7 Key Innovations in Wind Turbine Blade Segmentation A 2024 Engineering Analysis
7 Key Innovations in Wind Turbine Blade Segmentation A 2024 Engineering Analysis - Split Blade Technology Reduces Transport Costs by 32 Percent in Vestas V236 Project
The Vestas V236 project has showcased the potential of split blade technology, leading to a notable 32% decrease in transportation expenses. This innovation is integral to the deployment of the V236-15 MW turbine, the first 15 MW model to enter the market. While the benefits of this approach are apparent, the extensive testing and certification phases needed for such advanced turbines raise valid questions about their immediate commercial availability and full operational reliability. The V236 project also underscores Vestas' focus on sustainability through its exploration of circularity for blade materials, highlighting the evolving emphasis on environmentally responsible wind energy projects. This drive towards a more circular economy for wind power, while promising, will require significant further developments and time for widespread adoption.
The Vestas V236 project, featuring the industry's first 15 MW turbine, has successfully utilized a novel approach: splitting the turbine blades into segments. This "split blade" technique fundamentally alters how these massive components are transported. Instead of needing specialized, oversized vehicles and infrastructure, the segmented design allows for more conventional transport methods. The V236 project, with its 115.5-meter long prototype blades, has seen a 32% reduction in transport costs. This decrease is largely due to the smaller, more manageable sizes of the individual blade segments, which can be moved using standard shipping containers.
This modular approach to blade production provides intriguing advantages beyond cost savings. Shipping segments instead of a single massive blade opens up the possibility of utilizing more conventional transport routes and infrastructure, making it feasible to transport blades to sites previously inaccessible. Furthermore, the segmented design permits parallel manufacturing across different locations, offering opportunities to leverage local workforce and resources, and potentially accelerating production timelines. While these benefits seem promising, the transition to split blade designs hasn't been entirely seamless. Optimizing aerodynamic performance of the segmented blades has been a challenge, requiring extensive testing to ensure that the joints between sections don't negatively impact the turbine's overall energy output.
Early evaluations of split blade technology also point to potential environmental benefits. Simpler transport arrangements coupled with lighter blade segments appear to have reduced fuel consumption, suggesting lower transport-related carbon footprints. This, along with other research looking into circularity of blades, may eventually lead to more sustainable turbine lifecycles. Whether the technological hurdles can be overcome and the cost savings fully realized remains to be seen, but the V236 project demonstrates the wind energy industry's push for more adaptable and economical designs that are likely to influence the future of turbine manufacturing.
7 Key Innovations in Wind Turbine Blade Segmentation A 2024 Engineering Analysis - Machine Learning Algorithms Optimize Segment Connection Points for 50MW Turbines
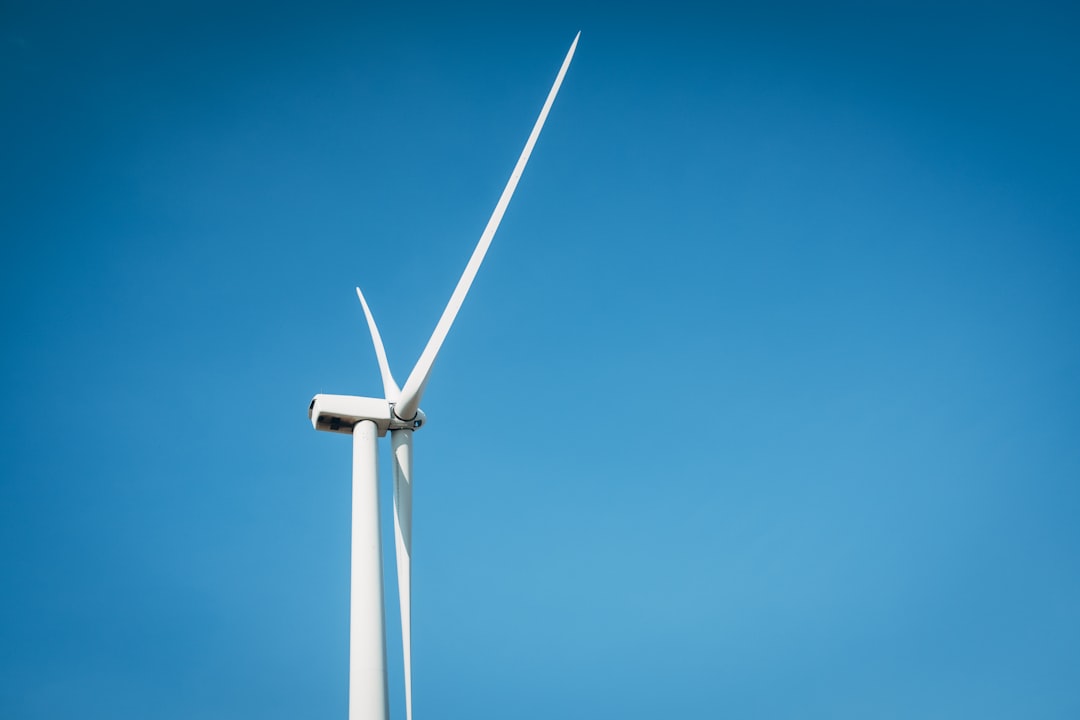
The development of 50 MW turbines necessitates innovative approaches to blade design, and machine learning is emerging as a tool for optimizing the connection points between blade segments. This optimization is critical as segmented blades are becoming more common to manage the transportation and assembly of these massive components. The use of machine learning algorithms could potentially lead to longer and more aerodynamically optimized blade designs, improving turbine efficiency. Researchers are using AI-powered multi-objective optimization frameworks to refine various aspects of turbine performance, including aerodynamic characteristics and blade shape. Beyond the initial design, these algorithms could potentially improve turbine maintenance and operational reliability over the long-term. However, the successful implementation of these algorithms will require extensive testing and careful integration into existing turbine design methodologies. The full potential of these machine learning applications, while promising, remains to be seen and depends on their successful integration into real-world scenarios.
Machine learning algorithms are increasingly being used to refine the design of 50 MW turbine blades, specifically focusing on the connection points between segments. The goal is to find the ideal locations for these connections, improving the overall structural integrity and performance of the blades. While this seems like a natural application of machine learning, we still need to understand the limitations of the approach.
The segmentation of these massive turbine blades is crucial for handling and transporting them. However, optimizing the connection points to maintain aerodynamic performance and structural integrity is complex. By using machine learning algorithms, designers can explore many connection point configurations and analyze how these configurations would respond to various wind conditions and stress scenarios. This virtual testing can reduce the need for extensive physical prototypes, potentially shortening the development cycle.
One interesting aspect of this optimization is how machine learning can leverage past data from previous wind turbine designs. By analyzing historical performance data, these algorithms can identify trends that lead to more efficient and cost-effective designs. This aspect ties directly to the overarching need for cost-competitiveness within the wind energy sector. It also reinforces the push towards designing turbines that can better adapt to local conditions and weather patterns.
It's crucial to acknowledge that relying solely on machine learning outputs can be a double-edged sword. The design process needs to ensure that these automated solutions don't inadvertently introduce weaknesses or flaws that would otherwise be apparent through conventional engineering methods. For example, if optimized connection points compromise the blade's aerodynamic profile or increase the risk of failure in specific conditions, the gains in design time and cost might be outweighed by future operational challenges.
Furthermore, while machine learning is quite effective at identifying optimal connections, understanding how these designs will actually perform in the real-world remains a challenge. There is a risk of over-reliance on machine learning predictions without fully accounting for uncertainties and edge cases. There's also the matter of making sure the machine learning models are well-trained, using relevant datasets. Biases in the training data or incorrect assumptions about wind and load conditions could produce inaccurate results.
Nevertheless, the application of machine learning to wind turbine design shows how advanced computation techniques are being used to solve complex engineering challenges. It is not an entirely new field, but its application to segmentation optimization is a clear sign of the evolving design processes for next generation wind turbines. Whether it fully lives up to its promise of reduced costs and improved performance will depend on further research and practical implementations. We are still in the early stages of understanding how to fully integrate and manage the output of machine learning within the existing process. But the initial indications suggest there are substantial possibilities.
7 Key Innovations in Wind Turbine Blade Segmentation A 2024 Engineering Analysis - Bio-Based Resins Replace Traditional Epoxy in Blade Joint Construction
Wind turbine blade production is seeing a shift towards more sustainable materials, specifically with the introduction of bio-based resins like PECAN. This change presents a compelling alternative to the traditional epoxy resins commonly used in blade construction. PECAN, derived from readily available plant waste like sorbitol, appears to fit within existing manufacturing workflows. This offers a potentially more environmentally friendly approach to blade creation, as opposed to epoxy, which poses significant challenges for recycling.
A 9-meter prototype wind turbine blade utilizing PECAN successfully demonstrated the potential for using this bio-based resin in large-scale projects, showing promise for broader industry adoption. The potential for simpler breakdown and recycling of bio-based resins is particularly interesting. It could represent a major step forward in addressing the current difficulty in recycling conventional turbine blade materials. This aligns with the industry's evolving focus on sustainability, which has been driven by a broader global push for greener energy solutions. However, as with any new material, long-term performance and durability testing are crucial to ensure PECAN's true viability and widespread adoption within the turbine manufacturing process.
Bio-based resins, like PECAN, are being explored as a potential replacement for traditional epoxy in wind turbine blade construction. These new materials are designed to integrate with current manufacturing practices, making the shift potentially smoother than some other innovations. PECAN, for instance, is entirely derived from plant-based sources like sorbitol, which is a byproduct of some agricultural processes. This offers an interesting avenue towards greater sustainability.
A prototype 9-meter wind turbine blade successfully incorporated PECAN, suggesting that these bio-based materials are suitable for larger wind energy applications. The common epoxy thermosets that are currently used often face challenges related to recycling, which can be a hurdle for the broader sustainability goals of the industry. Initial research suggests that plant-based resins might break down more readily, potentially enabling cheaper and more effective blade recycling solutions.
Developing durable and recyclable blades is crucial for ensuring long-term performance and environmental responsibility. The field of wind turbine blade engineering is increasingly focused on innovative materials and improved aerodynamic design, in hopes of both better performance and more sustainable lifecycles. Scientists are actively pursuing resins that easily break down, allowing for easier recycling and potential repurposing of retired blades. This is seen as a key pathway toward making wind turbine technology more sustainable.
Early research from NREL has shown that bio-based resins can outperform conventional epoxies in certain stress tests. This could be a significant turning point, shifting future wind turbine blade design towards a more plant-based material selection. The drive for more sustainable energy sources and materials in the wind energy sector broadly reflects the global need to increase renewable energy capacity. While these new resins seem promising, their ability to truly rival traditional epoxies over the long term still needs to be proven through rigorous testing and field trials. It is interesting to consider the implications of these materials for future wind turbine design and the potential changes to manufacturing, transportation, and maintenance processes that might be necessary for broader implementation.
7 Key Innovations in Wind Turbine Blade Segmentation A 2024 Engineering Analysis - Automated Assembly Systems Cut Blade Connection Time from 48 to 12 Hours
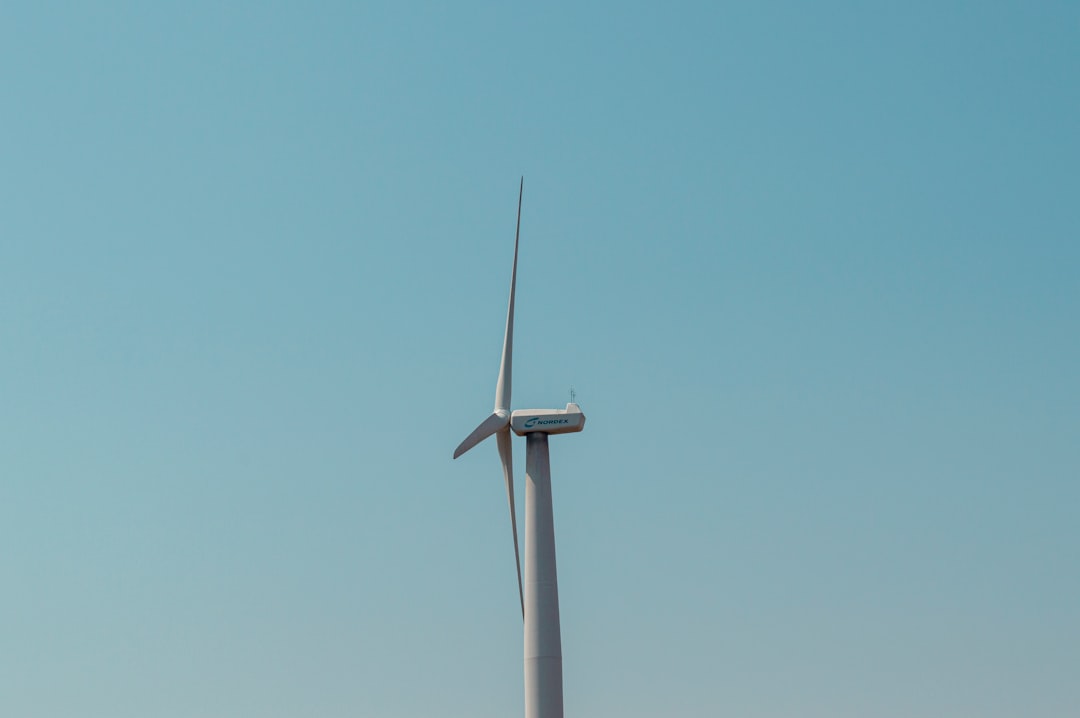
Automated assembly systems are significantly reducing the time it takes to connect wind turbine blade segments, dropping it from a 48-hour process down to just 12 hours. This dramatic reduction in assembly time offers a compelling boost to manufacturing efficiency. Beyond simply speeding things up, this type of automation helps ensure greater precision during the assembly process, which is crucial for maximizing the amount of energy harnessed from the wind. These advancements are part of a broader trend in wind turbine manufacturing, where automation is being incorporated across various stages, including supply chain management and refining the tools and techniques used in manufacturing. The push towards automation is fueled by the industry's efforts to improve sustainability and reduce environmental impact, while simultaneously meeting the rising need for larger and more powerful wind turbines. Although widespread implementation of these automated systems is still evolving, the potential for significantly improved manufacturing processes is clear, presenting a necessary step in the ongoing development of wind power.
Automated assembly systems have proven remarkably effective in reducing the time needed to connect wind turbine blade segments. This advancement has shaved a significant amount of time off the process, bringing it down from a 48-hour ordeal to a mere 12 hours. This is a substantial improvement that directly impacts overall production efficiency.
The accuracy and consistency of the blade profile is paramount in optimizing energy capture from wind. The automated systems, with their inherent precision, are instrumental in consistently achieving the needed tolerances and minimizing any variation between blades. This is particularly crucial given the large scale and complex structure of modern wind turbine blades.
There's a growing trend toward automation in wind turbine blade production. This broader movement can be classified into two main areas: managing the supply chain and employing automation in toolpath generation for tasks like finishing the blades.
A primary goal in incorporating automated systems into domestic wind blade manufacturing is to bolster the stability of the supply chain and simultaneously reduce the environmental impact related to transportation. By reducing reliance on long-distance transport and potentially creating a more distributed manufacturing model, we can lessen the carbon footprint of this industry.
It's worth noting that traditional wind turbine blade manufacturing is, by its nature, heavily labor-intensive. This inherent feature of the production process highlights the need for automation solutions to improve efficiency and potentially address labor shortages.
One of the major benefits of automation is the potential for a significant reduction in the cycle time required to build a blade. Further, automation leads to more consistent quality between turbine blades, minimizing variability. Using robots in this context also permits the employment of larger and more efficient tools, which, in turn, can contribute to reducing the cost per turbine.
Looking forward, we can anticipate enhanced automation leading to a swifter path to market for new turbine designs. This can also contribute to reduced engineering and production costs, alongside improvement in quality control. There's also a distinct potential for greater flexibility in blade design and customization, potentially leading to a new era of turbine innovation.
Currently, there's an emerging focus on deploying robotics to refine the finishing stages of wind blade production. Although this area has seen some noteworthy advancements, wider adoption across the industry is still in its early stages.
The design philosophy behind modern wind turbine blades is deeply rooted in the principles of aeronautical engineering. A fundamental tenet is the pursuit of lightweight designs which contribute to higher overall performance.
As the scale of wind turbines continues to grow, the need for sophisticated automation techniques in the manufacturing process becomes increasingly apparent. Successfully tackling the manufacturing challenges inherent in these larger turbines will require automation to ensure production can keep up with demand.
7 Key Innovations in Wind Turbine Blade Segmentation A 2024 Engineering Analysis - Thermal Stress Monitoring System Prevents Joint Failures in Desert Installations
Desert environments present unique challenges for wind turbine installations, primarily due to extreme temperature fluctuations that can induce significant thermal stress on structural components, particularly at joints. A newly developed Thermal Stress Monitoring System addresses this issue by continuously monitoring these stresses. It achieves this through a combination of strategically placed sensors and data logging systems that provide a real-time view of the stresses experienced by joints within the turbine structure.
The system's key purpose is to proactively identify potential failures before they occur. By detecting changes in thermal stress patterns, operators can intervene early, preventing the gradual deterioration that leads to joint failures. This proactive approach becomes increasingly crucial as wind turbines grow in size and complexity, leading to more intricate and potentially vulnerable joint designs. The reliability of these joints is paramount, as failures can cause costly downtime and even safety risks.
While the focus here is on desert environments, the need for advanced monitoring technologies like this is likely to expand across various operating conditions. As the industry continues its shift towards larger and more sophisticated turbines, the ability to predict and prevent failures through intelligent monitoring becomes a central concern. This innovation emphasizes a broader movement towards more robust and data-driven maintenance strategies for the wind energy sector, a necessary adaptation as turbines face increasingly demanding operational environments.
In desert environments, the substantial temperature swings can create considerable thermal stress on wind turbine components, especially at the joints within segmented blades. These stresses can cause strains that potentially surpass the design limits of the joint materials, ultimately leading to premature failures and shortening the operational lifespan of the turbine.
By implementing a thermal stress monitoring system, we can proactively manage potential issues. This system continuously monitors the temperature and stress experienced at the critical joints using a combination of sensors and data-logging techniques. The real-time data allows for the implementation of predictive maintenance strategies. This means maintenance can be scheduled based on detected stress patterns rather than relying on a fixed schedule, potentially preventing unexpected failures and costly downtime.
The choice of materials for joint construction becomes crucial when considering thermal stress. Different materials react differently to temperature fluctuations. For example, there's growing research exploring the use of materials like polyethylene fibers in place of traditional epoxies due to their higher resistance to thermal cycling. Understanding these material responses is essential for selecting the best components for harsh desert environments.
Furthermore, the thermal stress on turbine blades doesn't remain constant. It varies throughout the year, influenced by seasonal changes. Therefore, it's critical to have a continuous monitoring system to understand the degradation patterns associated with these fluctuating thermal stresses. This detailed understanding leads to the creation of more robust designs that are explicitly adapted to extreme desert conditions.
The precision of thermal stress measurement has increased thanks to advancements in sensor technology. Fiber optic sensors, for instance, provide continuous and highly accurate data. This continuous data stream allows for immediate detection of abnormal temperature patterns, potentially signaling the start of joint failure.
While the initial investment in a thermal stress monitoring system might be substantial, the potential long-term savings are significant. Reduced maintenance, fewer replacements, and prolonged operational lifetimes can offset the upfront costs. This emphasizes the need for careful consideration and a cost-benefit analysis during engineering decisions.
Integrating thermal data with broader turbine monitoring systems that collect wind speed, load, and material strain data enables the development of more holistic predictive models. These comprehensive models can pinpoint likely failure points, highlighting the benefits of interdisciplinary collaboration and analysis within turbine design.
The capacity for real-time analysis of thermal stress data is particularly crucial in desert environments. Conditions can change quickly, so swift decisions are necessary to maintain optimal turbine performance and energy output during periods of high demand.
The continuous feedback generated from thermal monitoring provides valuable information for quickly iterating on turbine designs. Engineers can analyze how current designs withstand thermal stresses and apply those learnings to develop future iterations that address known issues and push innovation.
The detailed understanding of thermal stress effects also drives the development of new joint connection techniques. This includes improved fastening methods and bonding materials that are better equipped to handle the variations in thermal expansion, ultimately leading to more resilient joints that withstand extreme conditions.
Overall, recognizing the importance of thermal stress in desert environments is vital for designing and maintaining wind turbines. The development and implementation of monitoring systems and materials that mitigate its effects are crucial steps towards ensuring the reliable and long-term operation of wind power in these challenging environments.
7 Key Innovations in Wind Turbine Blade Segmentation A 2024 Engineering Analysis - Load Distribution Software Maps Optimal Segmentation Points for Custom Lengths
Software designed to manage load distribution has become a pivotal tool in determining the best places to segment wind turbine blades when custom lengths are needed. This software can accurately predict how loads are distributed across the blade, guiding engineers to identify optimal segmentation points. This ability to precisely pinpoint segmentation locations is crucial for achieving designs that are both easily transported and perform well. As the wind energy industry aims for larger turbine blades to capture more wind energy and potentially reduce costs, this type of software becomes essential for bridging the gap between design ambitions and practical production. These optimized segmentation points ultimately streamline on-site assembly and, in theory, help reduce the environmental impact of transporting massive turbine components. While the software presents exciting possibilities, it is important to emphasize that the performance advantages predicted by the software still need rigorous testing to confirm their real-world effectiveness.
Software designed for load distribution has become a valuable tool in wind turbine blade design, particularly in the context of segmented blades. It can help pinpoint the best places to segment custom-length blades, improving the overall design process and enabling more efficient transport. This software essentially acts as a virtual testing ground, where designers can explore a wide range of segmentation patterns and analyze how they would perform under various conditions.
One of the key benefits of using this software is that it allows for more sophisticated, dynamic load analysis. This means the software can consider how a blade will respond to different wind conditions and create a design that’s optimized for those fluctuations. This ability to anticipate variable loads can improve the blade's overall performance and its structural integrity.
Beyond load analysis, the software often uses algorithms to fine-tune the shape of the segments themselves, searching for designs that are both aerodynamically efficient and structurally sound while minimizing weight. These types of algorithms are often employed to improve the blade design overall.
A critical function of this software is the ability to conduct simulations to predict how different segmentation strategies would behave under various stress conditions. This predictive capability is important because it allows engineers to identify and mitigate potential problems in the design stage, helping to prevent future failures during operation.
Furthermore, the software generates detailed visualizations of stress distribution across the blade, clearly showing how different segmentation options impact stress levels at crucial joints. Using these maps, engineers can identify and address potential areas of stress concentration, which is critical for designing reliable blades.
An interesting development is the ability to incorporate real-world data from operating turbines into the software's analysis. This means that the software can learn and adapt its recommendations based on how actual blades perform, potentially refining the design process over time.
In addition to focusing on purely mechanical aspects, the software often incorporates optimization that considers the cost and ease of manufacturing as well. This approach helps create designs that meet a wide range of project requirements in a practical way.
The software also allows for sensitivity analyses, essentially helping engineers assess how different materials or environmental conditions might affect the performance of the segmentation points. This approach leads to a more robust overall design, as it's less sensitive to potential variations in the real world.
Many of these software packages also include features that encourage collaboration. They can serve as a platform for structural, materials, and aerodynamic engineers to work together seamlessly on a blade design, sharing information and streamlining the development process.
Finally, the software can be used to predict the long-term performance of a segmented blade. By incorporating fatigue life and maintenance requirements into the analyses, engineers can gain a deeper understanding of how different segmentation strategies might impact the blade's lifecycle. In some cases, these tools are incorporating machine learning that allows the software to adapt its strategies over time. The more data is fed into these tools, the better they may become at understanding optimal segmentation points.
These tools have the potential to significantly improve the design and manufacturing process of segmented wind turbine blades. As wind turbines continue to grow in size and complexity, using this type of software will likely be critical for developing robust and efficient designs that can withstand the various stresses they are exposed to. However, there are always concerns when relying on predictive modeling and optimization approaches. It's crucial to be aware of the software's limitations and to cross-check the results with traditional engineering analysis and testing.
More Posts from aistructuralreview.com: