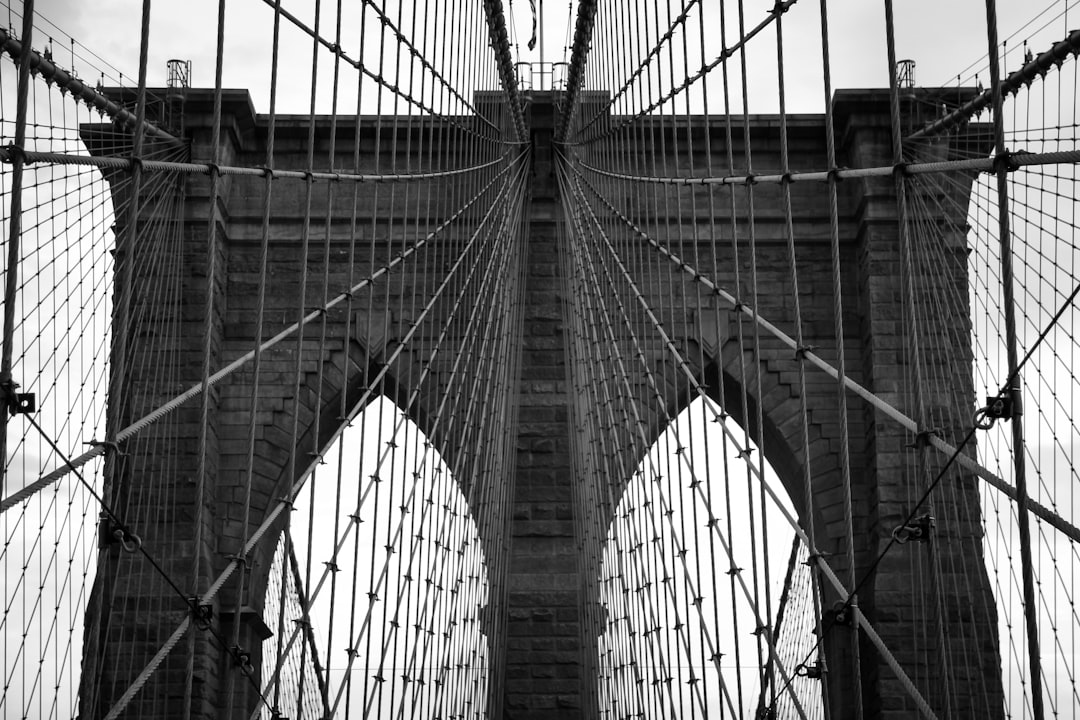
Instead of the conventional twisted cable design, the Brooklyn Bridge's steel wire system employed a parallel wire construction technique. This novel approach involved arranging multiple individual steel wires side-by-side, rather than twisting them together. This design choice yielded several benefits. Firstly, the parallel arrangement increased the overall tensile strength of the cables, enhancing the bridge's ability to withstand significant loads. Further, by reducing inductance in the cable, the parallel wire configuration improved the performance of the cable system for certain electrical applications. Moreover, using this method also lowered electromagnetic interference (EMI), improving its performance.
The prefabrication of these parallel wire strands was a key aspect of Roebling's approach, enabling them to produce the cables in a factory setting. This method offered significant advantages for quality control and efficiency in the manufacturing process.
Ultimately, this innovative parallel wire construction was not only integral to the structural integrity and durability of the Brooklyn Bridge, but it also laid the foundation for how future suspension bridges would be designed. The parallel wire system pioneered in the Brooklyn Bridge remains a testament to the groundbreaking engineering of the era, and it has influenced bridge design into the present day.
The Brooklyn Bridge's innovative use of parallel wire construction, as opposed to the more common twisted cable design, was a pivotal decision that significantly impacted the bridge's structural integrity and performance. Instead of twisting individual wires together, the bridge utilized a system of parallel wire strands, where each wire contributed to the overall strength while preserving the needed flexibility for a suspension bridge spanning the East River. This design choice allowed for the creation of longer, uninterrupted wire strands, minimizing potential weak points that could lead to failure, a significant improvement in both durability and reliability compared to using shorter segments in a twisted rope.
Furthermore, the parallel arrangement inherently reduced the fatigue experienced by the individual wires. This is because the stress was distributed more evenly among the parallel strands rather than being concentrated at the points where wires twisted in traditional designs. This even distribution also meant the bridge could handle dynamic forces like wind and traffic with greater ease. The parallel method gave the engineers more flexibility in the design process, allowing them to easily modify the number of wires in a cable to accommodate specific load requirements—a challenge with twisted cables.
The reduced cross-sectional area from using parallel wires, as opposed to a twisted configuration, made for a more streamlined cable design that minimized air resistance, a very practical consideration for a structure exposed to the windy conditions typical of the East River. Furthermore, the parallel construction allowed for the use of various cross-sectional shapes for the individual wires—such as round or flat—enhancing their ability to handle different stresses while still maintaining structural unity within the cable.
By carefully positioning wires in a parallel arrangement, engineers minimized the friction and contact between individual strands, reducing wear and tear on the surfaces of the wires. This meticulous design approach was crucial for long-term infrastructure projects, contributing to the cable's extended lifespan. Interestingly, the method also simplified the manufacturing process. Straightening and drawing wires, tasks in the production of parallel wires, are easier and simpler than the complex twisting procedures required for making standard twisted cables.
While the initial focus was on wire strength, the parallel design also proved to be advantageous for the inspection and maintenance of the rope systems. Since the wires were readily accessible within the parallel design, engineers could easily monitor the condition of individual wires without compromising the integrity of the whole cable, further highlighting the ingenuity of this engineering innovation. The parallel wire technique used in the Brooklyn Bridge was not just a technological advancement, but a practical solution that anticipated future inspection and maintenance needs for this iconic bridge.
7 Critical Engineering Innovations that Made the Brooklyn Bridge's Steel Wire System Revolutionary in 1883 - Galvanized Steel Wire Innovation Against Salt Water Corrosion
The Brooklyn Bridge's use of galvanized steel wire was a pivotal step in tackling the corrosive effects of saltwater, a constant threat to any marine structure. The bridge's reliance on 128 gauge galvanized steel effectively countered widespread corrosion, which can diminish the cross-section of the wire and, consequently, its load-bearing capacity. This innovation significantly improved the lifespan and reliability of the bridge's wire system.
However, the battle against corrosion wasn't entirely won. Galvanized steel, while offering protection, is still susceptible to issues like pitting corrosion. This localized corrosion can create stress points, potentially accelerating fatigue and compromising structural integrity over time. Furthermore, the corrosion rate of galvanized steel can fluctuate drastically based on factors like water content, pH levels, and salt concentration. These variables make it challenging to predict the long-term performance of the material in the harsh marine environment.
While galvanized steel can endure for decades, even exceeding 75 years in less severe settings, the constant exposure to seawater necessitates ongoing monitoring and potential maintenance or upgrades. The extended exposure can ultimately lead to corrosion products, affecting both the material's performance and its overall longevity. Areas subjected to constant seawater spray present unique challenges and may necessitate further protective layers, like epoxy or paint, over the zinc coating. The Brooklyn Bridge stands as a testament to the ingenuity of engineers who were attempting to resolve the challenge of salt water corrosion on steel wire in 1883, but also a reminder of the constant need for vigilance and adaptation when it comes to infrastructure exposed to such a hostile environment.
Galvanized steel wire's resistance to saltwater corrosion was a crucial innovation for the Brooklyn Bridge, particularly given its location near the East River. The zinc coating acts as a protective layer, sacrificing itself to prevent corrosion of the underlying steel. This "sacrificial anode" effect is particularly valuable when the coating is damaged, as the zinc continues to protect the steel.
The zinc coating's electrochemical properties create an electrical potential that hinders the steel's oxidation. This is key to the wire's effectiveness in marine settings. The thickness of the zinc coating can be adjusted to suit the environment's corrosiveness, with thicker coatings being more resilient in high-salinity areas like the East River.
While weathering steel, which develops a protective rust layer, is useful for certain environments, galvanized steel outperforms it in chemical settings. This makes galvanized steel a better choice for coastal structures facing constant exposure to seawater. The galvanization process itself creates a metallurgical bond between zinc and steel, yielding a stronger, more durable coating than alternatives like paint.
Further enhancing the wire's properties, heat treatment can improve tensile strength and ductility, traits beneficial for suspension bridges that experience fluctuating loads. The rough surface texture of galvanized steel allows it to bond well with materials like concrete, improving load transfer within the bridge's structure.
As galvanized steel ages, it develops a layer of zinc carbonate, which further strengthens its corrosion resistance. However, it's vital to note that excessive heat can damage the zinc coating, a consideration for high-temperature environments. Notably, galvanized steel's resilience under cyclic loading conditions underscores its suitability for dynamic structures like the Brooklyn Bridge.
It's interesting that while the choice of galvanized steel may seem obvious today, it represented a notable advancement in material science in the 1880s. It demonstrates that engineers at the time were acutely aware of the detrimental effects of saltwater corrosion and sought innovative solutions to ensure the long-term integrity of the bridge. While the expected lifespan of galvanized steel in harsh soil environments was around 35 to 50 years, engineers understood that conditions around the East River would likely be less corrosive. They were hoping that the zinc coating would allow the steel wires to last for over 75 years, which was a bold prediction at the time.
Of course, exposure to the marine environment leads to the formation of corrosion products, which can impact the wire's performance over time. Further, environmental factors like pH levels, moisture, and chloride concentrations can influence the corrosion rate. This underlines the importance of regular maintenance, particularly in seawater splash zones, where additional coatings like epoxy or paint are often applied over the zinc layer.
Looking at the historical context, we find that the procurement of galvanized steel wire for the Brooklyn Bridge was a competitive process, with various firms, including the Roebling factory in Trenton, vying for the contract. It's important to realize that galvanized steel's inclusion in the Brooklyn Bridge's design represented a significant step forward in engineering and construction during the late 19th century. The fact that Roebling's wires were 128 gauge (with a diameter of 0.165 inches), capable of withstanding 3,400 pounds of tension before breaking, underlines the level of sophistication that the company was bringing to wire production.
In conclusion, while the choice of galvanized steel might seem like a basic requirement for a saltwater bridge today, it was a significant innovation for its time. This seemingly small detail reveals a lot about how the engineers involved in the construction of the Brooklyn Bridge truly understood the challenges they faced in designing and building a safe, durable structure in a demanding location.
7 Critical Engineering Innovations that Made the Brooklyn Bridge's Steel Wire System Revolutionary in 1883 - Adjustable Steel Cable Saddle System on Gothic Towers

The Brooklyn Bridge's Gothic towers featured an adjustable steel cable saddle system, a design innovation crucial for the bridge's success. This system was engineered to distribute the immense loads carried by the main cables across the towers in a precise manner, allowing the bridge to respond to various stresses and forces. The ability to adjust the saddles was vital, ensuring the cables remained properly aligned and under appropriate tension. This, in turn, was essential for maintaining the bridge's structural integrity as a whole. This design marked a significant shift from prior practices and illustrated the advanced engineering thinking that contributed to the bridge's exceptional longevity and stability. This adjustable saddle system essentially laid the groundwork for many of the cable-stayed bridge designs that followed, establishing crucial principles that remain relevant to this day. While innovative, some may argue the system presented design and engineering complexities that had to be meticulously addressed during the construction and operational phases of the bridge, given the scale and nature of the forces present. Nonetheless, it's clear that the adjustable cable saddle was a defining characteristic of the Brooklyn Bridge.
The adjustable steel cable saddle system perched atop the Gothic towers of the Brooklyn Bridge was a remarkable innovation in load distribution. This system, a key component of the bridge's design, allowed for precise alignment and tensioning of the main cables. This was a critical feature, as any misalignment or uneven stress could lead to cable failure.
A unique locking mechanism within the saddles enabled quick adjustments to cable tension, a vital capability to accommodate shifts caused by thermal expansion and varying loads. This adaptability minimized the need for lengthy maintenance periods, ensuring the bridge's continued operation with minimal disruption. It's worth noting that the angle at which the cables connected to the Gothic towers was carefully chosen not only for its aesthetic appeal but also to distribute load efficiently across the tower structures.
Furthermore, the saddle's design incorporated a pivoting element to account for fluctuating forces like wind and traffic. This ensured consistent cable tension, regardless of external conditions. The materials used in the saddles were specifically selected for their ability to handle immense loads while resisting fatigue – a crucial property for a structure experiencing constant cyclic forces. The engineers carefully crafted the saddle's geometry to minimize stress concentration points, areas that are prone to failure in less well-designed cable systems, enhancing the bridge's overall safety margins.
This adjustable saddle system can be viewed as a precursor to the adaptable designs prevalent in modern cable-supported structures. The saddle system design underwent rigorous testing in prototypes, simulating dynamic loads to understand failure modes and optimize the design before implementation. The modular design of the saddle components allowed for interchangeability, streamlining repair and replacement processes. This forward-thinking approach to maintenance was a testament to the careful planning that went into the bridge's design.
The inclusion of the adjustable saddle system also amplified the Gothic towers' ability to withstand lateral forces caused by wind, a frequently overlooked factor in bridge design that has a profound impact on long-term structural integrity and performance. It's clear that the designers were keenly aware of the critical role wind loads would play in the bridge's lifespan. In essence, the saddle system is a shining example of how innovation, meticulously planned design, and careful execution resulted in a structure that was not only breathtaking to look at, but also capable of withstanding the rigors of its environment for decades.
7 Critical Engineering Innovations that Made the Brooklyn Bridge's Steel Wire System Revolutionary in 1883 - Steel Wire Anchor Plate Design for Equal Load Distribution
The design of steel wire anchor plates, crucial for ensuring even load distribution, played a vital role in the Brooklyn Bridge's structural integrity. These plates act as the connection point between the bridge's supporting columns and the foundations, efficiently transferring both vertical (axial) and horizontal (shear) forces. The design of these plates was critical for the bridge's stability and safety, especially under dynamic conditions like wind or moving traffic. Engineers had to consider a multitude of factors in their design, including the anticipated loads and how these forces would be distributed across the anchor plate.
The design methods developed for the Brooklyn Bridge, including the anchor plate design, highlighted the importance of careful planning and calculation in structural engineering. These innovations not only enabled effective load management in this massive project, but also established a foundation for future developments in bridge design. The emphasis on distributing loads evenly across the anchor plate showcased a sophisticated understanding of the forces at play. This focus on even load distribution across the anchor plate was a crucial part of the overall design process.
It's important to recognize that the anchor plate design, like other aspects of the Brooklyn Bridge, represents the spirit of innovation prevalent in 19th-century engineering. The meticulous attention to detail in these designs – ensuring forces were properly channeled and distributed – set a strong precedent for modern structural engineering practices. Today's engineers still adhere to many of the same principles of load distribution established during the construction of the Brooklyn Bridge, highlighting the enduring relevance of these early innovations. The approach to anchor plate design, then, was a vital step toward creating a structurally sound and enduring infrastructure project, reflecting an innovative and rigorous approach to engineering that persists in modern bridge design.
The effectiveness of the Brooklyn Bridge's steel wire anchor plate design in distributing loads evenly stemmed from a focus on precise geometry. These plates were carefully shaped to maximize their contact area with the supporting structures, leading to a more uniform transfer of forces from the massive cables. This was crucial, as it ensured the bridge's ability to effectively handle the immense tensile loads generated by the suspended deck.
These anchor plates served as vital transition points, converting the tensile forces from the main cables into compressive forces that the towers and the foundation could readily withstand. This conversion was fundamental to the overall stability of the bridge, preventing the immense cable forces from causing localized stress or potentially leading to failure.
The placement and spacing of the anchor plates weren't arbitrary; they were precisely calculated to avoid concentrated stress points. This attention to detail was paramount, as localized stress concentrations can lead to fatigue failure of materials over time. The design prevented such premature failures, ultimately contributing to the bridge's long-term structural integrity.
To further enhance the capacity of the anchor plates, high-carbon steel was typically employed in their construction. This material choice greatly increased their yield strength and improved the overall stiffness of the cable system. This was essential, considering the bridge's extensive span and the immense loads it was designed to bear.
Beyond load distribution, the design of the anchor plates cleverly considered long-term maintenance and inspection. The use of flat surfaces made it simpler for engineers to visually examine the plates for signs of wear and tear or corrosion. This accessibility was an important factor in a structure that would need to be maintained for decades.
It's also noteworthy that the engineers considered the impact of thermal expansion when designing the anchor plate system. The plates were configured to allow for minor movements due to temperature fluctuations, preventing excessive stress on both the cables and the plates themselves. This design feature demonstrates a sophisticated understanding of material behavior and its effect on the bridge's performance.
The anchor plates were just one element within a larger design philosophy. Every component, including the cables, saddles, and towers, worked harmoniously to improve the bridge's resilience against the dynamic forces of live loads, like traffic and wind. This interconnectedness is a hallmark of good engineering design and was integral to the bridge's remarkable success.
One of the benefits of this approach was that if a single cable were to experience failure, the anchor plate design ensured that the load could be efficiently redistributed to the remaining cables and supporting structures. This ability to manage load redundancy greatly improved the bridge's overall safety.
Records indicate that achieving the necessary manufacturing tolerances for these anchor plates was a significant challenge. Even slight deviations from the intended design could significantly alter load distribution. This underscores the critical role engineering precision played in the success of this complex undertaking.
The principles used in the anchor plate design have undoubtedly had a lasting impact on engineering practices. Modern suspension bridges often integrate similar concepts to improve load distribution and enhance safety margins against dynamic forces. This highlights the innovative nature of the Brooklyn Bridge's engineering and its influence on subsequent bridge designs.
7 Critical Engineering Innovations that Made the Brooklyn Bridge's Steel Wire System Revolutionary in 1883 - Steel Wire Wrapping Machine Patent for Uniform Cable Tension
The Brooklyn Bridge's innovative cable system relied heavily on a patented steel wire wrapping machine designed to ensure uniform tension across the entire cable. This machine incorporated specific mechanisms to tightly and evenly wrap the individual steel wires, a crucial step in preventing any inconsistencies that could weaken or destabilize the cables. To further enhance cable uniformity, the wires were pre-shaped before being twisted into the final cable configuration. This method helped maintain their alignment and prevented twisting, ensuring consistent tension along the cable's length. The development and implementation of this specialized machine represented a significant advancement in cable construction techniques. It not only played a pivotal role in the Brooklyn Bridge's revolutionary design but also set a precedent for future bridge projects, demonstrating a new emphasis on precise manufacturing in achieving structural integrity. This advancement highlights the changing landscape of engineering in the late 19th century, where meticulous attention to detail was becoming increasingly important for large-scale infrastructure projects. While it might seem like a minor detail, this innovation was crucial for achieving the strength and stability needed for the bridge's enduring success.
The development of a specialized steel wire wrapping machine for the Brooklyn Bridge was a crucial innovation in achieving the desired uniform tension within the bridge's cable system. This machine, protected by a patent, played a vital role in ensuring the structural integrity of the bridge, as consistent tension across the wire ropes was paramount to prevent localized weaknesses that could lead to failures.
The patented design incorporated mechanisms to carefully control the spacing and layering of the individual wires as they were wrapped onto the cable core. This degree of control not only optimized the load distribution but also contributed significantly to the resilience of the cables under various stress conditions. This novel approach served as a model for future cable-manufacturing techniques.
Interestingly, the wrapping machine possessed the capability to adjust the winding tension based on the anticipated loads at specific points along the bridge. This adaptability allowed for customized cable sections tailored to the unique stress demands at different locations within the bridge's structure.
Furthermore, the machine was equipped with tension sensors that enabled real-time monitoring of cable integrity throughout the wrapping process. This allowed engineers to immediately identify any anomalies and ensure that the final product met the rigorous quality and strength standards set for the bridge.
The flexibility of the machine was truly noteworthy. It could accommodate wires with varying diameters, facilitating the use of different wire types and providing bespoke solutions to various loading scenarios. Most machines of that era were built for a fixed output, which limited adaptability. This was quite a different design philosophy.
Beyond just manufacturing the wire rope, the wrapping technique introduced by this machine contributed to reduced material waste. By precisely calculating the necessary length for each cable segment, it promoted a more sustainable approach to manufacturing, a practice less common in the industrial era.
The multi-layered winding process inherent in this technique resulted in enhanced tensile strength and improved fatigue resistance. This proved to be essential, as the cables were subject to continuous dynamic loads due to traffic and weather.
The automated wrapping process significantly reduced the labor time compared to the traditional methods that relied heavily on manual winding and estimations. This efficiency was crucial to the timely completion of the Brooklyn Bridge, one of the largest infrastructure projects of its time.
The patent also included innovations that increased the compatibility with a variety of steel alloys, thereby allowing for the use of advanced materials in the wire production process. This ability to leverage advancements in metallurgy further improved the cables' performance characteristics, compared to those constructed from standard-grade steels.
While the wrapping machine represented a significant engineering achievement, there were technological hurdles related to the speed of operation. Striking the right balance between speed and the needed precise control over tension was a considerable challenge, as increasing the speed could compromise the critical uniform tension requirements under significant loading conditions. This is a common engineering trade-off still experienced today.
7 Critical Engineering Innovations that Made the Brooklyn Bridge's Steel Wire System Revolutionary in 1883 - Diagonal Stay Cable Configuration with Steel Wire Strands
The Brooklyn Bridge's incorporation of a diagonal stay cable configuration was a novel approach that significantly improved its structural performance. This innovative design, a brainchild of John Roebling, blended traditional suspension cables with a system of diagonally arranged stay cables. This hybrid approach created a more robust structure, crucial for handling the bridge's long spans and the dynamic forces it encountered. Each stay cable was formed by tightly twisting numerous strands of high-strength steel wire, increasing the bridge's overall resilience and load distribution capabilities. This configuration provided an element of redundancy, as the stay cables acted as a secondary support system to the main suspension cables, reducing the likelihood of catastrophic failure. Not only did this system enhance the bridge's ability to withstand environmental forces like wind and changing temperatures, but it also provided a blueprint for the development of future cable-stayed bridges. The Brooklyn Bridge's design highlighted the capabilities of modern engineering in tackling the complex challenges of large-scale infrastructure projects.
The Brooklyn Bridge's innovative use of diagonal stay cables, in addition to the main suspension cables, was a significant departure from traditional bridge designs of the time. This configuration wasn't just about supporting the weight of the bridge deck; it was a clever way to manage various forces, particularly those arising from wind and the movement of traffic. By strategically arranging steel wire strands at angles, the engineers could distribute lateral loads effectively, lessening the impact on the towers and anchorages. This approach was a brilliant way to distribute loads, because if one wire failed, the others could continue to support the bridge's weight, lessening the chance of a major failure. It's fascinating how they took into account the tensile strength of each individual wire and distributed them so the tension was distributed and not concentrated.
This diagonal design also helped the bridge respond better to dynamic forces. It allowed the structure to flex and sway a bit under load, instead of rigidly resisting movement. This flexibility helped dissipate energy from external forces like gusts of wind, enhancing overall stability and safety. It's a testament to their understanding of the dynamic forces the bridge would be exposed to, and they were mindful of material efficiency. By carefully adjusting the cable angles, they could achieve the needed structural integrity with less steel, showcasing a thoughtful and efficient approach to resource utilization.
The diagonal cable arrangement also enhanced the bridge's resistance to twisting forces, or torsion. This was crucial for a bridge of such a vast span, and it prevented any potential twisting that could lead to catastrophic failure. Beyond functionality, the diagonal arrangement has a striking visual appeal, showcasing how the bridge's design beautifully merged form and function. The carefully designed "nodes" where these diagonal cables connect to the primary structure are critical. They were engineered to handle the complex forces at play and ensure those forces are transferred effectively throughout the bridge framework. This multi-directional force management was something never done on this scale at that point in time.
Another aspect of the diagonal cable system is that it contributes to vibration damping. Each diagonal cable acted like a damper to help the bridge absorb oscillations caused by wind or traffic. This approach ensured a more comfortable and safer ride for people crossing the bridge. Interestingly, the success of the Brooklyn Bridge's diagonal stay cable system has had a profound impact on bridge design globally. Engineers around the world continue to draw inspiration from its principles. This makes it a significant milestone in structural engineering and is part of the legacy that we still see today.
Developing this diagonal stay cable system wasn't a simple feat. It required incredibly complex engineering calculations that accounted for factors like wind, traffic loads, and even thermal expansion of the materials. It was a feat of balancing rigorous theoretical analysis with the practical challenges of construction. The innovative work done with the diagonal cable configuration underscores the ingenuity and foresight that went into making the Brooklyn Bridge not just a marvel of engineering but a testament to the power of careful planning and detailed design in the face of complex challenges.
More Posts from aistructuralreview.com: