Understanding Gauge vs
Absolute Pressure in Aircraft Altimeter Calibration A Technical Deep-Dive
Understanding Gauge vs
Absolute Pressure in Aircraft Altimeter Calibration A Technical Deep-Dive - Fundamental Differences Between Gauge and Absolute Pressure Measurement Systems
The core difference between gauge and absolute pressure systems lies in how they define the zero point for pressure. Gauge pressure measures the pressure above or below ambient atmospheric pressure. Think of it as a relative measurement, where the surrounding air pressure acts as the reference point. As a consequence, gauge pressure readings change with shifts in atmospheric pressure, which can occur due to weather patterns or variations in altitude.
Absolute pressure, on the other hand, uses a true vacuum as its zero reference. It captures the total pressure exerted on a surface, encompassing both the pressure from the fluid and the atmospheric pressure. This makes it a more stable and unchanging measurement. Because it's not affected by changes in surrounding air pressure, absolute pressure proves essential in situations where consistent and reliable pressure readings are crucial.
The impact of this difference is especially evident in fields like aircraft altimeter calibration. In such scenarios, precise pressure measurement is critical for safety and navigation. Similarly, in environments where pressure can change dramatically, such as deep underwater, using absolute pressure ensures a correct understanding of the total force exerted on objects and structures. In essence, comprehending the difference between gauge and absolute pressure is paramount for ensuring accurate pressure measurements and calculations in engineering and scientific disciplines.
1. Gauge pressure hinges on atmospheric pressure as its zero point, which means it can dip below zero when the measured pressure falls beneath atmospheric pressure. Absolute pressure, in contrast, always registers as a positive value because it uses a perfect vacuum as its starting point, resulting in a fundamentally different perspective on pressure.
2. Gauge pressure readings are susceptible to changes in atmospheric pressure, leading to shifts in measured values and making calibrations tricky. These variations require ongoing adjustments to keep readings accurate. Absolute pressure systems, on the other hand, provide a stable baseline unaffected by fluctuations in atmospheric pressure, hence streamlining calibration processes.
3. Many aircraft altimeters function based on absolute pressure readings, employing internal reference sources to guarantee consistent altitude readings. This internal reference is vital in mitigating the impact of daily atmospheric variations that could distort readings if relying on gauge pressure alone.
4. The choice between gauge and absolute pressure measurement systems can influence the design and material selection of pressure-sensitive components within a system. For instance, components within a system intended for gauge pressure must be robust enough to withstand pressure variations while also needing specific tolerances.
5. Gauge pressure sensors often struggle to account for altitude and temperature effects, causing inaccuracies, especially in demanding fields like aviation. Absolute pressure sensors are inherently designed to factor in these changing environmental variables. This innate adaptation makes them considerably more reliable during flights where altitude is constantly changing.
6. In certain aerospace applications like engine control systems, absolute pressure sensors are favored due to the precise control they allow for fuel-air mixtures. These mixture calculations hinge on accurate, stable pressure metrics that remain unchanged throughout the flight.
7. Applications involving vacuums often necessitate absolute pressure measurements because gauge pressure systems simply can't measure below atmospheric pressure. This limitation poses a significant hurdle when working in deeply vacuumed environments, limiting the gauge pressure's usefulness.
8. Calibrating gauge pressure systems often needs a concurrent reference atmospheric pressure measurement. This adds complexity to the calibration process. On the other hand, absolute pressure sensors can be readily calibrated directly using a known vacuum source, simplifying the procedure significantly.
9. Some sophisticated instruments integrate both pressure measurement systems for a more comprehensive understanding of a system. A good example is an aircraft system where gauge pressure can offer a useful relative pressure reading, but absolute pressure is utilized for precise altitude or density calculations which are crucial for safety.
10. The decision to use either gauge or absolute pressure in a system has ramifications for how automated systems are controlled. Depending on whether the pressure being used is relative or absolute, feedback mechanisms in the system can need to be carefully designed to respond appropriately and effectively.
Understanding Gauge vs
Absolute Pressure in Aircraft Altimeter Calibration A Technical Deep-Dive - Aircraft Static Port Design and Its Role in Pressure Detection
Aircraft rely on static ports to gather atmospheric pressure data, a crucial input for instruments that determine altitude, airspeed, and vertical speed. These ports essentially sample the surrounding air pressure and feed this information to various onboard systems. As an aircraft climbs, the external air pressure naturally decreases, and the static port faithfully captures these changes.
However, the reliability of the pressure data relies on the static port remaining unobstructed. Ice formation or debris can block the port, trapping the existing pressure reading and causing the altimeter to freeze, essentially displaying a false altitude. This potential for inaccurate readings highlights the importance of proper static port design and placement, ideally in locations shielded from airflow disruptions and equipped with heating elements to combat ice buildup.
The design of static ports, therefore, has direct implications for the accuracy and safety of flight. Their ability to provide a reliable representation of static pressure, unaffected by airflow irregularities and environmental conditions, is crucial for the proper functioning of flight instruments. Ultimately, ensuring that static ports are correctly positioned and maintained is a critical part of ensuring flight safety.
1. The placement of a static port on an aircraft is crucial for obtaining accurate readings of static air pressure, which is fundamental for determining altitude, airspeed, and vertical speed. Ideally, they're located where airflow disturbances are minimal, as even minor disruptions can lead to incorrect data impacting flight safety.
2. The design of a static port, including its size and angle, aims to minimize the effects of boundary layer influences on pressure readings. This design process is a careful balancing act, considering factors such as aircraft shape and airspeed to ensure consistent results.
3. Ice buildup on a static port is a persistent problem that can obstruct or distort the airflow, causing unreliable pressure readings. While anti-ice systems are implemented, pilots must remain vigilant about possible deviations in altitude indications.
4. The relationship between altitude and static pressure, as described by the Barometric formula, guides engineers in understanding how pressure changes with increasing height. This fundamental principle underpins the design and calibration of altimeters and airspeed indicators.
5. Before a static port's final design, computational fluid dynamics (CFD) simulations are often employed. This allows engineers to optimize the port's design for different flight conditions, helping to ensure accurate pressure readings throughout the flight envelope.
6. Intriguingly, even minor variations in the static port design can lead to substantial differences in pressure readings. This reinforces the emphasis on high precision during the design phase of aerospace engineering—a poorly located port could lead to inaccuracies throughout the flight.
7. In aircraft with multiple engines, some designs use a differential static pressure system, averaging readings from several ports. This redundant setup offers better accuracy by potentially compensating for issues at individual ports due to airflow irregularities.
8. Aircraft manufacturers constantly weigh the aesthetics of a sleek aircraft exterior against the functional needs of static port design. While a streamlined fuselage is aerodynamically beneficial, it can sometimes hinder pressure measurement accuracy if not properly considered during the design process.
9. An inaccurate static port, whether from miscalibration or poor placement, can result in a "static source error." This leads to inaccurate altitude readings, which could be quite hazardous, especially during instrument approaches.
10. Modern aircraft commonly incorporate digital pressure sensors with static ports. This enhances data processing and allows for real-time diagnostics, improving the accuracy of altitude and airspeed information. However, these new systems need careful calibration and validation to guarantee reliable readings.
Understanding Gauge vs
Absolute Pressure in Aircraft Altimeter Calibration A Technical Deep-Dive - Converting Raw Pressure Data into Accurate Altitude Readings
Precise altitude determination in aviation relies on accurately converting raw pressure data into meaningful altitude readings. This conversion process is fundamentally tied to the distinction between gauge and absolute pressure, with absolute pressure proving more reliable due to its incorporation of total pressure, encompassing both atmospheric and fluid pressures. Aircraft altimeters, which are critical for safe navigation, depend on this conversion. Maintaining accuracy in these readings is crucial as atmospheric pressure fluctuates due to changes in altitude and weather. Air density, intricately linked to pressure, also varies with altitude, and these changes must be meticulously considered during altitude calculation. If these factors aren't carefully accounted for, errors in pressure readings can translate into significant errors in altitude, underscoring the importance of meticulous calibration procedures for aircraft altimeters. A thorough understanding of how these factors interplay is paramount for ensuring the reliability of altitude information and the safety of aircraft operations.
1. As an aircraft ascends, atmospheric pressure drops predictably, roughly 1 inch of mercury for every thousand feet gained. This relationship is fundamental to converting raw pressure data into meaningful altitude readings, but it demands meticulous calculations to ensure accuracy across a flight's entire altitude range.
2. The International Standard Atmosphere (ISA) model provides a theoretical framework for linking pressure to altitude, assuming a standardized temperature profile. While useful as a starting point, engineers constantly grapple with the fact that real-world atmospheric conditions deviate considerably from this idealized model. This creates a need for adjustments and corrections to achieve accurate altitude calculations.
3. Altimeters often display pressure in inches of mercury or hectopascals (hPa), but a mismatch in units can quickly lead to altitude interpretation errors. Consistent, careful unit conversions are crucial for safety and operational accuracy, as even a slight mistake can significantly impact aircraft performance.
4. Temperature has a noticeable impact on barometric altimeters. Warmer air expands, influencing pressure readings and, as a result, potentially causing inaccurate altitude displays. Consequently, altimeter calibration procedures must incorporate temperature corrections to ensure the instruments faithfully represent true altitude.
5. Setting the correct altimeter reference, or local altimeter setting, is critical for accurate altitude information. Pilots need to continuously adjust this setting during flights as atmospheric pressure changes, a process that is crucial for avoiding miscalculations, particularly during ascent and descent phases.
6. The "standard atmosphere" model, while conceptually handy, is a simplified representation of a complex system. Extreme weather events can drastically deviate from these assumptions. In such cases, engineers must account for these local conditions to improve altitude reading reliability.
7. Altitude calibration becomes more complex in mountainous regions, where terrain-induced variations in atmospheric pressure are more pronounced. Aircraft operating in these areas must deal with these local differences to guarantee accurate navigation and safe flight operations.
8. While digital pressure sensors promise greater precision and quicker response times, they introduce another layer of complexity. Engineers need to carefully validate these sensors' performance under a wide range of environmental conditions to ensure raw pressure data remains accurate. Otherwise, you risk introducing errors in the conversion process.
9. Atmospheric pressure isn't static; it's influenced by weather systems like high-pressure zones and frontal passages. Understanding these fluctuations is crucial for processing raw pressure data and achieving reliable altitude readings throughout a flight.
10. The process of translating raw pressure readings into altitude is prone to imperfections. Instrument errors and calibration drift can introduce inaccuracies. Therefore, regular maintenance and recalibration are necessary to maintain a high level of accuracy and ensure flight safety.
Understanding Gauge vs
Absolute Pressure in Aircraft Altimeter Calibration A Technical Deep-Dive - Temperature Effects on Altimeter Accuracy and Compensation Methods
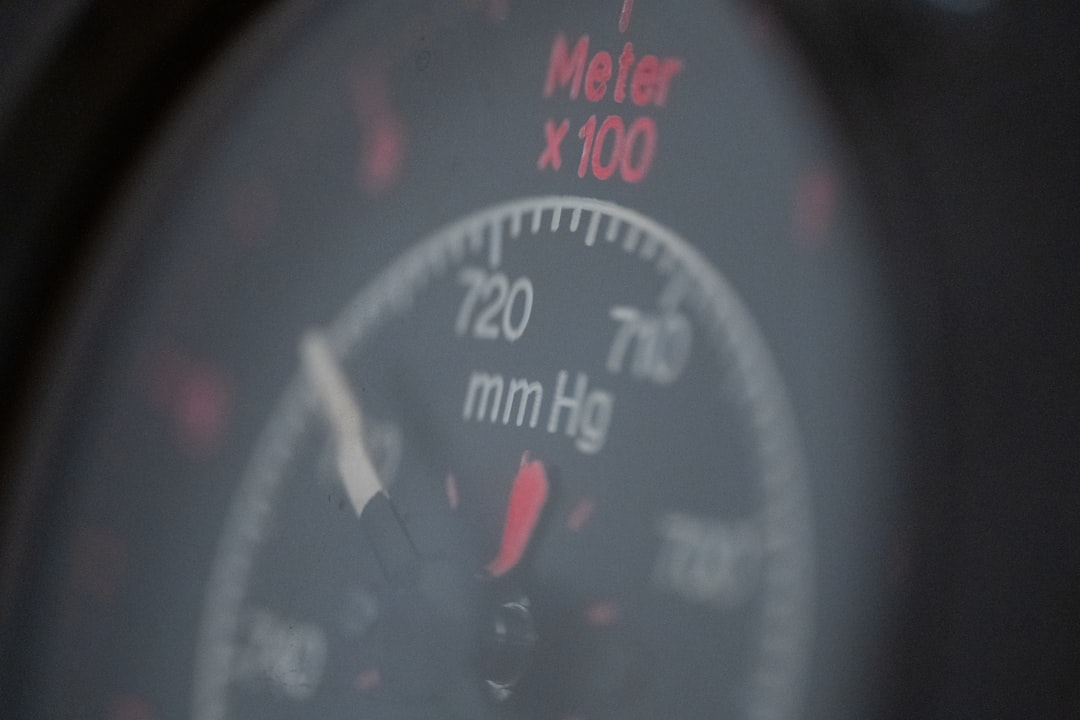
Aircraft altimeters, while designed to measure altitude based on air pressure, are significantly affected by temperature changes. When the actual air temperature deviates from the standard temperature profile established by the International Standard Atmosphere (ISA), the altimeter's readings can be inaccurate. For example, in colder-than-standard temperatures, the indicated altitude will be higher than the aircraft's true altitude, creating a potential hazard. This occurs because the relationship between pressure and altitude is affected by temperature changes.
The degree of error introduced by temperature changes is roughly 4 feet per degree Celsius difference from ISA. This highlights the need for corrective measures, especially in situations where temperatures are significantly different from standard. Pilots and flight crews need to use temperature correction charts or procedures to adjust for these inaccuracies. These adjustments can be quite complex in extreme temperature situations. The importance of accurate altitude determination for safe flight underscores the need for pilots to use appropriate compensation techniques in any non-standard temperature conditions.
It is important to note that the altimeter itself doesn't automatically adjust for temperature changes. The calibration process for altimeters focuses on pressure settings, not temperature. Because of this lack of automatic temperature compensation, understanding the effects of temperature is critical for ensuring accurate altitude measurements. This understanding is vital in ensuring safe flight operations across a range of temperature conditions and altitudes.
1. Air temperature significantly influences altimeter readings, particularly in high-performance aircraft, where a deviation of up to 200 feet can occur. This is due to how temperature affects air density and pressure, making temperature correction crucial for accurate altimeter calibration.
2. When the temperature rises, the air becomes less dense at a given altitude, leading to what's known as an "altimeter error." This can be especially problematic during approaches and landings, where accurate altitude is essential for safety, as pilots could be misled about their true height above the ground.
3. Conversely, cold temperatures make the air denser, resulting in altimeter readings that are higher than the actual altitude. This can increase the risk of incidents like controlled flight into terrain (CFIT) if not properly compensated for during flight.
4. Some aircraft employ automated temperature compensation algorithms that adjust altitude readings based on real-time temperature data. While beneficial, these systems require careful calibration to avoid introducing new errors into the altitude calculation process.
5. Testing has revealed that altitude accuracy can suffer considerably in extreme temperature conditions, like those found at high altitudes in Arctic or tropical regions. This puts pressure on engineers to design altimeters capable of consistently providing accurate readings across a wider temperature range.
6. Interestingly, different aircraft types may have different compensation methods. Turboprop aircraft, for example, usually rely on pilot-entered temperature adjustments, whereas some turbojet aircraft use automatic temperature adjustments built into their systems.
7. While the International Civil Aviation Organization (ICAO) provides guidelines for correcting altimeter readings due to temperature, not all aircraft have the necessary systems to comply with those standards. This leads to variations in the accuracy of altitude readings across different aircraft types.
8. In many cases, sensor malfunctions or improper calibration can lead to incorrect temperature readings. This can trigger a chain reaction of errors, making data from the sensors unreliable for autopilot and other automated systems that rely on accurate altitude data.
9. Rapid shifts in temperature, often seen during changing weather conditions, can cause significant discrepancies between calibrated and actual altitude, particularly during crucial flight phases. This underscores the importance of monitoring temperature and pressure accurately in real-time.
10. Temperature-related altimeter errors are a factor that air traffic controllers and pilots must consider. Differences in altitude readings between aircraft can make traffic separation more challenging and highlight the need for improved communication protocols between pilots and controllers.
Understanding Gauge vs
Absolute Pressure in Aircraft Altimeter Calibration A Technical Deep-Dive - QNH vs QFE Settings in Real World Flight Operations
In the realm of aircraft operations, the proper use of QNH and QFE altimeter settings is paramount for ensuring accurate altitude information, especially during critical flight stages like takeoff and landing. QNH aligns the altimeter to display altitude relative to mean sea level (MSL), a crucial factor for navigating varied terrains. Conversely, QFE provides the aircraft's height above a specific reference point, most often the runway's threshold. The consequences of using incorrect settings can be severe, leading to misjudgments of altitude that threaten safe separation from the ground and other aircraft. Furthermore, pilots are continuously required to adjust altimeter settings as they traverse different geographic locations and altitudes, highlighting the vital role of accurate calibration in aviation. The ability to accurately understand and utilize these settings enhances navigation precision and bolsters safety across a spectrum of atmospheric environments. Failure to adhere to proper calibration procedures can introduce significant risks into flight operations, underscoring the importance of their consistent and accurate usage.
1. QNH and QFE are two distinct altimeter settings used in flight, each serving a specific purpose. QNH sets the altimeter to indicate altitude above mean sea level (MSL) by referencing standard atmospheric pressure, while QFE aligns the altimeter with the airfield elevation, effectively setting the runway as zero altitude. This difference in reference points can affect a pilot's perception of altitude and their situational awareness during flight.
2. The choice between QNH and QFE can influence approach altitudes, especially in variable weather conditions. For instance, using QFE might lead to lower reported altitudes compared to QNH, which could increase the risk of encountering terrain if not carefully managed during descent. This difference becomes crucial in mountainous or complex terrain.
3. Pilots often prefer QNH for its standardized reference across air traffic management (ATM) systems, especially in areas with diverse local altimeter settings. This standardized reference allows for easier coordination and altitude adjustments among aircraft, ultimately improving safety, particularly in busier airspace.
4. Atmospheric pressure changes significantly with weather patterns, requiring regular updates to the QNH setting. If the QNH is outdated, pilots might rely on inaccurate pressure information, resulting in altitude errors, particularly pronounced in areas with significant altitude variations, like mountainous terrain.
5. The sensitivity of QNH is quite apparent—a mere 1 hPa discrepancy can lead to an altitude error of roughly 30 feet. This highlights the need for thorough pre-flight calculations and continuous updates to maintain accurate altimeter readings for pilot and aircraft safety.
6. Some aircraft operations, like military and general aviation, might favor QFE for tactical or local flying, which simplifies referencing the airfield elevation. However, this can create confusion when transitioning to environments that predominantly use QNH, highlighting the need for consistent communication and understanding across operations.
7. While QFE is less common in commercial aviation, it finds frequent use in glider operations where maintaining proximity to the ground is essential for landing accuracy. This demonstrates the diversity in operational environments where pressure settings are critical for safety.
8. The accuracy of both QNH and QFE are susceptible to errors if factors like temperature, humidity, and altitude are not calculated properly. Accurate calibration of altimeter settings, therefore, remains critical for reliable navigation and overall aircraft safety in all phases of flight.
9. Improved atmospheric models, including updates to the International Standard Atmosphere (ISA), have led to a shift towards standardizing on QNH in many aviation sectors. This standardization promotes a more unified understanding of altitude information and minimizes discrepancies across different aviation contexts.
10. The integration of multi-function displays in modern avionics allows for the simultaneous presentation of QNH, QFE, and other pertinent pressure data. While this technology improves situational awareness and decision-making for pilots, it's crucial to ensure pilots retain fundamental knowledge of pressure-altitude relationships, as reliance solely on technology could lead to issues if systems malfunction or provide inaccurate readings.
Understanding Gauge vs
Absolute Pressure in Aircraft Altimeter Calibration A Technical Deep-Dive - Digital vs Analog Altimeter Calibration Techniques for Modern Aircraft
Modern aircraft increasingly feature both digital and analog altimeters, leading to a growing importance in understanding the distinct calibration techniques for each. Digital altimeters, with their advanced electronic components, often provide greater accuracy, sometimes displaying altitude down to a single foot. These systems also allow for more nimble adjustments during calibration. In contrast, analog altimeters, with their reliance on mechanical components, can be more susceptible to errors during calibration or when atmospheric pressure changes. The choice between these two types of altimeters, therefore, isn't simply a matter of preference but a careful evaluation of potential errors, pilot workload, and overall flight safety. As aircraft navigation grows more intricate, it's critical for aviation professionals to recognize the advantages and limitations of both digital and analog altimeter systems to ensure precise altitude readings and safe operations.
1. Digital altimeters offer a higher degree of accuracy in altitude readings compared to their analog counterparts, potentially reducing errors related to human interpretation. However, the immediate visual feedback provided by analog gauges can be beneficial in high-pressure situations, where rapid comprehension of altitude is critical.
2. Both types of altimeters demand regular calibration, but digital systems often incorporate self-diagnostic capabilities. These diagnostics can flag calibration errors with specific codes, providing engineers with a clearer pathway to pinpoint and rectify problems before a flight. This potentially simplifies maintenance and reduces the risk of undetected errors.
3. Digital altimeters rely on complex signal processing algorithms to translate raw pressure data into meaningful altitude information. This intricate relationship creates potential vulnerabilities. For instance, if a sensor surpasses the limits of its accompanying algorithms, it can lead to inaccurate altitude readings if not properly managed during design and maintenance.
4. Digital altimeters tend to be more sensitive to fluctuations in temperature and humidity compared to analog devices. While this sensitivity allows for more precise measurements under stable conditions, it also means digital systems may yield misleading altitude data if they are not carefully calibrated for anticipated operational environments.
5. The failure mechanisms of digital and analog altimeters differ. Mechanical failures, like sticking mechanisms or inaccurate readings, are common failure modes for analog systems. Digital systems can experience more complex issues like software glitches or memory overflow errors. If left unaddressed, such failures might go unnoticed until a critical juncture in a flight.
6. Maintenance procedures for digital and analog altimeters vary. Digital systems often necessitate specialized tools and software updates for calibration and diagnostics, while analog counterparts can be recalibrated through simpler mechanical adjustments. This difference highlights a trade-off between the level of maintenance support needed for each type of system.
7. Some modern aircraft incorporate analog backup altimeters, which act as a failsafe in the event of a complete electronic failure. This emphasis on redundancy underscores the importance of having fallback systems that can reliably maintain essential functions during critical situations.
8. Digital altimeters can overwhelm pilots with excessive information through a poorly designed user interface. This abundance of data, while potentially beneficial in some contexts, can actually hinder quick decision-making during complex flight phases. In contrast, analog systems provide a more direct and intuitive presentation of altitude, which is essential in high-stress environments.
9. Digital altimeters, owing to the underlying technology, have a defined limit to their operating range. If extreme changes in pressure occur, the sensor may reach a saturation point, producing inaccurate altitude indications. While rare, such events are something to consider, and this type of dynamic range limitation does not occur as frequently in analog systems.
10. The aerospace industry shows a steady trend towards incorporating increasingly complex digital systems in aircraft. However, the relative simplicity and proven reliability of analog altimeters remain valuable assets. Engineers often emphasize the significance of maintaining these technologies as a critical failsafe due to the inherent challenges in understanding and troubleshooting the intricacies of complex digital systems. This perspective highlights a persistent tension between technological advancement and a desire for systems that are easier to troubleshoot and understand.
More Posts from aistructuralreview.com: