Nanoscale Analysis Reveals How Chromium-Rich Oxide Scales Form Protective Barriers in AISI 316L Stainless Steel at 800°C
Nanoscale Analysis Reveals How Chromium-Rich Oxide Scales Form Protective Barriers in AISI 316L Stainless Steel at 800°C - Nanoscale Distribution Patterns Show Mixed Chromium Iron Oxide Formation at Steel Surface
Examination at the nanoscale reveals a nuanced picture of oxide formation on the AISI 316L stainless steel surface after exposure to 800°C. The oxide layer isn't simply a uniform coating of chromium oxide, but rather a complex mixture of chromium and iron oxides. This mixed composition, observed through detailed analysis, highlights a non-uniform distribution of chromium within the oxide film. The presence of both chromium and iron oxides suggests that the oxidation process isn't exclusively driven by the preferential movement of chromium to the surface, but likely involves a more complex interplay between the two elements.
The observed polyhedral structures of the oxide grains, along with the identified bilayer structure, indicate that the protective oxide film develops through a series of intricate processes. It appears the initial stages of oxidation involve the formation of a layer primarily comprised of chromium(III) oxides, followed by the development of an outer layer with a higher concentration of iron oxides. This complex development process raises interesting questions about the role of iron in the protective properties of the oxide film, especially given the previously recognized importance of chromium-rich oxides in corrosion resistance. Understanding the interplay of chromium and iron oxide formation is essential for gaining a comprehensive grasp of how the surface oxide layer protects the steel under these high-temperature conditions. It is vital for predicting the long-term performance of the steel and improving the design of materials for such environments.
Examining the steel surface at the nanoscale reveals a fascinating picture of how chromium and iron oxides intermingle during the initial stages of oxidation. We find that the oxide layer isn't a uniform blanket of chromium oxide, as one might initially expect. Instead, there's a complex distribution of chromium and iron oxides, forming a mixed oxide layer, particularly near the steel-oxide interface. This mixed composition, evident in the nanoscale patterns, suggests that the formation process isn't simply a case of chromium preferentially oxidizing to form a pure Cr₂O₃ layer. It seems like a dynamic interplay between chromium and iron dictates how the oxide layer develops.
Interestingly, techniques like XPS, when combined with angle-resolved measurements, provide further evidence for this mixed chromium-iron oxide phase. This suggests a gradual transition in composition as you move from the steel surface into the oxide layer, supporting the idea of a bilayer structure proposed in other studies. The inner layer, closer to the steel, appears to be dominated by chromium oxides, while the outer layer contains a higher concentration of iron oxides. This supports the idea that there's a strong link between the oxide formation process, the oxide phase distribution and, ultimately, the protective capabilities of the layer.
It's important to note that the specific nature of this mixed oxide layer is likely influenced by various factors during oxidation, potentially including temperature, oxygen concentration, and even the underlying alloy microstructure. Understanding how these environmental factors affect the mixed oxide formation at the nanoscale could pave the way for engineering more robust, protective oxide scales on steel surfaces, especially when dealing with high-temperature environments where AISI 316L stainless steel is often employed. This type of understanding at the nanoscale offers clues into why certain alloying elements enhance the performance of AISI 316L steel – such as the contribution of molybdenum and nickel to the stability of the chromium-rich oxide phases.
It seems there is still much to be uncovered about the exact roles these elements play. Continued research could lead to the development of new alloys with fine-tuned nanoscale structures, specifically optimized for high-temperature applications. It is important to keep in mind that a better understanding of the formation of these chromium-rich oxide layers is critical for designing durable stainless steels with enhanced performance in challenging operating environments.
Nanoscale Analysis Reveals How Chromium-Rich Oxide Scales Form Protective Barriers in AISI 316L Stainless Steel at 800°C - Advanced Microscopy Methods Map Protective Layer Development in Real Time
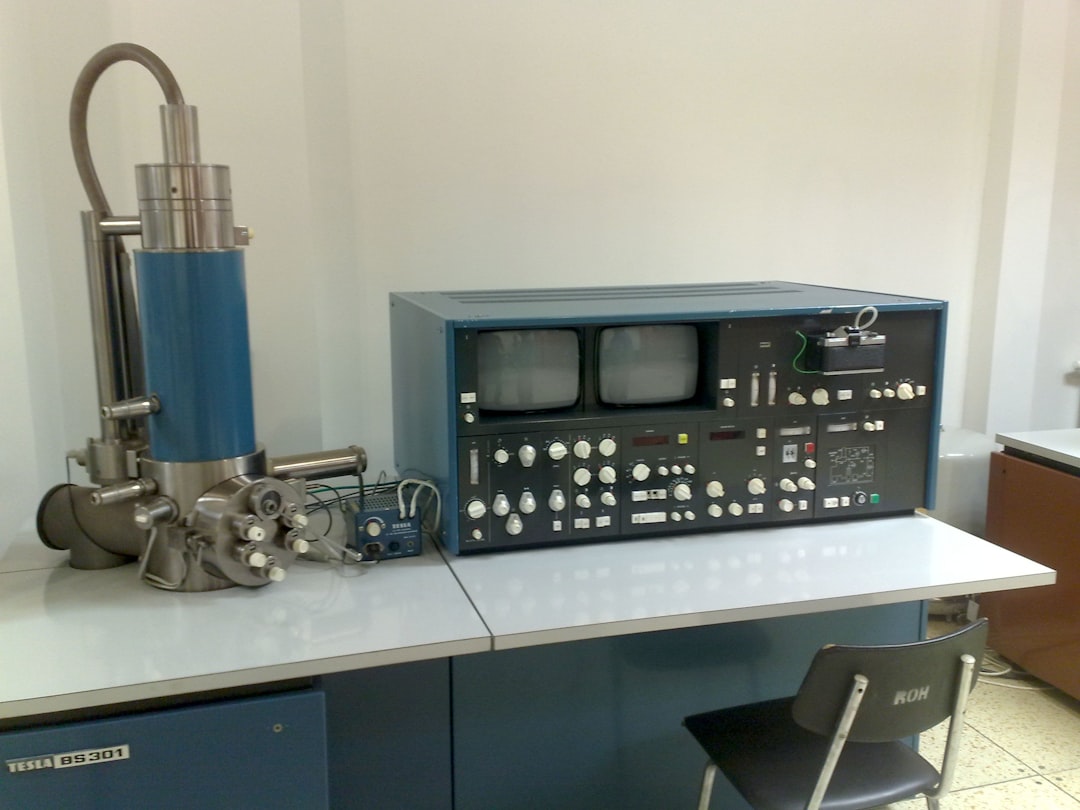
Recent advancements in microscopy techniques have enabled a more in-depth understanding of how protective layers form on materials, especially in the context of high-temperature environments. This is particularly relevant to understanding the behavior of AISI 316L stainless steel at 800°C, where chromium-rich oxide scales are crucial for protecting against corrosion.
Methods like scanning probe microscopy and specialized transmission electron microscopy, capable of capturing events in real-time, are shedding light on the dynamic processes that create these protective layers. This includes observing the complex interplay of chromium and iron oxides as they contribute to the formation of the protective bilayer structure. It is now possible to observe the ultrafast nature of protective layer formation, revealing a more detailed picture of how the protective layers develop and highlighting the factors that influence their effectiveness.
While these advanced microscopy approaches offer invaluable insights, researchers continue to grapple with challenges, such as mitigating any damage that can occur during sample preparation using focused ion beams. These artifacts could potentially distort the accurate observation of protective layer formation and hinder accurate interpretations. Continued investigation of these challenges, coupled with the power of advanced microscopy, will be crucial for designing materials with enhanced durability in extreme environments. A clearer understanding of protective layer formation is fundamental for tailoring materials, particularly for applications that involve prolonged exposure to high temperatures.
Real-time observations using advanced microscopy, like in situ TEM, are providing a new window into how protective layers form on AISI 316L stainless steel at high temperatures. We're able to see the dynamic oxidation process unfold, giving us valuable clues about what's happening at the nanoscale.
The interface between the steel and the forming oxide isn't a simple transition. Instead, it's a complex dance of microstructural changes that have a major impact on how well the stainless steel holds up against corrosion. It's fascinating to see how these alterations affect the long-term durability of the steel.
The mixed oxide layer that forms isn't static. Its composition changes depending on things like temperature and the availability of oxygen. Understanding how the proportions of chromium and iron oxides shift is important, as it clearly impacts the protective quality of the layer.
The other elements in the steel, like molybdenum and nickel, play a crucial role in how the chrome-rich oxide layer forms. They seem to tweak the oxidation process and contribute to the stability of the oxide film at high temperatures. This hints at the possibility of fine-tuning alloy composition to enhance protection.
The polyhedral shapes of the oxide grains aren't just pretty; they may give us insights into how grain boundaries in the oxide affect its protective capabilities. This sort of detail is crucial when thinking about how the oxide layer resists corrosive environments.
The oxide scale isn't uniformly thick across the entire surface. Thickness variations might create preferential paths for ion movement, potentially compromising the integrity of the protective barrier. We'd need to know more about these variations to ensure the protection is consistent.
At 800°C, the formation of both chromium and iron oxides speeds up significantly. This highlights how temperature sensitivity might be a key factor for designing protective layers in applications with fluctuating temperatures.
The shift from chromium(III) oxide to iron oxide at the surface suggests that protection isn't just about having a stable oxide layer. It's about phase stability shifts, which could potentially be leveraged in future material design approaches.
With the detailed information from nanoscale analysis, it seems we could potentially develop predictive models to understand how protective oxide scales will behave in different operating conditions. This is extremely valuable for industries that rely heavily on AISI 316L.
This research is just the beginning. Further investigation into these mixed oxide phases might open up new avenues for developing alloys that not only resist oxidation but can also adapt or even repair their own protective oxide layers in response to environmental stresses. The goal here is to significantly extend the usable life of materials in extreme environments.
Nanoscale Analysis Reveals How Chromium-Rich Oxide Scales Form Protective Barriers in AISI 316L Stainless Steel at 800°C - Chemical Migration Creates Two Layer Structure During 800°C Heat Treatment
During the 800°C heat treatment of AISI 316L stainless steel, a fascinating two-layer structure emerges due to chemical migration within the material. This structural shift plays a key role in the formation of the protective chromium-rich oxide scales, which are crucial for shielding the steel in harsh environments. Essentially, a complex interaction causes the inner layer to be mainly chromium oxides, while the outer layer develops a higher concentration of iron oxides.
This intricate process, revealed by nanoscale investigations, exhibits variations in the oxide's thickness and hardness, providing insights into the dynamic nature of protective layer development during heat treatment. Moreover, the detailed composition of the oxide scales, considering the influence of other elements in the steel alloy, has a direct impact on the material's mechanical strength and corrosion resistance. Understanding these interconnected processes at the nanoscale is of utmost importance when designing and optimizing stainless steel materials for use in high-temperature applications where corrosion protection is paramount. Failing to comprehend these processes could lead to subpar results or unexpected performance in the long term.
The formation of the oxide layer on AISI 316L stainless steel at 800°C isn't a simple process. Instead of a single, uniform layer, we observe a distinct two-layer structure. This structure is characterized by an inner layer primarily composed of chromium oxides and an outer layer containing a higher concentration of iron oxides. This bilayer structure likely contributes to the protective mechanisms that safeguard the steel in high-temperature environments.
Chromium and iron don't migrate randomly during the oxidation process. Instead, their movement is intricately tied to temperature and other factors, which in turn control the distribution and stability of the oxides formed. This dynamic interplay highlights a complex interplay between chemistry and temperature.
It's noteworthy that the oxide layer's thickness and composition can vary significantly across the steel's surface. These variations introduce the possibility that the protective properties might not be uniform, which could lead to some areas being more vulnerable to corrosion than others. This raises some intriguing questions about how this surface variability affects the overall effectiveness of the protection mechanism.
The presence of alloying elements, such as molybdenum and nickel, further complicates the process in an interesting way. These elements seem to influence the oxidation dynamics, leading to a greater stability of the chromium-rich oxide phases. As a result, these alloying elements indirectly help increase the steel's long-term resilience in high-temperature scenarios.
Recent advancements in microscopy techniques have made it possible to watch oxidation events unfold in real-time. This is a valuable tool for researchers, allowing us to obtain a more accurate picture of the dynamic processes involved. However, the methods used to prepare samples for analysis, particularly those utilizing focused ion beams, can sometimes introduce artifacts that may interfere with accurate interpretations of the observed behaviors. This needs to be considered when studying the oxide formation process.
The polyhedral shapes of the oxide grains are not just a random phenomenon; they suggest a potential relationship between oxide grain boundaries and the protection it provides. How the boundaries influence the oxide layer's ability to resist harsh environments is another interesting facet worthy of continued investigation.
The rate of chromium and iron oxide formation significantly accelerates at higher temperatures. This temperature sensitivity implies that controlling the environment, especially in applications where temperatures fluctuate, is critical for optimizing the protective layer's performance.
The transition zone between the steel and the developing oxide layer is complex. It's not a simple transition but rather involves significant microstructural changes, which play a significant role in the steel's ability to resist corrosion during oxidation.
As the mixed oxide layers form and evolve, their compositions can shift over time. This suggests the protective mechanism is a dynamic process and must be considered when designing materials for high-temperature environments.
By combining our observations from nanoscale analyses, we might be able to create predictive models of oxide behavior in a variety of operational conditions. This kind of predictive capability will prove immensely useful in tailoring materials to achieve exceptional performance in challenging applications.
The study of oxide layer formation on AISI 316L stainless steel at 800°C, even at this early stage, has unveiled several intriguing features. The complexity of the protective layer formation indicates that we need to delve deeper into the interplay of chemical migration, temperature sensitivity, and the effects of alloying elements to fully understand the system. Future studies can potentially lead to the development of materials that not only resist corrosion but also possess the ability to repair or adapt their own protective layers in response to harsh conditions. The ultimate goal is to extend the lifespan of materials operating in challenging high-temperature environments.
Nanoscale Analysis Reveals How Chromium-Rich Oxide Scales Form Protective Barriers in AISI 316L Stainless Steel at 800°C - Local Oxygen Conditions Drive Protective Scale Growth and Breakdown
The development and eventual failure of protective oxide layers on AISI 316L stainless steel at 800°C are significantly influenced by the local oxygen environment. This protective layer, primarily composed of chromium and iron oxides, experiences variations in its composition and structure, leading to differences in its ability to protect the steel. It's not just the overall oxygen presence that matters; the specifics of where oxygen is available and at what levels can affect how the oxide layer grows. This localized oxygen environment impacts the distribution of chromium and iron in the oxide, affecting its protective properties.
For example, the introduction of water vapor can contribute to the breakdown of the otherwise protective scales, suggesting a complex interplay between moisture and oxygen availability. The manner in which elements like chromium and iron move, combined with shifts in oxide phases and the accessibility of other elements, ultimately controls the appearance and protective ability of the layer. This highlights the significance of understanding the oxygen environment's influence on oxide formation and how it relates to the ability of the oxide scale to defend the steel. Moving forward, a greater focus on these localized oxygen conditions will be vital for enhancing the durability and design of protective oxide layers for materials subjected to high-temperature environments. This could help engineers design more resistant materials for specific conditions.
The local oxygen environment significantly influences how fast and what kind of oxide layer forms on AISI 316L stainless steel. Changes in the amount of oxygen available can lead to differences in the thickness and protective capabilities of the oxide layer.
It's interesting that the formation of a two-layer structure isn't random, but rather a result of elements like chromium and iron moving strategically within the steel. The inner layer of the oxide seems to favor chromium oxides, while the outer layer leans towards iron oxides. This layered arrangement might be a key element in its protective role against corrosion.
The effectiveness of the protective oxide layers doesn't remain constant, as they change with the temperature. Understanding how different oxide phases transition, particularly at 800°C, could lead to breakthroughs in protection strategies for stainless steel in demanding environments.
We've also found that the oxide layer isn't perfectly uniform. Thickness variations across the surface could create weak spots that could eventually compromise the protective barrier. This observation indicates that perhaps material design needs to be refined to ensure consistent protection.
Alloying elements like molybdenum and nickel play an important role in stabilizing chromium oxides, a crucial element of the protective mechanism in high-temperature settings. It's not just about the structural strength; they actively participate in the oxidation process itself.
The field of microscopy has advanced, allowing us to observe oxidation in real-time. This helps scientists better understand how the oxide layer forms. However, this has brought up new challenges, such as potential flaws in the sample preparation that could impact our interpretations of what's really happening.
The oxide grains have unique polyhedral shapes, and these shapes might be linked to the protective capabilities of the layer. How the boundaries of these grains affect corrosion resistance is a question that needs more investigation.
Chromium and iron don't just move around randomly during the oxidation process. The way they migrate is closely tied to temperature and chemical reactions. Understanding this relationship between temperature and element movement is essential for creating optimal protective oxide layers.
We also see that the composition of the mixed oxide layers doesn't remain static. Instead, it changes over time based on surrounding conditions. This dynamic behavior is vital for designing materials that can adapt to changing conditions in their operational environments.
The information we're gaining from nanoscale analyses might lead to the development of prediction models that illustrate the behavior of protective oxide layers across different situations. This type of prediction capability would be immensely helpful in tailoring AISI 316L to meet the specific requirements of various high-temperature applications.
This research gives us a much more nuanced understanding of the oxidation behavior of AISI 316L stainless steel at 800°C. The complexity we've uncovered underscores the need for further studies that explore how chemical interactions, temperature sensitivity, and alloying elements work together to control the protective oxide layers. Hopefully, this leads to the development of materials that not only resist corrosion but can adapt and even heal their own protective layers in response to demanding conditions, thus significantly extending the lifetime of materials operating in extreme environments.
Nanoscale Analysis Reveals How Chromium-Rich Oxide Scales Form Protective Barriers in AISI 316L Stainless Steel at 800°C - Internal Oxidation Forms Secondary Barrier Below Primary Surface Layer
At 800°C, AISI 316L stainless steel experiences internal oxidation, a process that creates a secondary protective barrier beneath the initial surface layer. This secondary barrier exhibits a fascinating two-layered structure. The inner layer is predominantly composed of chromium oxides, while the outer layer has a higher concentration of iron oxides. The distinct composition of these layers contributes to the overall protective capacity of the steel against corrosive environments at elevated temperatures. This two-layer formation suggests complex chemical interactions and movement within the steel during high-temperature exposure. Importantly, it highlights how factors beyond simply the alloy composition, such as the local oxygen environment, play a crucial role in determining the effectiveness of the protective oxide scales. A comprehensive understanding of this two-layered system offers the possibility of developing more durable and robust stainless steel alloys that can withstand demanding high-temperature applications.
The formation of the two-layer oxide structure we see in AISI 316L at 800°C isn't just a product of high temperatures. It's a fascinating dance of chromium and iron atoms, influenced by the local environment, especially the oxygen around them. This suggests the environment plays a key role in dictating how the oxide layer grows.
Interestingly, the thickness of each oxide layer isn't uniform across the surface. This unevenness hints at the possibility of variations in oxygen concentration, which could lead to weak spots in the protection. This could explain any unexpected behavior in corrosion tests, and is something worth exploring further.
Certain alloying elements, like molybdenum, seem to make the chromium-rich oxide layers more stable. This is particularly important for preserving the protective layers at high temperatures where oxidation is a major concern. The increased stability could improve the material's long-term resistance in demanding environments.
New techniques that allow us to watch oxide layer formation in real-time have opened up exciting opportunities. We can now observe the dynamics of how elements move around and interact during oxidation in a way we couldn't before. This is a major step forward, and could ultimately help us design more effective coatings to protect materials in extreme conditions.
The oxide layers show these interesting polyhedral shapes. It's possible that how these shapes interact at the grain boundaries influences the protection provided. Figuring out how grain boundaries factor into corrosion resistance could lead to innovative approaches to design more robust oxide layers.
We've also learned that variations in the local environment, like changes in moisture and oxygen levels, can hasten the breakdown of the protective oxide layers. This suggests that the effectiveness of these layers depends on the specific conditions they face. It's not simply a matter of the material itself, but rather how the material interacts with its environment.
The change from chromium(III) oxide to iron oxide at the surface also raises questions about how stable these oxide phases are. Small fluctuations in temperature or the surrounding oxygen concentration could lead to shifts in phases, which may negatively impact protection.
The dependence of the mixed oxide layer on chromium and iron means that boosting one element's performance could hurt the other. This makes the process of designing improved alloys more challenging, as it requires considering the interplay between elements and their impacts on corrosion.
At a very detailed level, we can see that the protective layers aren't static. They seem to be able to respond and adjust to changing conditions. This could lead to a new generation of materials designed to self-repair or adapt to environmental shifts, enhancing their long-term performance.
The complex interplay between the microstructural changes happening during oxidation and the resulting protective capabilities is truly remarkable. It emphasizes the need for continued research into these mechanisms to fully grasp how protective oxide layers behave in different situations. Understanding these behaviors will ultimately enable us to design materials that withstand challenging operational environments for a much longer time.
Nanoscale Analysis Reveals How Chromium-Rich Oxide Scales Form Protective Barriers in AISI 316L Stainless Steel at 800°C - Matrix Analysis Shows Direct Link Between Temperature and Scale Stability
Detailed analysis of the oxide scales formed on AISI 316L stainless steel at 800°C reveals a strong link between temperature and the protective layer's stability. The research indicates that the development of the protective chromium-rich oxide layers is directly influenced by temperature, with a two-layered structure consistently emerging at higher temperatures. This structure, with a chromium-rich inner layer and an iron-rich outer layer, seems to be a key feature in how effectively it shields the steel.
Furthermore, the study emphasizes the importance of the local oxygen environment, showing that its variations significantly impact both the structure and protective performance of the oxide layer. The formation of these protective layers appears to be a complex interplay between chemical reactions inside the steel and the external conditions. Elements like chromium and iron move within the material, driven by temperature and oxygen availability, ultimately shaping the oxide layer that forms. This understanding of the interaction between internal processes and external factors is vital if we are to design and optimize stainless steel alloys for environments that push them to high temperatures. A thorough comprehension of this relationship is crucial for developing more durable and effective materials for high-temperature applications.
The high-temperature (800°C) oxidation of AISI 316L stainless steel reveals a dynamic interplay of factors influencing the development of protective oxide layers. We see that the temperature itself significantly boosts the formation of both chromium and iron oxides, suggesting a strong temperature dependence of the protective layer's formation and behavior.
Instead of a simple, uniform chromium oxide layer, we see a complex bilayer structure develop. This structure involves a chromium-rich inner layer and an iron-rich outer layer. Each layer appears to have a specific function in the overall protective mechanism against corrosion.
Further investigation into how chromium and iron migrate during this oxidation process shows a strong connection to local environmental conditions, like temperature and the amount of available oxygen. This dynamic relationship creates a non-linear response from the protective oxide layer to changes in the environment.
One interesting aspect is that the oxide layer's thickness isn't consistent across the steel's surface. We see variations that might lead to potential vulnerabilities or "weak points" in the protective barrier. Understanding these variations is important for accurately predicting long-term performance and corrosion resistance.
The inclusion of alloying elements like molybdenum and nickel in the AISI 316L steel has a noticeable impact on the oxidation process and oxide layer properties. It seems these elements particularly improve the stability of the chromium-rich oxide phases, which are vital for corrosion resistance. It's intriguing to consider that manipulating alloy composition could provide a way to enhance high-temperature performance.
The ability to observe oxidation processes in real time, thanks to new microscopy tools, is a game changer. We are now able to better understand how oxide layers evolve and respond to environmental stimuli. However, we need to acknowledge that techniques like using focused ion beams for sample preparation might cause artifacts that impact the interpretation of these observations.
The polyhedral shapes of the oxide grains, which are a recurring theme in this study, may be linked to the protection these layers offer. The behavior at the grain boundaries, which define the boundaries between these polyhedra, might be a crucial aspect influencing the oxide layer's resistance to corrosion.
The local oxygen environment has a dramatic effect on oxide formation and how well it protects the steel. Subtle changes in oxygen availability significantly influence how the protective oxide layer grows and its characteristics.
The transition from chromium(III) oxides to iron oxides at the oxide surface suggests a dynamic balance. This delicate balance is sensitive to changing environmental conditions. Understanding this equilibrium and phase stability is crucial for the future design of these materials for demanding applications.
The intricate interplay of microstructural changes within the oxide layers suggests a promising possibility: developing materials with adaptive characteristics. Perhaps materials can be designed with a built-in ability to self-repair or modify their protective layers in response to harsh conditions.
Overall, we've found a fascinating world of chemical and physical interactions within this seemingly simple system of AISI 316L stainless steel during high-temperature oxidation. Clearly, there's much we still need to learn about the detailed interactions of elements and environmental effects on the development and stability of these protective oxide layers. This ongoing work and future studies are vital if we are to design new and improved materials capable of operating under extremely harsh conditions.
More Posts from aistructuralreview.com: